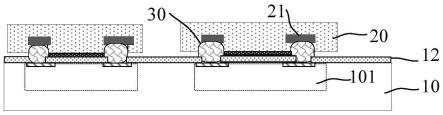
1.本发明涉及半导体器件制造领域,尤其涉及一种晶圆级系统封装方法。
背景技术:2.随着超大规模集成电路的发展趋势,集成电路特征尺寸持续减小,人们对集成电路的封装技术的要求相应也不断提高。现有的封装技术包括球栅阵列封装(ball grid array,bga)、芯片尺寸封装(chip scale package,csp)、晶圆级封装(wafer level package,wlp)、三维封装(3d)和系统封装(system in package,sip)。
3.目前,为了满足集成电路封装的更低成本、更可靠、更快及更高密度的目标,先进的封装方法主要采用三维立体堆叠模式的晶圆级系统封装(wafer level package system in package,wlpsip),与传统的系统封装相比,晶圆级系统封装是在晶圆上完成封装集成制程,具有大幅减小封装结构的面积、降低制造成本、优化电性能、批次制造等优势,可明显的降低工作量与设备的需求。
4.在晶圆级系统封装工艺中,不仅需要将两片裸芯片键合在一起以实现物理连接,同时还需要连接其互连引线,从而实现电性连接。
技术实现要素:5.本发明的目的在于提供一种晶圆级系统封装方法,简化封装工艺。
6.为了实现上述目的,本发明提供一种晶圆级系统封装方法,包括:
7.提供器件晶圆,所述器件晶圆包括多个第一芯片,所述第一芯片具有暴露出所述器件晶圆上表面的第一焊垫;
8.通过电镀工艺在所述第一焊垫上形成导电凸块;
9.形成所述导电凸块后,提供至少一个第二芯片,所述第二芯片的下表面具有第二焊垫;
10.将所述第二芯片键合在所述器件晶圆上,并使所述第二芯片的第二焊垫与所述导电凸块电连接。
11.本发明的有益效果在于:
12.通过电镀工艺形成导电凸块,之后进行焊接工艺完成晶圆级系统集成,电镀工艺可以同时形成整个晶圆上的导电凸块,可以提高效率,而且,与半导体的前段工艺兼容,从而可以利用前段工艺完成晶圆级系统集成,使整个系统集成的工艺效率大大提升,节省了前段工艺与封装工艺之间的转接。
13.进一步地,通过干膜键合第二芯片和器件晶圆,一方面干膜是可光刻材料,可以通过半导体工艺形成所需的图案样式,工艺简单且与半导体工艺兼容,可批量化生产。而且干膜的弹性模量比较小,在受到热应力时可以很容易变形而不至于破损,减小第二芯片与器件晶圆的结合应力。光刻干膜时,可以在预形成导电凸块的区域外周保留围墙结构的干膜,这样在形成导电凸块时,由于干膜的阻挡,可以形成预期形状的导电凸块,防止导电凸块横
向外溢。
14.进一步地,形成可光刻的键合材料时,其投影以第二芯片的中心为中心,覆盖面积大于第二芯片面积的10%,优选覆盖第二芯片的全部下表面(除第二焊垫所在的区域),这样,在后续工艺形成塑封层时,保证第二芯片下方没有空隙,提高结合强度,提高成品率。
15.进一步地,通过将多个第二芯片先键合在器件晶圆上,对多个第二芯片实现了预对准,因此多个第二芯片与导电凸块可以同时进行热压键合,相较于将每个第二芯片和导电凸块依次键合大幅度提高了制造效率。进一步地,第二焊垫与导电凸块在垂直于器件晶圆表面方向上重叠区域的面积大于第二焊垫面积的一半,以提高两者的结合强度。
附图说明
16.为了更清楚地说明本发明实施例或现有技术中的技术方案,下面将对实施例或现有技术描述中所需要使用的附图作简单地介绍,显而易见地,下面描述中的附图仅仅是本发明的一些实施例,对于本领域普通技术人员来讲,在不付出创造性劳动的前提下,还可以根据这些附图获得其他的附图。
17.图1至图8示出了根据本发明实施例1的一种晶圆级系统封装方法中不同步骤中对应的结构示意图。
18.图9示出了根据本发明实施例2的一种晶圆级系统封装方法中形成开口步骤中对应的结构示意图。
19.附图标记说明:
20.10-晶圆;11-第一焊垫;101-第一芯片;12-介质层;13-硅通孔结构;20-第二芯片;21-第二焊垫;30-导电凸块;40-可光刻的键合材料;50-封装层;41-开口;60-封盖基板;200-基板;61-电连接结构。
具体实施方式
21.以下结合附图和具体实施例对本发明进一步详细说明。根据下面的说明和附图,本发明的优点和特征将更清楚,然而,需说明的是,本发明技术方案的构思可按照多种不同的形式实施,并不局限于在此阐述的特定实施例。附图均采用非常简化的形式且均使用非精准的比例,仅用以方便、明晰地辅助说明本发明实施例的目的。
22.应当明白,当元件或层被称为“在...上”、“与...相邻”、“连接到”或“耦合到”其它元件或层时,其可以直接地在其它元件或层上、与之相邻、连接或耦合到其它元件或层,或者可以存在居间的元件或层。相反,当元件被称为“直接在...上”、“与...直接相邻”、“直接连接到”或“直接耦合到”其它元件或层时,则不存在居间的元件或层。应当明白,尽管可使用术语第一、第二、第三等描述各种元件、部件、区、层和/或部分,这些元件、部件、区、层和/或部分不应当被这些术语限制。这些术语仅仅用来区分一个元件、部件、区、层或部分与另一个元件、部件、区、层或部分。因此,在不脱离本发明教导之下,下面讨论的第一元件、部件、区、层或部分可表示为第二元件、部件、区、层或部分。
23.空间关系术语例如“在...下”、“在...下面”、“下面的”、“在...之下”、“在...之上”、“上面的”等,在这里可为了方便描述而被使用从而描述图中所示的一个元件或特征与其它元件或特征的关系。应当明白,除了图中所示的取向以外,空间关系术语意图还包括使
用和操作中的器件的不同取向。例如,如果附图中的器件翻转,然后,描述为“在其它元件下面”或“在其之下”或“在其下”元件或特征将取向为在其它元件或特征“上”。因此,示例性术语“在...下面”和“在...下”可包括上和下两个取向。器件可以另外地取向(旋转90度或其它取向)并且在此使用的空间描述语相应地被解释。
24.在此使用的术语的目的仅在于描述具体实施例并且不作为本发明的限制。在此使用时,单数形式的“一”、“一个”和“所述/该”也意图包括复数形式,除非上下文清楚指出另外的方式。还应明白术语“组成”和/或“包括”,当在该说明书中使用时,确定所述特征、整数、步骤、操作、元件和/或部件的存在,但不排除一个或更多其它的特征、整数、步骤、操作、元件、部件和/或组的存在或添加。在此使用时,术语“和/或”包括相关所列项目的任何及所有组合。
25.如果本文的方法包括一系列步骤,且本文所呈现的这些步骤的顺序并非必须是可执行这些步骤的唯一顺序,且一些的步骤可被省略和/或一些本文未描述的其他步骤可被添加到该方法。若某附图中的构件与其他附图中的构件相同,虽然在所有附图中都可轻易辨认出这些构件,但为了使附图的说明更为清楚,本说明书不会将所有相同构件的标号标于每一图中。
26.实施例1
27.本发明一实施例提供了一种晶圆级系统封装方法,包括以下步骤:
28.s01:提供器件晶圆,所述器件晶圆包括第一芯片,所述第一芯片具有暴露出所述器件晶圆上表面的第一焊垫;
29.s02:通过电镀工艺在所述第一焊垫上形成导电凸块;
30.s03:形成所述导电凸块后,提供至少一个第二芯片,所述第二芯片的下表面具有第二焊垫;
31.s04:将所述第二芯片键合在所述器件晶圆上,并使所述第二芯片的第二焊垫与所述导电凸块电连接。
32.需要说明的是,本说明书中的s0n不代表制造工艺的先后顺序。
33.图1至图8示出了本实施例的晶圆级系统封装方法的不同步骤对应的结构示意图,请参考图1至图8,详细说明各步骤。
34.参考图1,提供器件晶圆,器件晶圆包括晶圆10以及形成在所述晶圆10上表面的第一芯片101,所述第一芯片101的上表面暴露出第一焊垫11,第一焊垫11可以是焊盘(pad)。本实施例中,晶圆10为硅衬底。在其他实施例中,所述晶圆10的材料还可以为锗、锗化硅、碳化硅、砷化镓或镓化铟等其他半导体材料,所述半导体衬底还能够为绝缘体上的硅衬底或者绝缘体上的锗衬底等其他类型的衬底。所述半导体材料可以是适宜于工艺需要或易于集成的材料。根据实际工艺需求,所述晶圆10的厚度为10微米至100微米。
35.第一芯片101可以是通过半导体工艺形成在晶圆10上。如,所述器件晶圆为完成器件制作的待封装晶圆。形成于晶圆10中的多个第一芯片101可以为同一类型或不同类型的芯片。需要说明的是,所述器件晶圆可以采用集成电路制作技术所制成,例如在第一半导体衬底上通过沉积、刻蚀等工艺形成n型金属氧化物半导体(n-metal-oxide-semiconductor,nmos)器件和p型金属氧化物半导体(p-metal-oxide-semiconductor,pmos)器件等,在所述器件上形成介质层、金属互连结构以及与所述金属互连结电连接的焊盘等结构,从而使所
述器件晶圆中集成至少一个第一芯片101。
36.在另一实施例中,第一芯片101可以是制作好的芯片,粘合在器件晶圆的上表面。此时,器件晶圆内部没有微器件,器件晶圆也可以内部集成有mos管等微器件,第一芯片与微器件通过互连结构电连接。
37.继续参考图1,本实施例中,器件晶圆的上表面形成有露出所述第一焊垫11的介质层12。介质层12具有一定的厚度,可以在后续形成导电凸块的步骤中提供空间。
38.参考图2,在器件晶圆的上表面形成可光刻的键合材料40,所述可光刻的键合材料40用于在后期工艺中将第二芯片粘合在器件晶圆的上表面。本实施例中,可光刻的键合材料40包括膜状干膜或液态干膜,在其他实施例中,也可以选择其他光敏粘合材料。膜状干膜是将无溶剂型光致抗蚀剂涂在涤纶片基上,再覆上聚乙烯薄膜;使用时揭去聚乙烯薄膜,把无溶剂型光致抗蚀剂压于基版上,经曝光显影处理,即可在干膜内形成图形。液态干膜指的是膜状干膜中的成分以液态的形式存在。干膜是一种永久键合膜,粘结强度较高。膜状干膜可以通过贴膜的方式形成在器件晶圆上,液态干膜通过旋涂工艺涂布在器件晶圆上,之后对液态干膜进行固化处理。通过干膜键合第二芯片和器件晶圆,一方面干膜是可光刻材料,可以通过半导体工艺形成所需的图案样式,工艺简单且与半导体工艺兼容,可批量化生产。而且干膜的弹性模量比较小,在受到热应力时可以很容易变形而不至于破损,减小第二芯片与器件晶圆的结合应力。
39.在一个可选的实施例中,形成完所述可光刻的键合材料后,还包括:图形化所述可光刻的键合材料,在预形成所述导电凸块的区域外周形成围墙结构。围墙结构围成的内部为形成导电凸块的区域,围墙结构优选为封闭的环形结构,围成的空间为柱形。光刻可光刻的键合材料时,在预形成导电凸块的区域外周保留围墙结构的可光刻的键合材料,这样在形成导电凸块时,由于围墙的阻挡,可以形成预期形状的导电凸块,防止导电凸块横向外溢。
40.本实施例中,可光刻的键合材料40形成在器件晶圆的表面,在另一个实施例中,可光刻的键合材料40也可以形成在第二芯片20的表面。
41.本实施例中,形成的所述可光刻的键合材料40的厚度为5-200μm,如15μm、30μm、80μm、150μm等。且所述可光刻的键合材料40在所述器件晶圆表面方向上的投影以所述第二芯片20的中心为中心,并至少覆盖所述第二芯片面积的10%。具体为,可光刻的键合材料40的厚度和后期工艺中形成的导电凸块的高度相关。两者的相关性在后面形成导电凸块的时候进行详细介绍。本实施例中,可光刻的键合材料40至少覆盖第二芯片面积的10%,其覆盖在第二芯片的中央位置。优选覆盖第二芯片的全部下表面(除第二焊垫所在的区域)。因为在后续工艺中形成塑封层时,塑封层不容易填充至第二芯片的中间位置(因为距离第二芯片的边缘较远),本方案的可光刻的键合材料40不但起到粘合的作用,还起到了提前密封的作用,可光刻的键合材料40和后续工艺中的塑封层共同起到密封第二芯片的作用。可选方案中,可光刻的键合材料40覆盖第二芯片20的全部下表面(除第二焊垫所在的区域),这样,在后续工艺形成塑封层时,保证第二芯片下方没有空隙,提高结合强度,提高成品率。
42.继续参考图2,通过电镀工艺在所述第一焊垫11上形成导电凸块30。导电凸块的材料包括:铜、钛、铝、金、镍、铁、锡、银、锌或铬中的任意一种。
43.形成的导电凸块30的高度和干膜的高度以及第二芯片的结构有关系,当第二芯片
的第二焊垫与第二芯片的下表面相平时,导电凸块30的高度和干膜的高度(本实施例中还包括介质层12的高度)大致等高,这样第二芯片和干膜粘合的同时,第二焊垫21与导电凸块30正好相接触。当第二焊垫21相对于第二芯片20的下表面向下凹陷时,导电凸块30的高度等于凹陷的深度+干膜厚度+介质层12的厚度。可选实施例中,导电凸块的高度为5-200μm。如10μm、50μm、100μm。
44.电镀工艺包括化学镀钯浸金(enepig)或化学镍金(enig),其中enepig或enig的工艺参数可以参照表1。
45.表1
[0046][0047]
通过电镀工艺形成导电凸块,之后进行焊接工艺完成晶圆级系统集成,电镀工艺可以同时形成整个晶圆上的导电凸块,可以提高效率,而且,与半导体的前段工艺兼容,从而可以利用前段工艺完成晶圆级系统集成,使整个系统集成的工艺效率大大提升,节省了前段工艺与封装工艺之间的转接。
[0048]
在进行化学镀之前,为了更好的完成电镀工艺,可以先对焊垫的表面进行清洁,以去除焊垫表面的自然氧化层、提高焊垫的表面湿润度(wetabilities);之后,可以进行活化工艺,促进镀层金属在待镀金属上的形核生长。
[0049]
为了更好的实现电镀,形成比较完善的导电凸块40,第一焊垫、第二焊垫的设置也需要满足一定的要求,比如:所述第一焊垫暴露出面积为5-200平方微米,在该范围内,焊垫可以与电镀液较充分的接触,避免焊垫与镀液不充分接触而影响导电凸块与焊垫的接触,比如接触面积过小影响电阻,或者,无法接触造成电接触不良;而且,也可以保证接触面积不会过大而降低电镀效率及不会占用过多的面。
[0050]
形成的导电凸块的横截面积大于10平方微米,既可以保证导电凸块占用的面积不会太大,也可以保证导电凸块与焊垫之间的结合强度。
[0051]
可选方案中,导电凸块的材料与第一焊垫的材料相同,这样更容易形成导电凸块。当然,第一焊垫的材料可以与导电凸块的材料不同,为了后续更容易形成导电凸块,可以在第一焊垫上先形成材料层,该材料层的材料与导电凸块的材料相同,形成材料层的方法可以为沉积工艺。
[0052]
参考图3,提供至少一个第二芯片20,所述第二芯片20的下表面具有第二焊垫21。所述第二芯片20用于作为晶圆级封装中的待集成芯片,本实施例晶圆级封装方法可以实现异质集成。相应地,所述第二芯片20可以是硅晶圆制成的芯片,也可以是其他材质形成的芯片。所述第二芯片20采用集成电路制作技术所制成,可以为存储芯片、通讯芯片、处理器或
逻辑芯片。所述第二芯片20通常包括形成于半导体衬底上的nmos器件或pmos器件等。第二焊垫21位于所述第二芯片20的下表面,用于实现所述第二芯片200与其他器件的电性连接。具体地,所述第二焊垫21可以是焊盘(pad)。本实施例中,所述第二焊垫21的材料包括铜、钛、铝、金、镍、铁、锡、银、锌或铬中的任意一种,优选方案中,第二焊垫和导电凸块的材料组合包括金-金、铜-铜、铜-锡或金-锡。
[0053]
多个第二芯片为同功能芯片;所述多个第二芯片至少包括两种不同功能的芯片;所述第一芯片为无源器件或者有源器件。
[0054]
所述第二芯片可以是传感器模组芯片、mems芯片、滤波器芯片、逻辑芯片、存储芯片、电容、电感等,电容可以是mlcc电容。所述传感器模组芯片包括至少传感射频信号、红外辐射信号、可见光信号、声波信号、电磁波信号其中之一的模组芯片;所述滤波器芯片包括:表面声波谐振器、体声波谐振器至少其中之一。第二芯片可以是经过封装的芯片,则后续无需进行塑封工艺。第二芯片也可以是经过裸芯片,第二芯片也可以是顶面有屏蔽层的芯片。
[0055]
本实施例中,所述第二焊垫21和所述导电凸块30的材料为金属,通过热压键合工艺将所述第二焊垫21与所述导电凸块30电连接。每个所述第二焊垫21与每个所述导电凸块30逐一进行热压键合;或者多个所述第二焊垫21与多个所述导电凸块30同时进行热压键合。通过将多个第二芯片20先键合在器件晶圆上,对多个第二芯片20实现了预对准,因此多个第二芯片20与导电凸块30可以同时进行热压键合,相较于将每个第二芯片20和导电凸块30依次键合大幅度提高了制造效率。
[0056]
本实施例中,所述第一焊垫11或所述第二焊垫21的面积为5-200平方微米;第二焊垫21与导电凸块30在垂直于器件晶圆表面方向上重叠区域的面积大于第二焊垫21面积的一半,以提高两者的结合强度,可选方案中,导电凸块30和第二焊垫21相互正对,即在垂直于器件晶圆表面方向上,两者最大程度上相互重叠。在可选方案中,所述导电凸块的横截面积大于10平方微米,以保证结构强度。
[0057]
本实施例中,多个第二芯片20逐一键合在晶圆的表面。参考图4,在另一个实施例中,所述第二芯片20具有第二焊垫21的面为正面,与正面相背的面为背面,所述第二芯片20键合于所述器件晶圆之前,将所述第二芯片20的背面临时键合于基板200上;将所述第二芯片20键合在所述晶圆上后,解键合所述基板。基板200可以是载体晶圆,用于临时固定所述多个第二芯片20,所述基板200还用于在第二芯片20与器件晶圆键合的过程中,为第二芯片20起到支撑作用,从而提高键合的可靠性。所述第二芯片20通过粘合层或静电键合临时键合于所述基板200上。静电键合技术是不用任何粘结剂实现键合的一种方法。在键合过程中,将要键合的第二芯片和基板分别连接不同的电极,在电压作用下使第二芯片和基板表面形成电荷,且所述第二芯片与基板表面电荷电性不同,从而在第二芯片与基板键合过程中产生较大的静电引力,实现两者的物理连接。相应地,在解键合的过程中,可以通过化学方法或机械剥离的方式使所述基板与所述第二芯片20相分离。
[0058]
参考图5,本实施例中,键合所述第二芯片20后还包括:形成塑封层50,所述塑封层50至少填充于相邻的所述第二芯片之间。本实施例中,所述封装层50覆盖器件晶圆的表面及所述第二芯片20,也就是说,所述封装层50填充于所述第二芯片20之间的间隙且覆盖在第二芯片20上.塑封层实现对第二芯片的密封,从而更好地隔绝空气和水分,进而提高了封装效果。具体地,可以通过注塑工艺形成所述封装层50。注塑工艺的填充性能较好,可以使
注塑剂较好地填充在多个第二芯片20之间,从而使第二芯片20具有良好的封装效果。在其他实施例中,还可以采用其他工艺形成所述封装层。另外,根据第二芯片的不同性能,第二芯片的上表面也可以暴露在塑封层的外部。
[0059]
参考图6,本实施例中,第一芯片101与第一焊垫相对的表面(图5中第一芯片101的下表面)具有第三焊垫,形成所述塑封层50后,本方法还包括:对所述器件晶圆的背面进行减薄处理;并从减薄后的所述器件晶圆的背面形成硅通孔结构13,所述硅通孔结构13连接于所述第三焊垫。
[0060]
通过对所述器件晶圆的背面进行减薄处理,以减小所述器件晶圆的厚度,从而改善所述器件晶圆的散热效果;此外,减小所述器件晶圆的厚度还有利于减小形成通孔互连结构的难度以及减小封装后封装结构的整体厚度,进而提高所述封装结构的性能。本实施例中,所述减薄处理所采用的工艺可以为背部研磨工艺、化学机械抛光(chemical mechanical polishing,cmp)工艺和湿法刻蚀工艺中的一种或多种。
[0061]
为了有效控制所述减薄处理的停止位置,在所述器件晶圆的制造工艺中,通常在所述器件晶圆的半导体衬底内形成用于限定所述停止位置的深沟槽隔离结构,从而使所述减薄处理停止于所述深沟槽隔离结构的底部。在另一实施例中,还可以在所述器件晶圆的制造工艺中,采用中性掺杂离子(例如氧离子和氮离子中的一种或两种)在所述器件晶圆的半导体衬底内形成停止区,从而使所述减薄处理停止于所述停止区的底部。在其他实施例中,当所述器件晶圆的半导体衬底为绝缘体上的硅衬底或者绝缘体上的锗衬底时,还可以对所述半导体衬底的底部衬底层进行减薄处理,从而能够较好地停止于所述绝缘体层的底部。
[0062]
需要说明的是,在所述减薄处理后,所述器件晶圆的厚度不宜过小,也不宜过大。如果所述器件晶圆的厚度过小,则所述器件晶圆的机械性能相应较差,且容易对形成于所述器件晶圆内的器件等结构产生不良影响;如果所述器件晶圆的厚度过大,则不利于提高所述封装结构的性能。为此,本实施例中,减薄之后所述器件晶圆的厚度为5μm至10μm。
[0063]
在对器件晶圆减薄处理后,在所述器件晶圆内形成与所述第三焊垫电连接的硅通孔结构13。通过所述硅通孔结构13实现与第三焊垫电连接。由于所述第二芯片20与所述第一焊垫11通过导电凸块30电性连接,因此所述第二芯片20通过所述导电凸块20、第一焊垫11以及硅通孔结构13与其他电路电性连接。
[0064]
参考图7和图8,在一个实施例中,键合所述第二芯片后(图3之后),所述方法还包括:提供封盖基板60,所述封盖基板60的第一表面包含空腔,键合所述封盖基板60的第一表面与所述器件晶圆,并使所述空腔至少遮盖所述第二芯片的一部分。封盖基板60的材料可以为:可以为硅、锗、锗化硅、碳化硅、砷化镓或镓化铟等半导体材料,也可以是介质材料。封盖基板60中形成有空腔,空腔可以较大,一个空腔可以同时容纳多个第二芯片20,封盖基板也可以包括多个子空腔,每个子空腔容纳一个或多个第二芯片20。参考图8,在可选的实施例中,空腔也可以只覆盖一个第二芯片20的一部分,如只覆盖第二芯片的主体部分。如对于体声波谐振器或者表声波谐振器或者红外热堆传感器,芯片需要形成有空腔结构,并且空腔结构对应芯片结构的功能区,并不是将整个芯片包括在空腔中。如对于体声波谐振器(baw)和表声波谐振器(saw)以及牢固安置型体声波谐振器(smr)在主体谐振区上方设置有上空腔,本实施例中的空腔可以作为上空腔,对于红外热电堆传感器,其功能区下方设置有
用于隔热的隔热空腔,本实施例形成的空腔可以作为隔热空腔,对于超声波传感器,膜状的振动部悬空设置,上表面用于接收超声波,下表面遮盖空腔,本实施例的空腔可以作为超声波传感器的下空腔。
[0065]
可选实施例中,封盖基板键合在器件晶圆上后,形成的空腔为密封的空腔,可以防止外界环境对空腔内器件的污染(水分、灰尘、油脂等)。继续参考图8,在一个实施例中,第二芯片包括互连结构,互连结构暴露出第二芯片的上表面,所述方法还包括:形成贯穿所述封盖基板60的电性引出结构61,所述电性引出结构61的一端连接于所述第二芯片的互连结构,另一端位于所述封盖基板60的上表面。通过电连接结构61,将所述第二芯片20的电性引出。
[0066]
实施例2
[0067]
参考图9,本实施例与实施例1的区别在于,第二芯片20下方需要有空腔,形成完可光刻的键合材料40后,还包括:图形化可光刻的键合材料40,在可光刻的键合材料40中形成开口41,开口41的深度等于或小于可光刻的键合材料40的厚度。形成开口41的区域对应第二芯片20的工作区域,后期工艺键合第二芯片后,形成空腔,此空腔作为第二芯片的工作腔(如隔热空腔)。当第二芯片20的下方需要形成空腔时,通过在可光刻的键合层中形成开口,可以节省工艺步骤(否则需要在制造第二芯片时形成空腔)。本实施例中,开口41用于隔热,因此对于开口41的深度并不做限定,开口41可以贯穿可光刻的键合材料40(开口深度与可光刻的键合材料40厚度相同)也可以只贯穿可光刻的键合材料40的一部分厚度(开口深度小于可光刻的键合材料40的厚度)。在其他实施例中,如果需要对开口的深度进行限定,则在形成可光刻的键合材料时,形成合适的厚度。对于空腔型体声波谐振器(fbar)和表声波谐振器(saw)在主体谐振区下方设置有下空腔,上方形成有封盖,封盖和主体谐振区之间形成了上空腔,本实施例中的空腔可以即可以作为上空腔也可以作为下空腔。对于牢固安置型体声波谐振器(smr),其上方也封盖之间形成有上空腔,本实施例中的空腔可以作为上空腔。对于红外热电堆传感器,其功能区下方设置有用于隔热的隔热空腔,本实施例形成的空腔可以作为隔热空腔。对于超声波传感器,膜状的振动部悬空设置,上表面用于接收超声波,下表面遮盖空腔,本实施例的空腔可以作为超声波传感器的下空腔。
[0068]
综上,通过电镀工艺形成导电凸块,之后进行焊接工艺完成晶圆级系统集成,电镀工艺可以同时形成整个晶圆上的导电凸块,可以提高效率,而且,与半导体的前段工艺兼容,从而可以利用前段工艺完成晶圆级系统集成,使整个系统集成的工艺效率大大提升,节省了前段工艺与封装工艺之间的转接。
[0069]
进一步地,通过干膜键合第二芯片和器件晶圆,一方面干膜是可光刻材料,可以通过半导体工艺形成所需的图案样式,工艺简单且与半导体工艺兼容,可批量化生产。而且干膜的弹性模量比较小,在受到热应力时可以很容易变形而不至于破损,减小第二芯片与器件晶圆的结合应力。光刻干膜时,可以在预形成导电凸块的区域外周保留围墙结构的干膜,这样在形成导电凸块时,由于干膜的阻挡,可以形成预期形状的导电凸块,防止导电凸块横向外溢。
[0070]
进一步地,形成可光刻的键合材料时,其投影以第二芯片的中心为中心,覆盖面积大于第二芯片面积的10%,优选覆盖第二芯片的全部下表面(除第二焊垫所在的区域),这样,在后续工艺形成塑封层时,保证第二芯片下方没有空隙,提高结合强度,提高成品率。
[0071]
进一步地,通过将多个第二芯片先键合在器件晶圆上,对多个第二芯片实现了预对准,因此多个第二芯片与导电凸块可以同时进行热压键合,相较于将每个第二芯片和导电凸块依次键合大幅度提高了制造效率。进一步地,第二焊垫与导电凸块在垂直于器件晶圆表面方向上重叠区域的面积大于第二焊垫面积的一半,以提高两者的结合强度。
[0072]
需要说明的是,本说明书中的各个实施例均采用相关的方式描述,各个实施例之间相同相似的部分互相参见即可,每个实施例重点说明的都是与其他实施例的不同之处。
[0073]
上述描述仅是对本发明较佳实施例的描述,并非对本发明范围的任何限定,本发明领域的普通技术人员根据上述揭示内容做的任何变更、修饰,均属于权利要求书的保护范围。