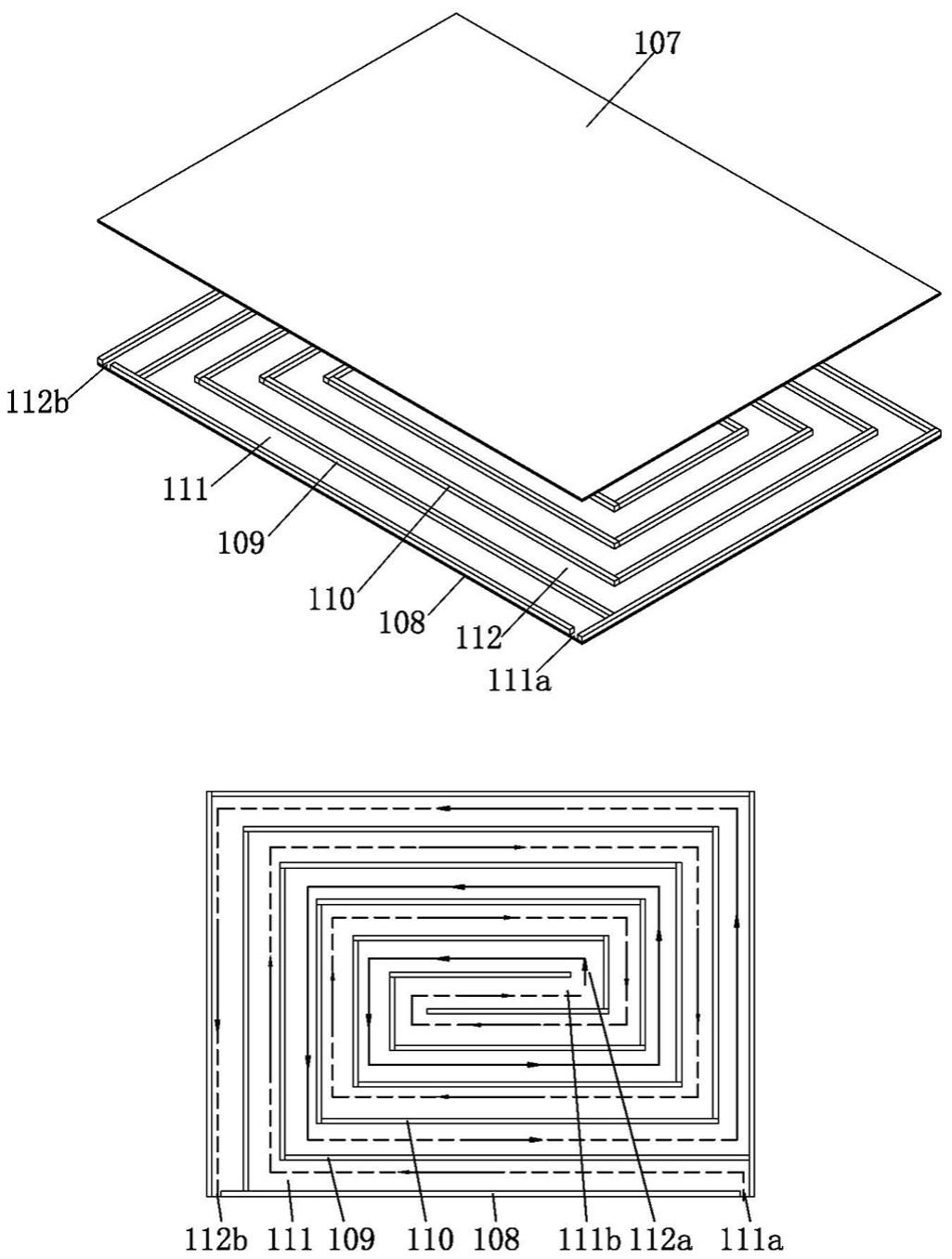
1.发明涉及实木板材加工技术领域,具体涉及一种实木板材的加工装置及加工方法。
背景技术:2.巴沙木属于纤维素类,纤维素为细菌、真菌和虫类的食物,亲水性太强,由于原料的巴沙木含水率高,为了能够长时间存放而不发霉,通常对切割后的巴沙木进行干燥处理。
3.cn113580296a公开了一种实木板材的原料预处理方法,其中处理过为:在切割后所得的实木原料板材表面涂刷一层油性防霉剂;将经过防霉处理后的板材堆放至通风处进行风干处理;将经过一次干燥后的板材浸泡于盛有预处理液的浸泡池中;浸泡完成后将板材从浸泡池中取出并装入干燥窑中,通过干燥窑对进行加热烘干处理。
4.虽然经过上述处理后的板材在短时间内具有防霉的效果,但是,由于板材内始终含有水分,长时间存放后还是会导致板材长霉,物别是在连续潮湿的天气,由于空气中的湿度大,面且板材又不通风,更容易导致长霉。
5.此外,cn112357575a公开了一种板材加工装置,这种加工装置虽然能对板材进行切割,但是无法对上述风力叶片中使用的板材进行全面加工。
技术实现要素:6.本发明提供一种可以在长期保存时避免长霉的实木板材的加工装置及加工方法。
7.实木板材的加工装置,包括:对板材的表面进行打磨的打磨机;测量板材含水量的水分仪;对板材进行烘干的第一烘干设备;对板材开设通风孔的钻孔机;所述第一烘干设备包括干燥罐以及位于干燥罐内的多个排列成多层的热辐射板,热辐射板包括上盖、下盖、第一涡旋部件、第二涡旋部件,第一涡旋部件和第二涡旋部件位于上盖和下盖之间且布置成迷宫状,在上盖与下盖、第一涡旋部件以及第二涡旋部件之间形成供加热介质流动的第一流道和第二流道,第一流道的第一输入端位于上盖或下盖的侧壁上,第一流道的第一输出端与第二流道的第二输入端配合,第二流道的第二输出端位于上盖或下盖的侧壁上。
8.实木板材的加工方法,包括以下步骤:s1,将实木原料加工成板材后,采用打磨机对板材的表面进行打磨;s2,在板材表面涂刷一层油性防霉剂,将经过防霉处理后的板材堆放至通风处进行风干处理;s3,将经过一次干燥后的板材浸泡于盛有预处理液的浸泡池中,浸泡完成后将板材从浸泡池中取出并装入第一烘干设备中进行加热干烘;
s4,对板材进行含水率测量,每张板材随机测多个点;s5,如果步骤s4中的每一个检测点的含水率均小于11.5%,则在板材上开设通风孔,如果步骤s4中任意一个检测点的含水率大于11.5%,将板材送入第二烘干设备加热干烘;s6,将完成开设通风孔的板材码放到千层架上,相邻两个板材之间通过垫块分隔,以形成通风的空间。
9.本发明对板材涂刷防霉剂以及进行浸泡(预处理液为杀菌剂与杀虫剂的混合液)后,既可以起到防霉的作用,又可起到杀虫的作用,在板材上进行了钻孔处理,使板材在保存期间能够进行通风,而且还对板材进行了干燥作理,由此使得板材在长时间保存的情况下不会长霉,也不会受到虫类和菌类的侵犯。经过本发明的方法处理后的板材,特别适用于填充到风力发电叶片内。例如按照风力发电叶片内腔的形状,将板材分切后进行填充。
附图说明
10.图1为本发明的工艺流程图。
11.图2为风力发电叶片芯材的打磨机主视图。
12.图3为在图2的基础上隐藏了一部分零件后的示意图。
13.图4为打磨机构的示意图。
14.图5为升降工作台的结构图。
15.图6为伸缩旋转夹持机构与芯材配合的示意图。
16.图7为升降顶料机构持的结构示意图。
17.图8为搬运机器人的结构示意图。
18.图9为除尘机构的结构示意图。
19.图10为气刀的结构示意图。
20.图11为第四升降驱动器的结构示意图。
21.图12为本发明中第一烘干设备的示意图。
22.图13为本发明中热辐射板的示意图。
23.图14为钻孔机的主视图。
24.图15为钻头执行组件的一部分与第一升降驱动机构的配合示意图。
25.图16为压料机构与钻头执行组件的配合示意图。
26.图17为在图15的基础上隐藏了一部分零件后的示意图。
27.图18为防尘罩与钻头执行组件的配合示意图。
具体实施方式
28.如图1,本发明的实木板材的加工方法,包括以下步骤:s1,将实木原料加工成板材s后,码放在自然环境的千层架上进行风干,风干之后再采用打磨机对板材s的表面进行打磨。打磨时打磨机分多次下降,首次至最后一次打磨进给的厚度按递减进行。每次打磨进给的厚度最多为2mm,例如板材s厚度为18mm,需要加工成15mm厚的板材,第一次设置打磨厚度参数为16mm,第二次设为15.5mm, 第三次设为15mm。
29.通过上述步骤s1对板材s进行打磨后,全面检测每张板材s的外观,包括:翘曲检
测,凸型翘曲:2m长的板材s翘曲高度小于10mm,凹型翘曲:3m长的板材s翘曲高度小于16mm;孔洞检测:每张板材的孔洞不超过15个,每个孔洞的直径不能超过3mm,;缺角检测:每张板材s允许最大缺角8
×
8mm;划痕压伤:每张板材s的第一表面s1和第二面s2的深度小于1mm、宽度小于3mm、长度小于30mm的划伤压痕不超过3处。检测完成之后,所有的指标满足上述要求后,进入步骤s2。
30.s2,在板材s表面涂刷一层油性防霉剂,将经过防霉处理后的板材堆放至通风处进行风干处理。
31.s3,将经过一次干燥后的板材浸泡于盛有预处理液的浸泡池中,浸泡完成后将板材s从浸泡池中取出并装入第一烘干设备中进行加热干烘。
32.s4,对板材进行含水率测量,每张板材s随机测多个点,任意一点含水率不得超过11.5%。
33.s5,如果步骤s4中的每一个检测点的含水率均小于11.5%,则在板材上开设通风孔,如果步骤s3中任意一个检测点的含水率均大于11.5%,将板材送入第二烘干设备加热干烘。
34.s6,将完成开设通风孔的板材s码放到千层架上,相邻两个板材s之间通过垫块分隔,以形成通风的空间。
35.s7,对板材s进行包装前,将码放有板材s的千层架送入第二烘干设备中进行包装前的干烘。对于厚度≤20.32mm的板材,采用60-65℃的干烘温度,干烘2-2.5小时后,继续检测多个点的含水率是否大于11.5%,如果含水率仍然超标,则继续干烘,但每间隔20-40分钟检测一次含水率。对于厚度>20.32mm的板材,采用60-65℃的干烘温度,干烘3-3.5小时后,继续检测多个点的含水率是否大于11.5%,如果含水率仍然超标,则继续干烘,但每间隔20-40分钟检测一次含水率。
36.如图2至图18所示,本发明的实木板材的加工装置,包括对板材s的表面进行打磨的打磨机、测量板材s含水量的水分仪(水分仪在图中未示出)、对板材s进行烘干的第一烘干设备、对板材s开设通风孔的钻孔机,下面对每部分进行详细说明:如图2至图11所示,打磨机包括机架a、打磨机构b,升降工作台c、伸缩旋转夹持机构d、升降顶料机构e,下面对打磨机进行详细说明:如图2至图4所示,机架a具有内侧作业空间a1,机架a由两个独立的第一机架1组成,两个第一机架1间隔布置后,在两个第一机架1之间形成内侧作业空间a1,打磨机构b、升降工作台c均位于内侧作业空间a1中,每个第一机架1由空心的钢管连接而成,这些钢管之间的连接方式包括焊接、螺钉连接、铆接等多种方式。将第一机架1分成第一区域2以及位于第一区域下方的第二区域3,其中第一区域2用于安装打磨机构b,第二区域3用于安装伸缩旋转夹持机构d。
37.如图2至图4所示,所述打磨机构b为多自由度的打磨机构b,打磨机构b位于内侧作业空间a1中且两端分别与机架a配合,本实施例中,打磨机构b的自由度包括沿机架a的横向x(即通常所说的x轴方向)移动,沿机架a的竖向y(即通常所说的y轴方向)移动,沿机架a的纵向z(即通常所说的z轴方向)移动,本实施例中的打磨机构b可以沿机架a的多个方向进行移动后,从而能对板材s的表面进行全方位的打磨。
38.如图2至图4,打磨机构b包括支撑框架10、第一框架11、第一直线驱动器12、移动板
13、第二直线驱动器14、第三直线驱动器15、打磨驱动器16、打磨头17,下面对打磨机构b中的各部分及相互之间的关系进行说明:如图2至图4,第一框架11沿机架a的横向x移动,第一框架11与支撑框架10滑动配合,第一直线驱动器12与第一框架11连接。第一直线驱动器12由第一电机以及第一丝杆机构组成,第一电机与第一丝杆机构中的丝杆连接,第一丝杆机构中的第一螺母与第一框架11固定,第一框架11通过第一滑块与支撑框架10滑动配合。第一直线驱动器12工作时,驱动第一框架11沿机架a的横向x移动。
39.如图2至图4,移动板13沿机架a的纵向z移动,移动板13与第一框架11滑动配合,第二直线驱动器14与移动板13连接。第二直线驱动器14由第二电机以及第二丝杆机构组成,第二电机与第二丝杆机构中的丝杆连接,第二丝杆机构中的第二螺母与移动板13固定,移动板13通过第二滑块与第一框架11滑动配合。第二直线驱动器14工作时,驱动移动板13沿机架a的纵向z移动。
40.如图2至图4,第三直线驱动器15驱动支撑框架10沿机架a竖向y移动,第三直线驱动器15由第三电机、第三丝杆机构、升降滑块组成,第三电机与第三丝杆机构中的丝杆连接,第三丝杆机构中的第三螺母与升降滑块固定,升降滑块与支撑框架10固定,升降滑块与安装在机架a上的滑轨滑动配合。第三直线驱动器15工作时,支撑框架10沿机架a的竖向y移动。
41.如图2至图4,打磨驱动器16安装在移动板13上,打磨头17一端与打磨驱动器16连接,打磨头17的另一端穿过支撑框架10。当打磨机构b沿着机架a的横向x、纵向z、竖向y移动时,打磨头17则对板材s的表面形成全方向的打磨。
42.如图2、图3和图5,升降工作台c对板材s的若干部位形成支撑,升降工作台c位于机架a的内侧,升降工作台c位于打磨机构b的下方;升降工作台c对板材s形成均匀的支撑作用,避免板材s在打磨时受力不均而影响打磨效果。当板材s的第一表面s1和第二表面s2进行位置对调时,升降工作台c复位与板材s分离,以对板材s的翻转形成让位作用,从而避免升降工作台c对板材s的翻转形成干涉作用,在翻转完成后,升降工作台c重新进给,从而对板材s重新形成支撑。
43.如图2、图3和图5,升降工作台c包括工作台20、底板21、第二升降驱动器22、叉形铰接架23,工作台20上设有供升降顶料机构e穿过的开口(开口在图中未示出)。第二升降驱动器22用于驱动工作台20进行升降,第二升降驱动器22分别与工作台20和底板21连接,叉形铰接架23分别与工作台20和底板21连接。第二升降驱动器22可以采用气缸或液压缸或电动丝杆,本实施例中,第二升降驱动器22优先采用液压缸。本实施例中,第二升降驱动器22和叉形铰接架23的数量均采用两个。
44.如图2、图3和图5,工作台20可以采用板状结构,工作台20也可以采用框架的结构,本实施例中工作台20优先采用板状结构,工作台20上的开口位于该工作台20的中部,当需要使板材s翻转时,升降顶料机构e向板材s进给,在进给过程中穿过工作台20上的开口,然后对板材s进行举升,从而使板材s与工作台20分离。
45.如图2、图3和图6,伸缩旋转夹持机构d向内侧作业空间a1进给对板材s夹持后进行翻转,伸缩旋转夹持机构d设置在机架a上,伸缩旋转夹持机构d的主要作用是,对与工作台20分离的板材s进行夹持,然后再驱动板材s旋转180
°
,从而使板材s的第一表面s1和第二表
面s2进行位置对调。
46.如图3和图6,本实施例中,伸缩旋转夹持机构d包括伸缩驱动器30、旋转驱动器31、夹爪32,旋转驱动器31与伸缩驱动器30的输出端连接,旋转驱动器31与机架a配合,夹爪32与旋转驱动器31的输出端连接。伸缩驱动器30为直线驱动器,该直线驱动器为气缸或液压缸或者电动丝杆中的一种,本实施例中优先采用电动丝杆。伸缩驱动器30的主要作用是使夹爪32根据需要的移动距离移动到板材s的位置,或者使夹爪32复位远离升降工作台c,以避免夹爪32对升降工作台c或者打磨机构b形成干涉或碰撞。
47.如图3和图6,本实施例中,旋转驱动器31为马达或旋转气缸,本实施例中,旋转驱动器31优先采用电机,在机架a上设有通孔,该通孔的内壁面上设有花键,旋转驱动器31的外周面上也设有花键,旋转驱动器31与机架a上的通孔通过花键配合,从而对旋转驱动器31形成导向和支撑作用。
48.如图3和图6,本实施例中,夹爪32优先采用气动手指,夹爪32的作用是对板材s进行夹持,并在旋转驱动器31的旋转作用下带动板材s翻转,从而使板材s的第一表面s1和第二表面s2进行位置对调。
49.如图3和图7,升降顶料机构e将板材s顶起以供伸缩旋转夹持机构d进给后对芯材进行夹持,即升降顶料机构e将板材s顶起后,在板材s与升降工作台c之间形成间隔空间,夹爪32的其中一个手指插入到间隔空间内,另一个手指位于板材s的上方,从而可以对板材s进行夹持。
50.升降顶料机构e与升降工作台c配合,升降顶料机构e位于机架a的侧部。升降顶料机构e与工作台20上的开口配合,当需要使板材s翻转时,升降顶料机构向板材s进给,在进给过程中穿过工作台20上的开口,然后对板材s进行举升,从而使板材s与工作台20分离。
51.如图3和图7,升降顶料机构e包括第三升降驱动器40、顶料板41,顶料板41的一端与第三升降驱动器40的输出端连接,顶料板41一端的宽度小于该顶料板41另一端的宽度,顶料板41的另一端为自由端。顶料板41的另一端优先与工作台20上的开口间隙配合,这样,在打磨过程中,顶料板41可以对板材s形成支撑作用,以弥补工作台20开口位置没有支撑的问题。
52.如图2和图3,本实施例中的打磨机还包括第一伸缩定位组件f、第二伸缩定位组件h,第一伸缩定位组件f对板材s沿机架a横向延伸的第一侧面进行定位,第一伸缩定位组件f设置在升降工作台c上,第一伸缩定位组件f由直线驱动器以及与直线驱动器输出端连接的定位板组成,直线驱动器的轴向与机架a的纵向z平行,直线驱动器可以采用气缸、液压缸或电动丝杆等。
53.如图2和图3,第二伸缩定位组件h对板材s沿机架a纵向延伸的第二侧面进行定位,第二伸缩定位组件h的一端与机架a固定,第二伸缩定位组件h的另一端为自由端,当第二伸缩定位组件h向板材s进给,第二伸缩定位组件h的另一端与板材s的第二侧面形成抵顶时,第二伸缩定位组件h对板材s的第二侧面形成定位。本实施例中,在两个第一机架1上均安装有第二伸缩定位组件h,每个第二伸缩定位组件h由直线驱动器以及与直线驱动器输出端连接的定位板组成,直线驱动器的轴向与机架a的横向x平行,直线驱动器可以采用气缸、液压缸或电动丝杆等。
54.如图2和图3,第一伸缩定位组件f和第二伸缩定位组件h采用伸缩的结构,当对板
材s进行翻转时,需要使第一伸缩定位组件f和第二伸缩定位组件h复位,使第一伸缩定位组件f和第二伸缩定位组件h与板材s进行分离,以避免第一伸缩定位组件f和第二伸缩定位组件h对板材s的翻转形成干涉。同时,通过第一伸缩定位组件f和第二伸缩定位组件h可以使板材s居中在工作台20上。
55.如图2和图8,本实施例中的打磨机还包括搬运机器人j,搬运机器人j将完成打磨的板材s搬运到指定位置,本实施例中的搬运机器人j包括机器人本体50、连接板51、钩爪52、压板53、压板驱动器54,连接板51与机器人本体50的输出端连接,连接板51呈l型,钩爪52呈l型,连接板51与机器人本体50的输出端连接,钩爪52的一端与连接板51的一端连接,压板驱动器54采用气缸或液压缸等直线驱动器,压板驱动器54的一端与连接板51固定,压板53与压板驱动器54的另一端固定后,在压板53与钩爪52的另一端之间形成容纳板材s一部分的容纳空间55,当容纳空间55与板材s配合后,压板驱动器54驱动压板53向钩爪52移动,从而板材s被夹紧在钩爪52与压板53之间,机器人本体50则可以将完成打磨的板材s搬到指定位置。
56.如图2、图9至图11,本实施例中的打磨机还包括除尘机构k,除尘机构k用于接收搬运机器人j搬运来的板材s,并对板材s表面的粉尘进行吹扫,且将粉尘抽走。
57.除尘机构k包括滚筒输送架60、罩体61、输气机62、气刀63、抽气机64,罩体61安装在滚筒输送架60上,气刀63位于罩体61的内部,气刀63自身具有用于接收气体的内腔,气刀63的出气口63a呈扁平状,气刀63的出气口63a沿着罩体61的纵向延伸,因此,从气刀63输出的气体不但具有压力,而且呈刀片状。输送机62与罩体61连接,输送机62与气刀63连接,将气体或压缩气体输入到气刀63的内腔中,抽气机64安装在罩体61上。
58.如图2、图9至图11,除尘机构k还包括第四升降驱动器,第四升降驱动器由气缸65、支撑板66以及多个推料板67组成,气缸65的输出端与支撑板66固定,支撑板66与推料板67固定,多个推料板67呈间隔布置,当气缸65的活塞杆伸出后,推料板67穿过相邻两个滚筒之间的间隔空间,从而将板材s顶起,使板材s与气刀63之间的间距缩短,同时,由于气流在罩体61内流动,这样可以对板材s的第一表面s1和第二表面s2上的粉尘均能形成吹扫,从而提升除尘效率。还可以在罩体61内布置两个气刀63,其中一个气刀位于滚筒输送架60的上方,另一个气刀位于滚筒输送架60的下方,这样除尘效果会更好。
59.包括以下步骤:s11,将板材s加载到升降工作台c上。例如,通过人工或其他方式(例如机器人、转运输送线等)将板材s送到工作台20上。
60.s12,升降工作台c将板材s举升到打磨工位。第二升降驱动器22驱动工作台20上升,从而对板材s举升,同时叉形铰接架23也随着工作台20升起,叉形铰接架23对工作台20具有支撑作用。
61.s13,打磨机构b向板材s进给,打磨机构b对板材s的整个第一表面s1进行打磨;打磨机构b分别沿机架a的横向x、竖向y以及纵向z移动,本实施例中的打磨机构b可以沿机架a的多个方向进行移动后,对板材s的表面进行全方位的打磨。
62.s14,打磨机构b对板材s的第一表面s1打磨完成后,打磨机构b复位,升降顶料机构e向板材s进给,升降顶料机构e穿过升降工作台c后将板材s顶起后,使板材s与升降工作台c分离,升降工作台c复位。升降工作台c和打磨机构b复位后,打磨机构b和升降工作台c远离
板材s,为板材s的翻转提供让位空间,避免升降工作台c和打磨机构b对板材s的翻转形成干涉。
63.s15,伸缩旋转夹持机构d向板材s进给后对板材s进行夹持,此时由于板材s获得伸缩旋转夹持机构d的支撑作用,控制升降顶料机构e复位,以避免即将翻转板材s时对翻转过程形成干涉,伸缩旋转夹持机构d旋转带动板材s翻转,使板材s的第一表面s1和第二表面s2所在位置对调。
64.s16,升降工作台c和升降顶料机构e向板材s进给,板材s与升降顶料机构e配合后,伸缩旋转夹持机构d松开对板材s的夹持并复位,升降顶料机构e复位,使第一表面s1和第二表面s2位置对调的板材s落在升降工作台c上,然后执行步骤s13对整个第二表面s2进行打磨。
65.如图11和图,第一烘干设备包括干燥罐以及位于干燥罐内的多个排列成多层的热辐射板103,本实施例采用热辐射板103对板材s进行加热烘干的方式,使板材s的受热均匀,并且加热效率高,干燥的速度快。另外,采用转架套106与立柱105的配合方式对端盖104进行开或关,这种相对于端盖通过铰铰与罐体100的连接方式而言,本实施例中的端盖104在开启后可以完全与罐体100分离,避免对上料和下料形成阻碍。
66.假如热辐射板103内只有一条流道,加热介质(热油)从输入端流向输出端时,温度会越来越低,导致位于热辐射板103上板材s受热不均匀,从而干燥效率低。
67.如图12,本实施例中的热辐射板103包括上盖107、下盖108、第一涡旋部件109、第二涡旋部件110,第一涡旋部件109和第二涡旋部件110位于上盖107和下盖108之间且布置成迷宫状,在上盖107与下盖108、第一涡旋部件109以及第二涡旋部件110之间形成供加热介质流动的第一流道111和第二流道112,第一流道111的第一输入端111a位于上盖107或下盖108的侧壁上,第一流道111的第一输出端111b与第二流道112的第二输入端112a配合,第二流道112的第二输出端112b位于上盖107或下盖108的侧壁上。
68.如图12,这种结构的热辐射板103,由于第一流道111和第二流道112相互穿插,如果将第一流道111作为输入流道,第二流道112作为输出流道,经过对位于热辐射板103上板材s进行热辐射之后,第二流道112的介质的温度会低于第一流道111中的介质的温度,但通过第二流道112和第一流道111进行热交换,在第一流道111和第二流道112的同一位置,第二流道112中的介质温度接近于第一流道111介质温度,由此,热辐射板103内的温度是均匀的。
69.如图11,干燥罐包括罐体100、内支架102、端盖104,转架套106,罐体100内部设有底座101,内支架102与底座101固定,热辐射板103排列成多层并与内支架102固定,罐体100的外周面上设有立柱105,转架套106的一端与端盖104固定,转架套106的一端套在立柱105上并与立柱105转动地配合。罐体100上设有排气机113,从板材s内蒸发出的水汽通过排气机103排走。
70.本实施例采用钻孔机开设通风孔,如图13至图17所示,本实施例中的钻孔机包括钻孔机构,所述钻孔机构包括底座121、固定架122、第一工作台123,所述底座121与固定架122固定连接,所述固定架122与第一工作台123滑动配合,所述底座121上设有第一升降驱动机构124和导向部件125,所述第一升降驱动机构124的一端至少设有一组钻头执行组件,每组钻头执行组件包括多个钻头129、一个第二驱动器130,钻头执行组件还包括具有多个
输出端的传动箱体131,所述第二驱动器130与传动箱体131的输入端配合,传动箱体131的每个输出端均连接一个钻头129,这些钻头129排列成一排或多排,所述传动箱体131与第一升降驱动机构124固定连接且与底座121滑动配合。
71.如图13至图17所示,所述钻孔机还包括与传动箱体131连接且随着传动箱体131升降的压料机构,压料机构与第一工作台123之间的间距小于钻头129与第一工作台123之间的间距,传动箱体131在向位于第一工作台123上的板材s进给时,先通过压料机构压在板材s上之后,再由钻头执行组件对板材s进行钻孔。
72.如图13至图17所示,本实施例中,第一工作台123由工作台本体、第一滑轨、第一驱动器、第一齿条组成,第一滑轨和第一齿条安装在工作台本体的两侧,固定架122与第一驱动器固定,第一驱动器由电机和第一齿轮组成,电机与第一齿轮连接,第一齿轮与第一齿条啮合,电机工作时带第一齿轮转动,第一齿轮通过与第一齿条的啮合关系带动固定架122沿第一工作台123的横向x移动。
73.如图13至图17所示,在本实施例中,第一升降驱动机构124采用液压驱动缸或气缸,第二驱动器130优先采用马达,当板材s送至第一工作台123上的固定位置后,第一升降驱动机构124带动整个钻头执行组件沿着底座121上的导向部件125移动并向板材s进给,当第一升降驱动机构124带动钻头执行组件的传动箱体131上的压料机构接触到板材s后,第一升降驱动机构124继续进给,压料机构将板材s压在第一工作台123上,此时,第二驱动器130工作,带动传动箱体131转动,传动箱体131以带动安装在传动箱体131的每个输出端的每一个钻头129旋转,当第一升降驱动机构124继续向板材s进给,压料机构将板材s越压越紧,同时钻头129进行板材的钻孔。
74.如图13至图17所示,所述传动箱体131包括:第一传动轴132、主动部件133、从动部件134、传动组件135、第一箱体136、第二箱体137、连接座138;第一传动轴132可转动地与第一箱体136配合,主动部件133安装在第一传动轴132一端,第一传动轴132的另一端穿过第一箱体136、连接座138后与从动部件134连接;连接座138的一端与第一箱体136固定,连接座138的另一端与第二箱体137固定;主动部件133与第二驱动器130的输出端配合,主动部件133为一对齿轮传动部件或一对皮带传动部件,本实施例中优先采用齿轮传动部件,齿轮传动部件中的一个齿轮与第二驱动器130连接,另一个齿轮与第一传动轴132连接,两个齿轮相互啮合。
75.如图13至图17所示,从动部件134和传动组件135位于第二箱体137内,传动组件135与从动部件134配合,所述钻头129与传动组件135连接。从动部件134为齿轮,从动部件134位于第二箱体137的中部,传动组件135排列在从动部件134的两侧,从动部件134优先采用齿轮,传动组件135由多个传动齿轮和连接钻头129的连接轴组成,传动齿轮可转动地安装在第二箱体137内,连接轴的一端与传动齿轮连接,连接轴的另一端穿过第二箱体137暴露在第二箱体137外部,连接轴的另一端与钻头129连接。
76.当第二驱动器130工作时,第二驱动器130的输出端带动主动部件133转动,然后,主动部件133通过第一传动轴132来带动安装在第一传动轴132另一端上的从动部件134转动,然后从动部件134驱动传动组件135转动,然后传动组件135带动钻头129旋转,在本实施例中,第一箱体136主要是安装第二驱动器130的输出端、主动部件133以及第一传动轴132,而连接座138主要将第一箱体136、第二箱体137连接在一起。
77.如图13至图17所示,压料机构包括第一连接板140、套筒141、弹性部件142、压料板143、导杆144,第一连接板140与传动箱体131固定,本实施例中,第一连接板140优先与传动箱体131中的第二箱体137固定,第一连接板140的两端延伸到第二箱体137的外侧,从而形成用于安装套筒141的第一安装部,套筒141穿过第一连接板140并与第一连接板140固定,即套筒141穿过所述第一安装部,导杆21穿过套筒141,导杆21的一端与压料板143固定,导杆144的另一端设有用于限制导杆144脱离套筒141的限位部145,弹性部件142套在导杆144上,弹性部件142的一端与套筒141配合,弹性部件142的另一端与压料板143配合。
78.如图13至图17所示,在本实施例中,弹性部件142优先采用压缩弹簧,当第一升降驱动机构124驱动钻头执行组件向板材s进给时,首先压料板143接触到板材s,然后随着第一升降驱动机构124驱动钻头执行组件继续向板材s进给后,传动箱体131的重力依次通过第一连接板140、套筒141、弹性部件142、压料板143加载到板材s上,由于导杆144与套筒141滑动配合,从而弹性部件142被套筒141压缩,弹性部件142在被压缩的同时,又会因为自身的弹力一直与压料板143抵顶,当钻孔完成后,第一升降驱动机构124带动钻头执行组件复位时,导杆144会伴随着弹性部件142的张力而复位,此时,通过限位部145来保证导杆144不会完全脱落出套筒141。
79.如图13至图17所示,采用上述钻孔机对板材s进行钻孔的方法:s51,首先将板材s送到在第一工作台123上的加工位置。
80.s52,第一升降驱动机构124工作,使第一升降驱动机构124驱动钻头执行组件沿着底座121上的导向部件125向板材s移动。
81.s53,压料机构首先接触到位于第一工作台123上的板材s,并随着钻头执行组件的进给,钻头执行组件的重力以及压料机构的重力均加载在板材s上,以对板材s形成钻孔前的定位;s54,第二驱动器130驱动传动箱体131带动钻头129旋转,随着第一升降驱动机构124驱动钻头129继续进给,钻头129对板材s进行钻孔。
82.s55,本排钻孔完成后,第一升降驱动机构124带动钻头执行组件沿着底座121上的导向部件125复位。
83.s56,固定架122带动底座121沿着第一工作台123的横向x行走,使底座121移动到下一排的钻孔位置,重复步骤s52至s55,如此重复,完成所有需要的钻孔。完成钻孔(开设通风孔)后的板材s还可以送到除尘机构k中进行除尘。
84.由于钻头129在对板材进行钻孔时会产生非常多的粉尘,这些粉尘会对环境造成影响,以及对设备本身造成影响,而现有技术去除粉尘的方法则是在采用体积较大的防尘装置,将底座121、固定架122、第一升降驱动机构124、导向部件125、钻头129、第二驱动器130、传动箱体131全部笼罩起来,这种方法不仅会对设备的散热造成影响,而且会导致整个设备体积较大,所以不适用。
85.如图18所示,在第二箱体137上设置了防尘罩150,防尘罩150上设有接口151,接口151与一个吸尘装置(图中未示出)连接,防尘罩150为具有弹性的防尘罩150,防尘罩150例如采用橡胶材料制成,所有的钻头129均位于防尘罩150内,当第一升降驱动机构124驱动钻头执行组件向板材进给时,防尘罩150与上述压料机构同时接触到板材s,并且会随着第一升降驱动机构124驱动钻头执行组件向板材s继续进给的同时而被压缩,在钻孔时,由于防
尘罩150对所有钻头129形成了笼罩,钻头129对板材s钻孔时所产生的粉尘全部在防尘罩150与板材抵顶后所形成的空腔内,然后再在接口151上接上吸尘装置,将上述空腔内的粉尘全部吸走。