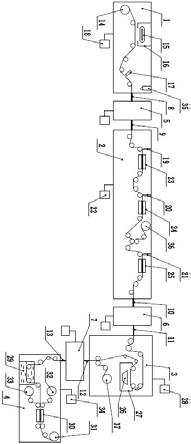
1.本发明属于新能源储能技术领域,特别是涉及一种柔性有机新能源电池组件的制备方法及其生产装备。
背景技术:2.近年来,随着可再生能源发电和电动汽车的快速发展,给新能源电池产业带来了新的发展机遇,新能源电池产业化技术及应用日益受到世界各国的重视。光伏、锂电等新能源电池由于受原材料成本、设备和产业技术成熟度等因素影响,导致电池成本居高不下,政府多采用税收优惠或补贴政策进行产业扶持,因此,新能源电池的产业化技术和装备已经成为制约其大规模推广应用的瓶颈。
3.有机新能源电池组件具有体量轻薄、原材料成本低、适合做成大面积柔性器件等优点,便于与柔性薄膜基底的卷对卷(r2r)大规模制造技术线相结合,可以显著降低有机新能源电池组件的成本,具有广阔的应用前景。
4.目前,有机新能源电池组件的各工序设备兼容性较差,产品需要在不同的设备里完成多道工序,柔性薄膜产品在设备之间流转过程中易于接触大气环境,使电池组件中的不同结构之间附着较多的水氧成分,这些水氧成分在电池组件产品中易于形成扩散,另外,现有的有机新能源电池组件的封装层的阻水阻氧性能差异较大,以上因素都会严重影响电池组件的性能稳定性和使用寿命。因此,有机新能源电池组件的卷对卷连续式生产装备、产业化技术瓶颈以及封装稳定性问题成为目前亟待解决的关键性问题。
技术实现要素:5.为解决上述问题,本发明提供一种柔性有机新能源电池组件的制备方法,主要包括涂层制备阶段和固化剪裁阶段;其中,涂层制备阶段是在一种多腔室连续式卷对卷镀膜设备上实施的;通过涂层制备阶段,实现在柔性基底上完成新能源电池功能单元各膜层的制备以及封装剂的填充制备。涂层制备阶段主要包括如下工序:(1)在多腔室连续式卷对卷设备的磁控溅射镀膜区域中,通过磁控溅射镀膜方法在柔性基底上沉积新能源电池功能单元中的ito层;(2)在多腔室连续式卷对卷设备的槽模涂布区域中,通过槽模涂布方法在ito层上依次沉积新能源电池功能单元中的电子传输层、有机活性层和空穴传输层;(3)在多腔室连续式卷对卷设备的蒸发镀膜区域中,通过蒸发镀膜方法在空穴传输层上沉积新能源电池功能单元中的金属电极层;(4)在多腔室连续式卷对卷设备的浸渍涂布区域中,通过浸渍涂布方法在柔性膜和新能源电池功能单元的外表面涂布封装剂,然后在涂布有封装剂的柔性膜下表面和新能源电池功能单元的上表面分别覆盖上保护膜和下保护膜;在多腔室连续式卷对卷设备的多个区域之间是连通式的,不设置封闭式阀门,在多腔室连续式卷对卷设备中实施涂层制备阶段过程中,柔性基底以卷对卷的形式在设备中
连续不停顿地传送走行。
6.所述的电子传输层为zno,厚度为20
‑
50nm;有机活性层的厚度为100
‑
300nm;空穴传输层为pedot
‑
pss,厚度为1
‑
5nm;金属电极层为ag,厚度为100
‑
300nm。pedot
‑
pss是指由pedot和pss两种物质构成的混合物,pedot是edot(3,4
‑
乙烯二氧噻吩单体)的聚合物,pss是聚苯乙烯磺酸盐。
7.电子传输层、有机活性层、空穴传输层中的每一层涂布完成后以及封装剂涂布完成并覆盖上保护膜和下保护膜后,还要经过干燥箱加热干燥。其中,槽模涂布区域的干燥箱加热温度为100~180℃,浸渍涂布区域中的干燥箱加热温度为150~200℃。
8.在ito层、有机活性层和金属电极层完成制备后分别还包括图案形成工序,图案形成的方法选自激光刻蚀、机械刻蚀和掩模遮挡中的至少一种。在本发明一种优选的实施方式中,在磁控溅射镀膜区域的末端设置有激光刻蚀装置,在槽模涂布区域内设置有机械刻蚀装置以及掩模压合机构,在蒸发镀膜区域内设置有掩模分离机构,掩模压合机构和掩模分离机构组成掩模遮挡装置,通过激光刻蚀装置、机械刻蚀装置以及掩模遮挡装置在不同阶段在膜层上形成图案。
9.在上述的工序(1)开始之前,还包括:将柔性基底置于放卷辊上,然后进行穿膜;穿膜完成后关闭生产设备两端的室门,开启真空机组,对生产设备整体进行抽真空,使生产设备各工作区域达到本底真空度;然后向磁控溅射镀膜区域充入氩气,向槽模涂布区域和浸渍涂布区域充入氮气或氩气,使各工作区域达到各自的工作压强和工作真空度。
10.为保证可实现不同的工艺要求,四个工作区域的工作压强(工作真空度)亦有差异。磁控溅射镀膜区域的工作真空度为1
×
10
‑
2 ‑ꢀ
1pa范围内,槽模涂布区域的工作压强为500
‑
5000pa范围内,蒸发镀膜区域的工作真空度为1
×
10
‑3‑ꢀ6×
10
‑1pa范围内,浸渍涂布区域的工作压强为1
×
104‑ꢀ
9.5
×
104pa;在磁控溅射镀膜区域和槽模涂布区域之间、槽模涂布区域和蒸发镀膜区域之间以及蒸发镀膜区域和浸渍涂布区域之间均分别设置有过渡腔室,过渡腔室的总数为3个以上;过渡腔室的两端均设置有超细狭缝,通过降低流导和气体捕集降低气体分子的通过几率,实现不同气体组分和不同压强的隔绝。
11.过渡腔室中设有压力传感器和真空抽气系统,压力传感器实时监控过渡腔室中的真空度,当过渡腔室中的真空度低于第1压力设定值时,则增大真空抽气系统中的蝶阀开度以提高过渡腔室中的真空度,当过渡腔室中的真空度高于第2压力设定值时,则降低蝶阀开度,同时通入一定量氩气,以维持过渡腔室内的真空度的稳定。
12.超细狭缝的内壁上排布有多个微腔,从压强较低侧至压强较高侧的方向上,微腔的排布数量密度逐渐增大。由于超细狭缝两侧存在一定压差,使气体分子存在从压强较高的一侧向压强较低的一侧流动的趋势,所以通过在超细狭缝壁排布有多个微腔,且压强较高侧数量密度大,实现对气体分子的捕集,进一步降低气体分子的通过几率。
13.超细狭缝的间隙b为需要通过的带有膜层的柔性基底厚度的1.5倍以上,且b至少为1毫米;超细狭缝在柔性基底走行方向上的长度l为1米以上;并且长度l与b3×△
p成正比,其中,
△
p为超细狭缝两侧的压强差。
14.本发明通过上述独特的过渡腔室
‑
超细狭缝这一动密封装置,使磁控溅射镀膜区域、槽模涂布区域、蒸发镀膜区域及浸渍涂布区域这4个工作压强差异巨大的工作区域实现互相连通,并且保持相互之间的工作压强和气氛的隔绝,使柔性基底可以在整个生产设备
中连续不断的走膜完成各膜层的制备。首先通过超细狭缝的长度l与间隙b的精密尺寸设计,使超细狭缝恰好在超细狭缝两侧的气体流态范畴内形成特定的流导条件,该流导条件使超细狭缝两侧在相互连通的情况下仍可保持稳定的工作压强跨度,该工作压强跨度可达103量级,另一方面,超细狭缝壁上微腔结构的设置可实现对气体分子的捕集,进一步降低气体分子的通过几率;同时,在两段超细狭缝之间还设置过渡腔室,过渡腔室通过压力传感器和可调的真空抽气系统的设置,可维持稳定的过渡真空度环境,起到中继站的作用。通过过渡腔室和超细狭缝互相配合的设置,可实现在该过渡腔室
‑
超细狭缝动密封装置两侧保持高达106‑
109量级的工作压强跨度,同时实现气氛的隔绝。
15.所述的封装剂为压敏胶粘剂,且压敏胶粘剂要将柔性基底和新能源电池单元的边缘四周均包裹在内。压敏胶粘剂中还包括聚丙烯酸甲酯和紫外固化胶粘剂;在固化剪裁阶段中,包括对柔性有机新能源电池组件进行紫外光照射固化封装的步骤;柔性基底和新能源电池单元边缘四周形成的密封结构以及阻水阻氧的上保护膜和下保护膜抑制氧和水分向柔性有机新能源电池组件内部扩散。
16.整个槽模涂布和浸渍涂布过程均在负压条件下进行,因此大大降低了膜层形成及封装过程中混入的水汽和氧气含量,提高了柔性有机新能源电池组件的产品质量、稳定性和寿命。
17.固化剪裁阶段在一种固化剪裁装置中进行。固化剪裁装置主要包括裁切腔室、卷绕传输系统、控制器、紫外光发射器、铡刀和承接机构;卷绕传输系统包括放卷辊、定位辊、支撑辊;控制器设置在支撑辊的上方,紫外光发射器设置在控制器上;铡刀设置在承接机构的上游,铡刀由气动装置驱动;裁切腔室还设置有传感器,用来监测柔性有机新能源电池组件的位置。
18.固化剪裁阶段是在常压环境下进行的,具体包括:传感器监测柔性有机新能源电池组件的传输位置,并将输出信号传输到控制器;控制器控制卷绕传输系统以10~20个单元为一组的方式间歇性传输柔性有机新能源电池组件,并控制紫外光发射器在对应位置对柔性有机新能源电池组件进行照射固化封装。紫外光照射固化封装的同时,铡刀会下落对柔性有机新能源电池组件进行裁切,只在柔性有机新能源电池组件边缘留下衔接段,确保传输的持续。切断的柔性有机新能源电池组件落在承接机构上。该固化剪裁装置的照射固化封装与裁切同步进行,提升了生产效率。
19.本发明还涉及一种制备柔性有机新能源电池组件的生产设备,用于上述的柔性有机新能源电池组件的制备方法中的涂层制备阶段,即在柔性基底上连续完成新能源电池功能单元各膜层的制备以及封装剂的填充制备。
20.该设备为一种多腔室连续式卷对卷镀膜设备,主要包括:磁控溅射镀膜区域、槽模涂布区域、蒸发镀膜区域、浸渍涂布区域;其中,磁控溅射镀膜区域的工作真空度为1
×
10
‑
2 ‑ꢀ
1pa范围内,槽模涂布区域的工作压强为500
‑
5000pa范围内,蒸发镀膜区域的工作真空度为1
×
10
‑3‑ꢀ6×
10
‑1pa范围内,浸渍涂布区域的工作压强为1
×
104‑ꢀ
9.5
×
104pa;各区域之间是连通式的,不设置封闭式阀门,在该设备工作过程中,柔性基底以卷对卷的形式在设备中连续不停顿地传送走行。
21.由于磁控溅射镀膜区域、槽模涂布区域、蒸发镀膜区域及浸渍涂布区域的工作压强(工作真空度)存在很大差异,在现有技术里是无法实现在同一设备里兼容并互相连通
的。本发明通过独特的过渡腔室
‑
超细狭缝这一动密封装置解决了这一技术问题。
22.本发明在磁控溅射镀膜区域和槽模涂布区域之间、槽模涂布区域和蒸发镀膜区域之间以及蒸发镀膜区域和浸渍涂布区域之间均分别设置有过渡腔室;过渡腔室的总数为3个以上。在过渡腔室中设有压力传感器和真空抽气系统,压力传感器实时监控过渡腔室中的真空度,当过渡腔室中的真空度低于第1压力设定值时,则增大真空抽气系统中的蝶阀开度以提高过渡腔室中的真空度,当过渡腔室中的真空度高于第2压力设定值时,则降低蝶阀开度,同时通入一定量氩气,以维持过渡腔室内的真空度的稳定;第1压力设定值的数值高于第2压力设定值的数值。
23.同时,过渡腔室的两端均设置有超细狭缝,通过降低流导和气体捕集降低气体分子的通过几率,实现不同气体组分和不同压强的隔绝;超细狭缝的内壁上排布有多个微腔,从压强较低侧至压强较高侧的方向上,微腔的排布数量密度逐渐增大。超细狭缝的间隙b为需要通过的带有膜层的柔性基底厚度的1.5倍以上,且b至少为1毫米;超细狭缝在柔性基底走行方向上的长度l为1米以上;并且长度l与b3×△
p成正比,其中,
△
p为超细狭缝两侧的压强差。
24.以上的过渡腔室
‑
超细狭缝动密封装置技术方案,首先通过超细狭缝的长度l与间隙b的精密尺寸设计,使超细狭缝恰好在超细狭缝两侧的气体流态范畴内形成特定的流导条件,该流导条件使超细狭缝两侧在相互连通的情况下仍可保持稳定的工作压强跨度,该工作压强跨度可达103量级,另一方面,超细狭缝壁上微腔结构的设置可实现对气体分子的捕集,进一步降低气体分子的通过几率;同时,在两段超细狭缝之间还设置过渡腔室,过渡腔室通过压力传感器和可调的真空抽气系统的设置,可维持稳定的过渡真空度环境,起到中继站的作用。通过过渡腔室和超细狭缝互相配合的设置,可实现在该过渡腔室
‑
超细狭缝动密封装置两侧保持高达106‑
109量级工作压强跨度,同时实现气氛的隔绝。由此,可使磁控溅射镀膜区域、槽模涂布区域、蒸发镀膜区域及浸渍涂布区域这4个工作压强差异巨大的工作区域实现互相连通,并且保持相互之间的工作压强和气氛的隔绝,使柔性基底可以在整个生产设备中连续不断的走膜完成各膜层的制备。
25.在磁控溅射镀膜区域中,设置有放卷辊、磁控溅射靶、溅射挡板、膜厚检测器、磁控溅射真空系统;该区域主要通过磁控溅射镀膜方法在柔性基底上沉积新能源电池功能单元中的ito层。
26.在槽模涂布区域中,设置有槽模、干燥箱、槽模真空系统;槽模和干燥箱的数量均为3个,分别完成新能源电池功能单元中的电子传输层、有机活性层和空穴传输层的槽模涂布制备;槽模涂布过后需要用干燥箱干燥,干燥箱的加热温度为100
‑
200℃。
27.在蒸发镀膜区域中,设置有蒸发源、蒸发挡板、蒸发真空系统;该区域主要通过蒸发镀膜方法在空穴传输层上沉积新能源电池功能单元中的金属电极层。
28.在浸渍涂布区域中,设置有浸渍涂布槽、干燥箱、收卷辊、保护膜压印装置及浸渍涂布真空系统;该区域主要通过浸渍涂布方法在柔性膜和新能源电池功能单元的外表面涂布封装剂,然后在涂布有封装剂的柔性膜下表面和新能源电池功能单元的上表面分别覆盖上保护膜和下保护膜。
29.各区域和各过渡腔室中均设置有导向辊和张力调节辊。各区域中根据需要还设置有固定辊。
30.在磁控溅射镀膜区域、槽模涂布区域和蒸发镀膜区域中还分别设置有图案形成装置,图案形成装置为选自激光刻蚀装置、机械刻蚀装置和掩模遮挡装置中的至少一种。
31.在本发明一种优选的实施方式中,在磁控溅射镀膜区域的末端设置有激光刻蚀装置,在槽模涂布区域内设置有机械刻蚀装置以及掩模压合机构,在蒸发镀膜区域内设置有掩模分离机构,掩模压合机构和掩模分离机构组成掩模遮挡装置,通过激光刻蚀装置、机械刻蚀装置以及掩模遮挡装置在不同阶段在膜层上形成图案。
32.上述柔性有机新能源电池组件的生产设备的大致工作过程为:将柔性基底置于放卷辊上,然后进行穿膜;穿膜完成后关闭生产设备两端的室门,开启真空机组,对生产设备整体进行抽真空,使生产设备各工作区域达到本底真空度;然后向磁控溅射镀膜区域充入氩气,向槽模涂布区域和浸渍涂布区域充入氮气或氩气,使各工作区域达到各自的工作压强(工作真空度);开启磁控溅射靶、蒸发源、槽模、干燥箱、保护膜压印装置、掩模遮挡装置、激光刻蚀装置以及机械刻蚀装置等各工作区域中的工作装置,同时开启各辊使柔性基底走膜,使柔性基底依次通过磁控溅射镀膜区域、槽模涂布区域、蒸发镀膜区域及浸渍涂布区域,在柔性基底上制备ito层、电子传输层、有机活性层、空穴传输层及金属电极层,并涂布封装剂、覆盖上下保护膜。在不同阶段,还要通过激光刻蚀装置、机械刻蚀装置和掩模遮挡装置在膜层上形成图案。
33.本发明还涉及一种采用上述制备方法制造的柔性有机新能源电池组件,该柔性有机新能源电池组件适于采用卷对卷制备技术大规模生产。该柔性有机新能源电池组件主要包括柔性基底、有机新能源电池功能单元和保护膜;有机新能源电池功能单元位于柔性基底的上表面,在有机新能源电池功能单元的上表面覆盖有上保护膜,在柔性基底的下表面覆盖有下保护膜。有机新能源电池功能单元从柔性基底自下而上依次包括ito层、电子传输层、有机活性层、空穴传输层、金属电极层。
34.所述的电子传输层为zno,厚度为20
‑
50nm;有机活性层的厚度为100
‑
300nm;空穴传输层为pedot
‑
pss,厚度为1
‑
5nm;金属电极层为ag,厚度为100
‑
300nm。pedot
‑
pss是指由pedot和pss两种物质构成的混合物,pedot是edot(3,4
‑
乙烯二氧噻吩单体)的聚合物,pss是聚苯乙烯磺酸盐。
35.上保护膜和下保护膜的覆盖面积要超出柔性基底和有机新能源电池功能单元的边缘,在上保护膜和有机新能源电池功能单元之间、下保护膜和柔性基底之间以及上保护膜和下保护膜之间均填充有压敏胶粘剂,且压敏胶粘剂要将柔性基底和有机新能源电池单元的边缘四周均包裹在内。压敏胶粘剂中还包括聚丙烯酸甲酯和紫外固化胶粘剂,将聚丙烯酸甲酯和紫外固化胶粘剂加入到压敏胶粘剂中,能够抑制水分和氧气的横向扩散,对柔性有机新能源电池组件的封装具有优越性,与普通压敏胶粘剂相比具有显著的水氧渗透阻隔密封效果,所生产的柔性有机新能源电池组件有更高的稳定性和寿命。
36.柔性基底的材质由选自pet、pi、pp、pvc、ptfe中的一种构成,它们在较宽的温度范围内具有优良的物理机械性能,在高温高频下,电学性能良好,耐疲劳性和尺寸稳定性也很好,这为保证柔性有机新能源电池组件的质量提供了良好的基础;上保护膜和下保护膜的材质具有阻水阻氧性能,这为边缘密封提供了屏障,用以抑制氧和水分的横向扩散。
37.本发明的有益效果:1.通过独特的过渡腔室
‑
超细狭缝这一动密封装置,实现在该过渡腔室
‑
超细狭缝
动密封装置两侧保持高达106‑
109量级的工作压强跨度,同时实现气氛的隔绝,使磁控溅射镀膜区域、槽模涂布区域、蒸发镀膜区域及浸渍涂布区域这4个工作压强差异巨大的工作区域实现互相连通。
38.2. 该生产设备和制备方法使柔性基底在整个生产设备中连续不断的走膜完成各膜层的制备及封装。柔性有机新能源电池组件的整个膜层制备以及封装剂填充过程均在同一生产设备中隔绝大气完成,避免了产品在不同设备之间流转过程中接触大气环境,杜绝了电池组件中的不同结构层之间附着较多的水氧成分,极大提升了电池组件的产品稳定性和使用寿命。
39.3. 在封装过程中,将聚丙烯酸甲酯和紫外固化胶粘剂加入到压敏胶粘剂中,与普通压敏胶粘剂相比具有显著的水氧密封效果,在产品使用过程中能够抑制水分和氧气的横向扩散,使柔性有机新能源电池组件有更高的稳定性和使用寿命。
40.4. 整个涂布和封装过程均在负压条件下进行,因此大大降低了薄膜封装过程中混入的水汽和氧气含量,提高了有机新能源电池组件的产品质量和寿命。
附图说明
41.图1是本发明所涉及的制备柔性有机新能源电池组件生产设备的一种实施方式的示意图。
42.图2是本发明所涉及的柔性有机新能源电池组件的固化裁切装置的示意图。
43.图3是本发明所涉及的柔性有机新能源电池组件中一个单元的一种实施方式的结构示意图。
44.图4是本发明所涉及的过渡腔室
‑
超细狭缝动密封装置的结构示意图。
45.图5是本发明所涉及的超细狭缝的结构示意图。
46.所附附图并非按照比例绘制,旨在展示本发明的基本原理和基本结构,附图中的各结构特征和部件均采用了简化的画法。本发明技术方案所覆盖的实施方式也不限于所附附图所举实施方式和实施例。
具体实施方式
47.下面结合附图进一步说明本发明的实施方式。
48.图1是本发明所采用的制备柔性有机新能源电池组件的生产设备的一种实施方式的示意图,用于本发明的柔性有机新能源电池组件的制备方法中的涂层制备阶段,即在柔性基底上连续完成新能源电池功能单元各膜层的制备以及封装剂的填充制备。该设备为多腔室的连续式卷对卷形式,主要包括:磁控溅射镀膜区域1、槽模涂布区域2、蒸发镀膜区域3、浸渍涂布区域4; 在本实施例中,磁控溅射镀膜区域1的工作真空度约为3
×
10
‑2,槽模涂布区域2的工作压强约为1000pa,蒸发镀膜区域的工作真空度约为6
×
10
‑3,浸渍涂布区域的工作压强约为3
×
104pa。各区域之间是连通式的,不设置封闭式阀门,在该设备工作过程中,柔性基底以卷对卷的形式在设备中连续不停顿地传送走行。
49.在磁控溅射镀膜区域1和槽模涂布区域2之间设置有过渡腔室5,槽模涂布区域2和蒸发镀膜区域3之间设置有过渡腔室6,蒸发镀膜区域3和浸渍涂布区域4之间设置有过渡腔室7。在过渡腔室5两端分别设置有超细狭缝8、9,在过渡腔室6两端分别设置有超细狭缝10、
11,在过渡腔室7两端分别设置有超细狭缝12、13。
50.在磁控溅射镀膜区域1中,设置有放卷辊14、磁控溅射靶15、溅射挡板16、膜厚检测器17、磁控溅射真空系统18;该工作区域主要通过磁控溅射镀膜方法在柔性基底上沉积新能源电池功能单元中的ito层。
51.在槽模涂布区域2中,设置有槽模、干燥箱、槽模真空系统22;槽模和干燥箱的数量均为3个,分别为槽模19、20、21,以及干燥箱23、24、25。其中,槽模19完成新能源电池功能单元中的电子传输层的槽模涂布,槽模20完成有机活性层的槽模涂布,槽模21完成空穴传输层的槽模涂布;槽模涂布过后需要用干燥箱干燥,干燥箱的加热温度为100
‑
200℃。
52.在蒸发镀膜区域3中,设置有蒸发源26、蒸发挡板27、蒸发真空系统28;该区域主要通过蒸发镀膜方法在空穴传输层上沉积新能源电池功能单元中的金属电极层。
53.在浸渍涂布区域4中,设置有浸渍涂布槽29、干燥箱30、收卷辊31、上保护膜压印装置32、下保护膜压印装置33及浸渍涂布真空系统34;该区域主要通过浸渍涂布方法在柔性膜和新能源电池功能单元的外表面涂布封装剂,然后在涂布有封装剂的柔性膜下表面和新能源电池功能单元的上表面分别覆盖上保护膜和下保护膜。
54.各区域和各过渡腔室中根据需要还设置有固定辊、导向辊和张力调节辊。
55.在磁控溅射镀膜区域、槽模涂布区域和蒸发镀膜区域中还分别设置有图案形成装置,图案形成装置为选自激光刻蚀装置、机械刻蚀装置和掩模遮挡装置中的至少一种。
56.在本实施方式中,在磁控溅射镀膜区域的末端设置有激光刻蚀装置35,在槽模涂布区域2内设置有机械刻蚀装置以及掩模压合机构36,在蒸发镀膜区域3内设置有掩模分离机构37,掩模压合机构36和掩模分离机构37组成掩模遮挡装置,通过激光刻蚀装置、机械刻蚀装置以及掩模遮挡装置在不同阶段在膜层上形成图案。
57.下面以过渡腔室5为例,结合图4进一步说明本发明的过渡腔室
‑
超细狭缝动密封装置的构成。如图4所示,过渡腔室5的两侧为超细狭缝8和超细狭缝9,由超细狭缝8、9和过渡腔室5组成了磁控溅射镀膜区域1和槽模涂布区域2之间的过渡腔室
‑
超细狭缝动密封装置。在过渡腔室5中设置有压力传感器38和真空抽气系统39,压力传感器38实时监控过渡腔室5中的真空度,当过渡腔室5中的真空度低于第1压力设定值时,则增大真空抽气系统39中的蝶阀开度以提高过渡腔室5中的真空度,当过渡腔室5中的真空度高于第2压力设定值时,则降低蝶阀开度,同时通入一定量氩气,以维持过渡腔室5内的真空度的稳定;第1压力设定值的数值高于第2压力设定值的数值。过渡腔室5的两端均设置有超细狭缝,通过降低流导和气体捕集降低气体分子的通过几率,实现不同气体组分和不同压强的隔绝。
58.以超细狭缝8为例,图5是本发明中超细狭缝的结构示意图。超细狭缝8的壁上排布有多个微腔40,从压强较低的磁控溅射镀膜区域1侧至压强较高的过渡腔室5侧的方向上,微腔的排布数量密度逐渐增大。超细狭缝的间隙b为需要通过的带有膜层的柔性基底厚度的1.5倍以上,且b至少为1毫米;超细狭缝在柔性基底走行方向上的长度l为1米以上;并且长度l与b3×△
p成正比,其中,
△
p为超细狭缝两侧的压强差。
59.上述柔性有机新能源电池组件的生产设备的大致工作过程为:首先,将柔性基底置于放卷辊上,然后进行穿膜;穿膜完成后关闭生产设备两端的室门,开启真空系统,对生产设备整体进行抽真空,使生产设备各工作区域达到本底真空度;然后向磁控溅射镀膜区域充入氩气,向槽模涂布区域和浸渍涂布区域充入氮气或氩气,使各工作区域达到各自的
工作压强(工作真空度);开启磁控溅射靶、蒸发源、槽模、干燥箱、保护膜压印装置、掩模遮挡装置、激光刻蚀装置以及机械刻蚀装置等各工作区域中的工作装置,同时开启各辊使柔性基底走膜,使柔性基底依次通过磁控溅射镀膜区域、槽模涂布区域、蒸发镀膜区域及浸渍涂布区域,在柔性基底上制备ito层、电子传输层、有机活性层、空穴传输层及金属电极层,并涂布封装剂、覆盖上下保护膜。在不同阶段,还要通过激光刻蚀装置、机械刻蚀装置和掩模遮挡装置在膜层上形成图案。
60.本发明中的一种柔性有机新能源电池组件的制备方法,主要包括涂层制备阶段和固化剪裁阶段;其中,涂层制备阶段是在上述的多腔室连续式卷对卷镀膜设备上实施的;通过涂层制备阶段,实现在柔性基底上完成新能源电池功能单元各膜层的制备以及封装剂的填充制备。涂层制备阶段主要包括如下工序:(1)在多腔室连续式卷对卷设备的磁控溅射镀膜区域1中,通过磁控溅射镀膜方法在柔性基底上沉积新能源电池功能单元中的ito层;(2)在多腔室连续式卷对卷设备的槽模涂布区域2中,通过槽模涂布方法在ito层上依次沉积新能源电池功能单元中的电子传输层、有机活性层和空穴传输层;(3)在多腔室连续式卷对卷设备的蒸发镀膜区域3中,通过蒸发镀膜方法在空穴传输层上沉积新能源电池功能单元中的金属电极层;(4)在多腔室连续式卷对卷设备的浸渍涂布区域4中,通过浸渍涂布方法在柔性膜和新能源电池功能单元的外表面涂布封装剂,然后在涂布有封装剂的柔性膜下表面和新能源电池功能单元的上表面分别覆盖上保护膜和下保护膜;在多腔室连续式卷对卷设备的多个区域之间是连通式的,不设置封闭式阀门,在多腔室连续式卷对卷设备中实施涂层制备阶段过程中,柔性基底以卷对卷的形式在设备中连续不停顿地传送走行。
61.所述的电子传输层为zno,厚度为20
‑
50nm;有机活性层的厚度为100
‑
300nm;空穴传输层为pedot
‑
pss,厚度为1
‑
5nm;金属电极层为ag,厚度为100
‑
300nm。pedot
‑
pss是指由pedot和pss两种物质构成的混合物,pedot是edot(3,4
‑
乙烯二氧噻吩单体)的聚合物,pss是聚苯乙烯磺酸盐。
62.电子传输层、有机活性层、空穴传输层中的每一层涂布完成后以及封装剂涂布完成并覆盖上保护膜和下保护膜后,还要经过干燥箱加热干燥。其中,槽模涂布区域的干燥箱加热温度为100~180℃,浸渍涂布区域中的干燥箱加热温度为150~200℃。
63.在ito层、有机活性层和金属电极层完成制备后分别还包括图案形成工序,图案形成的方法选自激光刻蚀、机械刻蚀和掩模遮挡中的至少一种。在本实施方式中,在磁控溅射镀膜区域的末端设置有激光刻蚀装置35,在槽模涂布区域2内设置有机械刻蚀装置以及掩模压合机构36,在蒸发镀膜区域3内设置有掩模分离机构37,掩模压合机构36和掩模分离机构37组成掩模遮挡装置,通过激光刻蚀装置、机械刻蚀装置以及掩模遮挡装置在不同阶段在膜层上形成图案。
64.为保证可实现不同的工艺要求,四个工作区域的工作压强(工作真空度)亦有差异。磁控溅射镀膜区域的工作真空度为1
×
10
‑
2 ‑ꢀ
1pa范围内,槽模涂布区域的工作压强为500
‑
5000pa范围内,蒸发镀膜区域的工作真空度为1
×
10
‑3‑ꢀ6×
10
‑1pa范围内,浸渍涂布区域的工作压强为1
×
104‑ꢀ
9.5
×
104pa;在磁控溅射镀膜区域和槽模涂布区域之间、槽模涂布
区域和蒸发镀膜区域之间以及蒸发镀膜区域和浸渍涂布区域之间均分别设置有过渡腔室,过渡腔室的总数为3个以上;过渡腔室的两端均设置有超细狭缝,通过降低流导和气体捕集降低气体分子的通过几率,实现不同气体组分和不同压强的隔绝。
65.过渡腔室中设有压力传感器和真空抽气系统,压力传感器实时监控过渡腔室中的真空度,当过渡腔室中的真空度低于第1压力设定值时,则增大真空抽气系统中的蝶阀开度以提高过渡腔室中的真空度,当过渡腔室中的真空度高于第2压力设定值时,则降低蝶阀开度,同时通入一定量氩气,以维持过渡腔室内的真空度的稳定。
66.超细狭缝的壁上排布有多个微腔,从压强较低侧至压强较高侧的方向上,微腔的排布数量密度逐渐增大。由于超细狭缝两侧存在一定压差,使气体分子存在从压强较高的一侧向压强较低的一侧流动的趋势,所以通过在超细狭缝壁排布有多个微腔,且压强较高侧数量密度大,实现对气体分子的捕集,进一步降低气体分子的通过几率。
67.所述的封装剂为压敏胶粘剂,且压敏胶粘剂要将柔性基底和新能源电池单元的边缘四周均包裹在内。压敏胶粘剂中还包括聚丙烯酸甲酯和紫外固化胶粘剂;在固化剪裁阶段中,包括对柔性有机新能源电池组件进行紫外光照射固化封装的步骤;柔性基底和新能源电池单元边缘四周形成的密封结构以及阻水阻氧的上保护膜和下保护膜抑制氧和水分向柔性有机新能源电池组件内部扩散。
68.整个槽模涂布和浸渍涂布过程均在负压条件下进行,因此大大降低了膜层形成及封装过程中混入的水汽和氧气含量,提高了柔性有机新能源电池组件的产品质量、稳定性和寿命。
69.本发明的制备方法中的固化剪裁阶段是在一种固化剪裁装置中进行的,图2是该固化裁切装置的示意图。固化剪裁装置主要包括裁切腔室41、卷绕传输系统、控制器42、紫外光发射器43、铡刀44和承接机构45;卷绕传输系统包括放卷辊46、定位辊47、支撑辊48;控制器42设置在支撑辊48的上方,紫外光发射器43设置在控制器42上;铡刀44设置在承接机构45的上游,铡刀44由气动装置49驱动;裁切腔室还设置有传感器,用来监测柔性有机新能源电池组件的位置。
70.固化剪裁阶段是在常压环境下进行的,具体包括:传感器监测柔性有机新能源电池组件的传输位置,并将输出信号传输到控制器;控制器控制卷绕传输系统以10~20个单元为一组的方式间歇性传输柔性有机新能源电池组件,并控制紫外光发射器在对应位置对柔性有机新能源电池组件进行照射固化封装。紫外光照射固化封装的同时,铡刀会下落对柔性有机新能源电池组件进行裁切,只在柔性有机新能源电池组件边缘留下衔接段,确保传输的持续。切断的柔性有机新能源电池组件落在承接机构上。该固化剪裁装置的照射固化封装与裁切同步进行,提升了生产效率。
71.本发明还涉及一种采用本发明的制备方法制造的柔性有机新能源电池组件,该柔性有机新能源电池组件适于采用卷对卷制备技术大规模生产。图3是本发明柔性有机新能源电池组件中一个单元的一种实施方式的结构示意图。该柔性有机新能源电池组件单元主要包括柔性基底50、有机新能源电池功能单元和保护膜;有机新能源电池功能单元位于柔性基底50的上表面,在有机新能源电池功能单元的上表面覆盖有上保护膜51,在柔性基底的下表面覆盖有下保护膜52。有机新能源电池功能单元从柔性基底自下而上依次包括ito层53、电子传输层54、有机活性层55、空穴传输层56、金属电极层57。
72.所述的电子传输层54为zno,厚度为20
‑
50nm;有机活性层55的厚度为100
‑
300nm;空穴传输层56为pedot
‑
pss,厚度为1
‑
5nm;金属电极层57为ag,厚度为100
‑
300nm。pedot
‑
pss是指由pedot和pss两种物质构成的混合物,pedot是edot(3,4
‑
乙烯二氧噻吩单体)的聚合物,pss是聚苯乙烯磺酸盐。
73.上保护膜51和下保护膜52的覆盖面积要超出柔性基底和有机新能源电池功能单元的边缘,在上保护膜和有机新能源电池功能单元之间、下保护膜和柔性基底之间以及上保护膜和下保护膜之间均填充有压敏胶粘剂58,且压敏胶粘剂58要将柔性基底和有机新能源电池单元的边缘四周均包裹在内。压敏胶粘剂中还包括聚丙烯酸甲酯和紫外固化胶粘剂,将聚丙烯酸甲酯和紫外固化胶粘剂加入到压敏胶粘剂中,能够抑制水分和氧气的横向扩散,对柔性有机新能源电池组件的封装具有优越性,与普通压敏胶粘剂相比具有显著的水氧渗透阻隔密封效果,所生产的柔性有机新能源电池组件有更高的稳定性和寿命。
74.柔性基底50的材质由选自pet、pi、pp、pvc、ptfe中的一种构成,它们在较宽的温度范围内具有优良的物理机械性能,在高温高频下,电学性能良好,耐疲劳性和尺寸稳定性也很好,这为保证柔性有机新能源电池组件的质量提供了良好的基础;上保护膜和下保护膜的材质具有阻水阻氧性能,这为边缘密封提供了屏障,用以抑制氧和水分的横向扩散。
75.下面通过实施例进一步说明本发明的显著效果。
76.实施例1采用本发明中的柔性有机新能源电池组件的制备方法制备出柔性有机新能源电池组件1,柔性有机新能源电池组件1的整个膜层制备以及封装剂填充过程均在本发明的多腔室连续式卷对卷设备上隔绝大气实施完成,避免了产品在不同设备之间流转过程中接触大气环境,杜绝了电池组件中的不同结构层之间附着较多的水氧成分,同时在采用压敏胶粘剂中加入聚丙烯酸甲酯和紫外固化胶粘剂进行填充封装。
77.实施例2采用本发明中的柔性有机新能源电池组件的制备方法制备出柔性有机新能源电池组件2,柔性有机新能源电池组件2的整个膜层制备以及封装剂填充过程均在本发明的多腔室连续式卷对卷设备上隔绝大气实施完成,避免了产品在不同设备之间流转过程中接触大气环境,杜绝了电池组件中的不同结构层之间附着较多的水氧成分。柔性有机新能源电池组件2采用与柔性有机新能源电池组件1相同的膜层结构和成分,不同的是采用普通的压敏胶粘剂进行填充封装,即未在压敏胶粘剂加入聚丙烯酸甲酯和紫外固化胶粘剂。
78.对比例1采用普通的生产设备上完成柔性有机新能源电池组件的膜层制备以及封装剂填充,即采用单独的卷对卷磁控溅射镀膜机进行ito层的制备,然后在单独的卷对卷槽模涂布机上完成电子传输层、有机活性层和空穴传输层的制备,然后在单独的卷对卷蒸发镀膜机上完成金属电极层的制备,然后在卷对卷浸渍涂布机上进行压敏胶粘剂的填充封装;产品在上述不同设备间流转时是在大气环境中进行的,由此制成柔性有机新能源电池组件3。柔性有机新能源电池组件3采用与柔性有机新能源电池组件1相同的膜层结构和成分,并同样在压敏胶粘剂中加入聚丙烯酸甲酯和紫外固化胶粘剂进行填充封装。
79.对比例2采用普通的生产设备上完成柔性有机新能源电池组件的膜层制备以及封装剂填
充,即采用单独的卷对卷磁控溅射镀膜机进行ito层的制备,然后在单独的卷对卷槽模涂布机上完成电子传输层、有机活性层和空穴传输层的制备,然后在单独的卷对卷蒸发镀膜机上完成金属电极层的制备,然后在卷对卷浸渍涂布机上进行压敏胶粘剂的填充封装;产品在上述不同设备间流转时是在大气环境中进行的,由此制成柔性有机新能源电池组件4。柔性有机新能源电池组件4采用与柔性有机新能源电池组件1相同的膜层结构和成分,但采用了普通的压敏胶粘剂进行填充封装,即未在压敏胶粘剂加入聚丙烯酸甲酯和紫外固化胶粘剂。
80.对柔性有机新能源电池组件1至4进行加速试验,并通过tem观察其水氧扩散层,以扩散层厚度为指标来评价柔性有机新能源电池组件的质量稳定性及使用寿命。
81.结果显示,实施例1的扩散层厚度约为8nm,实施例2的扩散层厚度约为18nm;对比例1和对比例2扩散层厚度分别约为80nm和146nm。从测试结果中可以看出,实施例1采用本发明的生产设备和制备方法,制造过程是在多腔室连续式卷对卷设备上隔绝大气实施完成的,避免了产品在不同设备之间流转过程中接触大气环境,杜绝了电池组件中的不同结构层之间附着较多的水氧成分,同时在采用压敏胶粘剂中加入聚丙烯酸甲酯和紫外固化胶粘剂进行填充封装,所以加速试验性能最为优异,扩散层厚度仅为对比例1的1/10,约为对比例2的1/18。而实施例2虽然只采用普通的压敏胶粘剂进行填充封装,即未在压敏胶粘剂加入聚丙烯酸甲酯和紫外固化胶粘剂,但因为其制造过程是在本发明的多腔室连续式卷对卷设备上隔绝大气实施完成的,避免了产品在不同设备之间流转过程中接触大气环境,杜绝了电池组件中的不同结构层之间附着较多的水氧成分,所以加速试验性能也比较突出,扩散层厚度约为对比例1的1/5,约为对比例2的1/8。由此可见本发明的制备方法和生产设备突出的技术效果。