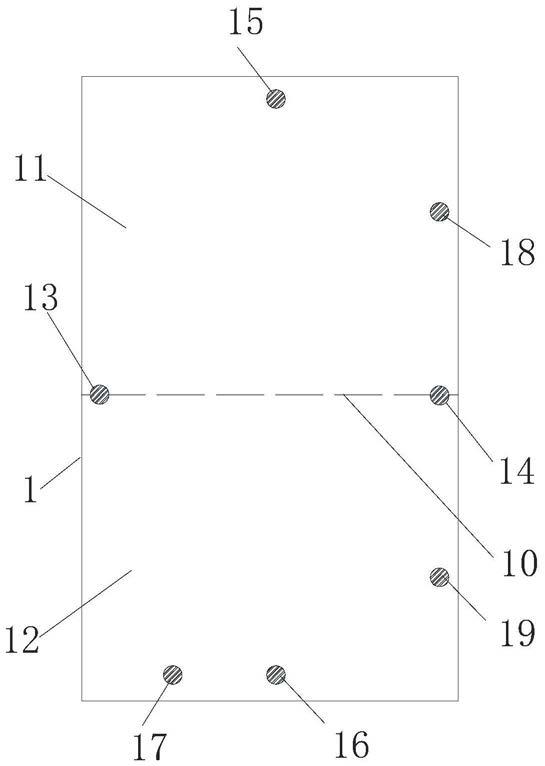
[0001]
本发明涉及印制线路板制作技术领域,具体涉及一种大尺寸印制板的钻孔方法。
背景技术:[0002]
在印制电路板生产制造中,为提高板材利用率、降低生产成本,提高人均效率和产值,采用拼版生产方法,根据产品设计尺寸,大料先开出生产单元pnl,pnl上再分为若干交货单元set,每一set再由一定数量的产品单元pcs构成。
[0003]
印制电路板的制作工艺流程为:开料
→
制作内层线路
→
压合
→
钻孔
→
沉铜
→
全板电镀
→
制作外层线路
→
制作阻焊层
→
表面处理
→
成型
→
fqc;在上述钻孔工序中,受钻孔设备自身可加工产品最大尺寸的限制,超过一定尺寸大拼板的产品无法按照正常流程进行钻孔生产,不利于降低生产成本和提高效率,钻机最大可加工产品尺寸为535*720(宽边*长边)mm,长边超过720mm的板件无法进行正常生产,且分两次生产容易出现孔偏的问题。
技术实现要素:[0004]
本发明针对现有线路板存在上述缺陷的问题,提供一种大尺寸印制板的钻孔方法,该方法可解决尺寸超出钻机加工尺寸的印制电路板钻孔和孔偏的问题。
[0005]
为了解决上述技术问题,本发明提供了一种大尺寸印制板的钻孔方法,将印制板以长边的中心线为界分为前半部分和后半部分,所述钻孔方法包括以下步骤:
[0006]
s1、按拼板尺寸开出芯板;
[0007]
s2、在芯板上制作内层线路,并在芯板的板边制作出多个靶标,所述靶标包括分别设于芯板两长边的中间位置处的第一靶标和第二靶标、分别设于芯板两短边的中间位置处的第三靶标和第四靶标、设于第三靶标或第四靶标一侧并位于芯板的短边上的第五靶标以及设于第一靶标或第二靶标两侧并位于芯板的长边上的第六靶标和第七靶标;
[0008]
s3、通过半固化片将芯板和外层铜箔压合成生产板;
[0009]
s4、而后通过x-ray打靶机在生产板上对应第一靶标、第二靶标、第三靶标、第四靶标、第五靶标、第六靶标和第七靶标的位置处分别钻出第一靶孔、第二靶孔、第三靶孔、第四靶孔、第五靶孔、第六靶孔和第七靶孔;
[0010]
s5、分别测量第一靶孔和第二靶孔之间的靶距以及第六靶孔和第七靶孔之间的靶距,将测量得到的靶距与设计的靶距标准值进行对比计算出生产板的涨缩系数,进而计算出钻孔时所需要的钻带系数;
[0011]
s6、以第一靶孔、第二靶孔和第三靶孔作为定位点并根据所述钻带系数在生产板的前半部分进行钻孔加工,并以第一靶孔、第二靶孔和第四靶孔作为定位点并根据所述钻带系数在生产板的后半部分进行钻孔加工。
[0012]
进一步的,步骤s1中,所述芯板的长边尺寸大于720mm。
[0013]
进一步的,步骤s2中,第五靶标设于第三靶标的一侧,且第五靶标和第三靶标的靶心位于同一横向直线上。
[0014]
进一步的,步骤s2中,第五靶标设于第四靶标的一侧,且第五靶标和第四靶标的靶心位于同一横向直线上。
[0015]
进一步的,步骤s2中,第六靶标和第七靶标分设于第一靶标的两侧,且第六靶标、第七靶标和第一靶标的靶心位于同一竖向直线上。
[0016]
进一步的,步骤s2中,第六靶标和第七靶标与第一靶标之间的距离相同。
[0017]
进一步的,步骤s2中,第六靶标和第七靶标分设于第二靶标的两侧,且第六靶标、第七靶标和第二靶标的靶心位于同一竖向直线上。
[0018]
进一步的,步骤s2中,第六靶标和第七靶标与第二靶标之间的距离相同。
[0019]
进一步的,步骤s2中,第六靶标和第七靶标之间的靶距为x-ray打靶机最大可加工尺寸。
[0020]
进一步的,步骤s6中包括以下步骤:
[0021]
s61、以第一靶孔、第二靶孔和第三靶孔作为定位点并根据所述钻带系数制作出对生产板的前半部分进行钻孔加工的第一钻带,并以第一靶孔、第二靶孔和第四靶孔作为定位点并根据所述钻带系数制作出对生产板的后半部分进行钻孔加工的第二钻带;
[0022]
s62、将生产板的前半部分固定于钻机的台面上,按照第一钻带并以第一靶孔、第二靶孔和第三靶孔作为定位点对生产板的前半部分进行钻孔加工;
[0023]
s63、将生产板翻转,并使生产板的后半部分固定于钻机的台面上,且第一靶孔、第二靶孔与第一次钻孔时的第一靶孔、第二靶孔对位重合,第四靶孔与第一次钻孔时的第三靶孔对位重合;
[0024]
s64、通过钻机对第二钻带进行镜像处理,而后再按照镜像处理后的第二钻带并以第一靶孔、第二靶孔和第四靶孔作为定位点对生产板的后半部分进行钻孔加工。
[0025]
与现有技术相比,本发明具有如下有益效果:
[0026]
本发明通过将超大尺寸的印制板以长边中心线为界分为前半部分和后半部分,在制作内层芯板上的线路时,在芯板的四个板边的中间分别制作一个靶标,而后分别以长边的两个靶孔和短边的其中一个靶孔配合作为定位点依次对印制板的前半部分和后半部分进行钻孔加工,采用对半分段钻孔的方法,分两次完成大尺寸板件的钻孔,解决了尺寸超出钻机加工尺寸的印制电路板钻孔问题,降低了生产成本和提高了生产效率,且通过测量长边和短边的靶孔距离得到板的涨缩系数,进而计算出钻孔时的钻带系数,确保对位良好,避免钻孔后出现孔偏的问题,另外利用两短边上的靶孔测量长边上的涨缩系数时因板尺寸太大导致无法测量,因此本发明通过在其中一长边上位于中间靶孔的两侧均设置一个靶孔,利用这两个额外的靶孔可测量处板长边上的涨缩系数,解决了因板件太长导致无法测量压合涨缩的问题,进而减少因钻带系数不匹配导致的偏孔现象,提高了钻孔品质。
[0027]
本发明中在钻完前半部分的孔时,将生产板翻转过来并使其后半部分固定于钻机的台面上,且使钻后半部分时的靶孔与第一次钻孔时的靶孔位置重合,这样可简单通过钻机对第二钻带进行镜像处理后即可完成对生产板后半部分的钻孔加工,减少了第二钻孔时需要进行二次对位的工序,简化了生产流程,降低了生产成本和提高了生产效率。
附图说明
[0028]
图1为在芯板的板边上设置靶标的示意图。
具体实施方式
[0029]
为了更充分的理解本发明的技术内容,下面将结合具体实施例对本发明的技术方案作进一步介绍和说明。
[0030]
实施例
[0031]
本实施例所示的一种印制板的制作方法,里面包含对大尺寸印制板的钻孔方法,依次包括以下处理工序:
[0032]
(1)开料:按拼板尺寸520mm
×
820mm开出芯板,芯板板厚为1mm,芯板的外层铜面厚度均为1oz;并将芯板1以长边中心线10为分界分为前半部分11和后半部分12(如图1所示)。
[0033]
(2)、制作内层线路(负片工艺):根据图形定位孔,在芯板上用垂直涂布机涂布感光膜,感光膜的膜厚控制8μm,采用全自动曝光机,以5-6格曝光尺(21格曝光尺)完成内层线路和内层靶标曝光,经显影后形成内层线路图形和靶标图形;内层蚀刻,将曝光显影后的芯板上蚀刻出内层线路和多个靶标,内层线宽量测为3mil,如图1所示,靶标包括分别设于芯板两长边的中间位置处的第一靶标13和第二靶标14、分别设于芯板两短边的中间位置处的第三靶标15和第四靶标16、设于第三靶标或第四靶标一侧并位于芯板的短边上的第五靶标17以及设于第一靶标或第二靶标两侧并位于芯板的长边上的第六靶标18和第七靶标19;内层aoi,然后检查内层线路的开短路、线路缺口、线路针孔等缺陷,有缺陷报废处理,无缺陷的产品出到下一流程。
[0034]
其中,当第五靶标设于第三靶标的一侧时,第五靶标和第三靶标的靶心位于同一横向直线上;当第五靶标设于第四靶标的一侧时,第五靶标和第四靶标的靶心位于同一横向直线上。
[0035]
其中,当第六靶标和第七靶标分设于第一靶标的两侧时,第六靶标、第七靶标和第一靶标的靶心位于同一竖向直线上,且第六靶标和第七靶标与第一靶标之间的距离相同;或当第六靶标和第七靶标分设于第二靶标的两侧时,第六靶标、第七靶标和第二靶标的靶心位于同一竖向直线上,且第六靶标和第七靶标与第二靶标之间的距离相同;上述中,第六靶标和第七靶标之间的靶距控制在x-ray打靶机最大可加工尺寸范围内,避免因第六靶标和第七靶标的距离太大出现无法测量靶距的问题,从而利用第六靶标和第七靶标来测量后期压合后的板长边上的涨缩量,利用第一靶标和第二靶标来测量后期压合后的板短边上的涨缩量,利用第五靶标作为方向靶标,用于识别板的前半部分和后半部分。
[0036]
(3)、压合:棕化速度按照底铜铜厚进行棕化,将外层铜箔、半固化片、芯板、半固化片、外层铜箔按要求依次叠合,然后根据板料tg选用适当的层压条件进行压合,形成生产板。
[0037]
(4)钻靶孔:通过x-ray打靶机抓取生产板内层中的靶标,而后在生产板上对应第一靶标、第二靶标、第三靶标、第四靶标、第五靶标、第六靶标和第七靶标的位置处分别钻出上下贯穿的第一靶孔、第二靶孔、第三靶孔、第四靶孔、第五靶孔、第六靶孔和第七靶孔;具体的,靶孔的尺寸与靶标相同,从而对位将靶标全部钻除,表面靶孔尺寸比靶标小导致钻孔时出现孔偏的问题,致使后期测量的靶距不准。
[0038]
(5)测量涨缩系数:分别测量第一靶孔和第二靶孔之间的靶距以及第六靶孔和第七靶抠门和之间的靶距,将测量得到的靶距与设计的靶距标准值(该靶距标准值即制作靶孔图形时的靶距)进行对比计算出生产板的涨缩系数,进而计算出钻孔时所需要的钻带系
数。
[0039]
(6)制作钻带:采用重复使用第一靶孔和第二靶孔两个靶孔分别与第三靶孔和第四靶孔配合定位的方式,制作出两个分别对应生产板的前后两部分进行对半钻孔的钻带;具体的,先以第一靶孔、第二靶孔和第三靶孔作为定位点并根据所述钻带系数制作出对生产板的前半部分进行钻孔加工的第一钻带,再以第一靶孔、第二靶孔和第四靶孔作为定位点并根据所述钻带系数制作出对生产板的后半部分进行钻孔加工的第二钻带。
[0040]
(7)外层钻孔:具体包括以下步骤:
[0041]
a、将生产板的前半部分固定于日立钻机的台面上,按照第一钻带并以第一靶孔、第二靶孔和第三靶孔作为定位点对生产板的前半部分进行钻孔加工;
[0042]
b、将生产板以其短边作为翻转轴进行翻转,并使生产板的后半部分固定于日立钻机的台面上,且第一靶孔、第二靶孔分别与第一次钻孔时的第一靶孔、第二靶孔对位重合,即长边上的两靶孔位置保持不变,而第四靶孔与第一次钻孔时的第三靶孔对位重合;
[0043]
c、通过日立钻机对第二钻带进行镜像处理,而后再按照镜像处理后的第二钻带并以第一靶孔、第二靶孔和第四靶孔作为定位点对生产板的后半部分进行钻孔加工。
[0044]
(8)、沉铜:使生产板上的孔金属化,背光测试10级,孔中的沉铜厚度为0.5μm。
[0045]
(9)、全板电镀:根据现有技术并按设计要求对生产板进行全板电镀,加厚板面和孔内铜层。
[0046]
(10)、外层线路制作(正片工艺):外层图形转移,采用全自动曝光机和正片线路菲林,以5-7格曝光尺(21格曝光尺)完成外层线路曝光,经显影,在生产板上形成外层线路图形;外层图形电镀,然后在生产板上分别镀铜和镀锡,镀铜是以1.8asd的电流密度全板电镀60min,镀锡是以1.2asd的电流密度电镀10min,锡厚3-5μm;然后再依次退膜、蚀刻和退锡,在生产板上蚀刻出外层线路;外层aoi,然后检查外层线路的开短路、线路缺口、线路针孔等缺陷,有缺陷报废处理,无缺陷的产品出到下一流程。
[0047]
(11)、阻焊、丝印字符:根据现有技术并按设计要求在生产板上制作阻焊层并丝印字符。
[0048]
(12)、电气性能测试:检测线路板的电气性能,检测合格的线路板进入下一个加工环节;
[0049]
(13)、表面处理(沉镍金):根据现有技术并按设计要求在生产板上做表面处理,阻焊开窗位的铜面和需背钻的通孔通化学原理,在铜层上均匀沉积一定要求厚度的镍层和金层。
[0050]
(14)、成型:根据现有技术并按设计要求锣外形,外型公差+/-0.05mm,制得线路板。
[0051]
(15)、fqc:根据客户验收标准及我司检验标准,对线路板外观进行检查,如有缺陷及时修理,保证为客户提供优良的品质控制。
[0052]
(16)、fqa:再次抽测线路板的外观、孔铜厚度、介质层厚度、绿油厚度、内层铜厚等是否符合客户的要求。
[0053]
(17)、包装:按照客户要求的包装方式以及包装数量,对线路板进行密封包装,并放干燥剂及湿度卡,然后出货。
[0054]
以上对本发明实施例所提供的技术方案进行了详细介绍,本文中应用了具体个例
对本发明实施例的原理以及实施方式进行了阐述,以上实施例的说明只适用于帮助理解本发明实施例的原理;同时,对于本领域的一般技术人员,依据本发明实施例,在具体实施方式以及应用范围上均会有改变之处,综上所述,本说明书内容不应理解为对本发明的限制。