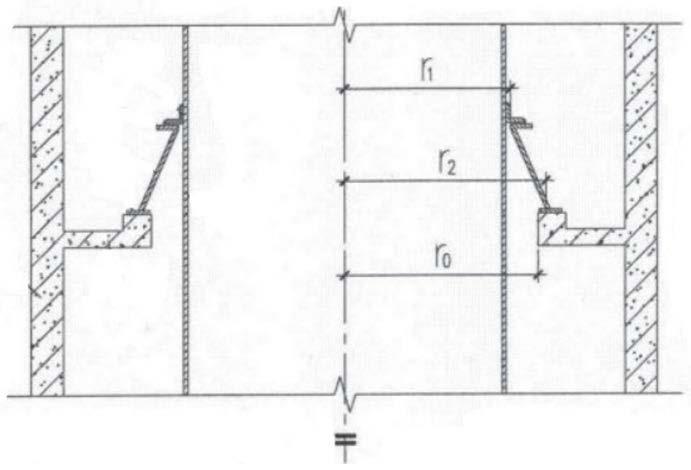
1.本实用新型属于烟囱防腐技术领域,尤其涉及一种外烟囱内部防腐的分段自立式排烟内筒。
背景技术:2.在我国能源结构中,燃烧煤炭占比高达70%以上,导致我国经济发达地区出现数个严重酸雨区,严重破坏了我们赖以生存的自然环境。为了解决这一环境问题,我国自2002年开始,在全国范围内实施燃煤电厂烟气脱硫,其中绝大多数为以石灰石——石膏法为代表的湿法烟气脱硫工艺,一般脱硫效率均可达到95%以上。由于湿法烟气脱硫工艺的增设,导致烟气排放温度由脱硫前的130℃降至45
‑
55℃,烟气中的含水率也由脱硫前的5%左右增加到脱硫后的13
‑
15%,成为含有少量二氧化硫和三氧化硫的饱和湿烟气,湿烟气中富含稀硫酸、稀盐酸等强腐蚀性物质,由此,大量的强腐蚀性脱硫烟气冷凝水在烟囱内壁产生。
3.目前,钢制烟囱的内壁通常采用在烧制的砖上进行胶或者各种胶类防腐材料的防腐涂覆,但是,由于防腐材料本身的性能局限以及施工工艺质量难以控制,这种防腐做法效果一直不理想。在这种情况下,现有烟囱已经进行过防腐处理的内壁表面,在3
‑
5年甚至更短的时间内,就会受到强腐蚀性气体的持续侵蚀而产生严重的腐蚀,为了不造成烟囱损坏,不得不重新进行新的防腐材料涂敷作业,造成锅炉停产检修维护,增加了大量直接或者间接生产成本。
4.针对上述问题,现有技术中给出了一些解决问题的方案。大体上来讲,基本都是利用原有的钢制外筒或者钢筋混凝土外筒承受风荷载、地震以及内筒自重与水平位移等作用,并采用在外筒内部再设置一个内筒专门用于排放具有高温与腐蚀作用的烟气的方案。这种方案无需拆除原有烟囱,施工技术相对成熟,内筒材质可以选择高度抗腐蚀的材料,综合改造成本远远低于重新制造新的烟囱,所以被热力发电行业所广泛采用。
5.比如中国专利cn106869573a,如图1所示,公开了一种排烟筒支承装置,按受力性质划分为以受压为主支承装置和以受拉为主支承装置,以受压为主支承装置包括正截锥壳、下环板和上环板,正截锥壳的两端分别与下环板和上环板连接;以受拉为主支承装置包括倒截锥壳和下部环形角钢牛腿,下部环形角钢牛腿设于倒截锥壳的下部,正截锥壳或倒截锥壳的小口径端与排烟内筒连接,正截锥壳或倒截锥壳的大口径端与支承平台连接。但是这种方案支承平台连接支撑元件,再由支撑元件支撑内筒侧壁,所以,整个内筒侧壁在若干个特定的点附近承受了较大的力,导致内筒的壁厚不会设计的很薄;并且需要在内筒侧壁上设置独立的支撑结构,尤其会对玻璃钢内筒的制作造成非常大的障碍,并且在安装时对支撑结构之间的定位要求也非常高,造成施工时间不期望的延长。
6.比如中国专利cn204943523u,如图2所示,公开了一种套筒烟囱,包括钢筋混凝土外筒和砖内筒,砖内筒位于钢筋混凝土外筒内,砖内筒筒壁和钢筋混凝土外筒筒壁之间设有砖内筒支撑平台,砖内筒支撑平台将砖内筒分为上砖内筒和下砖内筒,砖内筒内表面设有砖内筒防腐层,上砖内筒的砖砌体和下砖内筒的砖砌体均竖直砌筑,上砖内筒和下砖内
筒之间通过柔性防腐板连接固定。腐蚀性物质(冷凝液)不易渗入砖内筒支撑平台,防腐性能好。实际上,这种砖内筒上做防腐属于已经淘汰的工艺,首先是支撑平台的建造非常费时费力,并且由于砖墙的堆砌特点,需要在外筒整个内壁设置支撑平台,而且平台的面积不能太小,整个施工过程非常浪费时间;二是砖内筒的防腐涂覆非常困难,质量难以保证,很可能几年后又要进行二次防腐处理;三是虽然有各种方法,但是鉴于砖的材质特点,防腐密封还是不能高质量低成本的完成,因此,国内近些年对这些烟囱都在拆除后以玻璃钢或者不锈钢钛板内筒替换。
7.比如中国专利cn203626371u,如图3所示,公开了一种钢筋混凝土烟囱内衬钢制内筒的结构,其特征在于,包括多个沿竖直方向依次设置的单元钢制内筒,所述的单元钢制内筒设于烟囱混凝土外筒内,烟囱混凝土外筒内壁设有混凝土牛腿,单元钢制内筒外壁设有支撑吊耳,每个单元钢制内筒通过支撑吊耳与安装在混凝土牛腿支撑处的支撑槽钢连接固定,相邻的单元钢制内筒之间密封连接。与前面现有技术相似,这种方案支承平台连接支撑元件,再由支撑元件支撑内筒侧壁,所以,整个内筒侧壁在若干个特定的点附近承受了较大的力,导致内筒的壁厚不会设计的很薄,造成一定程度的成本上升;并且需要在内筒侧壁上设置独立的支撑结构,并且在安装时对支撑结构之间的定位要求也非常高,造成施工成本和时间不期望地延长。此外,每段内筒之间的连接方式是焊接方式,操作难度和时间都是非常不经济的。
8.比如中国专利cn108756436a,如图4所示,公开了一种内筒薄壁型自立式钢烟囱,包含薄壁不锈钢内筒和碳钢外筒,外筒和内筒由若干分段构成,内筒由若干节构成,相互连接的上节内筒的下端设有双翻边,下节内筒的上端设有外胀单翻边,双翻边与外胀单翻边相承插,并通过ω卡箍进行固定,节与节之间的内筒相连接构成单段内筒;单段内筒的外壁设有支架耳,外筒的内壁上设有支架耳沉槽组件,支架耳卡入支架耳沉槽组件中,使单段内筒与单段外筒相对固定;段与段之间连接的内筒通过其上下口承插方式对接;段与段之间连接的外筒通过法兰连接,固定于基础上,形成自立式承载。这种方案在支承平台和内筒侧壁之间使用了非常复杂的连接结构,不仅整个内筒侧壁在若干个特定的点附近承受了较大的力,而且需要在内筒侧壁上焊接独立的支撑结构,然后通过导向机构插入外筒内壁的沉槽中。结构部件较多,加工精度要求高。此外,由于所有的分段内筒都需要堆叠在一起,所以为了连接可靠,必须采用复杂的承插结构,每段内筒的各节之间,采用了复杂的卡箍结构,施工工艺和连接结构复杂,可能的失效环节多。
9.有鉴于此,市场上需要提供一种支承结构简单,施工工艺简便可靠,安全性高,时间成本和施工成本低的烟囱内筒结构。
技术实现要素:10.本实用新型所要解决的技术问题在于,如何提供一种结构简单,支撑可靠,节约施工时间和成本的排烟内筒,以及如何有效降低施工难度,提高施工安全性和效率。
11.本实用新型的技术方案是,提供一种分段自立式排烟内筒,包括单节内筒,至少两层分段支承构件,每层分段支承构件固定连接在外烟囱内壁上,分段支承构件包括水平设置的支承底板,单节内筒竖立放置于支承底板上表面,每个支承底板上放置的单节内筒组成分段内筒,分段内筒至少由一节单节内筒组成,分段内筒的高度与支承底板之间的高度
基本一致。
12.优选的,排烟内筒采用本体自膨胀式的整体结构,每一段分段内筒上至少设置有一个与单节内筒本体一体化制造的u字型膨胀节。
13.优选的,分段支承构件还包括设置于支承底板上表面的至少一块加劲板,加劲板沿单节内筒的径向竖直设置,加劲板外端面固定至外烟囱内壁上。加劲板内端面靠近单节内筒的外壁设置,并且与支承底板内端面的距离略大于单节内筒的厚度。加劲板内边缘具有一倾斜面,能够引导单节内筒内壁在放置后与支承底板内端面基本对齐。支承底板外端面固定至外烟囱内壁,支承底板内端面呈弧形,弧形半径与单节内筒的半径基本一致。
14.优选的,分段支承构件还包括设置于支承底板下表面的限位板,限位板与支承底板内边缘的距离略大于单节内筒的厚度,能够对下层分段内筒径向方向进行限位。
15.优选的,每一层分段支承构件包括环形的分段支承构件或者至少两个分离的分段支承构件。
16.优选的,单节内筒由玻璃钢缠绕工艺制成,组成分段内筒的单节内筒的数量为1
‑
6个,分段内筒顶部和上方支承底板的距离d为1
‑
10厘米。
17.优选的,单节内筒之间平口对接,分段内筒之间手糊连接层进行密封。
18.与现有技术相比,本实用新型的优点体现在:
19.1、在自立烟囱内筒领域,创造性地提出了分段自立的结构和施工方法。现有的整体自立结构,每一节单节内筒都是互相连接在一起的,有插接、卡扣、焊接等方式,所有的单节内筒实际上构成了一个整体型内筒,这样做可以提高内筒的整体性,并且施工也比较简单。但是,这种工艺由于下层单节内筒承受了上层单节内筒的重力,互相之间也要承受整体晃动产生的应力,一层层传导下来,使得在设计时不得不将部分甚至全部单节内筒的厚度增大,增加了生产的复杂性和成本。而本实用新型的分段自立式,则是反其道而行之,将这种整体性“破坏”,进而在破坏整体性的基础上,实现了整体结构的再造。本实用新型可以看成一个分段支承构件和一个分段内筒组成一个独立的内筒单元,整个内筒由若干个这种内筒单元组成,并且单元之间不会互相影响和干扰。这样,每个单元的支承构件所需要支撑的单节内筒数量就会很有限,大大的降低了支承构件要承担的重量。这种情况下,无需设计非常宽大厚实的支撑底座,只需设置一定数量的支承构件即可,而这种支承构件本身结构简单、成本低廉、施工简单。此外,每个单节内筒由于无需承担上方过多的重量,厚度可以设计的比较薄,接口也可以设计的简单甚至无需额外设计,节约了大量的时间和金钱成本。在此基础上,由于内筒整体重量的降低和支撑受力点的分散,使得在内筒施工过程中,无需再对外筒进行加固施工,节省了施工时间和成本。
20.2、本实用新型支承构件上设置了加劲板和限位板,完美地实现了利用简单结构实现有针对性的改进工艺流程适合度的目的。径向设置的加劲板在与外筒壁和支承底板垂直焊接后,极大地增强了分段支承构件的刚性和承载性,足以支撑有限数量的堆叠单节内筒。同时,加劲板以及其内端面倾斜面的设置,使得在提供强度的同时,还提供了针对单节内筒吊入安装的导向和定位功能,通过倾斜面,内筒可以简单快捷地直接沿着倾斜面滑动放置在支承构件的支承底板上,并且单节内筒的内壁边缘与支承底板的内端面可以实现一次对齐。支承结构设计便于快速安装,同时也切实地解决了安装质量控制问题,为下一步的密封工作打下了很好的基础。同时,加劲板的结构,也使得现场安装变得简单,由于加劲板通常
都要通过焊接的方式固定到外筒上,所以,径向安装的加劲板,所有的焊缝均外露可见,可以让施工人员的双手准确地找到并伸入到合适的位置完成整个焊接工作,很好地保证了焊接的质量和连接的强度。此外,安装在下方的限位板可以简单快捷地完成对下层分段内筒的定位和限位,使得每一段分段内筒稳定和减少晃动,并且即使是工艺要求提前焊接在支承底板下表面,也没有干扰到后续工序的进行,没有妨碍其他焊接工作的完成。
21.3、本实用新型摒弃了传统内筒的侧面支撑方式,让内筒重新回归受力状态比较完美的底部支撑,并且由于重量大大减轻,每一段分段内筒的受力状况得到很大改善,内部应力均匀地分散到整个内筒,使得内筒不再容易出现局部变形的问题。此外,由于内筒侧壁无需再设置连接结构和固定结构,使得内筒的加工更加简单,出现缺陷的可能性大幅降低,尤其是在使用玻璃钢作为内筒材质时,单节内筒可以一次性整体缠绕成型,不会再被一些多余的部件和结构破坏整体性,带来了更好的密封性能和防腐性能。
22.4、本实用新型的内筒优选采用玻璃钢材料,具有良好的耐酸、耐腐蚀和阻燃的性能。内筒整体在生产车间缠绕,一次性一体成型,质量可靠,密封和防腐性能优秀。玻璃钢材料重量轻强度高,在有限个单节内筒对接时,无需考虑过多的强度问题,仅需平口对接即可,内筒之间的对接缝容易处理,并且处理后密封性和一体性非常好。
23.5、由于采用分段自立方式,分段内筒之间没有直接连接,互不影响,无需在分段内筒之间设置辅助加强部件,比如卡箍等,简化了整体结构,节约了施工时间。在分段内筒之间进行密封时,采用了玻璃钢手糊的密封方式。由于采用同一种材料进行手糊涂覆,材料之间融合性好,密封性能保持一致,实现了分段内筒之间的“软性”连接,稳定性好,即使出现内筒晃动或者其他不良状况,也同样不容易开裂和变形,完全能够满足密封和连接的要求。
24.6、对电力生产厂家来讲,在追求成本平衡的情况下,无需对原有的烟囱进行大规模拆除或者改造,仅需在内部按照本实用新型的施工方法和内筒结构新建一个防腐内筒即可,特别是在外筒为钢制时,特别适合对原有烟囱进行低成本改造,由于分段支承构件在支撑内筒的同时,可以完成对内筒的定位和止晃功能,无需增加额外的稳定构件,利用一个部件实现了支撑、引导、定位和止晃几个作用,极大地简化了结构,降低了改造成本。顶部吊装的施工方式不需破坏原有烟囱结构,施工工艺简单,基本上只有焊接吊装和涂覆,操作步骤重复性高,没有技术难点。经测算总工期一般可以减少百分之四十,随之带来烟囱停止工作时间的大幅减少,比全程自立的玻璃钢结构,可以节省投资百分之三十以上。
25.7、本实用新型优选每一段分段内套筒上至少设置有一个与单节内套筒本体加工过程中一体化制造的u字型膨胀节。采用的本体自膨胀的方式消除一些外界因素,比如热胀冷缩等。无需设置额外的对抗热胀冷缩的结构,简化了整体结构,并且由于不产生与独立膨胀节之间的结构连接面和连接点,从而获得了更加可靠的整体内套筒结构,有效避免了附属膨胀节在投入使用3
‑
5年就会产生渗漏事件的发生。
附图说明
26.图1是现有技术中烟囱内筒支撑结构示意图;
27.图2是现有技术中烟囱内筒支撑结构示意图;
28.图3是现有技术中烟囱内筒支撑结构示意图;
29.图4是现有技术中烟囱内筒支撑结构示意图;
30.图5是本实用新型排烟内筒一个实施例a
‑
a剖面结构示意图;
31.图6是本实用新型排烟内筒一个实施例俯视结构示意图;
32.图7是本实用新型排烟内筒加劲板b
‑
b剖面结构示意图;
33.图8是本实用新型排烟内筒加劲板结构俯视示意图。
具体实施方式
34.下面对本实用新型的实施例作详细说明,下述实施例在以本实用新型技术方案为前提下进行实施,给出了详细的实施方式和具体的操作过程,但本实用新型的保护范围不限于下述的实施例。
35.参考图5,本实用新型涉及烟囱分段自立式防腐内筒领域,提供一种分段自立式排烟内筒,包括单节内筒1,至少两层分段支承构件2,每层分段支承构件2固定连接在外烟囱3内壁上,分段支承构件2包括水平设置的支承底板4,单节内筒1竖立放置于支承底板4上表面,每个支承底板4上放置的单节内筒1组成分段内筒5,分段内筒5至少由一节单节内筒1组成,分段内筒5的高度与支承底板4之间的高度基本一致。
36.分段支承构件2可以通过合适的方式固定至烟囱内筒3的内壁上,并借助坚固的烟囱内筒实现对分节内筒的支撑。通常,在内筒3是钢制的情况下,分段支承构件2直接水平焊接至内筒即可,如果内筒是其他材质,比如钢筋混凝土,则需要针对具体情况进行适合的设计,以保证分段支承构件2可以稳固地固定在内筒上。分段自立式内筒的核心,就在于把一整根内筒逐级的打断,然后各自支撑。所以,确定每节单节内筒1的长度以及每段分段内筒5的长度就非常重要。理论上,每层分段支承构件2可以仅支撑一节单节内筒,但是,由于单节内筒1的制作要遵循一定的工艺和设备条件,所以不太可能制作的太长,这就带来了一个问题,如果是一个120
‑
170米的普通烟囱,可能需要十几甚至二十多层的分段支承构件2,这明显是不经济的。根据现有实践的经验,从强度、制作便利性和成本经济性等几个方面考虑,6米左右的玻璃钢单节内筒1综合性能最好,3节单节内筒1组成一段18米左右的分段内筒5各方面指标比较均衡,可以很好地实现分段自立式的各种优点。这也就意味着,每隔18米左右会设置一层分段支承构件2,然后每层构件上放置一段长度18米左右的分段内筒5会是比较合理的选择。这里面的本体膨胀,是指在分段自立的形式下,玻璃钢内筒可以通过自身本体上加工的形状结构的膨胀变形消除热胀冷缩带来的影响。这里面提到的高度基本一致,实际上想表达的是两层支承底板4之间的距离,基本上会被几节堆叠在一起的单段内筒5所填满,底板之间的距离实际上是与单节内筒1的堆叠数量直接相关的。但是,因为工艺要求,多少都会存在一定的空隙,所以采用基本一致的说法。
37.每一层分段支承构件2包括环形的分段支承构件2或者至少两个分离的分段支承构件2。
38.理论上来讲,当每层分段支承构件2的数量在两个以上时,就能起到稳定支撑分段内筒5的作用,但是,由于支点较少,会导致为了安全性而不得不增大每个分段支承构件2的尺寸和厚度,所以,我们通常是根据单节内筒1的直径和长度,计算其产生的重力以和其他应力及膨胀,再与我们的标准分段支承构件2进行匹配,调整分段支承构件2的数量、尺寸,这样,每个分段支承构件2承受的重力就比较有限,并且分布的位置可以分散应力并增加稳定性,基本避免了在极端条件下分段内筒5出现安全问题。此外,在比较特殊的情况下,分段
支承构件2也可以整体上是一个环形构件,也就是沿着外筒内壁周向一圈都固定有分段支承构件2,这种方式安全性非常好,对分段内筒5的底边缘保护的非常到位,内筒稳定性也很好。但是,这种结构施工工艺变得复杂,用料和施工时间也相应增加,所以只是特殊情况下才使用。按照我们的计算,分段支承构件2数量在2
‑
50个之间已经可以满足各种不同工艺。
39.优选的,分段支承构件2还包括设置于支承底板4上表面的至少一块加劲板6。加劲板6沿单节内筒1的径向竖直设置,加劲板外端面13固定至烟囱内筒3内壁上。实践中,我们通常设置两块以上的加劲板6,这样,可以在竖直方向上很好地分散分段支承构件2的支承底板4外端面焊缝的受力,改变受力的方向,增加受力的面积,减少力矩,有效地增加了分段支承构件2的稳定性和承载性。
40.参考图7,加劲板内端面8靠近单节内筒1的外壁设置,并且与支承底板内端面9的距离略大于单节内筒1的厚度。加劲板6内边缘具有一倾斜面10,与加劲板内端面8相连,能够引导单节内筒1内壁在放置后与支承底板内端面9基本对齐。加劲板6除了增加分段支承构件2的刚性和抗弯强度外,还同时起到了引导单节内筒1进入指定位置的作用。由于加劲板内端面8与支承底板内端面9的距离略大于单节内筒1的厚度,同时支承底板4的内圆弧端面的半径与单节内筒1内壁的半径基本一致,所以,当单节内筒1沿着倾斜面10滑入到加劲板内端面8后,正好稳定放置在加劲板内端面8内侧。在完成引导作用后,加劲板内端面8又可以起到径向定位分段内筒5下端部的作用。
41.支承底板外端面11固定至烟囱内筒3内壁上,支承底板内端面9呈弧形,弧形半径与单节内筒1的半径基本一致。如图8所示,支承底板4大体上呈截面扇形,水平放置,外端面11一般直接焊接至外筒内壁,由于施工条件的限制,通常是先将限位板7焊接在构件下表面,然后再进行下一步焊接。由于施工工艺要求,支承底板4的内端面要与分段内筒5的内壁表面基本对齐,这样才能保证在进行密封涂覆后,不会在密封层内存在凸出的物体,不会影响密封层的性能,不会造成断裂和开口。
42.分段支承构件2还包括设置于支承底板4下表面的限位板7,限位板7与支承底板4内边缘的距离略大于单节内筒1的厚度,能够对下层分段内筒5径向方向进行限位。一般的自立式内筒,由于高度非常高,并且互相之间连接比较紧密,所以不可能避免的会带来稳定性的问题,解决的办法通常是增加独立的止晃机构。而本发明采用结构简单成本低廉的定位构件,只需要在分段支承构件2上下表面各焊接上一小段钢板,就能够与施工方法完美配合,利用一个部件同时实现四重作用,简化了工艺节约了成本。并且在下层分段内筒5下端已经通过加劲板内端面8进行定位后,限位板7可以非常容易地插入分段内筒5的外周实现上端的定位,进而完成准确的整体定位。
43.分段内筒5顶部和上方支承底板4的距离为1
‑
10厘米,优选2
‑
5厘米。我们在分段内筒5的顶部与支承底板的下表面之间,预留了几个厘米的工艺空隙,主要用来在焊接支承底板4和加劲板6时插入接渣板,以免焊接引起的火花和焊渣影响到内外筒的其他部分,既环保又安全。此外,还可以缓解热胀冷缩带来的部分影响。
44.优选的,每一段分段内筒5上至少设置有一个与单节内筒1本体加工过程中一体化制造的u字型膨胀节14。膨胀节14呈弧形,向外凸出于单节内筒1。由于内筒工作在温度较高的环境,不工作时温度又比较低,所以不可避免地会出现热胀冷缩现象。传统的分段自立式内筒,通常会在筒体上设置一些柔性膨胀节,以抵消热胀冷缩带来的影响。而本发明由于把
整个内筒已经切分为若干个独立的部分,所以可以引入新的方法来对抗热胀冷缩,也就是仅在每个分段内筒5内设置一个膨胀节14,比如一层分段内筒5包括三节单节内筒1,我们通常也仅在最上面一节单节内筒上设置一个膨胀节14,其他两节依然保持原始结构和形状不变,采用这种方式,依然可以取得非常理想地应对热胀冷缩的效果。这种本体自膨胀式膨胀节,结构简单整体性强,最重要的是材质和内筒筒体的材质完全一样,热膨胀系数的一致性和受力均匀程度及防腐性能均比一般柔性膨胀节好。此外,由于膨胀结构件是和部分单节内筒一体成型制作的,施工工艺与其他单节内筒1并无区别,所以对整个施工流程没有造成任何额外负担。
45.单节内筒1由玻璃钢或者钢复合材料制成,组成分段内筒5的单节内筒1的数量为1
‑
6个。单节内筒1之间平口或插口对接,分段内筒5之间手糊连接层12进行密封。由于单节内筒1的数量较少,互相之间的堆叠并没有对各个部件之间的受力状况产生巨大的变化,并且由于已经经过加劲板内端面8的定位,所以第二节单节内筒1可以比较容易地实现与第一节内筒的对接,因此,我们在施工中可以充分利用这种优势,直接进行单节内筒1之间的平口对接,这样,每个单节内筒的结构会变得相对简单,对接也变得比较容易,如果只堆叠三个单节内筒1,最下面的内筒基本不会产生太多的竖直方向形变,平口对接就可以满足安全和工艺要求;当工艺要求较高时,也可以采用插口对接的方式。根据本发明的内筒结构,在每个分段内筒5之间,实际上是存在一个支承底板4的厚度加一个工艺空隙d的间隙,而这里是必须要被密封的,否则将会造成防腐效果的大幅降低。我们通常采用玻璃钢材料作为密封材料,这样,可以用与上下内筒相同的材质及铺层设计完成密封,粘结性能和密封性能均非常好,内筒的使用寿命也能得到提升。通常通过手糊工艺将上下相邻的玻璃钢筒体接口部位粘结连接层,比如将浸润树脂粘结剂的玻璃纤维逐层铺敷,每层铺敷厚度不大于5mm,以免导致局部放热温度过高,影响产品质量,待糊制到要求厚度后,测量巴氏硬度达到30以上,进行下一个接口粘结工作。
46.本实用新型的分段自立式内筒通过以下方法施工安装,包括如下步骤:(a)固定安装最下层分段支承构件2;支撑件可以选用普通烟囱的支撑构件,但优选还是选用本发明设计的分段支承构件2,最下层的可以不焊接限位板7。这样标准统一,施工难度也相对较低,可以一直重复相同的施工步骤,节约大量的时间和成本。(b)将第一节单节内套筒1从烟囱顶部吊入,固定安装至下层分段支承构件2;由于有倾斜面10的导向,单节内套筒会顺利地进入预定位置,通常接缝的地方需要打胶进行密封,基本属于常规操作。(c)将组成第一段分段内套筒5的其他单节内套筒1依次向上叠加在第一节单节内套筒1上;目前看,我们一般是将三层单节内套筒1作为一段分段内套筒5,以保证施工效率、安全性和经济性。堆放过程中,由于下层单节内套筒1准确地定位在加劲板的内端面内侧,所以放置过程中都会受到该内端面的限制,而不会发生大的移动和晃动,有利于顺序堆叠。依靠重力放稳后,使用粘结材料密封接缝。当然,如果分段内套筒5只包括一节单节内套筒1,则无需重复此步骤。(d)将上一层分段支承构件2固定安装至烟囱内筒3的内壁上;此过程中,要注意支承底板4不能紧贴下层分段内套筒,要留下一定的距离作为热胀冷缩的空隙,还要注意限位板7的位置,要将内套筒在径向上定位。(e)依次重复重复步骤(b)、(c)和(d),直到完成整个烟囱高度上的单节内套筒1和分段内套筒5的组装。在组装完成后,还需要对每层分段内套筒5之间的空隙进行封闭,此时注意不能封闭分段内套筒和支承底板之间的空隙。步骤(a)和(d)中,还包括
将分段支承构件2焊接至烟囱钢内筒3上的操作。
47.以上所述仅为本实用新型的较佳实施例而已,并不用以限制本实用新型,凡在本实用新型的精神和原则之内所作的任何修改、等同替换和改进等,均应包含在本实用新型的保护范围之内。