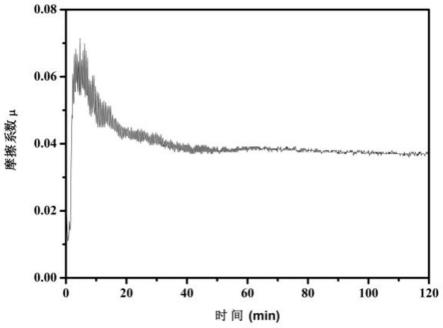
1.本发明涉及复合材料领域和润滑材料技术领域,尤其涉及一种自润滑纤维织物及其制备方法、自润滑衬垫织物复合材料及其制备方法。
背景技术:2.轴承作为工业领域的关键器件,它的主要功能是支撑机械旋转体,降低其运动过程中的摩擦系数,并保证回转精度。自润滑关节轴承作为高承载、耐磨损、自调心和转动等重要功能部件,在航空、航天、先进武器系统和高端民用领域中的应用非常广泛,已成为航空发动机、起落架、方向舵、平尾、襟翼等部位不可或缺的部件。自润滑衬垫是自润滑关节轴承中非常重要的组成部分,可以起到减摩抗磨、隔离金属、抗冲击,延长轴承服役寿命等作用。自润滑衬垫还具有强度高、免维护等优点,而且在高温、重载及高频等苛刻服役环境中表现出优异的自润滑性能和抗磨性能。随着高新技术领域对轴承性能的要求越来越高,对自润滑衬垫的综合性能也提出了越来越高的要求。
3.对于自润滑衬垫织物复合材料,其增强体为增强纤维和润滑纤维(ptfe)混编得到的二维织物,在整个复合材料中纤维-树脂之间的界面对复合材料的性能具有决定性的影响。纤维-树脂之间的界面表现出非常好的结合强度,材料内部应力只能通过纤维-树脂界面微裂纹的持续产生和扩展进行释放;界面结合强度过差,复合材料的力学强度和摩擦学性能会大幅度降低。因此,需要在纤维树脂之间构筑强度和韧性相匹配的界面修饰层,最大限度的提升自润滑衬垫织物复合材料的力学性能和摩擦学性能。
4.目前,针对自润滑衬垫织物复合材料的改性主要采用化学刻蚀、表面涂附涂层、接枝高分子聚合物等方法,采用上述方法改性制备得到的自润滑衬垫织物复合材料可以达到提升纤维-树脂界面结合强度的目的,并未考虑纤维-树脂的界面韧性。
技术实现要素:5.有鉴于此,本发明的目的在于提供一种自润滑纤维织物及其制备方法、自润滑衬垫织物复合材料及其制备方法。本发明提供的制备方法得到的自润滑纤维织物不仅能够增强纤维-树脂的结合强度,还能提高纤维-树脂的界面韧性。
6.为了实现上述发明目的,本发明提供以下技术方案:
7.本发明提供了一种自润滑纤维织物的制备方法,包括以下步骤:
8.将纤维织物进行等离子体处理,得到活化纤维织物;
9.在所述活化纤维织物的表面生长金属有机骨架化合物,得到金属有机骨架化合物修饰的纤维织物;
10.将所述金属有机骨架化合物修饰的纤维织物浸入刻蚀溶液中,进行刻蚀处理,得到金属氢氧化物负载的纤维织物;所述刻蚀溶液为金属盐乙醇溶液;所述金属盐乙醇溶液中的金属盐和金属有机骨架化合物前驱体溶液中的金属盐一致;
11.将所述金属氢氧化物负载的纤维织物浸入多巴胺-硅烷偶联剂-聚乙烯亚胺复合溶液,进行聚合交联反应,得到所述的自润滑纤维织物。
12.优选地,所述等离子体处理的功率为30w~200w,时间为1min~40min。
13.优选地,所述生长金属有机骨架化合物包括:将所述活化纤维织物浸入金属盐水溶液中,进行负载,然后加入有机化合物水溶液,进行复合反应;所述金属盐水溶液的浓度为0.005mol/l~0.5mol/l;所述有机化合物水溶液的浓度为0.05mol/l~1.2mol/l;所述金属盐水溶液和有机化合物水溶液的体积比为1:(1~3)。
14.优选地,所述金属盐水溶液中金属盐包括过渡金属盐;所述过渡金属盐包括钴离子盐或锌离子盐。
15.优选地,所述金属盐乙醇溶液中金属盐的浓度为0.005mol/l~0.5mol/l。
16.优选地,所述多巴胺-硅烷偶联剂-聚乙烯亚胺复合溶液中,多巴胺的浓度为0.1mg/ml~20mg/ml,硅烷偶联剂的浓度为0.1mg/ml~1g/ml,聚乙烯亚胺的浓度为0.1mg/ml~40mg/ml。
17.本发明还提供了上述技术方案所述的制备方法得到的自润滑纤维织物。
18.本发明还提供了一种自润滑衬垫织物复合材料,包括上述技术方案所述的自润滑纤维织物和树脂;所述树脂包括酚醛树脂、聚酰亚胺树脂或环氧树脂。
19.优选地,所述自润滑衬垫织物复合材料中自润滑纤维织物的质量分数为15~35%。
20.本发明还提供了上述技术方案所述的自润滑衬垫织物复合材料的制备方法,包括以下步骤:
21.将自润滑纤维织物浸渍于树脂中,进行固化,得到所述自润滑衬垫织物复合材料;
22.所述固化的温度为120~300℃,压力为0.1~1mpa,固化时间为30min~6h。
23.本发明提供了一种自润滑纤维织物的制备方法,包括以下步骤:将纤维织物进行等离子体处理,得到活化纤维织物;在所述活化纤维织物的表面生长金属有机骨架化合物,得到金属有机骨架化合物修饰的纤维织物;将所述金属有机骨架化合物修饰的纤维织物浸入刻蚀溶液中,进行刻蚀处理,得到金属氢氧化物负载的纤维织物;所述刻蚀溶液为金属盐乙醇溶液;所述金属盐乙醇溶液中的金属盐和金属有机骨架化合物前驱体溶液中的金属盐一致;将所述金属氢氧化物负载的纤维织物浸入多巴胺-硅烷偶联剂-聚乙烯亚胺复合溶液,进行聚合交联反应,得到所述自润滑纤维织物。本发明对纤维织物进行等离子体处理,增加了纤维织物表面-oh、-nh2等官能团的含量,提高纤维织物表面的活性,有利于后续物质的接枝和聚合。在所述活化纤维织物的表面生长金属有机骨架化合物,进而在纤维织物表面负载一层片状金属有机骨架化合物;将负载了金属有机骨架化合物的纤维织物浸入刻蚀溶液,利用刻蚀溶液中与金属有机骨架化合一致的金属盐对金属有机骨架化合物进行原位刻蚀,在纤维表面构筑垂直于纤维轴向分布的片层状金属氢氧化物,金属氢氧化物作为界面相中的增强组分,提高了纤维织物和树脂间的界面强度;将负载了金属氢氧化物的纤维织物浸入多巴胺-硅烷偶联剂-聚乙烯亚胺复合溶液,进行聚合交联反应,复合溶液中多巴胺、聚乙烯亚胺及硅烷偶联剂的聚合反应,将多巴胺、聚乙烯亚胺及硅烷偶联剂的共聚物修饰到金属氢氧化物片层之间,通过氢键及范德华作用力与金属氢氧化物相互作用,该聚合物作为界面相中的增韧组分,提高了纤维织物和树脂间的界面韧性。本发明的自润滑纤
维织物同时兼具界面增强组分(金属氢氧化物)和界面增韧组分(多巴胺-硅烷偶联剂-聚乙烯亚胺聚合层),在自润滑纤维织物受到外部和内部应力作用时,界面增强组分可以减少裂纹产生,而界面增韧组分可以抑制微裂纹的扩展,进而延长自润滑纤维织物的使用寿命。
24.本发明提供了上述技术方案所述的制备方法得到的自润滑纤维织物。本发明提供的自润滑纤维织物能够在纤维-树脂界面构筑强-韧一体化的界面相,即提升界面结合强度的同时,改善界面韧性。在自润滑纤维织物受到外部和内部应力作用时,强韧界面相中得增强组分可以减少裂纹产生,而增韧组分可以抑制微裂纹的扩展,进而延长自润滑纤维织物的使用寿命。
25.本发明提供了一种自润滑衬垫织物复合材料,包括上述技术方案所述的自润滑纤维织物和树脂;所述树脂包括酚醛树脂、聚酰亚胺树脂或环氧树脂。本发明的自润滑衬垫织物复合材料具有优异的自润滑性能和使用寿命。
附图说明
26.图1为实施例1所得仿生界面相改性自润滑纤维织物复合材料的摩擦系数随时间的变化关系图;
27.图2为实施例2中各自润滑衬垫织物复合材料的摩擦系数随时间的变化关系图;
28.图3为实施例2中各自润滑衬垫织物复合材料的平均摩擦系数图;
29.图4为实施例2中各自润滑衬垫织物复合材料的平均磨损率图;
30.图5为实施例3所得仿生界面相改性自润滑纤维织物树脂复合材料的摩擦系数随时间的变化关系图;
31.图6为实施例4所得仿生界面相改性自润滑纤维织物树脂复合材料的摩擦系数随时间的变化关系图。
具体实施方式
32.本发明提供了一种自润滑纤维织物的制备方法,包括以下步骤:
33.将纤维织物进行等离子体处理,得到活化纤维织物;
34.在所述活化纤维织物的表面生长金属有机骨架化合物,得到金属有机骨架化合物修饰的纤维织物;
35.将所述金属有机骨架化合物修饰的纤维织物浸入刻蚀溶液中,进行刻蚀处理,得到金属氢氧化物负载的纤维织物;所述刻蚀溶液为金属盐乙醇溶液;所述金属盐乙醇溶液中的金属盐和金属有机骨架化合物前驱体溶液中的金属盐一致;
36.将所述金属氢氧化物负载的纤维织物浸入多巴胺-硅烷偶联剂-聚乙烯亚胺复合溶液,进行聚合交联反应,得到所述自润滑纤维织物。
37.在本发明中,如无特殊说明,本发明所用原料均优选为市售产品。
38.本发明将纤维织物进行等离子体处理,得到活化纤维织物。
39.在本发明中,所述纤维织物优选包括芳纶纤维/聚四氟乙烯纤维混纺织物、聚酰亚胺纤维/聚四氟乙烯纤维混纺织物、玻璃纤维/聚四氟乙烯纤维混纺织物或聚醚醚酮纤维/聚四氟乙烯纤维混纺织物。在本发明中,所述纤维织物进行等离子处理前优选进行洗涤;本发明对所述洗涤的试剂和次数不做具体限定,只要能够将纤维织物表面的氧化物等洗涤干
净即可。
40.在本发明中,所述等离子处理的功率优选为30w~200w,进一步优选为100w;时间优选为1min~40min。
41.在本发明中,所述等离子体处理能够增加纤维织物表面-oh、-nh2等官能团的含量,有利于后续物质的接枝和复合。
42.得到活化纤维织物后,本发明在所述活化纤维织物的表面生长金属有机骨架化合物,得到金属有机骨架化合物修饰的纤维织物。
43.在本发明中,所述生长金属有机骨架化合物优选包括:将所述活化纤维织物浸入金属盐水溶液中,进行负载,然后加入有机化合物水溶液,进行复合反应。在本发明中,所述金属盐水溶液中的金属盐优选包括过渡金属盐;所述过渡金属盐优选包括钴离子盐或锌离子盐。在本发明中,所述有机化合物水溶液中的有机化合物优选包括2-甲基咪唑、对苯二甲酸、均苯三甲酸或1,2-二苯基-1,2-二(4-羧基苯)乙烯,进一步优选包括2-甲基咪唑。
44.在本发明中,所述金属盐水溶液的浓度优选为0.005mol/l~0.5mol/l,进一步优选为0.01~0.1mol/l,所述有机化合物水溶液的浓度优选为0.05mol/l~1.2mol/l,进一步优选为0.1~1.0mol/l。在本发明中,所述金属盐水溶液和有机化合物水溶液的体积比优选为1:(1~3),进一步优选为1:1。
45.在本发明中,所述负载的时间优选10~30min,进一步优选为15min;所述负载优选在超声的条件下进行。
46.在本发明中,所述复合反应的温度优选为室温,即既不需要额外加热也不需要额外降温。在本发明中,所述复合反应的时间优选为2~24h,进一步优选为8~16h。在本发明中,所述复合反应的方式优选为静置。
47.所述复合反应后,本发明将纤维织物取出,依次进行洗涤和干燥,得到所述金属有机骨架化合物修饰的纤维织物。在本发明中,所述洗涤的试剂优选包括水,所述水优选包括去离子水。在本发明中,所述干燥的温度优选为80℃,本发明对所述干燥的时间不做具体限定,只要干燥至恒重即可。
48.得到金属有机骨架化合物修饰的纤维织物后,本发明将所述金属有机骨架化合物修饰的纤维织物浸入刻蚀溶液中,进行刻蚀处理,得到金属氢氧化物负载的纤维织物;所述刻蚀溶液为金属盐乙醇溶液;所述金属盐乙醇溶液中的金属盐和金属有机骨架化合物前驱体溶液中的金属盐一致。
49.在本发明中,所述刻蚀溶液为金属盐乙醇溶液;所述金属盐乙醇溶液中的金属盐和金属有机骨架化合物前驱体溶液中的金属盐一致。在本发明中,所述金属盐乙醇溶液中金属盐的浓度优选为0.005mol/l~0.5mol/l。
50.在本发明中,所述刻蚀处理的温度优选为室温,即既不需要额外加热也不需要额外降温;所述刻蚀处理的时间优选为3min~2h,进一步优选为30~60min。在本发明中,所述刻蚀处理的方式优选为静置。
51.所述刻蚀处理后,本发明还包括将纤维织物取出,依次进行洗涤和干燥,得到金属氢氧化物负载的纤维织物。在本发明中,所述洗涤的试剂优选包括水,所述水优选包括去离子水。在本发明中,所述干燥的温度优选为80℃,本发明对所述干燥的时间不做具体限定,只要干燥至恒重即可。
52.在本发明中,所述刻蚀处理能够将金属有机骨架化合物进行原位刻蚀,得到强度增强组分金属氢氧化物。
53.得到金属氢氧化物负载的纤维织物后,本发明将所述金属氢氧化物负载的纤维织物浸入多巴胺-硅烷偶联剂-聚乙烯亚胺复合溶液,进行聚合交联反应,得到所述自润滑纤维织物。
54.在本发明中,所述多巴胺-硅烷偶联剂-聚乙烯亚胺复合溶液中多巴胺的浓度优选为0.1mg/ml~20mg/ml,进一步优选为1mg/ml~10mg/ml;硅烷偶联剂的浓度优选为0.1mg/ml~1g/ml,进一步优选为0.5mg/ml~100mg/ml,更优选为1mg/ml~10mg/ml聚乙烯亚胺的浓度优选为0.1mg/ml~40mg/ml,进一步优选为0.5mg/ml~30mg/ml,更优选为1mg/ml~10mg/ml。在本发明中,所述硅烷偶联剂优选包括3-氨丙基三乙氧基硅烷、1,2环氧丙基三乙氧基硅烷和3-巯基丙基三甲氧基硅烷中的一种或多种。
55.在本发明中,所述聚合交联反应的温度优选为室温,即既不需要额外加热也不需要额外降温;所述聚合交联反应的时间优选为2h~72h。在本发明中,所述聚合交联反应的方式优选为静置。
56.所述聚合交联反应后,本发明优选还包括将纤维织物取出,依次进行洗涤和干燥,得到所述自润滑纤维织物。在本发明中,所述洗涤的试剂优选包括水,所述水优选包括去离子水。在本发明中,所述干燥的温度优选为80℃,本发明对所述干燥的时间不做具体限定,只要干燥至恒重即可。
57.在本发明中,所述聚合交联反应能够在金属氢氧化物的表面形成增韧组分多巴胺-硅烷偶联剂-聚乙烯亚胺聚合物的杂化层。
58.本发明还提供了上述技术方案所述的制备方法得到的自润滑纤维织物。本发明提供的自润滑纤维织物能够在纤维-树脂界面构筑强-韧一体化的界面相,即提升界面结合强度的同时,改善界面韧性。在自润滑纤维织物受到外部和内部应力作用时,强韧界面相中得增强组分可以减少裂纹产生,而增韧组分可以抑制微裂纹的扩展,进而延长自润滑纤维织物的使用寿命。
59.本发明还提供了一种自润滑衬垫织物复合材料,包括上述技术方案所述的自润滑纤维织物和树脂;所述树脂包括酚醛树脂、聚酰亚胺树脂或环氧树脂。
60.在本发明中,所述自润滑衬垫织物复合材料中自润滑纤维织物的质量分数优选为15~35%。
61.本发明还提供了上述技术方案所述的自润滑衬垫织物复合材料的制备方法,包括以下步骤:
62.将自润滑纤维织物浸渍于树脂中,进行固化,得到所述自润滑衬垫织物复合材料。
63.本发明对所述浸渍的次数不做具体限定,只要能够使得自润滑衬垫织物复合材料中自润滑纤维织物的质量分数达到要求即可。
64.在本发明中,所述固化的温度优选为120~300℃;压力优选为0.1~1mpa;固化时间优选为30min~6h。
65.下面结合实施例对本发明提供的自润滑纤维织物及其制备方法、自润滑衬垫织物复合材料及其制备方法进行详细的说明,但是不能把它们理解为对本发明保护范围的限定。
66.实施例1
67.(1)将经过洗涤的nomex/ptfe自润滑纤维织物进行在空气气氛下进行等离子体处理,增加纤维表面活性官能团含量,其中等离子体处理功率为100w,时间为粘接面5min,润滑面5min。
68.(2)经空气等离子体活化处理的自润滑纤维织物浸入50ml六水合氯化钴溶液中(浓度为0.05mol/l),超声处理15min,随后将50ml 2-甲基咪唑溶液加入上述溶液中(浓度为0.4mol/l),静置反应8h,取出去离子水洗涤,80℃烘干,得到co-mofs负载自润滑纤维织物。反应体系所用溶剂为去离子水,浓度均为混合前的浓度。
69.(3)将co-mofs负载自润滑纤维织物浸入到6mg/ml的六水合氯化钴乙醇溶液中,刻蚀处理35min,得到金属氢氧化物负载的自润滑纤维织物;
70.(4)将金属氢氧化物负载的自润滑纤维织物浸入多巴胺-硅烷偶联剂-聚乙烯亚胺复合体系进行仿生界面相中增韧组分的制备,其中多巴胺的浓度为2mg/ml,3-氨丙基三乙氧基硅烷浓度为1mg/ml,聚乙烯亚胺浓度为1mg/ml,室温下反应24h,得到仿生界面相改性自润滑纤维织物。
71.将得到的仿生界面相改性自润滑纤维织物浸入酚醛树脂溶液中,反复浸渍,直至纤维织物的质量分数达到75
±
2%,将浸渍后的湿润的复合材料粘接于金属基材表面,在0.2mpa,184℃,固化处理140min,得到仿生界面相改性自润滑纤维织物复合材料。
72.在室温环境下,80mpa动载荷,转速280转/分钟,旋转摩擦试验2h,得到自润滑衬垫织物复合材料摩擦系数为:0.040,磨损率为:0.729
×
10-14
m3/n
·
m。
73.图1为所得仿生界面相改性自润滑纤维织物复合材料的摩擦系数随时间的变化关系图。从图1可以看出:本实施例所得仿生界面相改性自润滑纤维织物复合材料的摩擦系数虽然较小,但摩擦跑合期较长。
74.实施例2
75.(1)将经过洗涤的nomex/ptfe自润滑纤维织物进行在空气气氛下进行等离子体处理,增加纤维表面活性官能团含量,其中等离子体处理功率为100w,时间为粘接面10min,润滑面10min。
76.(2)经空气等离子体活化处理的自润滑纤维织物浸入50ml六水合氯化钴溶液中(浓度为0.05mol/l),超声处理15min,随后将50ml 2-甲基咪唑溶液加入上述溶液中(浓度为0.4mol/l),静置反应8h,取出去离子水洗涤,80℃烘干,得到co-mofs负载自润滑纤维织物。
77.(3)将co-mofs负载自润滑纤维织物浸入到6mg/ml的六水合氯化钴乙醇溶液中,刻蚀处理35min,得到金属氢氧化物负载的自润滑纤维织物。
78.(4)将金属氢氧化物负载的自润滑纤维织物浸入多巴胺-硅烷偶联剂-聚乙烯亚胺复合体系进行仿生界面相中增韧组分的制备,其中多巴胺的浓度为2mg/ml,3-氨丙基三乙氧基硅烷浓度为1mg/ml,聚乙烯亚胺浓度为1mg/ml,室温下反应24h,得到仿生界面相改性自润滑纤维织物。
79.将洗涤的nomex/ptfe自润滑纤维织物、步骤(2)得到的co-mofs负载自润滑纤维织物、步骤(3)得到的金属氢氧化物负载的自润滑纤维织物和步骤(4)得到的仿生界面相改性自润滑纤维织物分别浸入酚醛树脂溶液中,反复浸渍,直至织物质量分数达到75
±
2%,将
浸渍后的湿润的复合材料粘接于金属基材表面,在0.2mpa,184℃,固化处理140min,得到各自润滑衬垫织物复合材料。
80.在室温环境下,80mpa动载荷,转速280转/分钟,旋转摩擦试验2h,得到仿生界面相改性自润滑纤维织物复合材料的摩擦系数为:0.046,磨损率为:0.704
×
10-14
m3/n
·
m。
81.图2为各自润滑衬垫织物复合材料的摩擦系数随时间的变化关系图,其中(a)为未处理自润滑纤维织物树脂复合材料的摩擦系数随时间的变化关系图,(b)为co-mofs负载自润滑纤维织物树脂复合材料的摩擦系数随时间的变化关系图,(c)为金属氢氧化物负载的自润滑纤维织物树脂复合材料的摩擦系数随时间的变化关系图,(d)为仿生界面相改性自润滑纤维织物树脂复合材料的摩擦系数随时间的变化关系图。从图2可以看出:未处理自润滑纤维织物树脂复合材料、co-mofs负载自润滑纤维织物树脂复合材料及金属氢氧化物负载的自润滑纤维织物树脂复合材料的摩擦系数波动较大,跑合期较长。但是,对于仿生界面相改性自润滑纤维织物树脂复合材料,跑合期为25min,且稳定期摩擦系数波动非常小。
82.图3为各自润滑衬垫织物复合材料的平均摩擦系数图,图4为各自润滑衬垫织物复合材料的平均磨损率图,从图3和4可以看出:mofs负载后的co-mofs负载自润滑纤维织物树脂复合材料的摩擦系数增大,但衬垫磨损率大幅减小;对于co(oh)2改性和仿生界面相修饰的自润滑衬垫摩擦系数均减小,仿生界面相改性自润滑纤维织物树脂复合材料表现出最小的磨损率。
83.实施例3
84.(1)将经过洗涤的nomex/ptfe自润滑纤维织物进行在空气气氛下进行等离子体处理,增加纤维表面活性官能团含量,其中等离子体处理功率为100w,时间为粘接面5min,润滑面5min。
85.(2)经空气等离子体活化处理的自润滑纤维织物浸入50ml六水合氯化钴溶液中(浓度为0.05mol/l),超声处理15min,随后将50ml 2-甲基咪唑溶液加入上述溶液中(浓度为0.4mol/l),静置反应16h,取出去离子水洗涤,80℃烘干,得到co-mofs负载自润滑纤维织物。
86.(3)将co-mofs负载自润滑纤维织物浸入到6mg/ml的六水合氯化钴乙醇溶液中,刻蚀处理35min,得到金属氢氧化物负载的自润滑纤维织物;
87.(4)将金属氢氧化物负载的自润滑纤维织物浸入多巴胺-硅烷偶联剂-聚乙烯亚胺复合体系进行仿生界面相中增韧组分的制备,其中多巴胺的浓度为2mg/ml,3-氨丙基三乙氧基硅烷浓度为1mg/ml,聚乙烯亚胺浓度为1mg/ml,室温下反应24h,得到仿生界面相改性自润滑纤维织物。
88.将仿生界面相改性自润滑纤维织物浸入酚醛树脂溶液中,反复浸渍,直至织物质量分数达到75
±
2%,将浸渍后湿润的复合材料粘接于金属基材表面,在0.2mpa,184℃,固化处理140min,得到仿生界面相改性自润滑纤维织物树脂复合材料。
89.在室温环境下,80mpa动载荷,转速280转/分钟,旋转摩擦试验2h,得到仿生界面相改性自润滑纤维织物树脂复合材料的摩擦系数为:0.059,磨损率为:0.808
×
10-14
m3/n
·
m。
90.图5为所得仿生界面相改性自润滑纤维织物树脂复合材料的摩擦系数随时间的变化关系图。从图5可以看出:本实施例所得仿生界面相改性自润滑纤维织物树脂复合材料的摩擦系数波动较大,不稳定。
91.实施例4
92.(1)将经过洗涤的nomex/ptfe自润滑纤维织物进行在空气气氛下进行等离子体处理,增加纤维表面活性官能团含量,其中等离子体处理功率为100w,时间为粘接面5min,润滑面5min。
93.(2)经空气等离子体活化处理的自润滑纤维织物浸入50ml六水合氯化钴溶液中(浓度为0.05mol/l),超声处理15min,随后将50ml 2-甲基咪唑溶液加入上述溶液中(浓度为0.4mol/l),静置反应16h,取出去离子水洗涤,80℃烘干,得到co-mofs负载自润滑纤维织物。
94.(3)将co-mofs负载自润滑纤维织物浸入到6mg/ml的六水合氯化钴乙醇溶液中,刻蚀处理35min,得到金属氢氧化物负载的自润滑纤维织物。
95.(4)将金属氢氧化物负载的自润滑纤维织物浸入多巴胺-硅烷偶联剂-聚乙烯亚胺复合体系进行仿生界面相中增韧组分的制备,其中多巴胺的浓度为2mg/ml,3-氨丙基三乙氧基硅烷浓度为2mg/ml,聚乙烯亚胺浓度为1mg/ml,室温下反应24h,得到仿生界面相改性自润滑纤维织物。
96.将仿生界面相改性自润滑纤维织物浸入酚醛树脂溶液中,反复浸渍,直至织物质量分数达到75
±
2%,将浸渍后湿润的复合材料粘接于金属基材表面,在0.2mpa,184℃,固化处理140min,得到仿生界面相改性自润滑纤维织物树脂复合材料。
97.在室温环境下,80mpa动载荷,转速280转/分钟,旋转摩擦试验2h,得到仿生界面相改性自润滑纤维织物树脂复合材料的摩擦系数为:0.055,磨损率为:0.755
×
10-14
m3/n
·
m。
98.图6为所得仿生界面相改性自润滑纤维织物树脂复合材料的摩擦系数随时间的变化关系图。从图6可以看出:本实施例所得仿生界面相改性自润滑纤维织物树脂复合材料的摩擦系数波动较大,不稳定。
99.以上所述仅是本发明的优选实施方式,应当指出,对于本技术领域的普通技术人员来说,在不脱离本发明原理的前提下,还可以做出若干改进和润饰,这些改进和润饰也应视为本发明的保护范围。