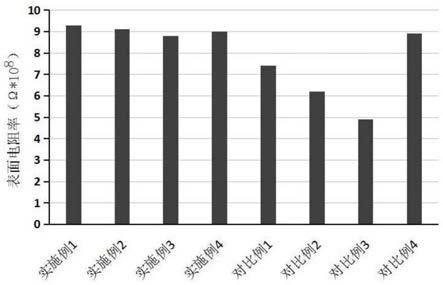
1.本发明涉及家具纺织用品技术领域,具体涉及一种抗静电、耐磨沙发面料及其制备方法。
背景技术:2.沙发是一种非常普遍的家具,从外部来看,主要分为皮质沙发和织物沙发。皮质沙发质感出色,显高档,但是保养复杂,而且价格高,目前使用最多的是织物沙发,织物沙发价格便宜,而且织物沙发通常会在沙发外部包裹一层沙发面料,沙发面料色彩多样化,可以更好的与家装的风格相呼应。
3.日常生活中,沙发面料是由棉纤维、亚麻纤维及化纤纤维中的几种成分经简单织造而成,获得的成品面料的抗静电效果一般,而且沙发表面较为干燥,使得沙发面料在使用时会形成并积累静电,进而吸附空气中的灰尘等,使得沙发面料容易变脏,而且由于沙发紧靠插座放置,静电作用严重时会导致出现火灾;此外,现有的沙发面料的耐磨性较差,长期使用后沙发表面经常出现磨痕而影响美观,而且还容易出现磨破、磨穿等现象,使得沙发内部的填充物外露,缩短沙发的使用寿命。
技术实现要素:4.为了解决上述背景技术中存在的问题,本发明的目的在于提供一种抗静电、耐磨沙发面料,其具有优异的耐磨能力和抗静电性能。此外,本发明还提供一种抗静电、耐磨沙发面料的制备方法。
5.为了实现上述目的,本发明采用以下技术方案:
6.本发明的第一方面,提供一种抗静电、耐磨沙发面料,包括面料层,所述面料层表面上设有抗静电层,所述面料层包括如下重量份的原料:亚麻纤维40-60份、竹纤维30-40份、抗静电改性聚酯纤维80-100份和氨纶纤维50-80份;氨纶纤维可选用抗磨抗褶皱能力好的聚氨基甲酸酯纤维。
7.其中,所述抗静电改性聚酯纤维制备方法如下:
8.(1)聚酯纤维的预处理:将聚酯纤维用丙酮溶液浸泡30-40min,用去离子水反复清洗,然后再将聚酯纤维浸入氢氧化钠溶液中浸泡,在50-60℃的条件下震荡10-20min,然后取出,用去离子水反复洗涤,再进行干燥处理;
9.(2)聚酯纤维的抗静电改性:将经过预处理后的聚酯纤维放入氧化石墨烯溶液中,加热煮沸、震荡处理20-30min,再用去离子水反复清洗后进行烘干处理,即得抗静电改性聚酯纤维;其中,所述氧化石墨烯溶液由质量比为(3-8):(4-6):(2-5):(12-18)可溶性淀粉、氧化石墨烯、乙醇、去离子水的混合配置而成。
10.本发明中通过将聚酯纤维先后采用丙酮溶液及氢氧化钠溶液进行水解预处理,使得聚酯纤维表面出现沟槽或微孔,使得氧化石墨烯可牢固附着在聚酯纤维表面,有效的提升了聚酯纤维的抗静电能力和力学性能,提升了沙发面料的使用寿命和抗静电能力。
11.优选地,所述聚酯纤维的制备过程如下:
12.(1)选取聚对苯二甲酸乙二醇酯母粒80-110份、聚氨基甲酸酯母粒60-70份、硅烷偶联剂1-3份、纳米二氧化硅10-15份、纳米氧化镁6-8份、纳米氮化硅10-12份充分混合;
13.(2)将混合后的原料加入至螺杆挤出机中挤出成粒,制得混合母粒;
14.(3)再将混合母粒经过湿法纺织即得。
15.本发明中选用硅烷偶联剂、纳米二氧化硅、纳米氧化镁和纳米氮化硅对聚氨酯纤维进行耐磨改性,使得聚酯纤维的耐磨性得到极大的提升,进而有效提升了沙面面料长时间时候后的耐磨效果。
16.优选地,所述双螺杆挤出机从加料侧至模头侧分为四段进行分段控温加热,一段温度为150-160℃,二段温度为170-190℃,三段温度为200-205℃,四段温度为210-220℃。
17.优选地,所述丙酮溶液的质量分数为20-30%。
18.优选地,所述氢氧化钠溶液的浓度为0.3-0.6mol/l。
19.本发明的第二方面,提供一种上述抗静电、耐磨沙发面料的制备方法,包括以下步骤:
20.s1、胚料的制备:将亚麻纤维、竹纤维、改性聚酯纤维和氨纶纤维按照相应的配比经过纺织制得胚料;
21.s2、染色整理:将纺织好的胚料放入染缸内采用染料进行染色处理;
22.s3、柔软平滑处理:向染缸内加入柔软剂和平滑剂处理10-20min;
23.s4、抗静电处理:向经过染色处理后的胚料表面上喷涂抗静电溶液,经通风干燥形成抗静电层;
24.s5、烘干定型:将经过抗静电处理后的面料在80-100℃下进行烘干处理20-30min,即得成品。
25.优选地,所述抗静电溶液由质量比为1:(1-2):(0.2-0.4):(8-12)的碳纳米管粉末、十二烷基磺酸钠、聚乙二醇、体积浓度为20%的乙醇水溶液混合制备而成。
26.本发明中通过抗静电溶液对胚料表面进行抗静电处理,抗静电溶液中的碳纳米管均匀分散在胚料表面形成抗静电层,在布料表面上形成导电网络,有效的将沙发面料表面的电荷分散导出,避免沙发面料表面静电产生,其协同抗静电改性后的聚酯纤维的抗静电效果,显著提升沙发面料的抗静电能力。
27.与现有技术相比,本发明具有如下有益效果:
28.本发明中的沙发面料选用亚麻纤维、竹纤维、抗静电改性聚酯纤维和氨纶纤维作为原料,亚麻纤维具有良好的抗静电性,可以避免沙发表面灰尘等的附着,竹纤维的透气性好、吸湿性好,避免沙发表面过于干燥,提升沙发面料的抗静电能力,氨纶纤维具有一定的抗磨性能,提升沙发面料的耐磨性和耐磨持久性;通过对聚酯纤维先后采用丙酮溶液及氢氧化钠溶液进行水解预处理,使得聚酯纤维表面出现沟槽或微孔,使得氧化石墨烯可牢固附着在聚酯纤维表面,有效的提升了聚酯纤维的抗静电能力和力学性能,提升了沙发面料的使用寿命和抗静电能力;同时还对胚布表面采用抗静电溶液进行抗静电处理,抗静电溶液中的碳纳米管均匀分散在胚料表面形成抗静电层,在布料表面上形成导电网络,有效的将沙发面料表面的电荷分散导出,避免沙发面料表面静电产生,其协同抗静电改性后的聚酯纤维的抗静电效果,显著提升沙发面料的抗静电能力。
附图说明
29.下面结合附图与具体实施例对本发明作进一步详细说明。
30.图1为本发明中沙发面料的层状结构示意图;
31.图2为本发明中聚酯纤维的制备工艺流程图;
32.图3为本发明中抗静电改性聚酯纤维的制备工艺流程图;
33.图4为本发明中沙发面料的制备工艺流程图;
34.图5为本发明中实施例1至实施例4、对比例1至对比例4中制得沙发面料的抗静电性变化曲线图;
35.图6为本发明中实施例1至实施例4、对比例1至对比例4中制得沙发面料的耐磨次数变化曲线;
36.其中,具体附图标记为:面料层1,抗静电层2。
具体实施方式
37.实施例1
38.一种抗静电、耐磨沙发面料,如图1所示,包括面料层1,面料层1表面上设有抗静电层2,面料层1包括如下原料:亚麻纤维480g、竹纤维360g、抗静电改性聚酯纤维930g和聚氨基甲酸酯纤维650g。
39.其中,抗静电改性聚酯纤维制备方法如图3所示:
40.(1)聚酯纤维的制备如图2所示:
41.a、选取聚对苯二甲酸乙二醇酯母粒820g、聚氨基甲酸酯母粒630g、硅烷偶联剂20g、纳米二氧化硅120g、纳米氧化镁60g、纳米氮化硅100g充分混合;
42.b、将混合后的原料加入至螺杆挤出机中挤出成粒,制得混合母粒,双螺杆挤出机从加料侧至模头侧分为四段进行分段控温加热,一段温度为150-160℃,二段温度为170-190℃,三段温度为200-205℃,四段温度为210-220℃;
43.c、再将混合母粒经过湿法纺织即得;
44.(2)聚酯纤维的预处理:将聚酯纤维用丙酮溶液浸泡30-40min,用去离子水反复清洗,然后再将聚酯纤维浸入氢氧化钠溶液中浸泡,在50-60℃的条件下震荡10-20min,然后取出,用去离子水反复洗涤,再进行干燥处理;其中,丙酮溶液的质量分数为20%,氢氧化钠溶液的浓度为0.5mol/l;
45.(3)聚酯纤维的抗静电改性:将经过预处理后的聚酯纤维放入氧化石墨烯溶液中,加热煮沸、震荡处理20-30min,再用去离子水反复清洗后进行烘干处理,即得抗静电改性聚酯纤维;其中,氧化石墨烯溶液由质量比为5:4:3:16可溶性淀粉、氧化石墨烯、乙醇、去离子水的混合配置而成。
46.抗静电、耐磨沙发面料的制备方法,如图4所示,包括以下步骤:
47.s1、胚料的制备:将亚麻纤维、竹纤维、改性聚酯纤维和氨纶纤维按照相应的配比经过纺织制得胚料;
48.s2、染色整理:将纺织好的胚料放入染缸内采用染料进行染色处理;
49.s3、柔软平滑处理:向染缸内加入柔软剂和平滑剂处理10-20min;
50.s4、抗静电处理:向经过染色处理后的胚料表面上喷涂抗静电溶液,经通风干燥形
成抗静电层2;其中,抗静电溶液由质量比为1:1:0.3:9的碳纳米管粉末、十二烷基磺酸钠、聚乙二醇、体积浓度为20%的乙醇水溶液混合制备而成;
51.s5、烘干定型:将经过抗静电处理后的面料在80-100℃下进行烘干处理20-30min,即得成品。
52.实施例2
53.一种抗静电、耐磨沙发面料,如图1所示,包括面料层1,面料层1表面上设有抗静电层2,面料层1包括如下原料:亚麻纤维400g、竹纤维400g、抗静电改性聚酯纤维1000g和聚氨基甲酸酯纤维500g。
54.其中,抗静电改性聚酯纤维制备方法如图3所示:
55.(1)聚酯纤维的制备如图2所示:
56.a、选取聚对苯二甲酸乙二醇酯母粒960g、聚氨基甲酸酯母粒680g、硅烷偶联剂10g、纳米二氧化硅100g、纳米氧化镁60g、纳米氮化硅100g充分混合;
57.b、将混合后的原料加入至螺杆挤出机中挤出成粒,制得混合母粒,双螺杆挤出机从加料侧至模头侧分为四段进行分段控温加热,一段温度为150-160℃,二段温度为170-190℃,三段温度为200-205℃,四段温度为210-220℃;
58.c、再将混合母粒经过湿法纺织即得;
59.(2)聚酯纤维的预处理:将聚酯纤维用丙酮溶液浸泡30-40min,用去离子水反复清洗,然后再将聚酯纤维浸入氢氧化钠溶液中浸泡,在50-60℃的条件下震荡10-20min,然后取出,用去离子水反复洗涤,再进行干燥处理;其中,丙酮溶液的质量分数为30%,氢氧化钠溶液的浓度为0.3mol/l;
60.(3)聚酯纤维的抗静电改性:将经过预处理后的聚酯纤维放入氧化石墨烯溶液中,加热煮沸、震荡处理20-30min,再用去离子水反复清洗后进行烘干处理,即得抗静电改性聚酯纤维;其中,氧化石墨烯溶液由质量比为3:6:2:15可溶性淀粉、氧化石墨烯、乙醇、去离子水的混合配置而成。
61.抗静电、耐磨沙发面料的制备方法,如图4所示,包括以下步骤:
62.s1、胚料的制备:将亚麻纤维、竹纤维、改性聚酯纤维和氨纶纤维按照相应的配比经过纺织制得胚料;
63.s2、染色整理:将纺织好的胚料放入染缸内采用染料进行染色处理;
64.s3、柔软平滑处理:向染缸内加入柔软剂和平滑剂处理10-20min;
65.s4、抗静电处理:向经过染色处理后的胚料表面上喷涂抗静电溶液,经通风干燥形成抗静电层2;其中,抗静电溶液由质量比为1:2:0.3:8的碳纳米管粉末、十二烷基磺酸钠、聚乙二醇、体积浓度为20%的乙醇水溶液混合制备而成;
66.s5、烘干定型:将经过抗静电处理后的面料在80-100℃下进行烘干处理20-30min,即得成品。
67.实施例3
68.一种抗静电、耐磨沙发面料,如图1所示,包括面料层1,面料层1表面上设有抗静电层2,面料层1包括如下原料:亚麻纤维540g、竹纤维320g、抗静电改性聚酯纤维860g和聚氨基甲酸酯纤维800g。
69.其中,抗静电改性聚酯纤维制备方法如图3所示:
70.(1)聚酯纤维的制备如图2所示:
71.a、选取聚对苯二甲酸乙二醇酯母粒800g、聚氨基甲酸酯母粒700g、硅烷偶联剂30g、纳米二氧化硅150g、纳米氧化镁80g、纳米氮化硅120g充分混合;
72.b、将混合后的原料加入至螺杆挤出机中挤出成粒,制得混合母粒,双螺杆挤出机从加料侧至模头侧分为四段进行分段控温加热,一段温度为150-160℃,二段温度为170-190℃,三段温度为200-205℃,四段温度为210-220℃;
73.c、再将混合母粒经过湿法纺织即得;
74.(2)聚酯纤维的预处理:将聚酯纤维用丙酮溶液浸泡30-40min,用去离子水反复清洗,然后再将聚酯纤维浸入氢氧化钠溶液中浸泡,在50-60℃的条件下震荡10-20min,然后取出,用去离子水反复洗涤,再进行干燥处理;其中,丙酮溶液的质量分数为20%,氢氧化钠溶液的浓度为0.6mol/l;
75.(3)聚酯纤维的抗静电改性:将经过预处理后的聚酯纤维放入氧化石墨烯溶液中,加热煮沸、震荡处理20-30min,再用去离子水反复清洗后进行烘干处理,即得抗静电改性聚酯纤维;其中,氧化石墨烯溶液由质量比为8:5:5:18可溶性淀粉、氧化石墨烯、乙醇、去离子水的混合配置而成。
76.抗静电、耐磨沙发面料的制备方法,如图4所示,包括以下步骤:
77.s1、胚料的制备:将亚麻纤维、竹纤维、改性聚酯纤维和氨纶纤维按照相应的配比经过纺织制得胚料;
78.s2、染色整理:将纺织好的胚料放入染缸内采用染料进行染色处理;
79.s3、柔软平滑处理:向染缸内加入柔软剂和平滑剂处理10-20min;
80.s4、抗静电处理:向经过染色处理后的胚料表面上喷涂抗静电溶液,经通风干燥形成抗静电层2;其中,抗静电溶液由质量比为1:1:0.2:12的碳纳米管粉末、十二烷基磺酸钠、聚乙二醇、体积浓度为20%的乙醇水溶液混合制备而成;
81.s5、烘干定型:将经过抗静电处理后的面料在80-100℃下进行烘干处理20-30min,即得成品。
82.实施例4
83.一种抗静电、耐磨沙发面料,如图1所示,包括面料层1,面料层1表面上设有抗静电层2,面料层1包括如下原料:亚麻纤维600g、竹纤维300g、抗静电改性聚酯纤维800g和聚氨基甲酸酯纤维580g。
84.其中,抗静电改性聚酯纤维制备方法如图3所示:
85.(1)聚酯纤维的制备如图2所示:
86.a、选取聚对苯二甲酸乙二醇酯母粒1100g、聚氨基甲酸酯母粒600g、硅烷偶联剂20g、纳米二氧化硅120g、纳米氧化镁60g、纳米氮化硅100g充分混合;
87.b、将混合后的原料加入至螺杆挤出机中挤出成粒,制得混合母粒,双螺杆挤出机从加料侧至模头侧分为四段进行分段控温加热,一段温度为150-160℃,二段温度为170-190℃,三段温度为200-205℃,四段温度为210-220℃;
88.c、再将混合母粒经过湿法纺织即得;
89.(2)聚酯纤维的预处理:将聚酯纤维用丙酮溶液浸泡30-40min,用去离子水反复清洗,然后再将聚酯纤维浸入氢氧化钠溶液中浸泡,在50-60℃的条件下震荡10-20min,然后
取出,用去离子水反复洗涤,再进行干燥处理;其中,丙酮溶液的质量分数为25%,氢氧化钠溶液的浓度为0.4mol/l;
90.(3)聚酯纤维的抗静电改性:将经过预处理后的聚酯纤维放入氧化石墨烯溶液中,加热煮沸、震荡处理20-30min,再用去离子水反复清洗后进行烘干处理,即得抗静电改性聚酯纤维;其中,氧化石墨烯溶液由质量比为6:4:4:12可溶性淀粉、氧化石墨烯、乙醇、去离子水的混合配置而成。
91.上述抗静电、耐磨沙发面料的制备方法,如图4所示,包括以下步骤:
92.s1、胚料的制备:将亚麻纤维、竹纤维、改性聚酯纤维和氨纶纤维按照相应的配比经过纺织制得胚料;
93.s2、染色整理:将纺织好的胚料放入染缸内采用染料进行染色处理;
94.s3、柔软平滑处理:向染缸内加入柔软剂和平滑剂处理10-20min;
95.s4、抗静电处理:向经过染色处理后的胚料表面上喷涂抗静电溶液,经通风干燥形成抗静电层2;其中,抗静电溶液由质量比为1:1:0.4:10的碳纳米管粉末、十二烷基磺酸钠、聚乙二醇、体积浓度为20%的乙醇水溶液混合制备而成;
96.s5、烘干定型:将经过抗静电处理后的面料在80-100℃下进行烘干处理20-30min,即得成品。
97.对比例1
98.对比例1为实施例1的对比实验例,两者区别点在于:对比例1中聚酯纤维未进行预处理和抗静电改性,其余均与实施例1相同。
99.对比例2
100.对比例2为实施例1的对比实验例,两者区别点在于:对比例2中未对染色后的胚料表面进行抗静电处理,其余均与实施例1相同。
101.对比例3
102.对比例3为实施例1的对比实验例,两者区别点在于:对比例3中聚酯纤维未进行预处理和抗静电改性,且未对染色后的胚料进行抗静电改性其余均与实施例1相同。
103.对比例4
104.对比例4为实施例1的对比实验例,两者区别点在于:对比例4中聚酯纤维制备过程中未加入硅烷偶联剂、纳米二氧化硅、纳米氧化镁和纳米氮化硅,其余均与实施例1相同。
105.实验例
106.分别对实施例1至实施例4、对比例1至对比例4中制得的沙发面料进行抗静电性和耐磨性测试。
107.抗静电性测试过程如下:按照gb/t24249-2009标准,测试沙发面料的表面电阻率。
108.耐磨性测试过程如下:
109.用马丁代尔耐磨仪对沙发面料进行耐磨性能测试分析。试样夹持器的质量为200g,法码的质量为300g,摩擦头的有效直径为30.0
±
0.5mm,磨料为标准羊毛磨料,测试前将样品在松弛状态下置于测试环境中18h以上,在测试过程中每隔1000次耐磨循环次数,暂停试验,将夹持器取下,用毛刷轻轻地清理试样和磨料表面的碎屑,然后再继续进行试验,直至试样出现明显的破洞为止,记录此时读数盘上的数值,取3组试样的平均值即为试样的耐磨循环次数。
110.具体测试结果见表1。
111.表1
[0112] 表面电阻率(ω)耐磨次数(次)实施例19.3
×
1082.9
×
104实施例29.1
×
1082.7
×
104实施例38.8
×
1082.6
×
104实施例49.0
×
1082.7
×
104对比例17.4
×
1082.5
×
104对比例26.2
×
1082.6
×
104对比例34.9
×
1082.5
×
104对比例48.9
×
1081.2
×
104[0113]
由表1中测试结果及图5中抗静电性变化曲线图可看出,实施例1至实施例4、对比例4制得的沙发面料的表面电阻率达到8.5
×
108以上,而对比例1至对比例3制得的沙发面料的表面电阻率低于8.5
×
108,尤其是对比例3制得的沙发面料的表面电阻率最低,说明本发明中通过对聚酯纤维进行抗静电处理,并对胚布表面采用抗静电溶液进行抗静电处理,两者协同作用,显著提升沙发面料的抗静电能力。
[0114]
由表1中测试结果及图6中的耐磨次数变化曲线可看出,实施例1至实施例4及对比例1至对比例3中制得的沙发面料的耐磨次数相对于对比例4制得的沙发面料的耐磨次数提升了一倍多,说明本发明中采用硅烷偶联剂、纳米二氧化硅、纳米氧化镁和纳米氮化硅对聚氨酯纤维进行耐磨改性,使得聚酯纤维的耐磨性得到极大的提升,进而有效提升了沙面面料长时间使用后的耐磨效果。
[0115]
以上应用了具体个例对本发明进行阐述,只是用于帮助理解本发明,并不用以限制本发明。对于本发明所属技术领域的技术人员,依据本发明的思想,还可以做出若干简单推演、变形或替换。