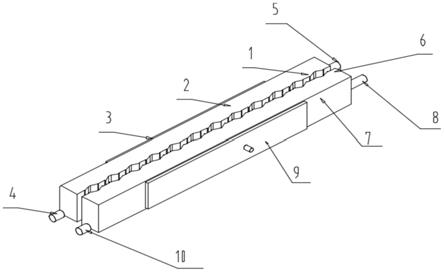
:
1.本发明涉及一种带流体通道的产品成型装置,适用于冷冻饮品机械上,属于食品机械技术领域。
背景技术::
2.现有的冷冻饮品、食品等模具的冻结和解冻方式相对较耗能和低效,其冻结成型往往采用浸入的方式,即将灌注了原料的模具的一部分浸入冷冻液中,然后经过相对较长的时间冷冻后从而将产品冻结成型,待产品冻结成型后进一步到达脱模区域进行脱模。脱模一般采用喷淋的方式,即将解冻液喷射到模具的下部,从而使产品表面解冻,且一体模模具还需机械手辅助将产品取下,才能顺利完成脱模,且产品的外观质量相对较差,产品颜色较为单一,无法满足市场需求。
3.上述结构的产品冻结成型方式适合一体模具,普适性较差;同时这种冻结成型方式也增加了产品被污染的可能,因此一种高效、低耗、卫生的冷冻饮品模具是必不可少的。
技术实现要素::
4.本发明针对现有技术存在的问题,提供一种带流体通道的产品成型装置,以提高产品的成型效率和成型质量。
5.本发明的具体技术方案如下:
6.一种带流体通道的产品成型装置,该装置包括可开合式配合的第一模具和第二模具,第一模具和第二模具组合时形成产品模腔,所述第一模具设有第一换热装置,第二模具设有第二换热装置。
7.进一步地,所述第一换热装置设置在第一模具外侧,与第一模具为一体式结构或组合式结构;所述第二换热装置设置在第二模具外侧,与第二模具采用一体式结构或组合式结构。
8.进一步地,所述第一模具和第二模具采用单模或多模结构。
9.进一步地,所述第一模具与第二模具采用左右平移开合结构或旋转开合结构。
10.进一步地,所述旋转式开合结构的第一模具和第二模具底部通过转轴铰接,所述左右平移开合结构时,两半模具通过开合板与动力单元相连接,进料口位于模具上方。
11.进一步地,第一、第二换热装置均设有介质腔、进液口与出液口。
12.进一步地,第一、第二换热装置为腔体结构,内侧壁为模具或与模具连接为一体,外周壁设置保温层。
13.进一步地,所述介质腔与模具规格相当,介质腔采用直通式结构或采用由隔板分隔的结构。
14.进一步地,所述隔板分隔式结构采用沿介质腔高度方向分层设置的多隔板结构;或采用沿介质腔长度方向设置的单隔板结构,并在单隔板上均匀设有若干喷淋孔。
15.进一步地,所述进液口经三通管分别连接冷冻液供液管路和脱模液供液管路以及
通气管路;所述出液口分别经二通管连接冷冻液回收管路和脱模液回收管路。
16.进一步地,所述进液口与出液口设置在换热装置的同侧或异侧,或进液口设置在换热装置的中部。
17.进一步地,所述第一模具和第二模具分别与开模机构传动连接。
18.本发明相比现有技术具有如下技术效果:
19.1、本发明带流体通道的产品成型装置采用两组模分别配置换热装置,通过换热装置与模具作用,完成模具内产品的成型与脱模,控制灵活、便捷;
20.2、本发明设计巧妙、结构简单,模具与换热装置组合设计,冷冻液和解冻液在换热装置介质腔体内流动,便于实现成型与脱模的精准控制,加工效率高;
21.3、本发明采用开合式模具结构,冷冻液与解冻液密封在介质腔中,实现了与产品的完全隔离,保证了产品的卫生与安全。
22.4、本发明带流体通道的产品成型装置,外置有保温层结构,保证了在产品的冷冻与解冻过程中,高效率的传递冷冻液与解冻液的能量,降低了损耗,确保产品脱模顺利,保证产品质量。
23.5、本发明采用开合式模具结构,可加工三色及多色产品,加工品种丰富,并更好的实现了产品的冻结与脱模,产品质量更高。
附图说明:
24.图1为带流体通道的产品成型装置结构示意图;
25.图2为带流体通道的产品成型装置的侧视图;
26.图3为图2的a
‑
a向视图;
27.图4为带流体通道的产品成型装置开模状态示意图;
28.图5为图4的b
‑
b向视图;
29.图6为带流体通道的产品成型装置闭模状态示意图;
30.图7为图5的c
‑
c向视图;
31.图8为带流体通道的产品成型装置的旋转开合方式示意图;
32.图9为图6的d
‑
d向视图;
33.图10为图9的e
‑
e向视图;
34.图中:1
‑
第一模具;2
‑
第一换热装置;3
‑
第一开合板;4
‑
出液口;5
‑
进液口;6
‑
第二模具;7
‑
第二换热装置;8
‑
进液口;9
‑
第二开合板;10
‑
出液口;11
‑
隔板;12
‑
隔板;13
‑
模腔; 14
‑
转轴;15
‑
旋转板;16
‑
拉杆;17
‑
保温层;18
‑
喷淋孔。
具体实施方式:
35.实施例一:
36.本发明的带流体通道的产品成型装置,如图1所示,包括第一模具1、第二模具6、第一换热装置2、第二换热装置7,第一模具1和第二模具6采用可开合式结构,第一模具1和第二模具6组合时形成完整的产品模腔。第一模具1设有第一换热装置2,并且两者设置为一体;第二模具6设有第二换热装置7,并具两者设置为一体。第一模具1和第二模具6采用相同的多模结构。
37.第一换热装置2和第二换热装置7分别设有介质腔、进液口与出液口。为保证换热充分,介质腔与模具规格相当,介质腔采用直通式结构或采用由隔板分隔式结构。
38.如第一换热装置的进液口5经三通管分别连接冷冻液供液管路和脱模液供液管路以及通气管路;出液口4分别经二通管连接冷冻液回收管路和脱模液回收管路。第二换热装置的进液口8与出液口10接法亦同。
39.工作时,第一、第二模具组合,向模具内灌注物料,物料灌注模具时,两组模具的换热装置的进液口同步灌入冷冻液,开始冻结模具原料,冷冻液又分别从相应的出液口流出,并流回冷冻液的回收装置,从物料灌注到产品冻结完成,换热装置内的冷冻液一直流动,可循环使用,较为精确的保证了产品冻结所需要的温度,且冷冻液用量少,耗能小,效率高。
40.当产品冻结完成,模具逐步向脱模区域移动,冷冻液停止泵入。由阀切换至解冻液管路,解冻液开始由两组模具的进液口流入,并由两组模具的出液口流回,期间解冻夜循环流动,保证达到产品脱模所需的温度,而后第一、第二模具同时打开,产品即可顺利脱模,保证了产品的卫生,脱模结束而解冻夜也停止泵入,产品脱模完成后。进入下一次灌注、成型、脱模,以此循环往复。此模具装置高效、节能、卫生,降低了投入成本,提高了产品竞争力,并且本发明可以根据不同的需求相应的增加或减少模具的数量。
41.实施例二:
42.如图1所示,本发明带流体通道的产品成型装置中,第一模具1与第二模具6 采用左右平移开合结构,两半模具通过开合板与动力单元相连接,进料口位于模具上方。模具采用多模腔结构。
43.第一换热装置2设置在第一模具1外侧,并与第一模具连接为一体;第二换热装置7 设置在第二模具6外侧,并与第二模具连接为一体。
44.第一、第二换热装置均设有介质腔、进液口与出液口。
45.第一模具和第二模具均设有进液口和出液口,进液口与出液口分别设置在换热装置的两侧。其中进液口经三通管分别连接冷冻液供液管路和脱模液供液管路以及通气管路;出液口分别经二通管连接冷冻液回收管路和脱模液回收管路。第一模具1和第二模具6通过分别与开模机构传动连接,实现模具有开合动作。
46.如图2、图3所示,第一、第二换热装置的介质腔均与模具的长宽尺寸规格相当,介质腔采用直通式结构,通过控制换热介质的流速,控制成型速度或脱模速度。由于产品成型时,模具中需要通冷冻液,产品脱模时需要通入脱膜液,不同阶段分别通入介质腔。成型时通过进液口通入冷冻液,快至脱模区时,冷冻液全部排出,经控制阀切换通入脱模液,脱模后脱模液停止泵入,准备下一次成型。
47.第一、第二模具闭合后结构如图6所示,形成完整的模腔13,或以通过灌注的方式向模腔内灌料,之后进一步成型、脱模。
48.实施例三:
49.本实例进一步设计在于,第一换热装置2与第一模具1采用一体结构,第二换热装置 7与第二模具6为一体结构,模具即为换热装置的侧壁,其他结构同实施例二。
50.实施例四:
51.如图5所示,本实例进一步设计在于,第一模具和第二模具匀采用导热的金属材料制作而成,便于换热及产品成型。第一、第二换热装置为腔体结构,内侧壁即为模具,外周壁
设置保温层,以防止换热装置的热量散失。本装置用于生产冷饮产品时,冷冻液的温度一般为
‑
50℃左右,脱模液温度一般为15℃。
52.实施例五:
53.如图4、图7所示,本实例进一步设计在于,带流体通道的产品成型装置中,第一、第二换热装置均设置隔板,第一换热装置沿介质腔高度方向分层设置三层隔板11,第二换热装置内沿介质腔高度方向分层设置三层隔板12,通过隔板将换热装置的介质腔上、下封闭式分隔,冷冻液或解冻液进入介质腔分层流动,可以有效地控制冷冻和解冻的效果,使换热均匀,保证产品的质量,介质腔还可以采用其他分隔方式,以便于介质与模具充分作用,提高效果。
54.实施例六:
55.如图9、图10所示,本实例进一步设计在于,第一、第二换热装置采用沿介质腔长度方向设置的单隔板结构,并单隔板上均匀设有若干喷淋孔18。使用时,液体经单隔板上喷淋孔18淋向模具,与模具换热。该换热装置的进液口设置在第一、第二换热装置的中部,出液口设置在换热装置朝向内侧的一侧。进液口设在换热装置中部,利于模具换热均匀。
56.实施例七:
57.如图8所示,本实例可选设计在于,带流体通道的产品成型装置中,第一模具1和第二模具采用旋转开合结构,第一模具和第二模具底部通过转轴铰接,进料口位于模具上方。模具采用多模腔结构。其中,第一模具和第二模具底部分别通一组旋转板15较接在转轴 14上,旋转板15上设有拉杆16,由拉杆16连接传动机构,控制模具的开合,进料口位于模具上方。模具打开时,第一模具和第二模具绕转轴14旋转,模具中成型好的产品可以通过下料装置取走;第一、第二模具闭合时,物料由模具上部进料口进料,模具底部密封。通过第一、第二换热装置完成产品的成型和脱模。
58.以上所述仅为本发明示意性的具体实施方式,并非用以限定本发明的范围。任何本领域的技术人员,在不脱离本发明的构思和原则的前提下所作出的等同变化与修改,均应属于本发明保护的范围。