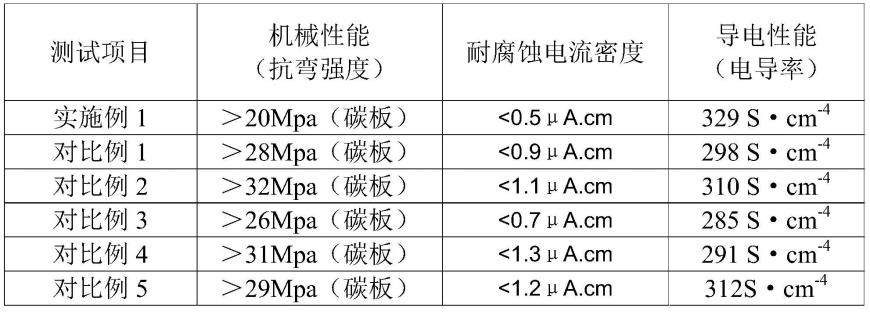
1.本公开涉及质子交换膜燃料电池技术领域,具体地,涉及一种燃料电池的金属双极板及其制备方法。
背景技术:2.随着新能源技术的日趋发展,以再生能源氢气为主要燃料的质子交换膜燃料电池(pemfc)因其在能源、环境问题上具备的巨大潜力而受到广泛的重视。
3.双极板是pemfc的核心组件之一,其质量的好坏直接决定电池堆输出功率的大小和使用寿命的长短。金属双极板因具有优异的力学性能和导电性能,成为当前pemfc双极板研究中关注的焦点,但是,纯金属双极板在质子交换膜燃料电池环境中易受腐蚀,金属板腐蚀后,释放出可能毒害催化剂的金属离子,或形成可增加界面接触电阻的致密氧化膜,从而影响燃料电池的输出功率和使用寿命。
4.也就是说,已有的双极板的机械性能、耐腐蚀性能和导电性能仍然存在不足。
技术实现要素:5.为了克服已有的双极板的上述不足,本公开提供了一种燃料电池的金属双极板及其制备方法。
6.本公开提供了一种燃料电池的金属双极板,所述金属双极板包括金属基板和覆盖在所述金属基板上的涂层;所述涂层包括覆盖在所述金属基板上的第一涂层和覆盖在所述第一涂层上的第二涂层;所述第一涂层为具有孔洞的石墨烯层;所述第二涂层含有氧化石墨烯和聚四氟乙烯;所述孔洞中填充有所述氧化石墨烯和所述聚四氟乙烯。
7.可选地,所述具有孔洞的石墨烯层中,所述孔洞的孔径为0.5~1nm。所述第二涂层中,所述氧化石墨烯与所述聚四氟乙烯的重量比为0.003~0.1:1,优选为0.08~0.1:1。
8.可选地,所述金属基板的厚度为1~1.1mm,所述第一涂层的厚度为25~67nm,所述第二涂层的厚度为2~15nm。
9.可选地,所述金属基板包括金属铝、铝合金、不锈钢和金属钛中的至少一种,优选为金属铝和/或铝合金。
10.可选地,所述氧化石墨烯中的氧碳原子比o/c为1:2.5~3.5,优选为1:3;所述聚四氟乙烯的分子量为5000~20000。
11.本公开还提供了一种燃料电池的金属双极板的制备方法,所述制备方法包括如下步骤:
12.(1)将金属基板在第一浸渍液中进行第一浸渍,得到表面附着有凝胶层的金属基板;所述第一浸渍液为含有氧化石墨烯和交联剂的水溶液;所述交联剂为基板表面离解的金属阳离子;
13.(2)将所述表面附着有凝胶层的金属基板在还原气氛中进行还原处理,得到表面附着有石墨烯层的金属基板;
14.(3)将所述表面附着有石墨烯层的金属基板在第二浸渍液中进行第二浸渍,得到所述金属双极板;所述第二浸渍液为含有氧化石墨烯和聚四氟乙烯的混合液;所述第二浸渍液的溶剂为有机溶剂,所述有机溶剂优选为dmf和/或nmp。
15.可选地,所述第一浸渍液中,所述氧化石墨烯与所述水的重量比为30~70:100,优选为50:100;所述第一浸渍温度50~100℃,优选为50~80℃;所述第一浸渍时间5~20h,优选为5~10h。
16.可选地,所述步骤(2)中的还原处理的条件包括:还原时间为1~12h,还原温度为40~60℃,气压为0.7~0.9pa,还原气氛为ch4和/或h2;所述还原处理的条件优选包括:还原时间为2~6h,还原温度为50~60℃,气压为0.8~0.9pa,还原气氛为h2。
17.可选地,所述第二浸渍液中,所述氧化石墨烯与所述聚四氟乙烯的重量比为0.003~0.1:1,优选为0.08~0.1:1;所述第二浸渍液中,氧化石墨烯的浓度为5-50g/l,优选为10-30g/l;所述第二浸渍温度为50~150℃,优选为80~150℃;所述第二浸渍压力为0.5~0.9pa,优选为0.7~0.9pa;所述第二浸渍时间为0.3~3h,优选为2~3h。
18.可选地,所述金属基板包括金属铝、铝合金、不锈钢和金属钛中的至少一种,优选为金属铝和/或铝合金。
19.通过上述技术方案,石墨烯复合涂层用于改性的金属双极板具有价格低、机械性能良好、耐腐蚀和导电性能优异的优点,可以满足燃料电池双极板的使用要求。
20.本公开的其他特征和优点将在随后的具体实施方式部分予以详细说明。
具体实施方式
21.以下对本公开的具体实施方式进行详细说明。应当理解的是,此处所描述的具体实施方式仅用于说明和解释本公开,并不用于限制本公开。
22.本公开提供了一种燃料电池的金属双极板,所述金属双极板包括金属基板和覆盖在所述金属基板上的涂层;所述涂层包括覆盖在所述金属基板上的第一涂层和覆盖在所述第一涂层上的第二涂层;所述第一涂层为具有孔洞的石墨烯层;石墨烯层为非晶碳涂层,其中,碳原子具有sp2和sp3两种杂化类型,所以涂层同时具有石墨和金刚石的性能,通过调节非晶碳涂层中sp2与sp3杂化的比例,可提高非晶碳涂层的导电性能和抗腐蚀性能,满足金属双极板在质子交换膜燃料电池中的使用要求。所述第二涂层含有氧化石墨烯和聚四氟乙烯;所述孔洞中填充有所述氧化石墨烯和所述聚四氟乙烯,使得基板表面的涂层结构致密,化学稳定性得以显著提高。
23.可选地,所述具有孔洞的石墨烯层中,所述孔洞的孔径为0.5~1nm;所述第二涂层中,所述氧化石墨烯与所述聚四氟乙烯的重量比为1:20~25,优选为1:23。
24.可选地,所述金属基板的厚度为1~1.1mm,所述第一涂层的厚度为25~67nm,所述第二涂层的厚度为2~15nm。
25.可选地,所述金属基板包括金属铝、铝合金、不锈钢和金属钛中的至少一种,优选为金属铝和/或铝合金。所述不锈钢可以包括316l不锈钢和304不锈钢;金属铝基板一方面比不锈钢基板重量轻,另一方面金属铝基板的制造成本也大大低于不锈钢基板,同时,所述金属铝的导电率是不锈钢的21~44倍,导热率是不锈钢的10~29倍,优选选择使用金属铝基板。
26.可选地,所述氧化石墨烯中的氧碳原子比o/c为1:2.5~3.5,优选为1:3;所述聚四氟乙烯的分子量为5000~20000。
27.本公开还提供了一种燃料电池的金属双极板的制备方法,所述制备方法包括如下步骤:
28.(1)将金属基板在第一浸渍液中进行第一浸渍,得到表面附着有凝胶层的金属基板;所述第一浸渍液为含有氧化石墨烯和交联剂的水溶液;所述交联剂为金属基板表面离解的铝离子;
29.(2)将所述表面附着有凝胶层的金属基板在还原气氛中进行还原处理,得到表面附着有石墨烯层的金属基板;(3)将所述表面附着有石墨烯层的金属基板在第二浸渍液中进行第二浸渍,得到所述金属双极板;所述第二浸渍液为含有氧化石墨烯和聚四氟乙烯的混合液。
30.可选地,所述第一浸渍液中,所述氧化石墨烯与所述水的重量比为30~70:100,优选为50:100;所述第一浸渍温度为50~100℃,优选为50~80℃;所述第一浸渍时间为5~20h,优选为5~10h。
31.可选地,所述步骤(2)中的还原处理的条件包括:还原时间为1~12h,还原温度为40~60℃,气压为0.7~0.9pa,还原气氛为ch4和/或h2;所述还原处理的条件优选包括:还原时间为2~6h,还原温度为50~60℃,气压为0.8~0.9pa,还原气氛为h2。通过调节沉积条件实现对石墨烯层中sp2杂化与sp3杂化比例的调控,进而优选出耐腐蚀性能和导电性能较好的金属双极板。
32.石墨烯涂层虽然大大提高了金属双极板的导电、耐蚀性能,但是石墨烯涂层中的柱状结构和孔洞等缺陷会导致涂层耐蚀性能明显降低,涂层中的柱状晶结构被认为存在腐蚀介质扩散通道,因此腐蚀介质更容易穿过涂层与金属基底反应;涂层中存在的孔洞缺陷则会导致涂层的屏蔽机制失效,增大腐蚀介质与金属基板直接接触的概率,进而加速基板腐蚀,所以要在第一涂层表面加固第二涂层,最后在金属双极板表面得到石墨烯复合涂层。
33.可选地,所述第二浸渍液中,所述氧化石墨烯与所述聚四氟乙烯的重量比为0.003~0.1:1,优选为0.08~0.1:1;所述第二浸渍液中,氧化石墨烯的浓度为5-50g/l,优选为10-30g/l;所述第二浸渍温度50~150℃,优选为80~150℃;所述第二浸渍压力0.5~0.9pa,优选为0.7~0.9pa;所述第二浸渍时间0.3~3h,优选为2~3h。
34.经步骤(1)~(3)得到的石墨烯复合涂层金属双极板具有更好的耐腐蚀性、化学稳定性和导电性。
35.特别优选地,本公开的制备方法包括:(1)将金属基板在第一浸渍液中进行第一浸渍,得到表面附着有凝胶层的金属铝和/或铝合金基板;所述第一浸渍液为含有氧化石墨烯的水溶液;所述第一浸渍液中,氧化石墨烯与水的重量比为50:100;所述第一浸渍温度为50~80℃;所述第一浸渍时间为5~10h。(2)将所述表面附着有凝胶层的金属铝和/或铝合金基板在还原气氛中进行还原处理,得到表面附着有石墨烯涂层的金属铝和/或铝合金基板;所述还原处理的条件包括:还原时间为2~6h,还原温度为50~60℃,气压为0.8~0.9pa,还原气氛为h2。(3)将所述表面附着有石墨烯涂层的金属铝和/或铝合金基板在第二浸渍液中进行第二浸渍,得到所述金属双极板;所述第二浸渍液中,氧化石墨烯与聚四氟乙烯的重量比为0.08~0.1:1;所述第二浸渍液中,氧化石墨烯的浓度为10-30g/l;所述第二浸渍温度
为80~150℃;所述第二浸渍压力为0.7~0.9pa;所述第二浸渍时间为2~3h。
36.以下通过实施例进一步详细说明本公开。实施例中所用到的原材料均可通过商购途径获得。
37.实施例1
38.按照如下步骤制备金属双极板:
39.(1)将厚度为1mm的金属铝基板在第一浸渍液(氧化石墨烯与水的重量比为50:100的氧化石墨烯(购自先丰纳米,商品牌号为xf002-2,氧碳原子比o/c为1:3,以下相同)水溶液)中进行第一浸渍,得到表面附着有凝胶层的金属铝基板;所述第一浸渍温度为70℃;所述第一浸渍时间为6h。(2)将所述表面附着有凝胶层的金属铝基板在还原气氛(h2)中进行还原处理,得到表面附着有石墨烯涂层的金属铝基板;所述还原处理的条件包括:还原时间为4h,还原温度为60℃,气压为0.9pa。(3)将所述表面附着有石墨烯涂层的金属铝基板在第二浸渍液(氧化石墨烯和聚四氟乙烯(分子量为10000)混合液)中进行第二浸渍,得到本实施例的金属双极板;所述第二浸渍液中,溶剂为dmf,氧化石墨烯与聚四氟乙烯的重量比为0.09:1;所述第二浸渍液中,氧化石墨烯的浓度为20g/l;所述第二浸渍温度为100℃;所述第二浸渍压力为0.8pa;所述第二浸渍时间为2.5h,从而得到具有石墨烯复合涂层的金属双极板。
40.经过静态法低温氮吸附仪和涡流膜厚测厚仪检测具有石墨烯复合涂层的金属双极板,制备得到的石墨烯复合涂层具有如下特征:所述具有孔洞的石墨烯层中,所述孔洞的孔径为1nm;所述第一涂层的厚度为45nm,所述第二涂层的厚度为15nm。
41.对比例1
42.按照如下步骤制备金属双极板:
43.(1)金属铝基板在第一浸渍液(氧化石墨烯与水的重量比为50:100的氧化石墨烯水溶液)中进行第一浸渍,得到表面附着有凝胶层的金属铝基板;所述第一浸渍温度为70℃;所述第一浸渍时间为6h。(2)将所述表面附着有凝胶层的金属铝基板在还原气氛(h2)中进行还原处理,所述还原处理的条件包括:还原时间为4h,还原温度为60℃,气压为0.9pa,从而得到具有石墨烯涂层的金属双极板。
44.对比例2
45.将316l不锈钢基板置于容器内,将容器抽真空至10-7
torr,将气体ch4和h2按体积比1:1通入容器内,将气压保持在0.8pa进行还原;还原温度为50℃,还原时间为6h,在316l不锈钢基板表面制备得到类金刚石(dlc)涂层a。
46.对比例3
47.将316l不锈钢基板置于容器内,将容器抽真空至10-7
torr,将气体ch4和h2按体积比1:1通入容器内,将气压保持在0.9pa进行还原;还原温度为60℃,还原时间为12h,在316l不锈钢基板表面制备得到dlc涂层b。
48.对比例4
49.将316l不锈钢基板置于容器内,将容器抽真空至10-7
torr,将气体ch4通入容器内,将气压保持在0.8pa进行还原;还原温度为50℃,还原时间为6h,在316l不锈钢基板表面制备得到dlc涂层c。
50.对比例5
51.将316l不锈钢基板置于容器内,将容器抽真空至10-7
torr,将气体ch4和h2按体积比1:0通入容器内,将气压保持在0.9pa进行还原;还原温度为60℃,还原时间为12h,在316l不锈钢基板表面制备得到dlc涂层d。
52.对实施例1和对比例1-5的产品进行机械性能、耐腐蚀电流密度和导电性能测试,测试结果如表1所示:
53.表1
[0054][0055]
通过以上测试数据可知,本发明采用水热浸渍两道工序在金属铝基板表面制备了石墨烯复合涂层,由于第一涂层在含有氧化石墨烯和聚四氟乙烯的混合液中被完全浸渍,石墨烯涂层中的孔洞被有效填充,金属双极板的机械性能、耐腐蚀性能和导电性能均得到显著提升。
[0056]
以上详细描述了本公开的优选实施方式,但是,本公开并不限于上述实施方式中的具体细节,在本公开的技术构思范围内,可以对本公开的技术方案进行多种简单变型,这些简单变型均属于本公开的保护范围。
[0057]
另外需要说明的是,在上述具体实施方式中所描述的各个具体技术特征,在不矛盾的情况下,可以通过任何合适的方式进行组合,为了避免不必要的重复,本公开对各种可能的组合方式不再另行说明。
[0058]
此外,本公开的各种不同的实施方式之间也可以进行任意组合,只要其不违背本公开的思想,其同样应当视为本公开所公开的内容。