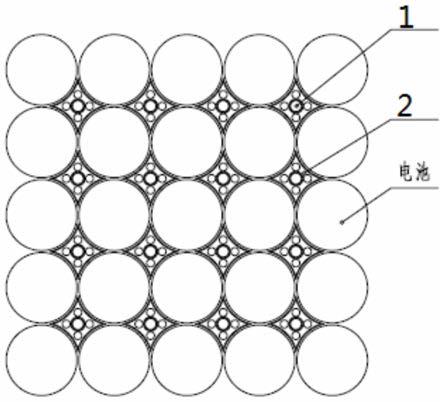
1.本申请涉及一种电池换热器及其制备方法,适用于蓄能产品换热的技术领域。
背景技术:2.由于日益加剧的环境问题与能源危机,在减少石油资源消耗和降低污染物排放等方面具有突出优势的新能源汽车,在近几年受到了全球范围内的普遍重视,而电动汽车在新能源汽车中最具代表性。动力电池组作为电动汽车的动力源,其工作性能的优劣将直接决定电动汽车的整车性能。当动力电池组在高温环境下工作或进行大电流充放电时,电池温度迅速上升,造成电池循环寿命下降,甚至会引起电池起火爆炸等安全问题。另一方面,若动力电池组中各电池单体间存在较大的温度差异,将导致电池组整体性能降低。为了将动力电池的温度控制在适宜的温度范围内,并保障电池温度的均匀性,需要为电动汽车动力电池组设计合理的电池热管理系统。
3.随着电池热管理技术的发展,形成了多种电池热管理系统,根据系统散热介质的不同可以将其分为基于空气介质的电池热管理系统、基于液体介质的电池热管理系统、基于相变材料的电池热管理系统和其它电池热管理系统。基于空气介质的电池热管理系统,是指通过自然对流或强制对流,使低温空气流经电池表面与电池进行热交换,以实现冷却电池的热管理系统。基于液体介质的电池热管理系统,是指通过使液体直接或间接与电池接触并进行热交换,以实现冷却电池的热管理系统。基于相变材料的电池热管理系统,是指采用相变材料将电池包覆,当相变材料吸收电池热量发生相变时,相变材料温度将维持在某一恒定值,以实现冷却电池的热管理系统。其他电池热管理系统包括通过热管、热电材料或多种散热方式相结合,以实现冷却电池的热管理系统。
技术实现要素:4.本申请的目的是设计一种电池换热器及其制备方法,其中的电池换热器基于空气介质,适用于自然对流或者强制对流对电池进行换热,具有换热面积大、换热效率高等优势,同时换热器位于电池之间的空隙,不占用额外的空间,从而可以在电池箱内放入更多的电池。
5.本申请涉及一种电池换热器,包括间隔设置的进料集管和出料集管,在所述进料集管和所述出料集管之间设置有多根管路,所述管路的一端连接所述进料集管,管路的另一端连接所述出料集管,所述管路设置在电池之间的空隙内,其中,所述进料集管和所述出料集管将多根并联的管路进行连接;或者,多根并联的管路串联成组,所述进料集管和所述出料集管将已经串联成组的管路进行连接。
6.其中,所述管路上横向设置有翅片,所述管路和所述翅片置于相邻电池之间的空隙内,所述翅片上设有与所述管路配合的通孔,所述翅片在所述管路的轴向配合处设置翻边;所述电池换热器的换热面与电池面贴合;所述进料集管设置在所述出料集管的上方;所述翅片上还设置有换热用的孔洞;所述翅片的外圈还设置有卷边。
7.本申请还涉及一种电池组件,包括多个电池形成的电池阵列和电池换热器,其特征在于,所述电池换热器是如上所述的电池换热器。
8.本申请还涉及一种新能源汽车,包括如上所述的电池组件。
9.本申请还涉及一种电池换热器的制备方法,包括以下步骤:
10.(1)管路落料:将管路按照设定长度进行裁剪落料;
11.(2)冲制翅片:将板料冲制成所需的翅片,翅片在冲制后堆叠成设定间距的翅片串;
12.(3)套片:将管路穿过翅片上的通孔,翅片上与管路配合的通孔稍大于管路的外径;
13.(4)组装:对需要弯管的管路进行弯管整形,进料集管、出料集管上的通孔对准管路,将管路伸进进料集管、出料集管上的通孔内,保持适当的伸进长度;
14.(5)钎焊:用工装模具夹持,将组装好的换热器放进钎焊炉内进行整体高温钎焊,利用管路、翅片、进料集管、出料集管上的钎焊镀层高温钎焊并在常温凝固,对管路配合间隙实现密封连接;
15.(6)检验:对换热器各个接管密封处进行密封性检查。
16.本申请还涉及一种电池换热器的制备方法,包括以下步骤:
17.(1)管路落料:将管路按照设定长度进行裁剪落料;;
18.(2)冲制翅片:将板料冲制成所需的翅片,翅片在冲制后堆叠成设定间距的翅片串;
19.(3)套片:将管路穿过翅片上的通孔,翅片上与管路配合的通孔稍大于管路的外径;
20.(4)胀管:利用球径比管路内径大但又小于翅片上通孔的胀珠在管路内拉胀或者用高压流体在管路内对管路形成塑性变形,将管路胀到与翅片过盈配合;
21.(5)组装:对需要弯管的管路进行弯管整形,将套片胀管的管路与进料集管、出料集管上的通孔组装在一起;
22.(6)焊接:采用高温火焰焊接的方式,将管路各个连接处进行焊接密封;
23.(7)检验:对换热器各个接管密封处进行密封性检查。
24.本申请的电池换热器布置在电池之间的空隙内,不额外占用电池箱的有效空间,可以在同样空间的电池箱内容纳更多电池,增加了汽车的续航里程。本申请所述的换热器与电池换热面实现配合接触,增大了电池换热面积的同时,减少了新能源汽车在行驶过程颠簸电池对换热器的冲击,增强了换热器的可靠性。
附图说明
25.图1显示本申请电池换热器中的管路的布置示意图。
26.图2显示本申请电池换热器的立体图。
27.图3显示本申请电池换热器中的管路的截面图。
28.图4显示本申请电池换热器中的翅片的示意图。
29.图5显示本申请电池换热器中的进料集管和出料集管的示意图。
30.图6显示本申请电池换热器中设有翅片的管路示意图。
31.图7显示本申请电池换热器的另一种实施例。
32.图8显示本申请电池换热器的又一种实施例。
具体实施方式
33.为使本申请的目的、技术方案和优点更加清楚明白,下文中将结合附图对本申请的实施例进行详细说明。需要说明的是,在不冲突的情况下,本申请中的实施例及实施例中的特征可以相互任意组合。
34.如图1
‑
2所示,本申请的电池换热器包括间隔设置的进料集管3和出料集管4,在进料集管3和出料集管4之间设置有多根管路1,管路1的一端连接进料集管3,管路1的另一端连接出料集管4,管路1设置在电池的空隙内。为了增大换热面积,还可以在管路1上横向布置翅片2。优选地,本申请的电池换热器的换热面与电池面贴合,这样电池的圆柱面的绝大部分面积可以与换热面进行热交换,提高了换热量。需要说明的是,本申请中进料集管和出料集管可以分别设置在电池的上下位置,也可以分别设置在电池的左右位置,还可以是其他方式的间隔设置;进料集管和出料集管的通道面积比值可以是0.1
‑
10。
35.电池换热器的管路1和翅片2置于电池阵列中相邻电池之间的空隙内。换热器内换热介质的循环流动,将通过换热器的管路1和翅片2与电池接触进行传导换热,也可以通过换热器的管路1和翅片2与电池之间的空气进行自然对流或强制对流换热。优选地,本申请中的进料集管3设置在出料集管4的上方,管路内流动的换热介质是从上向下方向流动,由于电池产生的热空气往上运行,因此可以与电池产生的热进行逆向热交换,从而提高换热效率。
36.换热介质从进料集管3流进换热器,并通过管路1和翅片2将换热介质的能量输出,随后换热介质进入出料集管4并流出换热器。进一步,为了实现换热器的管路1内换热介质均匀分布循环流动,在进料集管3和进料集管4内可以设置有挡流板5。为了进一步提高换热介质与管路的换热效率,管路1内的通道在轴向上可以是螺纹型。
37.在一种实施方式中,如图3所示,可以将管路1的外形与电池之间所形成的空隙相吻合,其中,图3中的左侧显示单通道管路的示意图,右侧显示多通道管路的示意图。如此设置,在增大管路换热面积的同时,与电池形成良好的接触减少空气热阻,提高换热效率。同时管路与电池之间的间隙减小,防止由于颠簸振动造成冲击损坏。
38.翅片2可以是铜、铝或不锈钢等金属薄片构成,具有良好的热传导性能。如图4所示,翅片2上设有与管路1配合的通孔21,翅片2与管路1可以通过过盈配合或者钎焊及粘结等方式,形成良好的热接触关系。翅片2的形状可以是圆形、椭圆形或者多边形等。翅片2在管路1轴向上可以形成密集排布,翅片2的外圈还可以设置卷边22,在增大换热面积的同时,也使翅片2形成一个具有较大机械强度的整体,增加抵抗颠簸振动引起的电池对换热器翅片的冲击,同时也防止翅片2对电池的冲击损伤。翅片2在管路1轴向上可以是等距离均匀排布,也可以根据热空气上升、冷空气下降的基本常识,进行不等间距排布。翅片2在管路1的轴向配合处设置翻边24,翻边可以进一步增大翅片2与管路1的接触面积,同时翅片2在管路1轴向的间距可以通过翻边形成的台阶高度进行精确控制,如图6所示。
39.优选地,如图4所示,翅片2上还可以设置孔洞23,当自然对流换热器发生轴向温度不均匀时,可以进一步进行换热。当强制对流时,空气流可以通过这些孔洞与翅片2进行换
热。
40.本申请中,进料集管3、出料集管4可以是由铜、铝、不锈钢等金属材料制成,在进料集管3、出料集管4上设有多个连接孔31,连接孔31的形状与管路1的轴向截面形状相匹配。进料集管3、出料集管4的轴向截面形状可以是圆形、椭圆形或多边形等。进料集管3、出料集管4与管路1可以通过钎焊等加工方式形成良好的密封结构,防止换热介质通过两者之间的配合间隙泄漏。
41.由于进料集管3、出料集管4设置在电池的两端,为了防止进料集管3、出料集管4对电池电极形成短路连接,可以在进料集管3、出料集管4与电池接触处用空间距离形成空气绝缘或者用绝缘材料进行隔离。进料集管3、出料集管4可以是直管,也可以是s型管,以便适应管路1在电池模组之间的布置。进一步的,如图5所示,为了减小进料集管3、出料集管4迂回过程所形成尺寸增加电池箱内占据的空间,可以采用圆弧过渡连接的方式,连接处采用钎焊的方式形成良好的密封结构。
42.本申请中,进料集管3、出料集管4可以通过“s”型迂回方式将多根并联的管路1进行密封连接,也可以将多根并联的管路1进行串联成组,然后再用进料集管3、出料集管4将已经串联成组的管路1进行密封连接,如图7所示。管路1可以是直管或“s”型管。
43.本申请的电池换热器进一步增大了换热效率,能够减少新能源汽车有限电能的无用功耗,从而进一步增加了新能源汽车的续航里程。
44.本申请还涉及一种电池组件,包括多个电池形成的电池阵列和如上所述的电池换热器,其中电池换热器的管路设置在电池之间形成的空隙内。本申请的电池组件的改进点在于电池换热器,其他部件可以采用现有技术,不再赘述。
45.本申请还涉及一种新能源汽车,其设有包括如上所述的电池换热器的电池组件。本申请的新能源汽车的改进点在于电池换热器,其他部件可以采用现有技术,不再赘述。需要说明的是,本申请所述的电池换热器不仅适用上述的新能源汽车电池组件的换热,同样可以用在其他储能设备内的换热。
46.如图8所示,在安装电池组件时,电池可以成组地放入换热器内,便于装配。由于换热器管路的进出接口及进料集管、出料集管都在一侧,可以对该侧进行绝缘处理形成绝缘层,防止电池与电池之间形成通路。
47.本申请所述的电池换热器由于管路、翅片所使用的材质是铝质与所使用的铜、或者不锈钢等其他金属材料,所采用的加工工艺略有不同。
48.一种铝质电池换热器的制备工艺,包括以下步骤:
49.(1)铝管落料:将铝管按照设定长度进行裁剪落料;
50.(2)冲制翅片:将铝板放入冲床冲制成所需的翅片,为了便于翅片套入铝管内,不再对翅片进行整理,翅片在冲制后堆叠成设定间距的翅片串;
51.(3)套片:将铝管穿过翅片上的通孔,为了便于套片,翅片上与铝管配合的通孔尺寸要稍大于铝管的外径或者形成的外形尺寸;
52.(4)组装:对需要弯管的管路按照要求进行弯管整形,进料集管、出料集管上的通孔对准铝管,将铝管伸进进料集管、出料集管上的通孔内,保持适当的伸进长度,至少要大于进料集管、出料集管壁厚的一倍;
53.(5)钎焊:用适当的工装模具夹持,将组装好的换热器半成品放进钎焊炉内进行整
体高温钎焊,利用铝管、翅片、进料集管、出料集管上的钎焊镀层高温钎焊并在常温凝固,对管路配合间隙实现密封连接;为了防止在焊接高温时环境中的氧气对铝质材料的氧化,可以采用氮气或者真空等方式实现保护;
54.(6)检验:用水检漏、氟检漏或者氦检漏等检漏手段,对换热器各个接管密封处进行气密性检查。
55.一种铜质、钢质等其他材料的电池换热器的制备工艺,包括以下步骤:
56.(1)落料:将铜管、不锈钢管按照设定长度进行裁剪落料;
57.(2)冲制翅片:将铜板或不锈钢板放入冲床冲制成所需的翅片,为了便于翅片套入管内,不再对翅片进行整理,翅片在冲制后堆叠成设定间距的翅片串;
58.(3)套片:将铜管、不锈钢管等其他金属管材穿过翅片上的通孔,为了便于套片,翅片上与铜管、不锈钢管等其他金属管材配合的通孔尺寸,要稍大于铜管、不锈钢管等其他金属管材的外径或者形成的外形尺寸;
59.(4)胀管:利用球径比管路内径大但又小于翅片上通孔的胀珠在管路内拉胀或者用高压流体在管路内对管路形成塑性变形,将管路胀到与翅片紧密过盈配合;
60.(5)组装:对需要弯管的管路进行弯管整形,将套片胀管的管路与进料集管、出料集管上的通孔组装在一起;
61.(6)焊接:采用高温火焰焊接的方式,将管路各个连接处进行焊接密封;
62.(7)检验:用水检漏、氟检漏或者氦检漏等检漏手段,对换热器各个接管密封处进行气密性检查。
63.虽然本申请所揭露的实施方式如上,但所述的内容只是为了便于理解本申请而采用的实施方式,并非用以限定本申请。任何本申请所属技术领域内的技术人员,在不脱离本申请所揭露的精神和范围的前提下,可以在实施的形式上及细节上作任何的修改与变化,但本申请的专利保护范围,仍须以所附的权利要求书所界定的范围为准。