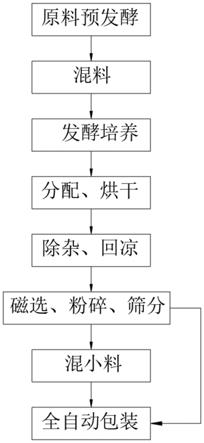
1.本专利申请涉及生物饲料发酵生产技术领域,特别是涉及一种生物饲料生产线。
背景技术:2.随着人民对健康食品的要求越来越高,农业农村部第194号和246号公告,自2020年1月1日起,停止生产、进口促生长类药物饲料添加剂(中药类除外);自2020年7月1日起,停止生产含有促生长类药物饲料添加剂(中药类除外)的商品饲料;废止相关品种标准,注销相关产品批准文号,指导各地全面推进药物饲料添加剂退出工作。这给生物饲料、有机酸、抗菌精油等替代产品带来很大需求。随着人民生活水平提高,肉蛋奶等蛋白营养的需求不断增加,畜牧养殖业得到很大发展,但我国饲用豆粕、玉米资源也逐渐出现短缺,大量依赖进口,农业农村部2021年4月21日发布《猪鸡饲料玉米豆粕减量替代技术方案》,要求使用非玉米豆粕日粮替代玉米豆粕日粮,但非玉米豆粕日粮替往往存在大量非淀粉多糖、胰蛋白酶抑制因子、植酸等抗营养因子,生物发酵饲料是解决此类抗营养因子,提高饲料原料消化吸收率的最佳技术方案。
3.常规生物饲料生产线一般为槽式发酵饲料生产线、圆盘发酵饲料生产线、货箱发酵饲料生产线等,一般分为配料、进料、发酵、出料、干燥、粉碎、包装等工序。现有技术存在以下不足:
4.1、批次化作业:现有生物饲料生产线多为批次生产,或有多个批次单元序列串联为连续生产线,均不不是连续化生产,设备启停频率高,废气排放时断时续,不利于智能化和清洁化生产。如利用萨拉丁箱结构的圆盘发酵机组成的发酵工段,需要按批次配料、进料、发酵、出料,发酵生产安排批次化,进料、出料时不通风,发酵时,通风又随着发酵越来越快,产热越来越多,需要不断调整风机频率;
5.2、依赖人工操作:现有生物饲料生产线一般能够实现机械化作业,但少有配备智能机器人,无法做到智能化生产,如一般生物饲料包装工段,基本没有配备机器人包装、码垛、拆垛、装车等智能化设备,依赖人工操作;
6.3、环境友好度低:常规生物饲料生产线废气因为周期性排放,不利于收集,而峰值排放,处理费用高,所以多采用无组织排放措施,如常规的池式、货箱式发酵,包装工段输送设备和缓冲仓呼吸口,没有配置废气集中收集、集中处理设备,环境卫生差,特别发酵异味和工业粉尘影响工人和周围居民。
7.白酒糟为酿酒工业固体废渣,以稻壳和粮食残渣为主,新鲜白酒糟水分含量60-66%,ph3.5-4.0,酸度大,略有粘性,通透性好,流动性差,容重0.5t/m3左右,为此,我们以白酒糟为原料提出一种生物饲料生产线。
技术实现要素:8.鉴于以上所述现有技术的缺点,本专利申请的目的在于提供一种生物饲料生产线,解决上述现有技术的问题。
9.为实现上述目的,本发明提供如下技术方案:
10.一种生物饲料生产线,具体包括如下步骤:
11.s1、原料预发酵:将白酒糟收集放置在收料池中,抓取后码垛存放,通过自然堆放预发酵排除白酒糟中的自由水分,再经输送板链运输进行混料发酵;
12.s2、混料:将辅料、菌种和步骤s1中的原料按照质量比为(5-10)%:(15-50)%:(40-80)%的比例依次投放入至连续式混合机内,进行混合均匀;
13.s3、发酵培养:将步骤s2中混合的物料运输至发酵箱内发酵,发酵温度为28-32℃,发酵周期为8-16h,通风量为60-180m3/(方物料*小时);
14.s4、分配、烘干:发酵培养后的物料,将0-50%物料返回至发酵前端,作为菌种被送入步骤s2中的连续式混合机内,将50-100%物料定量分配至烘干设备中进行烘干;
15.s5、除杂、回凉:将步骤s4中烘干的物料运输至第二筛分机中进行筛分除杂,同时,对物料进行降温回凉至室温后储存;
16.s6、磁选、粉碎、筛分:将步骤s5中储存的物料经自动除铁器除铁后进入粉碎机中进行粉碎,粉碎后经第三筛分机筛分后进入筛后缓存仓;
17.s7、全自动包装:使用全自动包装机对步骤s6中得到的物料进行封装入库码垛。
18.进一步的,所述步骤s6筛分后的物料还包括有与小料进行混合,将筛后缓存仓内的物料运输至混合机内,投放入小料,小料添加占比为0.2-2%,混合均匀。
19.进一步的,所述步骤s1存放后的白酒糟的水分含量为60-62%,容重为0.48-0.52t/m3;存放完成后由数量不少于一台的车间行吊抓斗抓取分别投入到相应的投料斗内,然后由投料斗下方的自动喂料机定量输出白酒糟至发酵输送板链上,预发酵后的白酒糟经除杂后进入步骤s2混料;
20.所述除杂包括白酒糟经发酵输送板链运输至第一筛分机,除去白酒糟中体积较大的杂物,筛出物落至相应的杂料灰斗车内,白酒糟由链板输送机送出,输送到皮带计量秤上,经称量后输送至原料混前皮带机上,后输送至带式自动除铁器处,吸出白酒糟中的废铁杂质,杂质由相应的杂质灰斗车自动收集,白酒糟继续由原料混前皮带机输送至双向板链输送机上,由双向板链输送机将白酒糟运送至连续式混合机内与辅料、菌种混合。
21.进一步的,所述步骤s2中的辅料是由麸皮、轻质碳酸钙、非蛋白氮按照质量比为(85-95)%:(4-10)%:(2-8)%的比例混合而成,非蛋白氮选自尿素或硫酸铵中的一种;
22.步骤s2中混合后的物料进入一号柔性分配仓,将物料定量分配给两条发酵线,每条发酵线上的配比率在0-100%范围内可调。
23.进一步的,所述步骤s3中单条发酵线上采用两台发酵箱串联使用,发酵产生的废气经水洗除味,控制臭气排放浓度低于1000无量纲,厂界周边臭气浓度低于20无量纲。
24.进一步的,所述步骤s4中发酵培养后的物料通过二号柔性分配仓,将50-100%物料定量分配给数量不少于一条的烘干线,同时,0-50%物料返回连续式混合机,作为菌种,每条烘干线上的配比率在0-100%范围内可调,烘干设备包括烘干机、热风炉和火道,烘干后使物料水分含量低于13%,物料容重为0.21-0.25t/m3,烘干过程中产生的废气通过旋风除尘、热交换器、水洗/水膜除尘,处理后的烘干废气排放颗粒物不大于30mg/m3,同时使用低氮燃烧器,控制氮氧化合物不大于180mg/m3,热气通过余热回收设备给发酵和烘干新风加热。
25.进一步的,所述步骤s5中烘干的物料以及旋风收集的物料分别由烘干机出料输送线送至对应的二次筛分机内进行二次筛分,筛分烘干时结团的块状物和较小杂物,筛出物分别落入到相应的杂料灰斗车内,二次筛分机筛下物经过螺旋输送机送到筛分出料刮板,筛分出料刮板将对应二次筛分的物料,分别进行筛分汇总、串线输送,筛分汇总后的物料经提升进入主料仓,设置两个主料仓,筛分汇总后的物料根据需要输入任意一主料仓;单个主料仓容积大于等于250m3,单个主料仓能够储存12个小时的物料,出仓时不结拱,不卡料;筛分汇总后的物料,不需要进入主料仓的,由粉碎物料提升机送至串线输送机,输入粉碎机中粉碎。
26.进一步的,所述步骤s6中,磁选、粉碎、筛分过程中包括不少于一组的过渡仓,每组过渡仓的出料端均设置有一自动除铁器,经除铁后的物料进入粉碎缓存仓,粉碎缓存仓出料后经锤片式粉碎机粉碎,粉碎过程,监测采集运行时间、轴承温度、电机电流,粉碎机筛片孔径1.2mm,产能≥4吨/h/台,粉碎后容重0.54t/m3,粉碎后进入粉碎收集室内,粉碎收集室物料经出料螺旋输送至第三筛分机,筛分后的物料进入筛后缓存仓内存储。
27.进一步的,所述混小料包括按照比例从小料仓下方的计量斗计量出小料,筛后缓存仓内的物料经混料计量斗计量后,依次进入混合机内进行混合;
28.小料选自蒙脱石、磷酸氢钙、氯化钠、维生素中的至少一种。
29.进一步的,所述步骤s2的混料区、步骤s4的分配烘干区、步骤s5的除杂回凉区、步骤s6的磁选粉碎筛分区、混小料区、步骤s7的全自动包装区均通过除尘管道与除尘器连接,通过滤筒除尘,控制粉尘≤30mg/m3;
30.所述步骤s1-s7中所使用的机械设备分别装配有plc控制系统,通过光纤实时将运行参数回传到中控室内的智能控制电脑上,对工艺参数、设备运维、实时能耗采集数据控制,实时核算分析。
31.与现有技术相比,本发明的有益效果是:
32.1、两次连续配料工艺:本发明使用自动喂料机、皮带计量秤、连续式混合机实现了发酵前物料的连续配料;本发明使用筛后缓存仓、小料仓、计量斗、批次混合机实现了包装前的小料连续添加,两次连续配料工艺确保了生产线的连续性;
33.2、串线输送工艺:本发明使用配料后一号柔性分配仓、发酵后二号柔性分配仓、烘干后筛分汇总输送串线输送、粉碎转运串线输送,多条串线输送搭配使用增加了整条生产线的容错率,即使个别设备发生故障,不影响生产线的连续运转;
34.3、三次筛分、两次除铁工艺:本发明使用配料前一次筛分机筛出湿料大杂,干燥后二次筛分机筛出干料小杂,粉碎后三次筛分筛出粒度不合格产品;本发明使用配料前一次带式自动除铁器清除原料中铁质杂物,粉碎前二次自动除铁器清除生产线可能脱落铁质杂物;多重除杂设备搭配使用,避免因杂质破坏导致生产线故障停机,有效的保证了生产的连续性;
35.4、生产工序流水线设计:本发明将投料、配料(含菌种回加)、发酵、干燥、粉碎、包装、码垛、拆垛、装车各个工序合理整合,设计出一条流水线式生产线,每台设备均稳定运行,没有间断性开关机,也没有波峰波谷等复杂操作,有效保证生产线长期稳定运行,这种合理的生产工序流水线设计,设备工况变化少,利于智能化设计,废气排放稳定,没有峰值排放,利于清洁化生产;
36.5、智能化设备配置:本发明在配料工段、发酵工段、烘干工段、粉碎包装工段、出入库工段分别配有plc控制系统,通过光纤实时将设备运行参数回传到中控室,中控室配有智能控制电脑(配有备用电源),可以实现远程智能控制;通过大量使用自动化装备,如全自动包装机、机器人码垛机、机器人拆垛装车系统,可以实现无人值守级智能化生产。同时本发明在重要设备配有视频监视、在线温度感应器、雷达感应器、跑偏报警等数字仪表,可以实现自动纠正、报警等功能,最终实现黑灯工厂;
37.6、废气集中收集、集中处理设备配置:本发明配置除尘器,除尘器上的除尘管道连接到产生粉尘的各个区域,除尘管道将粉尘集中收集,通过滤筒除尘,控制粉尘≤30mg/m3;本发明在发酵区配置废气收集管网,将发酵废气集中收集,通过水洗塔吸附,控制臭气浓度≤1000无量纲;本发明在干燥区配置废气处理设备,将干燥废气通过旋风除尘器,水膜除尘器,控制控制粉尘≤30mg/m3,同时使用低氮燃烧器,控制no
x
≤180mg/m3,做到了废气的全程集中收集、集中处理,实现了清洁化生产。
附图说明
38.图1为本发明生产线流程示意图;
39.图2为本发明混料工段流程示意图;
40.图3为本发明发酵培养流程示意图;
41.图4为本发明发酵废气处理流程示意图;
42.图5为本发明烘干工段流程示意图;
43.图6为本发明粉碎工段流程示意图;
44.图7为本发明混小料工段流程示意图;
45.图8为本发明包装存放工段流程示意图;
46.图9为本发明成品出库装车流程示意图。
具体实施方式
47.以下通过特定的具体实例说明本专利申请的实施方式,本领域技术人员可由本说明书所揭露的内容轻易地了解本专利申请的其他优点与功效。本专利申请还可以通过另外不同的具体实施方式加以实施或应用,本说明书中的各项细节也可以基于不同观点与应用,在没有背离本专利申请的精神下进行各种修饰或改变。需说明的是,在不冲突的情况下,本技术中的实施例及实施例中的特征可以相互组合。
48.请参阅图1-9,本发明提供如下技术方案:
49.鉴于现有白酒糟为酿酒工业固体废渣,以稻壳和粮食残渣为主,新鲜白酒糟水分含量60-66%,容重0.5t/m3左右,现以白酒糟为原料进行饲料生产,具体如下:
50.一种生物饲料生产线,如图1所示,具体包括如下步骤:
51.s1、原料预发酵:将白酒糟收集放置在收料池中,抓取后码垛存放,通过自然堆放预发酵排除白酒糟中的自由水分,存放后的白酒糟的水分含量为60-62%,容重为0.48-0.52t/m3;存放完成后由数量不少于一台的车间行吊抓斗抓取分别投入到相应的投料斗内,然后由投料斗下方的自动喂料机定量输出白酒糟至发酵输送板链上,预发酵后的白酒糟经除杂后进入下一步;
52.除杂包括白酒糟经发酵输送板链运输至第一筛分机,除去白酒糟中体积较大的杂物,筛出物落至相应的杂料灰斗车内,白酒糟由链板输送机送出,输送到皮带计量秤上,经称量后输送至原料混前皮带机上,后输送至带式自动除铁器处,吸出白酒糟中的废铁杂质,杂质由相应的杂质灰斗车自动收集,白酒糟继续由原料混前皮带机输送至双向板链输送机上,由双向板链输送机将白酒糟运送至连续式混合机内与辅料、菌种混合。
53.s2、混料:将辅料、菌种和步骤s1中的原料按照质量比为(5-10)%:(15-50)%:(40-80)%的比例依次投放入至连续式混合机内,进行混合均匀,辅料是由麸皮、轻质碳酸钙、非蛋白氮按照质量比为(85-95)%:(4-10)%:(2-8)%的比例混合而成,非蛋白氮选自尿素或硫酸铵中的一种;混合后的物料进入一号柔性分配仓,将物料定量分配给两条发酵线,每条发酵线上的配比率在0-100%范围内可调;
54.s3、发酵培养:将步骤s2中混合的物料运输至发酵箱内发酵,单条发酵线上采用两台发酵箱串联使用,发酵温度为28-32℃,发酵周期为8-16h,通风量为60-180m3/(方物料*小时);通过自动调控通风量和通风温度,结合翻料,翻料6次,控制发酵条件,使微生物快速生长并发酵底物,实时采集物料温度,取样监测酵母生长和ph值变化情况,进出口物料水分变化情况;发酵外排气体呈饱和湿空气状态,含有机酸,呈酸性,发酵产生的废气经水洗除味后排出,排气量控制与通风量一致,控制臭气排放浓度低于1000无量纲,厂界周边臭气浓度低于20无量纲;
55.s4、分配、烘干:发酵培养后的物料通过二号柔性分配仓,将50-100%物料定量分配给数量不少于一条的烘干线,同时,0-50%物料返回连续式混合机,作为菌种,每条烘干线上的配比率在0-100%范围内可调,烘干设备包括烘干机、热风炉和火道,烘干后使物料水分含量低于13%,物料容重为0.21-0.25t/m3,烘干过程中产生的废气通过旋风除尘、热交换器、水洗/水膜除尘,处理后的烘干废气排放颗粒物不大于30mg/m3,同时使用低氮燃烧器,控制氮氧化合物不大于180mg/m3,热气通过余热回收设备给发酵和烘干新风加热。
56.s5、除杂、回凉:将步骤s4中,烘干的物料以及旋风收集的物料分别由烘干机出料输送线送至对应的二次筛分机内进行二次筛分,筛分烘干时结团的块状物和较小杂物,筛出物分别落入到相应的杂料灰斗车内,二次筛分机筛下物经过螺旋输送机送到筛分出料刮板,筛分出料刮板将对应二次筛分的物料,分别进行筛分汇总、串线输送,筛分汇总后的物料经提升进入主料仓,设置两个主料仓,筛分汇总后的物料根据需要输入任意一主料仓;单个主料仓容积大于等于250m3,单个主料仓能够储存12个小时的物料,出仓时不结拱,不卡料;筛分汇总后的物料,不需要进入主料仓的,由粉碎物料提升机送至串线输送机,输入粉碎机中粉碎;同时,对物料进行降温回凉至室温后储存;
57.s6、磁选、粉碎、筛分:将步骤s5中储存的物料经自动除铁器除铁后进入粉碎机中进行粉碎,粉碎后经第三筛分机筛分后进入暂存仓;
58.物料除杂回凉后进入过渡仓,过渡仓数量不少于一组,具体的为四组,其中三组正常使用,另一组备用,每组过渡仓的出料端均设置有一自动除铁器,经除铁后的物料进入粉碎缓存仓,粉碎缓存仓出料后经锤片式粉碎机粉碎,粉碎过程,监测采集运行时间、轴承温度、电机电流,粉碎机筛片孔径1.2mm,产能≥4吨/h/台,粉碎后容重0.54t/m3,粉碎后进入粉碎收集室内,粉碎收集室物料经出料螺旋输送至第三筛分机,筛分后的物料进入筛后缓存仓内存储;
59.s7、全自动包装:使用全自动包装机对步骤s6中得到的物料进行封装入库码垛。
60.步骤s6筛分后的物料还可以包括有与小料进行混合,用于制备适用于不同动物的饲料,将筛后缓存仓内的物料运输至混合机内,投放入小料,小料添加占比为0.2-2%;小料选自蒙脱石、磷酸氢钙、氯化钠、维生素中的至少一种,按照比例从小料仓下方的计量斗计量出小料,筛后缓存仓内的物料经混料计量斗计量后,依次进入混合机内进行混合均匀。
61.步骤s2的混料区、步骤s4的分配烘干区、步骤s5的除杂回凉区、步骤s6的磁选粉碎筛分区、混小料区、步骤s7的全自动包装区均通过除尘管道与除尘器连接,通过滤筒除尘,控制粉尘≤30mg/m3;步骤s1-s7中所使用的机械设备分别装配有plc控制系统,通过光纤实时将运行参数回传到中控室内的智能控制电脑上,对工艺参数、设备运维、实时能耗采集数据控制,实时核算分析,实现远程智能控制,在混料、发酵、烘干、磁选粉碎、混小料、全自动包装这些阶段上的设备配备视频监视、在线温度感应器、雷达感应器、跑偏报警等数字仪表,可以实现自动纠正、报警等功能,最终实现黑灯工厂。
62.实施例
63.为体现本发明的生产体系,做出如下生产流水线,具体包括混料工段、发酵工段、烘干工段、粉碎工段、混小料工段、包装存放工段。
64.混料工段如图2所示,包括原料接收与预发酵、投料和输送、除杂、辅料添加、混料。
65.一、原料接收与预发酵:白酒糟通过自卸车运输到预发酵车间,卸入收料池,由2台车间行车抓斗分别抓取到车间中部码垛存放;通过自然堆放发酵排出白酒糟中的自由水分;
66.二、投料和输送:1、白酒糟存放完成后(以水分小于62%为标准,容重0.5t/m3左右),由两台车间行吊抓斗中任一台抓取,后投入到相应的投料斗内;2、后由投料斗下方的自动喂料机,定量输出原料17t/h至发酵输送板链上;3、发酵输送板链将原料输送至第一筛分机处,发酵输送板链输出流量为17t/h;
67.三、除杂:1、第一筛分机除去原料中的石块、手套、塑料瓶、塑料袋等体积较大的杂物,筛下物由链板输送机送出,输送到皮带计量秤上;筛出物落到相应的杂料灰斗车;2、原料经皮带计量秤后,被输送至原料混前皮带机上,带式自动除铁器安装在原料混前皮带机上方,物料被送至带式自动除铁器处,带式自动除铁器吸出原料中的废铁杂质,杂质由相应的杂料灰斗车自动收集。原料则由原料混前皮带机继续输送至双向板链输送机上,然后运输至连续式混合机内,第一筛分机、链板输送机、皮带计量秤、原料混前皮带机、双向板链输送机的输送流量均为17t/h;
68.四、辅料添加:人工解袋,将辅料落入辅料缓存仓,辅料提升机(30m3/h)将辅料缓存仓内的辅料送入辅料分仓螺旋输送机,后被辅料分仓螺旋输送机分别送入1#(20m3)、2#(20m3)、3#(20m3)辅料仓,然后经辅料仓星型下料器和辅料仓流量秤一起流向辅料汇总输送螺旋机,经提升斗将辅料输送至连续式混合机内,提升斗的流量为5t/h,辅料添加的过程中在产生粉尘的进出料口处设置除尘管道与除尘器连接;
69.五、混料:将白酒糟、辅料以及菌种同步投入至连续式混合机内,按照比例混合均匀,菌种为经过发酵后的物料,由双向板链输送机送至连续式混合机内,实现连续式混合,连续式混合机的额定处理量为34t/h。
70.发酵工段如图3和图4所示,包括发酵培养和发酵废气处理。
71.一、发酵培养:如图3所示,包含两条连续发酵线,分别对物料进行发酵作业,发酵温度30℃,发酵周期12h,通风量小于180m3/(方物料*小时),翻料6次。每条发酵线装载物料合计(8.5t新糟+8.5t回糟)
×
12=204t,每条发酵线采用2台发酵箱串联使用,单台发酵箱三层链板装载酒糟102t;具体的,选择其中一路发酵线,从一号柔性分配仓途经发酵箱板链上料线和发酵箱星型下料器进入一号发酵箱内发酵,发酵后出料依次经发酵箱星型下料器、发酵箱中转提升板链上料线、发酵箱星型下料器进入二号发酵箱再次发酵,发酵后出料依次经发酵箱星型下料器、发酵箱中转输送至二号柔性分配仓,每条发酵线上设备的流量均为17t/h,新风或余热回收热风通过管道三通通入发酵鼓风机,发酵鼓风机启动对发酵箱内通风,且保温,通风量为120m3/(方物料*小时),发酵温度为30℃,单线发酵过程中进行翻料6次,二号柔性分配仓将50%的物料经回料衔接输送机和双向板链输送机输送至连续式混合机内,作为菌种;两条发酵线是并联,均是连续运行,单条发酵线日处理酒糟200t,当某一发酵线发生故障时,通过一号柔性分配仓保存一半的产能,避免因单个故障出现全线停产的局面;二、发酵废气处理:如图4所示,发酵过程中产生的废气经发酵水洗塔水洗除味,产生的废水排向污水站集中处理,除味后的气体经发酵水洗引风机排出。
72.烘干工段如图5所示,包括烘干、烘干废气处理、除杂和回凉。
73.一、烘干:二号柔性分配仓将50%物料定量分配给两条烘干线,每条烘干线的配比率可以调整,调整范围为0-100%,每条烘干线包括物料从二号柔性分配仓出料运输的烘干机进料输送线,烘干机进料输送线将物料输送至烘干机设备内进行烘干,单线烘干处理量为8.5t/h,烘干机设备包括依次顺序连接的烘干机、热风炉和火道,烘干后使物料水分含量低于13%,物料容重为0.23t/m3;
74.二、烘干废气处理:烘干过程中产生的废气通过旋风除尘、热交换器、水洗/水膜除尘,处理后的烘干废气排放颗粒物不大于30mg/m3,同时使用低氮燃烧器,控制氮氧化合物不大于180mg/m3,热气通过余热回收设备给发酵和烘干新风加热;
75.三、除杂和回凉:烘干的物料以及旋风收集的物料分别由烘干机出料输送线送至对应的二次筛分机内进行二次筛分,筛分烘干时结团的块状物和较小杂物,筛出物分别落入到相应的杂料灰斗车内,二次筛分机筛下物经过螺旋输送机送到筛分出料刮板,筛分出料刮板将对应二次筛分的物料,分别进行筛分汇总输送线(串线输送),烘干机设备之后的设备的进出料口均设置除尘管道,用于除尘。
76.粉碎工段如图6所示,筛分汇总输送线的物料进入粉碎物料提升机或主料仓物料提升机,经主料仓物料提升机的物料经主料仓串线输送机输送至主料仓内,主料仓包括两个,每个主料仓的出料口均设置主料仓出料螺旋机进入同一主料仓汇总刮板机,主料仓汇总刮板机将物料输送至粉碎物料提升机,粉碎物料提升机将物料经粉碎转运东西向串线输送机、粉碎转运南北向串线输送机分别输送至三个过渡仓内,留有一个过渡仓备用,每组过渡仓的出料端均设置有一自动除铁器,经除铁后的物料进入粉碎缓存仓,粉碎缓存仓出料后经锤片式粉碎机粉碎,粉碎过程,监测采集运行时间、轴承温度、电机电流,粉碎机筛片孔径1.2mm,产能≥4吨/h/台,粉碎后容重0.54t/m3,粉碎后进入粉碎收集室内,粉碎收集室物料依次经出料螺旋机、汇总刮板、出料提升机输送至第三筛分机,筛分后的物料进入筛后缓存仓内存储,不合格物料被输送至粉碎转运东西向串线输送机、粉碎转运南北向串线输送机重新进入过渡仓内,进行二次粉碎;粉碎工段设备的进出料口均设置除尘管道,用于除
尘。
77.混小料工段如图7所示,筛后缓存仓内的物料经筛后缓存仓出料机出料,经混料计量斗称重0.99t进入1t/次的混合机内,小料经小料人工吨袋拆包机或人工投料站拆袋存储,小料人工吨袋拆包机中的小料经小料斗提输送机和小料中转输送机输送至小料缓存仓内,人工投料站的出口直接连接小料缓存仓,小料缓存仓中小料经小料仓出料机出料运输至小料计量斗,小料计量斗称重0.01t的小料进入1t/次的混合机,二者混合,混合完成后进入混后缓存仓,依次经混后出料提升机、包装暂存仓刮板机进入包装暂存仓,其中,当筛后缓存仓内物料无需添加小料时,直接进入包装暂存仓;小料仓出料机的出口处还设置有备用小料计量斗,用于在小料计量斗出现问题后切换进小料,混小料工段各设备均通过除尘管道连接除尘器,除尘器内过滤的物料输送至尾料输送机。
78.包装存放工段如图8所示,混后缓存仓内的物料依次经混后出料提升机和包装暂存仓刮板机进入包装暂存仓内,包装暂存仓内的物料经全自动包装设备打包后输送至成品库,全自动包装设备的数量为两组,单组全自动包装设备的包装速度不小于200包/小时,包装规格为40kg/袋,每组全自动包装设备包括依次连接流水线作业的粉体全自动包装机、自动缝包机、立袋输送机、倒袋输送机和汇总输送机,粉体全自动包装机连接包装暂存仓的出料口,成品库内设置有码垛设备,码垛设备包括依次连接流水线作业的整形输送机、待码输送机、码垛机器人、码垛辊道输送机、缓存辊道输送机和输出输送机,托盘库输出托盘至码垛辊道输送机,整形输送机通过跨车间输送线与汇总输送机连接,输出输送机输送成品入库。
79.袋装物料向外运输时,如图9所示,成品库内的袋装物料经自动拆垛后进入装车棚自动装车,自动拆垛包括依次连接流水线作业的链条输送机、出库输送机、自动拆垛机、垛盘收集器,自动装车包括依次连接流水线作业的装车中转输送机、连续提升机、装车高速输送机、自动装车机,自动拆垛机将袋装成品运输至装车中转输送机。
80.本发明实现生物饲料的连续化生产,设备没有停机时间,设备利用率高,设备工况简单,废气排放速率低,没有峰值排放,解决了常规生物饲料生产设备投资大,工况复杂,难于程序化,废气峰值排放高,处理成本高等问题。
81.本发明通过大量使用智能化装备,模块化配置plc系统,智能化中控系统,重点设备配置视频、数字仪表等监视系统,解决了常规生物饲料生产依赖人工的问题。通过将人工经验数据化、智能化实现了无人值守级黑灯工厂。
82.本发明通过全程废气集中收集、集中处理装置,做到了全程有组织排放,解决了常规生物饲料生产,无组织排放废气的问题,实现了清洁化生产,打造了环境友好度高的生产线。
83.上述实施例仅例示性说明本专利申请的原理及其功效,而非用于限制本专利申请。任何熟悉此技术的人士皆可在不违背本专利申请的精神及范畴下,对上述实施例进行修饰或改变。因此,举凡所属技术领域中具有通常知识者在未脱离本专利申请所揭示的精神与技术思想下所完成的一切等效修饰或改变,仍应由本专利申请的权利要求所涵盖。