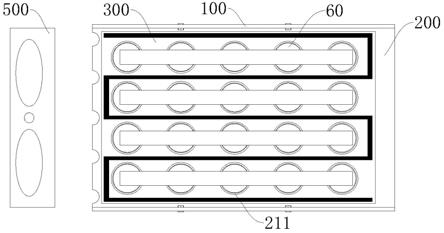
1.本发明涉及动力电池热管理技术领域,特别是涉及一种动力电池热管理装置。
背景技术:2.动力电池中锂离子电池能量密度高,体积小,循环寿命较长,在电动乘用车、商务车上应用潜力很大。而电池的工作温度,无论低温还是高温都是影响电池使用性能和循环性能的关键因素。
3.电池在工作过程中由于内部电化学反应产热以及焦耳热会导致温度上升,当电池超过适宜的温度时会影响电池的使用性能和循环寿命,严重地甚至会引起热失控,导致自燃、爆炸等事故。例如常规的三元锂正极材料电池温度需要控制在50摄氏度以内、电池温差在5摄氏度范围,以避免电池劣化加剧、甚至产生热失控和起火爆炸,提高安全性。而磷酸铁锂为正极材料的电池工作温度虽然可以提升到60摄氏度,但随着温度进一步上升,电池容量衰减明显,在高温下仍然会发生热失控和着火现象。
4.因此传统的电池中缺乏对温度进行管理的装置,导致电池在极端环境下性能变差,例如当电池温度较高时,电池更易发生热损害和热失控。而当温度较低时,电池内部电解液粘度增大,容易导致锂沉积形成锂枝晶,使得电池容量下降,严重时锂枝晶会刺破隔膜发生内短路,发生热失控事故。
技术实现要素:5.基于此,有必要针对传统电池缺乏温度管理装置,在极端环境下性能变差的问题,提供一种能够对电池温度进行控制的动力电池热管理装置。
6.一种动力电池热管理装置,包括箱体、热扩散板和加热部件;
7.所述热扩散板安装在所述箱体内,所述热扩散板上具有多个贯通的套筒,所述套筒用于嵌套电池并与所述电池进行热交换;
8.所述加热部件呈薄膜状,并贴合在热扩散板的表面,所述加热部件上间隔开设尺寸大于套筒的套接孔,所述套接孔套接在对应套筒上。
9.进一步的,所述热扩散板上具有多个贯穿孔,所述套筒由所述贯穿孔的内壁沿所述贯穿孔的轴向延展而成。
10.进一步的,所述套筒内壁设有导热层。
11.进一步的,所述热扩散板上间隔安装有多组扰流柱,所述加热部件表面间隔开设有多组套接孔,所述套接孔套接在扰流柱上。
12.进一步的,所述热扩散板表面和所述加热部件表面对应开设有多组间隔设置的通孔。
13.进一步的,所述加热部件的加热单元呈串联或并联穿设在各电池之间。
14.进一步的,所述加热单元穿设在各电池之间部分的宽度是外缘部分宽度的一半。
15.进一步的,所述加热单元围绕套接孔或扰流柱弯曲连接。
16.进一步的,所述箱体相对的两侧壁上开设有进风口和排风口,所述进风口和所述排风口内安装有风扇,且风扇与热扩散板之间留有间隔。
17.进一步的,所述热扩散板前端设有弧形开口,所述弧形开口对应电池之间间隔,用于风扇旋转鼓风、引流和辅助分配流量。
18.上述动力电池热管理装置,通过在箱体内安装热扩散板,并将热扩散板套装在多组电池上,在电池高温时通过空气流通对电池进行降温,在电池处于低温时热扩散板表面的加热部件对电池进行升温,本方法既能对高温电池进行降温、也能对低温电池有效加热,具有双向调温功能,具有优良的热管理性能。
附图说明
19.图1为动力电池热管理装置的结构示意图;
20.图2为通孔的结构示意图;
21.图3为贯穿孔的结构示意图;
22.图4为扰流柱的结构示意图;
23.图5为加热单元串联的结构示意图;
24.图6为加热单元并联的结构示意图;
25.图7为加热单元弯曲部分的结构示意图;
26.图8为未均衡温度下温度轮廓的平面模拟图;
27.图9为未均衡温度下温度轮廓的立体模拟图;
28.图10为未均衡温度下模组中心电池温升曲线图;
29.图11为均衡温度下温度轮廓的平面模拟图;
30.图12为均衡温度下温度轮廓的立体模拟图;
31.图13为均衡温度下1
‑
5号电池温升曲线图。
32.图中:100、箱体;200、热扩散板;210、贯穿孔;211、套筒;220、通孔;300、加热部件;310、绝缘膜;311、套接孔;320、加热单元;400、扰流柱;500、风扇;60、电池。
具体实施方式
33.为使本发明实施例的目的、技术方案和优点更加清楚,下面将结合本发明实施例中的附图,对本发明实施例中的技术方案进行清楚、完整地说明,显然,所描述的实施例是本发明一部分实施例,而不是全部的实施例。基于本发明中的实施例,本领域普通技术人员在没有做出创造性劳动前提下所获得的所有其他实施例,都属于本发明保护的范围。
34.如图1所示,在一个实施例中,一种动力电池热管理装置,包括箱体100、热扩散板200和加热部件300。热扩散板200安装在箱体100内,热扩散板200上具有多个贯通的套筒211,套筒211用于嵌套电池60并与电池60进行热交换,加热部件300呈薄膜状,并贴合在热扩散板200的表面,加热部件300上间隔开设尺寸大于套筒的套接孔,套接孔套接在对应套筒211上。
35.上述动力电池热管理装置,通过在箱体100内安装热扩散板200,并将热扩散板200套装在多组电池60上,在电池60高温时通过空气流通对电池60进行降温,在电池60处于低温时热扩散板200表面的加热部件300对电池60进行升温,本方法既能对高温电池60进行降
温、也能对低温电池60有效加热,具有双向调温功能,具有优良的热管理性能。
36.在实际使用中,箱体100内可间隔布置多组电池60,且电池60可以为多棱柱或圆柱形状,可采用铝塑软包等不同包装形式。箱体100通过空气冷却,箱体100材料为金属铝,并带有加强筋。加强筋不仅增大箱体100的机械强度和耐冲击性,也增加了箱体100的表面积,加速箱体100表面的传热作用。
37.如图2所示,在本实施例中,箱体100内至少安装一组热扩散板200,同时,为了进一步降低箱体100内温升和温度梯度,可以在箱体100内安装多层热扩散板200。热扩散板200的边缘紧贴箱体100内壁,热扩散板200的边缘折弯,并可通过螺栓与箱体100相连,起到密封和定位作用。
38.在材料选择上,热扩散板200可采用铝、铜、钛、铁等高导热率金属板,其厚度取值范围在0.5mm
‑
5mm,不仅导热效率高,并且易于加工。其表面带有经阳极氧化钝化处理后,具有电绝缘强度的氧化膜层,阳极氧化后的铝或其合金,提高了硬度和耐磨性,具有优良的电绝缘性。
39.上述热扩散板200一方面可增加对流换热面积,从而降低最高温差,另一方面,热扩散板200采用导热系数较高的材料如铝、铜、钛等制成,具有反向导热能力,能够降低电池60上游和下游之间的温差,提高电池60温度均匀性。
40.如图3所示,在本实施例中,热扩散板200上具有多个贯穿孔210,套筒211由贯穿孔210的内壁沿贯穿孔210的轴向延展而成。此设置为单向套筒211,而在使用中还可将套筒211设置为双向,其方法是将双层结构进行拆解,一部分做整体加工,另一部分进行焊接组合。
41.上述热扩散板200上的贯穿孔210内缘由机加工或者冲压工艺加工形成套筒211结构,可增大热扩散板200和电池60之间的导热面积,提高机械稳定性和导热效率。
42.在本实施例中,套筒211内壁设有导热层。其导热层为以聚氨酯、有机硅、环氧树脂或丙烯酸为基体,导热率不小于0.2w/mk的导热粘接胶层。一是保证套筒211和电池60之间的导热接触面充分,避免局部区域因加工、装配等原因形成的空隙造成的导热中空带,减小接触热阻。
43.在本实施例中,热扩散板200表面和加热部件300表面对应开设有多组间隔设置的通孔220。可降低风阻,平衡热扩散板200上下两侧的风量。
44.上述热扩散板200上的通孔220和套筒211可在cnc中一体加工,多层热扩散板200上的通孔220和套筒211可分层在cnc中一体加工,再经焊接成整体,套筒211可朝上或者朝下,结构简单,利于加工。
45.如图4所示,在本实施例中,热扩散板200上间隔安装有多组扰流柱400。且扰流柱400贯穿热扩散板200,扰流柱400的两端分别位于热扩散板200上下方的不同空间内。
46.在实际使用中,扰流柱400的截面不做具体限制,其可以为圆形、方形、菱形或星型。一方面可以增大换热面积,另一方面可以增强空气的紊流流动换热特性,提高对流换热系数,降低电池60的最高温度。
47.如图5、图6和图7所示,在本实施例中,加热部件300包括加热单元320和绝缘膜310;加热单元320夹在两组绝缘膜310之间,绝缘膜310和加热单元320表面间隔对应开设有多组套接孔311,套接孔311套接在扰流柱400上,加热单元320呈串联或并联穿设在各电池
60之间,加热单元320穿设在各电池60之间部分的宽度是外缘部分宽度的一半,并且加热单元320围绕套接孔311或扰流柱400弯曲连接,即加热单元320在靠近套接孔311或扰流柱400的位置呈弯曲设置,以避过套接孔311或扰流柱400。
48.具体的,加热单元320可采用导电膜片,绝缘膜310可采用聚醯亚胺膜,两层聚醯亚胺膜压合一层导电膜式通电后导电膜片产生焦耳热,将热量经热扩散板200和套筒211传导给电池60,对电池60进行快速加热。而且导电膜片厚度通常在几十微米到200微米范围之内,加热效率基本上100%,加热速度快,能实现快速调节温度功能。
49.由于电池外缘加热单元仅加热一侧电池,升温所需要的加热量比内部低,为保证电池外缘与内部升温速率接近,通过调整加热部件300中不同位置处导电膜片的宽度,而导电膜片的厚度在加工中都保持一致,使导电膜片产生的焦耳热不同,其中电池60模组内部导电膜片的宽度较小、电阻大、产生的焦耳热较大,而边缘导电膜片宽度较大、电阻较小,产热量较小,以保证边缘电池60温度与内部温度大致相同,促进加热部件300温度分布更均匀,对电池60模组加热也更均匀,提高了电池60使用寿命与可靠性。
50.在本实施例中,箱体100相对的两侧壁上开设有进风口和排风口,进风口和排风口内安装有风扇500,且风扇500与热扩散板200之间留有间隔。此处以风扇500安装在排风口为宜,可降低热扩散板200尾端的回流效应,还可避免冷风直吹电池60,减少电池60温度的不均匀度,两者相互配合以形成强制对流的主动式风冷散热结构。
51.热扩散板前端设有弧形开口,弧形开口对应电池之间间隔,用于风扇旋转鼓风、引流和辅助分配流量。
52.上述动力电池热管理装置通过开设进风口和排风口形成强制对流风道,添加扰流柱400、通风孔等散热手段,进一步加强了散热效果。由于加热部件300采用薄型设计,厚度薄,热阻小,基本不影响该侧面的风冷散热能力。加热与强制对流散热功能实现简单、成本低:热扩散板200结构加工容易,成本低,具有较好的韧性、更低的硬度,在受到冲击时弯曲变形可吸收应力,缓冲对电池60撞击强度,适用于动力电池60系统,而加热膜片本身为轻质柔性结构,可大规模制备生产,不改变电池60模组结构与成组效率,具有优异的加工、生产性能。
53.具体的,进风口上配置的风扇500是离心式鼓风扇,排风口上配置的风扇500是轴流式排风扇,以加强空气对流效果。
54.如图8和图9所示,在计算机数值模拟过程中,热扩散板200材料为铝合金6061、电池模组底部材料为绝缘橡胶,热扩散板200厚度为4.5mm,电池60型号为18650锂电池60(其中18表示直径为18mm,65表示长度为65mm,0表示为电池60)未均衡产温度的加热部件300发热功率对应电池60的温升速率3℃/min发热情况,发热量为46w,环境温度为0℃。
55.模拟结果:在0℃环境下,未均衡产温度的加热部件300设置的功率对应电池60的温升速率为3℃/min,对电池60加热600s后,热扩散板200和电池模组的温度云图。
56.如图10所示,未均衡产温度的加热部件300的加热功率对应电池60温升速率3℃/min升温速率,环境温度为0℃时,电池模组中不同电池60对应的温升与仿真结果相接近,最大偏差在3.28%,相关电池60序号排布如图5所示,但是其中导电膜片的宽度不做区别设置。
57.实验结果:在0℃环境下,未均衡产温度的加热部件300设置的功率对应电池60的
温升速率为3℃/min,对电池60加热600s后,对应电池60的体平均温度。
58.如图11和图12所示,在计算机数值模拟过程中,热扩散板200材料为铝合金6061、电池60模组底部材料为电绝缘材料,热扩散板200厚度为4.5mm,电池60型号为18650锂电池60(其中18表示直径为18mm,65表示长度为65mm,0表示为电池60)均衡产温度的加热部件300发热功率对应电池60温升速率3℃/min发热情况,发热量为46w,环境温度为0℃。
59.模拟结果:在0℃环境下,均衡产温度的加热部件300设置的功率对应电池60的温升速率为3℃/min,对电池60加热600s后,热扩散板200和电池模组的温度云图。
60.如图13所示为热管理实验测试结果:在24.5
±
0.5℃环境下和强制风冷时,电池模组3c放电倍率下的温升。
61.当电池模组在3c放电倍率且1.0m/s风速下,电池模组的最高温升为12.9℃,最高温度在37.4℃,放电结束时的最大温差在2.83℃,满足电池模组热管理要求。相关电池60序号排布如图5所示,但是其中导电膜片的宽度不做区别设置。
62.以上所述实施例仅表达了本发明的几种实施方式,其描述较为具体和详细,但并不能因此而理解为对本发明专利范围的限制。应当指出的是,对于本领域的普通技术人员来说,在不脱离本发明构思的前提下,还可以做出若干变形和改进,这些都属于本发明的保护范围。因此,本发明专利的保护范围应以所附权利要求为准。