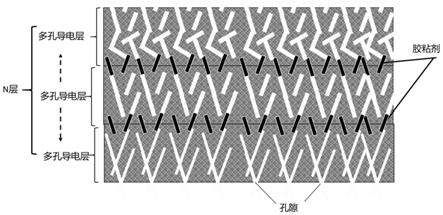
1.材料和电池技术领域,具体涉及一种粘合导电板及其制备方法。
背景技术:2.具有高电导率、低电阻和高抗弯强度的导电薄板在很多领域有着广泛的应用和技术研发的需求。例如,燃料电池中的双极板、液流电池中的双极板、电解槽的双极板等。以燃料电池为例,双极板是其中的关键部件,很大程度上决定了燃料电池的体积、重量、成本。开发具有高电导率、低电阻、高机械强度且具有大规模量产能力的双极板技术对燃料电池的发展有着重要作用。现有的各种燃料电池双极板比如金属板、石墨板、石墨复合板等均在性能、寿命或者生产效率等方面存在着瓶颈问题。
3.导电薄板的电导率和机械强度的相互制约的问题是本领域研究人员一直想解决的技术难题。传统技术中,提高电导率可以降低电阻,但是往往机械强度得不到保证;提高机械强度则电导率无法满足要求。为了解决现有复合板存在的问题,工程技术人员和研究人员对此进行了较多的改进。对现有文献进行检索,发现专利申请号为201210552504.5的中国专利介绍了一种聚合物
‑
碳材料复合导电板,其方法是将聚合物树脂和碳毡或者石墨毡通过热压的方法使得聚合物树脂进入碳毡或者石墨毡的孔隙,制备致密的树脂复合双极板。专利申请号为201410401746.3的中国专利介绍了一种酚醛树脂
‑
石墨
‑
石墨烯复合电池双极板栅板,其方法是将一定比列的酚醛树脂、石墨和石墨烯混合,通过模压的方法制备得到复合双极板。申请号为201410021214.7的中国专利公布了一中用于燃料电池的导电板,包含了上下表层导电层和中间的单元预制体。所述单元预制体为嵌有导电颗粒的聚合物薄膜,利用导电颗粒形成厚度方向的导电通路。申请号为201911178266.4的中国专利公布了一种导电板的制造方法,具体是两层柔性石墨之间填充金属层或者非金属夹层,然后通过浸胶、表面除胶等工艺制备燃料电池双极板。申请号为201710127266.6的中国专利公开了一种两侧带有液流电池电极的一体化电极的制备方法,具体是首先将热塑性树脂置于两层多孔导电材料之间,热压得到复合导电板,然后在复合导电板的两边通过加热粘结碳毡或者石墨毡得到一体化电极。申请号为201610819533.1的中国专利公开了一种导电板,具体是在两层柔性石墨之间加入导电骨架,导电骨架表面用添加导电填料的热熔性涂层包覆,将柔性石墨层和增强骨架放入模具进行压制。申请号为201811348912.2的中国专利公开了一种燃料电池双极板的制备方法,具体是在上下表层之间加入中间层和过度层,表层、中间层和过度层均由粘结剂、导电材料和增强材料组成,通过改变树脂含量得到不同的层,最后通过冷压、热压制得导电板。
4.以上技术制备的复合导电板并没有有效解决电导率和机械强度相互制约的问题,即使一定程度上缓解了两者矛盾,但是存在制备过程生产工艺复杂,对设备要求高,生产周期长等问题。
技术实现要素:5.针对现有技术中的缺陷,本发明的目的是提供一种粘合导电板及其制备方法,所得导电板弯曲强度高,厚度方向电导率高,加工工艺比较简单,容易实现工业化的快速批量生产,在燃料电池和液流电池等新能源技术中具有较好的应用前景,以切实解决工业化进程中的瓶颈问题。
6.本发明的目的是通过以下方案实现的:
7.本发明的第一方面提供一种粘合导电板,包括n层上下叠加的多孔导电层,所述多孔导电层的表面设有孔隙,相邻的多孔导电层之间通过胶粘剂粘合,所述胶粘剂填充于所述孔隙中,使相邻的多孔导电层粘合在一起从而形成粘合导电板,其中,n为大于等于2的整数,所述多孔导电层的表面的孔隙面积占比小于等于30%,所述多孔导电层的电导率大于等于150s/cm。
8.优选的,所述多孔导电层的两个表面均设有孔隙。
9.在一些实施例中,多孔导电层的表面设有孔隙,同时内部也可以设有孔隙。
10.在另一些实施例中,当n大于等于3时,位于最上层和最下层的多孔导电层可以只有一个表面设有孔隙,位于中间的多孔导电层两个表面均设有孔隙。
11.优选的,所述多孔导电层为多孔导电碳板或多孔金属板。
12.优选的,所述胶粘剂为热固性胶粘剂和/或热塑性胶粘剂。
13.优选的,所述热塑性胶粘剂包括聚偏氟乙烯树脂、聚乙烯、聚丙烯、聚酰亚胺、聚醚砜、聚醚醚酮、聚氯乙烯、聚偏氟乙烯
‑
六氟丙烯树脂、丙烯酸树脂中的至少一种,所述热固性胶粘剂包括环氧树脂、不饱和聚酯树脂(例如乙烯基酯树脂(vinyl ester resins))、酚醛树脂中的至少一种。更优选的,所述胶粘剂为环氧树脂、乙烯基酯树脂中的一种或者其组合。
14.优选的,所述多孔导电层的厚度范围为0.01mm~1.0mm。更优选的,所述多孔导电层的厚度范围为0.01mm~0.2mm。
15.优选的,所述多孔导电层表面孔隙的孔隙率为5%~70%。
16.优选的,所述多孔导电层表面孔隙的孔隙率为12%~62%。
17.优选的,所述多孔导电层的电导率大于等于200s/cm,更优选的,所述多孔导电层的电导率大于等于400s/cm,电导率越大越好,例如可以达到1
×
106s/cm。
18.优选的,所述多孔导电层表面上的单个孔隙平均面积小于等于0.25平方毫米,更优选的,孔隙的平均面积小于等于0.01平方毫米,最优选的,小于等于0.0025平方毫米,甚至可以小至0.6
×
10
‑
10
平方毫米。
19.优选的,所述多孔导电层的表面的孔隙面积占比为0.01%~10%。更优选的,所述多孔导电层的表面的孔隙面积占比为1%~10%。
20.优选的,所述多孔导电层的层数大于等于5层,更优选的,所述多孔导电层的层数为10~100层。
21.本发明的第二方面提供一种粘合导电板的制备方法,包含以下步骤:
22.步骤一:将胶粘剂涂于相邻的多孔导电层的接触面上;
23.步骤二:将步骤一得到的多孔导电层进行叠加,压合,待胶粘剂固化后即得到所述粘合导电板。
24.与现有技术相比,本发明具有如下的有益效果:1、本发明粘合导电板,通过多层粘合技术,使得导电板的弯曲强度大幅提高;通过多孔导电层的孔结构的设计,让胶粘剂进入导电层的孔隙,最大程度减少胶粘剂在导电层界面形成绝缘层,从而阻隔电子在不同导电层之间传导,有效解决了粘结剂粘结通常会造成的电阻显著增大的问题。2、通过孔隙率和孔隙在表面上的面积分布和尺寸分布的设计,本发明还能大幅减小胶粘剂在多孔导电层之间形成的非导电区域(胶粘剂)的平均面积和尺寸,减小电阻在导电板中分布的不均匀性,同时能够提升粘结强度和机械强度。最终,通过具有特殊表面孔结构的多孔导电层和多层结构导电板的创新,使其导电性能十分优良,机械强度高,解决了导电板高电导率和高强度相互制约的瓶颈问题,实现了导电板性能上的突破。
附图说明
25.通过阅读参照以下附图对非限制性实施例所作的详细描述,本发明的其它特征、目的和优点将会变得更明显:
26.图1为粘合导电板结构示意图;
27.图2为多孔导电材料表面孔隙面积占比定义示意图;
28.图3为多孔铝板的表面单个孔隙平均孔隙面积对面比电阻的影响趋势图(对比例1,实施例1
‑
5);
29.图4多孔导电层表面的孔隙率对粘合导电板面比电阻的影响趋势图(对比例2
‑
3,实施例6
‑
12);
30.图5为多孔导电层表面孔隙面积占比对粘合导电板面比电阻的趋势图(对比例4、5,实施例13
‑
18);
31.图6为多孔导电层层数对粘合导电碳板弯曲强度的影响趋势图(对比例6,实施例19
‑
23);
32.图7为本发明粘合导电板结构变形一的示意图;
33.图8为本发明粘合导电板结构变形二的示意图;
34.图9为面比电阻测试装置的结构示意图。
具体实施方式
35.下面结合具体实施例对本发明进行详细说明。以下实施例将有助于本领域的技术人员进一步理解本发明,但不以任何形式限制本发明。应当指出的是,对本领域的普通技术人员来说,在不脱离本发明构思的前提下,还可以做出若干变化和改进。这些都属于本发明的保护范围。
36.高电导率和高机械强度(如抗弯强度)是导电板的重要性能要求。常规技术中,通常通过添加增强纤维的方法来提高导电板的机械强度。然而,在引入增强纤维的过程中,会带来电导率降低,加工难度增大的问题。导电板的这个问题一直没有很好地解决,导致现在燃料电池或者液流电池双极板无法达到高性能、低成本、高生产效率的要求,限制了新能源技术的发展。
37.根据“钢丝绳原理”,可以通过制备具有多层结构导电板的方法,理论上可以大幅提高导电板的弯曲强度。但问题是,如何实现多层导电材料层与层之间的固定和连接。通过
胶粘剂进行粘结是较为可行的方法。但是,研究发现,用胶粘剂进行粘结的时候,胶会在导电层之间形成一层胶层,导致电阻大幅增加。虽然通过往胶粘剂中添加导电填料的方法可以一定程度上减小电阻,但是总体上电阻的增加仍旧比较显著。
38.通过反复论证后,得出了本发明的导电板结构,即采用表面具有多孔结构的导电层进行层层粘结,可以达到预期的效果。当多孔导电层表面涂适量的胶粘剂,施加一定的压力进行粘合时,胶可以被挤压到导电层表面的孔隙当中,孔隙中的胶会和相邻导电层孔隙中的胶进行粘合,产生铆钉效应,使得多孔导电层之间的粘结强度大幅提高。此外,由于多孔导电层之间仍旧有大量的导电材料直接接触,不会在层与层之间产生较大的电阻,因此可以大幅增加机械强度的同时,保持较高的电导率和较低的面比电阻。
39.在此基础上,进行了大量的实验研究,研究发现:要达到优化效果,有几个重要的条件需要满足。首先,多孔导电层本身需要有合适的孔隙率和足够高的电导率;其次多孔导电层的表面孔隙面积占比要适中,孔隙面积占比太小则粘结强度小,孔隙面积占比太大则层间的电阻太大;再次,多孔导电层表面孔隙的大小和孔隙率分别对于电阻也会产生影响。具体分析见实施例;最后,采用本发明的技术方案后,导电板的弯曲强度随着多孔导电层的层数的增加明显提高,但是电导率和面比电阻不会随之显著增加。获得了与传统技术方案明显不同的突出有益效果。
40.接下来结合具体实施例对本发明做进一步详细描述。
41.为了更好的对比本发明中各个参数对于粘合导电板性能的影响,以下实施例制备的粘合导电板的总厚度均为1.0
±
0.05mm。结构如图1所示,表面孔隙面积占比定义如图2所示。弯曲强度、电导率和面比电阻的测试方法说明如下:
42.弯曲强度测试方法参照标准:gb/t 9341
‑
2008/iso 178:2001。
43.电导率测试方法参照标准:gb/t20042.6。
44.面比电阻测试装置如图9所示,测试样品的两侧分别为碳纸和铜电极,铜电极通过导线和测试设备连接。两个铜电极之间施加的压力为1.5mpa。样品尺寸为5cm
×
5cm。当加载样品时,测得的电阻为r1(mω),不加载样品时测得的电阻为r2(mω)。则,样品的面比电阻为r=(r1
‑
r2)
×
25(mωcm2)。
45.实施例1(实施例1
‑
实施例5针对铝板的平均孔隙面积进行优化,数据如表1所示)
46.以厚度为0.2mm,孔隙率为19.6%,表面单个孔隙平均孔隙面积为0.6
×
10
‑
10
mm2,表面孔隙面积占比为19.6%,电导率为150.4s/cm的铝片作为多孔导电层,将环氧树脂(产品型号:ausbond150)涂于相邻的多孔导电层的接触面上,将涂胶后的5层多孔铝板进行叠加,在180℃,1mpa压力下进行压合,环氧树脂固化后得到所述粘合导电板。
47.所得粘合导电板的电导率为:141.3s/cm;面比电阻为:6.6mω.cm2;弯曲强度为:79mpa。
48.实施例2
49.以厚度为0.2mm,孔隙率为19.6%,表面单个孔隙平均孔隙面积为0.002mm2,表面孔隙面积占比为19.6%,电导率为150.4s/cm的铝片作为多孔导电层,将环氧树脂(产品型号:ausbond150)涂于相邻的多孔导电层的接触面上,将涂胶后的5层多孔铝板进行叠加,在180℃,1mpa压力下进行压合,环氧树脂固化后得到所述粘合导电板。
50.所得粘合导电板的电导率为:139.6s/cm;面比电阻为:7.2mω.cm2;弯曲强度为:
78mpa。
51.实施例3
52.以厚度为0.2mm,孔隙率为19.6%,表面单个孔隙平均孔隙面积为0.0079mm2,表面孔隙面积占比为19.6%,电导率为150.4s/cm的铝片作为多孔导电层,将环氧树脂(产品型号:ausbond150)涂于相邻的多孔导电层的接触面上,将涂胶后的5层多孔铝板进行叠加,在180℃,1mpa压力下进行压合,环氧树脂固化后得到所述粘合导电板。
53.所得粘合导电板的电导率为:136.3s/cm;面比电阻为:9.3mω.cm2;弯曲强度为:74mpa。
54.实施例4
55.以厚度为0.2mm,孔隙率为19.6%,表面单个孔隙平均孔隙面积为0.071mm2,表面孔隙面积占比为19.6%,电导率为150.4s/cm的铝片作为多孔导电层,将环氧树脂(产品型号:ausbond150)涂于相邻的多孔导电层的接触面上,将涂胶后的5层多孔铝板进行叠加,在180℃,1mpa压力下进行压合,环氧树脂固化后得到所述粘合导电板。
56.所得粘合导电板的电导率为:129.6s/cm;面比电阻为:11.5mω.cm2;弯曲强度为:71mpa。
57.实施例5
58.以厚度为0.2mm,孔隙率为19.6%,表面单个孔隙平均孔隙面积为0.25mm2,表面孔隙面积占比为19.6%,电导率为150.4s/cm的铝片作为多孔导电层,将环氧树脂(产品型号:ausbond150)涂于相邻的多孔导电层的接触面上,将涂胶后的5层多孔铝板进行叠加,在180℃,1mpa压力下进行压合,环氧树脂固化后得到所述粘合导电板。
59.所得粘合导电板的电导率为:123.7s/cm;面比电阻为:15.6mω.cm2;弯曲强度为:69mpa。
60.对比例1
61.对比例1和实施例1相比,唯一改变的就是多孔铝板的表面单个孔隙平均孔隙面积为0.785mm2。
62.所得粘合导电板的电导率为:90.7s/cm;面比电阻为:30.5mω.cm2;弯曲强度为:66mpa。
63.表1、粘合导电板中多孔导电层的表面平均孔隙面积优化结果
[0064] 实施例1实施例2实施例3实施例4实施例5对比例1厚度(mm)0.20.20.20.20.20.2孔隙率(%)19.619.619.619.619.619.6表面孔隙面积占比(%)19.619.619.619.619.619.6层数555555多孔导电层的电导率(s/cm)150.4150.4150.4150.4150.4150.4表面单个孔隙平均孔隙面积(mm2)0.6
×
10
‑
10
0.0020.00790.0710.250.785胶粘剂环氧树脂环氧树脂环氧树脂环氧树脂环氧树脂环氧树脂粘合导电板的电导率(s/cm)141.3139.6136.3129.6123.790.7面比电阻(mω.cm2)6.67.29.311.515.630.5弯曲强度(mpa)797874716966
[0065]
从表1数据和图3曲线可知,在其他条件不变的情况下,导电板的面比电阻随着多
孔导电层表面单个孔隙的平均孔隙面积的增大而增大,电导率和弯曲强度随着平均孔隙面积的增大而减小。平均孔隙面积小于0.25mm2时,导电板的面比电阻小于20mω.cm2。另外,我们发现,进一步减小平均孔隙面积,比如实施例3,面比电阻快速减小,性能大幅提升。在我们能够进行的实验范围内,我们发现表面单个孔隙的平均孔隙面积在非常小的时候,甚至在0.6
×
10
‑
10
mm2的时候粘合导电板的综合性能仍旧较好。
[0066]
实施例6(实施例6
‑
实施例12针对孔隙率进行优化,数据如表2所示)
[0067]
以厚度为0.1mm,孔隙率为5%,表面单个孔隙平均孔隙面积为0.0004mm2,表面孔隙面积占比为7.5%,电导率为308s/cm的碳板作为多孔导电层,将环氧树脂(产品型号:ausbond150)涂于相邻的多孔导电层的接触面上,将涂胶后的10层多孔碳板进行叠加,在150℃,1mpa压力下进行压合,环氧树脂固化后得到所述粘合导电板。
[0068]
所得粘合导电板的电导率为:160s/cm;面比电阻为:18.2mω.cm2;弯曲强度为:30.4mpa。
[0069]
实施例7
[0070]
以厚度为0.1mm,孔隙率为12%,表面单个孔隙平均孔隙面积为0.0004mm2,表面孔隙面积占比为7.5%,电导率为256s/cm的碳板作为多孔导电层,将环氧树脂(产品型号:ausbond150)涂于相邻的多孔导电层的接触面上,将涂胶后的10层多孔碳板进行叠加,在150℃,1mpa压力下进行压合,环氧树脂固化后得到所述粘合导电板。
[0071]
所得粘合导电板的电导率为:203s/cm;面比电阻为:9.6mω.cm2;弯曲强度为:33.4mpa。
[0072]
实施例8
[0073]
以厚度为0.1mm,孔隙率为30%,表面单个孔隙平均孔隙面积为0.0004mm2,表面孔隙面积占比为7.5%,电导率为244s/cm的碳板作为多孔导电层,将环氧树脂(产品型号:ausbond150)涂于相邻的多孔导电层的接触面上,将涂胶后的10层多孔碳板进行叠加,在150℃,1mpa压力下进行压合,环氧树脂固化后得到所述粘合导电板。
[0074]
所得粘合导电板的电导率为:235s/cm;面比电阻为:5.1mω.cm2;弯曲强度为:39.7mpa。
[0075]
实施例9
[0076]
以厚度为0.1mm,孔隙率为40%,表面单个孔隙平均孔隙面积为0.0004mm2,表面孔隙面积占比为7.5%,电导率为238/cm的碳板作为多孔导电层,将环氧树脂(产品型号:ausbond150)涂于相邻的多孔导电层的接触面上,将涂胶后的10层多孔碳板进行叠加,在150℃,1mpa压力下进行压合,环氧树脂固化后得到所述粘合导电板。
[0077]
所得粘合导电板的电导率为:232s/cm;面比电阻为:4.6mω.cm2;弯曲强度为:40.2mpa。
[0078]
实施例10
[0079]
以厚度为0.1mm,孔隙率为50%,表面单个孔隙平均孔隙面积为0.0004mm2,表面孔隙面积占比为7.5%,电导率为235/cm的碳板作为多孔导电材料,将环氧树脂(产品型号:ausbond150)涂于相邻的多孔导电层的接触面上,将涂胶后的10层多孔碳板进行叠加,在150℃,1mpa压力下进行压合,环氧树脂固化后得到所述粘合导电板。
[0080]
所得粘合导电板的电导率为:230s/cm;面比电阻为:4.1mω.cm2;弯曲强度为:
40.6mpa。
[0081]
实施例11
[0082]
以厚度为0.1mm,孔隙率为62%,表面单个孔隙平均孔隙面积为0.0004mm2,表面孔隙面积占比为7.5%,电导率为213s/cm的碳板作为多孔导电层,将环氧树脂(产品型号:ausbond150)涂于相邻的多孔导电层的接触面上,将涂胶后的10层多孔碳板进行叠加,在150℃,1mpa压力下进行压合,环氧树脂固化后得到所述粘合导电板。
[0083]
所得粘合导电板的电导率为:201s/cm;面比电阻为:6.8mω.cm2;弯曲强度为:36.7mpa。
[0084]
实施例12
[0085]
以厚度为0.1mm,孔隙率为70%,表面单个孔隙平均孔隙面积为0.0004mm2,表面孔隙面积占比为7.5%,电导率为192s/cm的碳板作为多孔导电层,将环氧树脂(产品型号:ausbond150)涂于相邻的多孔导电层的接触面上,将涂胶后的10层多孔碳板进行叠加,在150℃,1mpa压力下进行压合,环氧树脂固化后得到所述粘合导电板。
[0086]
所得粘合导电板的电导率为:181s/cm;面比电阻为:9.8mω.cm2;弯曲强度为:39.6mpa。
[0087]
对比例2
[0088]
本对比例和实施例6的方案相同,唯一不同的是选用的多孔碳板的孔隙率为3%,电导率为395s/cm。所得粘合导电板的电导率为:83s/cm;面比电阻为:43.2mω.cm2;弯曲强度为:29.6mpa。
[0089]
对比例3
[0090]
本对比例和实施例6的方案相同,唯一不同的是选用的多孔碳板的孔隙率为74%,电导率为144s/cm。所得粘合导电板的电导率为:102s/cm;面比电阻为:18.2mω.cm2;弯曲强度为:32.6mpa。
[0091]
表2、粘合导电板中多孔导电层的孔隙率优化结果
[0092]
[0093][0094]
从表2数据和图4曲线可知,在相同条件下,随着多孔导电层孔隙率的增加,多孔导电层的电导率会随之降低。粘合导电板的面比电阻随着多孔导电层孔隙率的增加呈现先减小后增加的趋势。孔隙率太小,多孔导电层之间的胶会更多地留在导电层之间非孔隙表面,会导致粘合导电板电阻增大。孔隙率太大的时候,多孔导电层本身电导率降低,从而也会使粘合导电板的电阻增加。通过实验,我们发现多孔层孔隙率为5%
‑
70%之间时,导电板的综合性能较好,特别是当多孔层孔隙率为12%
‑
62%之间时,粘合导电板的电导率、面比电阻和弯曲强度均比较理想。
[0095]
实施例13(实施例13
‑
实施例18针对表面孔隙面积占比进行优化,数据如表3所示)
[0096]
以厚度为0.1mm,孔隙率为27%,表面单个孔隙平均孔隙面积约为0.024mm2,表面孔隙面积占比为30%,电导率为237s/cm的天然石墨板作为多孔导电层,将乙烯基酯树脂(产品型号:上纬901)涂于相邻的多孔导电层的接触面上,将涂胶后的10层多孔天然石墨板进行叠加,在120℃,3mpa压力下进行压合,乙烯基酯树脂固化后得到所述粘合导电板。
[0097]
所得粘合导电板的电导率为:186s/cm;面比电阻为:19.6mω.cm2;弯曲强度为:37.2mpa。
[0098]
实施例14
[0099]
以厚度为0.1mm,孔隙率为27%,表面单个孔隙平均孔隙面积约为0.024mm2,表面孔隙面积占比为19%,电导率为237s/cm的天然石墨板作为多孔导电层,将乙烯基酯树脂(产品型号:上纬901)涂于相邻的多孔导电层的接触面上,将涂胶后的10层多孔天然石墨板进行叠加,在120℃,3mpa压力下进行压合,乙烯基酯树脂固化后得到所述粘合导电板。
[0100]
所得粘合导电板的电导率为:208s/cm;面比电阻为:13.6mω.cm2;弯曲强度为:35.7mpa。
[0101]
实施例15
[0102]
以厚度为0.1mm,孔隙率为27%,表面单个孔隙平均孔隙面积约为0.024mm2,表面孔隙面积占比为9%,电导率为237s/cm的天然石墨板作为多孔导电层,将乙烯基酯树脂(产品型号:上纬901)涂于相邻的多孔导电层的接触面上,将涂胶后的10层多孔天然石墨板进行叠加,在120℃,3mpa压力下进行压合,乙烯基酯树脂固化后得到所述粘合导电板。
[0103]
所得粘合导电板的电导率为:213s/cm;面比电阻为:7.1mω.cm2;弯曲强度为:33.1mpa。
[0104]
实施例16
[0105]
以厚度为0.1mm,孔隙率为27%,表面单个孔隙平均孔隙面积约为0.024mm2,表面孔隙面积占比为4%,电导率为237s/cm的天然石墨板作为多孔导电层,将乙烯基酯树脂(产品型号:上纬901)涂于相邻的多孔导电层的接触面上,将涂胶后的10层多孔天然石墨板进行叠加,在120℃,3mpa压力下进行压合,乙烯基酯树脂固化后得到所述粘合导电板。
[0106]
所得粘合导电板的电导率为:237s/cm;面比电阻为:3.1mω.cm2;弯曲强度为:32.7mpa。因为天然石墨质地较软,经过压实后,电导率会进一步提高。
[0107]
实施例17
[0108]
以厚度为0.1mm,孔隙率为27%,表面单个孔隙平均孔隙面积约为0.024mm2,表面孔隙面积占比为1%,电导率为237s/cm的天然石墨板作为多孔导电层,将乙烯基酯树脂(产品型号:上纬901)涂于相邻的多孔导电层的接触面上,将涂胶后的10层多孔天然石墨板进行叠加,在120℃,3mpa压力下进行压合,乙烯基酯树脂固化后得到所述粘合导电板。
[0109]
所得粘合导电板的电导率为:236s/cm;面比电阻为:3.6mω.cm2;弯曲强度为:26.8mpa。
[0110]
实施例18
[0111]
以厚度为0.1mm,孔隙率为27%,表面单个孔隙平均孔隙面积约为0.024mm2,表面孔隙面积占比为0.1%,电导率为237s/cm的天然石墨板作为多孔导电层,将乙烯基酯树脂(产品型号:上纬901)涂于相邻的多孔导电层的接触面上,将涂胶后的10层多孔天然石墨板进行叠加,在120℃,3mpa压力下进行压合,乙烯基酯树脂固化后得到所述粘合导电板。
[0112]
所得粘合导电板的电导率为:237s/cm;面比电阻为:5.9mω.cm2;弯曲强度为:25.1mpa。
[0113]
对比例4
[0114]
本对比例和实施例15的实施方案基本相同,唯一不同的是多孔碳板的表面孔隙面积占比为42%。
[0115]
所得粘合导电板的电导率为:148s/cm;面比电阻为:34.7mω.cm2;弯曲强度为:38.1mpa。
[0116]
对比例5
[0117]
本对比例和实施例15的实施方案基本相同,唯一不同的是多孔碳板的表面孔隙面积占比为0.008%。
[0118]
所得粘合导电板的电导率为:225s/cm;面比电阻为:11.2mω.cm2;弯曲强度为:16.3mpa。
[0119]
表3、粘合导电板中多孔导电层的表面孔隙面积占比优化结果
[0120]
[0121]
从表3数据和图5曲线可知,随着多孔导电层表面孔隙面积占比从0开始增大到4%,粘合导电板面比电阻显著降低,随着表面孔隙面积占比进一步增加,由于多孔导电层导电区域接触面积的减小,导致粘合导电板面比电阻增加。
[0122]
实施例19(实施例19
‑
实施例23针对多孔导电层的层数进行优化,数据如表4所示)
[0123]
以厚度为0.01mm,孔隙率为50%,表面单个孔隙平均孔隙面积约为2
×
10
‑6mm2,表面孔隙面积占比为5.8%,电导率为218s/cm的石墨片作为多孔导电层,将乙烯基酯树脂(产品型号:上纬901)涂于相邻的多孔导电层的接触面上,将涂胶后的100层多孔石墨片进行叠加,在200℃,5mpa压力下进行压合,乙烯基酯树脂固化后得到所述粘合导电板。
[0124]
所得粘合导电板的电导率为:181s/cm;面比电阻为:9.1mω.cm2;弯曲强度为:56.3mpa。
[0125]
实施例20
[0126]
以厚度为0.05mm,孔隙率为50%,表面单个孔隙平均孔隙面积约为2
×
10
‑6mm2,表面孔隙面积占比为5.8%,电导率为218s/cm的石墨片作为多孔导电层,将乙烯基酯树脂(产品型号:上纬901)涂于相邻的多孔导电层的接触面上,将涂胶后的20层多孔石墨片进行叠加,在200℃,5mpa压力下进行压合,乙烯基酯树脂固化后得到所述粘合导电板。
[0127]
所得粘合导电板的电导率为:216s/cm;面比电阻为:7.2mω.cm2;弯曲强度为:47.2mpa。
[0128]
实施例21
[0129]
以厚度为0.1mm,孔隙率为50%,表面单个孔隙平均孔隙面积约为2
×
10
‑6mm2,表面孔隙面积占比为5.8%,电导率为218s/cm的石墨片作为多孔导电层,将乙烯基酯树脂(产品型号:上纬901)涂于相邻的多孔导电层的接触面上,将涂胶后的10层多孔石墨片进行叠加,在200℃,5mpa压力下进行压合,乙烯基酯树脂固化后得到所述粘合导电板。
[0130]
所得粘合导电板的电导率为:232s/cm;面比电阻为:4.0mω.cm2;弯曲强度为:39.3mpa。
[0131]
实施例22
[0132]
以厚度为0.2mm,孔隙率为50%,表面单个孔隙平均孔隙面积约为2
×
10
‑6mm2,表面孔隙面积占比为5.8%,电导率为218s/cm的石墨片作为多孔导电层,将乙烯基酯树脂(产品型号:上纬901)涂于相邻的多孔导电层的接触面上,将涂胶后的5层多孔石墨片进行叠加,在200℃,5mpa压力下进行压合,乙烯基酯树脂固化后得到所述粘合导电板。
[0133]
所得粘合导电板的电导率为:220s/cm;面比电阻为:5.8mω.cm2;弯曲强度为:30.9mpa。
[0134]
实施例23
[0135]
以厚度为0.5mm,孔隙率为50%,表面单个孔隙平均孔隙面积约为2
×
10
‑6mm2,表面孔隙面积占比为5.8%,电导率为218s/cm的石墨片作为多孔导电层,将乙烯基酯树脂(产品型号:上纬901)涂于相邻的多孔导电层的接触面上,将涂胶后的2层多孔石墨片进行叠加,在200℃,5mpa压力下进行压合,乙烯基酯树脂固化后得到所述粘合导电板。
[0136]
所得粘合导电板的电导率为:186s/cm;面比电阻为:9.8mω.cm2;弯曲强度为:13.7mpa。
[0137]
对比例6
[0138]
此对比例和实施例19的方案基本相同,唯一不同的地方是采用厚度为1.0mm的石墨片没有采用层叠方式制备1.0mm厚导电板。
[0139]
所得粘合导电板的电导率为:218s/cm;面比电阻为:6.1mω.cm2;弯曲强度为:5.6mpa。
[0140]
表4、粘合导电板中多孔导电层的层数优化结果
[0141][0142]
从表4数据和图6曲线可知,随着多孔导电层层数的增加,粘合导电板的弯曲强度显著提升。
[0143]
实施例24(实施例24
‑
实施例34针对不同的胶粘剂进行筛选,数据如表5所示)
[0144]
以厚度为0.1mm,孔隙率为35%,表面单个孔隙平均孔隙面积约为0.0081mm2,表面孔隙面积占比为12%,电导率为326s/cm的膨胀石墨板作为多孔导电层,将乙烯基酯树脂(产品型号:上纬901)涂于相邻的多孔导电层的接触面上,将涂胶后的10层多孔膨胀石墨板进行叠加,在180℃,10mpa压力下进行压合,乙烯基酯树脂固化后得到所述粘合导电板。
[0145]
所得粘合导电板的电导率为:361s/cm;面比电阻为:2.3mω.cm2;弯曲强度为:39.5mpa。粘合导电板的电导率高于单层膨胀石墨板的电导率,是因为膨胀石墨板压合以后,更加紧密,然后这种紧密结构被胶粘剂固定下来,电导率反而提高了。
[0146]
实施例25
[0147]
以厚度为0.1mm,孔隙率为35%,表面单个孔隙平均孔隙面积约为0.0081mm2,表面孔隙面积占比为12%,电导率为326s/cm的膨胀石墨板作为多孔导电层,将酚醛树脂(产品型号:hk
‑
381d)涂于相邻的多孔导电层的接触面上,将涂胶后的10层多孔膨胀石墨板进行叠加,在180℃,10mpa压力下进行压合,酚醛树脂固化后得到所述粘合导电板。
[0148]
所得粘合导电板的电导率为:307s/cm;面比电阻为:3.7mω.cm2;弯曲强度为:29.6mpa。
[0149]
实施例26
[0150]
以厚度为0.1mm,孔隙率为35%,表面单个孔隙平均孔隙面积约为0.0081mm2,表面孔隙面积占比为12%,电导率为326s/cm的膨胀石墨板作为多孔导电层,将聚偏氟乙烯树脂(产品型号:阿科玛hsv900)涂于相邻的多孔导电层的接触面上,将涂胶后的10层多孔膨胀石墨板进行叠加,在180℃,10mpa压力下进行压合,聚偏氟乙烯树脂固化后得到所述粘合导电板。
[0151]
所得粘合导电板的电导率为:296s/cm;面比电阻为:5.8mω.cm2;弯曲强度为:24.3mpa。
[0152]
实施例27
[0153]
以厚度为0.1mm,孔隙率为35%,表面单个孔隙平均孔隙面积约为0.0081mm2,表面孔隙面积占比为12%,电导率为326s/cm的膨胀石墨板作为多孔导电层,将聚乙烯树脂(产品型号:ldpe/q281)涂于相邻的多孔导电层的接触面上,将涂胶后的10层多孔膨胀石墨板进行叠加,在180℃,10mpa压力下进行压合,聚乙烯树脂固化后得到所述粘合导电板。
[0154]
所得粘合导电板的电导率为:275s/cm;面比电阻为:8.1mω.cm2;弯曲强度为:22.2mpa。
[0155]
实施例28
[0156]
以厚度为0.1mm,孔隙率为35%,表面单个孔隙平均孔隙面积约为0.0081mm2,表面孔隙面积占比为12%,电导率为326s/cm的膨胀石墨板作为多孔导电层,将聚丙烯树脂(产品型号:sk
‑
r370y)涂于相邻的多孔导电层的接触面上,将涂胶后的10层多孔膨胀石墨板进行叠加,在180℃,10mpa压力下进行压合,聚丙烯树脂固化后得到所述粘合导电板。
[0157]
所得粘合导电板的电导率为:273s/cm;面比电阻为:8.4mω.cm2;弯曲强度为:25.2mpa。
[0158]
实施例29
[0159]
以厚度为0.1mm,孔隙率为35%,表面单个孔隙平均孔隙面积约为0.0081mm2,表面孔隙面积占比为12%,电导率为326s/cm的膨胀石墨板作为多孔导电层,将聚酰亚胺树脂溶液(产品型号:paa
‑
1003)涂于相邻的多孔导电层的接触面上,将涂胶后的10层多孔膨胀石墨板进行叠加,在180℃,10mpa压力下进行压合,聚酰亚胺树脂固化后得到所述粘合导电板。
[0160]
所得粘合导电板的电导率为:284s/cm;面比电阻为:8.1mω.cm2;弯曲强度为:28.3mpa。
[0161]
实施例30
[0162]
以厚度为0.1mm,孔隙率为35%,表面单个孔隙平均孔隙面积约为0.0081mm2,表面孔隙面积占比为12%,电导率为326s/cm的膨胀石墨板作为多孔导电层,将聚醚砜树脂溶液(产品型号:巴斯夫e2010)涂于相邻的多孔导电层的接触面上,将涂胶后的10层多孔膨胀石墨板进行叠加,在180℃,10mpa压力下进行压合,聚醚砜树脂固化后得到所述粘合导电板。
[0163]
所得粘合导电板的电导率为:285s/cm;面比电阻为:8.4mω.cm2;弯曲强度为:28.5mpa。
[0164]
实施例31
[0165]
以厚度为0.1mm,孔隙率为35%,表面单个孔隙平均孔隙面积约为0.0081mm2,表面孔隙面积占比为12%,电导率为326s/cm的膨胀石墨板作为多孔导电层,将聚醚醚酮(产品型号:威格斯l150)溶液涂于相邻的多孔导电层的接触面上,将涂胶后的10层多孔膨胀石墨板进行叠加,在180℃,10mpa压力下进行压合,聚醚醚酮树脂固化后得到所述粘合导电板。
[0166]
所得粘合导电板的电导率为:283s/cm;面比电阻为:8.7mω.cm2;弯曲强度为:28.3mpa。
[0167]
实施例32
[0168]
以厚度为0.1mm,孔隙率为35%,表面单个孔隙平均孔隙面积约为0.0081mm2,表面孔隙面积占比为12%,电导率为326s/cm的膨胀石墨板作为多孔导电层,将聚氯乙烯(产品型号:齐鲁石化s700)涂于相邻的多孔导电层的接触面上,将涂胶后的10层多孔膨胀石墨板进行叠加,在180℃,10mpa压力下进行压合,聚氯乙烯树脂固化后得到所述粘合导电板。
[0169]
所得粘合导电板的电导率为:265s/cm;面比电阻为:12.3mω.cm2;弯曲强度为:18.3mpa。
[0170]
实施例33
[0171]
以厚度为0.1mm,孔隙率为35%,表面单个孔隙平均孔隙面积约为0.0081mm2,表面孔隙面积占比为12%,电导率为326s/cm的膨胀石墨板作为多孔导电层,将聚偏氟乙烯
‑
六氟丙烯树脂(pvdf
‑
hfp,产品型号:solef 21510)涂于相邻的多孔导电层的接触面上,将涂胶后的10层多孔膨胀石墨板进行叠加,在180℃,10mpa压力下进行压合,聚偏氟乙烯
‑
六氟丙烯树脂固化后得到所述粘合导电板。
[0172]
所得粘合导电板的电导率为:283s/cm;面比电阻为:7.3mω.cm2;弯曲强度为:23.7mpa。
[0173]
实施例34
[0174]
以厚度为0.1mm,孔隙率为35%,表面单个孔隙平均孔隙面积约为0.0081mm2,表面孔隙面积占比为12%,电导率为326s/cm的膨胀石墨板作为多孔导电层,将丙烯酸树脂(产品型号:利仁
‑
838c)涂于相邻的多孔导电层的接触面上,将涂胶后的10层多孔膨胀石墨板进行叠加,在180℃,10mpa压力下进行压合,丙烯酸树脂固化后得到所述粘合导电板。
[0175]
所得粘合导电板的电导率为:264s/cm;面比电阻为:18.3mω.cm2;弯曲强度为:20.0mpa。
[0176]
实施例35
[0177]
以厚度为0.1mm,孔隙率为35%,表面单个孔隙平均孔隙面积约为0.0081mm2,表面孔隙面积占比为12%,电导率为326s/cm的膨胀石墨板作为多孔导电层,将环氧树脂(产品型号:ausbond150)涂于相邻的多孔导电层的接触面上,将涂胶后的10层多孔膨胀石墨板进行叠加,在180℃,10mpa压力下进行压合,环氧树脂固化后得到所述粘合导电板。
[0178]
所得粘合导电板的电导率为:358s/cm;面比电阻为:3.2mω.cm2;弯曲强度为:38.9mpa。
[0179]
表5、粘合导电板中多孔导电层间胶粘剂的优化结果
[0180][0181]
从表5数据可知,本发明所述的胶粘剂均能制备得到性能较好的粘合导电板,其中我们可以发现,相同情况下,热固性树脂的效果优于热塑性树脂。
[0182]
对比例7
[0183]
本对比例和实施例8方案基本相同,唯一不同的是采用电导率为109s/cm的碳板作为多孔导电层制备厚度为1.0mm的粘合导电板。
[0184]
所得粘合导电板的电导率为:97s/cm;面比电阻为:36.8mω.cm2;弯曲强度为:34.7mpa。
[0185]
从对比例7可以看出,多孔导电层的电导率对粘合导电板的电导率和面比电阻有显著影响,多孔导电层电导率太低则无法获得高电导率和低面比电阻的粘合导电板。经过实验研究发现,多孔导电层的电导率高于150s/cm时,可以制备得到电导率较高、面比电阻较小的粘合导电板,满足燃料电池和液流电池双极板的性能要求。
[0186]
应当说明的是,本发明的粘合导电板结构如图1所示,3层多孔导电层的两个表面及内部均设有孔隙,相邻的多孔导电层之间通过胶粘剂粘合,胶粘剂填充于表面孔隙中,使相邻的多孔导电层粘合在一起从而形成粘合导电板。当然还可以有其他变形。
[0187]
例如,粘合导电板结构的变形一如图7所示,当n大于等于3时,位于最上层和最下层的多孔导电层可以只有一个表面设有孔隙,位于中间的多孔导电层两个表面均设有孔隙,相邻的多孔导电层之间通过胶粘剂粘合,胶粘剂填充于表面孔隙中,使相邻的多孔导电层粘合在一起从而形成粘合导电板。在此基础上上,多孔导电层的内部也可以设有孔隙。
[0188]
粘合导电板结构的变形二如图8所示,3层多孔导电层两个表面均设有孔隙,相邻的多孔导电层之间通过胶粘剂粘合,胶粘剂填充于表面孔隙中,使相邻的多孔导电层粘合在一起从而形成粘合导电板。
[0189]
以上对本发明的具体实施例进行了描述。需要理解的是,本发明并不局限于上述特定实施方式,本领域技术人员可以在权利要求的范围内做出各种变化或修改,这并不影响本发明的实质内容。在不冲突的情况下,本技术的实施例和实施例中的特征可以任意相
互组合。