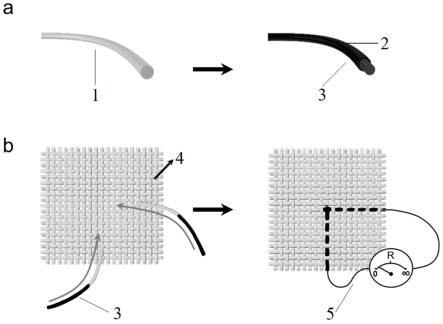
1.本发明涉及柔性电子电路与织物系统集成技术领域,尤其是涉及一种自连接织物电子电路及其制备与应用。
背景技术:2.近年来,织物电子器件的蓬勃发展,除了日渐完善单一器件的性能外,多个器件组成的系统将发挥出更加强大的功能,织物集成系统逐渐成为一种趋势。然而,器件之间的可靠连接以及整个系统良好的织物特性的保留难以通过焊接或使用导电胶实现,因为焊接所需的高温并不合适织物系统,而导电胶的粘合力不足且精度偏低。
3.因此,需要发展一种自连接织物电子电路自连接方法。
技术实现要素:4.为了解决上述问题,本发明的目的是提供一种自连接织物电子电路及其制备与应用。本发明首先将除水后的聚酯或聚醚与除水后的多羟基酸、二异氰酸酯反应,然后依次加入二硫化物、三乙胺、去离子水和乙二胺,反应后得到自连接水性聚氨酯;将自连接水性聚氨酯与导电组分混匀得到自连接电极材料;然后将自连接电极材料涂覆于纤维基底上,后处理得到自连接纤维电极;最后将自连接纤维电极编织到织物中,后处理得到自连接织物电子电路。本发明制备得到的自连接织物电子电路可以通过模块化组装以构建多层立体织物电路。经过测试,自连接后的织物电子电路在弯折与循环按压等条件下具有较好的电学与机械稳定性。
5.本发明制备步骤包括制备自连接水性聚氨酯,将其与导电组分均匀共混得到自连接电极材料;然后将自连接电极材料涂覆于纤维基底并烘干得到自连接纤维电极;最后将自连接纤维电极编织到织物中,自连接纤维电极在经纬交织点接触并完成自连接后,得到自连接织物电子电路。此外,还可将通过此方法构建的自连接织物电子电路进行模块化组装以构建多层立体织物电路。该方法可在室温条件下5秒完成,操作简便;也可在热处理条件下完成更高机械强度自连接,满足更多加工与应用需求。经过测试,自连接后的织物电子电路在弯折与循环按压等条件下具有较好的电学与机械稳定性。将自连接纤维电极编织进织物后,可通过模块化拼接与组装构建织物器件,具有可设计性。本发明所选用的自连接聚氨酯材料也可用于其它织物器件的构建,提高器件界面稳定性。因此,本发明创造性地扩充了织物电子系统集成新技术,在织物器件的构建与稳定性提升方面具有巨大的应用潜力。
6.在本发明中,通过纤维导线之间自连接很好地解决了上述问题,该方法仅需通过编织即可实现织物电子电路的连接问题,操作非常简便且连接效果稳定。此外,由于与织物集成的高度匹配,该方法还可通过设计,对织物模块进行不同方式的拼接与组装以构建不同的器件,以降低成本。不仅如此,该方法所用到的自连接组分也可用于其它织物器件的连接,从而提高其稳定性,具有普适性。
7.本发明的目的可以通过以下技术方案来实现:
8.本发明的第一个目的是提供一种自连接织物电子电路的制备方法,包括以下步骤:
9.(1)自连接水性聚氨酯的制备:将除水后的大分子多元醇与除水后的多羟基酸、二异氰酸酯反应,然后依次加入二硫化物、三乙胺和乙二胺,反应后得到自连接水性聚氨酯;
10.(2)自连接电极材料的制备:将步骤(1)制备得到的自连接水性聚氨酯与导电组分混匀得到自连接电极材料;
11.(3)自连接纤维电极的制备:将步骤(2)制备得到的自连接电极材料涂覆于纤维基底上,后处理得到自连接纤维电极;
12.(4)自连接织物电子电路的制备:将步骤(3)制备得到的自连接纤维电极编织到织物中,后处理得到自连接织物电子电路。
13.在本发明的一个实施方式中,步骤(1)中,所述大分子多元醇的数均分子量为1500-2500g/mol;
14.所述大分子多元醇包括但不限于聚醚多元醇、聚酯多元醇或聚碳酸酯多元醇;
15.所述聚酯多元醇包括但不限于聚对苯二甲酸乙二酯、聚己二酸丁二醇酯或聚对苯二甲酸二烯丙酯;
16.所述聚醚多元醇包括但不限于聚丙二醇、聚四氢呋喃二醇或四氢呋喃-氧化丙烯共聚二醇;
17.所述聚碳酸酯多元醇包括但不限于聚碳酸酯二元醇;
18.所述二异氰酸酯包括但不限于芳香族二异氰酸酯或脂肪族二异氰酸酯;
19.所述多羟基酸包括但不限于2,2-双(羟基甲基)丁酸或2,2-双(羟基甲基)丙酸;
20.所述二硫化物包括但不限于4,4'-二羟基二苯硫醚、二硫二(对氨基)苯或双(2
‑ꢀ
羟乙基)二硫化物。
21.在本发明的一个实施方式中,步骤(1)中,大分子多元醇与多羟基酸、二异氰酸酯反应时,利用月桂酸二丁基锡作为催化剂;
22.后续加入二硫化物、三乙胺和乙二胺反应时,利用去离子水作为乳化剂。
23.在本发明的一个实施方式中,大分子多元醇、多羟基酸、二异氰酸酯、月桂酸二丁基锡、二硫化物、三乙胺、去离子水和乙二胺的用量比为300份:240 份:600-950份:9-20份:150-200份:7-240份:40-100份:60-170份。
24.在本发明的一个实施方式中,步骤(1)中,具体步骤如下:
25.1)取300份大分子多元醇于三颈烧瓶中,在90-140℃的真空条件下除水3-6 h;取70-240份多羟基酸在80-130℃下除水4-6h;
26.2)三颈烧瓶中的大分子多元醇用氮气保护并冷凝回流,温度降至75-90℃后,加入步骤1)中除水后的多羟基酸、600-950份二异氰酸酯和9-20份月桂酸二丁基锡,搅拌反应6-7h;
27.3)降温至50-60℃,加入150-200份二硫化物到三颈烧瓶中,继续反应2-3h (为了保证各反应物之间的充分反应,反应过程中通过加入有机溶剂来调节反应的粘度);
28.4)降温至25-40℃,加入70-240份三乙胺,反应20-40min后,加入40-100 份去离子水和60-170份乙二胺,在1500-3000rpm的转速下继续反应20-40min,得到自连接水性聚氨酯。
29.在本发明的一个是实施方式中,步骤(2)中,所述导电组分包括但不限于碳基材料或金属粉末;
30.所述碳基材料包括但不限于石墨烯或多壁碳纳米管的水性分散液;
31.所述金属粉末包括但不限于银粉、铜粉或镍粉;
32.所述自连接电极材料中导电组分固含量为5%-60%。
33.在本发明的一个实施方式中,步骤(2)中,自连接电极材料通过增加增稠剂调节浓度,从而方便控制涂覆的厚度。
34.在本发明的一个是实施方式中,步骤(3)中,所述纤维基底选自金属纤维或高分子纤维中的一种;
35.所述金属纤维包括但不限于铁纤维、铜纤维、铝纤维、金纤维或银纤维;
36.所述高分子纤维包括但不限于尼龙纤维、涤纶纤维、腈纶纤维、芳纶纤维、丙纶纤维、棉纤维、麻纤维;
37.所述自连接电极材料的涂覆厚度为10-300μm。
38.在本发明的一个实施方式中,步骤(3)中,所述后处理为烘干处理。
39.在本发明的一个是实施方式中,步骤(4)中,所述织物选自涤纶、腈纶、芳纶、丙纶、棉或麻织物中的一种或几种。
40.在本发明的一个是实施方式中,步骤(4)中,所述后处理为自连接纤维电极在织物的经纬交织点接触并进行自连接后,完成织物电子电路连接,形成自连接织物电子电路。
41.在本发明的一个实施过程中,步骤(4)可在室温条件下5秒完成,操作简便;也可在热处理条件下完成更高机械强度自连接,满足更多加工与应用需求。
42.在本发明的一个实施方式中,所述“经纬交织点”指的是织物纬纱和经纱的交叉点。
43.本发明的第二个目的是提供一种通过上述方法制备得到的自连接织物电子电路。
44.在本发明的一个实施方式中,所述自连接织物电子电路允许模块化组装和拼接,进而构建多层立体织物电路;
45.也即:当多个织物电路模块拼接时,相邻织物模块中的自连接纤维电极接触并再一次进行自连接,完成模块化电路连接。
46.本发明的第三个目的是提供一种上述自连接织物电子电路在构建织物器件及制备可穿戴设备中的应用。
47.本发明制备得到的自连接织物电子电路在0-180
°
弯折过程中,电阻变化在 4%以内;在1000次的弯曲与按压过程中,电路电阻仍然保持平稳;
48.将所述自连接纤维电极编织于织物中的指定位置,把单个织物或整个织物的某个部分作为一个模块,利用纤维电极的自连接功能,对多个模块进行不同方式的组装与拼接,实现用相同的织物模块构建不同功能的织物器件。
49.对于需要依靠功能纤维在交织点的稳定搭接来工作的器件,允许将所述自连接聚氨酯涂覆于功能纤维表面,通过功能纤维之间的接触与自连接实现器件的可靠搭接与稳定工作。
50.本发明制备的自连接纤维电极,可用于织物器件的设计与构建。在自连接织物电子电路模块化组装的基础上并通过设计,将所述自连接纤维电极编织于织物中的指定位
置,把单个织物或整个织物的某个部分作为一个模块进行拼接,实现用相同的织物模块以不同的拼接方式构建不同结构的织物器件。
51.本发明所述的自连接水性聚氨酯,可用于相关可穿戴设备的制备,对于需要依靠功能纤维在交织点的稳定搭接以稳定工作的器件,可将所述自连接聚氨酯涂覆于功能纤维表面,通过功能纤维之间的接触与自连接实现器件的可靠搭接与稳定工作。
52.与现有技术相比,本发明具有以下有益效果:
53.(1)本发明的一种自连接织物电子电路的制备方法可在室温条件下5秒完成,操作简便;也可在热处理条件下完成更高机械强度自连接,满足更多加工与应用需求。
54.(2)本发明制备得到的一种自连接织物电子电路经过测试,自连接织物电子电路在弯折、循环弯曲与按压1000次等条件下,电路电阻变化小于6.7%。
55.(3)本发明将自连接纤维电极编织进织物后,可通过模块化拼接与组装构建织物器件,具有可设计性。
56.(4)本发明的思路可用于织物电子电路中电路元件的构建,如构建发光器件与发光织物,提高织物器件界面稳定性。
57.综上所述,本发明创造性地扩充了织物电子系统集成新技术,在织物器件的构建与稳定性提升方面具有巨大的应用潜力。
附图说明
58.图1为自连接纤维电极与自连接织物电子电路制备流程示意图。
59.图2为包含单个自连接点的织物电子电路沿水平、垂直与两个对角线弯折过程中的电阻变化。
60.图3a为包含单个自连接点的织物电子电路(圆点)和由不具备自连接功能的纤维电极构建的织物电子电路(三角形)在1000次弯曲过程中的电阻变化,图 3b为单个自连接点的织物电子电路在1000次按压过程中的电阻变化。
61.图4为包含多个自连接点的织物电路沿水平、垂直与两个对角线弯折过程中的电阻变化。
62.图5a为自连接织物电子电路制备方法构建织物线圈的示意图,图5b为织物线圈作为接收线圈的接收信号与铜线圈作为发射线圈的发射信号。
63.图6为基于同一自连接织物电子电路模块,按从左往右和从右往左方式分别构建左手螺旋结构和右手螺旋结构的织物线圈流程示意图。
64.图7为复合自连接聚氨酯的发光器件结构。
65.图中标号:1、尼龙纤维;2、自连接电极材料;3、自连接纤维电极;4、棉布;5、室温自连接织物电子电路;6、织物线圈;7、透明导电纤维;8、发光纤维;9、自连接功能层。
具体实施方式
66.本发明提供一种自连接织物电子电路的制备方法,包括以下步骤:
67.(1)自连接水性聚氨酯的制备:将除水后的大分子多元醇与除水后的多羟基酸、二异氰酸酯反应,然后依次加入二硫化物、三乙胺和乙二胺,反应后得到自连接水性聚氨酯;
68.(2)自连接电极材料的制备:将步骤(1)制备得到的自连接水性聚氨酯与导电组分
混匀得到自连接电极材料;
69.(3)自连接纤维电极的制备:将步骤(2)制备得到的自连接电极材料涂覆于纤维基底上,后处理得到自连接纤维电极;
70.(4)自连接织物电子电路的制备:将步骤(3)制备得到的自连接纤维电极编织到织物中,后处理得到自连接织物电子电路。
71.在本发明的一个实施方式中,步骤(1)中,所述大分子多元醇的数均分子量为1500-2500g/mol;
72.所述大分子多元醇包括但不限于聚醚多元醇、聚酯多元醇或聚碳酸酯多元醇;
73.所述聚酯多元醇包括但不限于聚对苯二甲酸乙二酯、聚己二酸丁二醇酯或聚对苯二甲酸二烯丙酯;
74.所述聚醚多元醇包括但不限于聚丙二醇、聚四氢呋喃二醇或四氢呋喃-氧化丙烯共聚二醇;
75.所述聚碳酸酯多元醇包括但不限于聚碳酸酯二元醇;
76.所述二异氰酸酯包括但不限于芳香族二异氰酸酯或脂肪族二异氰酸酯;
77.所述多羟基酸包括但不限于2,2-双(羟基甲基)丁酸或2,2-双(羟基甲基)丙酸;
78.所述二硫化物包括但不限于4,4'-二羟基二苯硫醚、二硫二(对氨基)苯或双(2
‑ꢀ
羟乙基)二硫化物。
79.在本发明的一个实施方式中,步骤(1)中,大分子多元醇与多羟基酸、二异氰酸酯反应时,利用月桂酸二丁基锡作为催化剂;
80.后续加入二硫化物、三乙胺和乙二胺反应时,利用去离子水作为乳化剂。
81.在本发明的一个实施方式中,大分子多元醇、多羟基酸、二异氰酸酯、月桂酸二丁基锡、二硫化物、三乙胺、去离子水和乙二胺的用量比为300份:240 份:600-950份:9-20份:150-200份:7-240份:40-100份:60-170份。
82.在本发明的一个实施方式中,步骤(1)中,具体步骤如下:
83.1)取300份大分子多元醇于三颈烧瓶中,在90-140℃的真空条件下除水3-6 h;取70-240份多羟基酸在80-130℃下除水4-6h;
84.2)三颈烧瓶中的大分子多元醇用氮气保护并冷凝回流,温度降至75-90℃后,加入步骤1)中除水后的多羟基酸、600-950份二异氰酸酯和9-20份月桂酸二丁基锡,搅拌反应6-7h;
85.3)降温至50-60℃,加入150-200份二硫化物到三颈烧瓶中,继续反应2-3h (为了保证各反应物之间的充分反应,反应过程中通过加入有机溶剂来调节反应的粘度);
86.4)降温至25-40℃,加入70-240份三乙胺,反应20-40min后,加入40-100 份去离子水和60-170份乙二胺,在1500-3000rpm的转速下继续反应20-40min,得到自连接水性聚氨酯。
87.在本发明的一个是实施方式中,步骤(2)中,所述导电组分包括但不限于碳基材料或金属粉末;
88.所述碳基材料包括但不限于石墨烯或多壁碳纳米管的水性分散液;
89.所述金属粉末包括但不限于银粉、铜粉或镍粉;
90.所述自连接电极材料中导电组分固含量为5%-60%。
91.在本发明的一个实施方式中,步骤(2)中,自连接电极材料通过增加增稠剂调节浓度,从而方便控制涂覆的厚度。
92.在本发明的一个是实施方式中,步骤(3)中,所述纤维基底选自金属纤维或高分子纤维中的一种;
93.所述金属纤维包括但不限于铁纤维、铜纤维、铝纤维、金纤维或银纤维;
94.所述高分子纤维包括但不限于尼龙纤维、涤纶纤维、腈纶纤维、芳纶纤维、丙纶纤维、棉纤维、麻纤维;
95.所述自连接电极材料的涂覆厚度为10-300μm。
96.在本发明的一个实施方式中,步骤(3)中,所述后处理为烘干处理。
97.在本发明的一个是实施方式中,步骤(4)中,所述织物选自涤纶、腈纶、芳纶、丙纶、棉或麻织物中的一种或几种。
98.在本发明的一个是实施方式中,步骤(4)中,所述后处理为自连接纤维电极在织物的经纬交织点接触并进行自连接后,完成织物电子电路连接,形成自连接织物电子电路。
99.在本发明的一个实施过程中,步骤(4)可在室温条件下5秒完成,操作简便;也可在热处理条件下完成更高机械强度自连接,满足更多加工与应用需求。
100.在本发明的一个实施方式中,所述“经纬交织点”指的是织物纬纱和经纱的交叉点。
101.本发明提供一种通过上述方法制备得到的自连接织物电子电路。
102.在本发明的一个实施方式中,所述自连接织物电子电路允许模块化组装和拼接,进而构建多层立体织物电路;
103.也即:当多个织物电路模块拼接时,相邻织物模块中的自连接纤维电极接触并再一次进行自连接,完成模块化电路连接。
104.本发明提供一种上述自连接织物电子电路在构建织物器件及制备可穿戴设备中的应用。
105.本发明制备得到的自连接织物电子电路在0-180
°
弯折过程中,电阻变化在 4%以内;在1000次的弯曲与按压过程中,电路电阻仍然保持平稳;
106.将所述自连接纤维电极编织于织物中的指定位置,把单个织物或整个织物的某个部分作为一个模块,利用纤维电极的自连接功能,对多个模块进行不同方式的组装与拼接,实现用相同的织物模块构建不同功能的织物器件。
107.对于需要依靠功能纤维在交织点的稳定搭接来工作的器件,允许将所述自连接聚氨酯涂覆于功能纤维表面,通过功能纤维之间的接触与自连接实现器件的可靠搭接与稳定工作。
108.本发明制备的自连接纤维电极,可用于织物器件的设计与构建。在自连接织物电子电路模块化组装的基础上并通过设计,将所述自连接纤维电极编织于织物中的指定位置,把单个织物或整个织物的某个部分作为一个模块进行拼接,实现用相同的织物模块以不同的拼接方式构建不同结构的织物器件。
109.本发明所述的自连接水性聚氨酯,可用于相关可穿戴设备的制备,对于需要依靠功能纤维在交织点的稳定搭接以稳定工作的器件,可将所述自连接聚氨酯涂覆于功能纤维表面,通过功能纤维之间的接触与自连接实现器件的可靠搭接与稳定工作。
110.下面结合附图和具体实施例对本发明进行详细说明。
111.下述实施例中,若无特殊说明,所有试剂均为市售试剂(各种溶剂均购自国药化学试剂有限公司),各种设备均购自商用设备,所有检测手段均为本领域常规检测手段。
112.实施例1
113.本实施例提供一种室温自连接织物电子电路及其制备方法。
114.(1)自连接水性聚氨酯的制备:取300份聚丙二醇于三颈烧瓶中,在110℃的真空条件下除水5h;取84份2,2-双(羟基甲基)丙酸在110℃下除水5h。三颈烧瓶中用氮气保护并冷凝回流,温度降至85℃后,加入除水后的2,2-双(羟基甲基)丙酸、610份异佛尔酮二异氰酸酯和17份月桂酸二丁基锡,搅拌反应6h。降温至55℃,加入160份二硫二(对氨基)苯,继续反应2.5h,过程中通过加入丙酮来调节反应的粘度。降温至30℃,加入84份三乙胺,反应20min后,加入44份去离子水和62份乙二胺,在1600rpm的转速下继续反应30min,得到自连接水性聚氨酯。
115.(2)自连接电极材料的制备:将多壁碳纳米管固含量为13.8%的水性分散液与步骤(1)中制备的自连接水性聚氨酯以固含量25%搅拌混合,加入增稠剂调节粘度,得到自连接电极材料2;
116.(3)自连接纤维电极的制备:将步骤(2)中制备的自连接电极材料2涂覆于尼龙纤维1上,70℃烘箱烘干后得到自连接纤维电极3(图1a)。
117.(4)室温自连接织物电子电路方法:将步骤(3)中制备的自连接纤维电极 3编织到棉布4中,自连接纤维电极3于25℃下在经纬交织点接触,5秒即可完成自连接,形成包含一个自连接点的室温自连接织物电子电路5(图1b)。室温自连接织物电子电路5在沿水平中线、竖直中线及两条对角线从0-180
°
的弯折过程中,电路电阻变化始终在4%以内(图2)。在1000次的弯曲过程,相比于由不具备自连接功能的纤维电极构建的织物电路,电阻保持在一个平衡状态(图3a);在1000次的按压过程中,电路电阻变化小于5.7%(图3b)。
118.实施例2
119.本实施例提供一种高强度自连接织物电子电路及其制备方法。
120.(1)高强度自连接水性聚氨酯的制备:取300份聚己二酸乙二醇酯于三颈烧瓶中,在110℃的真空条件下除水6h;取224份2,2-双(羟基甲基)丁酸在110℃下除水6h。三颈烧瓶中用氮气保护并冷凝回流,温度降至85℃后,加入除水后的 2,2-双(羟基甲基)丁酸、910份异佛尔酮二异氰酸酯和15份月桂酸二丁基锡,搅拌反应6h。降温至60℃,加入200份双(2-羟乙基)二硫化物到三颈烧瓶中,继续反应3h。过程中通过加入丙酮来调节反应的粘度。降温至30℃,加入224份三乙胺,反应20min后,加入90份去离子水和166份乙二胺,在1300rpm的转速下继续反应30min,得到高强度自连接水性聚氨酯。
121.(2)高强度自连接电极材料的制备:将镍粉(纯度大于99.999%)与步骤 (1)中制备的自连接水性聚氨酯以镍粉固含量为60%的比例搅拌混合,加入增稠剂调节粘度,制备得到高强度自连接电极材料。
122.(3)高强度自连接纤维电极的制备:将步骤(2)中制备的高强度自连接电极材料涂覆于尼龙纤维上,70℃烘箱烘干后得到高强度自连接纤维电极。
123.(4)高强度自连接织物电子电路方法:将步骤(3)中制备的高强度自连接纤维电极编织到棉布中,高强度自连接纤维电极在经纬交织点接触并在70℃条件下处理2小时完成
自连接后,形成包含三个自连接点的高强度自连接织物电子电路。此织物电路在沿水平中线和两条对角线从0-180
°
的弯折过程中,电路电阻变化始终在4%以内(图4)。
124.实施例3
125.本实施例提供一种具有信号接收功能的自连接织物电子电路——织物线圈及其制备方法。
126.(1)室温自连接水性聚氨酯的制备:取300份聚丙二醇于三颈烧瓶中,在 90℃的真空条件下除水3h;取70份2,2-双(羟基甲基)丙酸在80℃下除水4h。三颈烧瓶中用氮气保护并冷凝回流,温度降至75℃后,加入除水后的2,2-双(羟基甲基)丙酸、600份异佛尔酮二异氰酸酯和9份月桂酸二丁基锡,搅拌反应6h。降温至50℃,加入150份二硫二(对氨基)苯,继续反应2h。过程中通过加入丙酮来调节反应的粘度。降温至25℃,加入70份三乙胺,反应20min后,加入40份去离子水和60份乙二胺,在1500rpm的转速下继续反应20min,得到室温自连接水性聚氨酯。
127.(2)室温自连接电极材料的制备:将多壁碳纳米管固含量为13.8%的水性分散液与步骤(1)中制备的水性聚氨酯以碳纳米管固含量为5%的比例搅拌混合,加入增稠剂调节粘度,制备得到室温自连接电极材料;
128.(3)室温自连接纤维电极的制备:将步骤(2)中制备的室温自连接电极材料涂覆于尼龙纤维上,70℃烘箱烘干后得到室温自连接纤维电极。
129.(4)织物线圈的制备:将步骤(3)中制备的室温自连接纤维电极编织到麻布中的指定位置,构成具有设计图案的织物电子电路;再按照图5a所示方式,将织物电子电路等分的四个部分对齐并以“z”字形折叠;四根编织的自连接纤维电极在折叠后的四层麻布里头尾相连并在室温下5秒完成自连接,从而构成一个立体螺旋结构的织物线圈6。
130.(5)织物线圈6的模块化组装设计:将步骤(3)中制备的室温自连接纤维电极编织到麻布中的指定位置,构成具有设计图案的织物电子电路;再按照图6 所示方式,将织物电子电路等分的四个部分按照从左往右和从右往左两种方式进行依次折叠组装;四根编织的自连接纤维电极在折叠后的四层麻布里头尾相连并在室温下5秒完成自连接,可分别得到左手螺旋结构和右手螺旋结构的织物线圈 6。
131.(6)织物线圈6的表征:将步骤(4)中制备的织物线圈6作为接收线圈,利用电磁感应原理,接收由铜制线圈发射的正弦信号(图5b)。此外,在相同的制备方法下,由不具备自连接功能的普通聚氨酯制备电极材料,进而制备不具有自连接功能的纤维电极,将其编织到织物中并进行相同方式的折叠,由于纤维电极无法进行自连接,所构建的织物电路也无法形成一个线圈结构,其所接收信号的信号强度远小于通过自连接构建的织物线圈的接收信号(图5b)。
132.实施例4
133.本实施例提供一种在可穿戴电子器件中的应用——发光织物及其制备方法。
134.(1)高强度自连接水性聚氨酯的制备:取300份聚己二酸乙二醇酯于三颈烧瓶中,在140℃的真空条件下除水6h;取240份2,2-双(羟基甲基)丁酸在130℃下除水6h。三颈烧瓶中用氮气保护并冷凝回流,温度降至90℃后,加入除水后的 2,2-双(羟基甲基)丁酸、950份异佛尔酮二异氰酸酯和20份月桂酸二丁基锡,搅拌反应7h。降温至60℃,加入200份双(2-羟乙基)二硫化物到三颈烧瓶中,继续反应3h。过程中通过加入丙酮来调节反应的粘度。降温
至40℃,加入240份三乙胺,反应40min后,加入100份去离子水和170份乙二胺,在3000rpm的转速下继续反应40min,得到高强度自连接水性聚氨酯。
135.(2)发光织物的制备:以离子凝胶作为透明导电纤维7,在镀银尼龙复丝上负载一层含有zns颗粒的电致发光活性层制备发光纤维8,发光织物由透明导电纤维7与发光纤维8编织得到(复旦大学,一种具有显示功能的电子织物及其制备方法:cn202110071716.0[p],2021-05-18)。两种功能纤维交织界面处的发光颗粒受交流电场激发而发光,因此,一个交织点构成一个发光单元,交织点的界面接触稳定性直接决定了发光单元的性能。在透明导电纤维与发光纤维上各涂覆一层步骤(1)制备得到的自连接水性聚氨酯作为自连接功能层9,两种功能纤维在交织点进行自连接从而形成牢固搭接的稳定发光单元界面(图7)。将两种功能纤维编织到棉布中,构建包含64个发光单元(8
×
8阵列)、密度为2ppi疏松编织结构的发光织物,在拉伸、弯曲等条件下所有发光单元均保持稳定工作。而基于不具备自连接功能的普通聚氨酯利用相同方法制备的发光织物,由于疏松的编织密度,在各种形变条件下,其中的发光单元界面接触不稳定,导致大量发光单元失效。
[0136]
上述的对实施例的描述是为便于该技术领域的普通技术人员能理解和使用发明。熟悉本领域技术的人员显然可以容易地对这些实施例做出各种修改,并把在此说明的一般原理应用到其他实施例中而不必经过创造性的劳动。因此,本发明不限于上述实施例,本领域技术人员根据本发明的揭示,不脱离本发明范畴所做出的改进和修改都应该在本发明的保护范围之内。