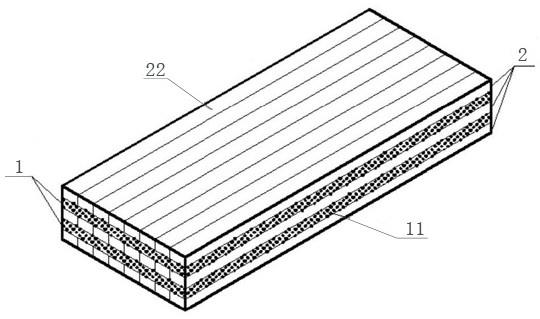
2.本发明属于一种竹木复合胶合材的制造方法及应用。
背景技术:3.我国竹资源面积、产量均居世界首位且竹资源培育和加工利用技术已属世界先进。目前,我国已形成了一个对竹资源由资源培育、加工、利用,出口贸易及生态旅游为一体的新产业。而我国木材资源匮乏,但我国速生人工林资源还较为丰富,因此充分发展我国竹资源和合理高效开发人工林速生木材资源是有效解决我国木材供需矛盾的重要途径。
4.竹材及竹产品具有强度高,韧性好等特点,而人工林速生材材质差,力学强度不高。通过竹木复合可以充分发挥各自的优势,因此发展竹木复合材料具有很大的市场潜力。我国在竹木复合产品研究和利用方面具有一定的基础,比较成熟的产品有竹木复合集装箱底板、竹木复合层积材、竹木复合地板及覆膜竹材胶合板等。但整体上看,在竹木复合结构、机械化加工程度及新产品开发方面还存在不足。
5.中国专利公开号cn1037675a介绍一种新型竹木复合人造板及制造方法,采用表面层由的细刨花或锯屑、竹席采用竹黄片编织、竹席位于表面层与芯层之间,芯层采用粗刨花铺装成均匀或渐变结构,表面层、竹席与芯层的中心面呈对称结构。但竹木复合结构单调,强度低。
6.中国专利公开号cn207789927u介绍一种竹木人造板,包括竹片层,竹片层上方从下往上依次设置有木片层、第一加固层、可延展层以及浸胶纸层,竹片层下方从上往下依次设置有第二加固层、消音层、防虫层、防潮层以及防水层;能够延长竹木人造板的使用寿命以及能够降低竹木人造板在使用的过程中与其它设备碰撞发出的声音的分呗,从而避免了噪声污染和对工作人员的听力的影响。但亦存在竹木复合结构单调,强度低,用途面窄的不足。
7.中国专利号201410091743.4介绍竹木复合板的卷装竹帘连续化自动铺装方法及其设备;方法包括竹材的采集,竹秆锯截, 破篾,竹篾筛分,木单板浸胶,卷装竹帘编织,干燥等步骤。设备包括竹篾称重装置、竹篾测厚装置、编卷帘装置和竹木连续制板装置。其中竹木连续制板装置包括机体、液压门架、卷筒轴、液压缸、电机、传输架、链条、压实门架、压实组轮、刀架和操作箱。本发明方法能有效控制竹木复合板的制造工艺,能有效避免的人工操作引起产品质量的下降,能制造出质量好和强度高的竹木复合板;该装置具有设计合理,结构简单,制作成本低,操作和维修方便,加载稳定精度高和生产效率好的优点。但亦存在竹木复合结构单调,强度低,用途面窄的不足且不能通过调整产品层数、尺寸等实现不同强度、多种幅面和用途的竹木复合胶合材,不能通过单元分级达到竹木复合胶合材的强度和尺寸稳定性。
技术实现要素:8.本发明的目的是设计一种竹木复合胶合材的制造方法及应用,能通过调整产品层
数及尺寸等实现不同强度,多种幅面和用途的竹木复合胶合材,能通过单元分级达到竹木复合胶合材的强度和尺寸稳定性。
9.为此, 一种竹木复合胶合材的结构是:竹木复合胶合材是由若干个主向层材和若干个次向层材上下相错、交替叠加拼装组坯、浸胶、压制固化所构成;主、次向层材上、下交替数层构成竹木复合胶合材;上、下相邻的主、次向层材交替设置且同向缝相错开设置;上、下相邻的主、次向层材交错呈20
°
~90
°
设置;竹木复合胶合材的层数为奇数,且至少为3层;竹木复合胶合材的上、下端面为次向层材,或为主向层材;木材单元或木质人造板材为次向层用材,同层的次向层的厚度相同;竹材及竹材人板材为主向层用材,同层的主向层的厚度相同;或:一种竹木复合胶合材的结构是:竹木复合胶合材是由若干个主次混合层材和若干个次主混合层材上下相错、交替叠加拼装组坯、浸胶、压制固化所构成;主次、次主混合层材上、下交替数层构成竹木复合胶合材;上、下相邻的主次、次主混合层材交替设置且同向缝相错开设置;上、下相邻的主次、次主混合层交错呈20
°
~90
°
设置;或主、次向层材与主次、次主混合层材上、下交替数层构成竹木复合胶合材;上、下相邻的主、次向层材与主次、次主混合层材交替设置且同向缝相错开设置;上、下相邻的主、次向层材与主次、次主混合层交错呈20
°
~90
°
设置;竹木复合胶合材的层数为奇数,且至少为3层;位于同层一组对应侧边的层材为木材单元或木质人造板材且竹材或竹材人板材与木材单元或木质人造板材在同层间隔设置为次主混合层用材,同层的次主混合层的厚度相同;位于同层一组对应侧边的层材为竹材单元或竹材人板材且竹材或竹材人板材与木材单元或木质人造板材在同层间隔设置为主次混合层用材,同层的主次混合层的厚度相同;一种竹木复合胶合材的制造方法,包括如下步骤: (1) 准备好次向层用材、主向层用材;(2)根据竹木复合胶合材产品的幅面和厚度需求:将次向层用材、主向层用材尺寸规则的单元分别进行定长、定宽、定厚加工,确保加工的精度,对于不规则单元,需保证其单元大小均匀;用于同层的次向层的厚度相同,同层的主向层的厚度相同,同层的次主混合层的厚度相同,同层的主次混合层的厚度相同;(3)基本构成单元的含水率控制:为了保证竹木复合胶合材的胶合质量,需要对各构成单元进行干燥以控制其含水率,对于基本加工单元,次向层用材干燥后的含水率控制在9~15%;主向层用材干燥后的含水率控制在5~11%;(4)基本构成单元的施胶:对于不规则单元的竹束,竹篾,竹帘及竹席,采用浸胶的方法进行施胶;而对于规则单元,采用涂胶或喷淋的方式施胶,侧面无需涂胶;将组成次向层材的木材单元或木质人造板材、组成主向层材的竹材单元或竹质人
min,加压时间60~90 min。施胶量为180~200 g/m2。
15.作为上述技术方案的进一步描述:所述的正交组坯时,相邻层的组坯单元的长度等于相邻层的组坯单元横向挤压后宽度。
16.作为上述技术方案的进一步描述:所述的将竹木复合板再装入压机是可根据胶粘剂种类和板材厚度选择加压方式,压力0.3~3mpa,固化温度5~140
°
c,时间20~90min。
17.作为上述技术方案的进一步描述:所述的组坯时同一层采用相同等级或质量单元,相邻层能根据设计的需要选择不同等级及质量的单元,能灵活调整各个构成单元在竹木复合胶合材中所占的比例,木材或木材人造板比例能为0%~100%,竹材或竹材人造板在竹木复合胶合材中的比例能为100%~0%。
18.作为上述技术方案的进一步描述:所述的竹木复合胶合材产品平行度板面对角线之差小于3.2 mm,垂直度相邻板角沿直线方向的偏差小于1.6 mm。
19.作为上述技术方案的进一步描述:用于但不限于家具、地板、集装箱底板,车厢板、建筑结构材、建筑装饰材。
20.一种竹木复合胶合材的用途是:用于但不限于家具、地板、集装箱底板,车厢板、建筑结构材、建筑装饰材。
21.上述结构和方法达到了本发明的目的。
22.(1) 、本发明充分发挥我国竹材、速生人工林木材资源优势,以传统竹、木材加工单元(木片、木刨花、木单板、实木锯材、竹材展平板、竹片、竹篾、竹束等),能通过调配单元类型和质量百分比,调整产品层数及尺寸等实现不同强度,多种幅面和用途正交竹木复合胶合材(cltb)的制造;能通过单元分级保证了竹木复合胶合材(cltb)的强度和尺寸稳定性。
23.(2) 、本发明改变了传统竹木复合材的组合方式和制备方法,为开发多种规格家具、地板等用非结构用材及集装箱底板,车厢板,建筑、桥梁等领域结构用材开辟了新的路径。
24.(3) 、本发明方法能提供一种竹木复合胶合材, 且能制造出质量好、制作成本低和不同用途强度高的竹木复合胶合材,且方法简单、实用。
附图说明
25.图1为本发明的正交组坯结构示意图;图2为本发明的正交组坯侧面结构示意图;图3为本发明的主次混合层材的结构示意图;图4为本发明的次主混合层材的结构示意图;图5为本发明的斜交组坯结构示意图;图6为本发明经正交组坯制成的产品结构示意图;图7为本发明的另一实施例产品的结构示意图;图8为本发明的另一实施例产品的结构示意图;图9为本发明的另一实施例产品的结构示意图;图10为本发明的另一实施例产品的结构示意图。
具体实施方式
26.下面将结合本发明实施例中的附图,对本发明实施例中的技术方案进行清楚、完整地描述,显然,所描述的实施例仅仅是本发明一部分实施例,而不是全部的实施例。基于本发明中的实施例,本领域普通技术人员在没有做出创造性劳动前提下所获得的所有其他实施例,都属于本发明保护的范围。下述实施例中的实验方法、结构和装置等,如无特殊说明,均为常规方法、结构和装置等,均可从商业途径得到。
27.实施例1:如图1、图2和图6所示,竹木复合胶合材是由若干个主向层材和若干个次向层材上下相错、交替叠加拼装组坯、浸胶、压制固化所构成。木材单元或木质人造板材22为次向层2用材,同层的次向层的厚度相同。竹材及竹材人板材11为主向层1用材,同层的主向层的厚度相同。
28.选长度2m、宽度10~30cm、厚2~5cm的木单板(为杨木、或柳木、或其它木制成),木单板的纤维纵长向为长度向,同层的木单板的厚度相同。选长度70~210cm、宽度3~30cm、厚1~2cm的竹人造单板,同层的竹人造单板的厚度相同,竹人造单板的纤维纵长向为长度向。
29.对各木单板和竹人造单板进行干燥,干燥后的各木单板含水率控制在10%;对干燥后的竹人造单板的含水率控制在10%。
30.选同厚度的7块木单板并排置在压机的组坯台上,各木单板两端对齐,相邻的木单板的侧面相互贴合,在相互贴合的木单板侧面上涂胶,胶为水溶性酚醛树脂胶粘剂,固体含量为54%,固化温度120~150℃;或为水溶性酚醛树脂为胶粘剂,固体含量为54%;或为单组分聚氨酯(pur):型号dh 106,浅棕色,使用温度为5℃~35℃,切变强度大于10 mpa,25℃时,其粘度为8000~20000 mpa.s,开放时间20~30 min,加压时间60~90 min。施胶量为180~200 g/m2。
31.选用单组分聚氨酯(pur):型号dh 106。形成位于底面的次向层材2;在底面的次向层材上端面涂胶,将各竹人造单板长度向与本单板的长度向垂直(90o) 设置,即上、下相邻的主、次向层材的长度向垂直呈90
°
设置;相邻的各竹人造单板的侧面相互贴合,在相互贴合的竹人造单板侧面上涂胶,各竹人造单板并排设置略大于下层次向层材的长度,形成位于中间的主向层材1;正交组坯时,相邻层的组坯单元的长度等于相邻层的组坯单元横向挤压后宽度。本实施例中各竹人造单板的长度向等于下层次向层材的横向挤压后宽度,若:下层次向层材的组坯完后横向宽度为180cm,涂胶挤压后横向宽度178cm,则位于下层次向层材上端的各竹人造单板的长度为178cm,组坯时竹人造单板的长度两端分别距下层次向层材宽度边等距(即1cm),以留出下层次向层材的涂胶挤压收缩量。各层依此类推,故不再累述。
32.各层依此类推,主、次向层材上、下交替奇数的数层;上、下相邻的主、次向层材交替设置且同向缝相错开设置;可形成如图1所示的从下至上依次为次向层材、主向层材、次向层材的三层正交竹木复合胶合材。如图2和图6所示的五层正交竹木复合胶合材,从下至上依次为次向层材、主向层材、次向层材、主向层材、次向层材构成。
33.而后,六面(上下、左右、前后)挤压粘合后的竹木复合胶合材,三层正交竹木复合胶合材的六面挤压压力0.3mpa,固化温度35
°
c,时间70分钟。
34.五层正交竹木复合胶合材的六面挤压压力1mpa,固化温度130
°
c,时间50分钟。
35.最后加工,将竹木复合胶合材裁边,得三层正交竹木复合胶合材;或五层正交竹木复合胶合材。竹木复合胶合材产品平行度板面对角线之差小于3.2 mm,垂直度相邻板角沿直线方向的偏差小于1.6 mm。
36.竹木复合胶合材产品用于但不限于家具、地板、集装箱底板,车厢板、建筑结构材、建筑装饰材。
37.实施例2:如图10所示,本实施例以侧拼型竹层板与杉木正交复合为例,采用侧拼型竹层板与人工林杉木锯材制作成三层结构竹木正交复合材(cross-laminated bamboo and timber,简称clbt),具体制作过程所涉及到的技术方案为:三层结构clbt,上、下层为侧拼型竹层板,中间为杉木锯材;侧拼型竹层板铺装方向为clbt板材的强轴方向,即主向层(longitudinal layer),杉木锯材铺装方向为clbt板材的弱轴方向,即次向层(cross layer),组坯时,相同层的单元具有相同的强度等级和规格尺寸。本实施例中三层结构的竹木正交复合clbt的生产过程,具体如下:选料:表、背层为侧拼型竹层板,芯层为人工林杉木锯材;刨光:对所选两种单元进行刨光,以去除灰尘和杂质,精刨后侧拼型竹层板的规格尺寸为:4000 mm
×
240 mm
×
15 mm(长
×
宽
×
厚),人工林杉木锯材的规格尺寸为:4000 mm
×
120 mm
×
25 mm(长
×
宽
×
厚);含水率控制:将所选两种单元的含水率调节至7~15%;选层:侧拼型竹层板作为clbt板材的强轴方向,即主向层(longitudinal layer),杉木锯材作为clbt板材的弱轴方向,即次向层(cross layer);施胶:结构用竹木正交复合材料选择结构用胶粘剂,本实施例中选用的水溶性酚醛树脂胶粘剂,施胶量为200g/m2,开放时间为20min,板材侧面不施胶;组坯:将经上述处理的侧拼型竹层板与人工林杉木正交组坯,组坯时注意侧拼型竹层板的长度方向为clbt的长度方向,人工林杉木的长度方向为clbt的宽度方向,竹层板长度方向与杉木长度方向呈90
°
;加压成型:采用正向和侧面同时加压的方式,具体为:正向加压,即压力垂直于clbt的上下表面,加压压力为0.6mpa,侧面压力即压力垂直于板材侧边所对应的面,加压压力为0.3mpa,加压时间为45min,温度120
°
c。而后修边。
38.通过以上工艺制作而成的三层竹木正交复合clbt ,其规格尺寸为:4000 mm
×
1200 mm
×
55 mm(长
×
宽
×
厚),上表面侧拼型竹层板精刨后的厚度为15 mm,横向层人工林杉木锯材厚度为25 mm,最底层侧拼型竹层板精刨后的厚度为15 mm,侧拼型竹层板在clbt厚度方向的占比约为54.54%。
39.本发明cltb制成的材料性能与人工速生林木材性能对比表:表1 基本单元物理力学性能(平均值)
表2 五种板材基本物理力学性能(平均值)表3 板材基本尺寸
测试结果表明:本发明的侧拼型竹层板与杉木正交复合后形成的竹木复合胶合材(clbt),其强轴方向(主方向)的静曲强度为45.90mpa,弹性模量为12.02gpa,抗压强度为37.45mpa,滚动剪切强度6.03mpa,浸渍剥离率小于5%;以相同人工林杉木锯材(厚度为25 mm)制备的3层结构正交胶合木,其规格尺寸为:4000 mm
×
1200 mm
×
75 mm(长
×
宽
×
厚),其强轴方向的静曲强度为40.01mpa,弹性模量为11.40gpa,抗压强度25.69mpa,滚动剪切强度3.58mpa。
40.可以看出,本发明与纯杉木锯材制备的正交胶合木相比,其强轴方向的静曲强度、弹性模量、抗压强度、滚动剪切强度分别提高了14.72%,5.4%,45.77% 68.44%。
41.实施例3:如图7所示,与实施例1不同的是:竹木复合胶合材的上、下端面为主向层材,图7所示的五层正交竹木复合胶合材,从下至上依次为主向层1材、次向层2材、主向层材、次向层材、主向层材构成。主向层材的纤维纵长向1b为竹木复合胶合材的长度向,次向层材的纤维纵长向2b为竹木复合胶合材的宽度向。
42.组坯时同一层采用相同等级或质量单元,相邻层能根据设计的需要选择不同等级及质量的单元,能灵活调整各个构成单元在竹木复合胶合材中所占的比例。若:木材单元或木材人造板比例能为100%时,为全木复合胶合材。若:竹材或竹材人造板在竹木复合胶合材中的比例能为100%时,为全竹复合胶合材。
43.其余相同,故不再累述。
44.实施例4:如图8所示,与实施例3不同的是:竹木复合胶合材的主向层材均为拼装的主向层材,拼装的主向层材的基本单元包括竹材展平板、竹片、竹篾、竹束、竹刨花, 还包括竹地板材,竹集成材,竹席胶合板,竹帘胶合板、竹重组材,竹刨花板及定向刨花板中的一种,或数种的组合。若主向层材均为拼装的主向层材时,与其配合的次向层材的宽度应较宽,以符合主、次向层材上、下交替数层构成竹木复合胶合材;上、下相邻的主、次向层材交替设置且同向缝相错开设置。其余相同,故不再累述。
45.图8所示的五层正交竹木复合胶合材,从下至上依次为主向层材、次向层材、主向层材、次向层材、主向层材构成。主向层材的纤维纵长向1b为竹木复合胶合材的长度向,次向层材的纤维纵长向2b为竹木复合胶合材的宽度向。
46.其余相同,故不再累述。
47.实施例5:与实施例1不同的是:实施例1为正交组坯,即上、下相邻的主、次向层材的长度向垂直呈90
°
设置。本实施例中竹木复合胶合材采用斜交组坯:即上、下相邻的主、次向层材的长度向夹角呈20
°
~89
°
设置,相隔的主向层材或次向层材的斜度相同。主、次向层材上、下交替构成至少为3层的奇数层;上、下相邻的主、次向层材的同向缝相错开设置。
48.其余相同,故不再累述。
49.实施例6:如图3至图4所示,与实施例1不同的是:竹木复合胶合材的同层组坯单元
可采用:同层一组对应侧边的层材为木材单元或木质人造板材且竹材或竹材人板材与木材单元或木质人造板材22在同层间隔设置为次主混合层21用材,同层的次主混合层21的厚度相同;位于同层一组对应侧边的层材为竹材单元或竹材人板11材且竹材或竹材人板材与木材单元或木质人造板材在同层间隔设置为主次混合层12用材,同层的主次混合层12的厚度相同。
50.竹木复合胶合材是由若干个主次混合层材和若干个次主混合层材上下相错、交替叠加拼装组坯、浸胶、压制固化所构成;主次、次主混合层材上、下交替数层构成竹木复合胶合材;上、下相邻的主次、次主混合层材交替设置且同向缝相错开设置;上、下相邻的主次、次主混合层交错呈20
°
~90
°
设置。
51.其余相同,故不再累述。
52.实施例7:如图5所示,与实施例1、 5、6不同的是:混合组坯为:主向层材与主次、次主混合层材上、下交替构成至少为3层的奇数层;上、下相邻的主向层材与主次、次主混合层材同向缝相错开设置;上、下相邻的主向层材与主次、次主混合层材交错呈20
°
~90
°
设置;竹木复合胶合材的上、下端面为主向层材或为次向层材;或次向层材与主次、次主混合层材上、下交替构成至少为3层的奇数层;上、下相邻的次向层材与主次、次主混合层材同向缝相错开设置;上、下相邻的次向层材与主次、次主混合层材交错呈20
°
~90
°
设置。
53.即:主、次向层材与主次、次主混合层材上、下交替数层构成竹木复合胶合材;如:竹木复合胶合材从下至上依次为主向层、主次混合层12、主向层、主次混合层12、主向层。或再如:竹木复合胶合材从下至上依次为次向层、主次混合层12、次向层2、主次混合层12、次向层2。依此类推为主向层1、次向层2、主次混合层12、次主混合层21的任选所需不同层的组合。
54.如图5所示,同层的主次、次主混合层材可以斜置,但上、下相隔层的主次、次主混合层材的夹角相同,上、下相邻层的斜度相反。其余相同,故不再累述。
55.实施例7:如图9所示,与上述各实施例不同的是:可在竹木复合胶合材的上、下端面至少一端面胶粘装饰板3。装饰板为用木、或竹、或合成塑料、或金属制成的装饰板,装饰板3是在组坯时粘合在组坯时的竹木复合胶合材的上、下端面,而后加压成型。其余相同,故不再累述。
56.以上显示和描述了本发明的基本原理、主要特征和本发明的优点。本行业的技术人员应该了解,本发明不受上述实施例的限制,上述实施例和说明书中描述的仅为本发明的优选例,并不用来限制本发明,在不脱离本发明精神和范围的前提下,本发明还会有各种变化和改进,这些变化和改进都落入要求保护的本发明范围内。本发明要求保护范围由所附的权利要求书及其等效物界定。