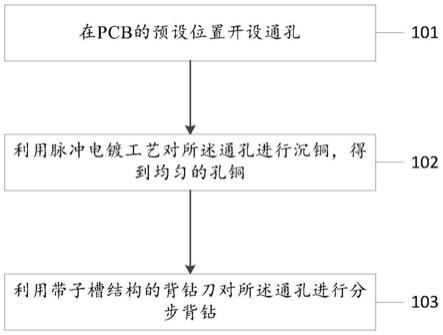
pcb背钻加工方法及pcb
技术领域
1.本技术涉及pcb制备技术领域,尤其涉及一种pcb背钻加工方法及pcb。
背景技术:2.pcb(printde circuit board),中文名称为印制电路板,作为电子元器件的支撑体,是一种重要的电子部件。pcb中过孔残桩(stub)对信号传输存在严重的影响,目前主要通过背钻方式减小过孔残桩的影响。
3.随着cpu的不断演进,导致用于安装cpu的pcb的加工难度增加—主要体现在pcb上用于安装cpu的位置针脚更密、传输线缩短且均以孔夹双线设计,传输线的损耗要求更高,且为降低损耗,该位置要求做背孔设计。
4.而采用现有的背钻加工方法对该位置进行背钻,会出现堵孔、背钻偏移、孔壁错位等缺陷,无法满足生产需求。
技术实现要素:5.为克服相关技术中存在的问题,本技术提供一种pcb背钻加工方法,该pcb背钻加工方法,能够避免背钻出现缺陷,满足生产需求。
6.本技术第一方面提供一种pcb背钻加工方法,包括:
7.在pcb的预设位置开设通孔;
8.利用脉冲电镀工艺对所述通孔进行沉铜,得到均匀的孔铜;
9.利用带子槽结构的背钻刀对所述通孔进行分步背钻,所述分步背钻为通过n次钻孔得到背钻孔,所述n根据所述背钻孔的深度确定,所述n为大于或等于1的整数。
10.在一种实施方式中,所述利用带子槽结构的背钻刀对所述通孔进行分步背钻包括:
11.获取所述预设位置的厚度;
12.根据所述厚度将所述预设位置上的通孔进行分类;
13.根据分类结果为所述通孔匹配对应的带子槽结构的背钻刀;
14.利用所述背钻刀对所述通孔进行分步背钻。
15.在一种实施方式中,所述n次钻孔的每次钻孔深度相等。
16.在一种实施方式中,所述在pcb的预设位置开设通孔之前,还包括:
17.内层板的线路设计,具体包括:对内层板的线路的稀疏区域和密集区域进行动态补偿设计;
18.采用真空蚀刻工艺对所述内层板进行线路蚀刻。
19.在一种实施方式中,所述进行内层的线路设计之后,所述采用真空蚀刻工艺对所述内层进行线路蚀刻之前,还包括:
20.通过激光直接成像技术ldi将线路图像转移到所述内层板。
21.在一种实施方式中,所述采用真空蚀刻工艺对所述内层板进行线路蚀刻之后,还
包括:
22.压合,具体包括:采用pin
‑
lam定位系统进行叠板压合;
23.测量各层间的涨缩值;
24.根据测量结果调整所述压合的控制参数,使得各层间的所述涨缩值相等。
25.在一种实施方式中,所述利用带子槽结构的背钻刀对所述通孔进行分步背钻之后,还包括:
26.利用超声波清洗所述背钻孔内的铜屑。
27.本技术第二方面提供一种pcb,该pcb采用第一方面提供的pcb背钻加工方法中的任一种pcb背钻加工方法制作。
28.本技术提供的技术方案可以包括以下有益效果:
29.本方案通过在pcb的预设位置开设通孔;利用脉冲电镀工艺对通孔进行沉铜,得到均匀的孔铜;利用带子槽结构的背钻刀对通孔进行分步背钻,分步背钻为通过n次钻孔得到背钻孔。均匀的孔铜可以保证钻孔过程中,背钻刀受力均匀,不会发生偏移而导致钻孔偏移,且通过脉冲电镀可以得到合理孔铜厚度进而保证钻孔过程中,背钻刀磨损减少,受阻程度降低;同时采用带子槽结构的背钻刀进行分步背钻,每一步钻孔结束,背钻孔内铜屑可以被有效带出孔外,避免堵孔的发生。
30.应当理解的是,以上的一般描述和后文的细节描述仅是示例性和解释性的,并不能限制本技术。
附图说明
31.通过结合附图对本技术示例性实施方式进行更详细的描述,本技术的上述以及其它目的、特征和优势将变得更加明显。
32.图1是本技术实施例示出的pcb背钻加工方法的流程示意图;
33.图2是本技术实施例示出的pcb背钻加工方法的另一流程示意图。
具体实施方式
34.下面将参照附图更详细地描述本技术的优选实施方式。虽然附图中显示了本技术的优选实施方式,然而应该理解,可以以各种形式实现本技术而不应被这里阐述的实施方式所限制。相反,提供这些实施方式是为了使本技术更加透彻和完整,并且能够将本技术的范围完整地传达给本领域的技术人员。
35.在本技术使用的术语是仅仅出于描述特定实施例的目的,而非旨在限制本技术。在本技术和所附权利要求书中所使用的单数形式的“一种”、“所述”和“该”也旨在包括多数形式,除非上下文清楚地表示其他含义。还应当理解,本文中使用的术语“和/或”是指并包含一个或多个相关联的列出项目的任何或所有可能组合。
36.应当理解,尽管在本技术可能采用术语“第一”、“第二”、“第三”等来描述各种信息,但这些信息不应限于这些术语。这些术语仅用来将同一类型的信息彼此区分开。例如,在不脱离本技术范围的情况下,第一信息也可以被称为第二信息,类似地,第二信息也可以被称为第一信息。由此,限定有“第一”、“第二”的特征可以明示或者隐含地包括一个或者更多个该特征。在本技术的描述中,“多个”的含义是两个或两个以上,除非另有明确具体的限
定。
37.采用现有的背钻加工方法对pcb上用于安装cpu的位置进行背钻,会出现堵孔、背钻偏移、孔壁错位等缺陷,无法满足生产需求。
38.针对上述问题,本技术实施例提供一种pcb背钻加工方法,能够避免背钻产生缺陷,可以满足生产需求。
39.以下结合附图详细描述本技术实施例的技术方案。
40.实施例一
41.图1是本技术实施例示出的pcb背钻加工方法的流程示意图。
42.参见图1,该pcb背钻加工方法具体包括:
43.101.在pcb的预设位置开设通孔;
44.背钻即利用机械钻孔机的深度控制功能,在某些镀通孔上用较大直径的钻刀钻具有一定深度的非导通孔,以除去部分孔铜。预设位置即需要进行背钻的位置。在该步骤中在pcb上需要进行背钻的对应位置进行钻通孔操作,简称为“一钻”。一钻采用4靶定位。
45.102.利用脉冲电镀工艺对所述通孔进行沉铜,得到均匀的孔铜;
46.脉冲电镀是使电镀回路周期性地接通和断开,或者在固定直流上再叠加某一波形脉冲的电镀方法。与普通电镀相比,这种方法具有镀层平整致密、附着性好,电流效率高、环保性能好等优点,在一般的研究和应用中,脉冲电镀所使用的脉冲方式可分为单向脉冲和双向脉冲两种。使用的脉冲波主要是矩形波和正弦波。
47.沉铜是在已钻孔的不导电的孔壁基材上镀上一层铜。
48.为了避免出现孔铜部分厚部分薄导致背钻刀在钻背钻孔时,各部位受力不均匀产生偏移,进而导致所钻出来的背钻孔发生偏移,在本实施例中,采用脉冲电镀工艺为步骤101中得到的通孔镀上一层均匀的孔铜。将脉冲电镀密度控制在15asf以下,长时间的电镀,空桶控制在30μm以内。
49.103.利用带子槽结构的背钻刀对所述通孔进行分步背钻;
50.带子槽结构的背钻刀即背钻刀上开设有排屑空间,在钻孔过程中,钻削所产生的铜屑会经由排屑空间排出。
51.分步背钻即通过背钻刀n次钻孔得到背钻孔,其中每次钻孔完毕后,背钻刀都会退出背钻一次,这样每次钻孔所产生的铜屑会被背钻刀有效带出孔外。且分步背钻可以延长背钻刀的寿命和保证pcb的性能稳定性,因为钻孔过程摩擦生热,背钻刀和背钻孔附件的温度会急剧升高,温度的升高会对内层铜和背钻刀产生影响,而采用分步背钻,背钻刀每完成一步钻孔都退出背钻孔,再重新进入,这样在背钻刀退出背钻孔后,背钻刀和背钻孔都能实现快速降温,不会形成热量的堆积。n根据背钻孔的深度和背钻刀的型号确定,具体的确定过程为不断试刀的过程:用同一型号的背钻刀在同一种pcb上钻不同深度的背钻孔,记录不同钻孔深度的钻孔效果,用无限逼近的方法,不断调整钻孔的深度直至找到能达到最佳钻孔效果的最优钻孔深度,以最优钻孔深度作为分步背钻中每次钻孔的最大钻孔深度,最佳钻孔效果可以理解为不偏钻且孔内无残留铜屑。
52.较佳地,利用带子槽结构的背钻刀对所述通孔进行分步背钻这一步骤可以优化成:获取预设位置的厚度;根据厚度将预设位置上的通孔进行分类;根据分类结果为通孔匹配对应的带子槽结构的背钻刀;利用所述背钻刀对所述通孔进行分步背钻。因为制造pcb的
每一个工艺流程都会产生一定的误差,有一些误差会导致pcb各个区域的厚度存在一定的差异,而不同厚度直接影响了背钻孔的实际深度,所以为了能钻出质量更好的背钻孔,需要通过不同厚度采用不同的背钻刀来钻孔的方法,将pcb的厚度这一影响因素带给被背钻孔的误差消除掉。这里所说的不同的背钻刀主要是不同寿命的背钻刀,因为背钻刀的寿命决定了背钻刀的钻削能力,而厚度厚的需要的钻削的次数会更多,所以的钻削能力更强,厚度薄的所需要的钻削能力弱一点。
53.进一步的,n次钻孔的每次钻孔深度相等。根据前述可知n等于背钻孔深度除以最佳钻孔深度,且逢小数自动进一位取整数,这样可能会出现的情况是,钻每个背钻孔的最后一刀的深度都是小于最优钻孔深度的,且钻孔深度不同,会导致控制的复杂程度提高,所以做出进一的优化,先通过背钻孔深度除以最佳钻孔深度,且逢小数自动进一位取整数求得对应的n,再通过背钻孔深度除以n得到实际的每次钻孔深度。如此每一刀的钻孔深度都是相等的,且都能达到最佳钻孔效果。
54.本实施例通过在pcb的预设位置开设通孔;利用脉冲电镀工艺对通孔进行沉铜,得到均匀的孔铜;利用带子槽结构的背钻刀对通孔进行分步背钻,分步背钻为通过n次钻孔得到背钻孔。均匀的孔铜可以保证钻孔过程中,背钻刀受力均匀,不会发生偏移而导致钻孔偏移,同时采用带子槽结构的背钻刀进行分步背钻,每一步钻孔结束,背钻孔内铜屑可以被有效带出孔外,避免堵孔的发生。
55.实施例二
56.本实施例提供一种pcb背钻加工方法,与上一实施例相比,本实施例进一步对pcb压合前的工艺进行优化设计,以给背钻创造更好的基础,如图2所示,具体包括:
57.201.内层板的线路设计;
58.具体包括:对内层板的线路的稀疏区域和密集区域进行动态补偿设计。
59.线路设计主要包括外部连接的布局、内部电子元件的布局、金属连线和通孔的布局。以eagle stream平台为例,其10z内层的双线线宽间距:3.5/4/3.5,需要在4mil的间距上钻背钻孔,导致背钻的容错率很低—只要发生偏钻或者错位,背钻刀钻孔时就可能将背钻孔两侧的线路钻削掉,最终会影响整个pcb的性能。为了提高背钻的容错率,在进行内层板的线路设计时,将线路秘籍的区域和线路稀疏的区域进行动态补偿—稀疏区域的线路间距适当减小,密集区域的线路间距适当增大。线路密集区域的线路间距增大,大大降低因背钻导致pcb内层线路出现电路缺陷的机率。
60.202.通过激光直接成像技术ldi将线路图像转移到所述内层板;
61.ldi是用激光扫描的方法直接将线路图像在pcb上成像,图像更精细,因省去曝光过程中的底片工序,节省装卸底片时间和成本,以及减小了因底片涨缩引发的偏差。偏差会导致内层线路与背钻孔区域产生相交,从而导致背钻时内层线路被背钻刀钻削,所以涨缩偏差的减小同样降低了背钻刀对内层线路的钻削机率。
62.203.采用真空蚀刻工艺对所述内层板进行线路蚀刻;
63.pcb进行蚀刻工艺时会出现水池效应:pcb水平传送时,位于板子下面和板子上面靠近边缘部分,蚀刻液容易流走,新旧蚀刻液更容易进行交换;而板中心的位置,容易形成“水池”,蚀刻液流动受到限制;因此pcb板上面中间的线路会比其他位置的蚀刻效果差一些。为了阻止“水池效应”的产生,通过吸取使用过的蚀刻液来可改善板面上部分的蚀刻液
的流动性,这种方法被称为真空蚀刻。真空蚀刻的实现原理:在蚀刻段中安装了喷嘴,也在喷管之间离线路板表面相对距离较近的位置安装了抽气单元。抽气单元使操作区域形成负压,刚好够防止蚀刻液产生“水池效应”的较低的吸力。经比较,板朝上部分与朝下部分的蚀刻效果基本一致。采用真空蚀刻进行内层线路蚀刻得到的铜厚度分布均匀。
64.204.采用pin
‑
lam定位系统进行叠板压合;
65.pin
‑
lam的制作流程包括:开机设置叠合模式—根据板厚、拼版尺寸与批量选择pin钉与钢板规格与数量,设置自动模式,掀起盖板;底盘定位与上pin钉—底盘移至中间,插上4个pin钉后顶起底盘,对准4个pin钉隔上18张新牛皮纸后盖上钢板;pcb板pin组合1—对准4个pin钉铺上下层清洁过的铜箔、pp片与芯片,按平芯板槽pin位置,检查pin高度是否足够长;pcb板pin组合2—对准4个pin钉铺上层铜箔,并清洁后盖上钢板,扭转开关,将pin针升至出板面3
‑
4mm的高度;循环第二、三层至完成—隔上牛皮纸扭动开关,缓慢将盖板方向并对准pin盖上,pin钉必须插上盖板3
‑
5mm的长度,严禁高出盖板。采用pin
‑
lam定位系统进行压合工艺,可以减小层间偏差,采用ldi和pin
‑
lam生产可以将层间偏差控制4mil以内,可以有效降低因背钻导致内层线路出现故障的机率。
66.优化地,压合之后测量各层间的涨缩值,然后根据测量结果调整压合的控制参数,使得各层间的涨缩值相等
67.205.开设通孔
‑
沉铜
‑
分步背钻;
68.该步骤的内容与实施例中步骤101
‑
103的内容相似,此处不作赘述,需要说明的是,分步背钻的每一次钻孔都是采用cdd自动对位,同时将铝片提前开cdd定位窗,避免铝片上台面时蘑菇头撞击板面导致定位偏移。背钻刀的寿命控制在200以内。
69.206.利用超声波清洗所述背钻孔内的铜屑;
70.超声波清洗(ultrasonic cleaning)是利用超声波在液体中的空化作用、加速度作用及直进流作用对液体和污物直接、间接的作用,使污物层被分散、乳化、剥离而达到清洗目的。目前所用的超声波清洗机中,空化作用和直进流作用应用得更多。
71.背钻完成后将pcb过超声波和高压水洗,背钻面向下,过机速度需要控制在2m/min以内,100%验孔透光状态。
72.本实施通过对内层板的线路的稀疏区域和密集区域进行动态补偿设计,提高背钻的容错率;ldi和pin
‑
lam的结合使用,以将层间偏差控制在小范围内,降低背钻刀对内层线路的钻削机率;再通过超声波对背钻孔进行清洗,以清除背钻孔内可能残留的铜屑。同时对多个工艺进行调整优化,避免了背钻出现堵孔、偏移和孔壁错位等缺陷,满足生产需求。
73.附图中的流程图和框图显示了根据本技术的多个实施例的系统和方法的可能实现的体系架构、功能和操作。在这点上,流程图或框图中的每个方框可以代表一个模块、程序段或代码的一部分,所述模块、程序段或代码的一部分包含一个或多个用于实现规定的逻辑功能的可执行指令。也应当注意,在有些作为替换的实现中,方框中所标记的功能也可以以不同于附图中所标记的顺序发生。例如,两个连续的方框实际上可以基本并行地执行,它们有时也可以按相反的顺序执行,这依所涉及的功能而定。也要注意的是,框图和/或流程图中的每个方框、以及框图和/或流程图中的方框的组合,可以用执行规定的功能或操作的专用的基于硬件的系统来实现,或者可以用专用硬件与计算机指令的组合来实现。
74.以上已经描述了本技术的各实施例,上述说明是示例性的,并非穷尽性的,并且也
不限于所披露的各实施例。在不偏离所说明的各实施例的范围和精神的情况下,对于本技术领域的普通技术人员来说许多修改和变更都是显而易见的。本文中所用术语的选择,旨在最好地解释各实施例的原理、实际应用或对市场中的技术的改进,或者使本技术领域的其它普通技术人员能理解本文披露的各实施例。