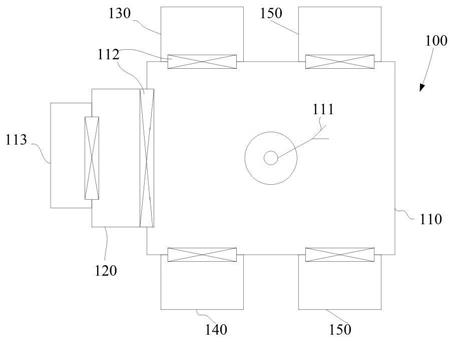
1.本发明涉及半导体领域,特别涉及一种半导体外延结构及其应用。
背景技术:2.氮化镓(gan)是宽禁带材料,电阻率高,氮化镓基二极管芯片在生产、运送过程中产生的静电电荷不易消失,累积到一定程度可以产生很高的静电电压。蓝宝石衬底的二极管芯片正负电极位于芯片同一侧,间距很小,因此对静电的承受能力很小,极易被静电击穿失效,影响器件的寿命。
3.氮化镓基二极管的半导体外延结构的有源区采用gan/ingan量子阱垒区,但由于gan/algan两种材料的晶格常数不同,容易产生极化效应,引起位错缺陷,如果这种缺陷得不到有效控制,穿过gan/ingan量子阱垒区的线位错会导致大量表面缺陷,形成漏电通道,表面缺陷也影响发光层两侧的半导体层内离子掺杂的效率,进而影响影响空穴浓度,影响芯片发光效率。
技术实现要素:4.鉴于上述现有技术的缺陷,本发明提出一种半导体外延结构及其应用,旨在改善有源层的发光质量,以及半导体层内离子的掺杂效率,进而提升二极管芯片的发光效率。
5.为实现上述目的及其他目的,本发明提出一种半导体设备,该半导体外延结构包括:
6.衬底;
7.第一半导体层,设置在所述衬底上;
8.有源层,设置在所述第一半导体层上;
9.第二半导体层,设置在所述有源层上;以及
10.空穴注入层,设置在所述第二半导体层上,且所述空穴注入层包括非或低掺杂的氮化镓层,和/或掺杂的氮化镓层。
11.可选的,所述空穴注入层包括第一掺杂层和第二掺杂层,所述第二掺杂层位于所述第一掺杂层上,且所述第一掺杂层的掺杂浓度小于所述第二掺杂层的掺杂浓度。
12.可选的,所述第一掺杂层具有第一掺杂浓度,所述第一掺杂浓度的范围为0~1
×
1019atom/cm3。
13.可选的,所述第二掺杂层具有第二掺杂浓度,所述第二掺杂浓度的范围为0~1
×
1019atom/cm3。
14.可选的,所述第二半导体层具有第三掺杂浓度,且所述第三掺杂浓度小于所述第二掺杂浓度。
15.可选的,所述第一掺杂层的厚度为所述第二掺杂层厚度的40%~50%。
16.可选的,所述空穴注入层还包括第三掺杂层,且所述第三掺杂层位于所述第二掺杂层上,且所述第三掺杂层的浓度大于所述第二掺杂层的掺杂浓度。
17.可选的,所述空穴注入层包括inx1gay1n、inx2gay2n和inx3gay3n,且x3<x2<x1≤1。
18.可选的,所述空穴注入层包括交替的inx1gay1n与inx2gay2n的n个周期循环,且n≥1,xn<...<x3<x2<x1≤1。
19.本发明还提供一种半导体器件,包括如上所述的半导体外延结构。
20.本发明还提供一种发光二极管,其特征在于,包括如上所述的半导体外延结构。
21.本发明还提供一种微型发光二极管,其特征在于,包括如上所述的半导体外延结构。
22.本发明还提供一种微型发光二极管显示器,其特征在于,包括如上所述的微型发光二极管。
23.综上所述,本发明提出一种半导体外延结构及其应用,通过设置空穴注入层,将通过不同厚度、不同浓度的gan和ingan的组合,减少algan层、p型掺杂层中间的晶格失配,减少位错密度,改善表面形貌。通过不同浓度的in掺杂,利用in原子强活性特性,进一步促进p型mg掺杂的效率,提高空穴浓度,从而增加了单位时间内复合产生的光子数目,进而增强了发光二极管的发光强度和效率。本发明提出一种半导体外延结构及其应用,可以获得高质量的外延结构,可以提高耐压具有较高的耐压性能,提高所述半导体外延结构的质量。
附图说明
24.图1:本实施例中半导体设备结构示意图。
25.图2:本实施例中一过度腔结构示意图。
26.图3:本实施例中清洗腔结构示意图。
27.图4:本实施例中预热腔结构示意图。
28.图5:本实施例中生长腔结构示意图。
29.图6:本实施例中靶材及背板结构简要示意图。
30.图7:本实施例中另一半导体设备结构简要示意图。
31.图8:本实施例中沉积腔结构示意图。
32.图9:第一沉积腔体的结构示意图。
33.图10:扩散板的示意图。
34.图11:第一进气管路和第二进气管路的结构示意图。
35.图12:基板入口的示意图。
36.图13:第二管路的示意图。
37.图14:一种半导体设备的结构示意图。
38.图15:一种设置有空穴注入层的半导体外延结构图。
39.图16:一种极性面与非极性面示意图。
40.图17:一种具有稳定波长的半导体外延结构图。
41.图18:一种设置有电阻层的半导体外延结构图。
42.图19:图18所示的半导体外延结构等效电路图。
43.图20:一种微型发光二极管结构示意图。
44.图21:一种大角度微型发光二极管结构示意图。
45.图22:一种小角度微型发光二极管结构示意图。
46.图23:图21所示的遮挡层结构示意图。
47.图24:一种覆盖两个侧面的遮挡层示意图。
48.图25:一种覆盖四个侧面的遮挡层示意图。
49.图26:一种设置有填平层的微型发光二极管结构示意图。
50.图27:图25所示的填平层的结构示意图。
51.图28:图25所示的微型发光二极管焊接在基板上的受力示意图。
52.图29:未设置填平层的微型发光二极管结构的发光角度示意图。
53.图30:图25所示微型发光二极的发光角度示意图。
54.图31:一种电极上设置有金属叠层的微型发光二极管示意图。
55.图32:一种具有特殊导电结构的微型发光二极管示意图。
56.图33:一种具有防水保护层的微型发光二极管示意图。
57.图34:图32所示的保护膜层的结构示意图。
58.图35:图33所示的突出结构的电镜图。
59.图36:疏水性不同的表面,液滴边缘切线与基准面之间的夹角示意图。
60.图37:一种电极之间设置支撑层的微型发光二极管示意图。
61.图38:一种微型发光二极管转移装置结构示意图。
62.图39:一种微型发光二极管转移装置的结构俯视图。
63.图40:一种微型发光二极管转移装置的切割槽示意图。
64.图41:一种微型发光二极管转移装置的切割位置示意图。
65.图42:一种微型发光二极管显示面板的结构示意图。
66.图43:一种微型发光二极管显示面板的俯视图。
67.图44:一种电子装置结构示意图。
68.图45:一种半导体器件结构示意图。
69.图46:一种射频模组结构示意图。
具体实施方式
70.以下通过特定的具体实例说明本发明的实施方式,本领域技术人员可由本说明书所揭露的内容轻易地了解本发明的其他优点与功效。本发明还可以通过另外不同的具体实施方式加以实施或应用,本说明书中的各项细节也可以基于不同观点与应用,在没有背离本发明的精神下进行各种修饰或改变。
71.请参阅图1,本实施例提出一种半导体设备100,例如可以为化学气相沉积设备,也可以为物理气相沉积设备,当然也可以是物理气相沉积设备、化学气相沉积设备或其他半导体设备的组合。
72.如图1所示,在本发明一实施例中,半导体设备100内设置多个腔室,在发明一实施例中,半导体设备100例如可以包括传送腔110,预热腔140,清洗腔130,过渡腔120及多个生长腔150。在半导体器件制造过程中,可先对基板进行衬底预热以及等离子清洗,将清洗完成后的衬底转移至生长腔150,在生长腔150中进行薄膜生长,之后进行冷却处理。
73.如图1所示,在本实施例中,传送腔110包括基板装卸机械手臂111,可操作基板装
卸机械手臂111,以于各腔室之间传送基板。还可以根据不同腔体的空间尺寸大小调整基板装卸机械手臂111的大小。更具体地,基板装卸机械手臂111可具有适以同时将两基板从一个腔室传送至另一个腔室的双基板装卸叶片。基板可经由狭缝阀112在传送腔110与其它腔室之间传送。基板装卸机械手臂111的移动可由马达驱动系统(未示出)控制,而马达驱动系统可包括伺服电动机或步进电动机。
74.如图1,在一些实施例中,该半导体设备还包括一制造界面113,在制造界面113内包括卡匣及基板装卸机械手臂(未示出),卡匣含有需要进行处理的基板,基板装卸机械手臂可包含基板规划系统,以将卡匣内的基板装载至过渡腔120内,具体地,将基板放置在载台的托盘上。
75.如图1,在本实施例中,预热腔140连接传送腔110,预热腔140位于传送腔110的侧壁上,当基板进入过渡腔120时,传送腔110内的基板装卸机械手臂111随后将基板从过渡腔120传送至预热腔140中以进行预热并进行等离子体清洁。
76.如图1,在本实施例中,在该传送腔110的侧壁上设置多个生长腔150,当基板完成相应的工艺后,传送腔110内的基板装卸机械手臂111将基板传送至生长腔150内进行作业,由于在生长腔150内形成均匀的磁场,由此可在基板的表面形成均匀的溅射离子,从而在基板上形成均匀的薄膜。
77.如图2,在本实施例中,该过渡腔120连接传送腔110,其中该过渡腔120位于制造界面113与传送腔110之间。过渡腔120在制造界面113与传送腔110之间提供真空界面。
78.如图1和图2,在一些实施例中,过渡腔120可实现基板的传递、预热以及清洗的过程。该过渡腔120包括一壳体120a,该壳体120a例如为密封的圆柱体,同时在该壳体120a的侧壁上设有抽气口及排气口。过渡腔120设置多条气路通道例如进气口128。在过渡腔120内加装多条气路例如进气口128以及电源实现烘烤预热和等离子清洗过程,使用单独泵进行气体抽充,使整个工艺流程更加顺畅以节省整体耗时。
79.如图2,在一些实施例中,该过渡腔120内设有一载台122,载台122通过升降基座电机121固定在壳体120a的底部。载台122上可以设置托盘123,托盘123上可以设置多层开口式传送盒124以起到同时传盘的作用。在本实施例中,该载台122可例如为圆柱形或矩形或其他形状,该载台122可例如通过升降基座电机121固定在壳体120a内。在壳体120a的内部可以设置激光传感器125。过渡腔120允许多盘同时进入,只需在开始时抽真空一次,结束时充大气一次,节省中间传盘频繁的充抽时间,减少了传输节点的充抽耗时。
80.如图1和图2,在一些实施例中,该过渡腔120还包括一抽气口,该抽气口连接真空泵327,通过该真空泵127对过渡腔120进行抽真空。在过渡腔120中新增多路n2气路以通入气体,使腔室未传盘时可提供气冷以代替冷却腔。
81.请再参阅图1和图2,在本发明另一实施例中,过渡腔120仅实现基板的传递功能,在清洗腔130内实现基板的等离子清洗以及冷却。在本实施例中,清洗腔130连接传送腔110,清洗腔130位于传送腔110的侧壁上,当基板进入过渡腔120时,传送腔110内的基板装卸机械手臂111随后将基板从过渡腔120传送至清洗腔130中以进行清洗,在基板上生长薄膜后,将基板传递至清洗腔130冷却。
82.如图3,在该清洗腔130内设置有基板支撑组件131,基板支撑组件131设置在清洗腔130的底部,且基板支撑组件131未接触清洗腔130。基板支撑组件131包括台座电极1311
及静电卡盘1312,静电卡盘1312设置在台座电极1311上,静电卡盘1312用于放置基板,该静电卡盘1312上可至少放置一个基板,在一些实施例中,可在静电卡盘1312上设置多个基板,同时对多个基板进行清洗工作,从而提高工作效率。
83.如图3,在本实施例中,该基板支撑组件131连接有升降旋转机构134,具体地,该升降旋转机构134连接在台座电极1311上,通过该升降旋转机构134可实现基板支撑组件131的升降或旋转,间接实现基板的升降或旋转。当基板支撑组件131旋转上升或下降时,基板与电极132的距离发生变化,以调整台座电极1311与电极132之间的电场强度,使得等离子体能够更好的清洗基板。
84.如图3,在本实施例中,该清洗腔130内还包括一电极132,该电极132相对设置在基板支撑组件131的上方,该电极132未接触清洗腔130的顶部,在一些实施例中,电极132与基板支撑组件131的距离可在2
‑
25cm。该电极132同时还连接一升降旋转机构133,该升降旋转机构133的与升降旋转机构134的结构一致。当电极132进行旋转上升或下降时,电极132与基板之间的距离发生变化,以调节电极132与基板之间的电场强度,使得等离子体能够均匀的清洗基板。当电极132与基板支撑组件131同时发生旋转时,电极132的旋转速度与基板支撑组件131的旋转速度可相同或存在一定的速度差,以使得等离子体均匀的清洗基板。
85.如图3,在本实施例中,该基板支撑组件131还连接至少一个射频偏压电源138,具体地,该射频偏压电源138连接台座电极1311上。该射频偏压电源138的射频频率可以是高频、中频或低频。该射频电源137和射频偏压电源138均由同步脉冲来驱动,能够同时开关,降低清洗腔130内的电子温度,并且同步脉冲对于基板密集区域的清洗(刻蚀深度)具有良好的控制。
86.如图3,在本实施例中,该清洗腔130还包括进气口,该进气口靠近电极132,该进气口连接气体源135,通过气体源135向清洗腔130内输送气体,该气体为用于清洗应用的前驱物气体。在本实施例中,该清洗腔130还包括抽气口,该抽气口靠近基板支撑组件131,该抽气口连接一真空泵136,该真空泵136用于抽取清洗腔130内的气体。
87.如图1、图3和图4所示,在本发明又一实施例中,在进行半导体制备时,需要在基板上生长薄膜前需要将基板放在预热腔140内进行预加热,预热后的基板传输至清洗腔130清洁,将清洁后的基板传输至生长腔150生长薄膜,在薄膜生长完成后,再传送至清洗腔130中冷却。在形成薄膜的过程中,因在预热腔140内预热基板与清洗腔130内清洁的过程中,易导致热辐射流失,在本实施例中,在预热腔140内加装清洗结构,可在对基板进行预热时,同时对基板进行等离子清洗。
88.如图4所示,在本发明又一实施例中,该预热腔140包括壳体140a,在该壳体140a的底部设有支架141,该支架141可例如为空心结构,然后将导线放置在支架141的内部结构中,将导线连接在加热器142上。在本实施例中,该支架141可例如为耐高温材料。
89.如图4,在预热腔140内设置有加热器142,该加热器142固定在支架141上,该加热器142可包括底盘以及设置在地盘底部的加热线圈。在托盘143上靠近基板144的一面上还设有多个测量点,然后将多个测量点连接一测温装置,该测温装置可设置在预热腔140内或者设置在该预热腔140的外侧,通过该测温装置可实时测出基板144上的温度,从而可控制基板144的表面温度及其热均匀性。
90.如图4,在该预热腔140的底部还可设有至少一抽气口,该抽气口连接真空泵145,
通过该真空泵145对预热腔140进行抽真空处理,以获得真空状态的预热腔140。在预热腔140内设置至少一个加热器142,需要说明的是,还可以在预热腔140的侧壁上设置多个加热器142,或者在预热腔140的顶部上设置多个加热器,以保证预热腔140整体温度的均匀性。
91.请再参阅图4,在预热腔140的顶部,且位于基板144上方,可以设置至少一电极149,该电极149未接触预热腔140的顶部,且电极149与基板144的距离可在2~25cm,例如在10~20cm,又例如在16~18cm。该电极149同时还连接升降旋转机构146,该升降旋转机构146可以与图3中的升降旋转机构133的结构一致,当电极149进行旋转上升或下降时,电极149与基板之间的距离发生变化,以调节电极149与基板之间的电场强度,使得等离子体能够均匀的清洗基板。
92.请一并参阅图3和图4,在支架141和加热器142上还可以有设置升降旋转机构134和射频偏压电源138。当电极149与基板144同时发生旋转时,电极149的旋转速度与加热器142上基板144的旋转速度可相同或存在预设的速度差,以使得等离子体均匀的清洗基板。且电极149还连接至少一射频电源148,该射频电源148与图3所示的射频电源148相同设置。
93.请再参阅图4,在预热腔140的侧壁上还设置有进气口,该进气口靠近电极149,该进气口连接气体源147,通过气体源147向预热腔140内输送气体,该气体为用于清洗应用的前驱物气体。
94.请一并参阅图1、图3和图4,等离子清洗的过程需要在高温恒定的环境中进行,在预热腔140内加装等离子清洗装置,在进行预热基板的同时,可同步对基板进行等离子清洗。将基板在预热腔140中加热后,可以不需要再转移至清洗腔130进行清洁,可在预热腔140内进行预热及清洁后,直接转移至生长腔150内形成薄膜。
95.请参阅图5至图7,生长腔150包括生长腔壳体151,基座152,靶材153及磁体154。在生长腔150内部或侧壁加装循环水冷装置1508,如图5所示。基座152可设置在生长腔壳体151的底端,在基座152上允许放置一个或多个基板155。基座152可由多种材料形成,包括碳化硅或涂有碳化硅的石墨。基座152还连接一驱动单元156,驱动单元156连接控制单元(未显示),驱动单元156用于驱动基座152上升或下降,驱动单元156可以采用诸如伺服电机或步进电机等的驱动装置,控制单元用于在磁控溅射的过程中控制驱动单元156驱动基座152上升,以使靶材153与基座152的间距始终保持预定值不变。
96.请参阅图5至图7,在本实施例中,靶材153设置在生长腔壳体151的顶部,靶材153与溅射电源(未显示)电连接,在磁控溅射过程中,溅射电源向靶材153输出溅射功率,以使在生长腔壳体151内形成的等离子体刻蚀靶材153。靶材153具有至少一个表面部分是由将在设置在基座152上的基板155上溅射沉积的材料组成的。机台工艺腔中磁体154与托盘一样大,例如小于或等于330mm时,托盘外圈靠外位置氮化铝沉积厚度偏薄,会影响整体厚度均匀性。在本实施例中,靶材153及背板1509整体扩大,将靶材153受轰击面的直径设置为大于或等于例如400mm~600mm,则磁铁运转覆盖面直径大于或等于400mm~600mm。在靶材153和背板1509的外侧,使用保护环1510将其包围,且保护环为陶瓷环或不锈钢环。在一些实施例中,在将基板155载入生长腔壳体151之后,可通过使用含铝靶材和含氮处理气体在基板155上沉积连续的氮化铝薄膜,在溅射工艺期间使用的处理气体可包括但不限于含氮气体和惰性气体。
97.请参阅图5至图7,在本实施例中,磁体154位于靶材153的上方,磁体154围绕靶材
153的中心轴进行旋转,且磁体154可围绕靶材153的中心轴旋转任意角度。在本实施例中,该磁体154连接一驱动机构,该驱动机构带动该磁体154进行旋转的同时,还可以进行上下往复运动。该驱动机构包括第一电机157,传动杆158,第二电机159及升降组件。其中第一电机157通过传动杆158连接第二电机159,第一电机157可通过传动杆158带动第二电机159进行上下往复运动,第一电机157驱动传动杆158正向,或反向转动可使第二电机159作往复运动。在本实施例中,该升降组件包括外轴1501及内轴1502,在本实施例中,第二电机159通过输出轴1504连接内轴1502,输出轴1504部分位于外轴1501内,第二电机159通过输出轴1504可带动内轴1502进行旋转,同时第一电机157通过传动杆158带动第二电机159进行上下往复运动,当同时打开第一电机157及第二电机159时,内轴1502可在进行上下往复运动的同时,还可以进行旋转运动,从而可以带动内轴1502上的磁体154也作相应的运动。当打开第一电机157,关闭第二电机159时,该内轴1502可只进行上下往复运动。当关闭第一电机157,打开第二电机159时,该内轴1502可只进行旋转运动。由此工作人员可根据实现情况选择打开和/或关闭第一电机157和/或第二电机159。
98.请参阅图5至图7,在一些实施中,磁体154在作旋转运动时,靶材153可保持静止状态,也可绕自身中心轴旋转,但是靶材153和磁体154之间存在速度差。靶材153和磁体154的相对运动,可使得磁体154所产生的磁场均匀地扫描过靶材153的溅射面,且由于本实施例中电场与均匀分布于靶材153溅射面的磁场同时作用于二次电子,可调整二次电子的运动轨迹以增加二次电子与氩原子的碰撞次数,使得靶材153溅射面附近的氩原子被充分电离,以产生更多的氩离子。且通过更多的氩离子轰击靶材153,可有效地提高靶材153的溅射利用率和溅射均匀性,进一步提高沉积薄膜的质量和均匀性。
99.在本发明一实施例中,对于预热腔可实现预热以及清洗功能的半导体设备,本技术还提出一种半导体设备的使用方法,包括:
100.s11:将过渡腔中的所述多层开口式传送盒放置在所述托盘上,并将基板传送至预热腔;
101.s12:在预热腔中烘烤预热,并通入气体进行等离子清洗;
102.s13:在生长腔中生长薄膜;
103.s14:在清洗腔中腔通入气体,进行托盘冷却。
104.如图1和图8所示,在本发明一实施例中,在半导体设备100例如为化学气相沉积设备,则在传送腔110的侧壁上,设置有多个沉积腔。在本实施例中显示出四个沉积腔,即第一沉积腔161,第二沉积腔162,第三沉积腔163和第四沉积腔164。传送腔110内的机械臂311可以将基板或晶圆依次送入第一沉积腔161,第二沉积腔162,第三沉积腔体163和第四沉积腔164中,以在基板或晶圆上形成薄膜。在本实施例中,第一沉积腔161,第二沉积腔162,第三沉积腔163和第四沉积腔164中至少包括一个可拆卸腔体,所述可拆卸腔体是指该腔体可以单独拆卸下来,不会影响整个半导体设备100的工作。本实施例例如将第一沉积腔161设置成可拆卸腔体。在其他实施例中,可单独设置一可拆卸腔体。
105.如图9所示,图9显示为第一沉积腔161的剖面图。从图中可以看出,该第一沉积腔161包括主腔体101,主腔体101内设置有底座102,底座102可以设置在主腔体101的底部。在主腔体102的顶部设置有射频组件103,射频组件103和底座102相对设置。射频组件103和底座102形成等离子产生区域。主腔体101的材料例如为不锈钢。在一些实施例中,射频组件
103在沉积过程中还可以进行旋转,从而使得薄膜沉积更均匀。
106.如图9所示,在一些实施例中,底座102还可连接一旋转单元,用于在膜沉积期间使底座102旋转,进一步改善镀膜的厚度均匀性,及改善镀膜的应力均匀性。
107.如图9所示,当然,在一些实施例中,还可以在底座102的背面设置一加热单元,通过该加热单元可以对基板进行加热。在一些实施例中,所述加热单元具体可以为射频加热器、红外辐射加热器或电阻加热器等,可以根据主腔体101的尺寸和材料进行不同的选择。在射频加热方式中,石墨的底座102被射频线圈通过诱导耦合加热,这种加热形式可以应用于大型的主腔体101。
108.如图9所示,在本实施例中,该射频组件103还连接一射频电源,通过射频电源向射频组件103提供电压,从而将反应源气体电离成等离子体。
109.如图9所示,在本实施例中,在主腔体101的顶部还包括一进气口,进气管路104连接该进气口,进气管路104的一端连接所述进气口,进气管路104的另一端连接外部气源105。通过该外部气源105,进气管路104和进气口可将反应气体输送至主腔体101内。
110.如图9所示,在本实施例中,该进气口设置在射频组件103的一侧,进气管路104包括第一管路1041和第二管路1042。第一管路1041的一端连接外部气源105,第一管路1041的另一端连接第二管路1042。第一管路1041例如通过快速接头107连接第二管路1042。通过旋转该快速结构107即可将第一管路1041和第二管路1042连接或分开。在第一管路106上设置有第一阀体106,当向主腔体101内输送气体时,第一阀体106例如是打开状态,当需要拆卸该腔体时,该第一阀体106例如是关闭状态,从而可以防止重金属粉尘进入无尘室内。
111.如图9和图10所示,在本实施例中,第二管路1042的一端延伸至主腔体101内,且在第二管路1042的一端设置有扩散板108。扩散板108上具有多个扩散孔1081。反应气体通过扩散孔1081可以均匀的扩散到主腔体101内。需要说明的时,这些扩散孔1081的直径可以相同也可以不同,这些扩散孔1081的排列密度也可以进行改变。
112.如图9和图11所示,在一些实施例中,还可以主腔体101的顶部设置多个进气口,也就是设置多个进气管路104,例如设置第一进气管路104a和第二进气管路104b,第一进气管路104a可以连接第一进气装置,第二进气管路104b可以连接第二进气装置。第一进气管路104a和第二进气管路104b位于主腔体101的两侧,且第一进气管路104a的高度大于第二进气管路104b的高度,由于第一进气管路104a和第二进气管路104b具有高度差,通过第一进气管路104a和第二进气管路104b向主腔体101输送的气体不会相互影响。
113.如图9所示,在本实施例中,在主腔体101的底部还设置至少一排气口,排气管路109的一端连接排气口,另一端连接抽气泵1013,通过该抽气泵1013对主腔体101进行抽气作业,以抽走多余的等离子体,进而减少多余的离子落到薄膜上的几率,提高薄膜的质量。在主腔体101的底部还设置第二阀体1014,第二阀体1014位于排气口上,当进行抽气作业时,第二阀体110处于打开状态,当完成沉积作业时,第二阀体1014可以处于关闭状态,以防止等离子体扩散出去。
114.如图8和图12所示,在本实施例中,该主腔体101还包括基板入口,传送腔110内的机械臂通过该基板入口将基板放置在主腔体101内。该基板入口包括两个伸缩门1011。当两个伸缩门1011打开时,也就是打开基板入口。当两个伸缩门1011关闭时,也就是关闭基板出口。该主腔体101还连接一锁紧单元1012,当拆卸该主腔体101时,该锁紧单元1012可以使得
基板入口保持锁紧状态,也就是当主腔体101断电后,锁紧单元1012可以使得基板入口保持关闭或锁紧状态。当基板入口保持锁紧状态时,可以防止主腔体101内剩余的等离子体向无尘室内扩散,从而防止造成无尘室重金属污染。
115.如图9所示,在本实施例中,该基板入口还可以作为基板出口,也就是说机械臂通过该基板入口将基板放进主腔体101内或者将基板拿出主腔体101。在一些实施例中,主腔体101还可以包括一基板出口,也就是说基板出口与基板入口相对设置,因此当机械臂通过基板入口将基板放置在主腔体101内,然后通过基板出口将基板拿出主腔体101。由于基板出口和基板入口相对设置,因此打开基板出口时,主腔体101内的重金属粉尘不会扩散至无尘室内,因此不会造成无尘室污染。
116.如图13所示,在一些实施例中,第二管路1042的端部还可以设计成弯折状,所述弯折状朝向射频组件103和底座102之间,使得气体在射频组件103和底座102之间扩散。
117.如图1和图9所示,在本实施例中,半导体设备100包括传送腔110和可拆卸腔体,传送腔110内的机械臂311将基板传送或传出可拆卸腔体内,当在任意一腔体完成作业时(包括预热、清洗、沉积、生长以及冷却),通过关闭第一阀体和第二阀体,从而气源内的气体无法进入可拆卸腔体内,同时可拆卸腔体内的反应气体也无法从排气口内排出,同时通过锁紧单元关闭可拆卸腔体的基板入口,然后将该可拆卸腔体移动至另一无尘室内,打开基板入口,然后取出基板,从而避免造成原来无尘室的重金属污染,然后可以对可拆卸腔体进行保养,然后在将该可拆卸腔体设置在传送腔的310的外侧。
118.如图14,在一些实施例中,半导体设备100的镀膜系统180内设置有多个反应腔170,反应腔170可以是物理气相沉积设备中的生长腔,也可以是化学沉积设备中的沉积腔。在本实施例中,反应腔170例如包括第一反应腔171和第二反应腔172。且第一反应腔171和第二反应腔172上均设置有两个腔门,例如为第一腔门173和第二腔门174。每个腔门与一个基板装卸机械手臂111对应传送,例如包括与第一腔门173对应的第一机械手臂111a,以及与第二腔门174对应的第二机械手臂111b,且反应腔170的一侧还设有进气管路183以及传输轨道181。且第一反应腔171和第二反应腔172之间通过开闭阀门连接,可方便运输基片,并提高加工效率。
119.如图14所示,第一腔门173和第二腔门174设置在第一反应腔171和第二反应腔172上,在一些实施例中,第一腔门173和第二腔门174设置在反应腔的同侧,在其他实施例中,第一腔门173和第二腔门174设置在反应腔的相对侧设置。第一腔门173和第二腔门174的具体结构可以为图12所示的伸缩门,在此不再次叙述。且在实际的薄膜生长过程中,第一腔门173作为基板入口/基板出口,第二腔门174作为基板出口/基板入口。将基板出口与基板入口分开,可减少基片的污染。与腔门对应设置的基板装卸机械手臂111,包括第一机械手臂111a和第二机械手臂111b。在基板的传送过程中,第一机械手臂111a例如可以通过第一腔门173将基板传入反应腔170内,第二机械手臂111b例如可以通过第二腔门174将基板从反应腔170内传出。设置两个机械臂可方便基板的拾取,同时传入和传出基板,且将传入和传出的基板装卸机械手臂111区分,可进一步减少基片的污染,进而可以提高沉积薄膜的质量和均匀性。
120.如图14所示,基座152(或底座102)设置在反应腔170的顶部,靶材153(或射频组件103)设置在反应腔170的底部。与图5(或图9)中的位置相反,反应物由下而上运动。在一些
实施例中,基座152上具有固定卡扣,用于固定基片。在本实施例中,基座152为磁性基座,允许在靶材153的相对侧放置多个磁性基座,此时,基座152可直接将基板吸附在基座152上,而不需要其他的结构固定基板。基座152可包括蓝宝石,碳化硅,硅,氮化镓,金刚石,铝酸锂,氧化锌,钨,铜和/或铝氮化镓等材料制成,且可以将基座152蒸镀上金属层,使得基座152具有金属性。在基座152内设置磁体,使基座152具有吸附功能。磁体在作旋转运动时,基座152可绕自身中心轴旋转。当磁体进行旋转时,可以通过动力源如电机来驱动基座152环绕自身中心轴旋转,使得磁体所产生的磁场紧紧吸附基座152,进一步提高沉积薄膜的质量和均匀性,且基座152的尺寸例如为2
‑
12英寸。
121.如图14所示,传输轨道181将反应腔170与其他半导体设备连接,例如将腔门与其他半导体设备连接,其中其他半导体设备可以为清洗设备、预热设备或其他半导体设备。进气管路182连接外部气源,外部气源通过进气管路182向该反应腔170内送入气体。进气管路182可包括第一进气管路和第二进气管路,第一进气管路连接第一反应腔171,第二进气管路连接第而反应腔172,该进气管路的设计方便气体的输入输出。
122.本技术的半导体设备可制造高质量无污染的薄膜,例如金属薄膜、半导体薄膜、绝缘薄膜、化合物薄膜或其他材料的薄膜。
123.如图15所示,在本发明一实施例中,当利用本公开的半导体设备来制造一半导体外延结构20时,半导体外延结构20可包括衬底200,以及依次设于衬底200上的第一半导体层203、有源层204和第二半导体结构21。
124.如图15所示,衬底200可以为蓝宝石衬底200。在其他实施例中,衬底200也可以采用硅(si)、碳化硅(sic)、砷化镓(gaas)、铝酸锂(lialo2)等材料制成。
125.如图15至图16所示,在一些实施例中,衬底200可选用无极化反应的晶轴材料制成,衬底200的材料具有无压电效应的晶轴,或者在衬底200上形成一层特殊的铺平层,以对衬底200的晶相方向进行选择,消除压电效应对衬底200的影响。在一些实施例中,衬底200可以选用n面(1100)或a面(1120)的材料制成,例如可以选用gan、aln以及inn等材料制成。在其他实施例中,当衬底200为其他衬底200,例如为sico3、sic等硅基材料制成时,可在衬底200上形成铺平层,以消除晶格缺陷。铺平层的材料可以选用第iia族元素与氮组成的化合物作,具体例如为非极性的aln材料或者非极性gan材料。选用特殊的晶轴材料或设置铺平层,可避免导入大电流时导致衬底200内晶格扭力的产生,进而产生压电空洞,导致材料的发热裂化。
126.如图15所示,在一些实施例中,为获取平整的衬底200表面,在对衬底200表面研磨抛光后,衬底200表面具有应力痕,会与其上设置的半导体层形成缺陷。可将衬底200表面的碎晶颗粒氧化,形成碎晶氧化物,再使用氧化物刻蚀液清洗碎晶氧化物,进而获取平整的衬底200表面。在一具体实施例中,衬底200例如为硅衬底,可通过研磨或者抛光等工艺进行初步表面加工,在衬底200表面形成硅的碎晶颗粒。碎晶颗粒的产生导致晶体晶格上出现应力痕,影响晶体的生长,因而需要对碎晶颗粒进行处理。在本实施例中,可选用物理或者化学的方法消除碎晶颗粒带来的影响。当使用物理方法时,可以在预热腔种加热衬底200,使得衬底200表面达到例如300~400度,同时向腔内通入氧气、或其他氧化物,使碎晶颗粒发生氧化反应,以生成碎晶氧化物。当使用化学方法时,可以使用双氧水等氧化剂与碎晶颗粒反应生成碎晶氧化物。在反应过程中,可以通过升温的方法提高氧化反应速率,温度的范围例
如为40~80度。在本实施例中,碎晶氧化物为二氧化硅,在进行氧化后,衬底200表面形成一层致密的二氧化硅层,可通过氧化物刻蚀液清洗,进而获取具有完整晶型的衬底200,使衬底200无碎晶缺陷。在本实施例中,可以使用氢氟酸、硫化铵去除碎晶氧化物。在其他实施例中,衬底200材料不限于硅衬底,也可以选取sic衬底以及其他衬底,因衬底200的材料不同,可以选用不同的方法氧化碎晶颗粒,以及不同的溶液去除碎晶氧化物。
127.如图15所示,在一些实施例中,会在第一半导体层203和衬底200之间设置缓冲层201,以减缓第一半导体层203和衬底200之间的晶格不匹配,进而导致位错、层错或者空洞型的缺陷。缓冲层201的材料可以但不仅限制为氮化铝、氮化镓等材料,但缓冲层201并不足以解决晶格不匹配的问题,进而产生空洞。在本实施例中,通过在衬底200和缓冲层201之间设置过渡金属层,可进一步减缓第一半导体层203和和缓冲层201之间的晶格不匹配问题。过渡金属层的材料可选用第iia族元素,例如可以选用铝,作为晶格铺层。在衬底200上沉积过渡金属层后,再对过渡金属层进行退火处理,在硅衬底200表面和过渡层之间形成退火界面,在退火时,腔体内填充有惰性气体,例如为氮气。在退火过程中,在过过渡金属层和衬底200的界面上,渡金属层中的金属al和衬底200中的si的晶格转换,进而减少了直接在硅衬底上生长缓冲层201产生的位错等缺陷。其中退火温度的范围可以为例如400~600度,具体时间例如为520度,退火处理的时间范围可以为例如5~30分钟。
128.如图15所示,在另一些实施例中,缓冲层201例如包括周期性的氮化铝层和遮挡层,因只有氮化铝层作为缓冲层的缺陷过多,可进行在氮化铝层内周期性插入遮挡层,以遮断缺陷,进而改善晶格缺陷。例如可以将反应腔的温度设置为例如500~1000度,并生长厚度例如为20~300nm缓冲层201。具体可先生长厚度例如为10~25nm的氮化铝层,并停止生长。此时,使用氮氧化物或氧气吹扫氮化铝层的表面30~60秒,进而在氮化铝层的表面形成厚度例如为3~5nm氧化铝层,作为遮挡层。遮挡层例如为呈球形的氧化铝,设置在缺陷的地方,可阻挡晶格缺陷,随着缓冲层201厚度的增加,晶格缺陷越来越少,进而改善缓冲层201的质量。其中氮氧化物可以为一氧化二氮(n2o)或二氧化氮(no2)。如此重复生长氮化铝层,再在氮化铝层上形成遮挡层,最终形成厚度例如为20~300nm的缓冲层201。其中每层遮挡层都可减缓其上一层氮化铝层中的晶格缺陷,使缓冲层201的厚度越高,缺陷越少。具体可根据所需缓冲层201的厚度设置每次生长的氮化铝层厚度,本技术对此并无限制。
129.如图15所示,在其他实施例中,缓冲层201例如为氮化镓层。具体可在温度例如为500~850℃,又例如为500~550℃,反应腔压力例如为100torr~650torr,又例如为200~500torr的条件下,向反应腔内通入氨气和三甲基镓(tmga),进而在衬底200上生长一层厚度例如为200~400埃或400~600埃的氮化镓,形成缓冲层201。
130.如图15所示,在形成缓冲层201后,可在缓冲层201上生长一层无掺杂的氮化镓层202,具体可在温度例如为1000~1200℃,又例如为1050℃~1200℃,反应腔压力例如为100torr~500torr,有例如为200~500torr的条件下,向反应腔内通入氨气和三甲基镓(tmga),进而在缓冲层201上生长一层厚度例如为10000~30000埃的氮化镓,形成无掺杂的氮化镓层202。通过设置在衬底200和第一半导体层203之间设置缓冲层201和无掺杂的氮化镓层202,可减缓衬底200和第一半导体层203之间的晶格不匹配问题,提高半导体外延结构20的质量。
131.如图15所示,第一半导体层203例如为第一类型的氮化镓层,具体例如为n型氮化
镓层,则第一半导体层203的掺杂离子可为硅。在本实施例中,可在温度例如为1000~1200℃,又例如为1050℃~1200℃,在反应腔压力例如为100torr~600torr,又例如为200~500torr的条件下,向反应腔内通入氨气、三甲基镓(tmga)和硅烷(sih4),进而在无掺杂的氮化镓层202上生长一层厚度例如为10000~30000埃,又例如为20000~40000埃的n型氮化镓层。第一半导体层203中硅离子的离子浓度例如为1
×
10
18
~7
×
10
18
atom/cm3,又例如为8
×
10
18
~2
×
10
19
atoms/cm3。在一些实施例中,第一半导体层203可以为掺杂了硅离子的n型氮化镓层和非掺杂的氮化镓层的超晶格结构,在其他实施例中,第一半导体层203可以包括n型氮化镓层以及设置在n型氮化镓上的超晶格结构。
132.如图15所示,有源层204位于第一半导体层203上,在本实施例中,有源层204包括一个或多个交替形成的周期性量子垒层和量子阱层,且量子垒层例如包括gan/algan超晶格结构,量子阱层例如包括ingan。有源层204的厚度例如为200nm~300nm,且每个周期的量子阱层的厚度例如为3nm~4nm,每个周期的量子垒层的厚度例如为12nm~16nm,其中,构成量子垒层的中gan的厚度例如为1.5nm~3nm,构成量子垒层的中algan的厚度例如为1.5nm~3nm。本实施例中的有源层204采用调制掺杂的gan/algan超晶格结构,可有效的引导冲击电流,使脉冲电流在gan/algan结构的二维电子气中,在横向方向上传导,使得脉冲电流的密度分布更加均匀,可以有效的提升电子与空穴的复合效率。
133.如图15所示,可在温度例如为810~860℃、压力例如为200~500torr的条件下,生长一层厚度例如为1nm~3nm的gan,然后在gan上生长一层厚度例如为1nm~3nm调制掺杂的algan。gan和algan组成一超晶格单元结构,交替连续生长2~6个周期的超晶格单元结构,可形成超晶格结构的量子垒层。在形成量子垒层后,改变生长条件,在温度例如为710~760℃、压力例如为200~500torr的条件下,在量子垒层上生长厚度例如为2~6nm的ingan,形成量子阱层,其中铟源例如为三甲基铟(tmin)。交替连续生长2~6或9~12个周期的量子垒层和量子阱层,可形成有源层204。
134.如图15所示,在一些实施例中,第二半导体结构21可包括第二半导体层205和空穴注入层22,第二半导体层205位于有源层204上,空穴注入层22位于第二半导体层205上。其中第二半导体层205为电子阻挡层,可以为第二类型的氮化镓层,或可以为第二类型的氮化铝镓层,也可以为采用非或低掺杂镁的algan制成,在一些实施例中,第二半导体层205包括3~10周期循环的p型gan层和p型algan层。
135.具体的,如图15所示,在一实施例中,第二半导体层205为p型algan层,则可以在温度例如为700~950℃、压力例如为50~500torr的条件下,在有源层204上生长厚度为5~10nm的algan,形成p型algan层,其中mg掺杂浓度为0~1
×
10
16
atom/cm3。
136.具体的,如图15所示,在其他实施例中,第二半导体层205包括单层的p型gan层和p型algan层,则可以在温度为例如为700~900℃,压力例如为200~500torr的条件下,生长厚度例如为20~30nm的gan,形成p型gan层,其中mg的掺杂浓度为1
×
10
19
~1
×
10
20
atom/cm3。之后在温度例如为800~950℃、压力例如为200~500torr的条件下,在p型gan层上生长厚度例如为5~10nm的algan,形成p型algan层,其中mg掺杂浓度例如为1
×
10
19
atom/cm3。
137.具体的,如图15所示,在又一实施例中,第二半导体层205包括周期性的p型gan层和p型algan层,则可以在温度例如为700~800℃、压力例如为200~500torr的条件下,在有源层204上生长厚度例如为5~10nm的gan,形成p型gan层,其中mg掺杂浓度为1
×
10e
19
atom/
cm3。在温度例如为700~950℃、压力例如为50~500torr的条件下,在p型gan层上生长厚度例如为5~10nm的algan,形成p型algan层,其中mg掺杂浓度为0~1
×
10e16atom/cm3。并交替连续生长3~10个周期的p型gan层和p型algan层。
138.如图15所示,空穴注入层22位于第二半导体层205上,且空穴注入层22包括非或低掺杂in
x
ga
y
n层,和/或掺杂in
x
ga
y
n层,即空穴注入层22包括in
x
ga
y
n层,且0≤x≤1,0≤y≤1。其中非掺杂in
x
ga
y
n层为未掺杂其他离子的in
x
ga
y
n层,掺杂in
x
ga
y
n层例如由掺杂了mg的in
x
ga
y
n制成。
139.如图15所示,在一具体实施例中,第二半导体层205例如为p型氮化铝镓层,其上设置的空穴注入层22至少包括第一掺杂层206和第二掺杂层207,第一掺杂层206位于第二半导体层205上,第二掺杂层207位于第一掺杂层206上。第一掺杂层206为非或低掺杂inxgayn层,且第一掺杂层206的掺杂浓度例如为第一掺杂浓度,第二掺杂层207为掺杂inxgayn层,且第二掺杂层207的掺杂浓度例如为第二掺杂浓度,第二半导体层205例如具有第三掺杂浓度。其中第一掺杂浓度小于第二掺杂浓度,第三掺杂浓度小于第二掺杂浓度,且第一掺杂浓度的范围为0~1
×
10
19
atom/cm3。且第一掺杂层206的厚度小于第二掺杂层207的厚度,第一掺杂层206的厚度例如为第二掺杂层207厚度的40%~50%,具体例如为第二掺杂层207厚度的30%。
140.如图15所示,在本发明又一实施例中,空穴注入层22包括第一掺杂层206和第二掺杂层207,且第一掺杂层206为非掺杂inxgayn层,第二掺杂层207为掺杂inxgayn层,即第一掺杂层206的第一掺杂浓度为零,第二掺杂层207为掺杂了镁的inxgayn层。
141.如图15所示,在其他实施例中,空穴注入层22还包括第三掺杂层,第三掺杂层位于第二掺杂层207上,第三掺杂层例如为掺杂了镁的inxgayn,且第三掺杂层的第四掺杂浓度大于第二掺杂浓度。
142.如图15所示,在一具体实施例中,第一掺杂层206为非掺杂inxgayn层,第二掺杂层207为低掺杂inxgayn层,第三掺杂层为掺杂inxgayn层。则在温度例如为800~950℃,压力例如为200~500torr的条件下,生长厚度例如为2~5nm的gan,形成的非掺杂inxgayn层为第一掺杂层206。其次,在在温度例如为800~950℃,压力例如为200~500torr的条件下,生长厚度为例如5~50nm的gan,其中,镁的掺杂浓度例如为1
×
10
16
~1
×
10
17
atom/cm3,形成低掺杂inxgayn层为第二掺杂层207。最后,在温度例如为800~950℃,压力例如为200~500torr的条件下,生长厚度例如为10~20nm的gan,其中,镁的掺杂浓度为1
×
10
18
~1
×
10
19
atom/cm3,形成掺杂inxgayn层为第三掺杂层。
143.如图15所示,在本发明再一实施例中,掺杂in
x
ga
y
n层包括但不限由n层in
x1
ga
y1
n、in
x2
ga
y2
n、in
x3
ga
y3
n的叠加,或是交替的in
x1
ga
y1
n与in
x2
ga
y2
n的n个周期循环,其中n≥1,x3<x2<x1≤1,xn<...<x3<x2<x1≤1。在一具体实施例中,n等于3,x1等于1,x2等于0.2,x3等于0.05,即空穴注入层22包括依次设置的inn、in
0.2
ga
0.8
n、in
0.05
ga
0.95
n掺杂层。本发明中所述的空穴注入层22能有效提高外延结构的空穴浓度,提高发光效率。
144.如图17所示,在本发明另一实施例中,还提供一种高波长稳定性好的半导体外延结构20,且所述半导体外延结构20为一种绿光外延结构,且有源层204例如包括应力释放层208、第一有源层209和第二有源层210,且第一有源层209位于应力释放层208上,第二有源层210位于第一有源层209上。
145.如图17所示,应力释放层208的材料为inxga(1
‑
x)n和gan,其中0.17<x<0.35,且gan中掺杂有硅离子,且硅离子的掺杂浓度例如为a,且a范围为5
×
10
17
~1
×
10
18
atoms/cm3,且应力释放层208的厚度为3~40nm。具体的,应力释放层208可包周期循环的量子阱层和量子垒层,且应力释放层208的生长周期例如为2~6,又例如为3。在本实施例中,可在温度例如为750~950℃,反应腔压力例如为200~500torr的条件下,通入流量例如为30000~60000sccm的氨气(nh3)、50~100sccm的三乙基镓(tega)和500~1000sccm的三甲基铟(tmin)和100~130l/min的氮气(n2),进而在第一半导体层203上生长一层1nm~3nm的ingan,形成量子阱层。之后,可以在温度例如为750~950℃,反应腔压力例如为200~500torr的条件下,通入流量为30000~60000sccm的氨气(nh3)、100~200sccm的三甲基镓(tmga)、100~130l/min的氮气(n2)及1~2sccm的硅烷(sih4),进而在量子阱层上生长一层30~40nm的n型gan层,形成量子垒层。重复生长2~6个周期的量子阱层和量子垒层,可获得应力释放层208。
146.如图17所示,第一有源层209包括例如3~8个周期循环的势垒层和势阱层,所述周期数具体例如为5。在一些实施例中,势垒层的材料例如为alzga(1
‑
z)n,且0≤z<0.3,势阱层的材料例如为inyga(1
‑
y)n,且0.17<y<0.4。其中势垒层中掺杂有硅离子,且硅离子的掺杂浓度为b,且a>b,且b范围为5
×
10
16
~1
×
10
17
atoms/cm3。在其他实施例中,势垒层的材料还可以为gan,或algan与gan的交替生长的2~6个周期的超晶格层,且势垒层的厚度l1例如为70~150埃,又例如为120埃。在本实施例中,可以在温度例如为750~900℃,反应腔压力例如为200~500torr的条件下,向反应腔通入流量为50000
‑
70000sccm的氨气(nh3)、200
‑
1000sccm的三乙基镓(tega)、1
‑
2sccm的硅烷(sih4)及100
‑
130l/min的氮气(n2),进而在应力释放层208上生长一层1nm~3nm的n型gan,形成势垒层。进一步的,在温度例如为710~760℃。反应腔压力例如为200~500torr的条件下,在势垒层上生长一层厚度为2~6nm的ingan,形成势阱层。重复生长3~8个周期的势垒层和势阱层,可形成第一有源层209。
147.如图17所示,第二有源层210包括2~6个周期循环的in
u
ga1‑
u
n和gan,所述周期具体例如为3,且第二有源层210内in
u
ga1‑
u
n的铟含量为0.17<u<0.40,第二有源层210的gan内掺杂有硅离子,且硅离子的掺杂浓度为c,且a>c>b,c范围为5
×
10
16
‑1×
10
17
atoms/cm3且c可以是b的1.4倍。在本发明一具体实施例中,第二有源层210包括材料为n型gan的量子阱层,以及材料为ingan的量子垒层。在其他实施例中,量子阱层也可以为非掺杂si的gan与掺si层的gan的超晶格层。在本实施例中,例如在温度例如为750~900℃,反应腔压力例如为200~500torr的条件下,想反应腔内通入流量例如为50000
‑
70000sccm的氨气(nh3)、200
‑
1000sccm的三乙基镓(tega)、1
‑
2sccm的硅烷(sih4)及100
‑
130l/min的氮气(n2),进而在第一有源层209上生长除一层1nm~3nm的n型gan,可形成量子阱层,量子阱层的厚度l2的范围为70~150埃,且l1>l2=100埃。进一步的,在在温度例如为710~760℃,反应腔压力例如为200~500torr的条件下,在量子垒层上生长一层厚度为2~6nm的ingan,形成量子阱层。重复生长2~6个周期的量子垒层和量子阱层,可形成第二有源层210。
148.如图17所示,第二半导体结构21包括第二半导体层205、第三半导体层211和第四半导体层212,且第三半导体层211位于第二半导体层205上,第四半导体层212位于第三半导体层211上。且第二半导体层205为p型algan层,第三半导体层211和第四半导体层212为p型gan层,p型gan层例如是掺杂mg的gan层,且第四半导体层212的掺杂浓度大于第三半导体
层211的掺杂浓度。在本实施例中,可在温度例如为700~800℃,反应腔压力例如为200~500torr的条件下,有源层204上生长厚度为5~10nm的algan,形成第二半导体层205。其中,第二半导体层205中mg的掺杂浓度为1
×
10
18
~1
×
10
19
atom/cm3。之后,在温度例如为800~950℃,反应腔压力例如为200~500torr的条件下,生长厚度为20~30nm的gan,形成第三半导体层211。其中,mg的掺杂浓度为1
×
10
19
~1
×
10
20
atom/cm3。最后,在温度例如为800~950℃,反应腔压力例如为200~500torr的条件下,生长厚度为10~20nm的gan,形成第四半导体层212。其中,mg的掺杂浓度为1
×
10
18
~1
×
10
19
atom/cm3。
149.如图18所示,在本发明又一实施例中,为保证形成的发光二极管不会因反应过快,而出现闪烁的情况,可在第一半导体层203和有源层204之间设置一特殊结构的电阻层214,可延迟二极管熄灭的时间。且具有特殊结构的电阻层214的半导体外延结构20可制成发光二极管,配合节能电源使用,可减少总通电时间,以节约能耗,同时可保持人眼感受相同亮度,减少闪烁带来的影响,进而降低强光对于人眼的伤害。
150.如图18所示,第一半导体层203为氮化镓层203,且在氮化镓层203上设置有超晶格结构213,将电阻层214设置在氮化镓层203上,且位于氮化镓层203和超晶格结构213之间。在本实施例中,氮化镓层203例如包括轻掺杂的n型氮化镓层203a和重掺杂的n型氮化镓层203b。在重掺杂的n型氮化镓层203b设置一层电阻层214,并在电阻层214上设置超晶格结构213,有源层204位于超晶格结构213上。本实施例提供的电阻层214可减缓最终形成的发光二极管的放电速度,延长发光二极管的放电时间,避免因电源不稳定或占空比低导致的发光二极管的闪烁。
151.如图18所示,电阻层214的材料例如为alxga1
‑
xn,且x<0.15,电阻层214的厚度例如为50~200nm,可避免电阻层214太薄不好控制生长,以及电阻层214太厚出现开裂现象。在光阻层上蚀刻有多个开孔215,开孔215的方向平行于电阻层214的生长方向,且开孔215的直径例如为3~20um,相邻开孔215之间的间距例如为3~10um。在本实施例中,可在温度例如为700~900,反应腔的压力例如为500mbar的条件下,在反应腔内通入气体三乙基镓(tega)、三甲基铝(tmal)以及氨气(nh3),采用金属有机化合物化学气相沉淀(mocvd)的方式生成电阻层214。在生成的电阻层214后,采用电感耦合等离子体的蚀刻方法,蚀刻电阻层214形成开孔215,且开孔215穿透电阻层214,与重掺杂的n型氮化镓层203b接触。
152.如图19所示的蚀刻后的的半导体外延结构20的等效电路,c为不添加电阻层214时半导体外延结构20的等效电容,r0为不添加电阻层214时半导体外延结构20的等效电阻,r
l
为电阻层214的等效电阻,且r
l
可通过调节电阻层214上开孔的数量或直径调节,e为半导体外延结构20两端的电压。则电容的放电公式为:vt=e
×
(exp(
‑
t/r*c)),电容的放电时间为:t=rc
×
ln[e/vt],且r=r0+r
l
。由上述公式可知,放电时间的长短与电阻r呈正比,电阻r越大,电子流动越困难,放电时间越长。可根据实际需求调节r
l
的大小,即可通过开孔215的数量和直径调整电阻层214的等效电阻,且开口的数量越多、直径越大,电阻层214的等效电阻越小,且开孔还可限制电流流出。
[0153]
本技术中所形成高质量薄膜可应用于各种半导体结构、电子原件或电子装置中,例如开关元件、功率元件、射频元件、发光二极管、微型发光二极管、显示面板、手机、手表、笔记本电脑、投载式装置、充电装置、充电桩、虚拟现实(vr)装置、扩充现实(ar)装置、可携式电子装置、游戏机或其他电子装置。
[0154]
如图20所示,本实施例以及之后的实施例中的发明适用于微型发光二极管,包括microled,也可以是miniled,也可以是其他发光二极管,本技术中以微型发光二极管为例。其中,微型发光二极管包括衬底200、设置在衬底200上的半导体外延结构20,且半导体外延结构20包括第一半导体层203、有源层204和第二半导体结构21,所述微型发光二极管还包括与第一半导体层203连接的第一电极226以及与第二半导体结构21连接的第二电极227。且衬底200例如为蓝宝石衬底200,所述半导体外延结构20可以为如图15、图16或图17所示的半导体外延结构20。在一些实施例中,在半导体外延结构20的一侧,如图15以及图16所示,可设置一缺口23,缺口23设置在半导体外延结构20的一侧,且缺口23的底部与第一半导体层203接触。在一些实施例中,缺口23与第一半导体层203的表面接触,在其他实施例中,可蚀刻第二半导体结构21、有源层204以及部分第一半导体层203,形成缺口23。
[0155]
如图20所示,在第二半导体结构21上形成一层透明导电层220,透明导电层220覆盖第二半导体结构21,透明导电层220可采用氧化铟锡、氧化镓锌、氧化锌或氧化铟锌等材料制成。在一些实施例中,透明导电层220覆盖部分第二半导体结构21,在透明导电层220的两侧,透明导电层220与第二半导体层形成台阶228。在其他实施例中,透明导电层220可完全覆盖第二半导体结构21。当半导体外延结构20上设置有缺口23时,透明导电层220可覆盖第一半导体层203。
[0156]
如图20所示,在形成透明导电层220后,可分别在第一半导体层203和透明导电层220上沉积金属材料,例如沉积钛/氮化钛阻挡层及金属钨,在第一半导体层203上形成第一导电插塞221,在透明导电层220上形成第二导电插塞222。第一导电插塞221和第二导电插塞222齐平,且第一导电插塞221覆盖部分第一半导体层203,第二导电插塞222覆盖部分透明导电层220。在一些实施例中,可在半导体外延结构20的一侧开设开孔,且开孔的底壁与第一半导体层203接触,在开孔的侧壁上铺设绝缘物质,并在开孔内以及开口上形成第一导电插塞221。在其他实施例中,半导体外延结构20上设置有缺口23,可直接在缺口23上形成第一导电插塞221。
[0157]
如图20所示,在形成第一导电插塞221和第二导电插塞222后,在第一半导体层203和透明导电层220上依次沉积反射层223和保护层224。反射层223覆盖透明导电层220和台阶228,且暴露部分第一导电插塞221和第二导电插塞222。保护层224覆盖反射层223,以及部分或全部第一导电插塞221和第二导电插塞222。在形成反射层223和保护层224后,蚀刻二极管芯片外侧的保护层224、反射层223和半导体外延结构20,形成沟槽229。在沟槽229内以及保护层224上沉积绝缘层225,绝缘层225完全覆盖第一导电插塞221和第二导电插塞222。对绝缘层225和保护层224进行蚀刻,在第一导电插塞221和第二导电插塞222上方形成开口,且开口暴露出部分第一导电插塞221和部分第二导电插塞222,且开口的面积大于第一导电插塞221和第二导电插塞222的径向尺寸,在开口内沉积金属,形成与第一导电插塞221连接的第一电极226,与第二导电插塞222连接的第二电极227。再经过激光切割与劈裂,点分完成后,形成微型发光二极管。
[0158]
如图21所示,可在发光二极管上增加其他结构以改变微型发光二极管的出光方向,具体可根据具体需求改变微型发光二极管的出光方向。当微型发光二极管作为背光时,为减少混光距离,进而实现显示器等电子设备的超薄需求,可设置大角度的微型发光二极管。在一实施例中,可在微型发光二极管的衬底200上,且位于相对于半导体外延结构20的
一侧,设置散光叠层230,以增加微型发光二极管的出光角度,使微型发光二极管的角度大于等于160度。为方便描述,本技术将半导体外延结构20所在的一侧定义为衬底200的上表面,将衬底200相对于半导体外延结构20的一侧定义为下表面。
[0159]
如图21所示,散光叠层230包括设置在衬底200下表面的引光层231、第一反射层232、光震荡层233和第二反射层234。具体的,引光层231覆盖引光层231的下表面,且引光层231的折射率与衬底200的折射率相同,可保证光在引光层231上不发生偏转。引光层231的厚度可根发光层发出的光的波长以及引光层231的厚度设定,且引光层231的厚度符合的关系为:引光层231的厚度=波长/4
×
折射率。在一些实施例中,衬底200为蓝宝石衬底200,蓝宝石的折射率为1.77,则引光层231选用与蓝宝石折射率相同的氧化铝(al2o3)或氧化镁(mgo)制成。引光层231的厚度具体例如为10~200nm,又例如为60~80nm。在其他实施例中,当衬底200为其它材料制成时,可选择对应的引光层231材料,以及对应设置引光层231的厚度。
[0160]
如图21所示,第一反射层232位于引光层231相对于衬底200的一侧,且第一反射层232覆盖引光层231。第一反射层232为正向反射层223,允许由衬底200方向发出的光穿过第一反射层232,第一反射层232相对于衬底200方向发出的光将被第一反射层232反射。在一些实施例中,第一反射层232为周期循环生长的三氧化二钛(ti2o3)层和二氧化硅(sio2)层,且第一反射层232例如包括4~6个周期的ti2o3和sio2,又例如包括5个周期的ti2o3和sio2。其中三氧化二钛层覆盖引光层231,且三氧化二钛层的厚度例如为55~60nm,二氧化硅层覆盖三氧化二钛层,且二氧化硅层的厚度例如为90~100nm。
[0161]
如图21所示,光震荡层233位于第一反射层232相对于引光层231的一侧,且光震荡层233覆盖第一反射层232。光震荡层233的折射率小于衬底200的折射率,在一些实施例中,光震荡层233可选用折射率为1.46的二氧化硅(sio2)、折射率为1.38的氟化镁(mgf2),折射率为1.351的氮化钛(tin)或折射率为1.433的氟化钙(caf2)中的一种或多种制成。光震荡层233的厚度例如为100~500nm,又例如为300~400nm,可避免光震荡层233过厚,容易开裂,以及震荡层太薄,导致亮度损失太大,微型发光二极管最终发光的光的强度较弱。
[0162]
如图21所示,第二反射层234位于光震荡层233相对于第一反射层232的一侧,且第二反射层234覆盖光震荡层233。第二反射层234为反向反射层223,第二反射层234相对于衬底200方向发出的光穿过,由衬底200方向发出的光将被第二反射层234反射。在一些实施例中,第二反射层234为周期循环生长的二氧化硅(sio2)层和三氧化二钛(ti2o3)层,且第二反射层234例如包括2~3个周期的sio2和ti2o3,且二氧化硅层的厚度例如为90~100nm,三氧化二钛层覆盖二氧化硅层,三氧化二钛层的厚度例如为55~60nm。
[0163]
如图21所示,通过在微型发光二极管的衬底200下表面设置散光叠层230,当半导体外延结构20发出的光依次穿过引光层231、第一反射层232、光震荡层233后,被第二反射层234反射,在光震荡层233内发生偏折,当光反射或第一反射层232时,再被第一反射层232反射,最终从光震荡层233的侧边溢出。导致最终发出的光与衬底200所在的平面所呈的角度大于160度。
[0164]
如图22所示,在另一实施例中,为避免在形成显示装置或照明装置时,微型发光二极管的发光角度过大,造成相邻不同颜色的微型发光二极管颜色互相干预。还可以通过在衬底200外侧加遮挡层235,以缩小微型发光二极管的发光角度。在本实施例中,可通过在微
型发光二极管的外侧形成遮挡层235,以缩小发光角度。
[0165]
如图22所示,遮挡层235设置在微型发光二极管的外侧,具体如图23、图24以及图25所示,遮挡层235设置在衬底200的外侧,且与衬底200的侧壁贴合。遮挡层235可覆盖衬底200的一个或多个侧面,可通过在衬底200侧壁的不同位置设置遮挡层235,以改变微型发光二极管的发光范围。在一些实施例中,如图24所示,遮挡层235可以覆盖例如衬底200相对的两个侧面,此时微型发光二极管的发光角度的范围例如为90~115度,最大发光角度例如为115度。在另一些实施例中,如图25所示,遮挡层235可以覆盖衬底200的例如四个侧面,此时微型发光二极管的发光角度的范围例如为90~105,最大发光角度例如为105度。在其他实施例中,遮挡层235覆盖衬底200的例如一个侧面,此时微型发光二极管的发光角度的范围例如为90~120,最大发光角度例如为120度。遮挡层235覆盖衬底200的例如三个侧面,此时微型发光二极管的发光角度的范围例如为90~110,最大发光角度例如为110度。
[0166]
如图23,遮挡层235包括还原层236和镀膜层237,其中还原层236为衬底200侧壁的表面重新结晶与粗化形成。在本实施例中,衬底200例如是蓝宝石衬底200,可通过激光划边的方式将衬底200的侧壁重新结晶粗化。其中激光的光线波长例如为800~1200nm,通过激光将蓝宝石衬底200(al2o3)重新结晶成al或alo,最终重结晶后的衬底200侧壁表面可自然粗化。且重新结晶形成的al或alo均为不透光层且可以对光线进行反射,自然粗化的衬底200侧壁也可以增加反射。
[0167]
如图22和图23,镀膜层237覆盖在还原层236上,且例如可以在真空环境下,且在压力例如为1
×
103~9
×
103torr的条件下,通过蒸镀或溅射的方式在还原层236上形成镀膜层237。其中镀膜层237包括多层组合层,例如包括第一组合层238和第二组合层239,且第二组合层239覆盖在第一组合层238上。镀膜层237可以为金属层组合层,也可以为氧化层组合层。在一些实施例中,第一组合层238的材料为al,或者为al和ni,第二组合层239的材料为ti或pt,且镀膜层237的厚度例如为20~300nm。在其他实施例中,第一组合层238的材料为sio2或mgf2,第二组合层239的材料为ti2o5或sinx,且镀膜层237的厚度例如为50~100nm。其中,当镀膜层237是氧化组合层时,镀膜层237可以包括多个循环设置的第一组合层238和第二组合层239。
[0168]
如图26所示,在一些实施例中,半导体外延结构在长晶的过程中,半导体外延结构的表面可能会存在凹凸不平的缺陷,导致反射层223的效果不好。本实施例提供的一种微型发光二极管,可填平半导体外延结构的表面,同时可保证整体的膜层的应力平衡,避免因张应力造成镀膜层裂开,还可以增加出光效果。
[0169]
如图26所示,半导体外延结构20与透明导电层220接触的表面上存在凹凸不平的缺陷,可在图20、图21或图22所示的微型发光二极管的基础上,在透明导电层220和反射层223之间设置复合填平层240,以改善半导体外延结构上的缺陷,在保护层224和绝缘层225之间设置压合层243,以确保整体的膜层应力平衡,避免因张造成镀膜裂开。
[0170]
如图26至图27,填平层240位于透明导电层220相对于半导体外延结构的一侧,且覆盖透明导电层220。填平层240透明且不导电,且填平层240中的颗粒先粗后细。具体的,填平层240包括第一填平层240a和第二填平层240b,且第一填平层240a覆盖透明导电层220,且第一填平层240a的厚度例如为200~500nm,具体又例如为250nm或300nm,以完全覆盖半导体外延结构上的缺陷。第二填平层240b覆盖第一填平层240a,且第二填平层240b的厚度
例如为50~300nm,以填满第一填平层240a内颗粒之间的间隙。
[0171]
如图26至图27,在本实施例中,可采用pecvd沉积或蒸镀的方法在透明导电层220上形成填平层240,其中第一填平层240a的颗粒密度例如3~4g/cm3,且第一填平层240a的材料例如为氧化铝(al2o3)或氟化镁(mgf3),氧化铝的密度为3.5~3.9g/cm3,氟化镁的的密度为3.148g/cm3。第二填平层240b的颗粒密度例如为1.5~3g/cm3,且第二填平层240b的材料例如为二氧化硅(sio2)或氮化硅(sin),二氧化硅的密度为2.2g/cm3,氮化硅的密度为1.8~2.7g/cm3。填平层240先使用粗颗粒形成第一填平层240a,镀的速度快,后面再补细颗粒填平形成第二填平层240b,就不会有空洞,且膜层质料好,不容易脱落。
[0172]
如图26至图27,填平层240上设置有多个开孔241,且多个开孔241呈阵列设置。例如可以采用boe蚀刻液湿蚀刻出开孔241,或采用电感耦合等离子体(icp)干蚀刻的方法蚀刻出开孔241。开孔241呈柱状设置,且穿透第一填平层240a和第二填平层240b,其中开孔241的截面可呈圆形、方形、多边形或其他形状。在本实施例中,开孔241的孔径例如为3~5um,相邻开孔241之间的间隔例如为3~5um。孔径以及相邻开孔241之间的间隔设置可避免开孔241与间距过小,无法满足工艺需求,同时避免开口过大,填平层240与导电层之间的接触面积过小,而导致填平层240两侧电压差过高。
[0173]
如图26所示,保护层224覆盖在反射层223上,压合层243覆盖在保护层224上,绝缘层225覆盖在压合层243上。压合层243包括包括第一压合层和第二压合层,且第二压合层覆盖在第一压合层上。在室温条件下,第一压合层和第二压合层的厚度之比例如为3:8。且第一压合层和第二压合层的厚度例如为30~600nm,可避免压合层243太薄无法作用,以及太厚会出现开裂等问题。在一些施例中,压合层243包括例如1层第一压合层和例如1第二压合层。在其他实施例中,压合层243包括多个周期循环的第一压合层和第二压合层。
[0174]
如图26和图27所示,可采用pecvd沉积或蒸镀的方法在透明导电层220上形成压合层243,其中第一压合层的材料例如为二氧化硅(sio2),第二压合层的材料例如为二氧化钛(tio2)或ti2o5。
[0175]
请结合图26和图28所示,微型发光二极管安装在基板244上时,可通过第一焊盘245将第一电极226焊接在基板244上,通过第二焊盘246将第二电极227焊接在基板244上。当基板244表现出压应力,基板244上设置的薄膜表现出张应力时,基板244和薄膜的两侧会向薄膜一侧翘曲。当基板244表现出张应力,基板244上设置的薄膜表现出压应力时,基板244和薄膜的两侧会向基板244一侧翘曲。在本实施例中,基板244在室温条件下会表现出较小的张应力,而压合层243薄膜的应力变化情况如下:第二压合层(tio2或ti2o5)的厚度在300nm时,在室温下表现出的是张应力,例如为114mpa,第一压合层(sio2)的厚度在400nm时,在室温表现出是压应力,例如为
‑
56mpa。因基板244本身是另一个方向的张应力,所以第一压合层与第二压合层厚度要在3:8的组合,此时压合层243表现出的应力将近为0,且有多一点压应力,可与基板244的表现出的张应力抵消。在其他温度时,基板244会因应力过大翘曲,可通过调整薄膜的应力,使基板244和基板244上的薄膜达到平衡。
[0176]
如图29和图30所示,为了配合微型发光二极管高效节能的要求,对于倒装的亮度也需要越来越高。半导体外延结构在长晶的过程之中,由于表面易形成缺陷,产生表面凹凸不平,导致后面镀上反射镜之后,不会形成完全的镜面,导致于色散,光不集中,在封装成白光后,导致光效不好。本实施例提供的倒装微型发光二极管,如图29和图30所示,利用一特
殊复合填平层240,使外延表面填平,且使得光垂直反射能力增加。同时使用一压合层243,确保整体的膜层应力平衡,避免因张应力造成镀膜层237裂开,同时此两种设计,也将倒装所需要的光垂直反射能力强化,以增加出光效。
[0177]
如图31所示,微型发光二极管在使用时需要通过焊垫焊接在电路上,在焊接时,在焊垫与电极之间易产生空洞,可在电极上形成一层特殊形状的金属叠层250,以增加电极可焊性的良率。在本实施例中,金属叠层250的厚度例如为20~100um,且包括介质层251和软性金属层252,介质层251设置在第一电极226和第二电极227上,软性金属层252设置在介质层251上。具体的,介质层251采用合金制成,且例如包括镍(ni)层,以及金(au)、锡(sn)的合金。可在黄光条件下,在第一电极226和第二电极227上首先蒸镀或溅镀一层厚度例如为10~15nm的镍,再在镍上面蒸镀或溅镀一层厚度例如30~1000nm的金、锡合金,形成介质层251,且金、锡合金中金与锡的比例例如为80:20。其中介质层251在各点的厚度相同,整体呈柱状,具体可呈圆柱状。在第一电极226和第二电极227上形成一层介质层251,可防止软性金属层252扩散。
[0178]
如图31所示,软性金属层252设置在介质层251上,且覆盖介质层251。软性金属层252采用金属或合金制成,例如为金(au)、锡(sn)或银(ag)制成,或采用锡(sn)的合金制成。可在黄光条件下,在介质呈上镀或溅镀一层厚度例如为20~100um的金属或者合金,形成软性金属层252。其中随着软性金属层252厚度的增加,软性金属层252的半径逐渐减小,软性金属层252具体例如可呈圆台设置。当微型发光二极管与焊垫焊接时,可以将焊垫与电极之间的空洞顺势赶出去,再利用软性金属的特性,可填补不平的焊垫区域,更可以加大容许衬底200翘曲的窗口,增加产品的可靠性。
[0179]
如图32所示,在另一实施例中,可通过一种特殊的焊盘代替导电插塞和电极的作用,例如使用第一导电结构260代替第一导电插塞221和第一电极226,使用第二导电结构261代替第二导电插塞222。第一导电结构260和第二导电结构261具有伸缩性,可以是使用不平整的基板,以及焊接中回流焊的热膨胀产生的应力所产生的不良,同时减少封装空洞率。在本实施例中,第一导电结构260电性连接于第一半导体层,第二导电结构261电性连接于第二半导体层。第一导电结构260包括垫平层262、黏合层263、伸缩层264、叠嶂层265以及焊接层266,第二导电结构261包括黏合层263、伸缩层264、叠嶂层265以及焊接层266。
[0180]
如图32所示,垫平层262设置在半导体外延结构20的第一半导体层上,且垫平层262的高度与透明导电层220的高度相等。通过设置垫平层262,可使第一导电结构260和第二导电结构261的高度相等,避免造成歪斜。可以在200~300度的条件下,采用化学气相沉积法在第一半导体层上沉积一层垫平层262。且垫平层262的材料例如为sio2、sinx、al2o3、mgo或aln,垫平层262的厚度例如为900~1500nm,具体可与透明导电层220的高度相同。
[0181]
如图32所示,第一导电结构260的黏合层263设置在垫平层262上,第二导电结构261的黏合层263设置在透明导电层220上,第一导电结构260和第二导电结构261的黏合层263高度相等。可以在开光黄的条件下,在垫平层262或透明导电层220上蒸镀或溅镀一层黏合层263。黏合层263的材料例如为cr、ni、ti或氧化铟锡(ito),黏合层263的厚度例如为5~100nm,且黏合层263低于绝缘层225的高度。
[0182]
如图32所示,第一导电结构260和第二导电结构261的黏合层263上设置有伸缩层264,且第一导电结构260上的伸缩层264和第二导电结构261上的伸缩层264高度相等。可以
在开黄光的条件下,在黏合层263上蒸镀或溅镀一层伸缩层264。伸缩层264例为钛和铝的合金(ti/al)、镍和铝的合金(ni/al)、钛和银的合金(ti/ag)、或镍和银的合金(ni/ag)形成的复合层。伸缩层264高于绝缘层225,且伸缩层264的厚度例如为(50~200)*n nm,n的范围为3~9,当n值太小时,伸缩层264没有伸缩作用,当n数字太大,伸缩层264的电压偏高。
[0183]
如图32所示,第一导电结构260和第二导电结构261的伸缩层264上设置有叠嶂层265,且第一导电结构260上的叠嶂层265和第二导电结构261上的叠嶂层265高度相等。可以在开黄光的条件下,在伸缩层264上蒸镀或溅镀一层叠嶂层265。叠嶂层265的材料例如为铂(pt)和钛(ti)的合金,或钛(ti)和镍(ni)的合金,且叠嶂层265的厚度例如为100~300nm。
[0184]
如图32所示,第一导电结构260和第二导电结构261的叠嶂层265上设置有焊接层266,且第一导电结构260上的焊接层266和第二导电结构261上的焊接层266高度相等。可以在开黄光的条件下,在叠嶂层265上蒸镀或溅镀一层焊接层266。焊接层266的材料例如为锡(sn)或金锡合金(ausn),且焊接层266的厚度例如为80000~100000nm。
[0185]
如图33所示,微型发光二极管用于背光及照明时,由于各种不良环境的影响,常常造成微型发光二极管失效,尤其是水汽的渗入,对于微型发光二极管的损坏特别严重。本发明提供一种微型发光二极管,在发光区和电极上设置一特殊的防水保护层270,可以让水份不致停留在芯片上,使芯片保持干燥,进而避免水气的不良可防止水汽入侵。
[0186]
如图33所示,防水保护层270包括保护膜层271、疏水性膜层272和水栅栏层273。其中,防水保护层270设置在透明导电层220以及部分第一电极226和第二电极227上,疏水性膜层272设置在防水保护层270上,水栅栏层273设置在疏水性膜层272上。请结合图32所示,防水保护层270覆盖透明导电层220,并向着第一电极226和第二电极227延伸,且覆盖第一电极226和第二电极227的侧壁以及部分顶壁。如图34所示,保护膜层271包括第一防水保护层274、第二防水保护层275和第三防水保护层276,第二防水保护层275设置再第一防水保护层274上,第三防水保护层276设置在第二防水保护层275上。且可以采用离子体增强化学的气相沉积法分别沉积第一防水保护层274、第二防水保护层275和第三防水保护层276。其中,第一防水保护层274为氧化层,且厚度例如为100~300nm。第二防水保护层275为氧化层与氮化层的渐变层,且厚度例如为20nm,第三防水保护层276为非亲水性材料的氮化层,且厚度例如为20~50nm。具体的,第一防水保护层274的材料例如为二氧化硅(sio2),第二防水保护层275的材料例如为氮氧化硅(sion),第三防水保护层276的材料例如为氮化硅((sinx)。
[0187]
如图33所示,疏水性膜层272设置在防水保护层270上,并覆盖防水保护层270,且可以使用电子束蒸镀(electron beam evaporation)的方式形成疏水性膜层272,疏水性膜层272的厚度例如为2~5um。其中疏水性膜层272为超疏水的氮化层,例如可以为金属氮化层,具体例如可以为氮化硼(bn)或氮化铝(aln),以及其他超疏水的金属氮化层。
[0188]
如图33和图35所示,水栅栏层273设置在疏水性膜层272上,可通过对疏水性膜层272退火再结晶,在疏水性膜层272上形成多个突出结构,以形成水栅栏层273。水栅栏层273的厚度大于或等于1um,具体例如为2um,且水栅栏层273的厚度具体例如为突出结构的高度。具体可以在形成疏水性膜层272的时候,设置较厚的疏水性膜层272,具体的,退火结晶前的疏水性膜层272的厚度等于最终形成的疏水性膜层272的厚度与水栅栏层273的厚度之和。在形成疏水性膜层272后,将疏水性膜层272的顶部在200~300度的条件下,快速高温退
火或炉管退火,并持续时间30~60分后,使疏水性膜层272的顶部表面颗粒化,形成突出结构,多个突出结构组成水栅栏层273。
[0189]
如图36(a)所示,一般亲水性表面上液滴边缘切线与基准面之间的夹角小于90度,如图36(b)所示,疏水性表面液滴边缘切线与基准面之间的夹角范围可以为例如90
‑
150度,如图36(c)所示,超疏水性表面液滴边缘切线与基准面之间的夹角大于150度。本发明提供的保护膜层271的疏水性逐渐增强,在保护膜层271的最外层形成超疏水性表面,且在超疏水性的金属氮化层表面形成突出结构的水栅栏层273,进一步防止水汽入侵。
[0190]
如图37所示,在将发光二极管转移至显示基板上后,需要将衬底200剥离,以提高亮度。因电极设置在半导体外延结构的两侧,且两个电极之间为空洞结构,在衬底200剥离时,易导致半导体外延结构产生龟裂,造成漏电死灯。本发明提供一种微型发光二极管,可防止衬底200剥离时,半导体外延结构断裂。
[0191]
如图37所示,本实施例提供的一种微型发光二极管,在第一电极226和第二电极227之间形成支撑层280,且支撑层280填满第一电极226和第二电极227之间的间隙。具体可采用蒸镀、溅射或化学气相沉积法形成支撑层280,且支撑层280的材料例如为sio2、sinx、al2o3或类钻石膜(dlc)。支撑层280的高度不高于第一焊盘245和第二焊盘246,支撑层280的厚度具体例如可为300~4000nm。该微型发光二极管利用一个特殊的支撑层280,可以将会裂开的部份形成一个支撑,使其不会裂开,避免取晶顶伤,同时也可以避免因底层助焊剂或是锡膏扩散而导致漏电。
[0192]
如图38,形成微型发光二极管后,需要将多个微型发光二极管转移至基板上,本发明提供一种半导体设备,可将多个微型发光二极管切割后转移至基板上。其中,本实施例所述的半导体设备例如为一种微型发光二极管转移装置,所述微型发光二极管转移装置上设置有矩阵切割条,可将衬底上的多个微型发光二极管的区分成独立的晶圆,且每个晶圆上中至少包括一个mini led或micro led。矩阵吸盘可将微型发光二极管转移至基板上。本实施例提供的微型发光二极管转移装置可进行一体化切割,可提高作业效率。
[0193]
如图38所示,微型发光二极管转移装置包括基座301,筒座302设置在基座301上方,且筒座302内设置空槽,空槽的中性线与筒座302的中性线重合。升降台303设置在所述空槽内,升降台303顶面高出筒座302的顶面。旋转台304设置在升降台303上,悬臂305一端连接旋转台304,固定臂306连接悬臂305远离旋转台304的一端。转移板308设置在固定臂306下方,矩阵切割条309和矩阵吸盘310固定在转移板308,且矩阵吸盘310位于相邻矩阵切割条309之间。
[0194]
如图38,基座301设置在微型发光二极管转移装置的底部,对整个微型发光二极管转移装置起支撑作用。且在一些实施例中,为了实现微型发光二极管转移装置的移动,基座301可以设置运动轮组,运动轮组可以配置止动板。在运动轮组和止动板的作用下实现整个微型发光二极管转移装置位置的灵活调节。基座301上方可以设置筒座302,筒座302内部可以设置空槽,升降台303设置在空槽内,升降台303可以为圆柱体。升降台303的顶部高出筒座302,升降台303的内部设置有升降电机,控制升降台303在垂直方向上的运动。
[0195]
如图38,旋转台304设置在升降台303上,旋转台304可以为圆柱体,旋转台304的中心轴线与升降台303的中心轴线重合,且旋转台304的直径小于升降台303的直径。在一些实施例中,旋转台304的内部设置有旋转马达,旋转马达控制旋转台304做双向圆周运动。旋转
台304的侧面连接悬臂305。悬臂305与旋转台304焊接连接。悬臂305内部可以为中空结构,并可以设置有加强筋。悬臂305在旋转台304内部旋转电机的带动下沿着悬臂端部运动轨迹线314做双向圆周运动。
[0196]
如图38和图39,转移板308设置在固定臂306的下方。转移板308上表面与固定臂306对应的位置设置有螺栓孔。转移板308通过螺栓307和固定板306连接。转移板308通过悬臂305在旋转台304内部旋转电机的带动下沿着悬臂端部运动轨迹线314做双向圆周运动,实现晶圆在不同加工工艺腔中的转移。转移板308的下表面设置矩阵切割条309和矩阵吸盘310。连接转移板308和矩阵切割条309固定在转移板308下方,且矩阵吸盘310位于相邻矩阵切割条309之间,矩阵吸盘310可批量提取并固定待转移至目标阵列基板的晶圆311裸片。
[0197]
如图38和图39,矩阵切割条309和矩阵吸盘310固定在转移板308的下表面,且矩阵切割条309可以呈网格状分布,矩阵吸盘310交叉设置在矩阵切割条309的相邻切割条之间的区域。矩阵吸盘310的高度小于矩阵切割条的高度。矩阵切割条309端部可以为倒梯形结构,也可以为棱锥形结构,也可以为其他类似结构的组合或者结合。
[0198]
如图38和图41,晶圆311在载台12上完成不同的加工工艺过程,相邻晶圆之间形成切割槽。切割槽可以分为横向切割槽315和纵向切割槽316,切割槽的数量根据不同待加工晶圆的数量而不同。在一些实施例中,h1~h8为横向切割槽315,s1~s8为纵向切割槽316。矩阵切割条309对应横向切割槽315和纵向切割槽316,对晶圆311进行一体化切割,在横向和纵向上分割不同晶圆311。如图39所示,相邻晶圆311之间可以确定锯力线317,锯力线317垂直距离的切割面为应力集中面318。切割力由锯力线317作用于应力集中面318,分割完成后,矩阵吸盘310对晶圆311进行吸附固定。被吸附的晶圆311随着转移板308在旋转台304的旋转电机带动下沿着悬臂端部运动轨迹线314做双向圆周运动。在本发明的其他实施例中,可以将矩阵吸盘替换为如机械抓取、胶粘、静电吸附、气体吸附、电磁吸附等采用了相近原理的矩阵吸附体,实现晶圆311的一体化切割与转移。
[0199]
如图41,在本实施例中,锯片从晶圆311表面划过,对于薄的晶圆,锯片降低到晶圆的表面划出一条深入1/3晶圆厚度的浅槽。芯片分离方法仍沿用划片法和钻石划线法中所述的圆柱滚轴施压完成。
[0200]
如图42至图43,在一些实施例中,将微型发光二极管转移至基板244上后,基板244上设置有驱动电路296,发光二极管通过焊盘与驱动电路296连接,可形成微型发光二极管显示面板。在本实施例中,还提供一种微型发光二极管显示面板,包括基板244以及设置在基板244上的一种具有多个纳米孔的微型发光二极管,且纳米孔内设置有量子点。
[0201]
如图42至图43,本实施例中的微型发光二极管包括第一半导体层291以及设置在第一半导体层291上的第二半导体层292。其中,第一半导体层291可以连接有电极,第一半导体层291例如为n型氮化镓层。第二半导体层292设置在第一半导体层291上,且第二半导体层292也为氮化镓层,且例如为n型氮化镓层。在第二半导体层292上设置有多个阵列状的纳米孔293,具体可以将n型氮化镓层浸入酸性溶液中并施加偏压,在n型氮化镓层中形成纳米级孔隙,从而驱动n型氮化镓层的电化学蚀刻,形成纳米孔293,且可以通过改变施加的偏压或gan中硅掺杂浓度,改变纳米孔293的密度以及大小。纳米孔293的直径例如为50~200nm,相邻纳米孔293之间的间距例如为30~300nm。
[0202]
如图42至图43,在本实施例中,纳米孔293穿透第二半导体层292,当纳米孔293中
不设置量子点时,微型发光二极管发出紫外光或蓝色光。在纳米孔内293中设置有红色量子点295时,微型发光二极管可以发出红色的光,在纳米孔293内设置有绿色量子点294时,微型发光二极管可以发出绿色的光。在一些实施例中,红色量子点295、绿色量子点294以及空置的纳米孔293在第二半导体层292上依次排列。在其他实施例中,第二半导体层292上包括多个依次设置的第一类型发光阵列、第二类型发光阵列以及第三类型发光阵列。其中,第一类型发光阵列中的纳米孔293中填满红色量子点295,第二类型发光阵列中的纳米孔293中填满绿色量子点294,第三类型发光阵列中的纳米孔293为空置的纳米孔293。其中第一类型发光阵列、第二类型发光阵列和第三类型发光阵列的形状和大小相等,以使形成的微型发光二极管发光更加均匀,且阵列的长度例如为100~2000nm,宽度例如也为100~2000nm。将量子点设置子纳米孔293内可以提高量子点的吸收率,延长量子点的使用寿命。
[0203]
如图42至图43,在形成微型发光二极管显示面板时,基板244上设置有驱动电路296,且驱动电路296可以设置在基板244的表面,也可以设置在基板244内。将微型发光二极管与基板244键合后,驱动电路296可驱动微型发光二极管显示发光。在微型发光二极管上设置纳米孔293,并在纳米孔293内填充不同颜色的量子点,可避免不同色发光二极管的分拣,降低生产成本。
[0204]
请参阅图44,本公开还提供一种电子装置,所述电子装置包括微型发光二极管显示面板300以及电子装置本体301,微发光二极管面板300与电子装置本体301连接,其中微发光二极管面板300包括电路基板和多个微型发光二极管芯片。电子装置本体301包括控制器302、存储器303、电源304。其中,电源304可以将市电(220v交流电)转换为控制器302和存储器303所需要的直流电,同时为微发光二极管面板300提供电源。存储器303与电源304连接,用于存储电子装置工作的相关数据,控制器302与电源304连接,同时与存储器303连接,电源304用于为控制器302供电,控制器所述执行存储器303内的程序控制所述电子装置。其中,电子装置可例如是显示面板、手机、手表、笔记本电脑、投载式装置、充电装置、充电桩、虚拟现实(vr)装置、扩充现实(ar)装置、可携式电子装置、游戏机或其他电子装置。
[0205]
如图45所示,当应用本公开的半导体外延结构来制造半导体器件时,所述半导体器件包括衬底200、缓冲层201、第一半导体层203、第二半导体层205、源极301、漏极302以及栅极303。其中,缓冲层1401设置于衬底200上,第一半导体层203设置于缓冲层201上,第二半导体层205设置于第一半导体层203上,源极301形成于第二半导体层205上,漏极302形成于第二半导体层205上,栅极303形成于第二半导体层203上,且位于源极301和漏极302之间。在第二半导体层205上设置有源掺杂区303和漏掺杂区304,且源掺杂区303和漏掺杂区304例如为n型重掺杂区,且源极301设置在源掺杂区303上,漏极302设置在漏掺杂区304上。
[0206]
如图46,当应用本公开的半导体器件来射频模组时,所述射频模组包括所述半导体器件。所述射频模组主要包括射频(radio frequency,rf)切换器件311、射频(radio frequency,rf)有源器件314、射频(radio frequency,rf)无源器件312和控制器件313。其中射频(radio frequency,rf)有源器件314可以是本技术中的所述半导体器件,射频(radio frequency,rf)无源器件312可以是电容器、电阻器和电感器等无源器件。其中,射频(radio frequency,rf)切换器件311、射频(radio frequency,rf)有源器件314、射频(radio frequency,rf)无源器件312和控制器件313均形成于半导体衬底200上。
[0207]
以上描述仅为本技术的较佳实施例以及对所运用技术原理的说明,本领域技术人
员应当理解,本技术中所涉及的发明范围,并不限于上述技术特征的特定组合而成的技术方案,同时也应涵盖在不脱离所述发明构思的情况下,由上述技术特征或其等同特征进行任意组合而形成的其它技术方案,例如上述特征与本技术中公开的(但不限于)具有类似功能的技术特征进行互相替换而形成的技术方案。
[0208]
除说明书所述的技术特征外,其余技术特征为本领域技术人员的已知技术,为突出本发明的创新特点,其余技术特征在此不再赘述。