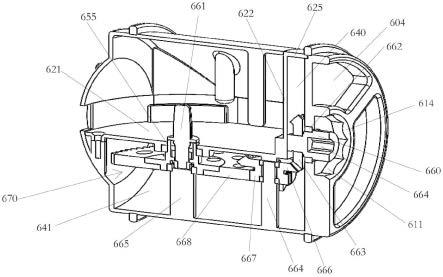
1.本实用新型涉及医疗器械技术领域,特别是涉及一种用于血管介入手术机器人的实现导丝旋转与递送的传动装置。
背景技术:2.微创血管介入手术是心脑血管疾病诊断、治疗的基本手段,目前实施的多数血管病变诊断、血管重建手术都需借助这项技术。导丝的操作是微创血管介入手术的核心内容之一,决定着手术质量的好坏。目前,介入医生借助数字剪影血管造影成像技术(dsa)手动完成导丝在病人血管内的定位操作。使用机器人装置进行导丝的定位操作,有利于提高定位操作精度与稳定度,将医护人员从辐射中解放出来,避免医护人员因穿着厚重铅衣而带来的附加伤害,避免医护人员因疲倦而造成术中操作不可靠的情况,改善传统介入手术极度依赖医生个人经验的情况,降低介入手术的学习曲线,为血管介入手术提供更精确的操作。
3.医用导管为空腔管状结构,内部的空腔用作造影剂注射通道或医疗器械输送通道。由于导管硬度较强不便于完成血管的选择,因此采用柔顺性较强的实心导丝引导导管进入靶定血管。手术过程中,医生在股动脉或桡动脉进行血管穿刺并留置血管鞘,作为导管进入血管的入口。导管经血管鞘进入患者体内的血管,导丝从导管内部的通道进入血管。通常由介入医生与其副手两人四手完成对导丝前进与后撤以及旋转的控制。
4.在利用机器人辅助血管介入手术时,利用机器人实现导丝前进与后撤以及导丝的旋转是最为核心的功能之一。要实现对导丝的运动控制,首先须实现导丝的无损夹持。由于导丝表面具有超滑泥鳅涂层,传统的夹持方法易出现夹持不紧或夹持过紧而损坏导丝表面涂层的情况。而导丝转动不能受夹持装置的干扰,因此导丝旋转装置必须与夹持装置一体化。同时,导丝会直接进入患者体内,对无菌条件有较高的要求。
5.根据导丝输送驱动力来源的不同,目前国内外导丝夹持器方案可分为两类:摩擦轮夹持与直推式输送方案。摩擦轮夹持是指利用一对或多对摩擦轮通过挤压夹持导丝,在主动轮的带动下,导丝可实现前进或后撤运动。该种情况下,导丝的旋转需要两个摩擦轮在垂直于导丝轴向方向上进行反方向运动以搓动导丝。另外一种方式是采用直推式输送方案,导丝的输送由专门的驱动机构带动夹持导丝的装置线性运动来实现。导丝夹持装置只需要实现导丝夹持即可,更多地需要考虑导丝旋转的实现。传统方式是为夹持装置增设额外驱动装置,带动导丝夹持装置从而导丝转动。从而实现导丝的小角度旋转,效率较低。
技术实现要素:6.传统血管介入手术机器人的导丝旋转与递送装置存在以下几个方面的问题:由于导丝表面具有超滑泥鳅涂层,当遇到阻力时,导丝容易滑动,导致导丝旋转与递送精度降低;通过夹持导丝实现导丝旋转的效果不稳定;而且无菌环境实现不彻底。
7.本实用新型旨在克服传统技术存在的上述缺陷,其目的是提供一种用于血管介入
手术机器人的导丝旋转与递送传动装置,能够实现导丝的精确递送与旋转,不会对导丝造成任何损伤;而且,该装置与机器人本体采用分离式结构,可实现术中无菌环境隔离。
8.根据本实用新型,提供了一种用于血管介入手术机器人的导丝旋转与递送传动装置,所述导丝旋转与递送传动装置包括:
9.外壳,该外壳包括下壳,下壳包括周向侧壁、设置在周向侧壁前端的前端盖板以及设置在周向侧壁后端的后端盖板,所述下壳的上部敞开;
10.导丝盘自转传动机构以及导丝盘自转驱动轴,所述导丝盘自转传动机构的输出端与所述导丝盘自转驱动轴连接,用以驱动导丝盘自转驱动轴旋转,所述导丝盘自转驱动轴用以连接导丝递送装置的导丝盘并驱动导丝盘自转;
11.分隔板,该分隔板包括水平板部分,水平板部分固定地安装在所述下壳中,水平板部分与所述下壳的位于水平板部分下面的部分之间形成安装空间,水平板部分上部用以安放导丝递送装置;水平板部分上形成有所述导丝盘自转驱动轴从中穿过的通孔;
12.定位装置,用以将安放在所述水平板部分上的导丝递送装置相对于外壳定位,使得导丝递送装置可以随同外壳一起旋转;
13.所述后端盖板上设置有纵向向后延伸的外壳旋转驱动轴,用于与外壳旋转动力输出轴连接来驱动外壳旋转,所述外壳旋转驱动轴为空心轴结构,形成有中心孔;
14.所述导丝盘自转传动机构包括导丝盘自转动力输入轴,以及设置在导丝盘自转动力输入轴与所述导丝盘自转驱动轴之间的传动组件,所述传动组件至少部分地设置在所述安装空间中,由导丝盘自转动力输入轴输入的动力经该传动组件传递给所述导丝盘自转驱动轴,所述导丝盘自转驱动轴延伸穿过所述水平板部分上形成的通孔;
15.所述导丝盘自转动力输入轴与所述外壳旋转驱动轴同轴设置,并位于所述外壳旋转驱动轴的中心孔中,用于与导丝盘自转动力输出轴连接来接收驱动力,所述导丝盘自转动力输入轴纵向前端延伸穿过所述后端盖板并由所述后端盖板支承;
16.所述外壳上设置有旋转支承轴,该旋转支承轴与所述外壳旋转驱动轴同轴设置,用以旋转支承所述外壳。
17.采用本实用新型技术方案,实现了如下技术效果:
18.1、导丝旋转与递送传动装置安装在器械操作盒中,与机器人本体完全脱离开来,彻底解决了手术中导丝旋转与递送传动装置与动力单元分离不彻底导致的无菌环境难以保障的难题;
19.2、本实用新型的导丝旋转与递送传动装置采用外壳旋转带动导丝盘旋转,进而带动导丝旋转的技术方案,导丝与导丝旋转装置无接触,不会因为导丝的超滑泥鳅涂层在湿润条件下明显减小导丝与接触部件之间的摩擦力而导致的旋转不稳定问题,实现了导丝的精准旋转运动;
20.3、本实用新型的导丝旋转与递送传动装置采用导丝盘旋转实现导丝递送的技术方案,不会产生现有技术中存在的导丝与夹持装置产生相对运动而导致递送不精确的问题,实现了导丝的精准递送,而且导丝不会受到损伤;
21.4、根据本实用新型的导丝旋转与递送传动装置,利用传动组件将源自机器人本体的动力单元的导丝旋转与递送驱动力传出,更有利于无菌环境实现;
22.5.本实用新型的导丝旋转与递送传动装置安装方便、快捷,最大程度降低了由于
医生对装置安装熟练度不足而导致的安装错误的可能性。
附图说明
23.下面结合附图和实施例对本实用新型作进一步详细说明,其中
24.图1是透视图,图示了用于血管介入手术机器人的从端部分的总体结构;
25.图2是根据本实用新型的导丝旋转与递送传动装置的透视图,其中上盖处于打开状态;
26.图3是根据本实用新型的导丝旋转与递送传动装置的透视图,其中上盖处于闭合状态;
27.图4是根据本实用新型的导丝旋转与递送传动装置的透视图,上盖处于打开状态,其中分隔板被去掉以显示下壳的内部结构;
28.图5是根据本实用新型的导丝旋转与递送传动装置的纵向剖视透视图;
29.图6是与本实用新型导丝旋转与递送传动装置配用的器械操作盒的透视图;
30.图7a是透视图,图示了根据本实用新型的导丝旋转与递送传动装置的另一实施例,其中上盖处于打开状态;
31.图7b是透视图,图示了根据本实用新型的导丝旋转与递送传动装置的另一实施例,其中上盖处于闭合状态;
32.图8是透视图,图示了带有凸嘴的导丝递送装置安装就位于下壳中的状态;
33.图9是透视图,图示了设置在外壳前端盖板上的导丝孔的结构;以及
34.图10是纵向剖视透视图,图示了导丝盘自转传动机构的另一实施例。
具体实施方式
35.下面结合附图对本实用新型的用于血管介入手术机器人的导丝旋转与递送传动装置进行详细的说明。在此应当指出,本实用新型的实施例仅仅是例示性的,其仅用于说明本实用新型的原理而非限制本实用新型。
36.首先参见图1,其图示了用于血管介入手术机器人的从端部分的总体结构。如图1所示,从端部分包括机器人本体1、器械操作盒组件2和导丝旋转与递送传动装置3。机器人本体1包括基座机构和动力单元,动力单元包括导管动力盒与导丝动力盒,导管动力盒安装在设置在基座中的滑块上并随滑块一起移动,导丝动力盒4设置在导管动力盒后部并与导管动力盒侧向连接固定。器械操作盒组件2的横向一侧与所述导管动力盒的相邻一侧侧向连接,其纵向后端与导丝动力盒4相邻设置,器械操作盒组件2随导管动力盒一起移动。导丝旋转与递送传动装置3配设在器械操作盒组件2上,其后端与导丝动力盒连接。
37.为了描述的方便,在以下的说明中,器械操作盒组件2的移动方向定义为纵向,器械操作盒组件的宽度方向定义为横向;使用中器械操作盒组件朝向人体血管的一端称为前端,背离血管的一端称为后端。
38.下面参见图2至图4,图2是根据本实用新型的导丝旋转与递送传动装置的透视图,其中上盖处于打开状态;图3是根据本实用新型的导丝旋转与递送传动装置的透视图,其中上盖处于闭合状态;图4是根据本实用新型的导丝旋转与递送传动装置的透视图,上盖处于打开状态,其中分隔板被去掉以显示下壳的内部结构。如图2所示,导丝旋转与递送传动装
置包括外壳600,外壳包括下壳601以及上盖602,下壳601的上部敞开。如图3所示,在上盖闭合的状态下,下壳与上盖的组合体形成一圆筒形外壳,包括筒身607以及前端盖板603和后端盖板604。如图2-4所示,平行于所述圆筒形外壳轴线的平面形成所述下壳601和上盖602的剖分面,所述后端盖板604为一整体圆盘,与下壳601一体形成;所述前端盖板603和筒身607由剖分面分割成两部分,分别隶属于下壳与上盖。下壳与上盖的上述剖分面形成两者的贴合面,在上盖闭合在下壳上时,上盖的贴合面与下壳的贴合面相互贴合。
39.如图2所示,上盖602的圆周壁端部与下壳601的圆周壁端部通过铰链610连接,从而上盖可以在打开位置与闭合位置之间枢转。为了将上盖牢靠地保持在闭合位置防止其无意打开,可以设置闭合锁定装置。
40.在所示实施例中,如图4所示,闭合锁定装置是磁铁组件,可以在下壳的前端盖板与圆周壁板结合处的贴合面上埋置磁铁件或铁磁材料件612,而在上盖的前端盖板与圆周壁板结合处的贴合面上埋置铁磁材料件或磁铁件614,通过磁铁件与铁磁材料件吸合作用将上盖保持在闭合位置。
41.对于闭合锁定装置,可以采用现有技术中的各种锁定装置,比如卡扣卡槽结构等,因此在此给出的示例仅作为说明的一个实例,而绝非用于限定所采用的闭合锁定装置的具体结构。
42.如图2所示,为了便于上盖的打开与闭合,作为一种优选的方案,可以在上盖的前端盖板上设置一圆柱611,通过握持圆柱来进行开闭操作。
43.此外,上盖也不必铰接在下壳上,而是一个与下壳独立的部件,在组装时通过比如卡扣卡槽结构连接在一起,比如像乐扣乐扣保鲜盒那样。
44.如图5所示,后端盖板604后侧形成有外壳旋转驱动轴614,外壳旋转驱动轴614沿纵向向后延伸,外壳旋转驱动轴的轴线与圆筒形外壳的轴线同轴。外壳旋转驱动轴614为空心轴,空心轴限定出纵向中心孔611。空心轴的结构既可以呈现为:中心孔是非圆形孔,比如可以是图5中所示的多边形孔或d形孔等,外周面是圆柱形;也可以呈现为:中心孔是圆形孔,外周面是非圆柱形,比如,截面呈多边形孔或d形。外壳旋转驱动轴614用于与驱动装置的具有适配结构的外壳旋转动力输出轴连接,使得外壳可以在驱动装置的驱动下旋转。
45.在实际使用中,通过将外壳旋转驱动轴614连接于驱动装置的外壳旋转动力输出轴来实现外壳旋转操作。为了确保外壳安装的稳定性,作为一种优选的方案,如图6所示,与导丝旋转与递送传动装置配用的器械操作盒组件上设置有圆弧形支承面301,该圆弧形支承面301与外壳的外圆周面接触用以提供支承。
46.为了确保外壳旋转操作的顺畅性,作为一种优选的方案,可以在外壳上设置滑轨。在图示实施例中,如图3所示,设置有两条滑轨615和616,分别位于圆筒形外壳的纵向两端,并沿外壳的周向设置。后端的滑轨615设置在外壳后端盖板的外圆周面上,前端的滑轨616由两段构成,一段617设置在上盖一侧,另一段618设置在下壳一侧,在上盖处于闭合位置时,两段滑轨周向接合形成一条完整的圆周滑轨。在操作中,两条滑轨与器械操作盒的圆弧形支承面301接触,由此确保圆筒旋转的顺畅性。
47.作为上述实施例的一种改型,可以不在圆筒形外壳上设置滑轨,而采用其它替代方案。如图6所示,可以在器械操作盒的圆弧形支承表面处设置两组支承滚轮302,位置分别对应于圆筒形外壳的纵向两端,每组支承滚轮包括若干个沿周向间隔布置的支承滚轮303,
对外壳进行滚动支承。
48.作为上述实施例的另一种改型,可以不用外壳的筒身作为导丝旋转与递送传动机构的旋转支撑,取而代之的是,如图7a和图7b所示,可以在前端盖板上设置纵向向前延伸的空心支承轴619,空心支承轴619的轴线与外壳旋转驱动轴的轴线同轴设置,该空心支承轴619用作导丝旋转与递送传动机构的旋转支撑。与此相对应,类似于用圆筒形壳体的筒身作为旋转支撑那样,可以在器械操作盒上设置相应的圆弧形支承面来支承空心支承轴619。类似于用圆筒形壳体的筒身作为旋转支撑那样,可以在空心支承轴上设置滑轨,或者可以在器械操作盒的圆弧形支承表面处设置支承滚轮。在图示实施例中,空心轴一部分设置在下壳上,另一部分设置在上盖上,上盖闭合时形成完整的空心轴。作为该空心轴的改型,可以采用其它的方案,比如可以根据下壳与上盖的结构而将整个空心轴设置在下壳上或者上盖上。在采用设置在前端盖板上的纵向向前延伸的空心支承轴619作为旋转支承的情况下,可以采用非圆筒形外壳,比如截面呈多边形的外壳等,如图7a和图7b图示了截面呈矩形的外壳实例。
49.为了确保外壳安装以及旋转的稳定性,作为一种优选的方案,如图6所示,在器械操作盒组件上设置有用于导丝旋转与递送传动装置的纵向定位装置305。在所示实施例中,所示纵向定位装置305包括两个纵向挡持件306,纵向挡持件可沿纵向移动,沿纵向朝向后侧受到偏压。在导丝旋转与递送传动装置配设在器械操作盒组件上时,两个纵向挡持件306抵接外壳的前端盖板。为了减少摩擦而便于外壳的旋转,两个纵向挡持件306上设置有滚珠,就像圆珠笔配设的滚珠那样,组装后纵向挡持件306上的滚珠抵触外壳的前端盖板。
50.如图2和图5所示,根据本实用新型的导丝旋转与递送传动装置,在下壳中设置有分隔板620,分隔板620固定地安装在下壳601中。分隔板620整体上呈l形,包括水平板部分621和直立板部分622。水平板部分621周向对称地安放在下壳中,其结构形状与下壳中相应部分的内轮廓相匹配,起到分隔作用,其上部用以安放导丝递送装置。水平板部分621与所述下壳的位于分隔板下面的部分之间形成安装空间641,见图5。直立板部分622与下壳的后端盖板604平行设置并与之间隔开,其包括上下两部分,下端部分623插装在下壳中,上端部分624位于下壳贴合面上方,外轮廓形状与上盖602外轮廓相吻合。此外,上端部分624还设置有自上端部分的外边缘沿纵向向后延伸的圆环形部分625,圆环形部分625的周向两端分别接合下壳的贴合面,圆环形部分的纵向后端抵靠后端盖板的前表面,从而在直立板部分622与外壳的后端盖板604之间形成安装空间640。
51.为了固定分隔板620,如图4所示,在下壳的圆周壁上设置有若干朝向分隔板水平板部分621延伸的凸柱626,凸柱上形成有螺纹孔627;相应地,如图2所示,在分隔板水平板部分621上与螺纹孔627相对应的位置上形成有螺钉孔628,借此,通过螺钉将分隔板水平板部分固定在下壳上。类似地,如图4和图2所示,在下壳的后端盖板604上设置有螺纹孔629,相应地,在分隔板直立板部分622上与螺纹孔629相对应的位置上形成有螺钉孔630,借此,通过螺钉将分隔板直立板部分固定在后端盖板604上。也可在分隔板直立板部分与后端盖板之间设置起支撑作用的圆筒形件,固定直立板部分时,螺钉延伸穿过圆筒形件的通孔并与后端盖板604上的螺纹孔629拧紧,而圆筒形件撑靠在直立板部分与后端盖板之间。作为一种选择,圆筒形件可以作为圆柱设置在直立板部分上或后端盖板上。
52.如图2所示,分隔板水平板部分的上部与下壳的圆周壁、前端盖板和分隔板直立板
部分限定出用以安放导丝递送装置的安装空间631。安装空间631可以根据导丝递送装置的外轮廓形状配设特定的定位结构。以具有圆形外轮廓的导丝递送装置为例,可以在分隔板的水平板部分与水平板部分之间的拐角处居中地设置凸台632,朝向导丝递送装置的一侧呈圆弧形,以适配导丝递送装置的外轮廓;类似地,也可以在下壳的圆周壁以及/或者前端盖板上设置内端呈圆弧形的凸块633等。作为一种优选的方案,如图3所示,外壳的前端盖板可以不是平板状,而是径向外端呈平板状圆环634,中间部分635呈拱顶形并向前部凸出,拱顶形部分的内轮廓与导丝递送装置的外轮廓相适配。借此,导丝递送装置得以安稳地安装就位下壳中。
53.对于带有凸嘴的导丝递送装置,可以在外壳前端盖板上设置孔口来适配凸嘴。如图2所示,孔口636可以单独形成在外壳的前端盖板上,或者孔口636可以部分形成在下壳的前端盖板上,部分形成在上盖的前端盖板上,取决于凸嘴的特定结构以及下壳与上盖的结构。图8图示了带有凸嘴51的导丝递送装置5安装就位于下壳中的状态。
54.对于不带有凸嘴的导丝递送装置,可以在外壳前端盖板上设置导丝孔,导丝孔可以单独形成在下壳的前端盖板上或者上盖的前端盖板上;或者部分形成在下壳的前端盖板上,部分形成在上盖的前端盖板上,上盖闭合时形成完整的导丝孔。作为一种优选的方案,如图9所示,可以单独在外壳的前端盖板上设置纵向延伸的凸起,该凸起上形成有纵向导丝孔。在图9所示实施例中,在下壳的前端盖板与上盖的前端盖板两者上分别设置凸起半部650和651,两个凸起的彼此相对的表面上设置有贯穿凹槽652和653,上盖闭合时,两个凹槽拼合成导丝孔。由此,可以延长导丝孔的纵向长度,以对导丝提供稳定的支撑和导向。作为上述方案的一种改型,带有导丝孔的纵向凸起可以单独形成在下壳的前端盖板上或者上盖的前端盖板上,取决于下壳与上盖的特定结构。
55.为了将安放在下壳中的导丝递送装置固定就位,防止外壳旋转时导丝递送装置脱位,本实用新型的导丝旋转与递送传动机构设置有定位装置。图4图示了定位装置的一个实施例,如图4所示,可以在上盖的圆周壁上设置若干朝向分隔板水平板部分延伸的圆柱637,在上盖处于闭合位置时,各圆柱顶部抵接导丝递送装置的盘盒或其它能够用以固定的部分,使导丝递送装置固定就位。
56.作为定位装置,可以采用其它多种方案。举例来说,可以在分隔板的水平板部分上设置磁铁件或铁磁性材料件,而所述导丝递送装置的对应部位处设置有铁磁性材料件或磁铁件,磁铁件与铁磁材料件组合体用作所述定位装置。因此,本实用新型不对用于使导丝递送装置固定就位的定位装置做特别限定,凡是能够实现定位功能的任何定位装置都在本实用新型的保护范围之内。在采用比如磁铁组合件作为定位装置的情况下,外壳的上盖也可以省去不用。
57.此外,如图2所示,在分隔板水平板部分上还设置有用于导丝盘自转驱动轴的安装孔655,在组装状态下,导丝盘自转驱动轴661延伸穿过该安装孔。
58.在上述实施例中,分隔板包括水平板部分和直立板部分,但直立板部分不是必须的,也可以省去不用。
59.下面描述实现导丝旋转的具体操作。
60.首先,将外壳的上盖打开,将导丝递送装置安装就位,使外壳旋转驱动轴与驱动装置的外壳旋转动力输出轴连接;然后闭合上盖,并利用定位装置将导丝递送装置固定,同时
利用锁定装置将上盖锁定;随后,启动驱动装置带动外壳旋转,进而外壳带动导丝递送装置旋转,从而实现导丝的旋转。
61.为了确保导丝旋转的稳定性和精确性,导丝递送装置在下壳中安装就位后,从导丝递送装置的导丝出口直线伸出的导丝部分应尽可能与外壳旋转驱动轴的轴线同轴,以保证导丝绕其自身轴线旋转而尽量避免导丝围绕外壳旋转驱动轴的轴线公转。
62.下面描述本实用新型的导丝旋转与递送传动装置的导丝盘自转传动机构,其用以驱动导丝递送装置的导丝盘自转,进而实现导丝的递送操作。
63.如图5所示,导丝盘自转传动机构包括导丝盘自转动力输入轴660,以及设置在导丝盘自转动力输入轴与导丝盘自转驱动轴661之间的传动组件670,由动力输入轴660输入的动力经传动组件传递给导丝盘自转驱动轴。该导丝盘自转驱动轴与导丝递送装置的导丝盘连接,用以驱动导丝盘自转从而实现导丝的递送和回撤,导丝盘自转驱动轴的横截面可以呈多边形或d形。
64.所述导丝盘自转动力输入轴660与所述外壳旋转驱动轴614同轴设置,并位于所述外壳旋转驱动轴的中心孔611中。动力输入轴660的动力输入端沿纵向向后延伸并形成有纵向孔664,该纵向孔是非圆形孔,比如可以是多边形孔或d形孔等,用于与驱动源(比如电机等)的导丝盘自转动力输出轴连接来接收驱动力;所述导丝盘自转动力输入轴纵向前端延伸穿过所述后端盖板604并通过轴承662支承在后端盖板上。
65.所述传动组件包括伞齿轮形式的第一传动齿轮663,于所述后端盖板前侧安装在导丝盘自转动力输入轴的动力输出端,位于安装空间640中,并随所述导丝盘自转动力输入轴一同旋转。
66.所述传动组件还包括中间轴664和输出轴665,中间轴与导丝盘自转动力输入轴垂直设置,并由设置在下壳圆周壁上的圆柱形成;此外,中间轴664垂直于水平板部分621。呈伞齿轮形式的第二传动齿轮666可转动地安装在中间轴664的与导丝盘自转动力输入轴相邻的一端,并与所述第一传动齿轮663啮合。
67.所述中间轴664上还设置有位于第二传动齿轮666下侧、呈直齿轮形式的第三传动齿轮667,第三传动齿轮随同第二传动齿轮一起绕中间轴旋转,第三传动齿轮可与第二传动齿轮一体形成。所述输出轴665平行于中间轴设置,并由设置在下壳圆周壁上的圆柱形成。呈直齿轮形式的第四传动齿轮668可转动地安装在输出轴665上,并与第三传动齿轮667啮合。导丝盘自转驱动轴661固定地安装在第四传动齿轮668上,或与第四传动齿轮一体形成,从水平板部分上形成的安装孔655伸出。
68.在操作中,导丝盘自转动力输入轴660接收动力源的动力,经由传动组件670将动力传递给导丝盘自转驱动轴661,导丝盘自转驱动轴661带动导丝盘旋转,实现导丝的递送与回撤操作。
69.下面参见图10,其图示了根据本实用新型另一实施例的导丝盘自转传动机构。
70.该实施例的导丝盘自转传动机构与上一实施例的导丝盘自转传动机构主要区别体现在如下方面。
71.在该实施例中,如图10所示,中间轴864平行于导丝盘自转动力输入轴860设置且位于导丝盘自转动力输入轴下方,中间轴864由设置在外壳后端盖板604上的圆柱形成。导丝盘自转动力输入轴的位于后端盖板前侧的动力输出端上设置有呈直齿轮形式的第一传
动齿轮863,中间轴上安装有与第一传动齿轮863啮合、呈直齿轮形式的第二传动齿轮866。中间轴864上还设置有位于第二传动齿轮866前侧、呈伞齿轮形式的第三传动齿轮867,第三传动齿轮与第二传动齿轮一同旋转,并可与第二传动齿轮一体形成。输出轴865垂直于中间轴864设置,并由设置在下壳圆周壁上的圆柱形成,输出轴上设置有呈伞齿轮形式的第四传动齿轮868,所述第四传动齿轮与第三传动齿轮867啮合。
72.上面参照附图结合具体实施例对本实用新型进行了描述,但这仅仅是为了说明的目的,而本实用新型并不局限于此。因此,对于本领域技术人员而言显而易见的是,可以在本实用新型的技术精神和范围内进行各种变化和修改,而这些变化和修改也应理解为属于本实用新型范畴,本实用新型的范围由要求保护的技术方案及其等同方案予以限定。