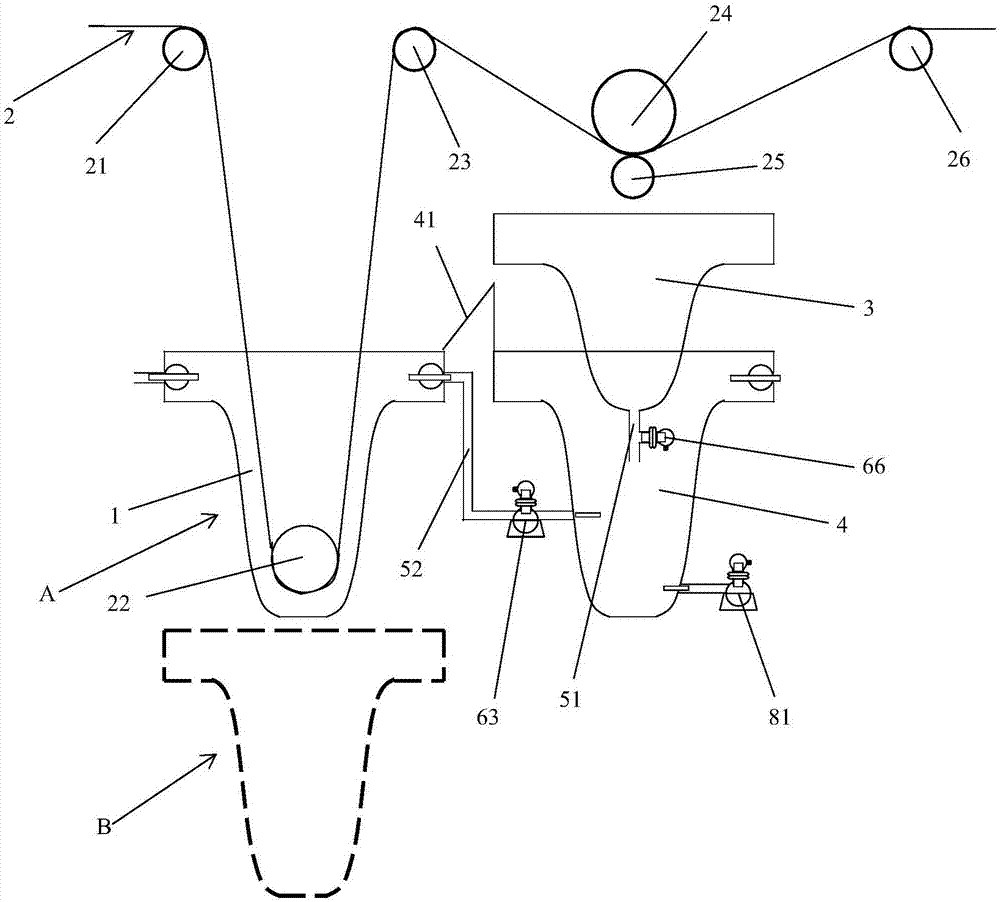
本实用新型纺织品印染
技术领域:
,具体涉及一种连续性浸轧式染色设备。
背景技术:
:纺织品染色属于高能耗高污染行业,废水排放量巨大,而且工序耗时较长,一缸织物的上染时间为6~8小时,在国家环保政策的严格管控下,行业内染缸数量迅速减少,但是市场需求却保持5%左右的增速,使得染厂爆仓,而上下游客户因为染厂排单不及时造成订单违约,遭受巨大经济损失,而且随着原材料和人力成本的上涨,印染企业也需要实现能加快生产速度,降低能耗和减少废水排放的生产方式,由于超临界二氧化碳染色技术成本过高,使大多数企业和印染科研机构争相研究常温常压下的浸轧式连续性染色技术,这种染色方式可以使能耗节省一半,生产速率增加10倍,但是产品质量却比高温高压下染缸染色的产品低,会因为上染时间短产生大量的色斑、色条、色花,经向、纬向、正反面的颜色色差较大等问题。随着纳米染料的兴起,解决了因为织物与染料接触时间短,染料大颗粒在织物表面分散不均匀而产生的色斑、色条、色花等问题,但是由于浸轧过程中轧余液不能排放,只能返回到正在运行的染液槽中,而由于不同颜色的染料、水、化学助剂跟织物结合的牢固程度不一样,所以轧余液的浓度和染料的初始浓度不同,造成染液中染料浓度和助剂浓度的变化,导致后染的布跟之前染的布出现颜色深浅和色光的差异,如果颜色为多种染料拼色,还会导致不同染料因为上染率不同而产生浓度变化较大的轧余液,轧余液返回染液槽后会导致拼色的染料成分比例发生变化,也会导致后染的布跟之前染的布出现色差,而若将轧余液直接排放而不回收利用,则会产生巨大的浪费,使染色成本增加十倍以上。要想使浸轧式染色实现产业化,必须解决轧余液浓度变化造成的织物头尾色差问题。技术实现要素:本实用新型的目的是提供一种能解决轧余液浓度变化造成的织物头尾色差问题的连续性浸轧式染色设备。为达到上述目的,本实用新型采用的技术方案是:本实用新型的一个目的是提供一种连续性浸轧式染色设备,包括进布装置、染液槽、均匀轧车、低温烘干机、高温焙烘机、收布装置,所述的染色设备还包括设置在所述的均匀轧车下方用于收集轧余液的分流槽,设置在所述的分流槽的下方的回流槽,用于检测所述的轧余液自所述的分流槽流入所述的回流槽中的流量的流量检测部件,储存有染料原液的染料原液储罐,储存有助剂的助剂储罐,用于将所述的染料原液储罐中的染料以及所述的助剂储罐中的助剂加入所述的回流槽中的补料装置,设置在所述的补料装置上用于控制所述的染料的添加流量的第一流量控制泵,设置在所述的补料装置上用于控制所述的助剂的添加流量的第二流量控制泵,设置在所述的回流槽中用于将所述的回流槽中的物料混合的第一混合装置,分别与所述的回流槽和所述的染液槽相连通的第二管道,设置在所述的第二管道上用于控制所述的回流槽中的物料向所述的染液槽中的添加流量的第三流量控制泵,储存有配制好的染液的染液储罐,分别与所述的染液储罐和所述的染液槽相连通的第六管道,设置在所述的第六管道上用于控制所述的染液储罐中的染液向所述的染液槽中的添加流量的第五流量控制泵,分别与所述的流量检测部件、所述的第一流量控制泵、所述的第二流量控制泵、所述的第三流量控制泵和所述的第五流量控制泵相连接的控制系统。具体地,所述的染色设备还包括与所述的分流槽相连通供所述的分流槽中的轧余液流入所述的回流槽中的第一管道,所述的流量检测部件设置在所述的第一管道上。具体地,所述的补料装置包括原料混合槽、分别与所述的原料混合槽和所述的回流槽相连通的第三管道、设置在所述的第三管道上用于控制所述的原料混合槽中的物料向所述的回流槽中的添加流量的第四流量控制泵、分别与所述的染料原液储罐和所述的原料混合槽相连通的第四管道、分别与所述的助剂储罐和所述的原料混合槽相连通的第五管道、设置在所述的原料混合槽中的第二混合装置,所述的第一流量控制泵设置在所述的第四管道上,所述的第二流量控制泵设置在所述的第五管道上,所述的第四流量控制泵与所述的控制系统相连接。优选地,所述的染料原液储罐有多个且分别用于储存不同的染料,所述的助剂储罐有多个且分别用于储存不同的助剂,所述的第四管道有多条且个数与所述的染料原液储罐的个数一致,每条所述的第四管道上分别设置有所述的第一流量控制泵,所述的第五管道有多条且个数与所述的助剂储罐的个数一致,每条所述的第五管道上分别设置有所述的第二流量控制泵。进一步优选地,所述的原料混合槽上开设有多个分别与所述的第四管道和所述的第五管道相连通的管道安装口、用于安装所述的第二混合装置的混合装置安装位、以及备用的备用口。进一步优选地,所述的补料装置还包括设置在所述的染液槽上且与所述的第二管道相连通的返回液回流管,所述的返回液回流管的位于所述的染液槽内的部分上开设有多个返回液出口。优选地,所述的第二混合装置为搅拌器。优选地,所述的染色设备还包括设置在所述的染液储罐内的第三混合装置;进一步优选地,所述的第三混合装置为搅拌器。优选地,所述的染色设备还包括设置在所述的染液槽上且与所述的第六管道相连通的染液补加管,所述的染液补加管的位于所述的染液槽内的部分上开设有多个染液出口。具体地,所述的染液槽能够上下移动从而具有工作位置与非工作位置,所述的工作位置位于所述的非工作位置的上方,当所述的染液槽处于所述的工作位置时,所述的进布装置的浸渍辊位于所述的染液槽内且位于液面下方;当所述的染液槽处于非工作位置时,所述的进布装置的浸渍辊位于所述的染液槽的上方。具体地,所述的染色设备还包括一端部与所述的回流槽相连接的导流板,当所述的染液槽处于工作位置时,所述的导流板的另一端部与所述的染液槽的上端部相接触。具体地,所述的第一混合装置为气泵。本文所涉及到的上下的方位词,是在连续性浸轧式染色设备处于使用状态时的方位作定义的。本实用新型的范围,并不限于上述技术特征的特定组合而成的技术方案,同时也应涵盖上述技术特征或其等同特征进行任意组合而形成的其他技术方案。例如上述特征与本申请中公开的(但不限于)具有类似功能的技术特征进行互相替换而形成的技术方案等。由于上述技术方案的运用,本实用新型与现有技术相比具有下列优点:本实用新型通过控制系统对各补料及加料过程流量的控制,使得轧余液中的各染料和助剂的浓度恢复到初始浓度后再返回染液槽的方式进行浓度平衡,解决了织物浸轧式染色的头尾色差问题,使这种低能耗的清洁染色技术实现产业化。附图说明附图1为本实用新型染液槽、分流槽、回流槽的平面示意图;附图2为本实用新型染液储罐与染液槽的内部正视图;附图3为本实用新型染液储罐与染液槽的外部正视图;附图4为本实用新型染液槽的内视图;附图5为本实用新型染液槽的外视图;附图6为本实用新型补料装置与回流槽的内正视图;附图7为本实用新型补料装置与回流槽的外正视图;附图8为本实用新型原料混合成槽的俯视图;其中:A、工作位置;B、非工作位置;1、染液槽;111、第一染料原液储罐;112、第二染料原液储罐;113、第三染料原液储罐;114、第四染料原液储罐;121、第一助剂储罐;122、第二助剂储罐;123、第三助剂储罐;124、第四助剂储罐;2、均匀轧车;21、第一导布辊;22、浸渍辊;23、第二导布辊;24、均匀轧车固定辊;25、均匀轧车活动辊;26、第三导布辊;3、分流槽;4、回流槽;41、导流板;51、第一管道;52、第二管道;53、第三管道;541、第四一管道;542、第四二管道;543、第四三管道;544、第四四管道;551、第五一管道;552、第五二管道;553、第五三管道;554、第五四管道;56、第六管道;611、第一一流量控制泵;612、第一二流量控制泵;613、第一三流量控制泵;614、第一四流量控制泵;621、第二一流量控制泵;622、第二二流量控制泵;623、第二三流量控制泵;624、第二四流量控制泵;63、第三流量控制泵;64、第四流量控制泵;65、第五流量控制泵;66、流量检测部件;71、原料混合槽;711、管道安装口;712、混合装置安装位;713、备用口;81、第一混合装置;82、第二混合装置;83、第三混合装置;9、染液储罐;91、染液补加管;92、返回液回流管。具体实施方式下面结合附图和具体实施例来对本实用新型的技术方案作进一步的阐述。首先对连续性浸轧式染色设备进行详细阐述。如各附图所示,包括进布装置、染液槽1、均匀轧车2、低温烘干机、高温焙烘机、收布装置、能够计算与控制染色设备中原料添加流量的控制系统。如附图1所示,进布装置包括第一导布辊21、浸渍辊22、第二导布辊23、第三导布辊26。均匀轧车2包括均匀轧车固定辊24、与均匀轧车固定辊24相配合用于对织物进行轧液的均匀轧车活动辊25。染液槽1能够上下移动从而具有工作位置A与非工作位置B,工作位置A位于非工作位置B的正上方,当染液槽1处于工作位置A时,进布装置的浸渍辊22位于染液槽1内的液面以下,从而在浸渍辊22的带动下使织物通过染液槽1中的染液;当染液槽1处于非工作位置B时,进布装置的浸渍辊位于染液槽1的正上方。染色设备工作时,染液槽1向上移动,处于工作位置A,织物通过第一导布辊21与浸渍辊22进入染液槽1进行染色,经过第二导布辊23,再通过均匀轧车固定辊24与均匀轧车活动辊25将轧余液挤出,织物再通过第三导布辊26依次进入低温烘干机、高温焙烘机、收布装置,完成织物的染色过程。染色设备包括一端部与回流槽4相连接的导流板41,当染液槽1处于工作位置A时,导流板41的另一端部与染液槽1的上端部相接触,优选地,导流板41与染液槽1接触的一端低于导流板41与回流槽4连接的一端,从而使得经过第二导布辊23附近时滴落的染液在导流板41的作用下进入染液槽1。染色设备还包括设置在均匀轧车2下方的分流槽3、设置在分流槽3下方的回流槽4、与分流槽3相连通供分流槽3中的轧余液流入回流槽4中的第一管道51、设置在第一管道51上用于搜集通过第一管道51的轧余液的流量的流量检测部件66。经过均匀轧车2挤压出来的轧余液进入分流槽3,同时经过第一管道51进入回流槽4,流量检测部件66与控制系统相连接,从而能够搜集通过第一管道51进入回流槽4的轧余液的流量。优选地,流量检测部件66为流量计。染色设备还包括分别与回流槽4和染液槽1相连通的第二管道52、设置在第二管道52上的第三流量控制泵63、设置在染液槽1上且与第二管道52相连通的返回液回流管92,在第二管道52和返回液回流管92相连接的位置的正对面设置多个返回液出口,使返回液进入返回液回流管92后从多个返回液出口流出,流入染液槽1。第三流量控制泵63与控制系统相连通且用于控制回流槽4中的返回液向染液槽1中的添加流量。控制系统控制第三流量控制泵63按照计算得到的流量将回流槽4中的返回液通过第二管道52输送至返回液回流管92,然后进入染液槽1完成返回液。回流槽4中还设置有用于将回流槽4中的返回液混合的第一混合装置81,优选地,第一混合装置81为气泵。如附图6、附图7所示,如果轧压过程中产生的轧余液直接返回染液槽1会导致拼色的染料成分比例发生变化,也会导致后染的布跟之前染的布出现色差,要想使浸轧式染色实现产业化,必须解决轧余液中各成分浓度变化造成的织物头尾色差问题,因此染色设备还包括储存有染料原液的染料原液储罐,储存有助剂的助剂储罐,用于将染料原液储罐中的染料原液以及助剂储罐中的助剂按照相应的比例补加到回流槽4的补料装置,从而使得轧余液中各染料和助剂的浓度恢复到初始浓度形成上述返回液,返回染液槽1继续进行织物的染色。补料装置包括原料混合槽71、第三管道53、设置第三管道53上第四流量控制泵64、第四管道、第五管道、第二混合装置82。第三管道53分别与原料混合槽71和回流槽4相连通,第四流量控制泵64与控制系统相连通且用于控制原料混合槽71中的物料向回流槽4中的添加流量,第二混合装置82设置在原料混合槽71中用于将原料混合槽71中的原料混合均匀;优选地,第二混合装置82为搅拌器。如附图8所示,原料混合槽71上开设有多个分别与第四管道和第五管道相连通的管道安装口711、用于安装第二混合装置82的混合装置安装位712、以及备用的备用口713。第四管道分别与染料原液储罐和原料混合槽71相连通,第五管道分别与助剂储罐和原料混合槽71相连通。染色设备还包括设置在第四管道上的第一流量控制泵,设置在第五管道上的第二流量控制泵,第一流量控制泵与控制系统相连通用于控制染料原液的添加流量,第二流量控制泵与控制系统相连通用于控制助剂的添加流量。如附图6、附图7所示,染料原液储罐有多个且分别用于储存不同的染料原液,第四管道有多条且个数与染料原液储罐的个数一致,每条第四管道上分别设置有第一流量控制泵;助剂储罐有多个且分别用于储存不同的助剂,第五管道有多条且个数与助剂储罐的个数一致,每条第五管道上分别设置有第二流量控制泵。本实施例中,染料原液储罐有四个,分别为第一染料原液储罐111、第二染料原液储罐112、第三染料原液储罐113以及第四染料原液储罐114,分别对应第一一流量控制泵611、第一二流量控制泵612、第一三流量控制泵613以及第一四流量控制泵614,且分别通过第四一管道541、第四二管道542、第四三管道543以及第四四管道544进入原料混合槽71。本实施例中,助剂储罐有四个,分别为第一助剂储罐121、第二助剂储罐122、第三助剂储罐123以及第四助剂储罐124,分别对应第二一流量控制泵621、第二二流量控制泵622、第二三流量控制泵623以及第二四流量控制泵624,且分别通过第五一管道551、第五二管道552、第五三管道553以及第五四管道554进入原料混合槽71。染色设备还包括储存有配制好的染液的染液储罐9、分别与染液储罐9和染液槽1相连通的第六管道56、设置在染液槽1上且与第六管道56相连通的染液补加管91、设置在第六管道56上的第五流量控制泵65、设置在染液储罐9内的第三混合装置83。在第六管道56和染液补加管91相连接的位置的正对面设置多个染液出口,使染液进入染液补加管91后从多个染液出口流出,流入染液槽1。第五流量控制泵65与控制系统相连接,用于控制染液储罐9中的染液向染液槽1中的添加流量;优选地,第三混合装置83为搅拌器,用于将染液储罐9中的染液混合均匀。控制系统对于整个连续性浸轧式染色设备的控制方法如下:(1)、由于任何一种颜色都是由红、黄、蓝三原色以不同的配比调制出来的,再配合不同的化学助剂以形成不同的色光,而黑色为常用色,可以直接采购原料,不经过三原色配色。经过技术人员的试验,得出常规型号的染料和助剂,在常规型号织物的上染率和携带率的数据,成立数据库,将数据库输入控制系统。(2)、将计算公式输入控制系统。(3)、将织物的信息、染料的信息和助剂的信息输入控制系统,根据数据库及相应的公式可计算出轧余液浓度的变化,然后根据每次染色所用织物、染料和助剂的种类,计算所需补充的染料原液和助剂。(4)、轧余液先流入分流槽3,再通过第一管道51进入回流槽4,流量检测部件66将检测到的流量数据及时输送至控制系统。(5)、回流槽4上方设置多个染料原液储罐和助剂储罐,染料原液储罐通过第四管道与原料混合槽71相连接,助剂储罐通过第五管道与原料混合槽71相连接,第四管道上设置第一流量控制泵,第五管道上设置第二流量控制泵,原料混合槽71通过第三管道53与回流槽4相连接,第三管道53上设置有第四流量控制泵64。控制系统通过公式计算出所有所需补充的染料原液和助剂的量,再控制第一流量控制泵、第二流量控制泵分别进行染料原液和助剂的补加,补加的染料原液和助剂在原料混合槽71中混合均匀后,第四流量控制泵64将原料混合槽71中的物料加入回流槽4中。此处,染料原液和助剂先在原料混合槽71中混合后,再连续通入回流槽4中,原料混合槽71中混合好的染料原液和助剂通入回流槽4中的流量为染料原液通入原料混合槽71中的流量与助剂通入原料混合槽71中的流量的总和(即W补料)。轧余液与补加的染料原液和助剂混合均匀后形成返回液,再由第三流量控制泵63在控制系统的的控制下输送返回液进入染液槽1。返回液返回染液槽1的流量数据由轧余液流量检测部件66和第四流量控制泵64的流量总和乘以一定的系数算得。(6)、返回液返回染液槽1的流量数据再返回控制系统,控制系统通过该流量和实验积累的织物上染率数据计算初始染液补充的量,该数量再通过控制系统控制初始染液的添加速度。参数和计算公式现定义与染料相关的参数见表1。表1染料的参数定义参数定义单位拼色染料1拼色染料2拼色染料3拼色染料4原料浓度g/LU1U2U3U4染液初始浓度g/LC1C2C3C4织物上染率%X1X2X3X4现定义与助剂相关的参数见表2:表2助剂的参数定义参数定义单位助剂1助剂2助剂3助剂4原料浓度g/LQ1Q2Q3Q4助剂初始浓度g/LP1P2P3P4织物携带率%Y1Y2Y3Y4另外定义水在织物上的携带率为X0,单位为%,织物运行速度为V,单位m/s;织物幅宽为S,单位为m,织物单位面积质量为M,单位为g/m2。定义轧余液产生的速度为W0,单位L/s,W0即为流量检测部件66检测到的流量数据。本实用新型所载“初始染液”为染色加工开始前配置好的染液,即将染料原液、助剂以及水按照设定配方配比混合得到的染液,其中,染液储罐9以及染色设备开始工作时染液槽1中盛装的染液均为初始染液。本实用新型所载“返回液”为向回流槽4中添加的染料原液、助剂以及从分流槽3流向回流槽4的轧余液混合所形成。本实用新型中的染料原液是指分散染料与十二烷基硫酸钠、甘油、分散剂、水、醋酸等配制成的染料原液。上表中,原料浓度是指染料和助剂本身的浓度,染液初始浓度是指染料和助剂在初始染液中的浓度。织物携带率为水或者某一种助剂在浸轧过程发生后,该成分在单位面积织物上携带的重量与同等面积织物重量的比,单位为%。(根据织物材质、助剂性质试验积累总结出来的定值)。上染率为染料在浸轧过程发生后,该染料在单位面积织物上携带的重量与同等面积织物重量的比,单位为%。(根据织物材质、染料性质试验积累总结出来的定值)。本实用新型为红、橙、蓝三原色和黑色共设置4个染料参数,若实际生产时少于4个则忽略多余参数;本实用新型除(分散剂在染料原液中已经加入,无需另外补加,所以不设置分散剂参数)匀染剂参数外,还设置了3个其他助剂参数(共4个参数),若实际生产时其他助剂少于4个则忽略多余参数。助剂1为匀染剂,助剂2、助剂3、助剂4为其他不确定的助剂,根据生产需要选择。计算公式见表3:表3各种原料需补加的流量计算公式公式编号公式所得数据单位数据代号及含义公式1VSM(1000X1-C1X0)/1000U1L/sW1,计算染料原液1补加量公式2VSM(1000X2-C2X0)/1000U2L/sW2,计算染料原液2补加量公式3VSM(1000X3-C3X0)/1000U3L/sW3,计算染料原液3补加量公式4VSM(1000X4-C4X0)/1000U4L/sW4,计算染料原液4补加量公式5VSM(1000Y1-P1X0)/1000Q1L/sW5,计算助剂1补加量公式6VSM(1000Y2-P2X0)/1000Q2L/sW6,计算助剂2补加量公式7VSM(1000Y3-P3X0)/1000Q3L/sW7,计算助剂3补加量公式8VSM(1000Y4-P4X0)/1000Q4L/sW8,计算助剂4补加量公式9W1+W2+W3+W4+W5+W6+W7+W8L/sW9,计算混合原料补加量,即W补料公式10(0.9~1.0)(W0+W9))L/sW10,计算返回液返回染液槽的流量,即W返回公式11(1.1~1.2)(VSMX0/1000)L/sW11,计算初始染液添加量,即W染液染色方法如下:将分散染料、十二烷基硫酸钠、甘油、分散剂以20~30wt%、5~7wt%、2~3wt%、3~5wt%的质量分数,加水搅拌配置成悬浊液,加入研磨机研磨到分散染料颗粒的粒径30~50nm,加醋酸调节pH值至5.5~6.0,其中分散剂按照专利号为201710343323.4的专利中的实施例一的方法制备,其中分散染料为分散红S-5BL、分散橙S-4RL、分散蓝S-3BG、分散黑EX-SF其中的一种,分别使用这四种染料进行上述操作,制成染料原液1、染料原液2、染料原液3、染料原液4,备用,将染料原液1、染料原液2、染料原液3、染料原液4中取用一部分分别加入到第一染料原液储罐111、第二染料原液储罐112、第三染料原液储罐113、第四染料原液储罐114。按照打样配色方案,将所需要的染料原液中的一种或几种与水混合,再按照一定的比例加入匀染剂,按生产需求分别加入渗透剂、增稠剂、增深剂等。其中染料原液从上一步骤制得,匀染剂按照专利号为201810173941.3的专利中的实施例一制备,然后将此染液加入到染液储罐9中。匀染剂按照40~50%的比例加入水中,并用醋酸调节pH值为5.5~6.0之间,搅拌溶解均匀后,加入到第一助剂储罐121,并分别将渗透剂、增稠剂、增深剂加入到第二助剂储罐122、第三助剂储罐123、第四助剂储罐124中。选用一批长度10000米,宽度1.6米整门幅退浆后的梭织涤纶织物用于生产,根据计算公式1、计算公式2、计算公式3、计算公式4、计算公式5、计算公式6、计算公式7、计算公式8、计算公式9计算各流量控制泵的流量,并将对应的计算数据分别输入第一一流量控制泵611、第一二流量控制泵612、第一三流量控制泵613、第一四流量控制泵614、第二一流量控制泵621、第二二流量控制泵622、第二三流量控制泵623、第二四流量控制泵624、第四流量控制泵64,染色机器开动以后,第一导布辊21和第一一流量控制泵611、第一二流量控制泵612、第一三流量控制泵613、第一四流量控制泵614、第二一流量控制泵621、第二二流量控制泵622、第二三流量控制泵623、第二四流量控制泵624以及第四流量控制泵64同时启动,根据织物厚度调节织物运行速度为50~100m/min,第一导布辊21带动织物进入染液槽1,织物与染液接触,开始染色,同时第一一流量控制泵611、第一二流量控制泵612、第一三流量控制泵613、第一四流量控制泵614、第二一流量控制泵621、第二二流量控制泵622、第二三流量控制泵623、第二四流量控制泵624、第四流量控制泵64同时开始补加染液和原料,上色后的织物经过均匀轧车2的轧压,再经第三导布辊26引导依次进入烘箱进行烘干和发色。均匀轧车压力范围为0.3~0.4MPa,轧余液进入分流槽3,经分流槽3底部流量检测部件66的检测通过第一管道51流入回流槽4,流量计读数记录为W0,打开回流槽4底部气泵81,对回流槽4内液体进行搅拌,控制系统按照计算公式9计算第四流量控制泵64的控制流量,并将数据反馈给第四流量控制泵64,将补料连续通入回流槽4。按照计算公式10计算第三流量控制泵63的控制流量,并将数据反馈给第四流量控制泵63,使回流槽4中的返回液按照该数据流量再返回染液槽1,按照计算公式11计算第五流量控制泵65的控制流量,并将数据反馈给第四流量控制泵65,使染液储罐9中的染液按照该数据流量流入染液槽1,使染液槽1内液面基本保持不变。织物经均匀轧车2轧压后进入行程120米的烘箱,于100~105℃烘干,再进入行程200米的高温焙烘机于180~185℃焙烘,即得成品。测试其头尾色差。实施例一染料原液制备过程中如上述染色方法所述,其中分散染料、十二烷基硫酸钠、甘油、分散剂的质量分数分别为:20wt%、3wt%、2wt%、1wt%,选用400D×300D的牛津布进行染色,该牛津布带水率为X0=58%,单位面积质量M=203g/m2,幅宽S=1.6m,设定织物运行速度V=1m/s进行染色,其中渗透剂选用杭州久灵化工有限公司生产的快T,所用染料和助剂的用量和参数见表4:表4实施例一所需染料和助剂的参数参数定义单位分散红S-5BL分散橙S-4RL分散蓝S-3BG匀染剂渗透剂原料浓度g/LU1=200U2=200U3=200Q1=48Q2=53初始浓度g/LC1=70C2=10C3=15P1=11.2P2=4.4织物携带率%X1=4.82X2=0.71X3=1.01Y1=0.92Y2=0.32以上述染料及助剂用量和设备运行参数,按照表3计算各染料原液和助剂的补加量见表5:表5实施例一中各种原料需补加的流量计算公式编号计算所得数值所得数据单位数值用途公式1W1=0.0123L/s计算分散红S-5BL原液补加量公式2W2=0.0021L/s计算分散橙S-4RL原液补加量公式3W3=0.0023L/s计算分散蓝S-3BG原液加量公式5W5=0.0183L/s计算匀染剂补加量公式6W6=0.0040L/s计算渗透剂补加量公式9W9=0.0390L/sW9,计算混合原料补加量公式10W10=0.5086L/sW10,计算返回液返回染液槽的流量公式11W11=0.2166L/sW11,计算初始染液添加量按照表4所计算的流量控制各个补加染料原液和助剂的管路进行原料补充,其中计算公式10的参数根据实验和经验选择为0.98,计算公式11的参数根据实验和经验选择为1.15,将均匀轧车2压力设定为0.4MPa,测得轧余液从分流槽3向回流槽4流过的瞬间流量W0为0.48L/s,烘干温度设定为105℃,发色温度设定为185℃,织物出高温焙烘机后得1#样品,测其头尾色差。实施例二染料原液制备过程中如上述染色方法所述,其中分散染料、十二烷基硫酸钠、甘油、分散剂的质量分数分别为:20wt%、3wt%、2wt%、1wt%,选用190T的涤塔夫进行染色,该牛津布带水率为X0=46%,单位面积质量M=58g/m2,幅宽S=1.6m,设定织物运行速度V=1.2m/s进行染色,其中渗透剂选用杭州久灵化工有限公司生产的快T,增稠剂采用传化智联股份有限公司生产的TF-315增稠剂,增深剂采用上海望界化工有限公司生产的FMBlackKD-500增深剂,所用染料和助剂的用量和参数见表6:表6实施例二所需染料和助剂的参数参数定义单位分散红S-5BL分散黑EX-SF匀染剂增稠剂增深剂原料浓度g/LU1=200U4=200Q1=48Q3=27Q4=56初始浓度g/LC1=7C4=150P1=8.5P3=3.8P4=12织物携带率%X1=0.36X4=7.74Y1=0.44Y3=0.28Y4=0.62以上述染料及助剂用量和设备运行参数,按照表3计算各染料原液和助剂的补加量见表7:表7实施例一中各种原料需补加的流量计算公式编号计算所得数值所得数据单位数值用途公式1W1=0.0002L/s计算分散红S-5BL原液补加量公式4W2=0.0047L/s计算分散黑EX-SF原液补加量公式5W3=0.0011L/s计算匀染剂补加量公式7W5=0.0043L/s计算增稠剂补加量公式8W6=0.0014L/s计算增深剂补加量公式9W9=0.0117L/sW9,计算混合原料补加量公式10W10=0.3605L/sW10,计算返回液返回染液槽的流量公式11W11=0.0615L/sW11,计算初始染液添加量按照表4所计算的流量控制各个补加染料原液和助剂的管路进行原料补充,其中计算公式10的参数根据实验和经验选择为0.97,计算公式11的参数根据实验和经验选择为1.20,将均匀轧车压力设定为0.3MPa,测得轧余液从分流槽3向回流槽1流过的瞬间流量W0为0.36L/s,烘干温度设定为100℃,发色温度设定为180℃,织物出高温焙烘机后得2#样品,测其头尾色差。对比例染料原液制备过程中如上述染色方法所述,其中分散染料、十二烷基硫酸钠、甘油、分散剂的质量分数分别为:20wt%、3wt%、2wt%、1wt%,选用400D×300D的牛津布进行染色,该牛津布带水率为X0=58%,单位面积质量M=203g/m2,幅宽S=1.6m,设定织物运行速度V=1m/s进行染色,其中渗透剂选用杭州久灵化工有限公司生产的快T,所用染料和助剂的用量见表8:表8对比例所需染料和助剂的用量参数定义单位分散红S-5BL分散橙S-4RL分散蓝S-3BG匀染剂渗透剂原料浓度g/LU1=200U2=200U3=200Q1=48Q2=53初始浓度g/LC1=70C2=10C3=15P1=11.2P2=4.4通过公式11计算初始染液的补充量为0.2L/s,染色开始后打开染液补加的第五流量控制泵65,关闭第一流量控制泵与第二流量控制泵。打开第三流量控制泵63,将流量检测部件66测得的瞬时流量直接反馈给第三流量控制泵63,以此流量将轧余液返回到染液槽1。将均匀轧车压力设定为0.4MPa,烘干温度设定为105℃,发色温度设定为185℃,织物出高温焙烘机后得3#样品,测其头尾色差。样品检测方法及检测结果:样品头尾色差利用上海仪电物理光学仪器有限公司生产的WSC-S型色差计进行检测。表91#、2#、3#色差数据对比测试项目1#2#3#头尾色差(NBS)0.020.030.78备注:1NBS相当于人类视觉阈值的5倍,0.2NBS以下人类视觉即认为无色差。以上对本实用新型做了详尽的描述,其目的在于让熟悉此领域技术的人士能够了解本实用新型的内容并加以实施,并不能以此限制本实用新型的保护范围,凡根据本实用新型的精神实质所作的等效变化或修饰,都应涵盖在本实用新型的保护范围内。当前第1页1 2 3