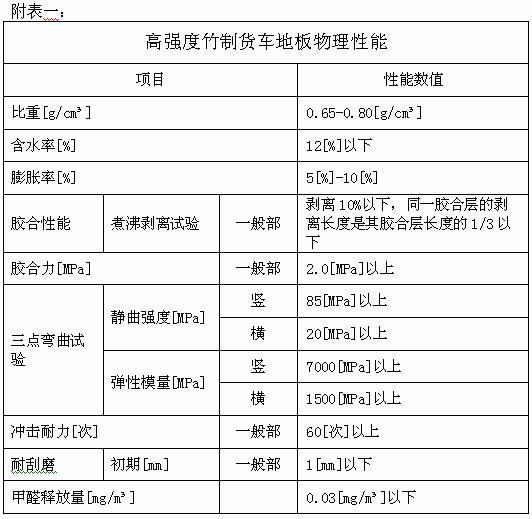
1.本发明涉及一种货车地板制造工艺及其产品,尤其是具有高强度竹制货车地板的制造方法及其产品。
背景技术:2.竹子是世界上生长最快的植物之一。研究显示,竹子的最高生长速度是每24小时可长1.21米,2-3个月即可完成高生长和粗生长。竹子成熟快,3-5年即可成林,且年年出笋长新竹,产量高,一次造林,可永续利用。竹子分布广泛,资源规模可观。全球已知竹类植物1642种,已知有39个国家竹林面积总计5000万公顷以上,年产竹材超过6亿吨。其中,中国有竹类植物800多种,采用竹材制板不但环保,而且原料来源广泛、价格低廉。
3.货车厢板或地板一般由面层、夹心层构成,如,cn201510655393.4公开了一种用于厢式货车的一次成型车厢板及制造工艺,该车厢板外层材料为玻璃钢,采用pvc泡沫板作为夹心层,该工艺包括以下步骤:1)脱模材料处理,常温固化;2)将表面毡、复合毡、pvc泡沫板、导流复合毡铺设;3)固定ω管和缠绕管、粘贴密封胶条、铺设脱模布和真空袋构成真空系统;4)将真空系统与树脂收集器密封连接,检测真空系统的密封性;5)真空保压;6)配置树脂,真空灌注;7)固化、脱模、后处理。与现有技术相比,本发明使用pvc泡沫板作为夹心层,具有防水、阻燃、耐酸碱、防蛀、质轻、硬度高、保温、隔音、减震的优点,真空导入一次成型,产品两面光滑。
4.cn202010238137.6本发明属于车厢板的制备技术领域,公开一种轻量化车厢板及其制备方法。包括第一面板层、第二面板层、夹芯层、骨架支撑层,所述夹芯层设置在第一面板层与第二面板层之间,夹芯层由若干个泡沫块相互拼接而成,夹心层和第一面板层之间、夹心层和第二面板层之间、夹心层的四周边缘以及夹心层中任意两个相邻泡沫块的拼接缝中一体成型填充有骨架支撑层,骨架支撑层与第一面板层、第二面板层一体成型。制备步骤如下:铺层、密封、配制胶液、注胶、固化、脱模,即得轻量化车厢板。本发明采用一体固化成型的方法,得到纤维增强树脂复合材料面板的同时在泡沫夹心层之间形成骨架支撑层,制备的车厢板,轻质保温,力学性能大大提高。
5.cn201520551206.3该实用新型涉及一种燕尾榫紧固结构车厢板,包括车厢板本体,车厢板本体包括两层玻璃钢板和轻质基础层,轻质基础层上设置有若干燕尾榫结构,上下两层玻璃钢板中设置榫槽,车厢板本体的拐角连接有中空的车厢板加强角,将车厢板本体的拐角增设车厢板加强角,克服车厢板边框因为板材太薄无法焊接、或者铰链连接处强度不够的缺陷,以轻质酚醛胶合板为基础结构层,以玻璃钢板为表面防护层,均为轻质环保材料,无污染,且对车体的载荷小,酚醛胶合板与玻璃钢板通过燕尾榫结构固定,结构稳固,具有较高的强度,抗冲击稳定性好,耐候性好,抗腐蚀,使用寿命长,在玻璃钢板外表面涂敷胶衣层,使本实用新型更美观、耐用。
6.cn202111611140.9本发明公开了一种车厢板,包括多个首尾相拼接的厢板单元,所述厢板单元包括板体部、第一拼接端和第二拼接端,所述第一拼接端和第二拼接端分别
设于所述板体部的两侧,相邻两单厢板单元,一厢板单元的第一拼接端与另一厢板单元的第二拼接端连接;其中,所述第一拼接端包括外插边、设有扣合空间的扣合槽和内接边,所述第二拼接端包括用于与所述内接边连接的内搭边、设有插接空间的插槽和扣合边,所述外插边设有插入所述插槽的插头,所述扣合边设有扣入所述扣合槽内的扣合端,所述插槽和扣合槽内还设有用于灌胶的灌胶空间,相应地还公开了一种车厢板的生产工艺。采用本发明,结构简单,防水性好,且组装工序简易。
7.cn204748815u实用新型专利涉及一种无胶拼接式车厢板,包括基板和具有防火功能的面板,面板上的每块竹片两端一定距离处均开有通孔,通孔内设置有连接轴,连接轴的一端设置有挡块,另一端设置有螺纹,螺纹上设置有螺帽,面板上的头尾两块竹片上均设置有相对应的凹槽,凹槽与竹片的通孔相对应,挡块和螺帽处在所述的凹槽内,通过这种方式就不需要在面板的竹条之间通过胶水固定,可以环保,并且牢固,基板表面开设有纵横贯通的向内凹的排气槽,达到解决具有防火功能的面板开胶鼓泡的目的,减少损失,提高经济效益,两端板采用纤维板,防裂纤维板粘合强度比竹地板粘合强度高,可以更好的使车厢板固定不容易开裂。
8.cn204748816u该实用新型涉及一种竹胶拼接式车厢板,包括车厢板本体,车厢板本体包括基板和具有防火功能的面板,车厢板本体的拐角连接有中空的车厢板加强角,基板表面开设有纵横贯通的向内凹的排气槽,排气槽处于基板和面板之间的位置,基板包括中层板和两端板,基板下表面设有卡槽,卡槽内设置有加强筋,面板表层设有一层聚氨酯树脂混合耐酸耐碱涂层,由于在基板表面开设有纵横贯通的向内凹的排气槽,达到解决具有防火功能的面板开胶鼓泡的目的,减少损失,提高经济效益,两端板采用纤维板,防裂纤维板粘合强度比竹片粘合强度高,可以更好的使车厢板固定不容易开裂。
9.cn112518913a涉及一种竹木复合板的加工方法及竹木复合板,属于竹材利用技术领域。一种竹木复合板的加工方法,其特征在于,将竹材等分成至少两半的竹板,将竹板的内弧面与外弧面加工去除竹节,可以采用铣或者刨的方式,使竹节处平滑,没有明显的凸起,将内弧面的半径与外弧面的半径加工成同半径,为了保证竹子的使用率,半径的长度为外弧面半径;在旋切木皮两侧刷胶,将两片竹板之间加一层旋切木皮进行拼压。通过上述的方法,加工出一种竹木复合板。本技术的方法加工的竹木复合板,对竹材的利用率提高。
10.cn107053366a本发明公开了一种留青竹木复合板,包括单面结构和双面结构,单面结构由留青竹板和细工木板胶合而成,双面结构由两块留青竹板和其间细工木板胶合而成,留青竹板外表面为竹青面,竹青面保持着一层天然竹青。此留青竹木复合板不仅保持留青竹板原有的高硬度、高强度、良好的耐磨性及耐腐蚀性,而且保留留青竹板竹青。本发明公开了一种留青竹木复合板加工工艺:选材,锯断,去外节,去内节,开口,软化,展平,定厚去黄,冷却定型,低温烘干,与细木工板粘合形成留青竹木复合板单元,拼接、粘合留青竹木复合板单元组成留青竹木复合板。此加工工艺过程中,毛竹软化无污染,留青竹板烘干过程中不变形,不开裂,竹青面保持了高的硬度、平整度、光滑度。
11.cn107053366b本发明公开了一种留青竹木复合板,包括单面结构和双面结构,单面结构由留青竹板和细工木板胶合而成,双面结构由两块留青竹板和其间细工木板胶合而成,留青竹板外表面为竹青面,竹青面保持着一层天然竹青。此留青竹木复合板不仅保持留青竹板原有的高硬度、高强度、良好的耐磨性及耐腐蚀性,而且保留留青竹板竹青。本发明
公开了一种留青竹木复合板加工工艺:选材,锯断,去外节,去内节,开口,软化,展平,定厚去黄,冷却定型,低温烘干,与细木工板粘合形成留青竹木复合板单元,拼接、粘合留青竹木复合板单元组成留青竹木复合板。此加工工艺过程中,毛竹软化无污染,留青竹板烘干过程中不变形,不开裂,竹青面保持了高的硬度、平整度、光滑度。
技术实现要素:12.本发明目的在于:提供一种高强度竹制货车地板制造工艺。
13.本发明的再一目的在于:提供上述工艺得到的产品。
14.本发明目的通过下述方案实现:一种货车地板制造工艺,以竹为原料,包括开片、接长、成型,至少采用下述步骤:步骤一,原料选择:釆用竹龄不少于4年,直径不小于50mm的毛竹;步骤二,开片:将选取的毛竹截成500-6000mm长度的毛竹段,通过开片机将毛竹段开成等宽的竹片2-4片,收集竹片和竹屑;或者/和,将选取的毛竹截成1050-2050mm长度的毛竹段,通过开片机开成宽度为15-24mm的竹胚条,收集竹胚条和竹屑,步骤三,将长度500-6000mm的竹片通过碾压工序展开,去掉竹青、竹黄、定厚,收集竹片和竹屑;或者,将长1050-2050mm、宽15-24mm的竹胚条用粗刨机进行刨去竹青、竹黄,得到竹条,收集竹条和竹屑,竹条编织竹帘;步骤四,将步骤二和步骤三得到的竹屑及残次品竹片和残次品竹条粉碎,得粉末颗粒状的竹粉;步骤五,将竹片、竹条、编织竹帘和竹粉进行干燥,至含水率8-12%;步骤六,将干燥处理的竹片和竹条进行接长部位加工,在接长部形成鎨形、齿形或斜面;步骤七,把干燥好的竹粉和胶粘剂按照1000克竹粉和(400-700)克胶粘剂,分别倒入搅拌机进行搅拌均匀,得竹粉胶,备用;步骤八,将干燥好的竹片和竹条实行两面或者四面施胶粘剂,或者,竹条编织竹帘浸泡在胶粘剂中施胶;步骤九,将施好胶的l500-6000mm的竹片,至少2片往宽度方向进行排列,釆用施好胶沾剂的宽为20-50mm的棉布带,使用树脂钉或其他钉子固定在竹片上;或者,采用无线或有线编织的方法排列连成n片适合生产操作尺寸的组合竹片;或者,将施好胶的l1050-2050mm竹条,至少2根以上的竹条往宽度方向进行排列,釆用无线或有线错位编织的接长或者采用其他接长技术把竹条连接成适合生产操作尺寸的帘状竹条;步骤十,竹胚组合,自下而上依序包括:先铺上底表层为酚醛树脂、三聚氰氨类覆膜材料或2mm以上的侧压单板,作为底层;第二层铺上施好胶粘剂的编织竹帘层;第三层铺上组合竹片或帘状竹条;第四层为横或纵方向铺上组合竹片、帘状竹条或2.5mm以上的木质缓冲层、玻璃纤维或编织竹帘,第五层同第三层,第六层同第二层,第七层面表层酚醛树脂、三聚氰氨类覆膜材料或2mm以上的侧压单板,得到不少于七层的竹板半成品;步骤十一,根据产品表面的防滑或不防滑要求,竹板半成品,经过130-160度的温
度,20-40kg/cm2的压力,一次性热压成型,得到高强度的竹制货车地板。
15.本发明在竹片通过碾压式展开加工和竹条通过粗刨机加工时,均已刨去表面的竹青和竹黄,特别是该粗刨竹条,不再需要像传统工艺,通过精刨机器二次进行精准定宽定厚,直接将以上的竹片和粗刨竹条用于该产品的生产制造,将材料利用率提高至90%以上。组合竹片或帘状竹条制备不需要更换企业现有设备,而且强度和支撑性也得到保证。
16.在上述方案基础上,可以对步骤二或步骤三所得的竹片或竹条进行脱脂处理。
17.在上述方案基础上,可以对步骤二或步骤三所得竹片或竹条进行防腐处理。
18.其步骤五的干燥温度控制在50-70℃,至竹片、竹条、竹粉和编织竹帘的含水率8-12%。
19.为达产品的厚度要求,步骤十中,根据产品的厚度重复增加第三、四和五层三层的结构层次。
20.进一步的,对于厚度规格要求严格的货车地板,在步骤十中,将施好胶粘剂的竹粉胶可分别铺设在第三、四和五层中,通过上述方式以及釆用塑料树脂钉或者固定件(如软质铝钉等)固定组合,得到l2000-10000*w140-2100*t12-50mm尺寸的半成品。不但可以通过施胶调整地板材,而且在降低成本的同时保证了强度要求。
21.步骤十一中,所得的高强度竹板可以经过切、锯、刨、打孔等深加工,制作成尺寸为长2000-10000x宽140-2200x高12-50mm规格的高强度竹制货车地板成品。
22.另外,步骤十中,第二层和第六层的编织竹帘可以用厚度为1-2.5mm的木质缓冲层代替。
23.本发明还提供了一种高强度竹制的货车地板,是根据上述任一制造工艺得到的。
24.所述的地板,自下而上依序包括:底表层为酚醛树脂、三聚氰氨类覆膜材料或2mm以上的侧压单板的底层;施好胶粘剂的编织竹帘的第二层;第三层组合竹片或帘状竹条作为骨架结构的第三层;第四层为横或纵方向铺上组合竹片、帘状竹条;第五层同第三层,第六层同第二层,面表层酚醛树脂、三聚氰氨类覆膜材料或2mm以上的侧压单板的第七层。
25.本发明中,在第三、第四间,以及第四层和第五层间可以采用竹粉胶层或者增加施好胶粘剂的编织竹帘作为层间缓冲层及高度调整层,以达到产品厚度的精准控制。
26.本发明最大限度的利用了竹材原料,通过碾压式展开加工和竹条粗刨机加工,均已刨去表面的竹青和竹黄,省去了精刨工序,直接将以上的竹片和粗刨竹条用于本发明产品的生产制造,将材料利用率提高至90%以上。本发明方法所制造的货车地板缓冲层采用编织竹帘,利用竹片不但可以保证强度也最大限度的利用了竹资源;利用组合竹片或者帘状竹条作为骨架结构很好的保证了强度,且无需投入新的设备。
27.竹制品在整个生命周期都保持低碳水平。竹产品与塑料产品相比,碳足迹为负值。竹制品使用后可完全自然降解,更好地保护环境,保护人类健康。原料来源易得,且稳定。
附图说明
28.图1,步骤二中竹片的结构示意图;图2,步骤二中竹胚条的结构示意图;图3,步骤三中竹片经碾压展开示意图;图4,竹片和竹条接长部位结构示意图;
图5,组合竹片示意图;图6,帘状竹条示意图;图7,竹胚组合示意图;图8,强度竹制货车地板示意图。
具体实施方式
29.实施例1一种货车地板,以竹为原料,包括开片、成型,采用下述步骤:步骤一,原料选择:釆用竹龄不少于4年,直径不小于50mm的毛竹,长度不限;步骤二,开片:根据毛竹的最佳利用率将选取的毛竹截成500-6000mm长度的毛竹段,通过开片机将毛竹段开成等宽的竹片2-4片,收集竹片和竹屑;或者,将选取的毛竹截成1050-2050mm长度的毛竹段,通过专用开片机开成宽度为15-24mm的竹胚条(普遍加工工艺为竹条),见图1和见图2所示,分别收集竹胚条、竹屑;步骤三,将长度500-6000mm同等宽度的竹片通过专用的机器进行碾压式展开,此工艺展开竹片的同时去掉竹青、竹黄、定厚,见图3所示,收集竹片和竹屑;或者,将长1050-2050mm、宽15-24mm的竹胚条采用专用的粗刨机刨去竹青、竹黄,该粗刨竹条统称为竹条,收集竹条和竹屑;步骤四,将步骤二和步骤三通过机器加工产生的竹屑及残次品竹片和竹条粉碎,得粉末颗粒状的竹粉;在此,可以对竹片或竹条进行脱脂或者不进行脱脂处理,进行防腐或者不进行防腐处理;步骤五,将竹片、竹条、编织竹帘和竹粉分别进行干燥,温度控制在50-70℃,干燥之后含水率8-12%;步骤六,根据产品尺寸,将干燥处理的竹片和竹条进行接长部位加工,在接长部形成鎨形(图4-1)、齿形(图4-2)或斜面(图4-3);步骤七,把以上干燥好的竹粉和胶粘剂按照1000克竹粉和(400-700)克胶粘剂,分别倒入搅拌机进行搅拌均匀,得竹粉胶,备用;步骤八,将以上干燥好的竹片和竹条实行两面或者四面施胶粘剂,竹条编织竹帘浸泡在胶粘剂中施胶;步骤九,将施好胶的l500-6000mm的竹片,根据产品规格要求,至少2片往宽度方向进行排列,釆用施好胶粘剂的宽为20-50mm的棉布带,用树脂钉(或其他不会对热压模具造成损伤的铝质钉子等固定件)固定在竹片上制备组合竹片(图5-1);或者,采用无线或有线编织的方法排列连成n片适合生产操作尺寸的组合竹片(见图5-2);或者,将施好胶的l1050-2050mm竹条,至少2根以上的竹条往宽度方向进行排列,釆用无线或有线错位编织的接长或者采用其他接长技术把竹条连接成适合生产操作尺寸的帘状竹条,其中,如图6-1所示,竹条采用齿形接长,采用有线错位编织的帘状竹条;如图6-2竹条采用斜面接长,用有线错位编织的帘状竹条;如图6-3竹条采用鎨形接长技术,有线编织的帘状竹条;
步骤十,根据产品使用要求以及尺寸要求进行如下竹胚组合步骤,自下而上依序包括:先铺上底表层为酚醛树脂、三聚氰氨类覆膜材料或2mm以上的侧压单板,作为底层1;在底层1上铺上施好胶粘剂的编织竹帘作为第二层2;第三层3为骨架结构层,铺上组合竹片或帘状竹条;第四层4为与第三层不同排列,如横或纵方向排列的组合竹片、帘状竹条;第五层5同第三层3,第六层6同第二层2,第七层7为表层,为表层有酚醛树脂、三聚氰氨类覆膜材料或2mm以上的侧压单板;其中,在第三层3、第四层4和第五层5上施加得竹粉胶,得到l2000-10000*w140-2100*t12-50mm尺寸的货车竹地板半成品(见图7a);步骤十一,根据产品表面的防滑或不防滑要求,将半成品在130-160℃的温度下,于20-40kg/cm2的压力下一次性热压成型,经过或不经过冷却处理,得高强度竹板。
30.根据产品的厚度要求,也可重复增加第三、四、五层等三层的结构层次,即能达到需要产品的厚度,同时为了组合竹片或帘状竹条之间的粘合紧密度、增加组合竹片、编织竹帘或帘状竹条的厚度,以及提高产品强度,将施好胶粘剂的竹粉分别铺设在第三、四、五层中。
31.可以对步骤十一得到的高强度竹板经过自动智能化设备加工完成切、锯、刨、打孔等深加工,制作成成品尺寸为l2000-10000xw140-2200xt12-50mm高强度竹制货车地板产品(见图8a),产品性能见表1。
32.以上高强度竹制货车地板釆用直径50mm以上的毛竹,该工艺解决竹材行业成本居高不下的难题,成本低、密度轻,强度强、竹粉得到了充分的利用,变废为宝,生产周期短等优点,省去了过去专门去竹节、去青、去黃的等工序,通过本实施例制造的竹制货车地板物理性能见附表一,本发明以竹代木,解决了只能生产侧压产品的传统工艺难题。
33.所制造的高强度竹板性能优异。
34.实施例2一种货车地板,与实施例步骤近似,只是第三层和第五层均采用帘状竹条,第四层采用组合竹片,按下述步骤制造:步骤一,原料选择:釆用竹龄不少于4年,直径不小于50mm的毛竹,长度不限;步骤二,开片:根据毛竹的最佳利用率将选取的毛竹截成500-6000mm长度的毛竹段,通过开片机将毛竹段开成等宽的竹片2-4片,收集竹片和竹屑;或者,将选取的毛竹截成1050-2050mm长度的毛竹段,通过专用开片机开成宽度为15-24mm的竹胚条(普遍加工工艺为竹条)(见图1)(见图2),收集竹胚条和竹屑;步骤三,将长度500-6000mm同等宽度的竹片通过专用的机器进行碾压式展开,此工艺展开竹片的同时去掉竹青、竹黄、定厚(见图3),收集竹片和竹屑;或者,将长1050-2050mm、宽15-24mm的竹胚条采用专用的粗刨机刨去竹青、竹黄,该粗刨竹条统称为竹条,收集竹条和竹屑;步骤四,将步骤二和步骤三通过机器加工产生的竹屑及残次品竹片和竹条粉碎,得粉末颗粒状的竹粉;在此,可以对竹片或竹条进行脱脂或者不进行脱脂处理,进行防腐或者不进行防腐处理;
步骤五,将竹片、竹条、编织竹帘和竹粉分别进行干燥,温度控制在50-70℃,干燥之后含水率8-12%;步骤六,根据产品尺寸,将干燥处理的竹片和竹条进行接长部位加工,在接长部形成鎨形(如图4-1)、齿形(如图4-2)或斜面(如图4-3);步骤七,把以上干燥好的竹粉和胶粘剂按照1000克竹粉和(400-700)克胶粘剂,分别倒入搅拌机进行搅拌均匀,得竹粉胶,备用;步骤八,将以上干燥好的竹片和竹条实行两面或者四面施胶粘剂,编织竹帘浸泡在胶粘剂中施胶;步骤九,将施好胶的l500-6000mm的竹片,至少2片往宽度方向进行排列,釆用施好胶粘剂的宽为20-50mm的棉布带,使用树脂钉或其他钉子固定在竹片上(图5-1);或者,采用无线或有线编织的方法排列连成n片适合生产操作尺寸的组合竹片(见图5-2);或者,将施好胶的l1050-2050mm竹条,至少2根以上的竹条往宽度方向进行排列,釆用无线或有线错位编织的接长或者采用其他接长技术把竹条连接成适合生产操作尺寸的帘状竹条(见图6);步骤十,根据产品使用要求以及尺寸要求进行如下步骤组胚组合竹胚组合,自下而上依序包括:先铺上底表层为酚醛树脂、三聚氰氨类覆膜材料或2mm以上的侧压单板,作为底层1;第二层2铺上施好胶粘剂的厚度为1-2.5mm的木质缓冲层或编织竹帘;第三层3’铺上帘状竹条;第四层4’为横或纵方向帘状竹条,即与第三层排列方向垂直;第五层5’同第三层,第六层6同第二层,第七层7表层酚醛树脂、三聚氰氨类覆膜材料或2mm以上的侧压单板,得到l2000-10000*w140-2100*t12-50mm尺寸的竹板半成品(见图7b);步骤十一,根据产品表面的防滑或不防滑要求,将半成品在130-160℃的温度下,于20-40kg/cm2的压力下一次性热压成型,经过或不经过冷却处理,得高强度竹板。
35.根据产品的厚度要求,可重复增加第三、四、五层等三层的结构层次,即能达到需要产品的厚度,同时为了帘状竹条之间的粘合紧密度、保证产品厚度规格,增加了编织竹帘,并将竹粉胶分别铺设在第三、四、五层中。
36.对步骤十一得到的高强度竹板经过自动智能化设备加工完成切、锯、刨、打孔等深加工,制作成成品尺寸r 高强度竹制货车地板产品,见图8b,产品性能也能满足要求。
37.其中,步骤二或步骤三得到的竹片或竹条可以进行脱脂处理及防腐处理,以增加本实施例所得产品的使用寿命和结构稳定性。
38.实施例3本实施例与实施例1步骤近似,只是第三层和第五层均采用组合竹片,第四层采用帘状竹条,按下述步骤制造:一种货车地板,以竹为原料,包括开片、成型,采用下述步骤:步骤一,原料选择:釆用竹龄不少于4年,直径不小于50mm的毛竹,长度不限;步骤二,开片:根据毛竹的最佳利用率将选取的毛竹截成500-6000mm长度的毛竹段,通过开片机将毛竹段开成等宽的竹片2-4片,收集竹片和竹屑;或者,将选取的毛竹截成1050-2050mm长度的毛竹段,通过专用开片机开成宽度为15-24mm的竹胚条(普遍加工工艺为竹条)(见图1)(见图2),收集竹胚条和竹屑;
步骤三,将长度500-6000mm同等宽度的竹片通过专用的机器进行碾压式展开,此工艺展开竹片的同时去掉竹青、竹黄、定厚(见图3),收集竹片和竹屑;或者,将长1050-2050mm、宽15-24mm的竹胚条采用专用的粗刨机刨去竹青、竹黄,该粗刨竹条统称为竹条,收集竹条和竹屑;步骤四,将步骤二和步骤三通过机器加工产生的竹屑及残次品竹片和竹条粉碎,得粉末颗粒状的竹粉;在此,可以对竹片或竹条进行脱脂或者不进行脱脂处理,进行防腐或者不进行防腐处理;步骤五,将竹片、竹条、编织竹帘和竹粉分别进行干燥,温度控制在50-70℃,干燥之后含水率8-12%;步骤六,根据产品尺寸,将干燥处理的竹片和竹条进行接长部位加工,在接长部形成鎨形(图4-1)、齿形(图4-2)或斜面(图4-3);步骤七,把以上干燥好的竹粉和胶粘剂按照1000克竹粉和(400-700)克胶粘剂,分别倒入搅拌机进行搅拌均匀,备用;步骤八,将以上干燥好的竹片和竹条实行两面或者四面施胶粘剂,编织竹帘浸泡在胶粘剂中施胶;步骤九,将施好胶的l500-6000mm的竹片,至少2片往宽度方向进行排列,釆用施好胶粘剂的宽为20-50mm的棉布带,使用树脂钉或其他钉子固定在竹片上(图5-1);或者,采用无线或有线编织的方法排列连成n片适合生产操作尺寸的组合竹片(见图5-2);或者,将施好胶的l1050-2050mm竹条,至少2根以上的竹条往宽度方向进行排列,釆用无线或有线错位编织的接长或者采用其他接长技术把竹条连接成适合生产操作尺寸的帘状竹条(见图6);步骤十,根据产品使用要求以及尺寸要求进行如下步骤组胚组合竹胚组合,自下而上依序包括:先铺上底表层为酚醛树脂、三聚氰氨类覆膜材料或2mm以上的侧压单板,作为底层1;第二层2铺上施好胶粘剂的厚度为1-2.5mm的木质缓冲层或编织竹帘;第三层3
’’
铺上组合竹片;第四层4
’’
为横或纵方向帘状竹条;第五层5
’’
同第三层,第六层6同第二层,第七层7表层酚醛树脂、三聚氰氨类覆膜材料或2mm以上的侧压单板,得到l2000-10000*w140-2100*t12-50mm尺寸的竹板半成品(见图7c);步骤十一,根据产品表面的防滑或不防滑要求,将半成品在130-160℃的温度下,于20-40kg/cm2的压力下一次性热压成型,经过或不经过冷却处理,得高强度竹板。
39.根据产品的厚度要求,可重复增加第三、四、五层等三层的结构层次,即能达到需要产品的厚度,同时为了组合竹片或帘状竹条之间的粘合紧密度、增加组合竹片、编织竹帘或帘状竹条的厚度,以及提高产品强度,将施好胶粘剂的竹粉胶分别铺设在第三、四、五层中。通过这些方式以及釆用塑料树脂钉或其固定件固定组合,得到l2000-10000*w140-2100*t12-50mm尺寸的半成品。
40.可以对步骤十一得到的高强度竹板经过自动智能化设备加工完成切、锯、刨、打孔等深加工,制作成成品规格的高强度竹制货车地板产品(图8c),产品性能见也能满足表1。
41.另外,步骤十一,第二层和第六层,编织竹帘用厚度为1-2.5mm的木质缓冲层代替。
42.以上高强度竹制货车地板釆用直径50mm以上的毛竹,该工艺解决竹材行业成本居高不下的难题,成本低、密度轻,强度强、竹粉得到了充分的利用,变废为宝,生产周期短等优点,省去了过去专门去竹节、去青、去黃的等工序,通过本发明制作的竹制货车地板物理性能见附表一,解决了只能生产侧压产品的传统工艺难题,本发明以竹代木,性能见下表一。