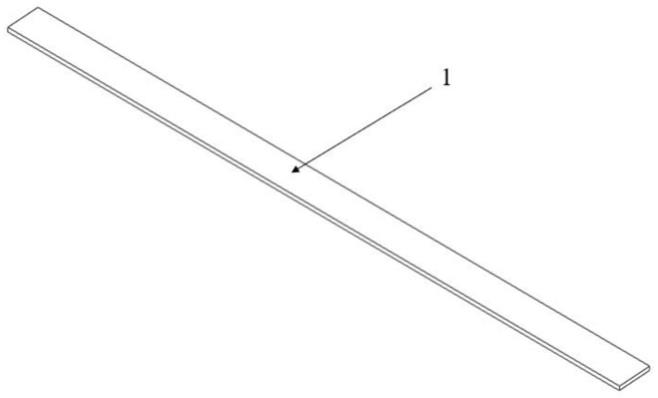
1.本发明提供一种可刚化的充气展开复合材料结构,属于复合材料结构设计领域。
背景技术:2.随着航天技术与工程实践的发展,航天器体积需求与运载器容积的矛盾始终是一个未解决的难题,解决这一难题的需要直接促进了充气展开结构的研究和发展。充气展开结构是指通过将原始构型按照特定的折叠方式折叠放置于装载装置中,待到需要时利用充气装置进行充气展开达到原始构型的结构。充气展开结构凭借其折叠后体积小、重量轻、工作效率较高的特点近几年在航空器上得到了广泛的应用,尤其是在大型空间结构如大型空间天线、薄膜太阳动力帆板、轻质运载工具、太空基地等有较好的应用前景。目前,传统的充气展开结构研究多以柔性薄膜材质为主,柔性薄膜充气展开结构虽然能较好地实现充气展开功能,但仍然存在一些如展开后刚度较小、展开过程不平稳、存在褶皱等问题,由于复合材料较传统薄膜材料具有刚度大、性能优越、可靠性高、耐腐蚀、可设计性强的优点,通过多组分材料在性能上起协同作用具有单一材料无法比拟的优越综合性能,在航空航天等领域中已经得到了广泛的应用。基于此,本发明一种可刚化的充气展开复合材料结构,充气展开复合材料结构具有性能优越、结构简单、可设计性强、刚度大、刚柔结合、结构稳定性好、展开形状精度高、可靠性较高的优点。此外,通过具有可设计性的加热片还可消除折叠方案所设计的折痕区域对展开后的褶皱与折痕处应力集中影响,因此,本发明有非常好的工程应用价值。
技术实现要素:3.本发明的目的在于提供一种可刚化的充气展开复合材料结构,以解决传统的充气展开结构存在刚度小、折痕处应力集中、展开形状精度低、展开后力学性能较差等问题。
4.本发明所采用的技术方案如下:
5.本发明提供一种可刚化的充气展开复合材料结构,由内胆、复合材料、加热片、端盖构成。充气展开复合材料结构的原始构型通过特定的折叠方式转变为折叠形态,此处采用z型折叠方式,横截面分为三部分,最外层为加热片,外层为复合材料,内层为内胆,在折叠的过程中内胆和外层复合材料共同到达折叠形态,充气展开过程内胆带动外层复合材料共同达到展开状态。内胆的材质为高分子聚合物材料,复合材料的组分为基体材料和增强材料,通过对复合材料加热,达到满足折叠要求的材料软化温度时,复合材料的刚度变小,加热部位的材料会及其柔软。本发明的充气展开复合材料结构通过贴加热片的方式对折叠展开过程中充气展开复合材料结构折叠方案所设计的折痕区域处的材料进行加热软化,实现充气展开复合材料结构在折叠展开过程刚柔结合;还作为一种锁定装置,在对折痕区域加热软化时整个充气展开复合材料结构处于开锁状态,折痕区域冷却时整个充气展开复合材料结构形状被固定,处于锁定状态,充气展开复合材料结构具有很好的稳定性;使用具有增强体的复合材料可获得刚度较大的充气展开复合材料结构;在充气展开复合材料结构折
叠方案所设计的折痕区域贴上加热片,加热片经过折叠前加热-展开过程加热-展开完成冷却的三重过程,实现在特定折叠方式下充气后顺利展开,消除了折痕区域的褶皱和折痕处应力集中的影响,获得了展开形状精度高且稳定的充气展开复合材料结构。
6.本发明提供一种可刚化的充气展开复合材料结构,所指的特定的折叠方式为随机折叠方式、z型折叠方式、卷曲折叠方式、多边形折叠方式、基于约束的折叠方式、基于压平-分析的折叠方式。
7.本发明提供一种可刚化的充气展开复合材料结构,内胆所用的高分子聚合物材料为聚乙烯、聚四氟乙烯、环氧树脂、苯乙烯、苯乙烯-丁二烯、反式聚异戊二烯、氰酸酯、聚氨酯、氯化聚乙烯、聚乙烯醇、丁基橡胶,充气展开复合材料结构中所述的“基体材料”为环氧树脂、聚酰亚胺树脂、双马来酰亚胺树脂、聚甲醛树脂、聚氯乙烯、聚乙烯和聚丙烯等聚烯烃树脂、不饱和聚酯,所述的“增强材料”为碳纤维、玻璃纤维、芳纶纤维、硼纤维、碳化硅纤维、植物纤维或以上纤维织物或以上纤维的短切纤维。
8.本发明提供一种可刚化的充气展开复合材料结构,所指的加热片具有可设计性,加热片可以任意形状贴在充气展开复合材料结构的任意位置,在对充气展开复合材料结构进行折叠前,对于不同的折叠方式可通过预先将加热片贴在充气展开复合材料结构中出现的任意折痕区域,通过加热加热片提前软化材料,冷却加热片恢复刚度,实现刚度较大的充气展开复合材料结构的顺利折叠和充气展开。
9.本发明提供一种可刚化的充气展开复合材料结构,充气展开复合材料结构的折叠后充气展开的步骤为:首先在充气展开复合材料结构折叠方案所设计的折痕区域处贴上加热片,对加热片通电进而加热折痕区域,达到满足折叠要求的材料软化温度时,此时加热片覆盖折痕区域处材料变的柔软,按照特定的折叠方式沿折叠方案所设计的折痕对充气展开复合材料结构进行折叠转变为折叠形态,对加热片断电冷却,此时整个充气展开复合材料结构的折痕区域重新变的刚硬,折叠形状被固定下来并处于锁定状态;需要充气展开时,在充气展开的过程中对所有加热片通电加热,此时充气展开复合材料结构的折痕处受到加热片的热作用,折痕区域再次达到材料软化温度,此时对充气展开复合材料结构充气,进行展开。被加热的折痕区域外的部位保持原有的刚度,实现折叠和充气展开过程刚柔结合,有利于提高展开效率和精度;等到充气展开复合材料结构达到完全展开形态后,断电使加热片冷却降温,此时加热片所覆盖的原有折痕区域恢复原有的刚度,充气展开结构再次处于锁定状态,消除了折痕区域的褶皱和折痕处应力集中的影响,获得了刚度大、展开形状精度较高、折展过程刚柔结合的充气展开复合材料结构。
10.本发明提供一种可刚化的充气展开复合材料结构,有益效果是本发明的充气展开复合材料结构具有性能优越、结构简单、可设计性强、刚度大、刚柔结合、结构稳定性好、展开形状精度高、可靠性较高的优点。此外,通过具有可设计性的加热片还可消除折叠方案所设计的折痕区域对展开后的褶皱与折痕区域应力集中的影响,因此,本发明有非常好的工程应用价值。
附图说明
11.图1是加热片的示意图。
12.图2是充气展开复合材料结构的内胆的示意图。
13.图3是充气展开复合材料结构最大端面的剖视示意图。
14.图4是充气展开复合材料结构折叠形态的示意图。
15.图5是充气展开复合材料结构展开过程的示意图。
16.图6是充气展开复合材料结构不同角度展开过程的示意图。
17.图7是充气展开复合材料结构展开形态的示意图。
18.图1中:1.加热片。
19.图2中:2.内胆。
20.图3中:3.复合材料结构。
21.图4中:4.密封端盖,5.开口端盖。
具体实施方式
22.下面结合附图和实施实例对本发明做出进一步的说明。
23.本发明提供一种可刚化的充气展开复合材料结构,由内胆、复合材料、加热片、端盖构成。充气展开复合材料结构的原始构型通过特定的折叠方式转变为折叠形态,此处采用z型折叠方式,横截面分为两部分,外层为复合材料,内层为内胆,内胆所用的高分子聚合物材料为聚乙烯、聚四氟乙烯、环氧树脂、苯乙烯、苯乙烯-丁二烯、反式聚异戊二烯、氰酸酯、聚氨酯、氯化聚乙烯、聚乙烯醇、丁基橡胶,充气展开复合材料结构中所述的“基体材料”为环氧树脂、聚酰亚胺树脂、双马来酰亚胺树脂、聚甲醛树脂、聚氯乙烯、聚乙烯和聚丙烯等聚烯烃树脂、不饱和聚酯,所述的“增强材料”为碳纤维、玻璃纤维、芳纶纤维、硼纤维、碳化硅纤维、植物纤维或以上纤维织物或以上纤维的短切纤维。
24.本发明实施例中,充气展开复合材料结构上所用的加热片1(如图1所示)具有很强的可设计性,材质柔软,可以任意形状贴在充气展开复合材料结构的任意折痕区域处,如图2所示,内胆2选取高分子聚合物材料,以特定的折叠方式放置于外层的复合材料内,在其底端设置进气口,具体地,如图3所示,充气展开复合材料结构端面的剖视图中外层为复合材料结构3,内层为内胆2,在复合材料结构3的折痕区域贴上加热片1,同时初始折叠形态下复合材料结构3和内胆2具有一定的间距,在充气展开复合材料结构达到完全展开形态时,复合材料结构3和内胆2的间距变为0,此时内胆2外侧完全和复合材料结构3内侧完全重合。
25.本发明实施例中,如图4所示,充气展开复合材料结构采取特定的折叠方式(此处采取z型折叠)由原始的充气展开复合材料结构展开形态(如图5所示)转变为充气展开复合材料结构折叠形态,充气展开复合材料结构的两侧分别设有端盖,一侧为密封端盖4,另一侧为设有进气口的开口端盖5,在充气展开复合材料结构折叠形态的折痕处分别贴上了加热片1,具体地,充气展开复合材料结构进行先折叠后再充气展开的过程:首先在充气展开复合材料结构展开形态(如图6所示)的折叠方案所设计的折痕区域处分别贴上加热片1,此时通电对折叠方案所设计的折痕区域处的加热片进行加热,进而使折叠方案所设计的折痕区域处的材料变的柔软,达到满足折叠要求的材料软化温度时,充气展开复合材料结构处于开锁状态,按照折叠方案所设计的折痕进行折叠到达充气展开复合材料结构折叠形态(如图4所示),达到折叠状态时便可断电对加热片1冷却,充气展开复合材料结构折叠形态固定,处于锁定状态,此折叠过程实现刚柔结合,且充气展开复合材料结构由初始的折痕区域加热软化的开锁状态到达充气展开复合材料结构折叠后冷却的锁定状态;待到需要进行
充气展开时,此时通电对覆盖在充气展开复合材料结构折叠形态(如图4所示)折痕区域处的加热片1进行加热,达到满足折叠要求的材料软化温度时,充气展开复合材料结构再次处于开锁状态,对充气展开复合材料结构折叠形态(如图4所示)进行充气,此时气体由开口端盖5的充气口进入到内胆2中,外层的复合材料结构3在内胆2的带动下进行展开,充气展开复合材料结构的展开过程如图5所示,充气展开复合材料结构的不同角度的展开过程如图6所示,折叠方案所设计的折痕区域处的材料变得柔软,保证了充气展开复合材料结构的顺利展开,此外由于加热片1使复合材料结构3的折痕处材料极为柔软,未贴加热片的区域则仍保持原有的刚度,实现了充气展开复合材料结构充气展开过程的刚柔结合的特性,充气达到所需的气体量后,最终充气展开后到达充气展开复合材料结构展开形态(如图7所示),断电加热片1冷却,此时充气展开复合材料结构整体恢复原有的较大刚度,充气展开复合材料结构形状被固定,处于锁定状态,消除了折叠方案设计的折痕区域的褶皱和折痕处应力集中的影响,最终获得刚度大、展开形状精度较高、结构稳定性好、折展过程刚柔结合的充气展开复合材料结构。