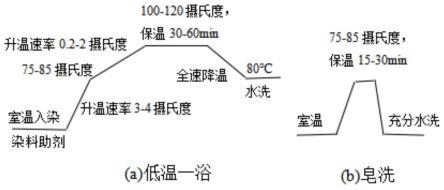
1.本发明涉及一种涤纶织物的碱减量低温染色一浴工艺,属于染整工艺技术领域。
背景技术:2.传统的分散染料结构中含有酯基、酰胺基、氰基等基团,在高温碱性染浴中易发生水解,导致上染率降低和染色涤纶织物色光不正的问题,因此涤纶织物染色通常在弱酸性条件下进行。涤纶织物在酸性条件染色时,涤纶低聚物融出,在织物表面形成焦油斑,产生染色疵病;涤纶低聚物聚落在设备内壁,难以清洗。
3.为改善织物手感涤纶织物需要碱减量处理。碱减量在高温强碱性进行,处理后需要对涤纶织物进行酸洗中和及多次水洗,以去除布面上残留的碱剂,防止织物带碱损伤及后续酸性染色过程对溶液酸性影响导致的染色疵病,工艺流程长,水耗和能耗较高。耐碱分散染料在高温强碱条件下具有优异的稳定性,使涤纶碱减量和染色可以一浴进行。
4.涤纶大分子排列紧密,玻璃化温度较高。在温度较低时,涤纶大分子链段运动相对较弱,分散染料难以上染。高温下(130℃)纤维分子链段运动加剧,单个无定形区尺寸增大,有利于染料上染,所以涤纶染色需在高温高压下进行。一些结构简单的芳香族有机化合物(载体)对涤纶分子具有增塑膨化作用,可有效降低涤纶的玻璃化温度,进而降低染色温度。
技术实现要素:5.针对上述问题,本发明提供了一种涤纶织物的碱减量低温染色一浴工艺。本发明通过在染浴中同时加入高耐碱分散染料、染色载体、碱剂、匀染剂、织物的方法,以低于常规涤纶染整加工步骤、染色温度的基础上获得具有仿丝绸效果的涤纶染色织物。本发明所述的一种涤纶织物的碱减量低温染色一浴工艺,主要包括如下步骤:
6.(1)在染浴中同时加入高耐碱分散染料、染色载体、碱剂、匀染剂。
7.(2)将待染色的织物投放到染浴中;由室温升温至70-90℃后,再升温至100-120℃,达到染色温度后保温30-60min,然后全速降温至80℃以下,排液。
8.(3)对所述涤纶染色织物进行皂洗、水洗,烘干以获得涤纶染色织物。
9.在本发明的一种实施方式中,所述高耐碱分散染料为分散红ha-r、分散黄ha-g、分散蓝ha-2r中的任一种或两种或三种的组合。
10.在本发明的一种实施方式中,所述高耐碱分散染料用量为0.5~4%o.m.f(对织物重)。
11.在本发明的一种实施方式中,所述染色载体为苯甲醇,用量为0.5~60ml/l。
12.在本发明的一种实施方式中,所述碱剂为氢氧化钠,用量为0.5~10g/l。
13.在本发明的一种实施方式中,所述匀染剂为耐碱型匀染剂7000z,用量为0.5~3g/l。
14.在本发明的一种实施方式中,染色浴比为1:10~30(织物重:溶液重)。
15.在本发明的一种实施方式中,染色过程为:以升温3-4℃/min进行升温,至75-85℃
后以0.5-2℃/min的升温速率升温至100-120℃保温30-60min,然后全速降温至80℃以下,排液;
16.在本发明的一种实施方式中,所述的皂洗具体为:按浴比1:10~30(织物重:溶液重)皂片1-2g/l,升温至75-85℃,保温15-30min,之后排液,水洗。
17.本发明的有益效果:
18.1,本发明采用的耐碱分散染料可进行涤纶织物碱减量和低温染色一浴处理,氢氧化钠和载体(苯甲醇)不会对染料造成破坏。
19.2,本发明的碱减量低温染色一浴工艺中,适度增大载体用量有利于提高织物k/s值及减量率;100~110℃碱减量低温染色一浴工艺中可达到先碱减量再130℃染色的常规工艺染色织物的k/s值,更加节能;根据减量率和碱用量的线性关系,调整一浴工艺碱用量,相同染料用量下,一浴工艺可达到常规工艺一样的织物k/s值和减量率。
20.3,本发明的碱减量低温染色一浴工艺染色织物色牢度与常规工艺相同,说明本发明的方法不会影响织物的各项牢度。
21.4,本发明的碱减量低温染色一浴工艺无需还原清洗步骤,且相较于先碱减量再染色的常规工艺染色温度更低,废水产生率下降,步骤更少,工艺流程大大缩短,属于节能环保工艺。
附图说明
22.图1:涤纶织物的碱减量低温染色一浴工艺的流程图。
具体实施方式
23.测试方法:
24.(1)白度、lab值、k/s值、色差
25.采用电脑测配色仪datacolor 500测试,织物折叠4层,测4个点,取平均值。
26.(2)摩擦牢度测试
27.按照gb/t 3920-2008《纺织品色牢度试验耐摩擦色牢度》测定,采用gb251-1995《评定沾色用灰色样卡》进行评级。
28.(3)耐水洗色牢度
29.按照gb/t 3921.1-2008《纺织品耐洗色牢度试验方法》进行测定,采用gb251-1995《评定沾色用灰色样卡》进行评级。
30.实施例1
31.按以下步骤对涤纶织物进行染色、皂洗,获取涤纶染色织物:
32.(1)在染浴中同时加入高耐碱分散染料(分散红ha-r、0.5%o.m.f)、染色载体(苯甲醇、30ml/l)、碱性溶液(氢氧化钠、10g/l)、匀染剂(7000z、1g/l),浴比为1:20。
33.(2)将待染色的织物投放到染浴中,以升温3.5℃/min进行升温,至80℃后以升温速率1.5℃/min升温至110℃保温60min,全速降温至80℃以下,排液。
34.(3)对所述涤纶染色织物进行皂洗,具体为:浴比1:20,皂片2g/l,升温至85℃,保温15min,之后排液,水洗,烘干以获得涤纶染色织物。
35.染色织物颜色特征值及减量率见表1,织物色牢度见表2。
36.对照列1
37.按实施例1对涤纶织物进行染色。
38.还原清洗:浴比1:20,保险粉2.5g/l,naoh 2g/l,温度80℃,保温20min后排水、水洗,烘干,得到涤纶染色织物。
39.染色织物颜色特征值及减量率见表1,织物色牢度见表2。
40.对照例2(传统先碱减量再染色工艺)
41.按照以下传统工艺对涤纶织物进行染色,获取涤纶染色织物:
42.(1)在染浴中添加碱性溶液(氢氧化钠、10g/l),浴比为1:20,投入待染织物,以升温3.5℃/min进行升温,至80℃后以升温速率1.5℃/min升温至110℃保温60min,然后全速降温速率降温至80℃以下,排液,获取碱减量后涤纶织物。
43.在染浴中同时加入高耐碱分散染料(分散红ha-r、0.5%o.m.f)、匀染剂(7000z、1g/l),浴比为1:20,投入上述碱减量后涤纶织物,以升温3.5℃/min进行升温,至80℃后以升温速率1.5℃/min升温至130℃保温60min,全速降温至80℃以下,排液,获得涤纶染色织物。
44.(3)对所述涤纶染色织物进行还原清洗,具体为:浴比1:20,保险粉2.5g/l,naoh 2g/l,温度80℃,保温20min后排水、水洗,烘干,得到涤纶染色织物。
45.染色织物颜色特征值及减量率见表1,织物色牢度见表2。
46.实施例2
47.按以下步骤对涤纶织物进行染色,获取涤纶染色织物:
48.(1)在染浴中同时加入高耐碱分散染料(分散红ha-r)0.5%o.m.f、染色载体(苯甲醇)0.5ml/l、氢氧化钠0.5g/l、匀染剂7000z 0.5g/l,浴比为1:10。
49.(2)将待染色的织物投放到染浴中,以升温3℃/min进行升温,至75℃后以升温速率0.5℃/min升温至100℃保温60min,然后全速降温至80℃以下,排液。
50.(3)对所述涤纶染色织物进行皂洗,具体为:浴比1:10,皂片2g/l,升温至75℃,保温30min,之后排液,水洗,烘干以获得涤纶染色织物。
51.染色织物颜色特征值及减量率见表1,织物色牢度见表2。
52.实施例3
53.按以下步骤对涤纶织物进行染色,获取涤纶染色织物:
54.(1)在染浴中同时加入高耐碱分散染料(分散黄ha-g)4%o.m.f、染色载体(苯甲醇)60ml/l、氢氧化钠10g/l、匀染剂7000z 3g/l,浴比为1:30。
55.(2)将待染色的织物投放到染浴中,以升温4℃/min进行升温,至85℃后以升温速率2℃/min升温至120℃保温30min,然后全速降温至80℃以下,排液。
56.(3)对所述涤纶染色织物进行皂洗,具体为:浴比1:30在染浴中加入相应的水,皂片1g/l,升温至85℃,保温15min,之后排液,水洗,烘干以获得涤纶染色织物。
57.染色织物颜色特征值及减量率见表1,织物色牢度见表2。
58.对照列3
59.按实施例3对涤纶织物进行染色。
60.还原清洗:浴比1:20,保险粉2.5g/l,naoh 2g/l,温度80℃,保温20min后排水、水洗,烘干,得到涤纶染色织物。
61.染色织物颜色特征值及减量率见表1,织物色牢度见表2。
62.实施例4
63.按以下步骤对涤纶织物进行染色,获取涤纶染色织物:
64.(1)在染浴中同时加入高耐碱分散染料(分散蓝ha-2r)2%o.m.f、染色载体(苯甲醇)30ml/l、氢氧化钠5g/l、匀染剂7000z 1.5g/l,浴比为1:20。
65.(2)将待染色的织物投放到染浴中,以升温4℃/min进行升温,至85℃后以升温速率2℃/min升温至110℃保温45min,然后全速降温至80℃以下,排液。
66.(3)对所述涤纶染色织物进行皂洗,具体为:浴比1:20在染浴中加入相应的水,皂片2g/l,升温至80℃,保温20min,之后排液,水洗,烘干以获得涤纶染色织物。
67.染色织物颜色特征值及减量率见表1,织物色牢度见表2。
68.对照列4
69.按实施例4对涤纶织物进行染色。
70.还原清洗:浴比1:20,保险粉2.5g/l,naoh 2g/l,温度80℃,保温20min后排水、水洗,烘干,得到涤纶染色织物。
71.染色织物颜色特征值及减量率见表1,织物色牢度见表2。
72.实施例5
73.按以下步骤对涤纶织物进行染色,获取涤纶染色织物:
74.(1)在染浴中同时加入高耐碱分散染料((分散红ha-r%0.5o.m.f、分散黄ha-g 1%o.m.f、分散蓝ha-2r 0.5%o.m.f)、染色载体(苯甲醇)30ml/l、氢氧化钠10g/l、匀染剂7000z 2g/l,浴比为1:20。
75.(2)将待染色的织物投放到染浴中,以升温4℃/min进行升温,至85℃后以升温速率1℃/min升温至110℃保温45min,然后全速降温至80℃以下,排液。
76.(3)对所述涤纶染色织物进行皂洗,具体为:浴比1:20在染浴中加入相应的水,皂片2g/l,升温至80℃,保温20min,之后排液,水洗,烘干以获得涤纶染色织物。
77.染色织物颜色特征值及减量率见表1,织物色牢度见表2。
78.对照列5
79.按实施例5对涤纶织物进行染色。
80.还原清洗:浴比1:20,保险粉2.5g/l,naoh 2g/l,温度80℃,保温20min后排水、水洗,烘干,得到涤纶染色织物。
81.染色织物颜色特征值及减量率见表1,织物色牢度见表2。
82.表1涤纶染色织物特征值及减量率
[0083][0084][0085]
表1列出了涤纶染色织物织物的颜色特征值及减量率。对比表1中实施例1和对照例1,实施例3和对照例3,实施例4和对照例4,实施例5和对照例5的数据可知,涤纶碱减量低温一浴工艺所得织物颜色特征值及减量率与其还原清洗后织物的颜色特征值及减量率基本一致,说明还原清洗与否对本发明题出的涤纶碱减量低温一浴工艺的染色效果无影响,即本发明提出的涤纶碱减量低温一浴工艺无需涤纶传统染色工艺的还原清洗步骤。对比表1中实施例1、实施例2及实施例4可知,涤纶碱减量低温一浴工艺的织物减量率可以通过控制染浴中碱用量调整。对比表1中实施例1和对照例2可知,涤纶碱减量低温一浴工艺所得织物颜色特征值及减量率与传统染整工艺(先碱减量再染色及还原清洗)所得织物颜色特征值及减量率基本一致,说明碱减量低温染色一浴工艺处理的织物可达到常规工艺的效果,而相较于涤纶织物的传统染整工艺,本发明提出的碱减量低温一浴工艺流程更短,染色温度更低,产生的废水更少,耗能明显减少。
[0086]
表2涤纶染色织物色牢度
[0087][0088]
表2列出了涤纶染色织物的耐水洗色牢度和耐摩擦色牢度。对比表1中实施例1和
对照例1,实施例3和对照例3,实施例4和对照例4,实施例5和对照例5的数据可知,涤纶碱减量低温一浴工艺与传统染色工艺所得织物都具有较高的耐水洗色牢度(染色织物不易发生水洗褪色且水洗过程中染料不易因脱色沾染到其他材质织物上)和耐摩擦色牢度(染色织物不在摩擦作用下褪色)。由该表还可发现,碱减量低温染色一浴工艺所得织物还原清洗与否都具有相同的耐水洗色牢度和耐摩擦色牢度,说明碱减量低温染色一浴工艺染色后仅需皂洗,无需传统工艺的碱性还原清洗步骤(以去除纤维表面浮色),即低温一浴工艺步骤更加环保。
[0089]
虽然本发明已以较佳实施例公开如上,但其并非用以限定本发明,任何熟悉此技术的人,在不脱离本发明的精神和范围内,都可做各种的改动与修饰,因此本发明的保护范围应该以权利要求书所界定的为准。