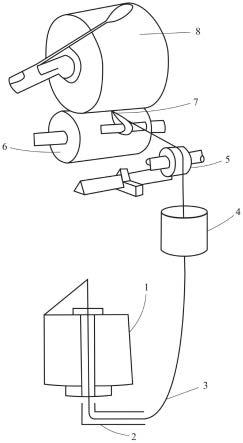
1.本发明涉及纺织技术领域,尤其涉及一种蚕丝仿桃皮绒织物。
背景技术:2.桃皮绒织物是由超细纤维组成的薄型织物,由于织物表面的绒短而密集,虽然肉眼几乎看不出绒毛但皮肤却能感知,因此织物的手感和外观更细腻。桃皮绒织物的开纤磨绒处理过程在其制备过程中至关重要,但该过程的生产工艺比较复杂且成本较高,因此,桃皮绒织物整体的生产效率并不高。基于上述原因,现有技术中通过在锦纶、涤纶等材料表面形成绒毛层来制备仿桃皮绒织物,但是现有的磨毛方法及应用的磨毛装置制得的纱线的质量不高,且容易在磨毛过程中对纱线进行损坏,致使最终得到的织物的手感受损。
3.现有技术中,中国专利申请号为202210104238.3,公开日期为2022年5月6日,名称为“绒毛机及绒毛纱的制备工艺”的发明专利中公开了一种绒毛机及绒毛纱的制备工艺,上述制备工艺中涉及到的磨毛机构包括回转盘和具有第一贯穿通道的磨毛件,第一贯穿通道的内壁为磨砂表面,通过回转盘的转动可引导纱线贴着第一贯穿通道的内壁做圆周运动,以使纱线被磨毛。上述磨毛过程中,纱线与第一贯穿通道的内壁进行摩擦,易使内壁温度过高和出现静电,不仅会对设备产生损坏,还会影响纱线的质量。
4.现有技术中,中国专利申请号为201621012077.1,公开日期为2017年3月22日,名称为“一种磨毛机”的实用新型中公开了一种磨毛机,包括机架、进布辊组、传动辊组、磨毛辊组和出布辊组,传动辊组和磨毛辊组之间设有加湿装置,加湿装置包括设有朝向面料表面的出水口的加湿体、转动连接于加湿体内的转动体、与加湿体相连通的进水管、驱动转动体转动的驱动组件。上述技术方案中,通过设置加湿装置对磨毛处理前的布料表面润湿,减少布料在磨毛过程中产生的静电,同时提升磨毛的质量。但对于吸水性较强的布料,应用上述装置进行磨毛处理时,由于布料表面浸润的水过多,磨毛过程不易进行,磨毛不充分;而对于吸水性弱的布料,无法对布料表面进行浸润,磨毛过程静电严重,因此,上述磨毛装置的适用性有限,且结构复杂。
5.有鉴于此,有必要设计一种更为简易的磨毛装置用于蚕丝仿桃皮绒织物的制备,以解决上述问题。
技术实现要素:6.本发明的目的在于提供一种蚕丝仿桃皮绒织物。
7.为实现上述发明目的,本发明提供了一种蚕丝仿桃皮绒织物,所述蚕丝仿桃皮绒织物通过将经过倍捻机加捻处理的蚕丝经磨毛处理后在织机上织造制得,所述磨毛处理通过加湿磨毛一体结构进行。
8.优选的,所述蚕丝仿桃皮绒织物的经纱密度为500~700根/10cm,纬纱密度为300~500根/10cm。
9.优选的,所述蚕丝仿桃皮绒织物的类型为平纹、斜纹及缎纹织物中的一种。
10.优选的,所述蚕丝的线密度为10~24tex,所述蚕丝的捻度为500~1200捻/m。
11.具体地,所述蚕丝的磨毛处理过程通过如下步骤进行:经倍捻机加捻后的蚕丝由贮纱盘引出后经过设置于所述贮纱盘一侧的加湿磨毛一体结构进行加湿磨毛处理后,再在超喂罗拉、往复导纱器及导纱罗拉的牵引下卷绕收集至纱筒上。
12.优选的,所述超喂罗拉的超喂率为50~80%。
13.优选的,所述加湿磨毛一体结构为砂轮。
14.优选的,所述砂轮为中空结构,所述砂轮的内径为20~30mm,所述砂轮的内壁设有磨料;优选的,所述磨料的目数为300~600目。
15.优选的,所述磨料上均匀分布有若干针孔;优选的,所述针孔的尺寸为100~150μm,针孔密度为30~40个/cm。
16.优选的,所述砂轮的中空夹层内填充有吸水脱脂棉。
17.本发明的有益效果是:
18.1、本发明提出的蚕丝仿桃皮绒织物,通过将经过倍捻机加捻处理的蚕丝经磨毛处理后在织机上织造制得,蚕丝的磨毛处理过程通过加湿磨毛一体结构进行;通过利用加湿磨毛一体结构对蚕丝进行磨毛处理,可制备出棉型感的蚕丝纱线,并最终制得超柔手感的仿桃皮绒蚕丝织物。
19.2、本发明提出的蚕丝仿桃皮绒织物,通过利用具有加湿磨毛功能的砂轮来对蚕丝进行磨毛处理,在砂轮的内壁设置针孔,同时,在砂轮的中空夹层内填充脱脂棉,可通过向中空夹层内注水使脱脂棉吸水来为磨毛过程中的蚕丝提供湿润的环境,脱脂棉上的水通过针孔与蚕丝接触以使蚕丝表面浸润,避免蚕丝磨毛过程蚕丝发生静电吸附在一起,确保蚕丝被充分磨毛;通过在蚕丝的磨毛过程同步进行加湿操作,可提升磨毛效果,有效确保了最终制得的仿桃皮绒织物表面平整、绒毛分布均匀且手感柔软。通过上述方式,提供了一种制备简单、质量高、手感好的蚕丝仿桃皮绒织物。此外,本发明提出的加湿磨毛一体结构也可应用于其他纱线的磨毛处理,进一步拓宽了上述方法的适用范围。
附图说明
20.图1为本发明中对蚕丝进行磨毛处理的加湿磨毛一体结构的结构示意图;
21.图2为图1中砂轮的内部结构示意图;
22.附图标记如下:
23.1、并纱筒子;2、贮纱盘;3、蚕丝;4、砂轮;5、超喂罗拉;6、往复导纱器;7、导纱罗拉;8、纱筒;9、磨料;10、密封圈;11、针孔;12、脱脂棉。
具体实施方式
24.为了使本发明的目的、技术方案和优点更加清楚,下面结合附图和具体实施例对本发明进行详细描述。
25.在此,还需要说明的是,为了避免因不必要的细节而模糊了本发明,在附图中仅仅示出了与本发明的方案密切相关的结构和/或处理步骤,而省略了与本发明关系不大的其他细节。
26.另外,还需要说明的是,术语“包括”、“包含”或者其任何其他变体意在涵盖非排他
性的包含,从而使得包括一系列要素的过程、方法、物品或者设备不仅包括那些要素,而且还包括没有明确列出的其他要素,或者是还包括为这种过程、方法、物品或者设备所固有的要素。
27.请参阅图1和图2所示,本发明提出的蚕丝仿桃皮绒织物为经过倍捻机加捻处理的蚕丝经磨毛处理后在织机上织造制得,蚕丝的磨毛处理过程通过加湿磨毛一体结构进行,加湿磨毛一体结构设置于贮纱盘2一侧,磨毛处理后的蚕丝依次通过超喂罗拉5、往复导纱器6及导纱罗拉7导至纱筒8进行卷绕收集。
28.优选的,蚕丝仿桃皮绒织物的经纱密度为500~700根/10cm,纬纱密度为300~500根/10cm,织物类型为平纹、斜纹及缎纹织物中的一种。
29.蚕丝磨毛处理过程包括如下步骤:从并纱筒子1上退绕出来的蚕丝3自并纱筒子1的顶端进入空心管中,经由锭子和贮纱盘2的回转加上捻回后从贮纱盘2的横向孔眼穿出,蚕丝3在贮纱盘外绕行一定弧度后引向上方,接着,蚕丝3进入砂轮4的内腔,蚕丝3在贮纱盘2的回转作用及砂轮4一侧的超喂罗拉5、往复导纱器6及导纱罗拉7的牵引作用下与砂轮4内壁接触,砂轮4内壁的磨料9给予蚕丝3一定的摩擦力,在蚕丝3的表面形成绒毛层。
30.优选的,蚕丝3的线密度为10~24tex。
31.优选的,砂轮4为中空结构,且内径为20~30mm;砂轮4的内壁设有磨料9,磨料9的目数为300~600目;磨料9上均匀分布有若干针孔11,针孔11的尺寸为100~150μm,针孔密度为30~40个/cm;砂轮4的中空夹层内填充有脱脂棉12,脱脂棉12通过砂轮4上端的密封圈10固定于中空夹层内,可通过使脱脂棉12吸水来为磨毛过程中的蚕丝3提供湿润的环境,避免磨毛过程出现静电,确保蚕丝被充分磨毛。
32.优选的,超喂罗拉5的超喂率为50~80%。
33.优选的,蚕丝3的捻度为500~1200捻/m。
34.下面结合具体的实施例对本发明进行进一步说明:
35.实施例1
36.对经过倍捻机加捻处理的蚕丝进行磨毛处理,磨毛处理过程通过如下步骤进行:使并纱筒子上退绕出来的蚕丝自并纱筒子的顶端进入空心管中,经由锭子和贮纱盘的回转加上捻回后从贮纱盘的横向孔眼穿出,蚕丝在贮纱盘外绕行一定弧度后引向上方,接着,蚕丝进入砂轮的内腔,利用砂轮内的磨料对其进行磨毛处理,砂轮的内径为20mm,内壁的磨料的目数为600目,磨料上设置有水针孔,针孔的尺寸为150μm,针孔密度为40个/cm。然后,使磨毛后的蚕丝依次经过超喂罗拉、往复导纱器及导纱罗拉,以将经过磨毛处理后的蚕丝导至纱筒进行卷绕收集,其中超喂罗拉的超喂率为78%;其中,蚕丝的捻度为800捻/m,线密度为15tex。最后,将经过磨毛处理的蚕丝在织机上织造成斜纹织物,织物的经纱密度为600根/10cm,纬纱密度为根500根/10cm。本实施例中蚕丝经过磨毛处理后其表面的毛羽数量为:1mm以内的毛羽量为3295根/m,2mm的毛羽量为36根/m,3mm及以上的毛羽量为0,所得织物手感滑糯,桃皮绒效果明显。
37.实施例2至3
38.实施例2至3与实施例1的区别仅在于:砂轮内壁磨料的目数不同,其他步骤与实施例1基本相同,在此不再赘述。实施例2至3的磨料目数的设置如表1所示,实施例2至3中蚕丝经过磨毛处理后其表面1mm毛羽量分别为2964和2803根/m,2mm的毛羽量分别为53和61根/
m,3mm及以上的毛羽量为0,所得织物手感滑糯,桃皮绒效果明显。
39.表1实施例1至3中设置的磨料目数
40.项目目数(目)实施例1600实施例2400实施例3300
41.实施例4至5
42.实施例4至5与实施例1的区别仅在于:砂轮的内径不同,其他步骤与实施例1基本相同,在此不再赘述。实施例4至5的砂轮内径的设置如表2所示,实施例4至5中蚕丝经过磨毛处理后其表面的1mm毛羽量分别为2978和2856根/m,2mm的毛羽量分别为48和56根/m,3mm及以上的毛羽量均为0,所得织物手感滑糯,桃皮绒效果明显。
43.表2实施例1和实施例4至5中设置的砂轮内径
44.项目砂轮内径(mm)实施例120实施例425实施例530
45.实施例6至7
46.实施例6至7与实施例1的区别仅在于:砂轮内壁磨料上的针孔的密度不同,其他步骤与实施例1基本相同,在此不再赘述。实施例6至7的针孔密度的设置如表3所示,实施例6至7的针孔密度的设置如表3所示,实施例6至7中蚕丝经过磨毛处理后其表面的毛羽量分别为3023和2954根/m,2mm的毛羽量分别为42和51根/m,3mm及以上的毛羽量均为0,所得织物手感滑糯,桃皮绒效果明显。
47.表3实施例1和实施例6至7中设置的针孔密度
48.项目针孔密度(个/cm)实施例140实施例635实施例730
49.对比例1
50.对比例1与实施例1的区别仅在于:不向磨料的中空夹层内注水,使蚕丝在磨料处于干燥的情况下进行磨毛处理,其他步骤与实施例1基本相同,在此不再赘述。对比例1中蚕丝经过磨毛处理后其表面的1mm毛羽数量为1995根/m,2mm的毛羽量为137根/m,3mm的毛羽量为25根/m,4mm的毛羽量为5根/m,5mm及以上的毛羽量为0,所得织物手感较滑糯,桃皮绒效果较差,结果表明,应用本发明提供的加湿磨毛一体结构对蚕丝进行磨毛处理的磨毛效果优良。
51.综上所述,本发明通过利用加湿磨毛一体结构对蚕丝进行磨毛处理,可制备出棉型感的蚕丝纱线,并最终制得超柔手感的仿桃皮绒蚕丝织物;通过利用具有加湿磨毛功能的砂轮来对蚕丝进行磨毛处理,在砂轮的内壁设置针孔,在砂轮的中空夹层内填充脱脂棉,磨毛处理时向中空夹层内注水使脱脂棉吸水,进而为磨毛过程中的蚕丝提供湿润的环境,
避免蚕丝在磨毛过程中受损,并能在避免磨毛过程中产生的静电的同时,对磨毛过程产生的热量进行分散,确保了磨毛处理后蚕丝的质量及最终制得的织物的手感。通过上述方式,提供了一种制备简单、质量高、手感好的蚕丝仿桃皮绒织物。
52.以上实施例仅用以说明本发明的技术方案而非限制,尽管参照较佳实施例对本发明进行了详细说明,本领域的普通技术人员应当理解,可以对本发明的技术方案进行修改或者等同替换,而不脱离本发明技术方案的精神和范围。