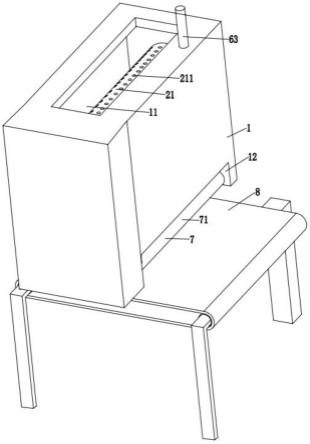
1.本发明涉及羽绒絮片制造技术领域,具体是一种抗菌吸湿的轻质仿羽绒絮片的生产设备及其生产工艺。
背景技术:2.仿羽绒絮片是由混合纤维丝铺设成一定厚度后注入粘接剂然后进行压缩冷却成型,现有的仿羽绒絮片的生产工艺中,主要对混合纤维丝进行注入粘接剂和压缩固化流程。
3.轻质仿羽绒絮片主要用于加工棉服和被褥,用于加工成羽绒絮片的混合纤维丝由于质量较轻、易于漂浮,在填充过程中难度较大,所以通常用粘接剂将混合纤维丝加工成具有一定厚度的薄片形成羽绒絮片,然后将羽绒絮片缝合进口袋状的胆布中,再将胆布缝合进棉服内衬中,由此加工成羽绒服,但是在实际生产中仍发现现有工艺以及生产设备存在一些不足,具体如下:
4.1.现有设备在加工时,由于混合纤维丝本身质量较轻、易于漂浮的特点,导致混合纤维丝在注入粘接剂时,粘接剂难以对混合纤维丝进行充分填充,进而导致混合纤维丝之间粘接不牢固,从而导致了形成羽绒絮片后不牢固的质量问题。
5.2.现有设备在加工时,由于混合纤维丝质量轻、易于漂浮的特点,导致混合纤维丝在加工时,尤其是注完粘接剂后,混合纤维丝容易附着在设备内部,进而大量堆积影响了设备的正常使用,并且造成了生产中的资源浪费。
6.3.现有设备在加工时,混合纤维丝在被压缩形成羽绒絮片过程中,由于表面具有粘接剂再被压缩时与传送带密切贴合,导致在压缩完成后粘接在传送带表面,如果强行扯下会破坏羽绒絮片表面结构,进而对羽绒絮片的成型和后续加工造成影响。
7.鉴于此,本发明提供一种能够对混合纤维丝充分填充粘接剂,并且能够对填充粘接剂后的混合纤维丝进行导向和清理,以及防止粘接在传送带表面,减少压缩固化时间的一种抗菌吸湿的轻质仿羽绒絮片的生产设备。
技术实现要素:8.为解决上述问题,本发明提供一种抗菌吸湿的轻质仿羽绒絮片的生产设备,用以解决混合纤维丝粘接剂附着不充分、混合纤维丝大量堆积和压缩固化加工时间长的问题。
9.本发明还提供了一种上述抗菌吸湿的轻质仿羽绒絮片生产工艺,用以解决羽绒絮片粘接在传送带表面的问题。
10.一种抗菌吸湿的轻质仿羽绒絮片的生产设备,包括壳体和传送带,壳体顶部开设有进料口,壳体下方侧壁开设有出料口,壳体侧壁固定安装有隔离板,壳体下方设置有传送带;一种抗菌吸湿的轻质仿羽绒絮片的生产设备还包括注胶机构、传动机构、检测控制机构、料斗、清洁机构和固化机构,进料口下方壳体侧壁设有注胶机构,注胶机构用于对混合纤维丝进行喷涂粘接剂;传动机构设于壳体侧壁的隔离板表面,并且通过隔离板与其余机构相隔;所述壳体内位于注胶机构上方固定设有检测控制机构,检测控制机构能够通过控
制系统控制注胶机构与清洁机构;所述壳体侧壁于所述注胶机构下方安装有料斗,所述料斗能够对喷涂完粘接剂的混合纤维丝进行导向,所述料斗上下两侧均设有清洁机构,所述料斗下侧的清洁机构下方设有固化机构,固化机构用于对混合纤维丝内部粘接剂进行固化和压缩,清洁机构能够对壳体内部侧壁和固化机构进行清洁。
11.作为本发明的可选方案,所述注胶机构包括旋转辊,旋转辊一端转动安装于壳体侧壁,所述旋转辊另一端贯穿安装于所述隔离板侧壁,所述旋转辊表面开设有多个喷胶口;粘接剂通过胶管流通至旋转辊内部,旋转辊能够使粘接剂呈水雾状喷出分布在旋转辊四周,进而在壳体内上方形成雾化粘接区域;旋转辊在旋转时能够使进料口进入的混合纤维丝旋转充分接触粘接剂,这样当混合纤维丝由进料口进入后受到旋转辊的旋转引导,混合纤维丝能够呈旋转式下落充分接触粘接剂;混合纤维丝质量较轻在空气中漂浮时间较长,混合纤维丝在漂浮的过程中,充分接触粘接剂的混合纤维丝因为粘接剂附着在混合纤维丝表面增加混合纤维丝的质量,使混合纤维丝下落速度加快,有利于提高混合纤维丝的加工效率;这样在混合纤维丝由进料口进料后,旋转辊喷涂粘接剂形成的雾状粘接区域,能够使混合纤维丝表面充分附着粘接剂,并且旋转时喷出粘接剂形成旋转气流带动混合纤维丝旋转下落,进一步使混合纤维丝表面附着的粘接剂更加充分。
12.作为本发明的可选方案,所述传动机构包括正反转电机和传动杆,正反转电机通过固定板倾斜固定安装于所述隔离板上方,传动杆一端固定连接于正反转电机,传动杆转动安装于第二固定板内,并且第二固定板和传动杆均倾斜安装于所述隔离板侧壁,传动杆表面与所述旋转辊贯穿端安装有相互啮合转动的锥齿轮;正反转电机与旋转辊的配合,能够实现旋转辊正反转喷出粘接剂形成不规则气流,不规则气流能够使混合纤维丝进行不规则旋转,进一步使混合纤维丝表面更加充分的附着粘接剂。
13.作为本发明的可选方案,所述检测控制机构包括浓度传感器和红外传感器,浓度传感器镶嵌安装于所述隔离板上方侧壁,红外传感器固定安装于旋转辊上方的壳体顶部,浓度传感器和红外传感器均与控制系统电连接;浓度传感器用于检测所述旋转辊喷出的雾状粘接剂于空气中漂浮的浓度,并通过控制系统控制旋转辊喷出压力,即空气中雾化粘接剂浓度低于w,浓度传感器检测后通过控制系统控制旋转辊提高压力使粘接剂喷出量提高;相反的,高于w时,浓度传感器通过控制系统降低旋转辊压力减少粘接剂喷出量;
14.红外传感器用于检测壳体侧壁附着的混合纤维丝,并通过控制系统使清洁机构对壳体侧壁的混合纤维丝进行清理,使混合纤维丝表面的粘接剂固化前就经过料斗落入传送带表面;浓度传感器通过控制系统与旋转辊的配合能够实现对喷出的粘接剂浓度进行调节,保证了混合纤维丝能够充分附着粘接剂;红外传感器与清理机构的配合能够使附着在壳体侧壁的混合纤维丝落入传送带继续使用,并且避免了因为混合纤维丝的大量堆积导致的设备问题;
15.浓度传感器能够通过控制系统调节旋转辊喷出的粘接剂流量,保证了雾化的粘接剂浓度,避免了浓度过低粘接剂附着不充分导致的质量问题,和粘接剂浓度和喷出量过高造成的资源浪费;红外传感器通过控制系统控制清洁机构能够清理粘连在壳体侧壁的混合纤维丝,避免了混合纤维丝于壳体侧壁粘连堆积导致的设备故障,并且在混合纤维丝表面粘接剂固化前就落入传送带,这样有利于减少设备故障和混合纤维丝在加工过程中的浪费。
16.作为本发明的可选方案,所述料斗为三角形结构并且沿壳体两侧对称安装,所述料斗表面开设有多个气孔,所述料斗用于对混合纤维丝进行导向使混合纤维丝稳定的落入传送带,所述料斗下侧开口于传送带对应,所述料斗表面气孔吹出的气体沿料斗表面向下,能够避免混合纤维丝粘连在料斗表面,并且使混合纤维丝按照气体流动方向稳定落入传送带,使混合纤维丝在经过雾化粘接后的不规则漂浮变为稳定的定向漂浮;料斗与旋转辊的配合能够使不规则旋转的混合纤维丝重新导向,使混合纤维丝正确的落入传送带表面。
17.作为本发明的可选方案,所述清洁机构包括第一毛刷和第二毛刷,第一毛刷呈口型结构滑动安装于料斗上方的壳体侧壁,第一毛刷顶部固定连接有用于驱动第一毛刷的气缸,气缸可拆卸的安装在壳体顶部,第一毛刷能够贴合壳体侧壁上下滑动进行清理混合纤维丝;第二毛刷为矩形结构,并且第二毛刷对称固定安装于两侧料斗下方;所述第一毛刷能够清理壳体侧壁粘连的混合纤维丝,红外传感器能够通过控制系统控制第一毛刷;第二毛刷用于清理固化机构,第一毛刷能够保持壳体内部的清洁,有利于提高设备的使用效率。
18.作为本发明的可选方案,所述固化机构包括压紧辊,所述传动机构还包括丝杠,丝杠通过第三固定板安装于隔离板侧壁,丝杠一端与传动杆底端通过安装相互啮合的锥齿轮进行同步转动,丝杠表面安装有滑动块,滑动块能够于固定板间滑动;压紧辊位于料斗下方并且一端固定连接于所述滑动块;所述压紧辊通过电机旋转,所述滑动块能够驱动所述压紧辊于传送带上方往复移动,所述压紧辊与所述传送带距离等于羽绒絮片的加工厚度;在混合纤维丝落入传送带表面后,所述压紧辊能够使混合纤维丝因为表面附着的粘接剂压缩加工成具有一定厚度的羽绒絮片,压紧辊于传送带表面往复移动,进一步的提高了加工成羽绒絮片的效率;
19.在压紧辊进行压缩加工时,部分羽绒絮片粘接至压紧辊表面,此时往复移动压缩的压紧辊移动至料斗下方的第二毛刷,第二毛刷与压紧辊表面接触并且对压紧辊表面的混合纤维丝进行清理,第二毛刷使清理后的混合纤维丝重新落入料斗下方的传送带;第二毛刷保证了压紧辊在压缩加工时的稳定性,避免了混合纤维丝粘接压紧辊表面导致的加工异常和设备故障,并且清理后的混合纤维丝落入传送带,进一步的减少了混合纤维丝在加工过程中的资源浪费,有效减少了生产成本。
20.作为本发明的可选方案,所述压紧辊内安装有电热丝,电热丝能够对压紧辊进行加热,使得压紧辊能够对混合纤维丝表面附着粘接剂进行热固化,有效的减少了粘接剂的凝固时间提高加工效率,往复移动能够避免长时间对同一位置的混合纤维丝进行加热固化,进而避免使混合纤维丝内粘接剂因为快速固化后粘接在传送带表面,从而避免了强行拉扯羽绒絮片致使的破坏羽绒絮片表面结构;并且往复移动增加了热固化的面积,在受到加热固化效果影响的混合纤维丝冷却之前能够再次对该区域混合纤维丝进行加热固化,进一步减少了粘接剂的凝固时间、提高混合纤维丝加工成羽绒絮片的效率;第二毛刷对压紧辊的清理,避免了压紧辊表面包裹大量的混合纤维丝,从而影响压紧辊对传送带表面的混合纤维丝粘接剂的固化效果,进一步的保证了压紧辊的热固化效果;压紧辊和第二毛刷的配合能够使粘接在压紧辊表面的羽绒絮片继续加工使用,并且保证了压紧辊的热固化效果。
21.作为本发明的可选方案,所述压紧辊表面设有多个凹凸面,在往复移动的过程中凹凸面交替的对混合纤维丝进行压缩固化,这样凹凸面能够在压紧辊对混合纤维丝进行压
缩固化的时候,避免羽绒絮片与传送带的密切贴合导致的粘接,有利于加工完成后的羽绒絮片脱离传送带。
22.一种抗菌吸湿的轻质仿羽绒絮片的生产工艺过程如下:
23.步骤一:注入粘接剂,将混合纤维丝放入进料口内,正反转电机启动并通过传动杆带动旋转辊同步转动,旋转辊呈雾化状喷出粘接剂,雾化粘接剂形成雾化粘接区,旋转辊正反转喷出的粘接剂引发的气流能够使混合纤维丝在壳体内进行不规则旋转,使混合纤维丝穿过雾化粘接区充分附着粘接剂;浓度传感器对空气中雾化粘接剂进行检测,并通过控制系统调整旋转辊喷出粘接剂压力,红外传感器检测到壳体侧壁堆积混合纤维丝,并通过控制系统控制第一毛刷清理壳体侧壁;然后经过料斗和气孔吹出的气流对混合纤维丝进行导向,使混合纤维丝能够稳定落入传送带表面,并且使混合纤维丝在重力作用下能够相互堆叠进行粘接;
24.步骤二:压缩固化,在完成步骤一后,电机通过传动杆带动丝杠同步正反转,丝杠通过滑动块带动压紧辊于固定板间往复滑动,这样能够使压紧辊于传送带表面对附着完粘接剂的混合纤维丝进行反复压缩使其成为具有一定厚度的羽绒絮片;并且在反复压缩的过程中,压紧辊内设置的电热丝对混合纤维丝表面附着的粘接剂进行加热固化,并且避免对同一位置的混合纤维丝加热固化,进而避免使粘接剂快速固化致使混合纤维丝粘接至传送带表面;
25.步骤三:冷却收卷,在对步骤二完成后的羽绒絮片进行自然冷却处理,传送带表面铺设有同步转动的多层分离网,各层分离网通过分离辊逐个分开;工作过程中,各层分离网协同配合将羽绒絮片脱离传送带,而后在分离辊的配合下,将分离网逐层与羽绒絮片剥离,最终让羽绒絮片卷绕在卷辊上;在分离网与羽绒絮片分离后,分离网通过回卷辊牵引贴合传送带;多层分离网能够使羽绒絮片顺利脱离传送带避免了相互粘接;卷辊对冷却完成的羽绒絮片进行收卷牵引,使羽绒絮片能够脱离传送带,并且通过分离网使混合纤维丝不与传送带不发生粘连情况。
26.其中,混合纤维丝包括木浆纤维和控温纤维;
27.木浆纤维采用纺前注射技术制成,纺前注射技术即木浆纤维在挤出成型时,通过小型注射器使注射器内物质熔炼混合至木浆纤维内;通过坊前注射技术向木浆纤维内添加有机酸、过氧化氢、甲基乙二醛、乳酸菌素其中一种或多种活性抗菌物质,在熔炼混合时活性抗菌能够均匀的分布在木浆纤维表面,这样能够提高木浆纤维的抗菌性和除臭性,进而保证人员在穿着时的健康情况;
28.控温纤维即聚酯纤维,采用四孔模头喷丝和物理法亲水整理方法制成;通过四孔喷头喷丝使控温纤维横截面呈四孔的圆形,这样能够提高控温纤维容纳静止空气的能力,进而提高了控温纤维的保暖性能;并且控温纤维在成型的过程中表面添加有亲水层,亲水层由亲水物质如淀粉接枝丙烯酸盐、纤维素接枝丙烯酸盐、交联聚丙烯酸盐其中一种或多种制成,这样能够提高控温纤维的亲水性能,从而提高羽绒絮片制成的服装舒适度;
29.由木浆纤维和控温纤维制成的羽绒絮片,通过木浆纤维和控温纤维表面的亲水层,使吸湿速干性能≥3级,吸湿排汗性能≥3级;并且热固化加工保证了羽绒絮片的蓬松性,进而保证了羽绒絮片的保暖性,能够使羽绒絮片的保暖性≥55%;并且纺前注射技术中添加的活性抗菌物质能够使抑菌率≥70%和醋酸降低率≥70%,并且活性抗菌物质通过熔
炼混合的方法能够在水洗50次以后依然保持良好的抑菌效果,即能够使抑菌率和醋酸降低率均保持在≥40%。
30.本发明通过以上技术方案,能够实现的有益效果为:
31.1.本发明所述的一种仿羽绒絮片生产设备,本发明通过旋转辊和浓度传感器以及传动机构相互配合的设计,使传动机构驱动旋转辊正反转喷出雾状粘接剂,实现了混合纤维丝发生不规则旋转再经过雾化粘接区后能够充分附着粘接剂;并且浓度传感器能够通过控制系统控制旋转辊喷射的粘接剂浓度,保证了混合纤维丝能够充分附着粘接剂,避免了因粘接剂附着不充分导致的粘接不牢靠的质量问题。
32.2.本发明所述的一种仿羽绒絮片生产设备,本发明通过料斗、旋转辊、红外传感器和第一毛刷的相互配合,实现了在混合纤维丝在经过旋转辊的牵引进行不规则旋转并且附着完粘接剂后,料斗能够对混合纤维丝进行固定导向稳定的落入传送带表面,避免了混合纤维丝长时间进行不规则转动无法落入传送带的情况,有利于实现后续加工提高生产效率;红外传感器检测到混合纤维丝粘接至壳体后通过控制系统控制第一毛刷滑动对混合纤维丝进行清理,能够避免混合纤维丝大量堆积在壳体侧壁造成的设备故障和材料浪费,有利于延长设备工作时间提高加工效率和减少成本浪费。
33.3.本发明所述的一种仿羽绒絮片生产设备,本发明通过第二毛刷、丝杠和压紧辊的相互配合,实现了在压紧辊进行压缩时第一毛刷对表面附着的混合纤维丝进行清理,避免了混合纤维丝粘接压紧辊表面导致的加工异常和设备故障,保证了压紧辊进行压缩加工时的稳定性,并且清理后的混合纤维丝落入传送带,进一步的减少了混合纤维丝在加工过程中的资源浪费。
34.4.本发明所述的一种仿羽绒絮片生产设备,本发明通过压紧辊内设有的电热丝能够通过丝杠往复移动增加了热固化的面积,减少了粘接剂的凝固时间,进一步提高混合纤维丝加工成羽绒絮片的效率,第二毛刷避免了压紧辊表面包裹大量的混合纤维丝,进一步提高了加热固化的效率;压紧辊表面的凹凸面能够在压紧辊对混合纤维丝进行压缩固化的时候,避免羽绒絮片与传送带的密切贴合导致的粘接,有利于加工完成后的羽绒絮片脱离传送带。
35.5.本发明所述的一种仿羽绒絮片生产工艺,本发明通过传送带表面铺设多层分离网的设计,能够使限位丝落在分离网表面形成羽绒絮片,从而避免羽绒絮片在粘接剂固化后粘接在传送带表面;并且多层分离网与分离辊的逐步分离设计,能够使分离网与羽绒絮片进行多次分离,从而减小分离网与羽绒絮片每次分离时的拉扯力度;当最后一层分离网与羽绒絮片分离时,拉扯力度经过多次减小,避免了分离网与羽绒絮片分离时破坏羽绒絮片表面的结构。
附图说明
36.下面对本发明的附图进行介绍,以便于本领域技术人员理解。
37.图1为本发明整体结构示意图;
38.图2为本发明传动机构结构示意图;
39.图3为本发明内部结构示意图
40.图4为本发明压紧辊凹凸面结构示意图;
41.图5为本发明工艺流程示意图;
42.图6为本发明羽绒絮片脱离传送带收卷示意图。
43.图中:壳体1、进料口11、出料口12、隔离板13、注胶机构2、旋转辊21、喷胶口211、传动机构3、正反转电机31、传动杆32、丝杠33、滑动块331、固定板34、第二固定板341、第三固定板342、检测控制机构4、浓度传感器41、红外传感器42、料斗5、气孔51、清洁机构6、第一毛刷61、第二毛刷62、气缸63、固化机构7、压紧辊71、凹凸面72、传送带8、卷辊81、分离网82、分离辊83、回卷辊84。
具体实施方式
44.为了便于本领域人员理解,下面对本发明的技术方案进行详细讲解。
45.如图1至3所示,一种抗菌吸湿的轻质仿羽绒絮片的生产设备,包括壳体1和传送带8,壳体1顶部开设有进料口11,壳体1下方侧壁开设有出料口12,壳体1侧壁固定安装有隔离板13,壳体1下方设置有传送带8;一种抗菌吸湿的轻质仿羽绒絮片的生产设备还包括注胶机构2、传动机构3、检测控制机构4、料斗5、清洁机构6和固化机构7,进料口11下方壳体1侧壁设有注胶机构2,注胶机构2用于对混合纤维丝进行喷涂粘接剂;传动机构3设于壳体1侧壁的隔离板13表面,并且通过隔离板13与其余机构相隔;所述壳体1内位于注胶机构2上方固定设有检测控制机构4,检测控制机构4能够通过控制系统控制注胶机构2与清洁机构6;所述壳体1侧壁于所述注胶机构2下方安装有料斗5,所述料斗5能够对喷涂完粘接剂的混合纤维丝进行导向,所述料斗5上下两侧均设有清洁机构6,所述料斗5下侧的清洁机构6下方设有固化机构7,固化机构7用于对混合纤维丝内部粘接剂进行固化和压缩,清洁机构6能够对壳体1内部侧壁和固化机构7进行清洁。
46.如图1至3所示,作为本发明的可选实施例,所述注胶机构2包括旋转辊21,旋转辊21一端转动安装于壳体1侧壁,所述旋转辊21另一端贯穿安装于所述隔离板13侧壁,所述旋转辊21表面开设有多个喷胶口211;粘接剂通过胶管流通至旋转辊21内部,旋转辊21能够使粘接剂呈水雾状喷出分布在旋转辊21四周,进而在壳体1内上方形成雾化粘接区域;旋转辊21在旋转时能够使进料口11进入的混合纤维丝旋转充分接触粘接剂,这样当混合纤维丝由进料口11进入后受到旋转辊21的旋转引导,混合纤维丝能够呈旋转式下落充分接触粘接剂;混合纤维丝质量较轻在空气中漂浮时间较长,混合纤维丝在漂浮的过程中,充分接触粘接剂的混合纤维丝因为粘接剂附着在混合纤维丝表面增加混合纤维丝的质量,使混合纤维丝下落速度加快,有利于提高混合纤维丝的加工效率;这样在混合纤维丝由进料口11进料后,旋转辊21喷涂粘接剂形成的雾状粘接区域,能够使混合纤维丝表面充分附着粘接剂,并且旋转时喷出粘接剂形成旋转气流带动混合纤维丝旋转下落,进一步使混合纤维丝表面附着的粘接剂更加充分。
47.如图2所示,作为本发明的可选实施例,所述传动机构3包括正反转电机31和传动杆32,正反转电机31通过固定板34倾斜固定安装于所述隔离板13上方,传动杆32一端固定连接于正反转电机31,传动杆32转动安装于第二固定板341内,并且第二固定板341和传动杆32均倾斜安装于所述隔离板侧壁,传动杆32表面与所述旋转辊21贯穿端安装有相互啮合转动的锥齿轮;正反转电机31与旋转辊21的配合,能够实现旋转辊21正反转喷出粘接剂形成不规则气流,不规则气流能够使混合纤维丝进行不规则旋转,进一步使混合纤维丝表面
更加充分的附着粘接剂。
48.如图3所示,作为本发明的可选实施例,所述检测控制机构4包括浓度传感器41和红外传感器42,浓度传感器41镶嵌安装于所述隔离板13上方侧壁,红外传感器42固定安装于旋转辊21上方的壳体1顶部,浓度传感器41和红外传感器42均与控制系统电连接;浓度传感器41用于检测所述旋转辊21喷出的雾状粘接剂于空气中漂浮的浓度,并通过控制系统控制旋转辊21喷出压力,即空气中雾化粘接剂浓度低于w时,浓度传感器41检测后通过控制系统控制旋转辊21提高压力使粘接剂喷出量提高;相反的,高于w时,浓度传感器41通过控制系统降低旋转辊21压力减少粘接剂喷出量;
49.红外传感器42用于检测壳体1侧壁附着的混合纤维丝,并通过控制系统使清洁机构6对壳体1侧壁的混合纤维丝进行清理,使混合纤维丝表面的粘接剂固化前就经过料斗5落入传送带8表面;浓度传感器41通过控制系统与旋转辊21的配合能够实现对喷出的粘接剂浓度进行调节,保证了混合纤维丝能够充分附着粘接剂;红外传感器42与清理机构的配合能够使附着在壳体1侧壁的混合纤维丝落入传送带8继续使用,并且避免了因为混合纤维丝的大量堆积导致的设备问题;
50.浓度传感器41能够通过控制系统调节旋转辊21喷出的粘接剂流量,保证了雾化的粘接剂浓度,避免了浓度过低粘接剂附着不充分导致的质量问题,和粘接剂浓度和喷出量过高造成的资源浪费;红外传感器42通过控制系统控制清洁机构6能够清理粘连在壳体1侧壁的混合纤维丝,避免了混合纤维丝于壳体1侧壁粘连堆积导致的设备故障,并且在混合纤维丝表面粘接剂固化前就落入传送带8,这样有利于减少设备故障和混合纤维丝在加工过程中的浪费。
51.如图3所示,作为本发明的可选实施例,所述料斗5为三角形结构并且沿壳体1两侧对称安装,所述料斗5表面开设有多个气孔51,所述料斗5用于对混合纤维丝进行导向使混合纤维丝稳定的落入传送带8,所述料斗5下侧开口于传送带8对应,所述料斗5表面气孔51吹出的气体沿料斗5表面向下,能够避免混合纤维丝粘连在料斗5表面,并且使混合纤维丝按照气体流动方向稳定落入传送带8,使混合纤维丝在经过雾化粘接后的不规则漂浮变为稳定的定向漂浮;料斗5与旋转辊21的配合能够使不规则旋转的混合纤维丝重新导向,使混合纤维丝正确的落入传送带8表面。
52.如图3所示,作为本发明的可选实施例,所述清洁机构6包括第一毛刷61和第二毛刷62,第一毛刷61呈口型结构滑动安装于料斗5上方的壳体1侧壁,第一毛刷61顶部固定连接有用于驱动第一毛刷的气缸63,气缸63可拆卸的安装在壳体1顶部,第一毛刷61能够贴合壳体侧壁上下滑动进行清理混合纤维丝;第二毛刷62为矩形结构,并且第二毛刷62对称固定安装于两侧料斗5下方;所述第一毛刷61能够清理壳体1侧壁粘连的混合纤维丝,红外传感器42能够通过控制系统控制第一毛刷61;第二毛刷62用于清理固化机构7,第一毛刷61能够保持壳体1内部的清洁,有利于提高设备的使用效率。
53.如图1至3所示,作为本发明的可选实施例,所述固化机构7包括压紧辊71,所述传动机构还包括丝杠33,丝杠33通过第三固定板342安装于隔离板13侧壁,丝杠33一端与传动杆32底端通过安装相互啮合的锥齿轮进行同步转动,丝杠表面安装有滑动块331,滑动块能够于固定板间滑动;压紧辊71位于料斗5下方并且一端固定连接于所述滑动块331;所述压紧辊71通过电机旋转,所述滑动块331能够驱动所述压紧辊71于传送带8上方往复移动,所
述压紧辊71与所述传送带8距离等于羽绒絮片的加工厚度;在混合纤维丝落入传送带8表面后,所述压紧辊71能够使混合纤维丝因为表面附着的粘接剂压缩加工成具有一定厚度的羽绒絮片,压紧辊71于传送带8表面往复移动,进一步的提高了加工成羽绒絮片的效率;
54.在压紧辊71进行压缩加工时,部分羽绒絮片粘接至压紧辊71表面,此时往复移动压缩的压紧辊71移动至料斗5下方的第二毛刷62,第二毛刷62与压紧辊71表面接触并且对压紧辊71表面的混合纤维丝进行清理,第二毛刷62使清理后的混合纤维丝重新落入料斗5下方的传送带8;第二毛刷62保证了压紧辊71在压缩加工时的稳定性,避免了混合纤维丝粘接压紧辊71表面导致的加工异常和设备故障,并且清理后的混合纤维丝落入传送带8,进一步的减少了混合纤维丝在加工过程中的资源浪费,有效减少了生产成本。
55.如图1至3所示,作为本发明的可选实施例,所述压紧辊71内安装有电热丝,电热丝能够对压紧辊71进行加热,使得压紧辊71能够对混合纤维丝表面附着粘接剂进行热固化,有效的减少了粘接剂的凝固时间提高加工效率,往复移动能够避免长时间对同一位置的混合纤维丝进行加热固化,进而避免使混合纤维丝内粘接剂因为快速固化后粘接在传送带8表面,从而避免了强行拉扯羽绒絮片致使的破坏羽绒絮片表面结构;并且往复移动增加了热固化的面积,在受到加热固化效果影响的混合纤维丝冷却之前能够再次对该区域混合纤维丝进行加热固化,进一步减少了粘接剂的凝固时间、提高混合纤维丝加工成羽绒絮片的效率;第二毛刷62对压紧辊71的清理,避免了压紧辊71表面包裹大量的混合纤维丝,从而影响压紧辊71对传送带8表面的混合纤维丝粘接剂的固化效果,进一步的保证了压紧辊71的热固化效果;压紧辊71和第二毛刷62的配合能够使粘接在压紧辊71表面的羽绒絮片继续加工使用,并且保证了压紧辊71的热固化效果。
56.如图1至4所示,作为本发明的可选实施例,所述压紧辊71表面设有多个凹凸面72,在往复移动的过程中凹凸面72交替的对混合纤维丝进行压缩固化,这样凹凸面72能够在压紧辊71对混合纤维丝进行压缩固化的时候,避免羽绒絮片与传送带8的密切贴合导致的粘接,有利于加工完成后的羽绒絮片脱离传送带8。
57.工作时,操作人员通过控制系统启动该设备,正反转电机31通过传动杆32带动旋转辊21和丝杠33进行正反转,混合纤维丝经由入料口间断进入,红外传感器42检测到混合纤维丝进入通过控制系统使旋转辊21喷射粘接剂,喷射的粘接剂在空气中形成雾化粘接区,混合纤维丝在漂浮的过程中受旋转辊21正反转牵引进行不规则旋转,不规则旋转在雾化区域中充分接触粘接剂,部分混合纤维丝在旋转过程中粘接在壳体1侧壁,经由红外传感器42检测使第一毛刷61向上滑动清理壳体1侧壁混合纤维丝,当旋转辊21喷射使空气中粘接剂含量过高,经由浓度传感器41检测降低旋转辊21喷射量,相反,空气中粘接剂含量过低时使旋转辊21喷射量增加;当红外传感器42检测到混合纤维丝停止进入时,通过控制系统控制旋转辊21停止喷射粘接剂;
58.随后混合纤维丝在充分附着粘接剂后质量增加,经由料斗5表面气孔51的气流牵引导向落入传送带8,压紧辊71旋转并且通过丝杠33能够于壳体1内部在传送带8表面往复移动,同时对混合纤维丝进行压缩使其成为羽绒絮片,并且内部电热丝对粘接剂进行加热固化,随即加工成型通过出料口12。
59.一种抗菌吸湿的轻质仿羽绒絮片的生产工艺过程如下:
60.步骤一:注入粘接剂,将混合纤维丝放入进料口12内,正反转电机31启动并通过传
动杆32带动旋转辊21同步转动,旋转辊21呈雾化状喷出粘接剂,雾化粘接剂形成雾化粘接区,旋转辊21正反转喷出的粘接剂引发的气流能够使混合纤维丝在壳体1内进行不规则旋转,使混合纤维丝穿过雾化粘接区充分附着粘接剂;浓度传感器41对空气中雾化粘接剂进行检测,并通过控制系统调整旋转辊21喷出粘接剂压力,红外传感器42检测到壳体1侧壁堆积混合纤维丝,并通过控制系统控制第一毛刷62清理壳体1侧壁;然后经过料斗5和气孔51吹出的气流对混合纤维丝进行导向,使混合纤维丝能够稳定落入传送带8表面,并且使混合纤维丝在重力作用下能够相互堆叠进行粘接;
61.步骤二:压缩固化,在完成步骤一后,电机通过传动杆带动丝杠同步正反转,丝杠通过滑动块带动压紧辊于固定板间往复滑动,这样能够使压紧辊71于传送带8表面对附着完粘接剂的混合纤维丝进行反复压缩使其成为具有一定厚度的羽绒絮片;并且在反复压缩的过程中,压紧辊71内设置的电热丝对混合纤维丝表面附着的粘接剂进行加热固化,并且避免对同一位置的混合纤维丝加热固化,进而避免使粘接剂快速固化致使混合纤维丝粘接至传送带8表面;
62.步骤三:冷却收卷,在对步骤二完成后的羽绒絮片进行自然冷却处理,传送带8表面铺设有同步转动的多层分离网82,各层分离网82通过分离辊83逐个分开;工作过程中,各层分离网82协同配合将羽绒絮片脱离传送带8,而后在分离辊83的配合下,将分离网82逐层与羽绒絮片剥离,最终让羽绒絮片卷绕在卷辊81上;在分离网82与羽绒絮片分离后,分离网82通过回卷辊84牵引贴合传送带8;多层分离网82能够使羽绒絮片顺利脱离传送带8避免了相互粘接;卷辊81对冷却完成的羽绒絮片进行收卷牵引,使羽绒絮片能够脱离传送带8,并且通过分离网82使混合纤维丝不与传送带8不发生粘连情况。
63.其中,混合纤维丝包括木浆纤维和控温纤维;
64.木浆纤维采用纺前注射技术制成,纺前注射技术即木浆纤维在挤出成型时,通过小型注射器使注射器内物质熔炼混合至木浆纤维内;通过坊前注射技术向木浆纤维内添加有机酸、过氧化氢、甲基乙二醛、乳酸菌素其中一种或多种活性抗菌物质,在熔炼混合时活性抗菌能够均匀的分布在木浆纤维表面,这样能够提高木浆纤维的抗菌性和除臭性,进而保证人员在穿着时的健康情况;
65.控温纤维即聚酯纤维,采用四孔模头喷丝和物理法亲水整理方法制成;通过四孔喷头喷丝使控温纤维横截面呈四孔的圆形,这样能够提高控温纤维容纳静止空气的能力,进而提高了控温纤维的保暖性能;并且控温纤维在成型的过程中表面添加有亲水层,亲水层由亲水物质如淀粉接枝丙烯酸盐、纤维素接枝丙烯酸盐、交联聚丙烯酸盐其中一种或多种制成,这样能够提高控温纤维的亲水性能,从而提高羽绒絮片制成的服装舒适度;
66.由木浆纤维和控温纤维制成的羽绒絮片,通过木浆纤维和控温纤维表面的亲水层,使吸湿速干性能≥3级,吸湿排汗性能≥3级;并且热固化加工保证了羽绒絮片的蓬松性,进而保证了羽绒絮片的保暖性,能够使羽绒絮片的保暖性≥55%;并且纺前注射技术中添加的活性抗菌物质能够使抑菌率≥70%和醋酸降低率≥70%,并且活性抗菌物质通过熔炼混合的方法能够在水洗50次以后依然保持良好的抑菌效果,即能够使抑菌率和醋酸降低率均保持在≥40%。
67.本发明仅以上述优选的实施例进行说明,并不限制本发明,各部件结构、设置关系及其连接关系都可做相应变换,在本发明技术方案基础上,凡根据本发明原理对个别部件
进行的改进和变换,均不排除在本发明的保护范围之外。