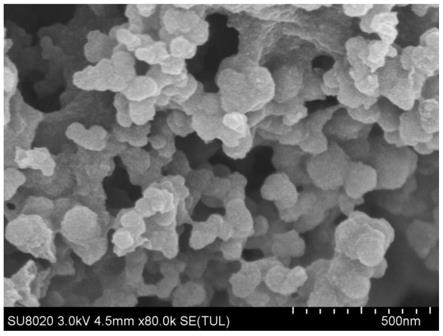
1.本发明属于新型能源材料领域,涉及一种多孔硅碳复合材料及其制备方法,特别涉及一种生物质基多孔硅碳复合负极材料及其制备方法。
背景技术:2.锂离子电池由于具有工作电压高、能量密度高、无污染、自放电小、循环寿命长等优点在储能和动力电池领域得到广泛应用。常规石墨类负极碳材料的理论容量仅为372mah
·
g
‑1,实际容量低,振实密度小,使得电极材料的体积能量密度较小,与磷酸铁锂、锰酸锂等正极材料匹配组装成商业电池的能量密度难以满足能源行业日益增高的能量密度要求。加之,其在快速充放电过程中易产生“锂枝晶”导致电池安全隐患。而硅基材料由于其具有高达4200mah
·
g
‑1的理论容量、约0.4v的低电压平台(li/li
+
)、高的安全性、优异的低温性能和自然储存丰富等优点成为下一代替代商用新型负极材料。
3.然而,硅基材料应用过程中存在的一些问题阻碍了其商业化应用。首先,在充放电过程中,硅基材料在嵌锂和脱锂的时候会产生高达300%的体积膨胀和收缩,会使硅颗粒挤压、粉化,使有效活性材料从集流体上脱落,电极结构被破坏,进而失去电接触引发容量迅速衰减,电池的循环稳定性能变差。其次,体积效应使硅基材料在断裂面不断形成新的、不稳定的sei膜,造成不可逆容量急增、电池内阻增大、库伦效率变低和导电性变差等问题。而且,硅属于半导体材料,其低的电导率和离子扩散系数降低了锂离子的扩散动力学性能。因而需要对硅基材料的结构进行优化设计以改善和提升其性能。常用的改性方法主要通过硅的纳米化处理来降低硅的体积变化,以及将硅与不同结构的碳基材料复合构建核
‑
壳、蛋黄
‑
壳、多孔等结构来缓解体积变化、增加材料导电性进而改善硅基材料的循环性能。
4.为了解决现有硅碳复合负极材料存在的问题,有必要研发一种新的生物质基多孔硅碳复合材料及制备方法。
技术实现要素:5.本发明针对上述问题,提出了一种生物质基多孔硅碳复合材料及制备方法。
6.本发明采用葛根残留物作为生物质基,本发明针对葛根产业中残留物(表皮、根须和残渣等)残余量大、处理方法单一,附加值低等问题,利用葛根残留物粉末在水中溶胀变粘形成三维多孔碳基材料的特性,在制备复合材料的过程中可用作粘结剂、增稠剂和首次包覆剂,提供了一条葛根残留物资源再利用制备生物质基多孔硅碳复合负极材料及其方法,制得的硅碳复合负极材料具有高容量、高倍率充放电性能、长循环寿命,以及生产成本低等方面的优势。这既为葛根残留物的循环再利用提供了全新技术路线,又解决了新型动力电池负极电极材料来源的问题。
7.本发明的生物质基多孔硅碳复合材料,以碳水化合物形成的部分石墨化薄包覆碳层均匀分散包覆纳米硅粉并桥接植物纤维形成的三维碳纤维骨架制备得到的三维多孔硅碳复合材料为前驱体,前驱体外包裹有经水热原位二次包覆的热解碳层。前驱体中多空结
构孔径为50nm~5μm,其质量占前驱体质量的50~60%,二次包覆层的质量为前驱体质量的5.0~15.0%。
8.本发明的生物质基多孔硅碳复合材料结构为:内核为纳米硅粉,纳米硅粉外均匀分散包覆碳水化合物形成的部分石墨化薄包覆碳层,所述纳米硅粉与所述石墨化薄包覆碳层之间桥接植物纤维形成三维碳纤维骨架的三维多孔硅碳复合材料,所述三维多孔硅碳复合材料外层二次包覆热解碳层。
9.具体的,一种生物质基多孔硅碳复合材料,所述纳米硅粒子的尺寸为30nm~100nm,其质量占所述三维多孔硅碳复合材料质量的5%~30%;
10.所述石墨化薄包覆碳层多空结构孔径为50nm~5μm,其质量占前驱体质量的50%~60%;
11.所述二次包覆热解碳层的厚度为5nm~15nm,其质量为前驱体质量的5.0%~15.0%。
12.本发明提供的以葛根残留物形成生物质基多孔碳材料来制备多孔硅碳复合负极材料的方法,以生产葛根粉时所残留的表皮、根须和过程残渣为原料,经过清洗、粉碎、提纯和干燥得到纯度较高的残留物微粉,残留物微粉和纳米硅粉在醇溶剂作用下均匀分散,搅拌加热,通过调控温度控制葛根残留物微粉的溶胀程度和粘度大小,然后经喷雾造粒、高温热解和粉碎筛分处理制得多孔硅碳复合前驱体,前驱体外再经水热原位二次有机包覆和热解处理后,最终得到生物质基多孔硅碳复合材料。
13.本发明提供的一种生物质基多孔硅碳复合材料的制备方法,具体步骤为:
14.一、制备生物质基多孔硅碳复合前驱体(p
‑
c/si)
15.s1葛根残留物预处理:室温下,将葛根残留物清洗干净后粉碎至粒径为3~5μm的微粉颗粒,并将粉碎后的葛根残留物粉末一步清洗提纯,充分干燥后得到纯净葛根残留物微粉;
16.具体如室温下,将葛根残留物用洗洁精做清洗剂搅拌清洗去除表面沙砾和内部残留杂质,然后粉碎至粒径为3~5μm的微粉颗粒,并将粉碎后的葛根残留物粉末在水溶液中用提纯设备进一步清洗提纯,在本领域技术人员可设计一定干燥温度和干燥时间下,将葛根残留物微粉充分干燥,如在温度为80℃~100℃的鼓风烘箱干燥12h~24h,得到纯净葛根残留物微粉;
17.本步骤中,所述葛根残留物为生产葛根产品时所残留的表皮、根须、生产残渣的一种或多种;
18.所述粉碎方式为机械粉碎、气流粉碎和研磨粉碎中的任意一种,设备可选用机械式粉碎机、辊筒磨粉机、气流粉碎机、研磨机等;
19.所述的提纯方式为自然沉降、过滤和离心中的一种,设备可选用真空抽滤机、加压过滤机、离心机、涡旋分离器、带式压榨过滤机、脱水机等;
20.本步骤将葛根残留物中的一些表层及内部杂质去除,以防杂质对电极材料的性能产生影响。将残留物粉碎至微粉颗粒,既能更好地进行提纯处理得到纯净原料,又能使微粉颗粒在后期加热溶胀变粘过程更加充分,形成稳定有效的三维多孔结构碳基材料。提纯是为了去除粉碎过程微粉中的一些悬浮杂质得到杂质含量在1%以下的纯净残留物微粉颗粒。
21.s2喷雾造粒:将葛根残留物微粉和纳米硅粉按质量比为100:(5.0~30.0)分散于醇溶剂溶液中进行液相机械混合,然后将混合浆料在加热设备中搅拌加热,调节温度控制葛根残留物粉末的溶胀性能来调整浆料的粘稠度,再经喷雾造粒得到生物质基多孔硅碳复合样;
22.本步骤中,所述纳米硅粉为30~100nm的硅粉粒子;
23.所述醇溶剂为甲醇、乙醇、异丙醇的一种或几种;
24.所述浆料中混合物质量分数为10~40%;
25.所述液相混合转速200~1500r/min,搅拌时间30~120min;
26.所述搅拌加热设备为磁力搅拌器,恒温油浴锅与恒温水浴锅的一种;
27.所述加热温度范围为50~120℃,搅拌速度为500~800r/min;
28.所述混合浆料加热搅拌,待葛根残留物微粉溶胀充分后,得到粘稠度为1000
‑
1500cp的混合浆料;
29.所述喷雾干燥机进口温度为180℃~260℃,出口温度为120℃~160℃;
30.喷雾干燥进料速度为10ml/min~50ml/min;
31.本步骤利用葛根微粉的溶胀变粘形成三维多孔碳基材料,在制备复合材料的过程中可用作粘结剂、增稠剂和首次包覆剂的特性,省去粘结剂、增稠剂和包覆剂的使用,直接以微粉作为粘结剂和包覆剂对纳米硅粉进行包覆和结构构造处理,经喷雾造粒得到有溶胀孔洞的生物质基多孔硅碳复合样。
32.s3高温炭化:将生物质基多孔硅碳复合样置于高温气氛炉,在保护性气体气氛下进行热解处理,热解结束待物料冷却后,粉碎得到生物质基多孔硅碳复合前驱体(p
‑
c/si);粉碎后通过细小筛网,得到的生物质基多孔硅碳复合前驱体均匀性较好,如通过150目筛网、200目筛网、250目筛网等;
33.本步骤中,所述保护性气体为氮气、氦气、氖气、氩气、氪气或氙气的一种或几种。流量为0.5l/min~10l/min;
34.所述热解处理,升温速度为2℃/min~5℃/min,热解温度为600℃~1100℃,热解炭化时间为2h~5h;
35.本步骤在保护性气氛中、高温条件下,残留物微粉中分布杂乱的纤维相互连接形成三维碳纤维骨架结构;而其中的碳水化合物形成薄的部分石墨化包覆层将纳米硅粉分散包覆并桥接三维碳纤维骨架结构形成三维多孔结构生物质基硅碳复合前驱体。
36.二、制备生物质基多孔硅碳复合材料(p
‑
c/si/c)
37.s4水热
‑
原位聚合包覆:将制备的生物质基多孔硅碳复合前驱体和有机碳源按质量比为1:(1.0~3.0)均匀混合,超声分散在水中,在水热反应釜中通过水热
‑
原位聚合进行二次碳包覆,对混合物溶液离心、洗涤、干燥后得到二次包覆复合材料;
38.本步骤中,所述生物质基多孔硅碳复合前驱体和有机碳源的混合物与水的固液质量比为(1.0~2.0):(20~40);
39.所述有机碳源为葡萄糖、蔗糖、聚乙二醇、羧甲基纤维素、水溶性酚醛树脂、聚乙烯醇的一种或几种;
40.所述水热
‑
原位聚合的温度为150℃~200℃,聚合时间为12h
‑
24h;
41.本步骤通过水热
‑
原位聚合的方法将有机碳源均匀的二次包覆在前驱体表层,得
到二次包覆复合材料。
42.s5热解处理:将得到的二次包覆复合材料置于高温气氛炉,在保护性气体气氛下进行热解碳化,待物料冷却后,粉碎得到生物质基多孔硅碳复合材料(p
‑
c/si/c);粉碎后通过细小筛网,得到的材料均匀性较好,如通过150目筛网、200目筛网、250目筛网等;
43.本步骤中,所述保护性气体为氮气、氩气的一种,流量为0.5l/min~10l/min;
44.所述热解处理,升温速度为2℃/min~5℃/min,热解温度为500℃~1000℃,恒温热解时间2h~4h;
45.本步骤在保护气氛、高温下,将有机碳源包覆层炭化为二次碳包覆层包裹在前驱体表层,得到最终的生物质基多孔硅碳复合材料。
46.进一步,本发明的生物质基多孔硅碳复合材料是一种锂离子电池负极材料。
47.本发明以利用率低、附加值小、价格低廉的葛根残留物和纳米硅粉为原料,利用葛根残留物粉末在水溶液中随着温度的升高,会溶胀变粘产生孔隙结构,以及具有优异的粘结包覆的特性将纳米级硅粉均匀分散包覆,经喷雾造粒和水热原位二次碳包覆后制备得到生物质基多孔硅碳复合材料。葛根残留物中分布杂乱的植物纤维烧结后形成的三维碳纤维骨架不仅为纳米硅材料在充放电循环过程中的体积膨胀提供缓冲空间来保护电极的完整,又缩短锂离子的扩散路径来提高锂离子的扩散速率,并通过微孔储锂和优异吸液性能提升材料的容量和电化学性能。碳水化合物形成薄的部分石墨化包覆层将纳米硅粉分散包覆并桥接三维碳纤维骨架结构形成三维多孔结构前驱体,其不仅保护前驱体材料中的纳米硅不与电解液接触发生副反应,又增加了电极材料的导电性能来提升材料的容量和倍率循环性能。前驱体外二次包覆的碳包覆层不仅可以进一步缓冲纳米硅材料在充放电循环过程中的体积效应,防止电极的剥离脱落,而且可以降低前驱体的电化学阻抗和比表面积来提升电极材料的电化学性能和机械加工性能。本发明既为葛根残留物的循环再利用提供了全新技术路线,又解决了新型动力电池硅碳负极电极材料来源的问题。
48.本发明有益效果如下:
49.1)本发明以生产葛根粉时所残留的表皮、根须和过程残渣作为制备生物质基多孔硅碳复合材料的原料,原料价格便宜。所制得复合材料的机械加工性能和电化学性能可以满足动力电池电极材料的要求。
50.2)本发明既为葛根残留物的循环再利用提供了全新技术路线,又为新型动力电池硅碳复合负极电极材料探索出新的原材料和制备方法。
51.3)本发明中葛根残留物微粉具有优异的粘结性和包覆性能,可通过调节加热温度来控制微粉的溶胀,进而控制浆料的粘度,最终将纳米硅分散包覆形成三维多孔结构前驱体。在制备过程中葛根残留物微粉可被综合用作粘结剂、增稠剂和首次包覆剂,省去相关辅材的加入。
52.4)本发明以葛根残留物微粉中分布杂乱的纤维相互连接形成三维碳纤维骨架结构,其中的碳水化合物形成薄的部分石墨化包覆层将纳米硅粉分散包覆并桥接三维碳纤维骨架构建三维多孔结构。该结构有效地缓冲纳米硅材料的体积膨胀、缩短了锂离子的扩散路径、提高了锂离子的扩散速率,并通过微孔储锂和优异吸液性能提升了电极材料的容量和电化学性能。
53.本发明所提出的制备方法简单,过程容易控制,材料成本低。
附图说明
54.图1是实施例3制得的复合材料p
‑
c/si/c的x射线衍射谱图,
55.图2是葛根残留物微粉溶胀炭化后样品的sem图(1μm),
56.图3是葛根残留物微粉溶胀炭化后样品的sem图(500nm),
57.图4是实施例3制得的复合材料p
‑
c/si/c的sem图,
58.图5是实施例3制得的复合材料p
‑
c/si/c的tem图。
具体实施方式
59.下面结合实施例及对应附图对上述实施方式作进一步详细说明:
60.对本发明实施例的表征,用x射线衍射仪(smartlab,日本理学)在cu ka的辐射下,以10
°
/min的扫描速度下对所制备的材料进行组成和结构表征。用扫描电子显微镜(sem;verios g4 uc,fei,usa)和透射电子显微镜(tem;talos 200f,fei,usa)观察电极材料的形貌。用动态氮吸附表面分析仪(jw
‑
dx,精微高博,中国)测定电极材料的比表面积。
61.用实施例和对比例得到的电极材料进行半电池测试,将电极材料、导电剂炭黑sp、粘结剂pvdf按照质量比85:7:8制浆涂覆极片,用金属锂片做对比电极,山东海容电源材料股份有限公司的hr
‑
8315型电解液做电解液,celgard 2400做隔膜,在高纯氩气保护的德国布劳恩mbraun手套箱中,制成cr2025扣式实验电池。用武汉市蓝电电子股份有限公司的ct2001a型蓝点电池测试系统进行恒流充放电测试,充放电电压范围为0.003~2.0v(vs.li
+
/li),测得0.1c首次放电容量mah/g,首次效率%,分别在0.1c、0.2c和0.5c各充放电活化3周后进行1c充放电循环测试,循环50周后测得放电容量mah/g,并用第50周1c放电容量与第1周1c放电容量之比,计算得到1c大倍率下循环50周后的容量保持率%。
62.实施例1
63.生物质基多孔硅碳复合材料的制备方法,具体步骤为:
64.一、制备生物质基多孔硅碳复合前驱体(p
‑
c/si)
65.s1葛根残留物预处理:室温下,将葛根残留物表皮用洗洁精做清洗剂搅拌清洗去除表面沙砾和内部残留杂质,然后粉碎至粒径为3μm~5μm的微粉颗粒,并将粉碎后的葛根残留物粉末在水溶液中用提纯设备进一步清洗提纯,在温度为100℃的鼓风烘箱干燥12h,得到纯净葛根残留物微粉。
66.s2喷雾造粒:称取100g葛根残留物微粉和5g的30nm硅粉分散于乙醇溶液中,葛根残留物微粉和纳米硅粉的质量和为葛根残留物微粉、纳米硅粉、溶剂之和的10%,在200r/min转速下液相机械混合120min。将混合液转移至恒温水浴锅上,在50℃的温度和800r/min的转速下搅拌至葛根微粉溶胀,得到粘稠度为1000cp的混合浆料,将所得均匀混合浆料以20ml/min的进料速度,在进口温度为260℃,出口温度为120℃,喷雾造粒得到有溶胀孔洞的生物质基多孔硅碳复合样。
67.s3高温炭化:将生物质基多孔硅碳复合样置于高温气氛炉,在氮气流量为5l/min,以2℃/min的升温速度,升温至800℃,热解处理3h,自然冷却至室温,粉碎后过250目筛网,得到生物质基多孔硅碳复合前驱体(p
‑
c/si),生物质基多孔硅碳复合前驱体(p
‑
c/si)为薄的部分石墨化包覆层将纳米硅粉分散包覆并桥接三维碳纤维骨架结构形成三维多孔结构生物质基硅碳复合前驱体。
68.二、制备生物质基多孔硅碳复合材料(p
‑
c/si/c)
69.s4水热包覆:将生物质基多孔硅碳复合前驱体(p
‑
c/si)和蔗糖按质量比为1:1加入水中,生物质基多孔硅碳复合前驱体(p
‑
c/si)和蔗糖与水的固液质量比为1:20,超声分散30min转移至水热反应釜中,在150℃聚合24h,经离心,洗涤,干燥后得到二次包覆复合材料。
70.s5热解处理:将得到的二次包覆复合材料置于高温气氛炉,在氮气流量为5l/min,以2℃/min的升温速度,升温至800℃,热解处理3h,自然冷却至室温,粉碎后过250目筛网,得到生物质基多孔硅碳复合材料(p
‑
c/si/c)。
71.本实施例得到的生物质基多孔硅碳复合材料(p
‑
c/si/c)纳米硅粒子的尺寸为30nm,其质量占所述三维多孔硅碳复合材料质量的5%;
72.所述石墨化薄包覆碳层多空结构孔径为50nm~2μm,其质量占前驱体质量的60%;
73.所述二次包覆热解碳层的厚度为5~10nm,其质量为前驱体质量的5%。
74.对实施例1制得的复合样品进行物理性能和化学性能测试。复合材料粉体的比表面积为37.47m2·
g
‑1,振实密度为0.68g
·
cm
‑1,0.1c的首次放电容量为432.1mah g
‑1,首次效率为77.5%。在1c的大倍率下循环50周后容量保持有210.5mah g
‑1,容量保持率为70.7%。测试结果汇总见表1。
75.实施例2
76.生物质基多孔硅碳复合材料的制备方法,具体步骤为:
77.一、制备生物质基多孔硅碳复合前驱体(p
‑
c/si)
78.s1葛根残留物预处理:室温下,将葛根残留物根须用洗洁精做清洗剂搅拌清洗去除表面沙砾和内部残留杂质,然后粉碎至粒径为3~5μm的微粉颗粒,并将粉碎后的葛根残留物粉末在水溶液中用提纯设备进一步清洗提纯,经真空抽滤机物理提纯和干燥处理后,得到纯净葛根残留物微粉。
79.s2喷雾造粒:称取100g葛根残留物微粉和30g的100nm硅粉分散于甲醇溶液中,葛根残留物微粉和纳米硅粉的质量和为葛根残留物微粉、纳米硅粉、溶剂之和的40%,在600r/min转速下液相机械混合110min。将混合液转移至恒温水浴锅上,在80℃的温度和700r/min的转速下搅拌至葛根微粉溶胀,得到粘稠度为1300cp的混合浆料,将所得均匀混合浆料以30ml/min的进料速度,在进口温度为240℃,出口温度为130℃,喷雾造粒得到有溶胀孔洞的生物质基多孔硅碳复合样。
80.s3高温炭化:将生物质基多孔硅碳复合样置于高温气氛炉,在氩气流量为6l/min,以3℃/min的升温速度,升温至850℃,热解处理3.5h,自然冷却至室温,粉碎后过150目筛网,得到生物质基多孔硅碳复合前驱体(p
‑
c/si),所述生物质基多孔硅碳复合前驱体(p
‑
c/si)为薄的部分石墨化包覆层将纳米硅粉分散包覆并桥接三维碳纤维骨架结构形成三维多孔结构生物质基硅碳复合前驱体。
81.二、制备生物质基多孔硅碳复合材料(p
‑
c/si/c)
82.s4水热包覆:将生物质基多孔硅碳复合前驱体(p
‑
c/si)和葡萄糖按质量比为1:1.5加入水中,生物质基多孔硅碳复合前驱体(p
‑
c/si)和葡萄糖与水的固液比质量为1:30,超声分散30min转移至水热反应釜中,在160℃聚合18h,经离心,洗涤,干燥后得到二次包覆复合材料。
83.s5热解处理:将得到的二次包覆复合材料置于高温气氛炉,在氩气流量为6l/min,以3℃/min的升温速度,升温至850℃,热解处理3.5h,自然冷却至室温,粉碎后过150目筛网,得到生物质基多孔硅碳复合材料(p
‑
c/si/c)。
84.本实施例得到的生物质基多孔硅碳复合材料(p
‑
c/si/c)纳米硅粒子的尺寸为100nm,其质量占所述三维多孔硅碳复合材料质量的30%;
85.所述石墨化薄包覆碳层多空结构孔径为100nm~5μm,其质量占前驱体质量的50%;
86.所述二次包覆热解碳层的厚度为10~15nm,其质量为前驱体质量的8%。
87.对实施例2制得的复合样品进行物理性能和化学性能测试。复合材料粉体的比表面积为38.96m2·
g
‑1,振实密度为0.70g
·
cm
‑1,0.1c的首次放电容量为1073.2mah g
‑1,首次效率为73.3%。在1c的大倍率下循环50周后容量保持有512.5mah g
‑1,容量保持率为63.5%。测试结果汇总见表1。
88.实施例3
89.生物质基多孔硅碳复合材料的制备方法,具体步骤为:
90.一、制备生物质基多孔硅碳复合前驱体(p
‑
c/si)
91.s1葛根残留物预处理:室温下,将葛根残留物过程残渣用洗洁精做清洗剂搅拌清洗去除表面沙砾和内部残留杂质,然后粉碎至粒径为3~5μm的微粉颗粒,并将粉碎后的葛根残留物粉末在水溶液中用提纯设备进一步清洗提纯,经离心机物理提纯和干燥处理后,得到纯净葛根残留物微粉。
92.s2喷雾造粒:称取100g葛根残留物微粉和20g的100nm硅粉分散于异丙醇溶液中,葛根残留物微粉和纳米硅粉的质量和为葛根残留物微粉、纳米硅粉、溶剂之和的35%,在700r/min转速下液相机械混合100min。将混合液转移至磁力搅拌器上,在100℃的温度和800r/min的转速下搅拌至葛根微粉溶胀,得到粘稠度为1350cp的混合浆料,所得均匀混合浆料以40ml/min的进料速度,在进口温度为250℃,出口温度为140℃,喷雾造粒得到有溶胀孔洞的生物质基多孔硅碳复合样。
93.s3高温炭化:将生物质基多孔硅碳复合样置于高温气氛炉,在氮气气流量为7l/min,以4℃/min的升温速度,升温至900℃,热解处理4h,自然冷却至室温,粉碎后过200目筛网,得到生物质基多孔硅碳复合前驱体(p
‑
c/si),所述生物质基多孔硅碳复合前驱体(p
‑
c/si)为薄的部分石墨化包覆层将纳米硅粉分散包覆并桥接三维碳纤维骨架结构形成三维多孔结构生物质基硅碳复合前驱体。
94.二、制备生物质基多孔硅碳复合材料(p
‑
c/si/c)
95.s4水热包覆:将生物质基多孔硅碳复合前驱体(p
‑
c/si)和水溶性酚醛树脂按质量比为1:2加入水中,生物质基多孔硅碳复合前驱体(p
‑
c/si)和水溶性酚醛树脂与水的固液质量比为1:20,超声分散30min转移至水热反应釜中,在170℃聚合16h,经离心,洗涤,干燥后得到二次包覆复合材料。
96.s5热解处理:将得到的二次包覆复合材料置于高温气氛炉,在氮气气流量为7l/min,以4℃/min的升温速度,升温至900℃,热解处理4h,自然冷却至室温,粉碎后过200目筛网,得到生物质基多孔硅碳复合材料(p
‑
c/si/c)。
97.本实施例得到的生物质基多孔硅碳复合材料(p
‑
c/si/c)纳米硅粒子的尺寸为
100nm,其质量占所述三维多孔硅碳复合材料质量的20%;
98.所述石墨化薄包覆碳层多空结构孔径为100nm~5μm,其质量占前驱体质量的60%;
99.所述二次包覆热解碳层的厚度为12~14nm,其质量为前驱体质量的12%。
100.对实施例3制得的复合样品进行物理性能和化学性能测试。复合材料粉体的比表面积为30.72m2·
g
‑1,振实密度为0.75g
·
cm
‑1,0.1c的首次放电容量为739.8mah g
‑1,首次效率为78.8%。在1c的大倍率下循环50周后容量保持有411.7mah g
‑1,容量保持率为75.2%。测试结果汇总见表1。
101.如图1所示,实施例3制得的复合材料p
‑
c/si/c的x射线衍射谱图,通过与相应的标准pdf卡片对比发现,在23.2
°
和43.5
°
附近观察到的衍射峰,分别对应于生物质基多孔碳材料的(002)和(101)晶面,而在28.4
°
,47.3
°
,56.1
°
,69.1
°
和76.4
°
处观察到的衍射峰分别对应于与晶体硅(pdf卡片号:27
‑
1402)的(111),(220),(311),(400)和(331)晶面。
102.通过xrd图谱分析可以发现制备得到的复合材料主要成分为碳材料和硅。
103.如图2、图3所示,葛根残留物微粉溶胀炭化后样品的sem图,葛根残留物微粉经溶胀和高温烧结后,其内部分布杂乱的纤维相互连接形成三维碳纤维骨架结构,而碳水化合物形成薄的部分石墨化包覆层将三维碳纤维骨架串联包裹并形成三维多孔碳材料,孔径大小为100nm~5μm。
104.如图4、图5所示,分别为实施例3制得的复合材料p
‑
c/si/c的sem图像和tem图像,葛根残留物微粉利用其优异的溶胀性能和粘结性能,将纳米硅粉均匀分散包覆并桥接植物纤维形成的三维碳纤维骨架得到生物质基多孔硅碳复合前驱体,前驱体经有机碳源形成的无定形碳层均匀二次包覆,包覆层厚度约为12~14nm。这说明已经按照预想将纳米硅分散在多孔碳材料中,并将有机碳层很好地包覆在表层。
105.实施例4
106.生物质基多孔硅碳复合材料的制备方法,具体步骤为:
107.一、制备生物质基多孔硅碳复合前驱体(p
‑
c/si)
108.s1葛根残留物预处理:将葛根残留物表皮、根须和过程残渣按质量比1:1:1混合后用洗洁精做清洗剂搅拌清洗去除表面沙砾和内部残留杂质,然后粉碎至粒径为3~5μm的微粉颗粒,并将粉碎后的葛根残留物粉末在水溶液中用提纯设备进一步清洗提纯,经离心机物理提纯和干燥处理后,得到纯净葛根残留物微粉。
109.s2喷雾造粒:称取100g葛根残留物微粉和20g的100nm硅粉分散于乙醇溶液中,葛根残留物微粉和纳米硅粉的质量和为葛根残留物微粉、纳米硅粉、溶剂之和的40%,在900r/min转速下液相机械混合80min。将混合液转移至恒温油浴锅上,在110℃的温度和500r/min的转速下搅拌至葛根微粉溶胀,得到粘稠度为1300cp的混合浆料,所得均匀混合浆料以45ml/min的进料速度,在进口温度为225℃,出口温度为160℃,喷雾造粒得到有溶胀孔洞的生物质基多孔硅碳复合样。
110.s3高温炭化:将生物质基多孔硅碳复合样置于高温气氛炉,在氩气气流量为8l/min,以5℃/min的升温速度,升温至950℃,热解处理4.5h,自然冷却至室温,粉碎后过200目筛网,得到生物质基多孔硅碳复合前驱体(p
‑
c/si),所述生物质基多孔硅碳复合前驱体(p
‑
c/si)为薄的部分石墨化包覆层将纳米硅粉分散包覆并桥接三维碳纤维骨架结构形成三维
多孔结构生物质基硅碳复合前驱体。
111.二、制备生物质基多孔硅碳复合材料(p
‑
c/si/c)
112.s4水热包覆:将生物质基多孔硅碳复合前驱体(p
‑
c/si)和聚乙烯醇按质量比为1:2.5加入水中,生物质基多孔硅碳复合前驱体(p
‑
c/si)和聚乙烯醇与水的固液质量比为2:40,超声分散30min转移至水热反应釜中,在180℃聚合14h,经离心,洗涤,干燥后得到二次包覆复合材料。
113.s5热解处理:将得到的二次包覆复合材料置于高温气氛炉,在氩气气流量为8l/min,以5℃/min的升温速度,升温至950℃,热解处理4.5h,自然冷却至室温,粉碎后过200目筛网,得到生物质基多孔硅碳复合材料(p
‑
c/si/c)。
114.本实施例得到的生物质基多孔硅碳复合材料(p
‑
c/si/c)纳米硅粒子的尺寸为100nm,其质量占所述三维多孔硅碳复合材料质量的20%;
115.所述石墨化薄包覆碳层多空结构孔径为80nm~3.5μm,其质量占前驱体质量的55%;
116.所述二次包覆热解碳层的厚度为10~12nm,其质量为前驱体质量的10%。
117.对实施例4制得的复合样品进行物理性能和化学性能测试。复合材料粉体的比表面积为34.35m2·
g
‑1,振实密度为0.72g
·
cm
‑1,0.1c的首次放电容量为728.4mah g
‑1,首次效率为75.9%。在1c的大倍率下循环50周后容量保持有406.9mah g
‑1,容量保持率为72.5%。测试结果汇总见表1。
118.实施例5
119.生物质基多孔硅碳复合材料的制备方法,具体步骤为:
120.一、制备生物质基多孔硅碳复合前驱体(p
‑
c/si)
121.s1葛根残留物预处理:室温下,将葛根残留物表皮、根须和过程残渣按质量比1:1:1混合后用洗洁精做清洗剂搅拌清洗去除表面沙砾和内部残留杂质,然后粉碎至粒径为3~5μm的微粉颗粒,并将粉碎后的葛根残留物粉末在水溶液中用提纯设备进一步清洗提纯,经离心机物理提纯和干燥处理后,得到纯净葛根残留物微粉。
122.s2喷雾造粒:称取100g葛根残留物微粉和20g的100nm硅粉分散于甲醇和乙醇溶液的混合溶液中,葛根残留物微粉和纳米硅粉的质量和为葛根残留物微粉、纳米硅粉、溶剂之和的40%,在1000r/min转速下液相机械混合60min。将混合液转移至磁力搅拌器上,在120℃的温度和700r/min的转速下搅拌至葛根微粉溶胀,得到粘稠度为1500cp的混合浆料,所得均匀混合浆料以50ml/min的进料速度,在进口温度为180℃,出口温度为130℃,喷雾造粒得到有溶胀孔洞的生物质基多孔硅碳复合样。
123.s3高温炭化:将生物质碳基硅复合样置于高温气氛炉,在氮气气流量为9l/min,以5℃/min的升温速度,升温至850℃,热解处理3.5h,自然冷却至室温,粉碎后过200目筛网,得到生物质基多孔硅碳复合前驱体(p
‑
c/si),所述生物质基多孔硅碳复合前驱体(p
‑
c/si)为薄的部分石墨化包覆层将纳米硅粉分散包覆并桥接三维碳纤维骨架结构形成三维多孔结构生物质基硅碳复合前驱体。
124.二、制备生物质基多孔硅碳复合材料(p
‑
c/si/c)
125.s4水热包覆:将生物质基多孔硅碳复合前驱体(p
‑
c/si)和聚乙二醇按质量比为1:3加入水中,生物质基多孔硅碳复合前驱体(p
‑
c/si)和聚乙二醇与水的固液质量比为2:30,
超声分散30min转移至水热反应釜中,在190℃聚合12h,经离心,洗涤,干燥后得到二次包覆复合材料。
126.s5热解处理:将得到的二次包覆复合材料置于高温气氛炉,在氮气气流量为9l/min,以5℃/min的升温速度,升温至850℃,热解处理3.5h,自然冷却至室温,粉碎后过200目筛网,得到生物质基多孔硅碳复合材料(p
‑
c/si/c)。
127.本实施例得到的生物质基多孔硅碳复合材料(p
‑
c/si/c)纳米硅粒子的尺寸为100nm,其质量占所述三维多孔硅碳复合材料质量的20%;
128.所述石墨化薄包覆碳层多空结构孔径为70nm~3.0μm,其质量占前驱体质量的53%;
129.所述二次包覆热解碳层的厚度为10~15nm,其质量为前驱体质量的15%。
130.对实施例5制得的复合样品进行物理性能和化学性能测试。复合材料粉体的比表面积为36.28m2·
g
‑1,振实密度为0.71g
·
cm
‑1,0.1c的首次放电容量为716.5mah g
‑1,首次效率为76.8%。在1c的大倍率下循环容量保持有397.6mah g
‑1,容量保持率为71.2%。测试结果汇总见表1。
131.对比例1
132.选用普通碳材料作为原材料制备硅碳复合材料,具体步骤为:
133.一、制备硅碳复合前驱体(c/si)
134.s1喷雾造粒:称取100g平均粒径d50为8.0的天然球型石墨和20g的100nm硅粉分散于异丙醇溶液中,加入50g包覆剂聚乙二醇和5g粘结剂羧甲基纤维素,其中,天然石墨、纳米硅粉、聚乙二醇和羧甲基纤维素的质量和为所有溶质和溶剂之和的35%,在700r/min转速下液相机械混合100min。得到粘稠度为1350cp的混合浆料,所得均匀混合浆料以40ml/min的进料速度,在进口温度为250℃,出口温度为140℃,喷雾造粒得到硅碳复合样。
135.s2高温炭化:将硅碳复合样置于高温气氛炉,在氮气气流量为7l/min,以4℃/min的升温速度,升温至900℃,热解处理4h,自然冷却至室温,粉碎后过200目筛网,得到硅碳复合前驱体(c/si)。
136.二、制备硅碳复合材料(c/si/c)
137.s3水热包覆:将硅碳复合前驱体(c/si)和水溶性酚醛树脂按质量比为1:2加入水中,硅碳复合前驱体(c/si)和水溶性酚醛树脂与水的固液质量比为1:20,超声分散30min转移至水热反应釜中,在170℃聚合16h,经离心,洗涤,干燥后得到二次包覆复合材料。
138.s4热解处理:将得到的二次包覆复合材料置于高温气氛炉,在氮气气流量为7l/min,以4℃/min的升温速度,升温至900℃,热解处理4h,自然冷却至室温,粉碎后过200目筛网,得到硅碳复合材料(c/si/c)。
139.本对比例得到的硅碳复合材料(c/si/c)纳米硅粒子的尺寸为100nm,其质量占所述硅碳复合材料质量的20%;
140.所述复合材料表面未检测到微孔结构。
141.所述二次包覆热解碳层的厚度为10~12nm,其质量为前驱体质量的12%。
142.对对比例1制得的复合样品进行物理性能和化学性能测试。复合材料粉体的比表面积为4.65m2·
g
‑1,振实密度为0.91g
·
cm
‑1,0.1c的首次放电容量为786.5mah g
‑1,首次效率为80.6%。在1c的大倍率下循环容量保持有340.6mah g
‑1,容量保持率为65.3%。测试结
果汇总见表1。
143.对比例2
144.选用玉米芯微粉作为生物质原材料制备生物质基多孔硅碳复合材料,具体步骤为:
145.一、制备生物质基多孔硅碳复合前驱体(p
’‑
c/si)
146.s1玉米芯预处理:室温下,将玉米棒脱粒后的玉米芯用洗洁精做清洗剂搅拌清洗去除表面沙砾和内部残留杂质,然后粉碎至粒径为3~5μm的微粉颗粒,并将粉碎后的玉米芯粉末在水溶液中用提纯设备进一步清洗提纯,经离心机物理提纯和干燥处理后,得到纯净玉米芯微粉。
147.s2喷雾造粒:称取100g粒径为3~5μm的玉米芯微粉和20g的100nm硅粉分散于异丙醇溶液中,葛根残留物微粉和纳米硅粉的质量和为葛根残留物微粉、纳米硅粉、溶剂之和的35%,在700r/min转速下液相机械混合100min。将混合液转移至磁力搅拌器上,在100℃的温度和800r/min的转速下搅拌,并加入黏结剂羧甲基纤维素调节浆料粘稠度,得到粘稠度为1350cp的混合浆料,所得均匀混合浆料以40ml/min的进料速度,在进口温度为250℃,出口温度为140℃,喷雾造粒得到生物质基硅碳复合样。
148.s3高温炭化:将生物质基硅碳复合样置于高温气氛炉,在氮气气流量为7l/min,以4℃/min的升温速度,升温至900℃,热解处理4h,自然冷却至室温,粉碎后过200目筛网,得到生物质基多孔硅碳复合前驱体(p
’‑
c/si)。
149.二、制备生物质基多孔硅碳复合材料(p
’‑
c/si/c)
150.s4水热包覆:将生物质基多孔硅碳复合前驱体(p
’‑
c/si)和水溶性酚醛树脂按质量比为1:2加入水中,生物质基多孔硅碳复合前驱体(p
’‑
c/si)和水溶性酚醛树脂与水的固液质量比为1:20,超声分散30min转移至水热反应釜中,在170℃聚合16h,经离心,洗涤,干燥后得到二次包覆复合材料。
151.s5热解处理:将得到的二次包覆复合材料置于高温气氛炉,在氮气气流量为7l/min,以4℃/min的升温速度,升温至900℃,热解处理4h,自然冷却至室温,粉碎后过200目筛网,得到生物质基多孔硅碳复合材料(p
’‑
c/si/c)。
152.本对比例得到的生物质基多孔硅碳复合材料(p
’‑
c/si/c)纳米硅粒子的尺寸为100nm,其质量占所述多孔硅碳复合材料质量的20%;
153.所述石墨化薄包覆碳层多空结构孔径为30nm~200nm,孔结构孔径较小,其质量占前驱体质量的40%;
154.所述二次包覆热解碳层的厚度为10~13nm,其质量为前驱体质量的12%。
155.对对比例2制得的复合样品进行物理性能和化学性能测试。复合材料粉体的比表面积为33.54m2·
g
‑1,振实密度为0.65g
·
cm
‑1,0.1c的首次放电容量为719.7mah g
‑1,首次效率为70.5%。在1c的大倍率下循环50周后容量保持有330.9mah g
‑1,容量保持率为60.1%。测试结果汇总见表1。
156.表1实施例与对比例样品的物理性能和化学性能测试结果
[0157][0158]
最后应说明的是:以上实施例仅用以说明本发明的技术方案,而非对其限制;尽管参照前述实施例对本发明进行了详细的说明,本领域的普通技术人员应当理解:其依然可以对前述实施例所记载的技术方案进行修改,或者对其中部分或者全部技术特征进行等同替换;而这些修改或者替换,并不使相应技术方案的本质脱离本发明实施例技术方案的范围。