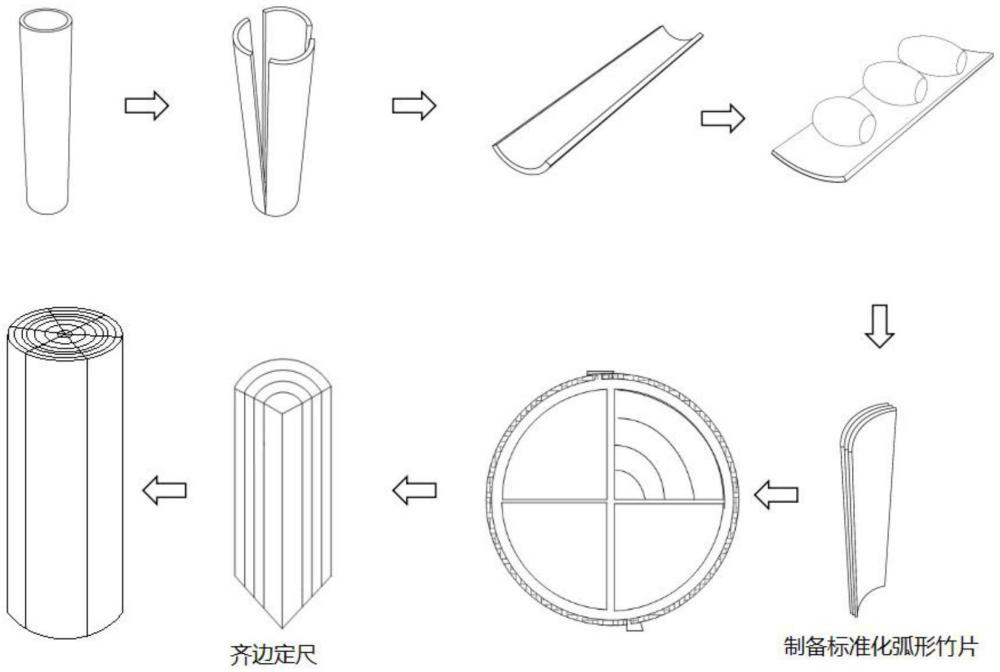
本发明涉及竹材加工领域,特别是涉及一种竹支撑构件的加工方法。
背景技术:
1、竹材是一种天然的生物质材料,具有中空壁薄且呈现一定尖削度的外观特征,且在竹秆长度方向上竹节有规律的分布,竹节像箍一样局部增强了管状竹秆横向强度。竹秆这种具有一定尖削度的管状结构赋予了竹材具有良好的强韧行,在发生大幅度弯曲也不劈裂破坏。
2、管材和柱材在日常生活中有着广泛的用途,是建筑结构中的重要构件。目前,建筑结构中常用的材质主要有木质、塑料、金属、竹木复合等,也有用竹秆直接用于热带简易房屋的支撑柱。竹材是一种天然的管材,呈中空锥形壳体结构,上细下粗,各向异性显著,无法作为标准形态的柱材/管材用于工业化产品当中。
3、标准形态的竹管材或竹柱材主要的加工方式有:一是对竹材秆进行加热软化调直;二是以重组竹为原料,将重组竹铣削加工成管材或柱材;三是以矩形竹片为原料,先将竹片组坯胶合成方材,再铣削加工成管材;四是以矩形竹片为原料,根据管材尺寸,在管材模具上直接组坯胶合成管材;五是以竹篾为原料,采用缠绕的方式制备竹缠绕管材。无论是以重组竹还是矩形竹片为原料,加工制备的竹管材,材料的利用率都很低,且破碎重组对竹材原料的破坏性大、胶黏剂用量也较大,易失去竹材原始表面优雅纹理、质感和良好的物理力学性质。采用缠绕的方式制备的竹管材,制备工序复杂,树脂含量高达50%左右,且依旧失去了竹材天然的纹理和梯度结构。
技术实现思路
1、为解决以上技术问题,本发明提供一种竹支撑构件的加工方法,提高了竹材的利用率,在外观质量和纹理上保持了竹材的原态梯度结构和表面纹理特征。
2、为实现上述目的,本发明提供了如下方案:
3、本发明提供一种竹支撑构件的加工方法,包括以下步骤:
4、步骤一、将竹材根据竹支撑构件的长度进行横截定段,得出多个竹筒;
5、步骤二、根据所述竹筒的小头端的外周长进行分级,之后将小头端的外周长处于同一等级的所述竹筒根据小头端的壁厚进行分级;
6、步骤三、将分级后的所述竹筒根据小头端的外周长和所需弧形竹片的尺寸剖分,所述弧形竹片的弧长不超过1/2圆弧长,所述弧形竹片的小头端和大头端的弧长不等,所述弧形竹片在长度方向上为不等宽度的梯度渐变弧形竹片;
7、步骤四、对多个所述弧形竹片进行宽度、厚度、弧度的规格化制备,得出一定规格的标准化弧形竹片和标准化扇形竹片;
8、步骤五、采用圆筒单元模块制备所述竹支撑构件的方式,各所述圆筒单元模块均包括多个沿周向依次粘接的所述标准化弧形竹片,当所需制备的所述竹支撑构件为竹管材时,最内侧的所述圆筒单元模块套设于中心模具上,多个所述圆筒单元模块由内至外依次粘接形成所述竹管材,在所述竹管材外部采用卡箍件进行固定,固化一段时间后取下所述卡箍件和中心模具;当所需制备的所述竹支撑构件为竹柱材时,先制作中心圆柱单元模块,所述中心圆柱单元模块包括多个沿周向依次粘接的所述标准化扇形竹片,再在所述中心圆柱单元模块的外部粘接至少一个所述圆筒单元模块形成所述竹柱材,在所述竹柱材外部采用卡箍件进行固定,固化一段时间后取下卡箍件;
9、或者采用层叠单元模块制备所述竹支撑构件的方式,当所需制备的所述竹支撑构件为竹管材时,所述层叠单元模块为弧形层叠单元模块,所述弧形层叠单元模块包括多个沿径向依次粘接的所述标准化弧形竹片,多个所述弧形层叠单元模块沿周向依次粘接形成所述竹管材,且使得所述竹管材套设于中心模具上,在所述竹管材外部采用卡箍件进行固定,固化一段时间后取下卡箍件和中心模具;当所需制备的所述竹支撑构件为竹柱材时,所述层叠单元模块为扇形层叠单元模块,所述扇形层叠单元模块包括一个所述标准化扇形竹片和至少一个沿径向粘接于所述标准化扇形竹片外部的标准化弧形竹片,多个所述扇形层叠单元模块沿周向依次粘接形成所述竹柱材,在所述竹柱材外部采用卡箍件进行固定,固化一段时间后取下卡箍件。
10、优选地,在步骤一中,所述竹筒的长度比所述竹支撑构件的长度长2cm~3cm作为加工余量。
11、优选地,在步骤二中,测量所述竹筒的小头端的外周长和壁厚,先以所述竹筒的小头端的外周长1mm的间隔进行分级,之后将小头端的外周长处于同一等级的所述竹筒以小头端的壁厚0.5mm的间隔进行分级。
12、优选地,在步骤四中,对所述弧形竹片的上、下表面进行去青、去黄、去节、定弧处理,对所述弧形竹片的两个侧面进行切割形成竹片侧向对接面,得出一定规格的所述标准化弧形竹片和所述标准化扇形竹片,使得一个所述标准化弧形竹片的竹片侧向对接面在对接组合时能够与其相邻的所述标准化弧形竹片的竹片侧向对接面相贴合,使得一个所述标准化扇形竹片的竹片侧向对接面在对接组合时能够与其相邻的所述标准化扇形竹片的竹片侧向对接面相贴合。
13、优选地,在步骤四中,所述标准化弧形竹片和所述标准化扇形竹片的圆心角为30°~90°,厚度为4mm~10mm;所述标准化弧形竹片和所述标准化扇形竹片的上下两端截面尺寸相同时,所述标准化弧形竹片和所述标准化扇形竹片的最大弦长均为2cm~10cm;所述标准化弧形竹片和所述标准化扇形竹片的上下两端分别为小头端和大头端时,所述标准化弧形竹片和所述标准化扇形竹片的小头端的最大弦长均为2cm~10cm。
14、优选地,在步骤五中,采用圆筒单元模块制备所述竹支撑构件的方式,当所需制备的所述竹支撑构件为竹管材时,任意相邻的两个所述圆筒单元模块的轴向接缝交错设置;当所需制备的所述竹支撑构件为竹柱材时,最内侧的所述圆筒单元模块的轴向接缝与所述中心圆柱单元模块的轴向接缝交错设置,任意相邻的两个所述圆筒单元模块的轴向接缝交错设置。
15、优选地,在步骤五中,采用圆筒单元模块制备所述竹支撑构件的方式,所述圆筒单元模块还包括多个第一植筋,各所述标准化弧形竹片的两侧均分别设置有所述第一植筋和第一孔洞,各所述标准化弧形竹片的所述第一植筋均用于插入与其相邻的所述标准化弧形竹片的所述第一孔洞中;当所需制备的所述竹支撑构件为竹柱材时,所述中心圆柱单元模块还包括多个第二植筋,各所述标准化扇形竹片的两侧均分别设置有所述第二植筋和第二孔洞,各所述标准化扇形竹片的所述第二植筋均用于插入与其相邻的所述标准化扇形竹片的所述第二孔洞中。
16、优选地,在步骤五中,采用层叠单元模块制备所述竹支撑构件的方式,当所需制备的所述竹支撑构件为竹管材时,所述层叠单元模块为弧形层叠单元模块,对所述弧形层叠单元模块进行施压和加热,之后根据所述竹管材的尺寸设计要求,对所述弧形层叠单元模块进行加工,使得上下两端的宽度和弧长达到设计要求,对所述弧形层叠单元模块的两个侧面进行切割形成弧形单元侧向对接面,使得一个所述弧形层叠单元模块的弧形单元侧向对接面在对接组合时能够与其相邻的所述弧形层叠单元模块的弧形单元侧向对接面相贴合;当所需制备的所述竹支撑构件为竹柱材时,所述层叠单元模块为扇形层叠单元模块,对所述扇形层叠单元模块进行施压和加热,之后根据所述竹柱材的尺寸设计要求,对所述扇形层叠单元模块进行加工,使得上下两端的宽度和弧长达到设计要求,对所述扇形层叠单元模块的两个侧面进行切割形成扇形单元侧向对接面,使得一个所述扇形层叠单元模块的扇形单元侧向对接面在对接组合时能够与其相邻的所述扇形层叠单元模块的扇形单元侧向对接面相贴合。
17、优选地,在步骤五中,采用层叠单元模块制备所述竹支撑构件的方式,当所需制备的所述竹支撑构件为竹管材时,所述层叠单元模块为弧形层叠单元模块,将所述弧形层叠单元模块放入真空袋,进行抽真空加压,将所述弧形层叠单元模块和真空袋一起放入加热装置中进行加热固化胶合,或者将所述弧形层叠单元模块放入固定模具中进行施压和加热;当所需制备的所述竹支撑构件为竹柱材时,所述层叠单元模块为扇形层叠单元模块,将所述扇形层叠单元模块放入真空袋,进行抽真空加压,将所述扇形层叠单元模块和真空袋一起放入加热装置中进行加热固化胶合,或者将所述扇形层叠单元模块放入固定模具中进行施压和加热。
18、优选地,在步骤五中,采用层叠单元模块制备所述竹支撑构件的方式,当所需制备的所述竹支撑构件为竹管材时,所述层叠单元模块为弧形层叠单元模块,各所述弧形层叠单元模块的两侧均分别设置有第三植筋和第三孔洞,各所述弧形层叠单元模块的所述第三植筋均用于插入与其相邻的所述弧形层叠单元模块的所述第三孔洞中;当所需制备的所述竹支撑构件为竹柱材时,所述层叠单元模块为扇形层叠单元模块,各所述扇形层叠单元模块的两侧均分别设置有第四植筋和第四孔洞,各所述扇形层叠单元模块的所述第四植筋均用于插入与其相邻的所述扇形层叠单元模块的所述第四孔洞中。
19、本发明相对于现有技术取得了以下技术效果:
20、本发明的竹支撑构件的加工方法将竹材截断成标准长度的竹筒,将其剖分成一定弧长的弧形竹片,对弧形竹片进行宽度、厚度、弧度的规格化制备,得出一定规格的标准化弧形竹片和标准化扇形竹片;采用多个圆筒单元模块制备出竹管材,采用中心圆柱单元模块和圆筒单元模块制备出竹柱材;或者采用弧形层叠单元模块制备出竹管材,采用扇形层叠单元模块制备出竹柱材。本发明利用竹材原态弧形特性,以弧用弧,减少材料自身的内应力,通过单元的标准化和规格化制备,实现了中空壁薄竹筒的厚壁化和实心化,减少加工过程中的竹材损耗量,提高了竹材的利用率,在外观质量和纹理上保持了竹材的原态梯度结构和表面纹理特征,相较于破碎重组和缠绕的制备方式,减少了胶黏剂用量。