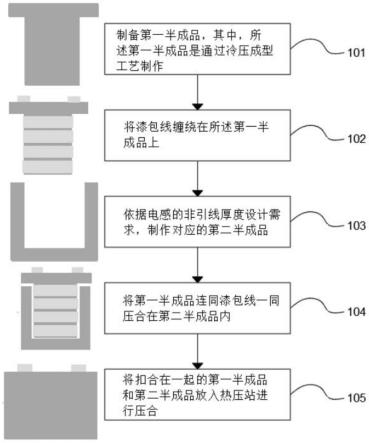
1.本发明属于电感技术领域,尤其涉及一种电感生产工艺。
背景技术:2.现有的电感热压填粉制程会受到粉材流动性和/或填粉板孔径的限制,导致电感的非引线面填粉量不足,从而成为电感感值的瓶颈。因此部分客户需求的高感值机种,现有的制程无法达成,或者良率较低。
技术实现要素:3.本发明提供了一种电感生产工艺,解决了现有技术中电感热压填粉制程,会受到粉材流动性和填粉板孔径的限制,导致电感的非引线面填粉量不足,从而成为电感感值的瓶颈的问题。
4.鉴于上述问题,本发明提出一种电感生产工艺,包括
5.s1.制备第一半成品,所述第一半成品包括平板和柱体,平板向下连接柱体,平板为矩形面且矩形面的各边沿自边沿线向外延伸形成边沿突出,相邻的两个边沿突出的侧边沿相互垂直形成垂直口,平板共形成四个垂直口。
6.s2.将漆包线缠绕在所述第一半成品的柱体。
7.s3.将第一半成品扣合在第二半成品内,所述第二半成品为柱形槽并能承装所述第一半成品的柱体,第一半成品的平板及边沿突出将所述第二半成品的顶部开口覆盖,并在平板的垂直口处保留与第二半成品的槽内联通的间隙,使漆包线的两端引线由其中的两个间隙引出,另外两个间隙中的至少一个能够作为填粉间隙。
8.s4.将扣合后的第一半成品和第二半成品一并放入热压站压合。
9.s5.将热压站压合后的成品间隔放置在平板上冷却。
10.进一步的,步骤s3包括
11.步骤3.1.第一半成品与第二半成品形成闭合体,漆包线缠绕第一半成品的柱体上并被包裹在第二半成品内。
12.步骤3.2.检测第一半成品与第二半成品间的贴合缝隙的间距,若所述贴合缝隙的间距小于设定值,则所述闭合体合格,若所述贴合缝隙的间距大于或等于设定值,则所述闭合体不合格,将所述闭合体重新分离并且再次进行植入。扣合后,使用ccd检测是否合格。
13.步骤3.3.将再次植入后的闭合体重复进行步骤3.1。
14.进一步的,所述设定值为2mm。
15.进一步的,步骤s4还包括,每一段压合后的产品间隔预设次数后检验其生产误差是否在正常范围内,若不是,则调整设备数据,并待调整后的设备生产的压合产品误差在正常范围内再进行批量生产。
16.进一步的,成品放置间隔为5cm,并且静置至产品冷却至室温。
17.进一步的,所述第一半成品通过冷压成型工艺制作。
18.进一步的,成品与平板之间还设置有垫板。
19.进一步的,平板为正方形面。
20.有益效果:与现有技术相比,本发明可以克服感值偏低、阻值偏高的技术难题,使电感有更高的感值以及更低的阻值,达到实现客户需求的电感感值和/或阻值的效果,并且可以实现量产的效果。
附图说明
21.图1为本发明实施例中一种电感生产工艺的工艺流程示意图。
22.图2为本发明实施例中的第一半成品的俯视图。
具体实施方式
23.本发明实施例提供了一种电感生产工艺,用于解决现有技术中电感热压填粉制程,会受到粉材流动性和填粉板孔径的限制,导致电感的非引线面填粉量不足,从而成为电感感值的瓶颈的问题。
24.本发明提供的技术方案是一种电感制备方法,包括:制备第一半成品,其中,所述第一半成品是通过冷压成型工艺制作。将漆包线缠绕在所述第一半成品上。依据电感的非引线厚度设计需求,制作对应的第二半成品。将第一半成品连同漆包线一同压合在第二半成品内,将扣合在一起的第一半成品和第二半成品放入热压站进行压合,压合过程中向第二半成品中注粉。将加工后的成品间隔放置在地面上冷却堆放。在制作第二半成品之前,工程研发人员会通过不同的厚度mapping测试,定义出来非引线侧所需要的厚度范围值,产线生产人员依据此范围进行制作。
25.在上述方案中,所述第一半成品包括平板和柱体,平板向下连接柱体,平板为矩形面且矩形面的各边沿自边沿线向外延伸形成边沿突出,相邻的两个边沿突出的侧边沿相互垂直形成垂直口,平板共形成四个垂直口。所述第二半成品为柱形槽并能承装所述第一半成品的柱体,第一半成品的平板及边沿突出将所述第二半成品的顶部开口覆盖,并在平板的垂直口处保留与第二半成品的槽内联通的间隙,使漆包线的两端引线由其中的两个间隙引出,另外两个间隙中的至少一个能够作为填粉间隙。
26.与现有技术相比,本发明通过制成第二半成品而非直接通过填粉的方式包裹具有包绕线的柱体,使得本发明能够实现批量生产,并且降低了填粉对线圈的刺破可能,并且通过垂直口的设置,正负极接头无需通过折线引出,并保证了热压填粉的均匀性,可以克服感值偏低、阻值偏高的技术难题,使电感有更高的感值以及更低的阻值,达到实现客户需求的电感感值和/或阻值的效果。
27.下面通过附图以及具体实施例对本发明技术方案做详细的说明,应当理解本技术实施例以及实施例中的具体特征是对本技术技术方案的详细的说明,而不是对本技术技术方案的限定,在不冲突的情况下,本技术实施例以及实施例中的技术特征可以相互组合。
28.本文中术语“和/或”,仅仅是一种描述关联对象的关联关系,表示可以存在三种关系,例如,a和/或b,可以表示:单独存在a,同时存在a和b,单独存在b这三种情况。另外,本文中字符“/”,一般表示前后关联对象是一种“或”的关系。
29.实施例一
30.图1为本发明实施例中一种电感生产工艺的工艺流程示意图。如图1所示,本发明实施例提供了一种电感生产工艺,包括:
31.准备板材,对板材进行打磨整理,将打磨好的板材堆放在一起,将所述板材置入冷压成型设备中;
32.步骤s101,制备第一半成品,其中,所述第一半成品是通过冷压成型工艺制作;
33.步骤s102,将漆包线缠绕在所述第一半成品上;
34.步骤s103,依据电感的非引线厚度设计需求,制作对应的第二半成品;
35.步骤s104,将第一半成品连同漆包线一同压合在第二半成品内;
36.步骤s105,将扣合在一起的第一半成品和第二半成品放入热压站进行压合;
37.冷却堆放,将加工后的成品间隔放置在地面上,其中,成品与地面之间还设置有垫板。
38.通过将传统的直接在立柱热压填粉模式,改善为提前压好热压所需的纵向截面为u型的第二半成品,再经过热压成型后产品具有可以克服感值偏低、阻值偏高的技术难题,使电感有更高的感值以及更低的阻值,达到实现客户需求的电感感值和/或阻值的效果。
39.在一种技术方案中,所述将第一半成品连同漆包线一同压合在第二半成品内包括以下步骤:步骤1011,第一半成品与第二半成品形成闭合体,其中的漆包线被包裹在第一半成品和第二半成品内;
40.步骤1012,检测第一半成品与第二半成品间的贴合缝隙的间距,若所述贴合缝隙的间距小于2mm,则所述闭合体合格,若所述贴合缝隙的间距大于或等于2mm,则所述闭合体不合格,将所述闭合体重新分离并且再次进行植入;
41.步骤1013,将再次植入后的闭合体重复进行步骤1012。
42.可选地,测量第一半成品与第二半成品间的贴合缝隙的间距可以使用游标卡尺人工测量,也可以使用电子测量设备测量,测量的数据误差在10um以内即可。
43.在一种技术方案中,所述第一半成品纵向截面为t型。
44.在一种技术方案中,所述第一半成品包括平板和柱体,平板向下连接柱体,平板为矩形面且矩形面的各边沿自边沿线向外延伸形成边沿突出,相邻的两个边沿突出的侧边沿相互垂直形成垂直口,平板共形成四个垂直口。该方案相较于直接使用矩形面的平板的方案,提供四个对称的垂直口对包绕线接头引出和热压站压合中作为填粉口。其能取得的效果主要包括以下几点:
45.对于包绕线的接头引出,现有直接使用矩形面的平板的方案其引出点是在长边侧并且处于相对位置,引出点位置相对固定,绕线时要考虑引出点位置,需经过折线将引线折到引出点。本发明形成的四个对称垂直口均可以作为引出位置,绕线时无需折线则可就近引出引线。
46.对于热压站压合步骤,而现有直接使用矩形面的平板的方案其加料点是在长边侧并且处于相对位置,加料后难以使得加料均匀分散在第二半成品和第一半成品之间,需要使用特别的振动盘配合。而本发明的四个对称垂直口均可以作为加料口,且对称口对称设置,加料均匀、分散均匀,使用一般性振动盘配合即可。
47.在一种技术方案中,平板为正方形面,能保证更好的对称性。
48.在一种技术方案中,所述将漆包线缠绕在所述第一半成品上步骤包括:将所述漆
包线缠绕在纵向截面为t型的半成品的下部。
49.在一种技术方案中,所述第二半成品纵向截面为u型。
50.在一种技术方案中,所述第一半成品与第二半成品形成闭合体包括:将纵向截面为t型半成品缠绕有漆包线的部分压合在所述纵向截面为u型半成品的开口处,所述纵向截面为t型半成品的顶部两端将所述纵向截面为u型半成品的顶部封闭。
51.在一种技术方案中,在所述将扣合在一起的第一半成品和第二半成品放入热压站进行压合步骤之后,所述生产工艺还包括,每一段压合后的产品间隔预设次数后检验其生产误差是否在正常范围内,若不是,则调整设备数据,待调整后的设备生产的压合产品误差在正常范围内,再进行批量生产。
52.在一种技术方案中,所述加工后的成品放置间隔为5cm,并且需要静置三个小时,使得产品冷却至室温。
53.本发明能解决良品率低的问题,使电感有更高的感值以及更低的阻值,达到实现客户需求的电感感值和/或阻值的效果,并实现量产。
54.在一种优选实施例中,所述的电感的磁芯制备方法如下:
55.(1)取所需量的羰基铁粉加入丙酮溶液中进行超声波清洗;
56.(2)去除丙酮溶液并将羰基铁粉干燥;
57.(3)将步骤(2)所得的羰基铁粉加入磷酸酒精溶液中进行超声波清洗,使羰基铁粉表面生成磷酸盐层;
58.(4)将步骤(3)所得羰基铁粉干燥并研磨;
59.(5)制备共混树脂;
60.(6)使用所述共混树脂对步骤(4)所得羰基铁粉包覆;
61.(7)对步骤(6)所得羰基铁粉脱模;
62.(8)对步骤(7)所得羰基铁粉压成型。
63.进一步的,所述步骤(5):将高温环氧树脂与有机硅树脂按照质量比为1:5的配比进行混合,然后加入丙酮,并添加固化剂,固化剂质量为高温环氧树脂与有机硅树脂二者总质量的10~20%,在超声清洗器中搅拌制得共混树脂。
64.进一步的,所述步骤(6):称取共混树脂,共混树脂的质量为所用羰基铁粉的2~3%,加入丙酮对共混树脂进行稀释,丙酮的添加量为羰基铁粉质量的10~20%,随后在共混树脂丙酮溶液中加入羰基铁粉,持续搅拌直至丙酮溶液完全挥发,将浆状磁粉在空气中晾干,用筛网进行造粒,最后将造粒后的粉末烘干得到共混树脂包覆的羰基铁粉。
65.进一步的,所述步骤(7):在共混树脂包覆的羰基铁粉中加入硬脂酸钡作为脱模剂充分混合,硬脂酸钡的质量为羰基铁粉质量的0.1~0.3%。
66.进一步的,所述步骤(8):将1.8g磁粉在6t/cm2、180℃条件下热压30s,得到外径13.5~14.5mm、内径7.5~8.5mm、高2.5~3.5mm的环状磁粉芯。
67.进一步的,所述步骤(8):在800mpa条件下冷压得到环状或柱状磁粉芯块体。
68.进一步的,步骤(1)的超声波清洗的时间为10min。
69.进一步的,步骤(3)的超声波清洗的时间为15min。
70.进一步的,步骤(4)的研磨是球磨,将磷酸包覆的羰基铁粉放置于65℃的真空干燥箱中干燥1小时,随后使用行星球磨机以250r/min的速度球磨1小时得超声波辅助的磷酸包
覆的羰基铁粉。
71.进一步的,所述步骤(6)中将浆状磁粉在空气中晾干25min,用80目筛网进行造粒,最后将造粒后的粉末放置于80℃中烘干30min得到共混树脂包覆的羰基铁粉。
72.实施例方案1:制备方法,包括如下步骤:
73.(1)洗涤粉末:把羰基铁粉加入到丙酮溶液中,再放入超声波清洗机中洗涤10min,以去除羰基铁粉表面油脂,最终倒掉丙酮溶液并在真空干燥箱中烘干。
74.(2)磷酸包覆:将干燥后的羰基铁粉加入到磷酸酒精溶液中反应,同时打开超声波清洗器,超声波清洗器的功率为300w,处理时间15min。目的是在超声波作用下,使羰基铁粉表面通过钝化反应生成磷酸盐层。
75.(3)烘干球磨:将磷酸包覆后得到的羰基铁粉放置于65℃的真空干燥箱中干燥1小时,随后使用行星球磨机以250r/min的速度球磨1小时,即可获得超声波辅助的磷酸包覆的羰基铁粉。
76.(4)制备共混树脂:将高温环氧树脂与有机硅树脂按照质量比为1:5的配比进行混合,然后加入少量丙酮,添加kh550固化剂,其质量为高温环氧树脂与有机硅树脂二者总质量的20%,在超声清洗器中搅拌15min,即可制得共混树脂。
77.(5)有机包覆:称取共混树脂,共混树脂的质量为所用羰基铁粉的3%,加入丙酮对共混树脂进行稀释,丙酮的添加量为羰基铁粉质量的12%,随后在共混树脂丙酮溶液中加入羰基铁粉,持续搅拌直至丙酮溶液完全挥发,将浆状磁粉(即共混树脂和羰基铁粉的混合粉末)在空气中晾干约25min,用80目筛网进行造粒,最后将造粒后的粉末放置于80℃中烘干30min,即得到共混树脂包覆的羰基铁粉。
78.(6)压制磁粉芯:在共混树脂包覆的羰基铁粉中加入硬脂酸钡作为脱模剂充分混合,硬脂酸钡的质量为羰基铁粉质量的0.2%。将1.8g磁粉在6t/cm2、180℃条件下热压30s,得到外径13.5~14.5mm、内径7.5~8.5mm、高2.5~3.5mm的环状磁粉芯。
79.用wk3260b磁性元件分析仪在1mhz、1v条件下测试磁环的电感值l和品质因数q,铜线直径为0.65mm,均匀密绕13.5圈。用wk3260b磁性元件分析仪和wk3265b直流偏流源在1mhz、1v条件下测试磁环0a电感和加25a直流叠加电感,计算出在25a直流下的叠加百分比,测试结果见表1。
80.实施例方案2:与上述实施例方案的区别在于步骤(4)中kh550固化剂质量为高温环氧树脂与有机硅树脂二者总质量的10~20%,在超声清洗器中搅拌10~20min,制得共混树脂。
81.实施例方案3:与上述实施例方案的区别在于步骤(5)中共混树脂的质量为所用磁粉的2~3%。
82.实施例方案4:与上述实施例方案的区别在于步骤(5)中丙酮的添加量为磁粉质量的10~20%。
83.实施例方案5:与上述实施例方案的区别在于步骤(5)中浆状磁粉在空气中晾干20~40min。
84.实施例方案6:与上述实施例方案的区别在于步骤(5)中将造粒后的粉末放置于80℃中烘干30~60min,得到共混树脂包覆的磁粉。
85.实施例方案7:与上述实施例方案的区别在于步骤(6)中硬脂酸钡的质量为磁粉质
量的0.1~0.3%。
86.实施例方案8:与上述实施例方案的区别在于步骤(6),在800mpa条件下冷压得到环状或柱状磁粉芯块体,即步骤(8)中的压成型可以使用热压或冷压。
87.实施例方案9:在一种实施例中,本发明的电感的磁粉芯的制备方法包括:合金冶炼、机械破碎、退火处理、绝缘包覆(无机-有机)、模压成型、热处理固化和表面喷漆,在该方法中,包覆的步骤为上述各实施例所述的方法。
88.对比例方案1:
89.磁粉的制备方法同实施例方案1,只是配方中的高温环氧树脂和有机硅树脂的共混树脂换成单独的高温环氧树脂,其他工艺及测试条件不变,具体结果见表1。
90.对比例方案2:
91.磁粉的制备方法同实施例方案1,只是配方中的高温环氧树脂和有机硅树脂的共混树脂换成单独的有机硅树脂,其他工艺及测试条件不变,具体结果见表1。
92.表1实施例性能测试结果
93.编号电感l(uh)磁导率q值25a下l下降(%)实施例12.1340.1215024.6对比例12.4348.1112829.1对比例22.1640.5113124.8
94.在一种可选的实施例方案中,先对羰基铁粉表面改性,再于表面生成磷酸盐层。改性方法如下:按重量计,羰基铁粉:纳米二氧化硅:硅烷偶联剂:氧化镁:=20:8:1:2,如在一种优选方案中,羰基铁粉20g、纳米二氧化硅8g、硅烷偶联剂1g、氧化镁2g。使用管式炉,里面放置装有羰基铁粉、二氧化硅和氧化镁的混合物。将氮气干燥去杂预热通入三通管,先由一路通向羰基铁粉和二氧化硅的混合物预热,预热完毕,再开启另一路压入偶联剂和高温氮气混合后汽化,一起进入反应器底部,使羰基铁粉、二氧化硅和氧化镁的混合物与偶联剂接触反应,控制反应温度加热,反应充分后关闭偶联剂一路,热氮气吹扫后,关闭容器,取出改性的羰基铁粉包覆物。再将干燥后的羰基铁粉包覆物加入到磷酸酒精溶液中反应,同时打开超声波清洗器,超声波清洗器的功率为300w,处理时间15min。目的是在超声波作用下,使羰基铁粉表面通过钝化反应生成磷酸盐层。
95.由于羰基铁粉表明容易与水和氧气反应,抗氧化能力差,且容易团聚,阻抗匹配性能较差,通过改性实验,能够氧化物包覆能提高抗氧化能力,分散均匀,提高阻抗匹配性。且能够为后续磷酸盐层包覆降低团聚性。且通过改性能够增强界面粘接性能,提高稳定性。
96.显然,本领域的技术人员可以对本发明进行各种改动和变型而不脱离本发明的精神和范围。这样,倘若本发明的这些修改和变型属于本发明权利要求及其等同技术的范围之内,则本发明也意图包含这些改动和变型在内。