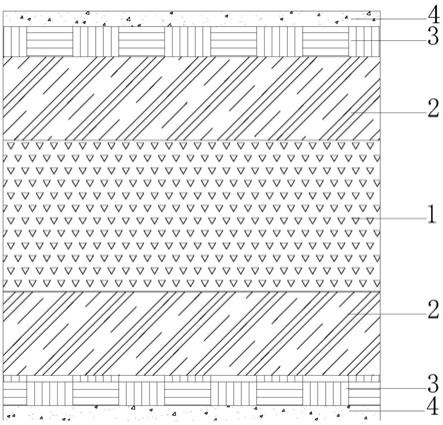
[0001]
本实用新型涉及胶合板技术领域,尤其涉及竹木胶合板。
背景技术:[0002]
竹胶合板具有材质坚韧、力学性能优异等优点。我国竹材资源丰富,生长周期短,具有一次种植、永续利用的特点,以竹胶合板替代木胶合板,可以解决木胶合板受限于木材资源短缺的问题。传统竹胶合板以竹席、竹帘等为制造单元,通过干燥、浸胶、沥胶、二次干燥、组坯、热压等工序制备而得。相比木胶合板,传统竹胶合板存在以下几方面问题:
[0003]
①
传统竹胶合板制造采用冷进-冷出热压成型工艺,即“进料-升温-保温热压-降温-卸压出料”工序,该工艺存在热压时间长、热能与冷却水消耗大等缺点,直接导致了传统竹胶合板长期存在生产效率低、能源消耗大、制造成本高等难题。
[0004]
而直接采用热进-热出热压成型工艺,由于板坯结构单一,单元间宏观微观孔隙致密,热压过程中水分难以向外迁移,造成局部蒸汽压力过大,易形成鼓泡变形和局部破坏等热压缺陷,产品质量严重下降等,无法使用。
[0005]
目前胶合板制造普遍采用二次组坯、二次热压生产工序,即板坯一次热压成型后再敷贴三聚氰胺浸渍纸并二次热压,工序复杂,生产成本高,并且敷贴三聚氰胺浸渍纸前还需将一次热压后的板坯砂光处理,进一步增加了工序,损耗了材料,增加了成本。
[0006]
②
板坯密度大,质量重,使用范围受限,且不利于装卸,运输成本高。
[0007]
③
板坯强度具有明显定向性,横向强度不佳,横纹握钉力差,应用范围受限。
[0008]
④
目前采用竹帘或竹席制作的胶合板,竹条的竹青和竹黄影响后续胶合成型工艺以及材料物理力学性能,因此都需要先进行去青去黄处理,导致竹材利用率降低,原料损失较大,生产成本增加。
[0009]
相比竹胶合板,木胶合板在表面硬度、弹性模量、抗拉强度等物理力学性能明显弱于竹胶合板。基于竹木材资源和竹木各自材性特点,结合生产实际和市场需求,以竹材和人工林速生材为制造单元,开发一种具有生产制造工序简单、生产成本较低、物理力学性优异等特点的新型竹木胶合板,对于推动传统竹胶合板转型升级,实现竹材高值化利用并缓解我国木材资源供需矛盾等方面具有重要意义。
技术实现要素:[0010]
本实用新型要解决的技术问题是克服现有技术的不足,提供一种生产周期短、热压缺陷少、密度适宜力学性能优异的一种竹木胶合板。
[0011]
为解决上述技术问题,本实用新型采用以下技术方案:
[0012]
一种竹木胶合板,所述竹木胶合板由竹篾帘层、木单板层、竹席层、浸渍纸层胶合而成,所述竹篾帘层两侧对称依次设置木单板层、竹席层和浸渍纸层,所述竹篾帘层由未去除竹青与竹黄的径向竹蔑编织而成,所述竹席层由去除竹青与竹黄的弦向竹篾经纬交织编织而成。
[0013]
作为对上述技术方案的进一步改进:
[0014]
所述木单板层表面设有凹槽。
[0015]
所述竹木胶合板的密度为0.6-0.75g/cm3,静曲强度为95-110mpa,握钉力为2200-2400n。
[0016]
所述竹篾帘层、木单板层、竹席层、浸渍纸层的厚度比为1-3∶0.8-2.2∶0.8-1∶0.5-0.8。
[0017]
所述凹槽的深度为0.1-0.3mm。
[0018]
与现有技术相比,本实用新型的优点在于:
[0019]
1、本实用新型的竹木胶合板,由于利用木单板层的人工林速生材密度约为竹材密度的一半,在竹席层和竹蔑帘层之间铺设木单板层可有效降低板材整体密度和重量,利于装卸,并减少运输成本。与此同时,木材微观构造上具有天然纵横交错的细胞排列结构,而竹材仅具备纵向排列的细胞结构,在竹席层和竹篾帘层之间铺设木单板层有利于提高板材横向强度,并增加板材厚度方向上握钉力,扩大了应用范围。
[0020]
2、本实用新型的竹木胶合板,竹席层由弦向竹篾经纬交织编制而成,竹蔑帘层由径向竹篾编制而成,竹席层、竹篾帘层和木单板层三者在宏观孔隙结构、细观孔隙结构与微观孔隙结构上有明显差异,三者构成的多层交错结构具有更多维度的孔隙气流通道,在载荷热压过程中形成了多尺度缓冲效应,为热压过程水分向外迁移提供了更多的孔隙结构空间和时间,防止热进-热出工艺条件下因局部水分迁移受阻而蒸汽压力过大导致的鼓泡等缺陷,奠定了热进-热出热压成型工艺可行性的基础。
[0021]
3、本实用新型的竹木胶合板,木单板层表面形成了全维度分布的微小凹槽,有利于在木单板层和竹席层、竹篾帘层之间形成全维度分布的胶钉结构,极大提高了木单板层与竹席层、竹帘层的胶合性能。
[0022]
4、本实用新型的竹木胶合板,竹篾帘层由未去除竹青与竹黄的径向竹篾编织而成,提高了竹材原料利用率,减少了工艺流程。并且径向竹篾厚度较薄,竹青与竹黄分布在径向竹篾的左右两个侧面而非上下两个宽面,因而不会对热压成型工艺以及板材成型质量产生明显影响。
附图说明
[0023]
图1是本实用新型实施例1的结构示意图。
[0024]
图2是图1中a处的局部放大图。
[0025]
图3是本实用新型实施例1竹筒的结构示意图。
[0026]
图4是图3中b处的局部剖视图。
[0027]
图5是本实用新型中弦向薄竹篾的成分结构示意图。
[0028]
图6是本实用新型中径向竹篾的成分结构示意图。
[0029]
图中各标号表示:1、竹篾帘层;2、木单板层;3、竹席层;4、浸渍纸层;5、竹筒;51、竹内节;52、竹黄;53、竹肉;54、竹青。
具体实施方式
[0030]
以下将结合说明书附图和具体实施例对本实用新型做进一步详细说明。除非特殊
说明,本实用新型采用的仪器或材料为市售。
[0031]
本实用新型的一种竹木胶合板,竹木胶合板由竹篾帘层1、木单板层2、竹席层3、浸渍纸层4胶合而成,竹篾帘层1两侧对称依次设置木单板层2、竹席层3和浸渍纸层4,竹篾帘层1由未去除竹青与竹黄的径向竹篾编织而成,竹席层3由去除竹青与竹黄的弦向竹篾经纬交织编织而成。本实用新型的竹席层3由弦向竹篾经纬交织编制而成,竹蔑帘层1由径向竹篾编制而成,竹席层3、竹篾帘1层和木单板层2三者在宏观孔隙结构、细观孔隙结构与微观孔隙结构上有明显差异,三者构成的多层交错结构具有更多维度的孔隙气流通道,在载荷热压过程中形成了多尺度缓冲效应,为热压过程水分向外迁移提供了更多的孔隙结构空间和时间,防止热进-热出工艺条件下因局部水分迁移受阻而蒸汽压力过大导致的鼓泡等缺陷,奠定了热进-热出热压成型工艺可行性的基础。
[0032]
木单板层2表面设有凹槽。凹槽有利于在木单板层2和竹席层3、竹篾帘层1之间形成全维度分布的胶钉结构,极大提高了木单板层2与竹席层3、竹帘层1的胶合性能。
[0033]
实施例1:
[0034]
本实施例的一种竹木胶合板的制备方法,包括以下步骤:
[0035]
(1)弦向薄竹篾和径向竹篾制备:选取6年生竹材,砍伐后截锯成竹筒5,竹筒5经剖竹机自动径向剖分后得到一定规格竹条。取一部分竹条将竹条去除竹内节51、竹青52、竹黄54,沿弦向(图4中c-c线所示方向)剖分成宽度20mm、厚度0.8mm的弦向薄竹篾(主要成分为竹肉53,如图5所示),用于编织竹席;另取一部分竹条,去除竹内节51,无需去除竹青52、竹黄54,直接沿径向(图4中d-d线所示方向)剖分成宽度8mm、厚度3mm的径向竹篾(主要成分包括竹黄52、竹肉53、竹青54,如图6所示),用于编织径向竹篾帘;
[0036]
(2)竹席和径向竹蔑帘制备:选取宽20mm、厚0.8mm的弦向薄竹篾,利用竹席编织机按经纬交织互穿编织成竹席,幅面尺寸根据产品要求。利用竹帘编织机将宽8mm、厚3mm的径向竹篾通过细棉线横拼成整张竹蔑帘,竹蔑帘厚度和长度分别为径向竹篾自身长度和厚度,宽度为多根径向竹篾横拼后的宽度,幅面尺寸根据产品要求;
[0037]
(3)木单板表面碾压刻蚀:利用刺钉辊筒碾压人工林速生材杨木单板,厚度2.2mm,初含水率60%,碾压后木单板表面布满圆孔状凹槽,凹槽直径0.6mm,凹痕深度0.3mm;
[0038]
(4)竹席、竹蔑帘、木单板干燥:将竹席、竹蔑帘、木单板含水率干燥至12%,干燥温度90℃;
[0039]
(5))竹席、竹蔑帘浸胶:采用浸胶方法对竹帘、竹蔑帘施胶,所用胶黏剂为酚醛树脂胶黏剂,固含量为45%,动力粘度40mpa
·
s,水溶倍数9倍,控制浸胶量为15%,浸胶后进行沥干处理;
[0040]
(6)木单板施胶:将厚度2.2mm的杨木单板进行双面涂胶,涂胶量300g/m2,所用胶黏剂为酚醛树脂胶黏剂,固含量45%,动力粘度200mpa
·
s,施胶后进行陈放处理;
[0041]
(7)竹帘、竹蔑帘二次干燥:将竹席、竹蔑帘进行二次干燥,干燥目标含水率为12%,干燥温度65℃;
[0042]
(8)铺装组坯:采用对称结构铺装,从上到下依次铺放三聚氰胺浸渍纸、竹席、木单板、径向竹篾帘、木单板、竹席、三聚氰胺浸渍纸,径向竹篾帘顺纹方向与木单板顺纹方向垂直;三聚氰胺浸渍纸厚度0.8mm,三聚氰胺含量为100%;
[0043]
(9)热压成型:采用热进-热出热压成型工艺。板坯完成组坯前,热压板提前升温,
热压板温度达到130℃时,将板坯放入热压机中,随后热压板立即闭合,在6mpa压力条件下保压,保压时间1.5min/mm,保压结束后分段降压,第一段从最高压力降至4mpa,第二段降至2mpa,第三段降至0,热压板打开,卸板,得到竹木胶合板毛边材;
[0044]
(10)裁边齐头:毛边材取出冷却后,利用裁边机将板材四边裁边齐头,得到竹木胶合板。
[0045]
取实施例1的杨木单板、竹帘、竹席分别按照实施例1的制备方法各自组坯热压成杨木胶合板、竹帘胶合板、竹席胶合板,并与实施例1的竹木胶合板进行性能检测。
[0046]
表1 竹木胶合板与其他板材性能对比
[0047][0048][0049]
实施例2:
[0050]
本实施例的一种竹木胶合板的制备方法,包括以下步骤:
[0051]
(1)弦向薄竹篾和径向竹篾制备:选取4年生竹材,砍伐后截锯成竹筒5,竹筒5经剖竹机自动径向剖分后得到一定规格竹条。将竹条除竹内节51、竹青52、竹黄54,沿弦向(图4中c-c线所示方向)剖分成宽度10mm、厚度0.5mm的弦向薄竹篾(主要成分为竹肉53,如图5所示),用于编织竹席;另取一部分竹条,去除竹内节51,无需去除竹青52、竹黄54,直接沿径向(图4中d-d线所示方向,如图6所示)剖分成宽度4mm、厚度1mm的径向竹篾(主要成分包括竹黄52、竹肉53、竹青54),用于编织径向竹篾帘;
[0052]
(2)竹席和径向竹蔑帘制备:选取宽10mm、厚0.5mm的弦向薄竹篾,利用竹席编织机按经纬交织互穿编织成竹席,幅面尺寸根据产品要求。利用竹帘编织机将宽4mm、厚1mm的径向竹篾通过细棉线横拼成整张竹蔑帘,竹蔑帘厚度和长度分别为径向竹篾自身长度和厚度,宽度为多根径向竹篾横拼后的宽度,幅面尺寸根据产品要求;
[0053]
(3)木单板表面碾压刻蚀:利用刺钉辊筒碾压人工林速生材桉木单板,厚度0.8mm,初含水率25%,碾压后木单板表面布满圆孔状凹槽,凹槽直径0.3mm,凹痕深度0.1mm;
[0054]
(4)竹席、竹蔑帘、木单板干燥:将竹席、竹蔑帘、木单板含水率干燥至8%,干燥温度45℃;
[0055]
(5)竹席、竹蔑帘浸胶:采用浸胶方法对竹席、竹蔑帘施胶,所用胶黏剂为中温快固酚醛树脂胶黏剂,固含量为25%,动力粘度25mpa
·
s,水溶倍数7倍,控制浸胶量为10%,浸胶后进行沥干处理;
[0056]
(6)木单板施胶:将厚度0.8mm的桉木单板进行双面涂胶,涂胶量150g/m2,所用胶黏剂为酚醛树脂胶黏剂,固含量35%,动力粘度125mpa
·
s,施胶后进行陈放处理;
[0057]
(7)竹席、竹蔑帘二次干燥:将竹席、竹蔑帘进行二次干燥,干燥目标含水率为5%,干燥温度45℃;
[0058]
(8)铺装组坯:采用对称结构铺装,从上到下依次铺放三聚氰胺浸渍纸、竹席、木单板、径向竹篾帘、木单板、竹席、三聚氰胺浸渍纸,径向竹篾帘顺纹方向与木单板顺纹方向垂直;三聚氰胺浸渍纸厚度0.8mm,三聚氰胺浸渍量为70%;
[0059]
(9)热压成型:采用热进-热出热压成型工艺。板坯完成组坯前,热压板提前升温,热压板温度达到110℃时,将板坯放入热压机中,随后热压板立即闭合,在3mpa压力条件下保压,保压时间0.8min/mm,保压结束后分段降压,第一段从最高压力降至2mpa,第二段降至1mpa,第三段降至0,热压板打开,卸板,得到竹木胶合板毛边材;
[0060]
(10)裁边齐头:毛边材取出冷却后,利用裁边机将板材四边裁边齐头,得到竹木胶合板。
[0061]
取实施例2的杨木单板、竹帘、竹席分别按照实施例2的制备方法各自组坯热压成杨木胶合板、竹帘胶合板、竹席胶合板,并与实施例2的竹木胶合板进行性能检测。
[0062]
表2 竹木胶合板与其他板材性能对比
[0063][0064]
虽然本实用新型已以较佳实施例揭示如上,然而并非用以限定本实用新型。任何熟悉本领域的技术人员,在不脱离本实用新型技术方案范围的情况下,都可利用上述揭示的技术内容对本实用新型技术方案做出许多可能的变动和修饰,或修改为等同变化的等效实施例。因此,凡是未脱离本实用新型技术方案的内容,依据本实用新型技术实质对以上实施例所做的任何简单修改、等同变化及修饰,均应落在本实用新型技术方案保护的范围内。