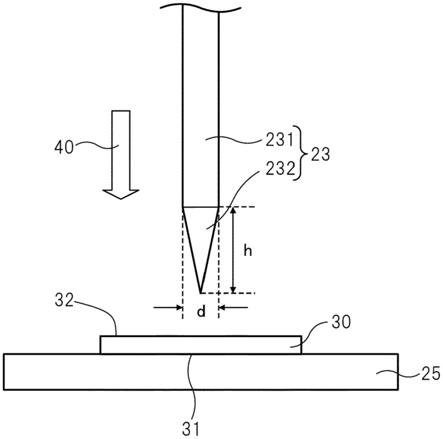
1.本发明涉及散热片及散热片的制造方法。
背景技术:2.在功率器件、晶体管、晶闸管、cpu等发热性电子部件中,如何高效地对使用时产生的热进行散热成为了重要课题。一直以来,作为这样的散热对策,通常是使由发热性电子部件产生的热向散热片等散热部件传导并散热而进行的。为了使由发热性电子部件产生的热高效地向散热部件进行热传导,期望在发热性电子部件与散热部件之间用散热材料填埋接触界面处的气隙。从容易操作的方面考虑,作为这样的散热材料,一直以来使用了散热片(例如,参见专利文献1)。
3.现有技术文献
4.专利文献
5.专利文献1:日本特开2012-39060号公报
技术实现要素:6.发明所要解决的课题
7.对于散热片而言,有时除了要求优异的热传导性以外还要求优异的绝缘性。在这样的情况下,若在散热片中产生绝缘不良,则有时在发热性电子部件中流通过大的电流,对发热性电子部件的损伤变大。因此,需要尽可能不导致散热片产生绝缘不良。
8.因此,本发明的目的在于提供能够抑制绝缘不良的产生的散热片及该散热片的制造方法。
9.用于解决课题的手段
10.本技术的发明人为了达成上述目的而开展了深入研究,结果发现,即使散热片本身没有缺陷,也会由于在散热部件中产生的毛刺、在发热性电子部件与散热部件之间配置散热片时的异物的夹入而产生散热片的绝缘不良。但是,难以完全防止在成型时或加工时在散热部件中产生的毛刺,也难以完全防止在发热性电子部件与散热部件之间配置散热片时夹入异物。因此,期望即使在散热部件中产生毛刺、或即使在发热性电子部件与散热部件之间配置散热片时夹入异物,也不会在散热片中产生绝缘不良。
11.本技术的发明人为了达成上述目的而进一步开展了深入研究,结果发现,下述散热片能够抑制由于在散热部件中产生的毛刺、在发热性电子部件与散热部件之间配置散热片时的异物的夹入而导致的散热片的绝缘不良的产生,所述散热片为:在通过使用针状电极作为上部电极并使用铝板作为下部电极、使针状电极侵入散热片而实施了绝缘击穿试验的情况下,散热片发生绝缘击穿时的针状电极的尖端与铝板之间的距离成为规定范围的散热片;或散热片不发生绝缘击穿而针状电极与铝板短路的散热片。
12.本发明基于上述的见解,其主旨如下。
13.[1]散热片,其厚度大于10μm,针对直接载置于铝板上的散热片,使外加了具有
60hz的频率的2.0kv的交流电压的、在尖端部分具备具有3mm的高度及0.75mm的底面直径的圆锥的针状电极,从散热片的与铝板接触的面的相反侧的面沿着散热片的厚度方向而按每次10μm来阶段性地侵入,并且在该侵入前及各阶段中保持60秒钟的情况下,散热片发生绝缘击穿时的针状电极的尖端与铝板之间的距离大于0μm且为80μm以下,或者散热片不发生绝缘击穿而针状电极与铝板短路。
[0014]
[2]如上述[1]所述的散热片,其中,散热片发生绝缘击穿时的针状电极的尖端与铝板之间的距离为50μm以下。
[0015]
[3]如上述[1]或[2]所述的散热片,其含有树脂粘结剂及无机填充材料。
[0016]
[4]如上述[3]所述的散热片,其中,树脂粘结剂为有机硅树脂。
[0017]
[5]如上述[3]或[4]所述的散热片,其中,无机填充材料为六方晶氮化硼的凝集粒子。
[0018]
[6]如上述[3]~[5]中任一项所述的散热片,其含有玻璃布。
[0019]
[7]如上述[3]~[6]中任一项所述的散热片,其含有包含玻璃化转变温度为200℃以上的树脂的基材树脂层。
[0020]
[8]散热片的制造方法,其包括下述工序:组合物制作工序,将液态树脂组合物、无机填充材料及溶剂混合从而制作散热片用组合物;片材成型工序,将散热片用组合物成型为片状从而制作散热片用组合物片材;预加热工序,一边对散热片用组合物片材进行加压,一边于比固化起始温度低的预加热温度对散热片用组合物片材进行预加热;以及,固化工序,一边对经预加热的散热片用组合物片材进行加压,一边于固化起始温度以上的温度对散热片用组合物片材进行加热。
[0021]
[9]如上述[8]所述的散热片的制造方法,其中,液态树脂组合物为液态有机硅树脂组合物,无机填充材料为六方晶氮化硼的凝集粒子,在预加热工序中,对散热片用组合物片材进行加压时的压力为50~200kgf/cm2,预加热温度为50~80℃,在固化工序中,对散热片用组合物片材进行加压时的压力为50~200kgf/cm2,固化起始温度以上的温度为130~200℃。
[0022]
[10]如上述[9]所述的散热片的制造方法,其中,在预加热工序中,于预加热温度对散热片用组合物片材进行预加热的加热时间为5~10分钟,在固化工序中,于固化起始温度以上的温度对散热片用组合物片材进行加热的加热时间为10~60分钟。
[0023]
[11]如上述[9]或[10]所述的散热片的制造方法,其还包括下述低分子硅氧烷去除工序:于130~200℃的加热温度,对于固化起始温度以上的温度加热后的散热片用组合物片材进行2~30小时加热。
[0024]
发明的效果
[0025]
根据本发明,可以提供能够抑制由于散热部件的毛刺、或者由于在发热性电子部件及散热片之间或散热部件及散热片之间混入的异物而产生的绝缘不良的散热片及该散热片的制造方法。
附图说明
[0026]
[图1]图1为示出绝缘击穿试验中使用的耐受电压试验机的一个例子的示意图。
[0027]
[图2]图2为用于对设置于耐受电压试验机的散热片进行说明的示意图。
[0028]
[图3]图3为示出绝缘击穿试验中的针状电极向散热片中的侵入距离与经过时间的关系的曲线图。
[0029]
[图4]图4为用于对耐异物评价试验的试验方法进行说明的示意图。
具体实施方式
[0030]
[散热片]
[0031]
以下,对本发明的散热片进行说明。
[0032]
(散热片发生绝缘击穿时的针状电极的尖端与铝板之间的距离)
[0033]
本发明的散热片的厚度大于10μm。此外,对于本发明的散热片而言,针对直接载置于铝板上的散热片,使外加了具有60hz的频率的2.0kv的交流电压的、在尖端部分具备具有3mm的高度及0.75mm的底面直径的圆锥的针状电极,从散热片的与铝板接触的面的相反侧的面沿着散热片的厚度方向而按每次10μm来阶段性地侵入,并且在侵入前及各阶段中保持60秒钟的情况下,散热片发生绝缘击穿时的针状电极的尖端与铝板之间的距离大于0μm且为80μm以下,或者散热片不发生绝缘击穿而针状电极与铝板短路。若上述绝缘击穿试验中散热片发生绝缘击穿时的针状电极的尖端与铝板之间的距离大于80μm,则有时由于散热部件的毛刺、或者由于在发热性电子部件及散热片之间或散热部件及散热片之间混入的异物,而不能确保与发热性电子部件及散热部件之间的电绝缘性。另外,若针状电极的尖端与铝板之间的距离为0μm,则针状电极与铝板短路,因此散热片不发生绝缘击穿。从这样的观点考虑,上述绝缘击穿试验中散热片发生绝缘击穿时的针状电极的尖端与铝板之间的距离优选为50μm以下,更优选为30μm以下,进一步优选为20μm以下。
[0034]
另外,在不能抑制由于散热部件的毛刺、或者由于在发热性电子部件及散热片之间或散热部件及散热片之间混入的异物而产生的绝缘不良的散热片中,在使针状电极侵入前发生绝缘击穿。而且,若该散热片的厚度为80μm以下,则上述绝缘击穿试验中散热片发生绝缘击穿时的针状电极的尖端与铝板之间的距离成为80μm以下。因此,本发明的散热片优选为在上述绝缘击穿试验中、在第一次的针状电极向散热片中的10μm的侵入过程中不发生绝缘击穿、在第二次以后的针状电极向散热片中的10μm的侵入过程中发生绝缘击穿这样的散热片。而且,优选地,在第二次以后的针状电极向散热片中的10μm的侵入过程中散热片发生绝缘击穿时的针状电极的尖端与铝板之间的距离大于0μm且为80μm以下,或者散热片不发生绝缘击穿而针状电极与铝板短路。
[0035]
在第二次以后的针状电极向散热片中的10μm的侵入过程中散热片发生绝缘击穿时的针状电极的尖端与铝板之间的距离优选大于0μm且为50μm以下,更优选大于0μm且为30μm以下,进一步优选大于0μm且为20μm以下。
[0036]
需要说明的是,本发明的散热片的厚度大于10μm是为了使得能够在针状电极与铝板不发生短路的情况下向散热片中侵入至少10μm。散热片的厚度的上限没有特别限定,适当地根据用途设定即可。
[0037]
上述的绝缘击穿试验例如可以使用图1所示的耐受电压试验机来实施。耐受电压试验机1具备:基底板11;2根支柱12、13,其垂直设置于基底板11上;固定板14,其固定于2根支柱12、13上,并且架设在2根支柱12、13之间;升降板15,其设置于固定板14的下方,并且以可上下移动的方式架设在2根支柱12、13之间;测微头16,其微分筒(stem)被固定于固定板
14,主轴的前端被固定于升降板15;为了使测微头16的主轴的前端不从升降板15脱离而设置的弹簧17、18,其一端被固定于固定板14,另一端被固定于升降板15;具有绝缘性的2根悬吊棒19、21,其是从升降板15悬垂地设置的;铝板22,其隔着悬吊棒19、21而设置于升降板15的下方;铝制的针状电极23,其以垂下的方式设置于铝板22;具有绝缘性的工作台24,其载置于基底板11;铝板25,其载置于工作台24上;耐受电压测量仪26,其在设置于升降板15下方的铝板22及载置于工作台24上的铝板25之间外加具有60hz的频率的2.0kv的交流电压,并且对散热片的绝缘击穿进行测量。耐受电压测量仪26可以使用例如菊水电子工业株式会社制的耐受电压试验器(型号:tos 5101)。
[0038]
若使测微头16的套筒(thimble)旋转,则测微头16的主轴活动,由此,固定有主轴的前端的升降板15沿上下方向移动。与之相伴,铝板22也沿上下方向移动,以垂下的方式设置于铝板22的针状电极23也沿上下方向移动。因此,通过使测微头16的套筒旋转,能够使针状电极23沿上下方向移动。另外,针状电极23的上下方向的移动距离可以由测微头16的刻度读取。此外,铝板22与针状电极23之间具有导电性,因此,若在2张铝板22、25之间外加交流电压,则在针状电极23与铝板25之间也外加了同样的交流电压。
[0039]
如图2所示,散热片30直接载置于铝板25上。而且,针状电极23沿箭头40的方向移动,从散热片30的与铝板25接触的面31的相反侧的面32,沿散热片30的厚度方向侵入。需要说明的是,针状电极23具有主体部分231及尖端部分232。而且,尖端部分232为具有3mm的高度(h)及0.75mm的底面直径(d)的圆锥。
[0040]
图3为示出绝缘击穿试验中的针状电极向散热片中的侵入距离与经过时间的关系的曲线图。如图3所示,在使针状电极侵入至散热片中之前,在针状电极及铝电极之间外加了交流电压之后,保持60秒钟。然后,使针状电极向散热片中侵入10μm,保持60秒钟。在不发生散热片的绝缘击穿的情况下,使针状电极进一步向散热片中侵入10μm,保持60秒钟。绝缘击穿试验中,实施使针状电极向散热片中侵入10μm并保持60秒钟这一工艺直至发生散热片的绝缘击穿、或者直至针状电极与铝板短路。
[0041]
上述的绝缘击穿试验中,认为本发明的散热片发生绝缘击穿时的针状电极的尖端与铝板之间的距离大于0μm且为80μm以下、或者本发明的散热片不发生绝缘击穿而针状电极与铝板短路的原因在于,通过一边从低温起缓缓地升高温度一边对后述的散热片用组合物片材进行加热加压,从而减少了散热片中的孔隙。更具体而言,认为其是由以下理由导致的。但是,该理由并不限定本发明。
[0042]
本发明的散热片例如可以通过下述方式来制作:将含有树脂、无机填充材料、和玻璃布的散热片用组合物成型,制作散热片用组合物片材之后,于规定的温度对散热片用组合物片材进行加热加压而使其固化。此外,对于本发明的散热片而言,在于上述规定的温度对散热片用组合物片材进行加热加压而使其固化之前,于比散热片用组合物片材的固化起始温度低的预加热温度对散热片用组合物片材进行加热加压。认为在于预加热温度进行加热的阶段中,散热片用组合物片材未固化,因此,能够通过加热加压而将树脂中的气泡充分除去。另外,可认为玻璃布的纤维的间隙的一部分由于加热加压而被无机填充材料填埋,或者上述间隙被无机填充材料压溃等。而且,认为由此使散热片的绝缘性得以改善。
[0043]
另外,使用块状的凝集粒子作为无机填充材料的情况下,认为由于以下理由而能够进一步改善散热片的绝缘性。在该情况下,本发明的散热片可以通过下述方式来制作:将
含有树脂、块状的凝集粒子、和玻璃布的散热片用组合物成型,制作散热片用组合物片材后,于规定的温度对散热片用组合物片材进行加热加压而使其固化。此外,对于本发明的散热片而言,在于上述温度对散热片用组合物片材进行加热加压而使其固化之前,于比散热片用组合物片材的固化起始温度低的预加热温度对散热片用组合物片材进行加热加压。在该阶段中,散热片用组合物片材未固化,因此,能够通过加热加压而将树脂中的气泡充分除去。另外,在块状的凝集粒子中的孔隙中也能够充分填充树脂。此外,在玻璃布中的孔隙中也能够充分填充树脂。通过上述方式,成为绝缘击穿的原因的气泡、孔隙被充分除去,因此认为,在上述的绝缘击穿试验中,本发明的散热片发生绝缘击穿时的针状电极的尖端与铝板之间的距离大于0μm且为80μm以下,或者本发明的散热片不发生绝缘击穿而针状电极与铝板短路。
[0044]
另外,在于预加热温度对散热片用组合物片材进行加热加压的阶段中,散热片用组合物片材未固化,因此,通过加压而使凝集粒子松散。散热片发生绝缘击穿时,电流从树脂中通过。因此,若通过加压而使凝集粒子松散,则在绝缘击穿试验中,发生绝缘击穿时,电流以从填充了块状一次粒子集合体的孔隙的树脂通过的方式流通,因此,电流经由复杂的路径从针状电极与铝板之间流通。
[0045]
如上所述,本发明的散热片不易发生绝缘击穿,认为在上述的绝缘击穿试验中,本发明的散热片发生绝缘击穿时的针状电极的尖端与铝板之间的距离大于0μm且为80μm以下,或者本发明的散热片不发生绝缘击穿而针状电极与铝板短路。
[0046]
(散热片的厚度)
[0047]
本发明的散热片的厚度大于10μm。若本发明的散热片的厚度为10μm以下,则针状电极不会与铝板短路,不能使针状电极向散热片中侵入10μm。另外,本发明的散热片的厚度优选大于20μm。若本发明的散热片的厚度大于20μm,则散热片能够进一步追随发热性电子部件的安装面的凹凸。从这样的观点考虑,本发明的散热片的厚度更优选为25μm以上,进一步优选为50μm以上,更进一步优选为100μm以上,特别优选为150μm以上。另外,从能够降低散热片的热阻这样的观点考虑,本发明的散热片的厚度优选为1000μm以下,更优选为650μm以下。
[0048]
(散热片的成分)
[0049]
本发明的散热片优选含有树脂粘结剂及无机填充材料。由此,容易制作在进行了上述绝缘击穿试验的情况下、散热片发生绝缘击穿时的针状电极的尖端与铝板之间的距离大于0μm且为80μm以下、或者散热片不发生绝缘击穿而针状电极与铝板短路的散热片。
[0050]
<树脂粘结剂>
[0051]
本发明的散热片中使用的树脂粘结剂只要是通常可用于散热片的树脂粘结剂,就没有特别限定。作为本发明的散热片中使用的树脂粘结剂,可举出例如环氧基树脂、有机硅树脂、丙烯酸树脂、酚醛树脂、三聚氰胺树脂、脲醛树脂、不饱和聚酯、氟树脂、聚酰胺(例如聚酰亚胺、聚酰胺酰亚胺、聚醚酰亚胺等)、聚酯(例如聚对苯二甲酸丁二醇酯、聚对苯二甲酸乙二醇酯等)、聚苯醚、聚氨酯、聚苯硫醚、全芳香族聚酯、聚砜、液晶聚合物、聚醚砜、聚碳酸酯、马来酰亚胺改性树脂、abs树脂、aas(丙烯腈-丙烯酸橡胶
·
苯乙烯)树脂、aes(丙烯腈
·
乙烯
·
丙烯
·
二烯橡胶-苯乙烯)树脂等。它们可以单独使用1种,或者组合2种以上而使用。从使散热片的操作容易这样的观点及利用散热片的柔软性来进一步提高散热片的密
合性这样的观点考虑,树脂粘结剂优选为橡胶或弹性体。这些之中,从耐热性、耐气候性、电绝缘性及化学稳定性的观点考虑,优选为有机硅树脂。
[0052]
从不含成为金属腐蚀的原因的离子性杂质、在反应后不产生副产物这样的观点考虑,本发明的散热片中使用的有机硅树脂优选为加成反应型有机硅树脂。加成反应型有机硅树脂是使用铂化合物作为催化剂、通过烯基与键合于硅原子的氢原子之间的氢化硅烷化反应进行固化而得到的有机硅树脂。加成反应型有机硅树脂中包括例如wacker asahikasei silicone co.,ltd.制的商品名“lr3303-20a/b”的有机硅。
[0053]
<无机填充材料>
[0054]
本发明的散热片中使用的无机填充材料(本说明书中有时表述为“填充材料”)只要是通常可用于散热片的无机填充材料,就没有特别限定。作为本发明的散热片中使用的无机填充材料,可举出例如氧化锌、氧化铝、氮化硼、氮化铝、碳化硅、氮化硅等。它们可以单独使用1种,或者组合2种以上而使用。这些之中,更优选为凝集成块状的无机填充材料。另外,无机填充材料之中,从热导率及化学稳定性的观点考虑,更优选为氮化硼。氮化硼在热传导性上具有各向异性,因此进一步优选为抑制了该热传导性的各向异性的块状氮化硼粒子。需要说明的是,块状氮化硼粒子是使六方晶氮化硼的鳞片状粒子凝集成块状而得到的粒子。
[0055]
(a)无机填充材料的平均粒径
[0056]
无机填充材料的平均粒径优选为5~90μm。若无机填充材料的平均粒径为5μm以上,则可以增高无机填充材料的含量。另一方面,若无机填充材料的平均粒径为90μm以下,则能够将散热片减薄。从这样的观点考虑,无机填充材料的平均粒径更优选为10~70μm,进一步优选为15~50μm,特别优选为15~45μm。需要说明的是,无机填充材料的平均粒径例如可以使用beckman-coulter,inc.制激光衍射散射法粒度分布测定装置(ls-13 320)来测定。作为无机填充材料的平均粒径,可以采用在测定处理之前未被供于均化器的情况下进行测定而得到的平均粒径。因此,无机填充材料为凝集粒子的情况下,无机填充材料的平均粒径为凝集粒子的平均粒径。需要说明的是,得到的平均粒径例如为基于体积统计值的平均粒径。
[0057]
(b)无机填充材料的含量
[0058]
相对于树脂粘结剂及无机填充材料的合计100体积%而言的无机填充材料的含量优选为30~85体积%。无机填充材料的含量为30体积%以上的情况下,散热片的热导率提高,容易得到充分的散热性能。另外,无机填充材料的含量为85体积%以下的情况下,能够抑制在散热片的成型时易于产生孔隙的情况,能够提高散热片的绝缘性、机械强度。从这样的观点考虑,相对于树脂粘结剂及无机填充材料的合计100体积%而言的无机填充材料的含量更优选为40~80体积%,进一步优选为45~70体积%。
[0059]
<增强层>
[0060]
本发明的散热片可以具备增强层。增强层担负进一步提高散热片的机械强度的作用,此外,在散热片被沿厚度方向压缩时,还发挥抑制散热片沿平面方向的拉伸、确保绝缘性的效果。作为增强层,可举出例如玻璃布、聚酯、聚酰胺、聚酰亚胺、聚碳酸酯、丙烯酸树脂等的树脂膜、棉、麻、芳族聚酰胺纤维、纤维素纤维、尼龙纤维、聚烯烃纤维等的布纤维网布、芳族聚酰胺纤维、纤维素纤维、尼龙纤维、聚烯烃纤维等的无纺布、不锈钢、铜、铝等的金属
纤维网布、铜、镍、铝等的金属箔等。它们可以单独使用1种,或者组合2种以上而使用。这些之中,从热传导性及绝缘性的观点考虑,优选为玻璃布。
[0061]
使用玻璃布作为增强层的情况下,可以使用通常市售那样的具有开口部的玻璃布。玻璃布的厚度优选为10μm~150μm。玻璃布的厚度为10μm以上的情况下,能够抑制玻璃布在操作时毁坏。另一方面,玻璃布的厚度为150μm以下的情况下,能够抑制由玻璃布导致的散热片的热导率的降低。从这样的观点考虑,玻璃布的厚度更优选为20~90μm,进一步优选为30~60μm。市售的玻璃布中包括纤维直径为4~9μm的玻璃布,可以将它们用于散热片。另外,玻璃布的拉伸强度例如为100~1000n/25mm。另外,从取得热传导性及强度的均衡性这样的观点考虑,玻璃布的开口部的一边的长度优选为0.1~1.0mm。可用于散热片的玻璃布中包括例如unitika ltd.制、商品名“h25 f104”。需要说明的是,增强层可配置在散热片的厚度方向中央附近。所谓中央附近,为厚度方向中央
±
1/4厚度的范围。
[0062]
散热片可以包含除树脂粘结剂、无机填充材料及增强层以外的其他成分。其他成分例如为添加剂、杂质等。散热片的体积100体积%中的其他成分的含量可以为例如5体积%以下,优选为3体积%以下,更优选为1体积%以下。
[0063]
作为添加剂,可举出例如增强剂、增量剂、耐热性提高剂、阻燃剂、粘接助剂、导电剂、表面处理剂、颜料等。
[0064]
<基材树脂层>
[0065]
本发明的散热片优选含有基材树脂层。基材树脂层担负进一步提高散热片的耐热性、绝缘性的作用。在该情况下,本发明的散热片包含:含有上述的树脂粘结剂及无机填充材料的树脂组合物层;和与该树脂组合物层相邻的基材树脂层。树脂组合物层可以具备上述的增强层。需要说明的是,树脂组合物层优选以树脂粘结剂及无机填充材料为主成分,其他成分可以为10体积%以下,可以为5体积%以下,可以为3体积%以下,可以为1体积%以下。
[0066]
基材树脂层优选包含玻璃化转变温度为200℃以上的树脂。若玻璃化转变温度为200℃以上,则可得到充分的耐热性,能够维持层叠体的绝缘性、热传导性良好。基材树脂层可以为由涂膜形成的层,也可以为由膜形成的层。
[0067]
作为构成基材树脂层的树脂,可举出聚酰亚胺、聚酰胺酰亚胺、聚酰胺(特别是芳香族聚酰胺)、聚醚砜、聚醚酰亚胺、聚萘二甲酸乙二醇酯、聚四氟乙烯(ptfe)或四氟乙烯
·
全氟烷基乙烯基醚共聚物(pfa)等,其中,优选为聚酰亚胺。另外,可以单独使用或者组合数种而使用。
[0068]
基材树脂层中的树脂的含量没有特别限定,但关于下限,优选为78体积%以上,更优选为80体积%以上,进一步优选为82体积%以上。关于上限,优选为92体积%以下,更优选为90体积%以下,进一步优选为88体积%以下。
[0069]
基材树脂层优选含有无机填充材料。通过使基材树脂层含有无机填充材料,能够提高绝缘性、热传导性、剥离强度等。尤其可推测剥离强度升高的原因在于,由无机填充材料在基材树脂层与树脂组合物层的界面处形成凹凸,产生锚定效应。作为无机填充材料,可以使用与上述的无机填充材料同样的材料。
[0070]
基材树脂层中的无机填充材料的含量没有特别限定,但关于下限,优选为8体积%以上,更优选为10体积%以上,进一步优选为12体积%以上。关于上限,优选为22体积%以
下,更优选为20体积%以下,进一步优选为18体积%以下。
[0071]
另外,在基材树脂层中,可以包含少量的上述添加剂,也可以包含少量的杂质。需要说明的是,在基材树脂层中,上述树脂与无机填料的总含量优选为90体积%以上,更优选为95体积%以上,进一步优选为97体积%以上。
[0072]
从绝缘性、热传导性、加工性的观点考虑,基材树脂层的厚度优选为以下的范围。关于下限,优选为0.010mm以上。通过设定为0.010mm以上,能够进一步改善绝缘性,并且还能够改善加工性。更优选为0.012mm以上,进一步优选为0.015mm以上。关于上限,优选为0.100mm以下。更优选为0.070mm以下,进一步优选为0.050mm以下。
[0073]
作为成为基材树脂层的膜,可以依照已知的膜制作方法来制作。另外,也可以获得在市场上销售的制品并使用。
[0074]
<散热片的形态>
[0075]
本发明的散热片的形态没有特别限定。可以为片状品,也可以为卷状品。
[0076]
[散热片的制造方法]
[0077]
本发明的散热片的制造方法包括下述工序:组合物制作工序,将液态树脂组合物、无机填充材料及溶剂混合从而制作散热片用组合物;片材成型工序,将散热片用组合物成型为片状从而制作散热片用组合物片材;预加热工序,一边对散热片用组合物片材进行加压,一边于比固化起始温度低的预加热温度对散热片用组合物片材进行预加热;以及,固化工序,一边对经预加热的散热片用组合物片材进行加压,一边于固化起始温度以上的温度对散热片用组合物片材进行加热。由此,能够制造本发明的散热片。以下,对各工序进行详细说明。
[0078]
(组合物制作工序)
[0079]
在组合物制作工序中,将液态树脂组合物、无机填充材料及溶剂混合从而制作散热片用组合物。液态树脂组合物是于室温(25℃)为液体的状态的树脂组合物。液体树脂组合物是若使其固化则成为本发明的散热片的树脂粘结剂的液体树脂组合物。从可得到作为优选的树脂粘结剂的有机硅树脂这样的观点考虑,优选的液态树脂组合物为液态硅橡胶。作为无机填充材料,可以使用与针对本发明的散热片中使用的填充材料说明过的无机填充材料相同的材料。无机填充材料优选为凝集成块状的粒子,更优选为块状氮化硼粒子。溶剂可用作例如粘度调节剂。溶剂只要能够将液态树脂组合物溶解,就没有特别限定。作为溶剂,可举出例如己烷、甲苯、庚烷等烃系溶剂、丙酮、甲基乙基酮等酮系溶剂等。优选的溶剂为烃系溶剂,更优选的溶剂为甲苯。
[0080]
(片材成型工序)
[0081]
在片材成型工序中,将散热片用组合物成型为片状从而制作散热片用组合物片材。例如,可以在具有脱模性的膜上涂布散热片用组合物,于60~80℃进行4~7分钟干燥,由此将散热片用组合物成型为片状。涂布方法没有特别限定,可以采用能均匀涂布的刮刀法、逗号涂布法、丝网印刷法、辊涂法等已知的涂布方法。但是,从能够以高精度控制所涂布的散热片用组合物的厚度这样的观点考虑,优选为刮刀法及逗号涂布法。需要说明的是,散热片具备增强层的情况下,优选的是,在具有脱模性的膜上载置增强层后,涂布散热片用组合物,进行干燥。在该情况下,可以以在散热片的厚度方向中央配置增强层的方式在增强层的两面涂布散热片用组合物并进行干燥。
[0082]
另外,在具备基材树脂层的散热片的情况下,在成为基材树脂层的基材片材上涂布树脂组合物。作为向基材片材的涂布方法,可以使用以往已知的方法、例如涂布机法、刮刀法、挤出成型法、注射成型法、加压成型法等。在具备基材树脂层的散热片的情况下,也可以以在散热片的厚度方向中央配置基材树脂层的方式在基材树脂层的两面涂布散热片用组合物并进行干燥。
[0083]
(预加热工序)
[0084]
在预加热工序中,一边对散热片用组合物片材进行加压,一边于比固化起始温度低的预加热温度对散热片用组合物片材进行预加热。预加热温度中,散热片用组合物片材未固化,因此,通过该工序,成为散热片的绝缘击穿的原因的气泡、孔隙被充分除去,能够抑制由于散热部件的毛刺、或者由于在发热性电子部件及散热片之间或散热部件及散热片之间混入的异物而产生的散热片的绝缘不良。需要说明的是,固化起始温度是指在散热片的差示扫描量热测定(dsc)中因散热片的固化而产生的发热峰上升的温度。因此,在比固化起始温度低的温度下,散热片用组合物片材不会开始固化。需要说明的是,将实施例中使用的wacker asahikasei silicone co.,ltd.制有机硅lr3303-20a与lr3303-20b以1:1的比例混合并通过差示扫描量热测定(dsc)而进行了测定时的发热峰的温度为90℃。另外,为了提高固化起始温度,可以适当地添加固化抑制剂等。
[0085]
另外,无机填充材料为凝集粒子的情况下,通过该工序,使凝集粒子松散,成为一次粒子以微弱的粒子间相互作用力聚集成块状而得到的块状一次粒子集合体。电流在散热片中以从填充了块状一次粒子集合体中的孔隙的树脂通过的方式流通,其结果是,经由复杂的路径而流通。由此,在散热片中不易发生绝缘不良,能够抑制由于散热部件的毛刺、或者由于在发热性电子部件及散热片之间或散热部件及散热片之间混入的异物而产生的散热片的绝缘不良。
[0086]
在预加热工序中对散热片用组合物片材进行加压时的压力优选为50~200kgf/cm2。通过使对散热片用组合物片材进行加压时的压力为50kgf/cm2以上,能够将树脂中的气泡更充分地除去,使散热片的密度增加,从而提高散热片的绝缘性。另外,通过使对散热片用组合物片材进行加压时的压力为200kgf/cm2以下,能够提高散热片的生产率,并且能够降低制造成本。
[0087]
另外,无机填充材料为凝集粒子的情况下,能够在保持凝集粒子的形状的同时使凝集粒子松散,因此,能够在不使热传导性降低的情况下抑制绝缘不良。从这样的观点考虑,对散热片用组合物片材进行加压时的压力更优选为70~150kgf/cm2。
[0088]
预加热温度优选为50~80℃。通过使预加热温度为50℃以上,能够抑制散热片用组合物片材中的凝集成块状的粒子的凝集过度崩溃、粒子发生取向并由此导致散热片的热导率降低的情况。另外,通过使加热温度为80℃以下,能够在不使树脂固化的情况下将树脂中的气泡充分除去,使散热片的密度增加,从而提高散热片的绝缘性。从这样的观点考虑,预加热温度更优选为55~75℃。
[0089]
于预加热温度对散热片用组合物片材进行预加热的加热时间优选为5~10分钟。通过使加热时间为5分钟以上,能够将树脂中的气泡更充分地除去,使散热片的密度增加,从而提高散热片的绝缘性。另外,通过使加热时间为10分钟以下,能够提高散热片的生产率,并且能够降低制造成本。从这样的观点考虑,加热时间更优选为6~9分钟。
[0090]
(固化工序)
[0091]
在固化工序中,一边对经预加热的散热片用组合物片材进行加压,一边于固化起始温度以上的温度对散热片用组合物片材进行加热。由此,散热片用组合物片材发生固化而成为散热片。
[0092]
在固化工序中对散热片用组合物片材进行加压时的压力优选为100~200kgf/cm2。通过使对散热片用组合物片材进行加压时的压力为100kgf/cm2以上,能够进一步除去树脂中的气泡,使散热片的密度增加,从而进一步提高散热片的绝缘性。另外,散热片具有增强层的情况下,能够提高树脂与增强层之间的接合性。另外,通过使对散热片用组合物片材进行加压时的压力为200kgf/cm2以下,能够提高散热片的生产率,并且能够降低制造成本。从这样的观点考虑,对散热片用组合物片材进行加压时的压力更优选为130~180kgf/cm2。另外,如上所述,本发明中,为了缓缓地进行加热加压从而降低散热片中的孔隙量,固化工序中的加压力大于预加热中的加压力。
[0093]
在固化工序中,对经预加热的散热片用组合物片材进行加热的温度只要为固化起始温度以上的温度,就没有特别限定,但优选为130~200℃。通过使散热片用组合物片材的加热温度为130℃以上,能够使散热片用组合物片材更充分地固化。另外,通过使散热片用组合物片材的加热温度为200℃以下,能够提高散热片的生产率,并且能够降低制造成本。从这样的观点考虑,散热片用组合物片材的加热温度更优选为140~180℃。
[0094]
在固化工序中对散热片用组合物片材进行加热的加热时间优选为10~60分钟。通过使加热时间为10分钟以上,能够使散热片用组合物片材更充分地固化。另外,通过使加热时间为60分钟以下,能够提高散热片的生产率,并且能够降低制造成本。
[0095]
(低分子硅氧烷去除工序)
[0096]
本发明的散热片的制造方法优选还包括下述低分子硅氧烷去除工序:于130~200℃的加热温度,对于固化起始温度以上的温度加热后的散热片用组合物片材进行2~30小时加热。由此,能够将树脂中的低分子硅氧烷除去。需要说明的是,若树脂中的低分子硅氧烷的浓度高,则存在下述情况:产生硅氧烷气体,由于因电气接点的滑动、火花等产生的能量而在电气接点上生成由硅氧化物形成的绝缘被膜,引起接点故障。
[0097]
通过使加热温度为130℃以上,能够将树脂中的低分子硅氧烷充分除去。通过使加热温度为200℃以下,能够确保散热片的柔软性。另外,能够提高散热片的生产率,并且能够降低制造成本。从这样的观点考虑,加热温度更优选为140~190℃。
[0098]
通过使加热时间为2小时以上,能够将树脂中的低分子硅氧烷充分除去。通过使加热时间为30小时以下,能够提高散热片的生产率,并且能够降低制造成本。从这样的观点考虑,加热时间更优选为3~10小时。
[0099]
实施例
[0100]
以下,对于本发明,利用实施例及比较例来进行详细说明。需要说明的是,本发明不限定于以下实施例。
[0101]
对实施例及比较例的散热片进行以下的评价。
[0102]
(散热片的厚度)
[0103]
使用测微计,在任意10个部位测定散热片的厚度,将其平均值作为实施例或比较例的散热片的厚度。
[0104]
(绝缘击穿试验)
[0105]
使用图1所示的耐受电压试验机进行绝缘击穿试验,测定了散热片发生绝缘击穿时的针状电极的尖端与铝板之间的距离。需要说明的是,作为耐受电压测量仪,使用菊水电子工业株式会社制的耐受电压试验器(型号:tos 5101)。使用该耐受电压试验器,在针状电极及铝板之间外加了具有60hz的频率的2.0kv的交流电压。另外,如上所述,使用在尖端部分具备具有3mm的高度及0.75mm的底面直径的圆锥的针状电极进行绝缘击穿试验。
[0106]
在工作台上的铝板上载置散热片后,旋转测微头的套筒,使针状电极下降直至针状电极的尖端以未侵入的方式接触散热片。然后,在针状电极及铝板之间外加了交流电压后,将该状态保持60秒钟。未发生散热片的绝缘击穿的情况下,旋转测微头的套筒并使针状电极下降10μm,使针状电极向散热片中侵入10μm。然后,将该状态保持60秒钟。
[0107]
未发生散热片的绝缘击穿的情况下,旋转测微头的套筒并使针状电极进一步下降10μm,使针状电极进一步向散热片中侵入10μm。然后,针状电极与铝板接触且针状电极未与铝板发生短路的情况下,将该状态保持60秒钟。未发生散热片的绝缘击穿的情况下,旋转测微头的套筒并使针状电极进一步下降10μm,使针状电极进一步向散热片中侵入10μm。然后,针状电极与铝板接触且针状电极未与铝板发生短路的情况下,将该状态保持60秒钟。实施这样的针状电极的下降及保持的操作直至发生散热片的绝缘击穿、或者直至针状电极与铝板短路。
[0108]
然后,从散热片的厚度减去发生了散热片的绝缘击穿时的针状电极向散热片中的侵入距离,由此算出散热片发生绝缘击穿时的针状电极的尖端与铝板之间的距离。针对5张散热片,算出散热片发生绝缘击穿时的针状电极的尖端与铝板之间的距离,将其平均值作为实施例或比较例中的散热片发生绝缘击穿时的针状电极的尖端与铝板之间的距离。
[0109]
(耐异物评价试验)
[0110]
如图4所示,利用直径为25mm的可动电极51(固定于未图示的升降板,能与升降板通电)、和直径为25mm的固定电极52夹持散热片53和异物54(直径为100μm,铝),依照jis c2110进行绝缘击穿试验。外加恒定的电压20秒钟,阶段性地使电压上升直至发生绝缘击穿,按以下的基准来评价散热片53相对于异物54的耐性。
[0111]
a:绝缘击穿电压为6kv以上
[0112]
b:绝缘击穿电压为4kv以上且低于6kv
[0113]
c:绝缘击穿电压低于4kv
[0114]
实施例及比较例的散热片如下所述地制作。
[0115]
[实施例1]
[0116]
(六方晶氮化硼的制作)
[0117]
将硼酸、三聚氰胺、及碳酸钙(均为试剂特级)以质量比为70:50:5的比例混合,在氮气气氛中,经1小时从室温升温至1400℃,于1400℃保持3小时后,经4小时升温至1900℃,于1900℃保持2小时后,冷却至室温,从而制造六方晶氮化硼。使其破碎后,进行粉碎,进行筛分,制作块状氮化硼粒子。所制作的块状氮化硼粒子的平均粒径为20μm。
[0118]
(散热片用组合物的制作)
[0119]
在22g的有机硅树脂(wacker asahikasei silicone co.,ltd.制,型号:lr3303-20a)及22g的有机硅树脂(wacker asahikasei silicone co.,ltd.制,型号:lr3303-20b)
中,添加137g的所制作的块状氮化硼粒子,然后,以固态成分浓度成为60wt%的方式添加作为粘度调节剂的甲苯,使用涡轮型搅拌叶片,利用搅拌机(heidon公司制,商品名:three-one motor)混合15小时,制作散热片用组合物。
[0120]
(散热片的制作)
[0121]
在teflon(注册商标)片材上配置作为增强层的玻璃布(unitika ltd.制,商品名:h25 f104)后,利用逗号涂布机将上述的散热片用组合物以0.2mm的厚度涂敷于玻璃布上,于75℃进行5分钟干燥。接下来,以玻璃布成为上侧的方式将经干燥的散热片用组合物颠倒过来,利用逗号涂布机以0.2mm的厚度涂敷于玻璃布上,于75℃进行5分钟干燥,制作在玻璃布的两面涂敷有散热片用组合物的散热片用组合物的片材。其后,使用平板加压机(株式会社柳濑制作所制),在预加热温度为70℃、压力为120kgf/cm2的条件下进行8分钟的加压。其后,一边进行压力为150kgf/cm2的加压,一边以10℃/分钟的升温速度使温度上升至150℃。然后,在加热温度(固化起始温度以上的温度)为150℃、压力为150kgf/cm2的条件下进行45分钟的加压,制作厚度为0.30mm的散热片。接着,于常压以150℃的温度对其进行4小时的加热,将低分子硅氧烷除去,制作实施例1的散热片。需要说明的是,散热片中的相对于树脂粘结剂及无机填充材料的合计100体积%而言的无机填充材料的含量为60体积%。
[0122]
[实施例2]
[0123]
将利用逗号涂布机在玻璃布上涂敷使用与实施例1同样的原料制作的散热片用组合物时的厚度从0.2mm变更为0.15mm。接下来,以玻璃布成为上侧的方式将经干燥的散热片用组合物颠倒过来,在玻璃布上,利用逗号涂布机,将0.2mm的厚度变更成0.15mm来进行涂敷。除此以外,利用与实施例1同样的方法,制作厚度为0.20mm的实施例2的散热片。
[0124]
[实施例3]
[0125]
代替玻璃布(unitika ltd.制,商品名:h25 f104)而将作为基材树脂层的聚酰亚胺膜(du pont-toray co.,ltd.制,商品名kapton100h,厚度为0.026mm)配置于teflon(注册商标)片材上,然后,利用逗号涂布机将上述的散热片用组合物以厚度
○○
mm涂敷于聚酰亚胺膜上,于75℃进行5分钟干燥,制作在聚酰亚胺膜的一面涂敷有散热片用组合物的散热片用组合物的片材。除此以外,与实施例1同样地操作,制作实施例3的散热片。
[0126]
[比较例1]
[0127]
对于在玻璃布的两面涂敷有散热片用组合物的散热片用组合物的片材,在未进行预加热工序的情况下进行固化工序,除此以外,与实施例1同样地操作,制作比较例1的散热片。
[0128]
[实施例4]
[0129]
在17g的有机硅树脂(wacker asahikasei silicone co.,ltd.制,型号:lr3303-20a)及17g的有机硅树脂(wacker asahikasei silicone co.,ltd.制,型号:lr3303-20b)中,添加191g的氧化铝(电化株式会社制,商品名:daw-20)、82g的氧化铝(球状)(电化株式会社制,商品名:daw-03),然后,以固态成分浓度成为80wt%的方式添加作为粘度调节剂的甲苯,使用涡轮型搅拌叶片,利用搅拌机(heidon公司制,商品名:three-one motor)混合15小时,制作散热片用组合物,除此以外,利用与实施例1同样的方法,制作实施例4的散热片。需要说明的是,散热片中的相对于树脂粘结剂及无机填充材料的合计100体积%而言的无机填充材料的含量为70体积%。
[0130]
[实施例5]
[0131]
将利用逗号涂布机在玻璃布上涂敷使用与实施例4同样的原料制作的散热片用组合物时的厚度从0.2mm变更为0.15mm,接下来,以玻璃布成为上侧的方式将经干燥的散热片用组合物颠倒过来,在玻璃布上,利用逗号涂布机,将0.2mm的厚度变更成0.15mm来进行涂敷,除此以外,与实施例4同样地操作,制作实施例5的散热片。
[0132]
[比较例2]
[0133]
除了不进行预加热工序以外,利用与实施例4同样的方法,制作散热片。
[0134]
将实施例1~5及比较例1、2的散热片的评价结果示于表1。
[0135]
[表1]
[0136]
表1
[0137][0138]
由以上的评价结果可知,对于在上述绝缘击穿试验中、散热片发生绝缘击穿时的针状电极的尖端与铝板之间的距离大于0μm且为80μm以下、或者散热片不发生绝缘击穿而针状电极与铝板短路的散热片而言,即使夹入异物,也不易发生绝缘不良。
[0139]
另外,针对散热片发生绝缘击穿时的针状电极的尖端与铝板之间的距离为20μm的实施例1的散热片、及散热片发生绝缘击穿时的针状电极的尖端与铝板之间的距离为10μm的实施例3的散热片,依照jis c2110,于室温(23℃)进一步进行了短时击穿试验。其结果是,与实施例1的散热片相比,实施例3的散热片尽管厚度更小,但绝缘击穿电压仅高3kv。由此可知,通过在散热片中设置基材树脂层,从而散热片即使夹入异物,也更不易发生绝缘不良。
[0140]
附图标记说明
[0141]
1 耐受电压试验机
[0142]
11 基底板
[0143]
12、13 支柱
[0144]
14 固定板
[0145]
15 升降板
[0146]
16 测微头
[0147]
17、18 弹簧
[0148]
19、21 悬吊棒
[0149]
22、25 铝板
[0150]
23 针状电极
[0151]
24 工作台
[0152]
26 耐受电压测量仪
[0153]
30、53 散热片
[0154]
51 可动电极
[0155]
52 固定电极
[0156]
54 异物。