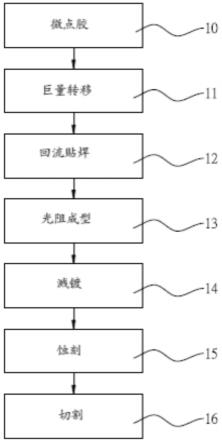
1.本发明涉及影像显示的领域,特别是指一种像素单元,其能电连接一个显示设备。
背景技术:2.已知的显示设备包括:液晶系技术(即液晶显示面板,原文缩写lcd) 和电浆系技术(即电浆显示面板)两种技术,让显示器拥有大尺寸与使用期限长的发光面板。然而,液晶显示面板存在功率效率与方向性等问题,电浆显示面板则有功率消耗和屏幕烙印等问题。
3.以有机发光二极管(organic light-emitting diode,缩写为oled)为基础开发的替代技术,迄今仍未得到令人满意的成果。甚至,该oled的使用期限较短,造成显示器的闪烁问题,降低智能型手机采用oled制作显示器的意愿。
4.另外,所述的lcd、电浆显示面板与oled等技术,采用薄膜沉积技术制造的控制电路称为薄膜晶体管(thin-film transistor,缩写为tft)。譬如 lcd通过连续沉积原料的薄膜形成5到9个通道区,电连接控制电路的晶体管、电容器、电气线路等组件,故依tft技术制造的控制电路成本非常昂贵。同时,tft技术制作大尺寸主动阵列,需要大面积沉积薄膜的机器或设备,实质上增加制造的成本,成为少数的投资者能够经营高成本tft技术的门坎。
5.因此,本案发明人致力于低成本、整合性高且量产率佳的发光装置研究,并申请中国第202010849066.3号、美国第16/999,086号以及中国台湾第 109125291号等国家和地区的专利,在案可稽。
技术实现要素:6.然而,本案发明人不因此自满,仍旧持续相关领域的技术研究,发明一种像素单元,其主要目的在于:延续前述的研究方向,实现微小体积的微型 led,占用显示设备最小的表面积,不仅具备影像完整的像素,而且填充率较佳。
7.本发明的像素单元制法,其主要目的在于:导电膜配合电极将电流导向焊垫,生产多个电连接点的像素单元,故焊垫是微型led与电极的共面电接触点,能够直接地结合显示设备的驱动电路,减少配电的线材数量。
8.源于上述目的的达成,本发明的像素单元,包括:一组焊垫;一个或多个电极焊接或固晶于对应的焊垫;一颗或多个微型led焊接或固晶于对应的焊垫,该微型led周边涂布一个光阻层,该光阻层不遮蔽微型led的顶面;一个外壳直接或间接包住光阻层与电极,使微型led和电极的顶面露出外壳;以及,一层导电膜形成于外壳的表面,该导电膜内侧的一个电路布局面电连接微型led与电极的顶面。
9.如此,本发明的像素单元,延续前述的研究方向,实现微小体积的微型 led,占用显示设备最小的表面积,不仅具备影像完整的像素,而且填充率较佳。其次,导电膜配合电极将电流导向焊垫,生产多个电连接点的像素单元,故焊垫是微型led与电极的共面电接触点,能够直接地结合显示设备的驱动电路,减少配电的线材数量。
10.为使本发明的目的、特征和优点浅显易懂,兹举一个或以上较佳的实施例,配合所
附的图式详细说明如下。
附图说明
11.图1为本发明制作像素单元的第一流程。
12.图2~9为第一流程从组件到成品的具体结构。
13.图10为第一流程制作像素单元的内部构造。
14.图11为本发明制作像素单元的第二流程。
15.图12~16为第二流程局部的构成。
16.图17为第二流程制作像素单元的内部构造。
17.附图标记说明:10、51-微点胶;11、52-巨量转移;12、53-回流贴焊; 13、54-光阻成型;14、55-溅镀;15、56-蚀刻;16、57-切割;17、67-像素单元;20-基板;21-接着物;22-移动平台;23-柱;24、61-成形部;25-贴附部; 26-焊垫;27、66-外壳;28-光阻层;30-led组;31-微型led;32、33-电极; 40-导电膜;41-电路布局面;42-第一纹路;43-第二纹路;50-基板成型;60
‑ꢀ
形成手段;62-槽;63-孔;64-填隙部。
具体实施方式
18.在图1中,从一项微点胶10步骤开始,历经巨量转移11、回流贴焊12、光阻成型13、溅镀14和蚀刻15等程序,到一项切割16步骤为止,完成本发明的第一流程,取得大量的像素单元。图2~图9显示组件到成品的具体结构,有助于第一流程的了解。通过图10的剖视角度,探索一个像素单元17的内部构造。
19.如图1、图2所示,通过至少一个移动设备(图未示),在一片基板20 布置一些接着物21,完成微点胶10步骤。该接着物21在基板20的部位是预先设置的。
20.在本实施例,该基板20是具备导电特性的金属板,如铜板。当然,其他具备导电特性的板片,亦能充当基板20使用。
21.此处所称的接着物21,泛指锡膏与银胶之一,或是其他具备导电性的焊料。
22.如图1、图3所示,在巨量转移11步骤中,单次转移若干led组30与多颗电极32到基板20的接着物21上。
23.其中,单颗电极32和led组30聚在一起。每个led组30是由三颗微型led 31所组成,每颗微型led 31的体积是一般led(原文light-emitting diode)体积的1/100。通电后,这些微型led 31分别发射红、绿、蓝(r、 g、b)光。
24.此处所称的转移,泛指一个移动平台22的底面配置多根柱23。在本实施例,四根柱23排成正方形视为一组。当移动平台22沿着高度方向执行升降运动,每组柱23的端面能够附着三颗微型led 31与单颗电极32。在移动平台22顺着水平方向位移,每组柱23带动led组30和电极32来到基板20 上方。待移动平台22再次升降运动后,该柱23离开led组30或电极32,该led组30或电极32粘着基板20的接着物21。
25.如图1、图4所示,进行回流贴焊12步骤,通过接着物21的加热固化手段,使led组30和电极32固定在基板20的单面。
26.此处所称的加热固化,泛指接着物21被回流焊接(reflow)技术熔化并冷却为贴附部25(见图6),该贴附部25是固体,足以让微型led 31与电极32紧密贴合(或附着)在基板20
表面。因此,所述的回流贴焊12步骤,又称固晶流程。
27.光阻成型13流程分成前、后步骤进行。前半部的流程中,除了顶面以外,该微型led 31的周围表面形成一个光阻层28。
28.此处所称的光阻层28,泛指光阻剂历经曝光显影的变化,保留在微型led31表面的物体。由于微型led 31的顶面发光,其底面接触贴附部25(见第 6图),只能用喷涂设备将光阻剂涂布在微型led 31周围的表面形成光阻层 28。
29.如图1、图5所示,光阻成型13步骤的后半段,通过一体成型手段,以不导电材料构成一层成形部24结合基板20的单面。同时,该成形部24包裹微型led 31的光阻层28(见图6)与电极32周围,使微型led 31和电极 32的顶面露出成形部24。
30.在本实施例,所述的成形部24通常会采用热固性塑料,譬如人造树脂 (epoxy resin)、环氧树脂(epoxy)等。通过不导电的热固性塑料制作成形部24自然是绝缘的。
31.如图1、图6所示,在成形部24、led组30和电极32的表面溅镀一层导电膜40,该导电膜40内侧具备一个电路布局面41,该电路布局面41电连接微型led 31与电极32的顶面,完成溅镀14步骤。
32.此处所称的溅镀(sputter deposition coating),泛指电浆体高能量的离子撞击固体靶(target)或源(source)的原子,该原子离开固体进入气体的物理过程。根据电子学的知识或技术人员的经验,溅镀亦称溅射(sputtering),属于气相沉积技术之一。
33.此处所称的导电膜40,其成分包括:氧化铟锡(ito)或掺锡氧化铟。由于氧化铟锡是铟(iii族)氧化物(in2o3)与锡(iv族)氧化物(sno2) 的混合物,在薄膜状态具备无色的透明特性,故导电膜40是透明的。
34.如图1、图7、图8所示,蚀刻14步骤的标的,区分为基板20与导电膜 40二对象。
35.此处所称的蚀刻,泛指酸性、腐蚀性或有研磨效能的物质,在固体的表面达成刻印或移除的目的。比方说,通过电浆的解离,形成离子与物质表面进行化学反应或是物理轰击,属于非等向性蚀刻(又称干式蚀刻)。或者,物质和化学液体进行化学反应,属于等向性蚀刻(亦称湿式蚀刻)。
36.在图7中,通过蚀刻的手段,该导电膜40形成相交的多条第一纹路42 和第二纹路43,从而在导电膜40表面规划若干方格区域。
37.在图8中,通过蚀刻的手段,该基板20(见图7)去除多余的部分形成多组焊垫26,该焊垫26连接贴附部25(见图10)而保留在成形部24的表面。
38.如图1、图7、图9、图10所示,依第一、第二纹路42、43方向,以雷射手段精准的切开导电膜40和成形部24,取得大量的像素单元17成品,完成切割15步骤。此刻,四片焊垫26为一组,配合电路布局面41电连接微型 led 31与电极32,共同组成像素单元17的电路。同时,该成形部24分成多个外壳27,这些外壳27的数量等于像素单元17的数量,每个外壳27是不导电的,包覆电性相连的led组30和电极32。
39.从图9、图10来看,该像素单元17的内部结构包括:一组焊垫26;一个电极32电连接该组焊垫26之一;三颗分别发射红、绿、蓝(r、g、b) 光的微型led 31为一个led组30,该led组30电连接其他的焊垫26,每颗微型led 31周边涂布一个光阻层28,该光阻层28不遮蔽微型led 31的顶面;一个不导电的外壳27包住光阻层28与电极32周围,使led组30和电极32的顶面露出外壳27;以及,一层导电膜40形成于外壳27、led组 30和电极32的表面,该导电膜
40内侧的一个电路布局面41电连接微型led31与电极32的顶面。
40.在电路方面,该微型led 31隶属p型或n型半导体,该半导体具备p、 n二个电极。假设,该微型led 31的n电极通过贴附部25电连接焊垫26,以微型led 31的p电极电连接导电膜40的电路布局面41,该电路布局面41 经由电极32电连接另一个焊垫26。
41.使用时,该像素单元17的焊垫26电连接一个显示设备(图未示),负极电流经焊垫26传输至微型led 31的n电极,正极电流通过电极32与电路布局面41输出至微型led 31的p电极。通电后,该微型led 31发射红、绿、蓝(r、g、b)光之一。
42.在本实施例,该光阻层28是黑色的,吸收所有的光,不反射任何颜色的光。该微型led 31的光入射透明的导电膜40,产生正确的颜色或趋近于真实的颜色。如此,该显示设备具备微型led 31的数量愈多,代表显示设备的分辨率愈高。同时,该微型led 31发射正确的光色,或是趋近于真实颜色,代表影像接近真实的物体。
43.根据第一流程,该像素单元17的优点:首先,该像素单元17拥有红、绿、蓝(r、g、b)三色光的微型led 31,不仅具备影像完整的像素(pixel),而且微型led 31的体积微小,使像素单元17占用显示设备的表面积最小,深具较佳的填充率。
44.其次,该焊垫26是微型led 31与电极32的共面电接触点,能够直接地结合显示设备的驱动电路。
45.再者,第一流程完成大量的微型led 31制作,产生多个电连接点的像素单元17,减少配电的线材数量。
46.图11是流程图,描绘本发明的第二流程,从一项基板成型50步骤开始,历经微点胶51、巨量转移52、回流贴焊53、光阻成型54、溅镀55和蚀刻56 等程序,到切割57步骤为止,取得功能相同于第一流程的像素单元。图12 ~图16显示部分组件的具体结构,有助于第二流程的了解。通过图17的剖视角度,探索像素单元67的内部构造。
47.如图11~图13所示,通过形成手段60,以不导电材料构成的成形部61 结合于基板20的单面,完成基板成型50步骤。采用三个槽62搭配一个孔63 的排列模式,顺着厚度方向凹陷于成形部61。在本实施例,该槽62是方形,该孔63是圆的,二者不会贯穿基板20。换句话说,所述的基板20封住槽62 与孔63的底部。
48.此处所称的形成手段60,泛指一体成型或是射出成型等技术之一。
49.所述的不导电材料,通常是指人造树脂(epoxy resin)、环氧树脂(epoxy) 等热固性塑料,具备不导电特性。因此,该成形部61是绝缘的。
50.利用移动设备(图未示)运送接着物布置在槽62或孔63底部的基板20 表面,完成微点胶51步骤。所述的接着物是锡膏、银胶或其他具备导电性的焊料。所述的基板20是铜板,或其他具备导电特性的板片。
51.如图11、图14所示,单次转移若干led组30与多颗电极33经过基板 20的槽62与孔63落在接着物上面,完成巨量转移52步骤。因为三个槽62 与一个孔63聚在一起,所以三颗微型led 31构成单一led组30和单颗电极33也聚在一起。当然,每颗微型led 41的体积是一般led体积的1/100,通电发射红光、绿光或蓝光。
52.在本实施例,该电极33是圆柱体,符合孔63的造型,却不同于前述的矩形体。
53.此处所称的转移,利用移动平台22的柱23(请参考图3)搬运led组30和电极33,故不予赘述。
54.该接着物被回流焊接技术熔化,冷却为固态的贴附部25,使微型led 31 与电极33贴附在基板20表面,完成回流贴焊53步骤。
55.光阻成型54前半段的流程,该微型led 31与槽62的壁面维持一个距离,允许光阻剂涂布微型led 31的周围,让一个光阻层28形成于微型led 31 的周围表面,却不遮蔽微型led 31的顶面。必要时,利用一个刷具刮除微型 led 31顶面的光阻剂,在本发明的容许范围内。
56.至于光阻剂如何成为光阻层28,请参考前面的说明,于此不再赘述。
57.光阻成型54步骤的后半段流程,则是让填隙剂无气泡地注入微型led 31 与槽壁的空隙,以及孔63的壁面至电极33的空隙,进而成为不导电的一个填隙部64。同时,该填隙部64包裹光阻层28,该微型led 31顶面的电极端露出填隙部64。当然,该填隙部64也能围住电极33周边,却不会覆盖电极 33的顶面。如此,该微型led 31和电极33的顶面就会露出成形部61与填隙部64。
58.如图11、图15所示,在led组30、电极33、成形部61和填隙部64的表面溅镀单层导电膜40,该导电膜40内侧的电路布局面41电连接微型led31与电极33的顶面,完成溅镀55步骤。
59.如图11、图16所示,蚀刻56步骤之标的区分为二:一为基板20,一为导电膜40。通过蚀刻的手段,在导电膜40形成多条相交的第一、第二纹路 42、43,并规划若干方格区域。
60.通过蚀刻的手段,该基板20去除多余部分形成多组焊垫26(参阅第8图),该焊垫26连接贴附部25(见图17)而保留在成形部61的表面。
61.如图11、图16、图17所示,依第一、第二纹路42、43方向,以雷射手段精准的切开导电膜40和成形部61,取得大量具备外壳66的像素单元67,完成切割57步骤。该像素单元67大致相同于第一流程的像素单元,故外壳 66还是拥有不导电特性,差异处在于:多了填隙部64,相对改变外壳66、微型led 31与电极33的联结关系。
62.从图17来看,该像素单元67的结构包括:一组焊垫26;一个电极33电连接该组焊垫26之一;三颗分别发射红、绿、蓝光的微型led 31为一个led 组30,该led组30电连接其他的焊垫26,每颗微型led 31周边涂布一个光阻层28,该光阻层28不遮蔽微型led 31的顶面;一个不导电的外壳66 形成多组槽62与多个孔63,该槽62接收相应的微型led 31,该微型led 31 电连接的焊垫26封住槽62底部,该孔63接收电极33,该电极33电连接的焊垫26封住孔63底部;多个填隙部64,该填隙部64填补微型led 31与槽 62的空隙,使外壳66间接包住光阻层28,抑或填补电极33和孔63的空隙,使外壳66间接包住电极33周围,使微型led 31和电极33的顶面露出填隙部64和外壳66;以及,一层导电膜40形成于外壳66、led组30、电极33 和填隙部64的表面,该导电膜40内侧一个电路布局面41电连接微型led 31 与电极33的顶面。
63.使用时,该像素单元67同样具备:
64.一、用三个微型led 31发射红、绿、蓝三色混成白光,不仅具备影像完整的像素,而且微型led 31微小的体积,使像素单元67占用显示设备的表面积最小,深具较佳的填充率。
65.二、该焊垫26是微型led 31与电极33的共面电接触点,能够直接地结合显示设备的驱动电路。
66.三、第二流程完成大量的微型led 31制作,产生多个电连接点的像素单元67,减少配电的线材数量。
67.在某些实施例中,该像素单元包括:一组焊垫;一个或多个电极焊接或固晶于对应的焊垫;一颗或多颗微型led焊接或固晶于对应的焊垫,该微型 led周边涂布一个光阻层,该光阻层不遮蔽微型led的顶面;一个外壳直接或间接包住光阻层与电极,使微型led和电极的顶面露出外壳;以及,一层导电膜形成于外壳的表面,该导电膜内侧的一个电路布局面电连接微型led 与电极的顶面。
68.无论led组是由同色光的多颗发射微型led组成,或是分别发射红、绿、蓝光的三颗微型led组成,该外壳直接或间接包住led组的光阻层与电极,同样能让像素单元达到相同目的与功效。