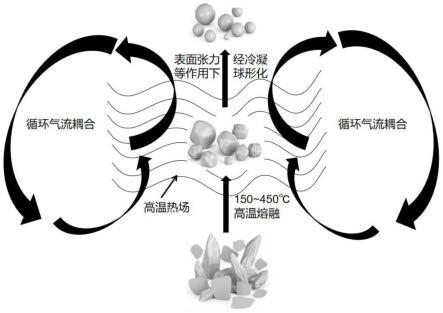
1.本发明涉及一种面向3d打印领域的生物可降解复合粉体的制备及其干法球化工艺。
背景技术:2.选择性激光烧结(sls)技术是一种基于粉体成型的3d打印技术,利用激光束使单层粉末熔融,并通过离散/堆积原理实现产品的层层烧结成型,与传统加工技术相比,sls加工技术的优势主要体现在自由成型和整体制造的特点,具有柔性度高、材料利用率高、成型速度快等,可用于生产具有任意复杂结构的制件,实现复杂制件的个性化定制生产。因此,sls技术在制备结构复杂,需定制化的再生组织器官方面得到广泛关注。
3.生物可降解粉体材料作为sls加工技术制备再生组织器官的基本原材料,不仅需要高球形度以保证良好的流动性和铺展性,还应具有合理的粒度及粒度分布以保证良好的成形质量。然而目前市场上没有适用于sls的生物可降解粉体材料,这主要是由于传统的粉体球形化工艺主要是湿法工艺,而生物可降解材料对湿度敏感,遇水后易降解,导致其性能急剧下降。此外,传统湿法工艺还可能有杂质混入、需消耗有机溶剂、产物不易分离,这可能会对正常组织器官产生不良影响。因此,开发一种环保高效、经济可靠、操作简单的生物可降解粉体材料制备工艺方法迫在眉睫。
技术实现要素:4.本发明的目的是针对现有技术的不足,而提供一种适用于sls技术制备再生组织器官的生物可降解复合粉体的制备及其干法球化工艺。本发明利用冷冻粉碎、真空干燥等工艺流程,获得均匀混合、合适粒径、形状不规则的复合粉体,再基于表面能最低原理进行球化处理,通过调控球化工艺参数和组分配比,克服球形率低、流动性差等关键技术难题,从而得到适用于sls技术制备组织器官再生的多元组分球形粉体,所得粉体球形率达到95%以上,流动性崩溃角小于33
°
。
5.本发明的一个目的是解决至少上述问题和/或缺陷,并提供至少后面将说明的优点。
6.为了实现根据本发明的这些目的和其它优点,提供了一种生物可降解复合粉体的制备及其干法球化工艺,包括以下步骤:
7.步骤a、将生物陶瓷和生物可降解高分子材料进行混合,获得复合粉体;
8.步骤b、采用冷冻粉碎机将复合粉体冷冻粉碎,真空干燥,过滤后获得均匀混合、粒径适宜、但形状不规则的二次复合粉体;
9.步骤c、将二次复合粉体匀速喂入高分子粉体球化机进行球化,球化至成球率达95%以上,然后冷却,得到多元组分复合球形粉体。
10.优选的是,所述步骤a中,生物陶瓷为羟基磷灰石、磷酸钙、二氧化硅、氧化钙、五氧化二磷、氧化铝、氮化硅、二氧化锆、半导体陶瓷、或硅酸盐中的至少一种,所述生物陶瓷的
粒径为1~300μm。
11.优选的是,所述生物可降解高分子材料为左旋聚乳酸、聚乳酸、聚乙二醇、聚氨酯,脂肪族聚酯、聚酯醚、聚膦腈、聚原酸酯、聚碳酸酯、聚酸酐、聚氨基酸、二氧化碳聚合物、聚丁二酸丁二醇酯、脂肪芳香聚酯、聚乙烯、丙烯酸树脂、聚己内酯、聚对苯二甲酸丙二醇酯、聚对二氧环己酮中的至少一种。
12.优选的是,所述步骤a中,以重量份计,生物陶瓷为10~1000份、生物可降解高分子材料为5~599份。
13.优选的是,所述步骤c中,球化的球化温度包括引风口温度和出料口温度;其中,引风口温度为150~450℃,在复合粉体变形温度以上10~50℃;出料口温度50~600℃,球化时间为2~30min;引风口温度的升温速率40~90℃/min;冷却的冷却速率40~90℃/min。
14.优选的是,步骤c中,球化的气流速度5~30m/s、颗粒停留时间5~60min、预热时间0.5~3h。
15.优选的是,步骤c中,将二次复合粉体匀速喂入高分子粉体球化机的喂料速率为1~20kg/h,冷却时间为0.5~3h。
16.优选的是,步骤b中,所述过滤的筛网目数为100~300目,粒径大小为50nm~200um;步骤c中,所述干燥温度40~90℃,干燥时间12~48h。
17.优选的是,所述冷冻粉碎机包括:
18.用于对物料进行存储、冷冻进行分级处理的进料单元;
19.用于将冷冻后的物料进行破碎处理的粉碎单元;
20.用于将粉碎后的物料颗粒从粉碎单元中分离出来的输出单元;
21.与进料单元、粉碎单元、输出单元相配合,以控制其工作状态的控制器;
22.其中,在进料单元的预处理仓、粉碎单元的粉碎仓,输出单元的出料仓上,分别设置有与液氮供给设备相连通的第一进料管、第二进料管、第三进料管;
23.所述第一进料管下方设置有与控制器通信连接的第一温度传感器;
24.所述粉碎仓与出料仓之间的第一连接管路上设置有第二温度传感器,所述出料仓在与第三进料管相配合的位置设置有流量控制阀。
25.本发明提供一种生物可降解复合粉体的制备及其干法球化工艺,基于表面能最低原理,利用高速射流技术,将不规则高分子粉体送入高温腔体,流经高温热场的粉末颗粒表面被瞬时加热熔化,并在表面张力、内聚力、重力等的共同作用下,驱使颗粒表面由高自由能的热力学非平衡态向平衡态转变,当颗粒收缩为球形时其表面各处受力平衡,达到能量最低的热力学稳定态,随后在降落过程中冷凝形成球形颗粒。通过调控多元组分质量配比、分子量大小、粒径分布等,实现满足再生组织器官的复合材料的制备。通过调控气流速度、温度场分布、颗粒停留时间、预热时间、以及冷却时间等工艺参数,实现高球形度、高流动性、表面光洁的生物可降解粉体材料的制备。
26.本发明至少包括以下有益效果:
27.其一,本发明针对单一材料难以满足再生组织器官对性能的需求,提出将生物陶瓷和可降解高分子进行复合获得多元组分材料,实现了材料间优势互补。
28.其二,本发明相比于传统湿法成球工艺,该法采用干法成球工艺技术,即在高速气流的作用下将不规则粉体颗粒引入高温球化腔,颗粒在高温加热条件下熔融收缩成球,整
个过程使用空气作为媒介,克服了传统湿法成球粉体遇水易降解关键性能问题。
29.其三,本发明通过调控球化温度、送料频率、气流速度、停留时间等,改变粉体材料组分配比、分子量大小、粒径分布等,实现球形度高、粒径可控、表面光洁的多元组分粉体制备,突破陶瓷-可降解高分子因流动困难而无法打印的技术瓶颈。
30.其四,本发明提出的干法成球工艺方法,操作简单,生产效率高,无有毒物质产生,清洁环保,为实现面向sls加工生物可降解粉体材料的批量化生产提供技术支撑。
31.本发明的其它优点、目标和特征将部分通过下面的说明体现,部分还将通过对本发明的研究和实践而为本领域的技术人员所理解。
附图说明:
32.图1为本发明干法成球原理图;
33.图2为本发明实施例2的原始粉末和球化处理后的粉末的sem图;
34.图3为本发明实施例2的原始粉末的休止角示意图;
35.图4为本发明实施例2的球化处理后的粉末的休止角示意图;
36.图5为本发明冷冻粉碎机的结构布局示意图;
37.图6为本发明粉碎组件的结构示意图;
38.图7为本发明粉碎组件的横截面示意图
39.图8为本发明的固定环的结构示意图;
40.图9为本发明内板的俯视结构示意图;
41.图10为本发明内板纵截面结构示意图。
具体实施方式:
42.下面结合附图对本发明做进一步的详细说明,以令本领域技术人员参照说明书文字能够据以实施。
43.应当理解,本文所使用的诸如“具有”、“包含”以及“包括”术语并不配出一个或多个其它元件或其组合的存在或添加。
44.一种应用生物可降解复合粉体的制备及其干法球化工艺,包括:
45.为满足sls加工的个性化需求,适应组织器官再生的性能需求,通过改变生物陶瓷材料和可降解高分子的组分配比、分子量、粒径大小等因素,调控引风口、出料口温度,气流速度、温度场分布、颗粒停留时间、进料频率、预热时间等工艺参数,将获得球形度高、流动性好、适宜粒径性能优异的多元组分球化粉体,实现了材料间性能互补,满足了sls技术制备组织器官再生的性能需求。
46.一种应用生物可降解复合粉体的制备及其干法球化工艺的反应原理,包括:
47.基于表面能最低原理,利用高速射流技术,将不规则高分子粉体送入高温腔体,流经高温热场的粉末颗粒表面被瞬时加热熔化,并在表面张力、内聚力、重力等的共同作用下,驱使颗粒表面由高自由能的热力学非平衡态向平衡态转变,当颗粒收缩为球形时其表面各处受力平衡,达到能量最低的热力学稳定态,随后在降落过程中冷凝形成球形颗粒,获得球形度高达95%以上、流动性崩溃角小于33
°
、力学性能稳定、表面光洁的性能优异多元复合球形粉体。
48.实施例1:
49.一种生物可降解复合粉体的制备及其干法球化工艺,包括:
50.将单一羟基磷灰石材料(分子量为1004.62,纯度99%,粒径20nm)进行粉体球化,先将其加入冷冻粉碎机粉碎,然后放置50℃真空干燥机中,进行36h真空干燥;再将干燥完成的多元组分粉体置入100目筛网以进行过滤,获得小于150um的粉体粒径;依次开启高分子粉体球化机的送风机、引风机、接着打开加热开关,再设定引风口温度282℃、出料口温度82℃、球化时间15min、气流速度10m/s、颗粒停留时间30min,以及送料速率6kg/h,随后开始升温,升温速率50℃/min;当引风口和出料口温度达到设定温度值后,继续对粉体球化机的球化室预热1h,当球化室的预热完成后,开始对进料斗进行喂料;设备正常运行后,应当定时收料和定时检查各系统运行情况,记录各工艺参数;实验结束,先关加热和喂料,再以冷却速率50℃/min进行冷却,当进口温度低于100℃后,关停送风机和引风机,最后关闭总电源;关闭电源一定时间后,待出料口,球化室、管道等部位温度进一步降低至60℃,便可以取出球化后的粉体产物,因羟基磷灰石本身缺乏结构的完整性和力学稳定性的特性,难以球化成形,经分析,所得球化粉体、具备球化率仅达60%、流动行差(崩溃角45
°
)、力学性能差、表面粗糙等性能。
51.实施例2:
52.将55%羟基磷灰石(分子量为1004.62,纯度99%,粒径20nm)与45%左旋聚乳酸组成的二元组分粉体加入冷冻粉碎机粉碎,然后放置50℃真空干燥机中,进行36h真空干燥;再将干燥完成的多元组分粉体置入200目筛网以进行过滤,获得小于75um的粉体粒径;依次开启高分子粉体球化机的送风机、引风机、接着打开加热开关,再设定引风口温度270℃、出料口温度75℃、球化时间20min、气流速度12m/s、颗粒停留时间30min,以及送料速率8kg/h,随后开始升温,升温速率65℃/min,当引风口和出料口温度达到设定温度值后,继续对粉体球化机的球化室预热1.5h,当球化室的预热完成后,开始对进料斗进行喂料;设备正常运行后,应当定时收料和定时检查各系统运行情况,记录各工艺参数;实验结束,先关加热和喂料,再以冷却速率60℃/min进行冷却,当进口温度低于100℃后,关停送风机和引风机,最后关闭总电源。关闭电源一定时间后,待出料口,球化室、管道等部位温度进一步降低至60℃,便可以取出球化后的多元组分粉体产物,经分析,所得多元组分球化粉体、具备球化率高达95%、流动性好(崩溃角30
°
)、力学性能好、可稳定降解、表面光洁等优异性能。
53.实施例3:
54.将80%羟基磷灰石(分子量为1004.62,纯度99%,粒径20nm)与20%左旋聚乳酸组成的二元组分粉体加入冷冻粉碎机粉碎,放置55℃真空干燥机中,进行24h真空干燥;再将干燥完成的多元组分粉体置入100目筛网以进行过滤,获得小于150um的粉体粒径;依次开启高分子粉体球化机的送风机、引风机、接着打开加热开关,再设定引风口温度275℃、出料口温度70℃、球化时间10min、气流速度7m/s、颗粒停留时间15min,以及送料速率20kg/h,随后开始升温,升温速率52℃/min;当引风口和出料口温度达到设定温度值后,继续对粉体球化机的球化室预热0.5h,当球化室的预热完成后,开始对进料斗进行喂料;设备正常运行后,应当定时收料和定时检查各系统运行情况,记录各工艺参数;实验结束,先关加热和喂料,再以冷却速率85℃/min进行冷却,当进口温度低于100℃后,关停送风机和引风机,最后关闭总电源。关闭电源一定时间后,待出料口,球化室、管道等部位温度进一步降低至60℃,
便可以取出球化后的多元组分粉体产物,经分析,所得多元组分球化粉体、流动性好(崩溃角31
°
)、可稳定降解、表面光洁,因羟基磷灰石过量将导致难以球化成形,力学稳定性降低,所以该粉体球化率只有60%、且力学性能一般。
55.实施例4:
56.将60%羟基磷灰石(分子量为1004.62)与30%左旋聚乳酸、10%聚乙二醇组成的三元组分粉体加入冷冻粉碎机粉碎,放置60℃真空干燥机中,进行24h真空干燥;再将干燥完成的多元组分粉体置入200目筛网以进行过滤,获得小于75um的粉体粒径;依次开启高分子粉体球化机的送风机、引风机、接着打开加热开关,再设定引风口温度280℃、出料口温度79℃、球化时间30min、气流速度14m/s、颗粒停留时间35min,以及送料速率10kg/h,随后开始升温,升温速率62℃/min,当引风口和出料口温度达到设定温度值后,继续对粉体球化机的球化室预热1.5h,当球化室的预热完成后,开始对进料斗进行喂料;设备正常运行后,应当定时收料和定时检查各系统运行情况,记录各工艺参数;实验结束,先关加热和喂料,再以冷却速率64℃/min进行冷却,当进口温度低于100℃后,关停送风机和引风机,最后关闭总电源。关闭电源一定时间后,待出料口,球化室、管道等部位温度进一步降低至60℃,便可以取出球化后的多元组分粉体产物,经分析,所得多元组分球化粉体、具备球化率高达95.5%、流动性好(崩溃角29
°
)、力学性能好、可稳定降解、表面光洁等优异性能。
57.实施例5:
58.将80%羟基磷灰石(分子量为1004.62)与10%左旋聚乳酸、10%聚乙二醇组成的三元组分粉体加入冷冻粉碎机粉碎,放置60℃真空干燥机中,进行24h真空干燥;再将干燥完成的多元组分粉体置入100目筛网以进行过滤,获得小于75um的粉体粒径;依次开启高分子粉体球化机的送风机、引风机、接着打开加热开关,再设定引风口温度280℃、出料口温度79℃、球化时间10min、气流速度5m/s、颗粒停留时间17min,以及送料速率18kg/h,随后开始升温,升温速率50℃/min;当引风口和出料口温度达到设定温度值后,继续对粉体球化机的球化室预热0.5h,当球化室的预热完成后,开始对进料斗进行喂料;设备正常运行后,应当定时收料和定时检查各系统运行情况,记录各工艺参数;实验结束,先关加热和喂料,再以冷却速率50℃/min进行冷却,当进口温度低于100℃后,关停送风机和引风机,最后关闭总电源。关闭电源一定时间后,待出料口,球化室、管道等部位温度进一步降低至60℃,便可以取出球化后的多元组分粉体产物,经分析,所得多元组分球化粉体、流动性好(崩溃角30
°
)、可稳定降解、表面光洁,因羟基磷灰石过量将导致难以球化成形,力学稳定性降低,所以该粉体球化率只有70%、且力学性能一般。
59.实施例6:
60.将50%羟基磷灰石(分子量为1004.62)与20%左旋聚乳酸、20%聚乙二醇、10%氧化铝组成的多元组分粉体加入冷冻粉碎机粉碎,放置50℃真空干燥机中,进行24h真空干燥;再将干燥完成的多元组分粉体置入100目筛网以进行过滤,获得小于75um的粉体粒径;依次开启高分子粉体球化机的送风机、引风机、接着打开加热开关,再设定引风口温度290℃、出料口温度90℃、球化时间13min、气流速度9m/s、颗粒停留时间19min,以及送料速率19kg/h,随后开始升温,升温速率51℃/min;当引风口和出料口温度达到设定温度值后,继续对粉体球化机的球化室预热1.5h,当球化室的预热完成后,开始对进料斗进行喂料;设备正常运行后,应当定时收料定时检查各系统运行情况,记录各工艺参数;实验结束,先关加
热和喂料,再以冷却速率60℃/min进行冷却,当进口温度低于100℃后,关停送风机和引风机,最后关闭总电源。关闭电源一定时间后,待出料口,球化室、管道等部位温度进一步降低至60℃,便可以取出球化后的多元组分粉体产物,经分析,所得多元组分球化粉体、球形度高达95%、流动性好(崩溃角28
°
)、可稳定降解、表面光洁,力学性能优异。
61.本发明实施例1~6中采用的冷冻粉碎机包括:
62.用于对物料进行存储、冷冻进行分级处理的进料单元;
63.用于将冷冻后的物料进行破碎处理的粉碎单元;
64.用于将粉碎后的物料颗粒从粉碎单元中分离出来的输出单元;
65.与进料单元、粉碎单元、输出单元相配合,以控制其工作状态的控制器;
66.其中,在进料单元的预处理仓1、粉碎单元的粉碎仓2,输出单元的出料仓3上,分别设置有与液氮供给设备相连通的第一进料管4、第二进料管5、第三进料管6,在实际应用中,预处理仓与液氮供给设备通过第一进料管相连,实现在预处理仓中对高分子材料的预冷操作,第二进料管可以实时地向粉碎仓通入液氮,保证其粉碎效果满足使用要求,而进一步的在输出单元上设置相配合的第三进料管可以对于长距离输出进行冷却补偿,保证物料的加工品质;
67.所述第一进料管下方设置有与控制器通信连接的第一温度传感器7,其设置在于第一进料管的下方,其用于对于预处理仓内部的温度进行实时获取,以根据温度的实时检测,控制第一进料管的工作状态,而进一步地根据需要也可以在进料螺杆下方设置相配合的第三温度传感器,可以用于对传输过程中的物料温度进行实时获取,进而同时根据温度确定是否需要实时进行温度补偿,保证物料的加工稳定性;
68.所述粉碎仓与出料仓之间的第一连接管路8上设置有第二温度传感器9,所述出料仓在与第三进料管相配合的位置设置有流量控制阀,在这种结构中,通过在安装风机的处理仓与粉碎仓之间设置相配合的温度感应器(温度传感器),用来监测温度的实时变化,而在液氮的第三进料管终端设置与温度调控相配合的开关(流量控制阀),使得其可发根据环境温度调控液氮的供给状态,供经流量,使环境温度保持稳定,避免可降解医用子材高分料在长距离管道输出过程中因冷能不足而吸水降解,在种结构中,各进料管配合温度传感器、开关,使得本发明可以物料的破碎加工全各进行沿程冷能实时补偿,根据温度的变化调节液氮供给,解决了可降解医用高分子材料在长距离管道输出过程中因冷能不足而吸水降解的难题。
69.如图5-7,所述进料单元被配置为包括:
70.与预处理器连通的料斗10,在实际应用中,料斗中可以根据需要设置相配合的搅拌机构,对料斗中的物料进行实时搅拌,保证其物料传输的稳定性;
71.将预处理仓与粉碎仓连通的进料螺杆11,在实际安装中,本方案的各装置通过箱体21进行进行封装,而料斗设置在箱体上方,预处理仓设置于箱体内部,与进料斗相连通,进料螺杆前后方向设置(图5中进料螺杆因位置原因部分未示出),进料螺杆前端与预处理仓相连,进料螺杆后端与粉碎仓相连;
72.设置在与料斗与预处理仓之间,进料螺杆与预处理仓之间的第一电控阀门(未示出),第二电控阀门(未示出),在实际应用时,通过各电控阀门工作状态的切换,使得在预处理工作中时,料斗不再向预处理仓中输送物料,而预处理仓也不向粉碎仓输送物料,直到预
处理完成,而对于预处理仓中的物料,当完成一次预处理后,只有当其物料输出完成时,才会从料斗中再次向粉碎仓中进行供料操作;
73.所述第一电控阀门,第二电控阀门被配置为为控制器通信连接,在这种结构中,通过控制器与第一电控阀门的配合,完成对料斗送料的控制,通过控制器与第二电控阀门的配合,完成对预处理仓向粉碎仓送料的控制,保证各环节的控制的自动化,保证设备运行的智能化和可控性。
74.所述预处理仓的外壳被配置为呈双层结构,以在外壳的层与层之间限定用于容纳保温材料的空腔,通过双层结构的设计,使得其相对于现有的单层仓来说,其保冷效果更好,同时工作中设备的结构稳定性更好,不会因冷能交换,对设备中的其它部件的外部结构造成影响;
75.所述外壳的内侧壁被配置为呈弧形结构,通过弧形结构的设计,使得其受到压力时,压力的分散均匀度更好,设备结构稳定性更好,且在实际应用时,物料与设备之间的干涉性更小。
76.所述预处理仓内部设置有对物料进行混料的搅拌机构,在实际应用中,预处理仓中可以根据需要设置相配合的搅拌机构,对预处理仓中的物料进行实时搅拌,保证其在冷媒输入时,物料与冷媒接触的均匀度和一致性更好。
77.所述粉碎单元被配置为包括:
78.设置在粉碎仓内部,以将输入至粉碎仓内的物料进行破碎处理的粉碎组件;
79.设置在粉碎仓上的空心轴(未示出),其一端连通至粉碎仓的腔体内部,另一端与第二进料管连通,在这种结构中,通入液氮的第二进料管在与粉碎仓连接处设有空心轴液氮直喷装置,使得液氮能直通粉碎仓,缩短了液氮的传输路径,实现了对物料的快速降温;
80.其中,所述粉碎组件被配置为包括:
81.设置在粉碎仓下方的动力机构(未示出),其用于提供工作中的动力,一般是采用电机作为动力来源;
82.设置在粉碎仓内部,并与动力机构的动力输出轴连接的转轴(未示出),其用于将电机产生的转动传递给与固定机构连接的叶片,以在旋转时产生破碎的作用力;
83.与转轴连接的固定机构12;
84.与固定件可拆卸连接的多个叶片13,其用于在旋转过程中产生切割的作用力,对物料进行破碎切割;
85.设置在粉碎仓内侧壁上,以与叶片相配合进行破碎操作的至少一个齿形盘14,其用于对离心时带至侧壁上的物料者撞击破碎操作,以通过切割、撞击破碎的协同作用对物料进行破碎操作,使得经预处理后,材质变干脆的物料能在有效的时间内,破碎到需要的品质,保证物料加工的效率。
86.所述固定机构被配置为包括:
87.呈桶形结构的固定件15;
88.在空间上呈放射排列的多个固定板16,固定件与固定件为一体设置,而限定槽设置在固定板内部,固定板的排布方式、个数与叶片的分布需要相配合,工作时转轴带动固定机构进行旋转,进而使得与固定板连接的叶片进行旋转;
89.其中,所述固定板一端被配置为与转轴连接,另一端被配置为与固定件的环形侧
壁连接;
90.所述固定件在与各固定板相配合的位置上,分别设置有伸入固定板内部限定槽17,即在空间上限定槽穿过固定件的环形侧壁,同时深入至固定板内部,完成对叶片的固定,保证叶片固定的刚性;
91.所述叶片上设置有多个定位孔18,所述固定板上设置有固定孔(未示出),所述叶片通过螺钉可调节式的设置在限定槽内部,在这种结构中,叶片可通过螺栓定位于限定槽内,不同定位孔之间的配合可以实现叶片空间伸展长度的调整,进而根据粉碎粒径的需要自由调节叶片与齿形盘之间的间隙,实现粉末粒径的精确调控,保证不同加工场景的实际应用需要。
92.如图5,所述输出单元被配置为包括:
93.设置在出料仓内部,并与第一连接管路相配合的风机(未示出),其用于通过工作中产生的抽吸作用力将物料从粉碎仓中吸出;
94.通过第二连接管路与出料仓的出料端呈连通状的出料斗19;
95.其中,所述出料口通过相配合的第三连接管路20与预处理仓、粉碎仓连通,出料斗所在位置通过相配合的第三连接管路分别与预处理仓和粉碎仓相连通,构成多级冷源闭路循环系统,提高液氮的利用效率,避免造成液氮的浪费,同时可以调节各仓内部的工作气压,使得其能恒定的处于较为稳定的工作环境之下。
96.所述第一进料管、第二进料管、第三进料管的外侧均设置有相配合的第一保温层;
97.所述第一连接管路、第二连接管路、第二连接管路的外侧均设置有相配合的第二保温层,在这种结构中,通过保温层的设计,使得设备工作中产生的冷能可以尽可能的减小释放、流失,保证设备其它各部件的工作温度不受影响;
98.其中,各保温层被配置为包括:
99.与各管路外部相配合的内层,其用于与管道的表面相配合,通过其本身具有的刚度,对管道进行保护和防护;
100.通过粘接层设置在内层上方的聚苯乙烯泡沫层,其用于起隔离的作用,减小冷量流失;
101.设置在聚苯乙烯泡沫层上方的金属涂层,其用于增加泡沫层的使用寿命,防止其在受冷以及长期暴露后,设备材质性能受到的影响,缩短使用寿命的问题;
102.其中,所述内层被配置为采用聚氨酯塑料制备以得到,其用于保证设备的使用寿命,以及具有一定的硬度,可以在泡沫层发生形变时,减小其直接作用于管道上的作用力,对管路进行防护作用;
103.所述聚苯乙烯泡沫层被配置为内径大于各管路外径的环形结构,且所述聚苯乙烯泡沫层上具有与各管路长度方向相配合的缺口,通过缺口的设计,使得其可以根据需要直接卡在管路下,其适应于安装管路后的防护操作,装配简单,易于实现;
104.所述聚苯乙烯泡沫层通过间隔预定距离设置的多个扎带或卡箍进而固定,其用于对套设后的泡沫层进行固定,保证其与管路配合的稳定性。
105.如图8-10,所述内层被配置为包括:
106.套设在各管路外部的多个固定环22;
107.设置在相邻两个固定环之间,以在空间上对各管路构成围合状的多个弧形内板
23,在这种结构中,通过固定环与弧形内板的配合,使得内层是分体式结构,可以对安装完成后的管路进行防护安装操作,同时这种结构的设计,使得其后期的维护更加容易,即在维护时,不需要对管路进行拆装,操作更为简单,损失可以显著降低,同时维护的时间可以大弧度缩小,而弧形结构的设计,使得其与管路外部结构的配合更好;
108.其中,所述固定环的内径被配置为大于各管路的外径,所述固定环的内侧壁上设置有多个梯形固定槽24,通过梯形固定槽的设定,保证内板插接后的稳定性;
109.各弧形内板的两端分别设置有与固定槽相配合的卡头25;
110.所述弧形内板高度被配置为大于卡头的高度,且与固定环的外径在空间上保持齐平,所述内板的内侧壁上设置有多个与管路外壁接触的弧形突出部26,通过结构限定,使得固定环在空间上通过弧形结构的突出部对固定环进行支撑固定,进而使得内板与管路表面不会存在接触,不会产生干涉,进而使得设备管路表面在遇到冲击时,首先通过泡沫进行缓冲,而当冲击压力过大时,因为固定环与管路不表面不产生接触,其冲击力可以通过弧形突出部进行释放和部分吸收,减小其受损程度,保证设备的工作稳定性和使用寿命。
111.其中液氮冷冻粉碎机的使用方法,包括:根据要求调整叶片与齿形盘之间的间距,设定预处理仓中复合粉体进行预定处理的预冷温度为165℃,设定粉碎仓中对复合粉体进行粉碎处理的粉碎温度为-150℃;
112.步骤二,关闭第二电控阀门,打开第一电控阀门将复合粉体通过料斗进入到预处理仓中进行储存,关闭第一电控阀门,用于预冷的液氮通过第一进料管进入预处理仓,对复合粉体进行预冷操作;
113.步骤三,当达到预处理仓达到设定的预冷温度,粉碎仓达到预定的粉碎温度,打开第二电控阀门,启动进料螺杆按照预定的进料速度将复合粉体送入粉碎仓,用于冷却的液氮通过第二进料管进入到粉碎仓,复合粉体在叶片和齿形盘的作用下粉碎成粉末状;
114.步骤四,粉末在出料仓中风机的作用下由粉碎仓输出至出料斗,以在出料斗处完成粉末的收集操作,在这种过程中,通过第二温度器对输出中物料的温度进行实时检测,在其温度过高时,通过开关的限定将第三进料管的工作状态切换成打开状态,按照设定向输出仓中再次输入冷媒,保证其在长距离传输过程中,物料性能指标的稳定性;
115.步骤五,在干燥箱中对收集的粉末进行干燥处理,其干燥温度控制在60℃,干燥时间24小时,在这种方案中,通过对各步骤的限定,使得其相对于现有技术而方主,工作流程可以根据需要进行调整,以保证工艺的稳定性和适应性。
116.本发明采用的冷冻粉碎机,与传统粉碎机相比,解决了生物可降解复合粉体在粉碎过程中因长距离管道输出时造成的冷能不足而吸水降解的问题;
117.并且本发明采用伸缩式微调叶片装置,叶片与齿形盘之间的间隙可自由调节,实现了粉体粒径的精确调控;本发明在粉碎腔内采用空心轴使液氮直通粉碎腔,缩短了液氮传输路径,实现了物料的快速降温;本发明采用多级冷源闭路循环系统,实现了冷能的高效循环利用;本发明针对性的外露的连接管路进行了保冷防护,防止其在使用过程中,对设备的其它部件使用寿命、工作稳定性造成的影响,减小冷量流失,保证使用效果满足使用要求。
118.尽管本发明的实施方案已公开如上,但其并不仅仅限于说明书和实施方式中所列运用。它完全可以被适用于各种适合本发明的领域。对于熟悉本领域的人员而言,可容易地
实现另外的修改。因此在不背离权利要求及等同范围所限定的一般概念下,本发明并不限于特定的细节和这里示出与描述的图例。