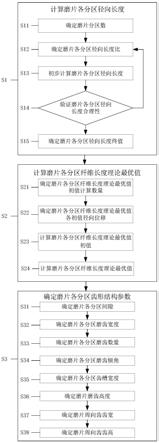
1.本发明涉及一种热磨机磨片设计方法,具体涉及一种基于纤维长度理论最优值的热磨机磨片设计方法,属于热磨机磨片设计技术领域。
背景技术:2.热磨机磨片是热磨机直接分离木纤维的关键部件,直接影响着纤维的分离质量和分离能耗。国外热磨机磨片生产厂商,对热磨理论研究较为深入,建立了完善的木材原料力学性能数据库,完全掌握了磨片齿形结构参数设置与研磨过程中木纤维几何形态变化之间的影响关系,形成了完善的热磨机磨片齿形结构参数设计理论,可针对纤维板厂的实际情况进行热磨机磨片的定制设计。他们根据纤维板生产厂原料的种类与配比,结合纤维板产品的实际用途要求,即对合格纤维的长度或直径尺寸的要求,能够设计出最适合的、符合纤维板厂现有热磨机使用的热磨机磨片齿形结构,使得磨片与该厂原料的匹配度最高,各研磨区研磨解离递进作用合理,磨片磨损均匀使用寿命长,生产的纤维合格率高,合格纤维的几何尺寸满足纤维板产品的实际用途要求,生产单位质量合格纤维消耗的能量低、成本低,大大增加了纤维产品的市场竞争力。
3.由于我国热磨机设备研究起步晚,各纤维板厂选择磨片的方式是根据自己厂里热磨机磨片的尺寸,在现有主流磨片中选择一款使用。所以存在不同地域的纤维板厂使用同一款热磨机磨片的现象,但是不同地域纤维板厂使用的木材原料的种类与配比相差较大。纤维板厂选择木材原料的主要原则是就近低成本原则,即主要以纤维板厂附近林场种植量大或运输便宜的树种为主,家具等木材产品加工后剩余的边角料等为辅,不同地域生产同一规格纤维板产品的人造板厂所用木材原料的种类与配比相差巨大。这导致不同纤维板厂生产同一规格纤维板产品所得到的合格纤维的质量参差不齐,纤维板产品的市场竞争力差,这也是我国纤维板产品很难走出国门的阻碍之一。
4.现有热磨机磨片齿形结构设计方法,主要是依据磨片齿形结构参数对纤维解离作用的影响,根据经验将各研磨区齿形结构参数机械的组合在一起,并且组合方式主要依据磨片的大小,没有考虑纤维板产品的实际用途要求,即没有将木材原料、磨片齿形结构参数设置、合格纤维几何尺寸之间建立有效的耦合对应关系;没有综合考虑磨片各研磨区研磨解离递进作用的合理性,忽略了磨片各研磨区齿形结构参数设置与纤维形态变化之间的匹配度;导致磨片各研磨区研磨解离递进作用不合理,致使磨片磨损极不均匀,极大的降低了磨片的使用寿命,且生产的纤维合格率低。因此,急需要一种可针对纤维板厂的实际情况和生产纤维产品的性能要求等条件进行热磨机磨片结构“量身”设计的热磨机磨片设计方法,以弥补现有设计方法的不足,提高纤维质量,延长磨片使用寿命,降低纤维板产品的生产成本,增加纤维板产品的市场竞争力。
技术实现要素:5.在下文中给出了关于本发明的简要概述,以便提供关于本发明的某些方面的基本
理解。应当理解,这个概述并不是关于本发明的穷举性概述。它并不是意图确定本发明的关键或重要部分,也不是意图限定本发明的范围。其目的仅仅是以简化的形式给出某些概念,以此作为稍后论述的更详细描述的前序。
6.鉴于此,针对现有设计磨片各研磨区研磨解离递进作用不合理,致使磨片磨损极不均匀,极大的降低了磨片的使用寿命,且生产的纤维合格率低的问题,本发明设计了一种基于纤维长度理论最优值的热磨机磨片设计方法,该设计方法能够根据纤维板厂的实际情况和纤维板产品的实际要求量身设计热磨机磨片,设计的磨片与纤维板厂木材原料匹配度高,磨片各研磨区研磨递进作用合理,磨片各研磨区磨损均匀、使用寿命长,生产的纤维合格率高。
7.为了实现上述目的,本发明的一种基于纤维长度理论最优值的热磨机磨片设计方法,具体步骤如下:
8.步骤1:计算磨片各分区径向长度
9.s11确定磨片分区数;
10.s12确定磨片各分区径向长度比;
11.s13初步计算磨片各分区径向长度;
12.s14验证磨片各分区径向长度合理性;
13.若磨片分区径向级差γ≥0,则磨片各分区径向长度分配合理;若磨片分区径向级差γ<0,则磨片各分区径向长度分配不合理,重复步骤s12~s14重新确定各分区径向长度;
14.s15确定磨片各分区径向长度终值;
15.步骤2:计算磨片各分区纤维长度理论最优值
16.s21确定磨片各分区纤维长度理论最优值初值计算数量;
17.s22确定磨片各分区纤维长度理论最优值各初值径向位移;
18.s23计算磨片各分区纤维长度理论最优值初值;
19.s24计算磨片各分区纤维长度理论最优值;
20.步骤3:确定磨片各分区齿形结构参数
21.s31确定磨片各分区间隙;
22.s32确定磨片各分区磨齿宽度;
23.s33确定磨片各分区磨齿数量;
24.s34确定磨片各分区磨齿倾角;
25.s35确定磨片各分区齿槽宽度;
26.s36确定磨片磨齿高度;
27.s37确定磨片周向齿齿宽;
28.s38确定磨片周向齿齿高。
29.进一步地:所述s11确定磨片分区数,具体为:
[0030][0031]
式中,q
f
四舍五入取整数,当q
f
≥4时,取q
f
=4,单位:个,d
w
为磨片外圆直径,单位:mm。
[0032]
进一步地:所述s12确定磨片各分区径向长度比,具体为:
[0033][0034]
式中,分别为从磨片外圆至内圆各分区的径向长度,单位:mm;分别为从磨片外圆至内圆各分区的径向长度所占比例值,均取整数,取值范围3~6。
[0035]
进一步地:所述s13初步计算磨片各分区径向长度,具体为:
[0036][0037]
式中,均取整数,单位:mm,d
n
为磨片內圆直径,单位:mm。
[0038]
进一步地:所述s14验证磨片各分区径向长度合理性,具体为:
[0039][0040]
式中,γ为磨片分区径向级差,若γ≥0,则磨片各分区径向长度分配合理;若γ<0,则磨片各分区径向长度分配不合理,重复步骤s12~s14重新确定各分区径向长度。
[0041]
进一步地:所述s15确定磨片各分区径向长度终值,具体为:
[0042][0043]
式中,l
fzi
为磨片第i分区径向长度终值,单位:mm。
[0044]
进一步地:所述s21确定磨片各分区纤维长度理论最优值初值计算数量,具体为:
[0045][0046]
式中,q
xwci
为磨片第i分区纤维长度理论最优值初值计算数量,q
xwci
四舍五入取整数,单位:个,当q
xwci
>5时,取q
xwci
=5。
[0047]
进一步地:所述s22确定磨片各分区纤维长度理论最优值各初值径向位移,具体为:
[0048][0049]
式中,l
mplij
为磨片第i分区第j纤维长度理论最优值初值径向位移,取整数,单位:mm,i=1、2、...、q
f
,j=1、2、...、q
xwci
,且令l
fz0
=0;η
i
为常整数,η
i
=5~10。
[0050]
进一步地:所述s23计算磨片各分区纤维长度理论最优值初值,具体为:
[0051][0052]
式中,l
xwlij
为磨片各分区径向位移为l
mplij
处的纤维长度理论最优值初值,单位:mm;l
yc
为木材原料最大线性尺寸均值,单位:mm,l
hg
为满足纤维板产品性能要求的合格纤维长度,单位:mm;σ
l
为磨片研磨强度。
[0053]
进一步地:所述s24计算磨片各分区纤维长度理论最优值,具体为:
[0054][0055]
式中,为磨片第i分区纤维长度理论最优值,单位:mm。
[0056]
进一步地:所述s31确定磨片各分区间隙,具体为:
[0057]
τ
i(i+1)
=δ
f(i+1) (i=1、2、...、q
f
‑1)
[0058]
式中,τ
i(i+1)
为磨片第i分区与第i+1分区之间的间隙,τ
i(i+1)
位于磨片第i分区内,当τ
i(i+1)
≥5时,取τ
i(i+1)
=5,单位:mm。
[0059]
进一步地:所述s32确定磨片各分区磨齿宽度,具体为:
[0060][0061]
式中,b
cki
为磨片第i分区磨齿宽度,四舍五入取整数,单位:mm;μ为齿宽系数,μ=0.4~0.9。
[0062]
进一步地:所述s33确定磨片各分区磨齿数量,具体为:
[0063][0064]
式中,n
i
为磨片第i分区磨齿数量,n
i
向最靠近能被6整除的整数方向取整,单位:个;λ
i
为区域系数,当i=1、2、...、q
f
‑
1时,λ
i
=1,当i=q
f
时,λ
i
=2。
[0065]
进一步地:所述s34确定磨片各分区磨齿倾角,具体为:
[0066][0067]
式中,α
i
为磨片第i分区磨齿倾角,四舍五入取整数,单位:度;ζ为磨齿倾角修正系数,ζ=
‑6°
~+6
°
。
[0068]
进一步地:所述s35确定磨片各分区齿槽宽度,具体为:
[0069][0070]
进一步地:所述s36确定磨片磨齿高度,具体为:
[0071][0072]
式中,h
mc
取整数,单位:mm;为齿高修正系数,单位:mm;
[0073]
进一步地:所述s37确定磨片周向齿齿宽,具体为:
[0074]
b
zcki
=b
cki (i=1、2、...、q
f
)。
[0075]
进一步地:所述s38确定磨片周向齿齿高,具体为:
[0076][0077]
式中,h
zmci
为磨片第i分区周向齿齿高,四舍五入保留一位小数,单位:mm。
[0078]
上述数值是作为本技术应用的一个例子,便于阐述本技术的控制方法和步骤,本技术的保护范围不限于以上数值范围。
[0079]
本发明所达到的效果为:
[0080]
(1)木材原料研磨解离过程中木材原料长度尺寸分解的变化规律完全由磨片齿形结构参数的设置决定。磨片性能的好坏直接体现在纤维形态变化规律的合理性上,即长度尺寸变化的合理性上。本发明的磨片设计方法根据磨片尺寸、磨片研磨强度、木材原料尺寸、纤维板产品要求合格纤维长度等,确定研磨过程中磨片各研磨区纤维长度尺寸的理论最优值,并以研磨过程中磨片各研磨区纤维长度尺寸的理论最优值为基础参数,结合磨片尺寸、磨片研磨强度、木材原料物理力学性质等推导出磨片各研磨区齿形结构参数。该设计方法将木材原料的力学性质和尺寸、磨片齿形结构参数设置和合格纤维几何尺寸之间建立了有效的耦合对应关系,设计的磨片齿形结构参数设置与研磨过程中纤维纵向分解形态变化规律匹配度高,磨片各研磨区递进作用合理。
[0081]
(2)本发明采用的磨片设计方法设计的磨片各研磨区都能将处于各研磨区的纤维研磨至适当的形态,各研磨区纤维形态变化合理,使得磨片各研磨区磨损均匀,磨片使用寿命长,研磨过程中能量消耗低,生产的纤维合格率高。
附图说明
[0082]
图1是本发明设计方法的流程图;
[0083]
图2是按照本发明设计方法设计出的磨片齿形结构示意图;
[0084]
图3是对比磨片结构示意图;
[0085]
图4是纤维长度对比图;
[0086]
图5是各类纤维占比图。
具体实施方式
[0087]
在下文中将结合附图对本发明的示范性实施例进行描述。为了清楚和简明起见,在说明书中并未描述实际实施方式的所有特征。然而,应该了解,在开发任何这种实际实施例的过程中必须做出很多特定于实施方式的决定,以便实现开发人员的具体目标,例如,符合与系统及业务相关的那些限制条件,并且这些限制条件可能会随着实施方式的不同而有所改变。此外,还应该了解,虽然开发工作有可能是非常复杂和费时的,但对得益于本发明公开内容的本领域技术人员来说,这种开发工作仅仅是例行的任务。
[0088]
本技术领域技术人员可以理解,除非另外定义,这里使用的所有术语(包括技术术语和科学术语)具有与本发明所属领域中的普通技术人员的一般理解相同的意义。还应该理解的是,诸如通用字典中定义的那些术语应该被理解为具有与现有技术的上下文中的意义一致的意义,并且除非像这里一样定义,不会用理想化或过于正式的含义来解释。
[0089]
在此,还需要说明的一点是,为了避免因不必要的细节而模糊了本发明,在附图中仅仅示出了与根据本发明的方案密切相关的装置结构和/或处理步骤,而省略了与本发明关系不大的其他细节。下面根据附图详细阐述本发明优选的实施方式。
[0090]
热磨机磨片配套于年产量20万m3的纤维板生产线,热磨机主电机功率4000kw,主轴转速1500r/min;热磨机原料为白松、杨木混合原料,其混合比例约为2:1,含有大约3%的树皮和少量硬杂木边角料,白松、杨木混合原料最大线性尺寸均值约为25mm,纤维板产品要求合格纤维长度均值为l
hg
=2.8mm;热磨机使用磨片尺寸为54英寸磨片,磨片外圆直径约1372mm,内圆直径约660mm,磨片研磨强度为1.863。
[0091]
设计步骤:
[0092]
结合图1,本实施例的热磨机磨片齿形结构设计方法,由以下步骤组成:
[0093]
一种基于纤维长度理论最优值的热磨机磨片设计方法,由以下步骤组成:
[0094]
s1:计算磨片各分区径向长度
[0095]
s11:确定磨片分区数:
[0096][0097]
式中,q
f
四舍五入取整数,当q
f
≥4时,取q
f
=4,单位:个,磨片外圆直径d
w
为1372mm;
[0098]
s12:确定磨片各分区径向长度比:
[0099]
l
f1
:l
f2
:l
f3
:l
f4
=δ
f1
:δ
f2
:δ
f3
:δ
f4
=4:3:3:5
[0100]
式中,l
f1
、l
f2
、l
f3
、l
f4
分别为从磨片外圆至内圆各分区的径向长度,单位:mm;δ
f1
、δ
f2
、δ
f3
、δ
f4
分别为从磨片外圆至内圆各分区的径向长度所占比例值,由于木材原料主要由白松和杨木组成,整体力学性能偏软,研磨解离强度适中,为了磨片各研磨区磨损均匀可适当增加破碎区和精磨区所占比例,故取δ
f1
=4,δ
f2
=3,δ
f3
=3,δ
f4
=5;
[0101]
s13:初步计算磨片各分区径向长度:
[0102]
[0103][0104][0105][0106]
式中,均取整数,单位:mm,磨片內圆直径d
n
为660mm;
[0107]
s14:验证磨片各分区径向长度合理性:
[0108][0109]
式中,磨片分区径向级差γ大于0,因此磨片各分区径向长度值分配合理;
[0110]
s15:确定磨片各分区径向长度终值:
[0111]
l
fz1
=95mm
[0112]
l
fz2
=70mm
[0113]
l
fz3
=70mm
[0114]
l
fz4
=121mm
[0115]
s2:计算磨片各分区纤维长度理论最优值
[0116]
s21:确定磨片各分区纤维长度理论最优值初值计算数量:
[0117][0118][0119][0120][0121]
s22:确定磨片各分区纤维长度理论最优值各初值径向位移:
[0122][0123][0124]
[0125][0126][0127][0128][0129][0130][0131][0132][0133][0134][0135][0136][0137][0138][0139][0140]
式中,l
mplij
为磨片第i分区第j纤维长度理论最优值初值径向位移,取整数,单位:
mm,i=1、2、...、q
f
,j=1、2、...、q
xwci
,且令l
fz0
=0;常整数η
i
根据磨片各分区径向长度所占比例关系进行取值,分别取η1=7、η2=5、η3=5、η4=8;
[0141]
s23:计算磨片各分区纤维长度理论最优值初值:
[0142][0143][0144][0145][0146][0147][0148][0149][0150][0151][0152][0153][0154][0155]
[0156][0157][0158][0159][0160]
式中,l
xwlij
为磨片各分区径向位移为l
mplij
处的纤维长度理论最优值初值,单位:mm;木材原料最大线性尺寸均值l
yc
为25mm,满足纤维板产品性能要求的合格纤维长度l
hg
为2.8mm,磨片研磨强度σ
l
为1.863;
[0161]
s24:计算磨片各分区纤维长度理论最优值:
[0162][0163][0164][0165][0166]
式中,为磨片第i分区纤维长度理论最优值,单位:mm;
[0167]
s3:确定磨片各分区齿形结构参数
[0168]
s31:确定磨片各分区间隙:
[0169]
τ
12
=δ
f2
=3mm
[0170]
τ
23
=δ
f3
=3mm
[0171]
τ
34
=δ
f4
=5mm
[0172]
式中,τ
i(i+1)
为磨片第i分区与第i+1分区之间的间隙,τ
i(i+1)
位于磨片第i分区内,当τ
i(i+1)
≥5时,取τ
i(i+1)
=5,单位:mm;
[0173]
s32:确定磨片各分区磨齿宽度:
[0174]
b
ck1
=0.6
×
1.863
×
3.773≈4.219≈4mm
[0175]
b
ck2
=0.6
×
1.863
×
6.34≈7.087≈7mm
[0176]
b
ck3
=0.6
×
1.863
×
8.508≈9.510≈10mm
[0177]
b
ck4
=0.6
×
1.863
×
11.41≈12.754≈13mm
[0178]
式中,b
cki
为磨片第i分区磨齿宽度,四舍五入取整数,单位:mm;由于本例虽然磨片尺寸较大,但木材原料力学强度低,因此μ可取中间偏大值,故μ取0.6;
[0179]
s33:确定磨片各分区磨齿数量:
[0180][0181][0182][0183][0184]
式中,n
i
为磨片第i分区磨齿数量,n
i
向最靠近能被6整除的整数方向取整,单位:个;λ
i
为区域系数,λ1=λ2=λ3=1,λ4=2;
[0185]
s34:确定磨片各分区磨齿倾角:
[0186]
α1=5
°
[0187][0188][0189][0190]
式中,α
i
为磨片第i分区磨齿倾角,四舍五入取整数,单位:度;ζ为磨齿倾角修正系数,综合考虑磨片尺寸和木材原料力学性能α1取中间值为5
°
,并且不需要对磨齿倾角进行修正,ζ=0
°
;
[0191]
s35:确定磨片各分区齿槽宽度:
[0192][0193][0194]
[0195][0196]
s36:确定磨片磨齿高度:
[0197]
h
mc
=4
×
1.863+0=7.452≈7mm
[0198]
式中,h
mc
取整数,单位:mm;为齿高修正系数,
[0199]
s37:确定磨片周向齿齿宽:
[0200]
b
zck1
=b
ck1
=4mm
[0201]
b
zck2
=b
ck2
=7mm
[0202]
b
zck3
=b
ck3
=10mm
[0203]
b
zck4
=b
ck4
=13mm
[0204]
s38:确定磨片周向齿齿高:
[0205]
h
zmc1
=h
zmc2
=h
zmc3
=7.0mm
[0206][0207]
式中,h
zmci
为磨片第i分区周向齿齿高,四舍五入保留一位小数,单位:mm;
[0208]
依照计算所得磨片结构参数绘制磨片结构示意图如图2所示。
[0209]
实验要求木材原料进入磨区之前经过水洗,去除木材原料里面的硬质颗粒等杂质,使原材料中没有其他杂质,以保证磨片能够正常磨损失效。
[0210]
在磨片正常磨损阶段,采集纤维样本,每副磨片采集200条纤维样本进行统计分析。根据设计要求满足纤维板力学性能要求的合格纤维长度为2.8mm,因此,以合格纤维长度的
±
20%作为纤维样本的筛分值将采集到的纤维样本分成三类,即:长纤维(>2.8
×
120%=3.36mm)、合格纤维(2.8
×
80%=2.24~2.8
×
120=3.36mm)和短纤维(<2.8
×
80%=2.24mm)。设计磨片(如图2所示)和对比磨片(如图3所示)生产纤维的统计结果如图4和图5所示。从统计结果可以看出,按照本设计方法设计的磨片生产的合格纤维长度的平均值为2.89mm,合格纤维样本数量占实验样本总数的83%,而对比磨片生产的合格纤维长度的平均值为3.05mm,合格纤维样本数量占实验样本总数的53%,可见设计磨片生产的纤维质量较高,且合格纤维的比例也较高。
[0211]
经实验验证本设计方法设计的磨片正常磨损失效的平均使用寿命约为26d,国内磨片平均使用寿命12d,磨片价格约为1.5万元/套([吴江,潘东杰,黄列群等.我国热磨机磨片的研究应用及发展[j].铸造技术,2015,36(10):2443
‑
2447.])。可见,本设计方法设计的磨片的正常磨损的平均使用寿命约为现有国产磨片的平均使用寿命长的2.17倍,则一年可以少更换磨片约16套,节约磨片采购费约16套
×
1.5万元/套=24万元;更换一套热磨机磨片的停机时间约为6h,则一年可减少停产更换磨片时间约16套
×
6h/套=96h,按每节省1h能产生利润约1.2万元,则每年节省时间的利润约为96h
×
1.2万元/h=115.2万元。
[0212]
以上实施例仅用于说明本发明的技术方案,而非对其限制;尽管参照上述各实施
例对本发明进行了详细的说明,本领域的普通技术人员应当理解:其依然可以对前述各实施例所记载的技术方案进行修改,或者对其中部分或者全部技术特征进行等同替换;而这些修改或者替换,并不使相应技术方案的本质脱离本发明实施例技术方案的范围。
[0213]
此外,应当理解,虽然本说明书按照实施方式加以描述,但并非每个实施方式仅包含一个独立的技术方案,说明书的这种叙述方式仅仅是为清楚起见,本领域技术人员应当将说明书作为一个整体,各实施例中的技术方案也可以经适当组合,形成本领域技术人员可以理解的其他实施方式。