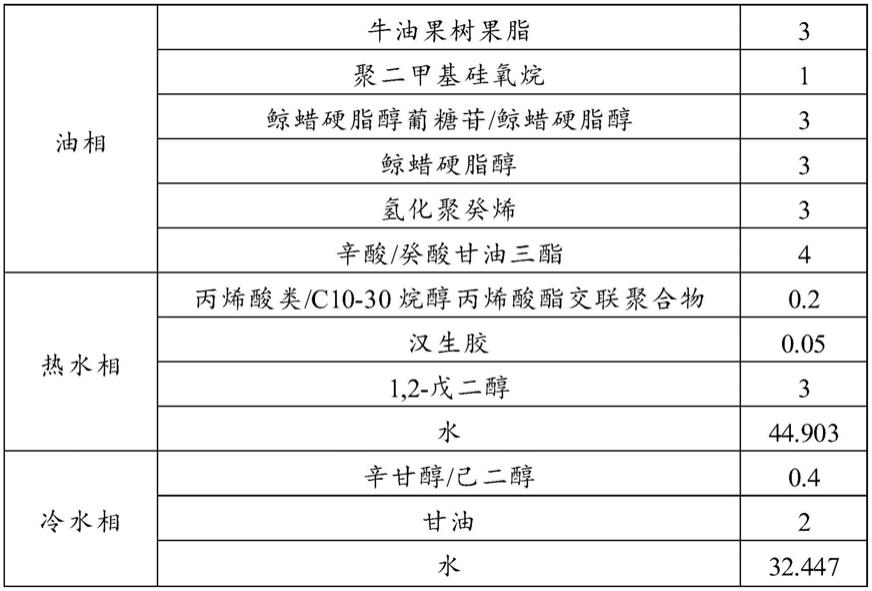
1.本发明涉及化妆品制备技术领域,尤其涉及一种降低化妆品乳化产品粒径的工艺。
背景技术:2.随着经济快速发展,人们对于美的追求日趋增加,我国化妆品的市场份额快速增长。与此同时,人们的环保意识不断增强,绿色环保化妆品表现出强劲的发展趋势。原料的绿色天然,包装的可持续,都是“绿色”概念的体现,除此之外,在产品的制造过程中,也应实行节能、降耗、减排、增效的清洁生产方式,以促进资源节约型、环境友好型社会的发展。
3.低能乳化工艺(lee)是t.j.lin(林
·
约瑟夫)提出的一种乳化技术,与传统的将油相、水相全部加热的生产方式不同,lee选择将热能和机械能有针对性地应用到乳化过程中,大幅度降低了能量的消耗。有文献报道,如果合理使用低能乳化技术,可降低能量消耗50%以上、产量增加100%,且不降低产品的质量。
4.低能乳化法将水相分为两部分,乳化过程中只对部分水相和油相进行加热乳化,且将部分水相以缓慢的速度加入油相,利用相转变的原理制成浓缩乳液,然后用剩余水相进行冷却稀释,最终得到乳液。此乳化过程并未均质,节约了相当大的热能和机械能;且没有用冷却水回流冷却,节约了水资源,有效减轻了废水处理的负担。
5.虽然上述乳化生产方式具有一定的节能效果,但在实际的工业生产过程中,由于未采用均质的方式,水相的添加速度十分缓慢,因此将会增加额外的时间成本和设备成本。
技术实现要素:6.本发明解决的技术问题在于提供一种降低化妆品乳化产品粒径的工艺,该工艺在降低化妆品粒径的同时还具有节能减排,降低时间成本的优点。
7.有鉴于此,本技术提供了一种降低化妆品乳化产品粒径的工艺,包括以下步骤:
8.将油相原料和热水相原料分别加热,将加热后的油相原料加入至加热后的热水相原料中,将得到的混合物进行均质,得到浓缩乳液;
9.将冷水相原料和所述浓缩乳液混合。
10.优选的,所述热水相原料和所述冷水相原料的质量比≥60:40。
11.优选的,所述热水相原料和所述冷水相原料的质量比为60:40。
12.优选的,所述加热的温度为70~90℃。
13.优选的,所述均质的时间为8~10min。
14.优选的,所述化妆品膏霜的粒径为700~750nm,pdi为0.100~0.150。
15.优选的,所述化妆品膏霜的粘度为200000mpa
·
s~250000mpa
·
s。
16.优选的,所述化妆品膏霜得到的时间为120~140min。
17.本技术提供了一种降低化妆品乳化产品粒径的工艺,其首先将油相原料和热水相原料分别加热,将加热后的油相原料加入至加热后的热水相原料中,均质后得到浓缩乳液;
然后将冷水相原料和浓缩乳液混合。本技术的水相采用热水相原料和冷水相原料分别加入的方法,且进行了均质处理,有利于减小化妆品乳化产品的粒径;进一步的,本技术将热能用于油相原料和热水相原料的加热,减少了热能的消耗,而冷水相原料用于浓缩乳液的稀释,加速了产品的冷却过程,降低了冷却过程中搅拌器的搅拌时间,减少了搅拌器消耗的机械能,缩短了化妆品乳化产品的制备时间,并且减少了冷却水的用量,节约水资源。
附图说明
18.图1为本发明降低化妆品乳化产品粒径的工艺简图;
19.图2为本发明利用利用不同比例的热水相:冷水相制备的膏霜在显微镜下的形态观察(400倍)(a:40%:60%,b:50%:50%,c:60%:40%,d:100%:0%);
20.图3为本发明不同工艺的膏霜粒径柱形图(a:传统工艺;b:节能工艺);
21.图4为本发明不同工艺面霜的主观评估结果图。
具体实施方式
22.为了进一步理解本发明,下面结合实施例对本发明优选实施方案进行描述,但是应当理解,这些描述只是为进一步说明本发明的特征和优点,而不是对本发明权利要求的限制。
23.鉴于现有技术中,化妆品乳化产品制备过程中能耗、品质不能同时兼顾的问题,本技术对化妆品原料的乳化过程进行了优化,工艺简图如图1所示,本技术提供的降低化妆品乳化产品粒径的工艺,在保证化妆品乳化产品质量的同时还能降低能耗。具体的,本发明实施例公开了一种降低化妆品乳化产品粒径的工艺,包括以下步骤:
24.将油相原料和热水相原料分别加热,将加热后的油相原料加入至加热后的热水相原料中,将得到的混合物进行均质,得到浓缩乳液;
25.将冷水相原料和所述浓缩乳液混合。
26.本技术提供的工艺适用于所有含有水相和油相的化妆品,例如霜类化妆品或乳液类化妆品,而不仅仅限于本技术实施例中具体配方的化妆品。在此情况下,本技术所述油相原料和水相原料为本领域技术人员熟知的化妆品中的油相和水相。
27.本技术提供的降低化妆品乳化产品粒径的工艺,具体是将水相分为了两部分,一部分作为热水相原料,一部分作为冷水相原料,本技术首先将油相原料和热水相原料分别加热,将加热后的油相原料加入至加热后的热水相原料中,再将得到的混合物进行均质,以得到浓缩乳液;在此过程中,所述加热的温度为70~90℃,在具体实施例中,所述加热的温度为80℃,以使油相充分熔化,为后期均质作准备。所述均质的技术方法为本领域技术人员熟知的技术方法,对其具体实施方法本技术不进行特别的限制;具体的,所述均质的时间为8~10min;更具体地,所述均质的时间为8min。
28.在得到浓缩乳液后,本技术则将冷水相原料与所述浓缩乳液混合。所述冷水相原料用于稀释且冷却降温所述浓缩乳液。在保证产品质量的同时降低能耗,所述热水相原料和所述冷水相原料的质量比根据不同的化妆品,可以为60:40,可以为40:60、可以为50:50,但是对于本技术实施例中的化妆品配方,所述热水相原料和所述冷水相原料的质量比≥60:40,更具体为60:40。
29.本技术提供的节能方法制备的化妆品膏霜的粒径为700~750nm,pdi为0.100~0.150,粘度为200000mpa
·
s~250000mpa
·
s,且所述化妆品乳化产品制备的时间为120~140min。因此,本技术提供的降低化妆品乳化产品粒径的工艺既能保证化妆品的质量,又能实现节能、环保的要求。
30.为了进一步理解本发明,下面结合实施例对本发明提供的降低化妆品乳化产品粒径的工艺进行详细说明,本发明的保护范围不受以下实施例的限制。
31.实施例
32.1实验部分
33.1.1实验材料
34.牛油果树果脂,浦恩;聚二甲基硅氧烷,奥凯;氢化聚癸烯,百好博;辛酸癸酸甘油三酯,basf;鲸蜡硬脂醇,basf;汉生胶,汉高;1,2-戊二醇,奥雪;鲸蜡硬脂醇葡糖苷/鲸蜡硬脂醇;丙烯酸类/c10-30烷醇丙烯酸酯交联聚合物;甘油;馨二醇68,德之馨;所用材料均为化妆品级;
35.1.2实验仪器
36.均质机,马尔文粒度仪,旋转粘度计,光学显微镜;
37.1.3实验方法
38.1.3.1利用优化的节能工艺制备膏霜
39.按照表1称取各项组分,将油相和热水相分别在80℃条件下加热,完全熔化后,将油相添加到热水相中,将混合物进行均质,形成浓缩乳液。均质完成后,将冷水相倒入浓缩乳液中进行稀释,搅拌均匀后,完成膏霜的制备。
40.表1 所选取o/w膏霜的配方组成数据表
[0041][0042]
[0043]
1.3.2节能工艺中热水相与冷水相比例的筛选
[0044]
为研究热水相与冷水相的比例对膏霜质量的影响情况,固定均质速度与均质时间,将热水相:冷水相的比例设置为40%:60%、50%:50%、60%:40%以及100%:0%,按“1.3.1”所述方法在实验室制备膏霜;以“能否制备出粒径均匀的膏霜”为筛选标准。
[0045]
1.3.3实验室工艺参数放大到生产
[0046]
将热水相:冷水相的比例设置为60%:40%,按照节能方法以工业化规模制备膏霜80kg,评价该工艺是否可以进行放大生产。以“膏霜的粒径大小、均一度”为标准。乳化产品的质量取决于最终用途和性能,本技术为了有一个统一的筛选标准,暂将乳化产品的质量定义为“粒径越细,质量越好”。
[0047]
1.3.4膏霜显微结构的观察
[0048]
取用参照样和对比样适量分别进行压片,采用显微镜观察乳化粒子微观结构,以图片形式直观呈现乳液内部结构信息,以此考察乳化粒子相对大小和粒径分布情况。
[0049]
1.3.5膏霜粒径的测量
[0050]
利用马尔文粒度仪对膏霜的粒径和pdi进行测定,测定前用纯水稀释。
[0051]
1.3.6膏霜粘度的测量
[0052]
膏霜制备完成的第二天,利用旋转粘度计对膏霜的粘度进行测定。,
[0053]
1.3.7膏霜的储存稳定性
[0054]
取等量的样品分别放置在25℃,40℃,-20℃,光照,冷热循环条件下保存,进行六个月的观察,检查是否出现分层、破乳等不稳定现象。
[0055]
1.3.8优化后工艺节省的时间/缩短制备时间
[0056]
对传统工艺、节能工艺制备同种膏霜的过程及其所花费的时间分别进行记录,计算节约的时间。
[0057]
1.3.9消费者喜好度测试
[0058]
参考astm乳霜产品感官评价词汇及标准结合产品使用时实际感受,建立了化妆品使用过程中的4种指标(见表2),指标体系包含评价阶段、指标名称、定义、打分范围。此项测试在恒温恒湿的感官评价实验室内进行(温度20~22℃,相对湿度50%~60%)。
[0059]
将样品按3位随机数字编码,筛选20名受试者进行半脸测试,用指腹挑起膏霜,感受膏体的挑起性、光泽度、细腻度,以1圈/s的速度涂抹于面部,感受铺展性及吸收的快慢;在涂抹结束后感受面霜的残留量,并对总体喜好度进行打分评价,统计平均分。
[0060]
1.3.10统计分析
[0061]
实验一式三份,结果以平均值
±
标准偏差表示。
[0062]
表2 本技术制备的膏霜评价指标数据表
[0063]
[0064][0065]
2结果
[0066]
2.1节能工艺中热水相与冷水相比例的筛选
[0067]
如图2所示,热水相含量为100%时,表示利用传统方式生产膏霜,将其作为对照,观察节能工艺制备的膏霜形态。和传统工艺制备的膏霜相比,利用40%的热水相制备膏霜时,粒径较大,且表面有油滴未发生乳化(白色箭头所示);当热水相的含量增加至60%时,粒径大小不再发生明显变化,且所有的油相和水相在乳化剂的作用下形成浓缩乳液,所以,本技术热水相的比例优选为60%。
[0068]
2.2不同工艺膏霜粒径的比较
[0069]
为了研究放大生产对由节能工艺制备的膏霜的质量影响,制备了80kg的膏霜,并以传统生产方式作为对照,对不同工艺膏霜的粒径进行测定,结果如图3所示:利用传统工艺生产的膏霜粒径为932.40
±
14.31nm,pdi为0.152
±
0.025;利用节能工艺生产的膏霜粒径为744.60
±
8.91nm,pdi为0.124
±
0.024。
[0070]
2.3不同工艺膏霜粘度的比较
[0071]
对传统工艺和节能工艺制备的膏霜分别在相同条件下进行粘度测试:利用传统工艺生产的膏霜粘度为144000mpa
·
s;利用节能工艺生产的膏霜粘度为214500mpa
·
s,节能工艺制备的膏霜粘度更大。
[0072]
2.4节能工艺制备的膏霜的稳定性
[0073]
在六个月的储存期中,各个条件均未发现分层、破乳等不稳定现象。
[0074]
2.5缩短生产时间,节约能源
[0075]
利用不同工艺分别制备80kg膏霜的生产过程及所用时间如表3所示。本技术将热能用于油相和60%水相的加热,减少了热能的消耗;剩余40%的常温水相用于浓缩乳液的稀释,加速了产品的冷却过程,降低了冷却过程中搅拌器的搅拌时间,减少了搅拌器消耗的机械能,缩短了27.27%的制备时间;并且减小冷却水的用量,节约水资源。
[0076]
表3 不同工艺的生产过程及时间数据表
[0077]
生产过程传统工艺消耗时间节能工艺消耗时间备料50min50min加热30min25min
均质10min10min冷却75min35min总耗时165min120min节约的时间 27.27%
[0078]
2.6消费者喜好度测试
[0079]
通过成对比较法,对两款不同工艺的面霜进行消费者喜好度测试,结果如图4所示。传统工艺生产的面霜挑起性更好,在涂抹过程中易于铺展;节能工艺生产的面霜粒径更小,光泽度和细腻度更好,更容易吸收,总体来说,在本次测试中,消费者更偏好于节能工艺生产的面霜。
[0080]
在上述内容中所述的传统工艺是指化妆品原料不区分热水相和冷水相,将全部的水相都用来加热,再和油相混合,均质后冷却水降温,即得到化妆品膏霜。节能工艺是指本技术所述的工艺方法。
[0081]
本技术提供的低能乳化工艺主要分为两个部分,首先将油相与热水相加热混合搅拌,形成浓缩乳液;其次用剩余未加热的水相进行冷却稀释。理论上,只要未加热的相足够大,就可以节约大量的能耗,但在实际生产过程中有一定的限度。本技术提供的低能乳化工艺不仅能够节约部分热能,缩短冷却时间,减少冷却水用量,还能制备出高质量的乳液。
[0082]
在上述过程中,本技术选取四个不同浓度的热水相制备膏霜,期望筛选出适合本体系的热水相比例,结果如图2所示。热水相为100%时,表示按照传统方式制备乳液;当热水相为40%时,乳液质地较稀,液珠尺寸大,且表面有油滴存在,可能归因于:(1)在理论上,40%水的比重高于油相,可以形成o/w的乳液,但由于增稠剂的存在,实际用于乳化的水少于40%,导致乳液表面存在少量油滴;(2)由于油滴的存在,体系未完全乳化,所以样品的质地较稀,且浓缩乳化体属于非牛顿型流体,由于剪应力正比于粘度和剪力的变化率,剪力的变化率不变,粘度降低导致剪应力减小,从而导致粒子尺寸较大;热水相含量增加至60%时,粒径降低,这是因为60%的水相足以和油相完全乳化,且在乳化过程中,利用和传统乳化工艺相同的均质速度和时间处理了更少的浓缩乳液,所以制备的膏霜粒径更小,更细腻,进而选择60%的热水相进行面霜的制备。
[0083]
随后,本技术利用节能工艺进行了80kg膏霜的放大生产,研究工业化生产对膏霜粒径的影响情况。以传统生产工艺作为对照,进行了粒径、粘度、储存稳定性、消费者喜好度的测试。由图3可知,节能工艺制备的膏霜粒径更小,pdi更低,说明膏霜的均匀度更好,外观更细腻光滑,更容易吸收,残留感更弱,所以多数消费者更偏好于节能工艺生产的面霜。粒度分析是衡量样品稳定性的重要指标,由图3可得,节能工艺制备的膏霜的pdi为0.124,说明其具有较长的货架期。
[0084]
样品粒径的减小导致料体厚度增加,流动性能下降,粘度增加;因此,本技术后续采用40%冷水相对浓缩乳液进行冷却稀释,缩短了冷却时间,同时也降低了冷却期间搅拌器的搅拌时间,一般来说,长时间的搅拌会降低乳液/膏霜的粘度,综上,节能工艺制备的膏霜粘度显著高于传统工艺制备的膏霜,增加了涂抹时膏体与皮肤的阻力。
[0085]
传统的乳化方式不仅从能源方面是浪费,而且从生产时间和效率方面更是浪费。本技术膏霜的制备过程和时间如表3所示。传统工艺制备膏霜需要2.75小时,30min用来加热,75min用来冷却;而采用节能工艺,节省了40min的冷却时间,缩短了27.27%的生产时
间,提高了生产效率;且节约了水资源,减轻了废水处理的负担,践行了绿色环保的清洁生产方式。在加热过程中,因只需加热60%水相,所以节约了部分热能;在后期的冷却过程中,也减少了搅拌所产生的机械能消耗,总的来说,节能工艺降低了碳排放,并改善了产品质量。
[0086]
综上,本技术采用了低能乳化工艺且对关键参数进行探究,并成功完成了从小试到工业化的放大生产。此工艺将热能和机械能更有针对性地应用到乳化过程,节约能源,缩短生产时间,提高了生产效率,体现了产品制造过程的绿色优势;而且只有60%的水参与乳化,相比于传统工艺,每单位重量的机械能增加;且浓缩乳液的粘度更大,剪应力增加,乳化作用增强,使得粒径更小,更容易吸收;肤感更细腻,光泽度更好,更受消费者青睐。
[0087]
以上实施例的说明只是用于帮助理解本发明的方法及其核心思想。应当指出,对于本技术领域的普通技术人员来说,在不脱离本发明原理的前提下,还可以对本发明进行若干改进和修饰,这些改进和修饰也落入本发明权利要求的保护范围内。
[0088]
对所公开的实施例的上述说明,使本领域专业技术人员能够实现或使用本发明。对这些实施例的多种修改对本领域的专业技术人员来说将是显而易见的,本文中所定义的一般原理可以在不脱离本发明的精神或范围的情况下,在其它实施例中实现。因此,本发明将不会被限制于本文所示的这些实施例,而是要符合与本文所公开的原理和新颖特点相一致的最宽的范围。