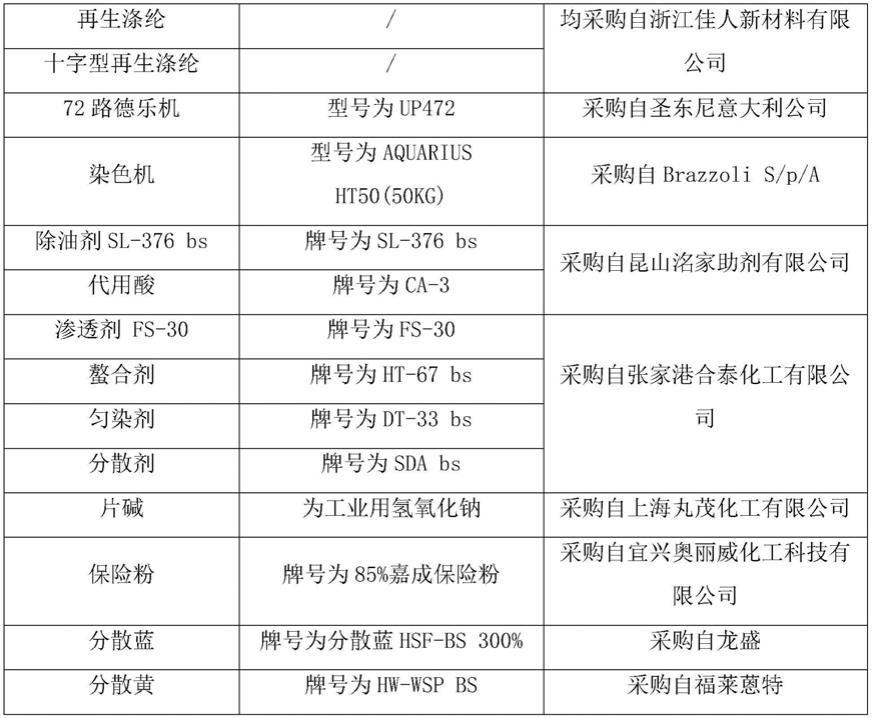
1.本技术涉及纺织技术领域,更具体地说,它涉及一种再生涤纶超亲水速干针织面料及其制备方法。
背景技术:2.针织面料是利用织针将纱线弯曲成圈并相互串套而形成的织物。针织面料广泛应用于服装、家纺等产品中,并受到广大消费者的喜爱。
3.随着人们对穿着服装舒适性的要求不断提高,人们选择贴身服装时,会比较注重服装的吸湿排汗性能。因为人体在出汗时,服装会吸附汗液,从而导致服装一定程度的变湿,而人体在潮湿环境下,舒适性会下降。
4.目前,为了提高服装的吸湿排汗性能,在针织面料在制备的过程中,会采用吸水整理剂使针织面料具有既亲水又速干的性能,从而提高所得服装的吸湿排汗性能。但是,随着服装清洗次数的增加,服装的吸湿排汗性能效果会逐渐减弱。
技术实现要素:5.为了提高针织面料亲水、速干性能的耐久性,本技术提供一种再生涤纶超亲水速干针织面料及其制备方法。
6.第一方面,本技术提供一种再生涤纶超亲水速干针织面料,采用如下的技术方案:一种再生涤纶超亲水速干针织面料,按重量百分比计算,由42-52%的再生涤纶和48-58%的十字型再生涤纶经过双面纬编后,再经过吸水整理剂浸轧而成;所述再生涤纶细度为0.3-0.6dpf;所述十字型再生涤纶细度为2.1-2.8dpf;所述dpf为每单根纤维的细度,且满足下列公式:dpf=d/f,其中d为丹尼尔,f为单纤维的根数。
7.通过采用上述技术方案,在上述配比下,由于采用单纤细度细的再生涤纶纤维和单纤细度细粗的十字型再生涤纶进行双面纬编得到的坯布,布面情况为表面细,里面粗。一方面,坯布中的纤维与纤维之间会形成良好的毛细管效应,具有增强水分传导作用的效果。另一方面,由于采用的十字型再生涤纶为异形截面涤纶纤维,其导湿性优于一般圆形截面涤纶纤维,可提高所得面料的速干性能。因此,通过本技术双面纬编得到的坯布,再通过后续的吸水整理剂浸轧后,最终所得的面料,不仅具有良好的亲水、速干性能。同时,由于采用特定涤纶所得的坯布结构特殊,还可进一步增强面料的亲水、速干性能。因此,本技术所得面料,具有提高面料亲水、速干性能耐久性的效果。
8.优选的,所述再生涤纶细度为0.5dpf,所述十字型再生涤纶细度为2.1dpf。
9.优选的,所述再生涤纶超亲水速干针织面料,所述再生涤纶为75d/144f再生涤纶,所述十字型再生涤纶为75d/36f十字型再生涤纶。
10.通过采用上述技术方案,由75d/144f再生涤纶和75d/36f十字型再生涤纶经过双
面纬编所得的坯布,其纤维与纤维之间形成的毛细管效应较强,因此,所得面料具有较好的亲水、速干性能,且亲水、速干效果持久。
11.第二方面,本技术提供一种再生涤纶超亲水速干针织面料的制备方法,采用如下的技术方案:一种再生涤纶超亲水速干针织面料的制备方法,包括以下步骤:s1织造工艺:将再生涤纶和十字型再生涤纶通过双面纬编成坯布;s2染色工艺:将s1中得到的坯布依次经过除油、染色、还原清洗后,得到染色后的坯布;s3后整工艺:将s2中得到的染色后的坯布依次经过脱水、开幅、吸水整理剂水溶液浸轧,得到带液率为60-75%的坯布后,再进行定型处理,即得到再生涤纶超亲水速干针织面料;其中,吸水整理剂水溶液中的吸水整理剂为sr-100t。
12.通过采用上述技术方案,采用再生涤纶和十字型再生涤纶纬编所得的坯布,依次经过上述的染色工艺和后整工艺后,最终所得的面料,不仅具有较好的亲水、速干性能,且亲水、速干效果持久。同时,所得面料的布面手感柔软,布面无油渍和色花等情况。
13.优选的,所述s1织造工艺中,再生涤纶线长为10-15cm/50n,十字型再生涤纶线长为7-8.5cm/50n。
14.通过采用上述技术方案,由于控制再生涤纶和十字型再生涤纶的线长在上述范围内,使得坯布中各纤维之间具有一定的松紧度,不仅促进了纤维与纤维之间的毛细管效应,增强了纤维之间水分传导的作用。同时,还提高纤维之间的导湿性。因此,所得面料具有较好的亲水、速干性能,且亲水、速干效果持久。
15.优选的,所述s1织造工艺中,针盘织针的排序为ab,针筒织针的排序为ab,采用罗纹对位,2枚织针一个循环;三角排列为六路一个循环,穿纱为:第1、4路穿入再生涤纶,作为正面纱和连接纱,针盘两道针,一针集圈、一针浮线,针筒两道针全部成圈;第2、3、5、6穿入十字型再生涤纶,作为反面纱,针盘两道针,一针成圈、一针浮线,针筒两道针全部浮线。
16.通过采用上述技术方案,由于反面纱的交织点多,贴近皮肤,有利于汗水的迅速扩散和传导,保持人体舒爽。同时,由于正面纱和连接纱形成的毛细管效应,可促使汗液迅速传到到面料外表面并蒸发,因此,所得面料具有较好的亲水、速干性能,且亲水、速干效果持久。
17.优选的,所述s1织造工艺中,再生涤纶的穿纱张力为5-6cn,十字型再生涤纶的穿纱张力为3-4cn,织机转速为18r/min。
18.通过采用上述技术方案,由于选择了比较适合的穿纱张力和转速,一方面,减少了断纱接纱的频率,而且在不影响布面品质和产能的前提下获得了品质优异的布面效果。另一方面,在一定程度上调节了纤维与纤维之间的松紧度,从而进一步提高所得的面料的亲水、速干性能,且亲水、速干效果持久。
19.优选的,所述s2染色工艺中,除油的具体步骤为:将si中的坯布在80-95℃的除油剂水溶液中浸泡处理后,即得除油后的坯布;其中,除油剂水溶液中的除油剂为除油剂sl-376bs、除油剂ht-173eco bs和乳化
精炼除油剂do-1173中的任意一种。
20.通过采用上述技术方案,由于采用上述种类的除油剂,并在80-95℃的条件下,均对坯布表面油渍和污渍的去除效果较好,因此减少了最终所得面料的布面出现色花等情况。
21.优选的,所述s2染色工艺中,所述坯布的染色过程的温度及时间控制如下:首先,以1.5℃-2.0/min的升温速率,由50℃升温至70℃,然后以1.0-1.5℃/min的升温速率,由70℃升温至130-132℃,保温30-45min;最后以2.5-3.0℃/min的降温速率从130
‑ꢀ
132℃降温至50℃。通过采用上述技术方案,由于控制坯布在染色过程中的升温速率,一方面,减少了所得坯布再染色过程中出现色花、色渍和勾丝等现象,提高所得面料的布面情况。另一方面,在上述温度梯度和升温速率条件下,还提高了所得面料的染色牢度。
22.优选的,所述s2染色工艺中,还原清洗的具体步骤为:将染色后的坯布依次在还原清洗水溶液和冰醋酸水溶液中浸泡后,即得还原清洗后的坯布;其中,所述还原清洗水溶液中的还原洗净剂为保险粉、还原洗净剂mc-08n(fa-004a)和还原洗净剂ht-rcbs中的一种或多种。
23.通过采用上述技术方案,由于使用优化后的清洗工艺,对ph控制得当,因此,使得此面料具有牢度优异的效果。
24.综上所述,本技术具有以下有益效果:1、由于本技术采用再生涤纶纤维和十字型再生涤纶进行双面纬编得到的坯布再经过吸水整理剂浸轧后,由于再生涤纶纤维的单纤细度细,十字型再生涤纶的单纤细度细粗,所得坯布表面细,里面粗,坯布中纤维与纤维之间形成毛细管作用,增强了水分的传导,同时,采用的十字型再生涤纶为导湿性优良的异形截面涤纶纤维,因此,所得面料具有较好的亲水、速干性能,且亲水、速干效果持久;2、本技术的方法,通过控制再生涤纶和十字型再生涤纶的线长,调节坯布中各纤维之间的松紧度,促进了纤维与纤维之间的毛细管效应,从而增强了纤维之间水分传导的作用,并提高纤维之间的导湿性;3、本技术的方法,通过控制再生涤纶和十字型再生涤纶的穿纱方式,使得反面纱的具有较多的交织点,促进水的扩散和传导,同时,正面纱和连接纱可形成优良的毛细管效应,促使水被传导蒸发,因此,所得面料具有较好的亲水、速干性能,且亲水、速干效果持久。
具体实施方式
25.以下结合实施例对本技术作进一步详细说明。
26.本技术实施例所采用的原料,除下列特殊说明外,其他均为市售。
27.对本技术实施例所得的再生涤纶超亲水速干针织面料和对比例所得的针织面料进行滴水扩散时间、水分残余率、蒸发速率、洗濯和摩擦检测,检测标准如下:滴水扩散时间检测:按照aatcc 79-2010。
28.水分残余率检测:按照gb/t9995-1997。
29.蒸发速率检测:按照gb/t 2165.1-2008《纺织品吸湿速干性评定第一部分:单项组合试验法》。
30.洗濯检测:按照《jis l0844:2011》中的a-2。
31.摩擦检测;按照jis l0849-2004《耐摩擦色牢度试验方法》。实施例
32.实施例1一种再生涤纶超亲水速干针织面料,由8.4kg的再生涤纶和11.6kg的十字型再生涤纶经过织造工艺织造后,再依次经过染色工艺和后整工艺处理,即得。
33.本实施例中,再生涤纶为75d/144f再生涤纶,十字型再生涤纶为75d/36f十字型再生涤纶;
75d/144f再生涤纶的进纱张力为5cn,线长为10cm/50n;75d/36f十字型再生涤纶的进纱张力为3cn,线长为7cm/50n。
34.再生涤纶超亲水速干针织面料的的制备方法如下:s1织造工艺:将再生涤纶和十字型再生涤纶,采用72路德乐机,在双面大圆机上编织交织而成坯布。
35.其中,采用的72路德乐机,机号为28g,筒径为30",转速为18r/min。
36.具体织造工艺如下:参照表1,针盘织针的排序为ab,针筒织针的排序为ab,采用罗纹对位,2枚织针一个循环。
37.编织方式为,采用六路一个循环进行编织,其中穿纱方式为,第1、4路穿入 75d/144f再生涤纶,作为正面纱和连接纱,针盘两道针,一针上集圈∪、一针浮线-,针筒两道针,全部成圈∧;第2、3、5、6穿入75d/36f十字型再生涤纶,作为反面纱,针盘两道针,一针上成圈∨、一针浮线-,针筒两道针全部浮线-。
38.表1-三角配置表表注:“∪”表示上集圈;“∨”表示上成圈;“∧”表示成圈;“-”表示浮线。
39.s2染色工艺处理:s21除油:按照坯布和除油剂水溶液的浴比为1:10,向染色机中加入水,然后向水中加入 1.5g/l的除油剂sl-376bs和1.5g/l的渗透剂fs-30,搅拌混合均匀后,得到除油剂水溶液。将s1中的坯布放入80℃的除油剂水溶液中,除油20min后,再排出除油剂水溶液,得到除油后的坯布。
40.其中,s1中的坯布在除油剂水溶液中的运行速度为30-60s/r(本实施例为30s/r),其中,s表示秒,r表示圈,s/r表示坯布在染色机的染缸中转一圈所需要的时间。
41.s22染色:按照坯布和染浴的浴比为1:10,向染色机中加入水,再将0.5g/l的环保修补剂、0.8g/l的代用酸、0.3g/l螯合剂、1g/l匀染剂和1g/l分散剂加入水中,搅拌混合后,升温至50℃,再加入0.4%分散蓝和0.06%分散黄,搅拌混合,得到染浴。
42.将s21除油后的坯布加入染浴中,调节染浴ph值为4.0-5.0后,采用一浴染色法,将坯布染色30min后,即得染色后的坯布。
43.其中,s21除油后的坯布在染浴中的运行速度为30-60s/r(本实施例为30s/r)。
44.在本技术实施例中,由于除油剂sl-376bs、除油剂ht-173eco bs和乳化精炼除油剂do-1173对面料的影响相同。所以本技术实施例中,仅以除油剂sl-376bs为例作简要说
明,但并不影响除油剂ht-173eco bs和乳化精炼除油剂do-1173在本技术中的应用。
45.s21除油后的坯布在染浴中,染浴的温度及时间控制如下:以1.5℃/min的升温速率,由50℃升温至70℃,然后以1.0℃/min的升温速率,由70℃升温至130℃,保温30min;最后以2.5-3.0℃/min的降温速率,由130℃降温至50℃,排出染液,得到染色后的坯布。
46.在本技术实施例中,由于本技术优选保护的坯布染色过程的温度及时间控制对面料的影响相同。所以本技术实施例中,染浴仅以上述温度及时间控制参数为例作简要说明,但并不影响本技术优选保护染浴的温度及时间在本技术中的应用。
47.s23还原清洗:按照坯布和还原清洗水溶液的浴比为1:10,向染色机中加入水、 2.0g/l片碱和2.0g/l保险粉,搅拌混合均匀后,得到ph为10-12的还原清洗水溶液,将还原清洗水溶液升温至80℃,使用还原清洗水溶液对s22中染色后的坯布进行清洗20min,排出还原清洗水溶液,得到碱性的还原清洗的坯布。
48.按照坯布和冰醋酸水溶液的浴比为1:10,向染色机中加入水和1.0g/l的冰醋酸调节溶液后,升温至50℃,得到ph为7的冰醋酸水溶液。将碱性的还原清洗的坯布加入50℃的冰醋酸水溶液中运行10min,其坯布的运行速度为30-60s/r(本实施例为30s/r),排出冰醋酸水溶液,得到还原清洗后的坯布。
49.在本技术实施例中,由于保险粉、还原洗净剂mc-08n(fa-004a)和还原洗净剂ht
‑ꢀ
rcbs对面料的影响相同。所以本技术实施例中,仅以还原洗净剂保险粉为例作简要说明,但并不影响还原洗净剂mc-08n(fa-004a)和还原洗净剂ht-rcbs在本技术中的应用。
50.s24脱水:将经s23中还原清洗的坯布脱水3min,得到脱水后的坯布。
51.s25开幅:将s24中脱水后的坯布传送至开幅机中进行开幅处理,其车速为30m/min, 得到开幅后的坯布,其中,坯布的门幅为150cm。
52.s3后整工艺处理:s31加助剂处理:将100l水和1kg的吸水整理剂sr-100t加入定型机的扎槽中,搅拌混合后,得到吸水整理剂水溶液。将经s25开幅后的坯布在定型机的扎槽中浸扎,得到加助剂处理后的坯布。其中,加助剂处理后的坯布的带液率为65-70%(本实施例为65%),定型机的速度为18-20m/min(本实施例为18m/min),轧辊的压力为27n。
53.s32定型:将经s31加助剂处理后的坯布传送至烘箱中,在温度为150℃、车速为 18m/min、超喂15%的条件下,进行定型处理2-3min(本实施例为3min),得到稳定的再生涤纶超亲水速干针织面料。
54.实施例2-3一种再生涤纶超亲水速干针织面料,与实施例1的不同之处在于,各原料组分及其相应的重量如下表所示。
55.对实施例1-3所得的再生涤纶超亲水速干针织面料,进行滴水扩散时间、水分残余率、蒸发速率、洗濯和摩擦检测,检测结果如下表所示。
56.从上表各项性能检测结果数据分析可知,本技术实施例1-3所得的再生涤纶超亲水速干针织面料,洗前的滴水扩散时间低至0.5-0.7s,洗5次后的滴水扩散时间低至0.5-0.6s;洗前和洗10次后的水分残余率均为0%;洗前的蒸发速率高达0.25-0.29g/h,洗5次后的蒸发速率高达0.27-0.3g/h;洗濯和摩擦级别均高达4-5级。由此表明,本技术所得的再生涤纶超亲水速干针织面料,具有较好的亲水、速干性能,优异的洗涤和摩擦牢度,且亲水、速干效果持久。
57.特别是,实施例2所得的再生涤纶超亲水速干针织面料,洗5次后的滴水扩散时间低至0.5s;洗前的蒸发速率高达0.29g/h,洗5次后的蒸发速率高达0.3g/h。由此表明,在再生涤纶超亲水速干针织面料的总原料中,再生涤纶细度为0.5dpf,具体为75d/144f再生涤纶;十字型再生涤纶细度为2.1dpf,具体为75d/36f十字形再生涤纶,不仅可提高所得面料的亲水、速干性能,还能延长面料的亲水、速干效果。
58.实施例4-11一种再生涤纶超亲水速干针织面料,与实施例2的不同之处在于,除采用的再生涤纶和十字型再生涤纶的规格和dpf不同外,其他均与实施例2相同。
59.再生涤纶和十字型再生涤纶的规格和dpf如下表所示。
60.对实施例4-11所得的再生涤纶超亲水速干针织面料,进行滴水扩散时间、水分残余率、蒸发速率、洗濯和摩擦检测,检测结果如下表所示。
61.从上表各项性能检测结果数据分析可知,本技术实施例4-11所得的再生涤纶超亲水速干针织面料,洗前的滴水扩散时间低至0.6-0.9s,洗5次后的滴水扩散时间低至0.5-1s;洗前的水分残余率低至0-1%,洗10次后的水分残余率低至0-2%;洗前的蒸发速率高达 0.24-0.29g/h,洗5次后的蒸发速率高达0.26-0.3g/h。由此表明,在再生涤纶超亲水速干针织面料的总原料中,再生涤纶细度为0.3-0.6dpf,十字型再生涤纶细度为2.1-2.8dpf时,所得的再生涤纶超亲水速干针织面料,具有较好的亲水、速干性能,且亲水、速干效果持久。
62.实施例12-14一种再生涤纶超亲水速干针织面料,与实施例2的不同之处在于,s1织造工艺中,除再生涤纶和十字型再生涤纶的进纱张力不同外,其他均与实施例2相同。
63.再生涤纶和十字型再生涤纶的进纱张力如下表所示。再生涤纶和十字型再生涤纶的进纱张力如下表所示。
64.对实施例12-14所得的再生涤纶超亲水速干针织面料,进行滴水扩散时间、水分残余率、蒸发速率、洗濯和摩擦检测,检测结果如下表所示。
65.从上表各项性能检测结果数据分析可知,本技术实施例2、12所得的再生涤纶超亲水速干针织面料,洗前的滴水扩散时间低至0.5-0.6s,洗5次后的滴水扩散时间低至0.5s;洗前和洗后的水分残余率均为0%;洗前的蒸发速率高达0.29-0.30g/h,洗5次后的蒸发速率高达0.3g/h。
66.本技术实施例13-14所得的再生涤纶超亲水速干针织面料,洗前的滴水扩散时间为 0.6-0.7s,洗5次后的滴水扩散时间为0.6-0.7s;洗前的水分残余率均为0%,洗后的水分残余率为0-1%;洗前的蒸发速率为0.24-0.25g/h,洗5次后的蒸发速率为0.25-0.26g/h。
67.依据实施例13-14所得的再生涤纶超亲水速干针织面料与实施例2所得的再生涤纶超亲水速干针织面料相比,洗前的滴水扩散时间相对提高了0-16.67%,洗5次后的滴水扩散时间相对提高了20-40%;洗前的蒸发速率为相对降低了13.79-17.24%,洗5次后的蒸发速率相对降低了13.33-16.67%。
68.由实施例2、实施例12、实施例13、实施例14并结合上表可得出,在本技术再生涤纶超亲水速干针织面料的织造工艺中,虽然再生涤纶的穿纱张力为4cn,十字型再生涤纶的穿纱张力为2cn,或再生涤纶的穿纱张力为7cn,十字型再生涤纶的穿纱张力为6cn,所得的面料的亲水、速干性能较好。但是,当控制再生涤纶的穿纱张力为5-6cn,十字型再生涤纶的穿纱张力为3-4cn,不仅可提高所得面料的亲水、速干性能,还能延长面料的亲水、速干效果。
69.实施例15-17一种再生涤纶超亲水速干针织面料,与实施例2的不同之处在于,s1织造工艺中,除再生涤纶和十字型再生涤纶的线长不同外,其他均与实施例2相同。
70.再生涤纶和十字型再生涤纶的进纱张力如下表所示。
71.对实施例15-17所得的再生涤纶超亲水速干针织面料,进行滴水扩散时间、水分残余率、蒸发速率、洗濯和摩擦检测,检测结果如下表所示。率、蒸发速率、洗濯和摩擦检测,检测结果如下表所示。
72.从上表各项性能检测结果数据分析可知,本技术实施例2和实施例15所得的再生涤纶超亲水速干针织面料,洗前的滴水扩散时间低至0.5-0.6s,洗5次后的滴水扩散时间低至0.5s;洗前和洗后的水分残余率均为0%;洗前的蒸发速率高达0.29-0.30g/h,洗5次后的蒸发速率高达0.3g/h。
73.本技术实施例16-17所得的再生涤纶超亲水速干针织面料,洗前的滴水扩散时间为 0.8-0.9s,洗5次后的滴水扩散时间为0.6-0.7s;洗前的水分残余率均为0%,洗后的水分残余率为0-1%;洗前的蒸发速率为0.24-0.25g/h,洗5次后的蒸发速率为0.25-0.26g/h。
74.依据实施例16-17所得的再生涤纶超亲水速干针织面料与实施例2所得的再生涤纶超亲水速干针织面料相比,洗前的滴水扩散时间相对提高了33.33-50%,洗5次后的滴水扩散时间相对提高了20-40%;洗前的蒸发速率为相对降低了13.79-17.24%,洗5次后的蒸发速率相对降低了13.33-16.7%。
75.由实施例2、实施例15、实施例16、实施例17并结合上表可得出,在本技术再生涤纶超亲水速干针织面料的织造工艺中,控制再生涤纶线长为10-15cm/50n,十字型再生涤纶线长为7-8.5cm/50n,可提高所得面料的亲水、速干性能,并能延长面料的亲水、速干效果。
76.对比例对比例1-4一种针织面料,与实施例2的不同之处在于,除再生涤纶和十字型再生涤纶的dpf不同外,其他均与实施例2相同。
77.再生涤纶和十字型再生涤纶的dpf和具体的规格如下表所示。再生涤纶和十字型再生涤纶的dpf和具体的规格如下表所示。
78.对对比例1-4所得的针织面料,进行滴水扩散时间、水分残余率、蒸发速率、洗濯和摩擦检测,检测结果如下表所示。
79.从上表各项性能检测结果数据分析可知,对比例1-4所得的针织面料,洗前的滴水扩散时间高达1-1.3s,洗5次后的滴水扩散时间高达1-1.2s;洗前的水分残余率为1-3%,洗
后的水分残余率为1-2%;洗前的蒸发速率低至0.17-0.21g/h,洗5次后的蒸发速率低至0.16
‑ꢀ
0.22g/h。
80.依据实施例2所得的再生涤纶超亲水速干针织面料与对比例1-4所得的针织面料相比,洗前的滴水扩散时间相对降低了40-53.85%,洗5次后的滴水扩散时间相对降低了50
‑ꢀ
58.33%;洗前和洗后的水分残余率均相对降低了100%;洗前的蒸发速率为相对提高了45
‑ꢀ
70.59%,洗5次后的蒸发速率相对降低了36.36-100%。由此表明。本技术的再生涤纶超亲水速干针织面料,按原料重量百分比计算,由42-52%的再生涤纶和48-58%的十字型再生涤纶经过双面纬编后,再经过吸水整理剂浸轧而成;其中再生涤纶细度为0.3-0.6dpf;十字型再生涤纶细度为2.1-2.8dpf,具有较好的亲水、速干性能,且亲水、速干效果持久。
81.本具体实施例仅仅是对本技术的解释,其并不是对本技术的限制,本领域技术人员在阅读完本说明书后可以根据需要对本实施例做出没有创造性贡献的修改,但只要在本技术的权利要求范围内都受到专利法的保护。