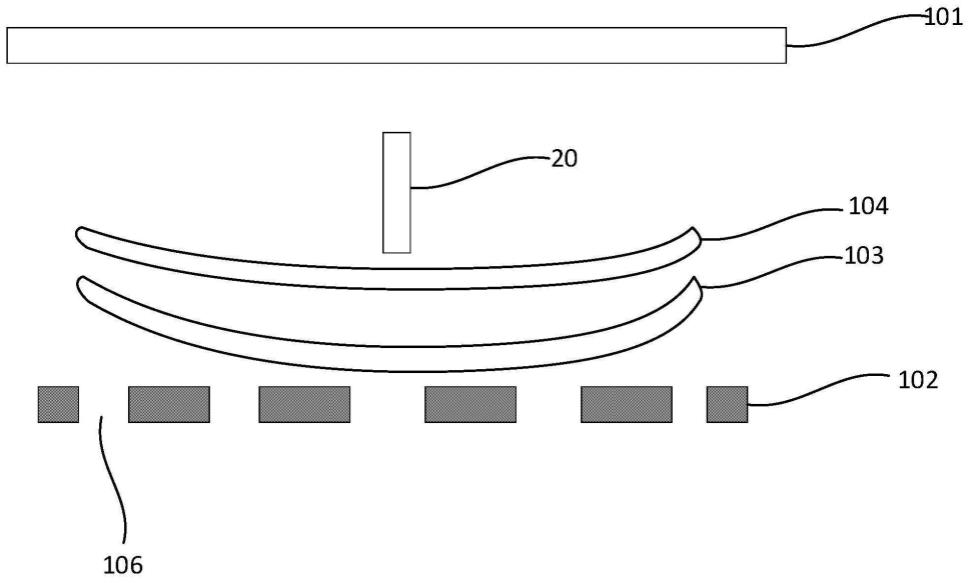
1.本发明属于半导体设备设计领域,特别是涉及一种晶圆键合设备。
背景技术:2.晶圆键合技术是指通过化学和物理作用将两块已镜面抛光的同质或异质的晶片紧密地结合起来,晶片接合后,界面的原子受到外力的作用而产生反应形成共价键结合成一体,并使接合界面达到特定的键合强度。
3.在mems和ic制造领域,键合工艺有着重要的地位,传统硅硅键合采用图形识别,镜头对准模式使上下硅片位置重合,继而进行直接键合。此模型在实际工艺操作中,由于硅片本身翘曲等因素,气体在键合过程中不易从硅片内部排出且会对位精度产生影响,典型的就是气泡增多或者对位精度较差,影响产品良率,极端情况下甚至报废产品。
4.通常的解决方式,就是管控前制程硅片来料的质量,键合之前要求硅片翘曲尽量保持一定的范围之内。但这样就无形之中给其他制程定义一个明显的卡控,使很多结构无法构建,且造成产品的生产过程成本大大的提高。
5.在mems和ic制造领域,为了满足不断增长的需求并克服摩尔定律的限制,多芯片堆叠作为一种解决方案被业界提出。随着先进封装技术的应用,2.5d堆叠采用硅通孔技术的发展与应用。如今,晶圆在竖直方向的扩展在所谓的3d堆叠中正变得越来越重要,而硅片之间混合键合技术被认为实现永久键合的最优方案。
6.实际工艺操作中,目前混合键合机台采用高精度对位系统,使上下晶圆基准对位,之后通过机台一个顶针对上层晶圆一个外部压力,让两片晶圆从中心开始接触,然后通过氢键迅速向四周蔓延,组中两片晶圆完成高精度预键合。
7.但是此过程有一个明显弊端,就是外部施加的压力会改变上层晶圆的形貌,尤其是受力点位会产生难以恢复的形变,导致后期预键合的晶圆产生轻微间隙且影响对准精度。这种形变对于厚度薄的基板越发明显。
技术实现要素:8.鉴于以上所述现有技术的缺点,本发明的目的在于提供一种晶圆键合设备,用于解决现有技术中半导体晶圆预键合受力过程产生的形变问题,以及如何减小形变量并提高键合精度的问题。
9.为实现上述目的及其他相关目的,本发明提供一种晶圆键合设备,所述晶圆键合设备包括:吸附装置,设置于第一晶圆及第二晶圆下方,所述第二晶圆位于所述第一晶圆上方;吹气顶针,设置于所述第二晶圆上方,用于在不接触所述第二晶圆的位置朝所述第二晶圆的中部区域进行吹气,以使所述第一晶圆与第二晶圆在吹气产生的压力下进行键合。
10.可选地,所述吹气顶针包括多个吹气孔,且各吹气孔产生的压力均独立可调,通过第一晶圆与第二晶圆的对位数据调整各吹气孔产生的压力,以减少第二晶圆的中部区域的形变和延展。
11.可选地,还包括一对准量测模块,用于获取第一晶圆与第二晶圆的对位数据,所述对位数据包括晶圆键合后受力区域形变量和延展量数据,并将该对位数据进行存储及反馈至所述晶圆键合设备。
12.可选地,所述吹气顶针配置有垂直运动装置,且在吹气顶针超所述第二晶圆的中部区域进行吹气时,所述吹气顶针与所述第二晶圆之间的间距为2~3毫米。
13.可选地,所述晶圆键合设备还包括:光敏测距器件,设置于第一晶圆及第二晶圆上方,用于通过光学信号的接收和反馈,确定第一晶圆与所述光敏测距器件的距离分布,以及确定第二晶圆与所述光敏测距器件的距离分布,从而获取所述第一晶圆的第一翘曲分布值及第二晶圆第二翘曲分布值;吸附装置,设置于第一晶圆下方,所述吸附装置包括多个吸附单元,以定量补偿第一晶圆的形变量所述吸附装置根据第一晶圆需要补偿的吸附值,自所述第一晶圆底部向所述第一晶圆给予吸附力,以定量补偿第一晶圆的形变量,使所述第一晶圆与所述第二晶圆的键合面保持相对平行。
14.可选地,所述光敏测距器件还用于依据第一翘曲分布值及第二晶圆第二翘曲分布值,获取第一晶圆各个区域所需要改变的形变量;所述吸附装置基于所述需要改变的形变量,控制相应区域的吸附力,以定量补偿第一晶圆的形变量,使所述第一晶圆与所述第二晶圆的键合面保持相对平行。
15.可选地,所述吸附力由以下公式获取:
16.f=k
△
x+b;
17.其中,f为吸附力,k为第二晶圆的弹性常数,b为固定常数。
18.可选地,所述吸附装置包括真空吸盘,所述真空吸盘表面具有多个吸附孔,通过设置所述真空吸盘的真空度以及吸附孔的孔径以调整所述吸附孔的吸附力,其中,所述吸附力的大小与所述真空度呈正相关,与所述吸附孔的孔径呈负相关。
19.可选地,所述真空吸盘包括多个真空腔体,各真空腔体对应设置有一个或多个吸附孔,且各真空腔体内的真空度独立可调,以控制相应区域的吸附力。
20.可选地,所述吸附孔的形状包括圆孔、弧形孔及环形孔中的一种。
21.如上所述,本发明的晶圆键合设备,具有以下有益效果:
22.本发明在键合机台在作业过程中,把受力顶针更改为多气孔的吹气顶针,使键合过程由硬接触变为软接触,克服晶圆受力发生形变问题,本发明采用多孔吹气的模式和机台内部反馈量测机制,可有效针对晶圆中间区域的精度和旋转偏差,进行有效的补偿,最终达到提高键合质量的效果。本发明可以完全解决键合过程中晶圆由于受力所产生的形变问题,提高键合精度和键合质量,实现真正意义上的晶圆之间金属互连技术。本发明可以和目前使用的混合键合机台很好的兼容性,具有很好的实际应用价值。
23.本发明根据上下两个晶圆的翘曲分布,对下卡盘不同区域接入相应的真空吸附孔,通过控制不同区域吸附孔的吸附值,机械改变底层晶圆的翘曲状况,使上下两个晶圆处于相对平行状态,使得在晶圆受力键合过程中,气泡和对准精度误差大大减少,提高键合工艺质量。
24.本发明在键合机台内部安装光敏测距器件,以及在下卡盘分区域接入不同吸附孔,通过机台内部模拟计算晶圆的翘曲分布,键合过程相应改变吸附值即可,与键合机台具有很好的兼容型,亦可广泛应用于多层键合,具有很好的实际应用价值。
25.采用本发明的设备及方法可以完全解决键合过程中晶圆翘曲以及键合时晶圆变形的问题,可以有效降低生产成本和工艺复杂度。
附图说明
26.图1显示为本发明实施例的晶圆键合设备的结构示意图。
27.图2显示为本发明实施例的晶圆键合设备的吸附装置的结构示意图。
28.图3显示为本发明实施例的晶圆键合设备获取晶圆翘曲分布值的原理示意图。
29.图4显示为本发明实施例的晶圆键合设备定量补偿晶圆定量补偿形变量的原理示意图。
30.图5显示为本发明实施例的晶圆键合设备的吹气顶针的吹气孔分布结构示意图。
31.图6显示本发明实施例量测键合后晶圆受力区域的形变量和延展量数据示意图。
32.图7显示为本发明实施例的晶圆键合设备的根据晶圆的数据进行补偿,通过调整对位数据和吹气孔不同气体的气量,有效地减少中心受力区域晶圆的形变和延展的示意图。
33.图8显示为本发明实施例的晶圆键合设备的吹气顶针可有效使晶圆受力均匀,从而发生规率形变的示意图。
34.图9显示为传统机台通过顶针对上层晶圆一个外部压力的,外部施加的压力改变上层晶圆的形貌的示意图。
35.元件标号说明
36.101
ꢀꢀꢀꢀꢀꢀꢀꢀꢀꢀꢀꢀꢀꢀꢀꢀꢀꢀꢀꢀꢀ
光敏测距器件
37.102
ꢀꢀꢀꢀꢀꢀꢀꢀꢀꢀꢀꢀꢀꢀꢀꢀꢀꢀꢀꢀꢀ
吸附装置
38.103
ꢀꢀꢀꢀꢀꢀꢀꢀꢀꢀꢀꢀꢀꢀꢀꢀꢀꢀꢀꢀꢀ
第一晶圆
39.104
ꢀꢀꢀꢀꢀꢀꢀꢀꢀꢀꢀꢀꢀꢀꢀꢀꢀꢀꢀꢀꢀ
第二晶圆
40.105
ꢀꢀꢀꢀꢀꢀꢀꢀꢀꢀꢀꢀꢀꢀꢀꢀꢀꢀꢀꢀꢀ
定量补偿形变量后的第一晶圆
41.106
ꢀꢀꢀꢀꢀꢀꢀꢀꢀꢀꢀꢀꢀꢀꢀꢀꢀꢀꢀꢀꢀ
吸附孔
42.1061
ꢀꢀꢀꢀꢀꢀꢀꢀꢀꢀꢀꢀꢀꢀꢀꢀꢀꢀꢀꢀ
圆孔
43.1062
ꢀꢀꢀꢀꢀꢀꢀꢀꢀꢀꢀꢀꢀꢀꢀꢀꢀꢀꢀꢀ
环形孔
44.1063
ꢀꢀꢀꢀꢀꢀꢀꢀꢀꢀꢀꢀꢀꢀꢀꢀꢀꢀꢀꢀ
弧形孔
45.20
ꢀꢀꢀꢀꢀꢀꢀꢀꢀꢀꢀꢀꢀꢀꢀꢀꢀꢀꢀꢀꢀꢀ
吹气顶针
46.201
ꢀꢀꢀꢀꢀꢀꢀꢀꢀꢀꢀꢀꢀꢀꢀꢀꢀꢀꢀꢀꢀ
吹气孔
47.30
ꢀꢀꢀꢀꢀꢀꢀꢀꢀꢀꢀꢀꢀꢀꢀꢀꢀꢀꢀꢀꢀꢀ
顶针
具体实施方式
48.以下通过特定的具体实例说明本发明的实施方式,本领域技术人员可由本说明书所揭露的内容轻易地了解本发明的其他优点与功效。本发明还可以通过另外不同的具体实施方式加以实施或应用,本说明书中的各项细节也可以基于不同观点与应用,在没有背离本发明的精神下进行各种修饰或改变。
49.如在详述本发明实施例时,为便于说明,表示器件结构的剖面图会不依一般比例作局部放大,而且所述示意图只是示例,其在此不应限制本发明保护的范围。此外,在实际
制作中应包含长度、宽度及深度的三维空间尺寸。
50.为了方便描述,此处可能使用诸如“之下”、“下方”、“低于”、“下面”、“上方”、“上”等的空间关系词语来描述附图中所示的一个元件或特征与其他元件或特征的关系。将理解到,这些空间关系词语意图包含使用中或操作中的器件的、除了附图中描绘的方向之外的其他方向。此外,当一层被称为在两层“之间”时,它可以是所述两层之间仅有的层,或者也可以存在一个或多个介于其间的层。
51.在本技术的上下文中,所描述的第一特征在第二特征“之上”的结构可以包括第一和第二特征形成为直接接触的实施例,也可以包括另外的特征形成在第一和第二特征之间的实施例,这样第一和第二特征可能不是直接接触。
52.需要说明的是,本实施例中所提供的图示仅以示意方式说明本发明的基本构想,遂图示中仅显示与本发明中有关的组件而非按照实际实施时的组件数目、形状及尺寸绘制,其实际实施时各组件的型态、数量及比例可为一种随意的改变,且其组件布局型态也可能更为复杂。
53.传统键合机台减小翘曲的模式一般是采用超大压力改变晶圆的翘曲值,但是这种模式会导致晶圆本身受压产生形变,影响键合精度。本发明的目的是在键合机台内部安装光敏测距器件101,模拟晶圆在键合过程中翘曲以及分布,继而反馈给键合机台。键合机台根据上下两层晶圆的翘曲分布,在键合过程受力过程中,分区域给予底层晶圆不同吸附强度,定量改变底层晶圆的翘曲值,使其接近顶层晶圆的翘曲分布,最终让两片晶圆保持相对的平行分布。
54.进一步地,目前混合晶圆直接键合技术,精度已经高达50nm,因此晶圆一个微小的形变都会影响到键合效果。传统通过机台一个顶针30对上层晶圆一个外部压力,如图9所示,让两片晶圆从中心开始接触,然后通过氢键迅速向四周蔓延,组中两片晶圆完成高精度预键合。但是此过程有一个明显弊端,就是外部施加的压力会改变上层晶圆的形貌,尤其是受力点位会产生难以恢复的形变,导致后期预键合的晶圆产生轻微间隙且影响对准精度。这种形变对于厚度薄的基板越发明显。
55.本发明通过量测两片晶圆的翘曲分布,计算出底层晶圆需要做出的形变。对于相同工艺制程的晶圆,其竖直方向的应变近似满足线性关系,相应写入键合机台生产程式,可针对来料晶圆不同的翘曲进行针对性的补偿,使其在键合过程始终中保持水平的状态,提高键合工艺质量。然后,在键合机台对位系统完成预对准之后,晶圆受到外力发生预键合,此时只需把外界对晶圆施加直接接触的外力,更改为气动阀控制的气流,通过吹气施力模型减少晶圆的形变量,继而克服键合受力过程中精度问题。且由于施力过程是发生在常温常压环境中,所以采用吹气施力模型不会对键合过程产生负面影响。
56.如图1及图8所示,本实施例提供一种晶圆键合设备,所述晶圆键合设备包括:光敏测距器件10、吸附装置102及吹气顶针。
57.吸附装置102设置于第一晶圆103及第二晶圆104下方,所述第二晶圆104位于所述第一晶圆103上方。
58.如图8所示,吹气顶针20设置于所述第二晶圆104上方,用于在不接触所述第二晶圆104的位置朝所述第二晶圆104的中部区域进行吹气,以使所述第一晶圆103与第二晶圆104在吹气产生的压力下进行键合。
59.如图5所示,所述吹气顶针20包括多个吹气孔201,且各吹气孔201产生的压力均独立可调,通过第一晶圆103与第二晶圆104的对位数据调整各吹气孔201产生的压力,以减少第二晶圆104的中部区域的形变和延展。所述吹气顶针20配置有垂直运动装置,且在吹气顶针超所述第二晶圆104的中部区域进行吹气时,所述吹气顶针20与所述第二晶圆104之间的间距为2~3毫米。
60.本发明采用吹气小孔吹气的模式施加压力,替代目前施力顶针局部硬接触,避免上层晶圆收到局部硬力,造成受力点区域形变过大。所述吹气顶针的气体可以采用氮气,且吹气顶针可沿用2cm
×
2cm的方形或直径2cm左右的圆形施力面积(与传统施力顶针的施力的面积保持一致),吹气小孔2mm
×
2mm(约50个气孔),且吹气小孔的气量可单独设置,因此采用吹气模式可有效使晶圆受力均匀,从而发生规率形变,如图8所示,保证键合过程中上下晶圆有序键合。
61.所述晶圆键合设备还包括一对准量测模块,用于获取第一晶圆103与第二晶圆104的对位数据,所述对位数据包括晶圆键合后受力区域形变量和延展量数据,如图6所示,并将该对位数据进行存储及反馈至所述晶圆键合设备。
62.另外,当晶圆完成键合之后,把晶圆传至对准量测模块,量测键合后晶圆受力区域形变量和延展量数据,如图6所示,之后可以根据此数据传回对准和吹气系统。按照同一批晶圆状态大约一致的规律,所述晶圆键合设备可以根据此晶圆的数据进行补偿,通过调整对位数据和吹气孔201不同气体的气量,如图7所示,有效地减少中心受力区域晶圆的形变和延展,保证在混合键合模式下对位的精度和电接触,实现真正意义下的金属互联。
63.所述光敏测距器件101设置于第一晶圆103及第二晶圆104上方,用于通过光学信号的接收和反馈,确定第一晶圆103的顶面与所述光敏测距器件101的距离分布,以及确定第二晶圆104的顶面与所述光敏测距器件101的距离分布,从而获取所述第一晶圆103的第一翘曲分布值及第二晶圆104第二翘曲分布值,所述第二晶圆104位于所述第一晶圆103上方。
64.例如,所述光敏测距器件101包括光敏测距卡盘,其向下方晶圆发射光线后经晶圆反射,当晶圆发生翘曲时,不同位置的反射光信号存在差异,光敏测距卡盘根据该差异确定晶圆的顶面与所述光敏测距卡盘的距离分布,从而获取所述晶圆的翘曲分布值,如图3所示。
65.在应用过程中,只需将所述光敏测距卡盘通过如螺丝等可拆卸的连接件将其固定于晶圆键合设备的内部上方即可,其可以与晶圆键合设备的供电线连接供电,也可以采用自身自带的电池供电,其可以通过有线或无线的方式,与所述吸附装置102连接,以实现其与所述吸附装置102的信号连接。
66.进一步地,在本实施例中,所述光敏测距器件101还用于依据第一翘曲分布值及第二晶圆104第二翘曲分布值,获取第二晶圆104各个区域所需要改变的形变量。
67.如图1~图4所示,所述吸附装置102设置于第一晶圆103下方,所述吸附装置102包括多个吸附单元,所述吸附装置102根据第一晶圆103需要补偿的吸附值,自所述第一晶圆103底部向所述第一晶圆103给予吸附力,以定量补偿第一晶圆103的形变量,获得定量补偿形变量后的第二晶圆105,使所述第一晶圆103与所述第二晶圆104的键合面保持相对平行。
68.在本实施例中,所述吸附装置102基于所述光敏测距器件101反馈的所述需要改变
的形变量,控制相应区域的吸附力,以定量补偿第一晶圆103的形变量,使所述第一晶圆103与所述第二晶圆104的键合面保持相对平行。
69.在本实施例中,所述吸附力由以下公式获取:f=k
△
x+b;其中,f为吸附力,k为第一晶圆103的弹性常数,b为固定常数。对于相同工艺制程的晶圆,其竖直方向的应变近似满足线性关系,相应写入键合设备生产程式,可针对来料晶圆不同的翘曲进行针对性的补偿,使其在键合过程始终中保持水平的状态,提高键合工艺质量。
70.如图1及图2所示,所述吸附装置102包括真空吸盘,所述真空吸盘表面具有多个吸附孔106,通过设置所述真空吸盘的真空度以及吸附孔106的孔径以调整所述吸附孔106的吸附力,其中,所述吸附力的大小与所述真空度呈正相关,与所述吸附孔106的孔径呈负相关。
71.为了进一步适应晶圆在不同区域的翘曲分布,在本实施例中,所述真空吸盘包括多个真空腔体,各真空腔体包含一个或多个吸附孔106,且各真空腔体内的真空度独立可调,以控制相应区域的吸附力。本示例分区域给予底层晶圆不同吸附强度,定量改变底层晶圆的翘曲值,使其接近顶层晶圆的翘曲分布,最终让两片晶圆保持相对的平行分布。
72.由于晶圆翘曲一般是晶圆边缘翘曲较为严重,而中部区域翘曲较小,在一个具体实施过程中,所述吸附装置102对应所述第一晶圆103边缘区域的吸附孔106的密度大于位于所述第一晶圆103中部区域的吸附孔106的密度,所述吸附装置102对应所述第一晶圆103边缘区域的吸附孔106的孔径小于位于所述第一晶圆103中部区域的吸附孔106的孔径。
73.所述吸附孔106的形状包括圆孔1061、弧形孔1063及环形孔1062中的一种,如图2所示,当然,所述吸附孔106的形状也可以为如矩形、三角形、菱形、椭圆形等,并不限于此处所列举的示例。在本实施例中,位于所述吸附装置102内部的吸附孔106为圆孔1061,位于所述吸附装置102中部的吸附孔106为环形孔1062,位于所述吸附装置102边缘的吸附孔106为弧形孔1063,进一步地,所述吸附装置102内部的圆孔1061、中部的环形孔1062及边缘的弧形孔1063均对应设置各自独立的真空腔,以使得各区域的吸附孔106的吸附力独立可调,该配置对改善晶圆翘曲适用性更广泛,可以应对大部分晶圆翘曲的形变补偿,从而在大部分情况下,不需要更换吸附装置102便能实现晶圆翘曲的形变补偿,可有效节约成本。
74.如图1~图4所示,本实施例还提供一种消除晶圆翘曲的晶圆键合方法,包括:
75.步骤1),提供如上任意一项所述的晶圆键合设备;
76.步骤2),将第一晶圆103放置于所述晶圆键合设备内,基于光敏测距器件101,通过光学信号的接收和反馈,确定第一晶圆103的顶面与所述光敏测距器件101的距离分布,从而获取所述第一晶圆103的第一翘曲分布值。
77.步骤3),将第二晶圆104放置于所述晶圆键合设备内的第一晶圆103上方,基于光敏测距器件101,通过光学信号的接收和反馈,确定第二晶圆104的顶面与所述光敏测距器件101的距离分布,从而获取所述第二晶圆104第二翘曲分布值。
78.步骤4),依据第一翘曲分布值及第二晶圆104第二翘曲分布值,获取第一晶圆103各个区域所需要改变的形变量;吸附装置102根据第一晶圆103需要补偿的吸附值,自所述第一晶圆103底部向所述第一晶圆103给予吸附力,以定量补偿第一晶圆103的形变量,使所述第一晶圆103与所述第二晶圆104的键合面保持相对平行。
79.步骤5),晶圆键合设备根据上一片键合片精度量测结果,由键合机台内部程式计
算得出此片晶圆需要补偿的值,进而得出各个气孔需要施加气体气量及速率。
80.步骤6),吹气顶针20向下缓慢移动,等到距离第一晶圆2-3mm时候停止运动,之后通过吹气孔201对第一晶圆103施加一个向下的压力,气体的气量可根据产品的厚度及芯片的尺寸相应调整,施力时间维持3-5秒。
81.步骤7),吹气过程结束,晶圆中心区域完成键合,之后其它区域由于氢键而迅速键合在一起,最终整片晶圆完成预键合。
82.步骤8),预键合之后的晶圆叠片,通过传送装置送至对准量测模块,进行键合精度量测,并把结果反馈给晶圆键合设备。
83.步骤9),完成键合精度量测,晶圆叠片再由传送装置送出晶圆键合设备,作业结束。
84.如上所述,本发明的晶圆键合设备,具有以下有益效果:
85.本发明在键合机台在作业过程中,把受力顶针更改为多气孔的吹气顶针,使键合过程由硬接触变为软接触,克服晶圆受力发生形变问题,本发明采用多孔吹气的模式和机台内部反馈量测机制,可有效针对晶圆中间区域的精度和旋转偏差,进行有效的补偿,最终达到提高键合质量的效果。本发明可以完全解决键合过程中晶圆由于受力所产生的形变问题,提高键合精度和键合质量,实现真正意义上的晶圆之间金属互连技术。本发明可以和目前使用的混合键合机台很好的兼容性,具有很好的实际应用价值。
86.本发明根据上下两个晶圆的翘曲分布,对下卡盘不同区域接入相应的真空吸附孔,通过控制不同区域吸附孔的吸附值,机械改变底层晶圆的翘曲状况,使上下两个晶圆处于相对平行状态,使得在晶圆受力键合过程中,气泡和对准精度误差大大减少,提高键合工艺质量。
87.本发明在键合机台内部安装光敏测距器件,以及在下卡盘分区域接入不同吸附孔,通过机台内部模拟计算晶圆的翘曲分布,键合过程相应改变吸附值即可,与键合机台具有很好的兼容型,亦可广泛应用于多层键合,具有很好的实际应用价值。
88.采用本发明的设备及方法可以完全解决键合过程中晶圆翘曲以及键合时晶圆变形的问题,可以有效降低生产成本和工艺复杂度。
89.所以,本发明有效克服了现有技术中的种种缺点而具高度产业利用价值。
90.上述实施例仅例示性说明本发明的原理及其功效,而非用于限制本发明。任何熟悉此技术的人士皆可在不违背本发明的精神及范畴下,对上述实施例进行修饰或改变。因此,举凡所属技术领域中具有通常知识者在未脱离本发明所揭示的精神与技术思想下所完成的一切等效修饰或改变,仍应由本发明的权利要求所涵盖。