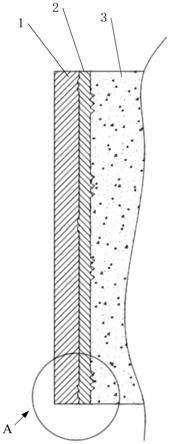
1.本发明涉及新型建筑材料领域,尤其涉及一种钢管束及生产方法。
背景技术:2.钢结构是由钢制材料组成的结构,是主要的建筑结构类型之一。结构主要由型钢和钢板等制成的钢梁、钢柱、钢桁架等构件组成,并采用硅烷化、纯锰磷化、水洗烘干、镀锌等除锈防锈工艺。各构件或部件之间通常采用焊缝、螺栓或铆钉连接。因其自重较轻,且施工简便,广泛应用于大型厂房、场馆、高层或超高层建筑等领域。钢管束是钢结构的一种,通过在钢管束浇筑混凝土,形成剪力墙的组成单元。自密实混凝土(self compacting concrete或self
‑
consolidating concrete,简称scc)是指在自身重力作用下,能够流动、密实,即使存在致密钢筋也能完全填充模板,同时获得很好均质性,并且不需要附加振动的混凝土,非常适合钢管束的浇筑填充。然而,自密实混凝土在硬化后的耐久性非常有限,尤其是在寒冷气候条件下;同时,自密实混凝土中还有不稳定的气泡,高流动自密实性混凝土与普通混凝相比,干燥收缩略大,容易与钢管束的表面脱离。因此,现在钢管束的浇筑填充自密实混凝土所得到的剪力墙的组成单元,存在质量不高的问题。
技术实现要素:3.本发明实施例提供一种钢管束,能够将钢管束的钢管主板与金属保温层进行复合,通过金属保温层对硬化后的自密实混凝土进行一定程度的保温,增加自密实混凝土在寒冷条件的耐久性,同时,通过金属保温层内表面设置的第二多面体凸起,对硬化后的自密实混凝土进行位置限定,增加钢管束的表面对硬化后的自密实混凝土的束缚力,从而钢管束与硬化后的自密实混凝土的结合稳定性,进而提高剪力墙的组成单元的质量,最终提高剪力墙的质量。
4.第一方面,本发明实施例提供一种钢管束,包括钢管主板以及金属保温层,所述钢管主板根据所述钢管束的形状围成对应的钢管束主体,所述金属保温层设置在所述钢管束主体的表面,并与所述钢管主板进行复合;
5.所述金属保温层的外表面设置有第一多面体凸起,所述金属保温层的内表面设置有第二多面体凸起,所述钢管主板的内表面设置有与所述第一多面体相配合的多面体凹坑,所述钢管主板的外表面为所述钢管束的外表面,所述钢管主板的内表面与所述金属保温层的外表面为复合连接;
6.所述第二多面体凸起具有表面粗糙度,其中,所述表面粗糙度根据自密实混凝土的状态参数进行确定,所述自密实混凝土用于浇筑所述钢管束以形成剪力墙的组成单元。
7.可选的,所述金属保温层的外表面包括第一复合区以及第二复合区,所述第一多面体凸起设置在所述第一复合区;
8.所述钢管主板的内表面包括第三复合区以及第四复合区,所述与所述第一多面体相配合的多面体凹坑设置在所述第三复合区;
9.所述第二复合区与所述第四复合区通过焊接进行复合,所述第一复合区与所述第三复合区通过冲击进行复合。
10.可选的,所述第一复合区与所述第二复合区的面积比例根据所述剪力墙的设计高度成正相关,所述第一复合区的形状、位置和数量根据所述剪力墙的组合形状相关。
11.可选的,所述金属保温层的内表面包括第一凸起区与第二凸起区,所述第二多面体凸起设置在所述第一凸起区与所述第二凸起区中,其中,在同一平面上,两个所述第二凸起区间隔设置,多个所述第一凸起区设置在两个所述第二凸起区之间。
12.可选的,所述第一多面体凸起为锥形多面体,所述锥形多面体的凸起高度根据所述剪力墙的组成单元的受力情况进行确定。
13.第二方面,提供一种钢管束的生产方法,所述钢管束的生产方法的步骤包括:
14.将第一型材预制成钢管主板以及将第二型材预制成金属保温层;
15.根据所述钢管束所用于的剪力墙的施工参数,对所述金属保温层的外表面进行第一多面体凸起加工,以及对所述金属保温层的内表面进行第二多面体凸起加工;
16.根据自密实混凝土的状态参数对所述第二多面体凸起进行表面加工,以使所述第二多面体凸起具有表面粗糙度,其中,所述自密实混凝土用于浇筑所述钢管束以形成剪力墙的组成单元;
17.根据所述第一多面体凸起对所述钢管主板的内表面进行多面体凹坑的加工,以使所述钢管主板的内表面与所述金属保温层的外表面相配合;
18.对所述钢管主板的内表面以及所述金属保温层的外表面进行复合,得到钢管束。
19.可选的,所述金属保温层的内表面包括第一凸起区与第二凸起区,所述第二多面体凸起设置在所述第一凸起区与所述第二凸起区中,其中,在同一平面上,两个所述第二凸起区间隔设置,多个所述第一凸起区设置在两个所述第二凸起区之间,所述根据所述钢管束所用于的剪力墙的施工参数,对所述金属保温层的内表面进行第二多面体凸起加工的步骤包括:
20.计算不同建筑高度下,所述剪力墙所需要的施工参数;
21.根据所述剪力墙所需要的施工参数,确定所述第一凸起区的形状、位置和数量。
22.可选的,所述金属保温层的外表面包括第一复合区以及第二复合区,所述第一多面体凸起设置在所述第一复合区;所述钢管主板的内表面包括第三复合区以及第四复合区,所述与所述第一多面体相配合的多面体凹坑设置在所述第三复合区;所述剪力墙的施工参数包括剪力墙的组合形状以及剪力墙的设计高度,所述根据所述钢管束所用于的剪力墙的施工参数,对所述金属保温层的外表面进行第一多面体凸起加工的步骤包括:
23.根据所述剪力墙的组合形状,确定所述第一复合区的形状、位置和数量;
24.根据所述剪力墙的设计高度,确定所述第一复合区与所述第二复合区的面积比例;
25.根据所述第一复合区的形状、位置和数量、所述第一复合区与所述第二复合区的面积比例,对所述金属保温层的外表面进行第一多面体凸起加工。
26.可选的,所述对所述金属保温层的内表面以及所述金属保温层的外表面进行复合,得到钢管束的步骤包括:
27.将所述钢管主板与所述金属保温层进行对齐;
28.将所述第二复合区与所述第四复合区通过焊接进行复合;
29.将所述第一复合区与所述第三复合区通过冲击进行复合,得到钢管束。
30.可选的,所述剪力墙的施工参数包括剪力墙的组成单元的受力情况,所述第一多面体凸起为锥形多面体,所述方法还包括:
31.根据所述剪力墙的组成单元的受力情况进行确定所述锥形多面体的凸起高度。
32.本发明实施例中,钢管束包括钢管主板以及金属保温层,所述钢管主板根据所述钢管束的形状围成对应的钢管束主体,所述金属保温层设置在所述钢管束主体的表面,并与所述钢管主板进行复合:所述金属保温层的外表面设置有第一多面体凸起,所述金属保温层的内表面设置有第二多面体凸起,所述钢管主板的内表面设置有与所述第一多面体相配合的多面体凹坑,所述钢管主板的外表面为所述钢管束的外表面,所述钢管主板的内表面与所述金属保温层的外表面为复合连接;所述第二多面体凸起具有表面粗糙度,其中,所述表面粗糙度根据自密实混凝土的状态参数进行确定,所述自密实混凝土用于浇筑所述钢管束以形成剪力墙的组成单元。本发明能够将钢管束的钢管主板与金属保温层进行复合,通过金属保温层对硬化后的自密实混凝土进行一定程度的保温,增加自密实混凝土在寒冷条件的耐久性,同时,通过金属保温层内表面设置的第二多面体凸起,对硬化后的自密实混凝土进行位置限定,增加钢管束的表面对硬化后的自密实混凝土的束缚力,从而钢管束与硬化后的自密实混凝土的结合稳定性,进而提高剪力墙的组成单元的质量,最终提高剪力墙的质量。
附图说明
33.为了更清楚地说明本发明实施例或现有技术中的技术方案,下面将对实施例或现有技术描述中所需要使用的附图作简单地介绍,显而易见地,下面描述中的附图仅仅是本发明的一些实施例,对于本领域普通技术人员来讲,在不付出创造性劳动的前提下,还可以根据这些附图获得其他的附图。
34.图1是本发明实施例提供的一种钢管束的结构示意图;
35.图2是本发明实施例提供的图1中a处的局部示意图;
36.图3是本发明实施例提供的另一种钢管束的结构示意图;
37.图4本发明实施例提供的提供一种钢管束的生产方法的流程图。
38.其中,1、钢管主板;11、多面体凹坑;2、金属保温层;21、第一多面体凸起;22、第二多面体凸起;221、第一凸起区;222、第二凸起区。
具体实施方式
39.下面将结合本发明实施例中的附图,对本发明实施例中的技术方案进行清楚、完整地描述,显然,所描述的实施例仅是本发明一部分实施例,而不是全部的实施例。基于本发明中的实施例,本领域普通技术人员在没有作出创造性劳动前提下所获得的所有其他实施例,都属于本发明保护的范围。
40.在本发明中,提出一种钢管束,本发明能够将钢管束的钢管主板与金属保温层进行复合,通过金属保温层对硬化后的自密实混凝土进行一定程度的保温,增加自密实混凝土在寒冷条件的耐久性,同时,通过金属保温层内表面设置的第二多面体凸起,对硬化后的
自密实混凝土进行位置限定,增加钢管束的表面对硬化后的自密实混凝土的束缚力,从而钢管束与硬化后的自密实混凝土的结合稳定性,进而提高剪力墙的组成单元的质量,最终提高剪力墙的质量。
41.请参见图1和图2,图1是本发明实施例提供的一种钢管束的结构示意图,图2是本发明实施例提供的图1中a处的局部示意图,如图1和图2所示,钢管束包括包括钢管主板1以及金属保温层22,上述钢管主板1根据上述钢管束的形状围成对应的钢管束主体,上述金属保温层2设置在上述钢管束主体的表面,并与上述钢管主板1进行复合。
42.上述金属保温层2的外表面设置有第一多面体凸起21,上述金属保温层2的内表面设置有第二多面体凸起22,上述钢管主板1的内表面设置有与上述第一多面体相配合的多面体凹坑11,上述钢管主板1的外表面为上述钢管束的外表面,上述钢管主板1的内表面与上述金属保温层2的外表面为复合连接。
43.上述第二多面体凸起22具有表面粗糙度,其中,上述表面粗糙度根据自密实混凝土的状态参数进行确定,上述自密实混凝土用于浇筑上述钢管束以形成剪力墙的组成单元。
44.在本发明实施例中,上述金属保温层2可以是两金属板材之间复合一层保温材料的复合金属板,上述金属保温层2包括第一金属板材与第二金属板材,第一金属板材与钢管主板1复合,上述第一金属板材、第二金属板材与钢管主板1所用金属材料相同。上述保温材料可以是硬质高密度聚氨酯发泡材料。
45.在一种可能的实施例中,为简化加工工艺,上述第二多面体凸起22可以是三面体凸起、四面体凸起、五面体凸起以及六面体凸起。当然,本发明实施例中第二多面体凸起22并不限定为上述的三面体凸起、四面体凸起、五面体凸起以及六面体凸起,在工艺技术提升,使得工艺成本下降的情况下,也可以考虑更面数更多的凸起作为第二多面体。
46.上述第一多面体凸起21的高于设置平面的高度为固定值,上述多面体凹坑11与第一多面体凸起21为配合结构,即第一多面体为三面体凸起时,则多面体凹坑11为三面体凹坑,第一多面体为四面体凸起时,则多面体凹坑11为四面体凹坑,第一多面体为五面体凸起时,则多面体凹坑11为五面体凹坑,第一多面体为六面体凸起时,则多面体凹坑11为六面体凹坑。
47.上述第二多面体凸起22具有表面粗糙度,是为了增加与自密实混凝土的接触面积,进一步增加钢管束对于自密实混凝土的束缚效果。上述表面粗糙度与自密实混凝土的状态参数进行确定。
48.具体的,自密实混凝土的状态参数包括外加剂掺量、砂率、扩展度、拌合物状态、拌合时间,具体的,可以通过下述式子对第二多面体凸起22的表面粗糙度进行确定:
[0049][0050][0051]
在上述式子中,r为第二多面体凸起22的表面粗糙度,ra为硬化后自密实混凝土的粗糙度,b为外加剂掺量,c为砂率,d为扩展度,e为拌合时间,s
i
为拌合物状态的状态值,本发明实施例中,拌合物状态的状态值s
i
可以取0.7、0.8、0.9、1.0、1.1、1.2、1.3总共7个值,
上述n为状态值的数量,n=7。上述y
j
为硬化后自密实混凝土表面轮廓线上到表面轮廓中线之间的距离,m为表面轮廓线上的采样点数量。需要说明的是,由于外加剂的加入,使得自密实混凝土的干燥收缩能力增加,因此,随着外加剂掺量的增加,第二多面体凸起22的表面粗糙度需要更高的,才能增加钢管束对于硬化后自密实混凝土的束缚效果。上述状态值s
i
为0.7时,拌合物状态为流动性好,各项指标正常,排气孔出浆时有较多水泥浆;上述状态值s
i
为0.8时,拌合物状态为稍干,各项指标正常,排气孔出浆时带碎石;上述状态值s
i
为0.9时,各项指标正常,排气孔出浆时有较多浮浆;上述状态值s
i
为1.0时,各项指标正常,排气孔出浆时有中量浮浆;上述状态值s
i
为1.1时,各项指标正常,排气孔出浆时有较少浮浆;上述状态值s
i
为1.2时,各项指标正常,排气孔出浆时有较少浮浆,碎石处于悬浮状态;上述状态值s
i
为1.3时,各项指标正常,排气孔出浆时为碎石,碎石处于悬浮状态。
[0052]
在本发明实施例中,能够将钢管束的钢管主板1与金属保温层2进行复合,通过金属保温层2对硬化后的自密实混凝土进行一定程度的保温,增加自密实混凝土在寒冷条件的耐久性,同时,通过金属保温层2内表面设置的第二多面体凸起22,对硬化后的自密实混凝土进行位置限定,增加钢管束的表面对硬化后的自密实混凝土的束缚力,从而提高钢管束与硬化后的自密实混凝土的结合稳定性,进而提高剪力墙的组成单元的质量,最终提高剪力墙的质量。
[0053]
可选的,上述金属保温层2的外表面包括第一复合区以及第二复合区,上述第一多面体凸起21设置在上述第一复合区;上述钢管主板1的内表面包括第三复合区以及第四复合区,上述与上述第一多面体相配合的多面体凹坑11设置在上述第三复合区;上述第二复合区与上述第四复合区通过焊接进行复合,上述第一复合区与上述第三复合区通过冲击进行复合。
[0054]
在本发明实施例中,上述金属保温层2的外表面与钢管主板1的内表面要进行复合,从而增加钢管束的强度。需要说明的是,本发明实施例不是在钢管主板1之中增加保温材料层,而是采用复合的方式增加金属保温层2,使得钢管主板1的强度增加。
[0055]
在一种可能的实施例中,上述金属保温层2的厚度不超过钢管主板1的厚度,优选的,上述金属保温层2的厚度为钢管主板1的厚度的1/2。
[0056]
需要说明的是,上述第二复合区与上述第四复合区为喷丸抛光面,可以通过焊接进行复合,上述第一复合区与上述第三复合区为配合的凹凸面,可以通过冲击进行复合,上述冲击复合可以采用爆炸法进行复合,采用爆炸法进行复合还可以提升材料性能。
[0057]
可选的,上述第一复合区与上述第二复合区的面积比例根据上述剪力墙的设计高度成正相关,上述第一复合区的形状、位置和数量根据上述剪力墙的组合形状相关。
[0058]
在本发明实施例中,上述第一复合区与上述第二复合区的面积比例随着剪力墙的设计高度的增加而增加。可以理解的是,在金属保温层2的面积不变的情况下,随着剪力墙的设计高度的增加,第一复合区的面积在变大。具体的,第一复合区与上述第二复合区的面积比例可以通过下述式子进行表示:
[0059][0060]
其中,上述式子中,r
1k
为第一复合区的面积,r
2k
为第二复合区的面积,h为建筑总设计高度,h
k
为当前钢管束所用于的高度。
[0061]
在本发明实施例中,上述剪力墙的组合形状可以是c型、一字型、z字型、t字型、十字型或l型,上述剪力墙的组合形状是由钢管束作为组合单元进行组合而成的,具体可以通过焊接、法兰连接等连接方式进行组合。
[0062]
具体的,当剪力墙的组合形状可以是c型时,第一复合区的形状可以是四边形,第一复合区的位置可以在两端与中间,数量为3;当剪力墙的组合形状可以是一字型时,第一复合区的形状可以是四边形,第一复合区的位置可以在两端,数量为2;当剪力墙的组合形状可以是z字型时,第一复合区的形状可以是多边形或半圆形,第一复合区的位置可以在两端和中间,数量为4(两端各一个第一复合区,中间两个复合区);当剪力墙的组合形状可以是t字型时,第一复合区的形状可以是多边形或半圆形,第一复合区的位置可以在两端和中间,数量为4(两端各一个第一复合区,中间两个复合区);当剪力墙的组合形状可以是十字型时,第一复合区的形状在交叉处的钢管束中可以是多边形或半圆形,第一复合区的位置可以在两端和中间,数量为4(两端各一个第一复合区,中间两个复合区),在非交叉处的钢管束中可以是四边形,第一复合区的位置可以在两端和中间,数量为3;当剪力墙的组合形状可以是l型时,第一复合区的形状可以是多边形或半圆形,第一复合区的位置可以在两端和中间,数量为3。
[0063]
可选的,上述金属保温层2的内表面包括第一凸起区221与第一凸起区222,上述第二多面体凸起22设置在上述第一凸起区221与上述第一凸起区222中,其中,在同一平面上,两个上述第一凸起区222间隔设置,多个上述第一凸起区221设置在两个上述第一凸起区222之间。
[0064]
具体的,在本发明实施例中,上述第一凸起区222可以设置为条状凸起区,该第一凸起区222的条状凸起区沿上述钢管束的转角边缘设置,上述第一凸起区221可以设置为条状凸起区,第一凸起区221的条状凸起区与第一凸起区222的条状凸起区垂直设置,以钢管束为纵向设置,钢管束的转角线也为纵向,则第一凸起区222的条状凸起区的方向也为纵向,而第一凸起区221的条状凸起区则为横向设置,如图3所示。上述第一凸起区221也可以设置为块状凸起区,第一凸起区221的块状凸起区设置在第一凸起区222的条状凸起区之间。
[0065]
可选的,上述第一多面体凸起21为锥形多面体,上述锥形多面体的凸起高度根据上述剪力墙的组成单元的受力情况进行确定。
[0066]
在本发明实施例中,剪力墙的组成单元的受力情况随着安装高度的增加而增大,因此,锥形多面体的凸起高度根据剪力墙的安装高度的增加而增加。
[0067]
上述锥形多面体可以是多面体各个面的顶端汇集成一个点,也可以是多面体各个面的顶端汇集在一个与底端截面平行的面上,上述与底端截面平行的面的面积小于底端的截面面积。
[0068]
本发明实施例中,钢管束包括钢管主板以及金属保温层,所述钢管主板根据所述钢管束的形状围成对应的钢管束主体,所述金属保温层设置在所述钢管束主体的表面,并与所述钢管主板进行复合:所述金属保温层的外表面设置有第一多面体凸起,所述金属保温层的内表面设置有第二多面体凸起,所述钢管主板的内表面设置有与所述第一多面体相配合的多面体凹坑,所述钢管主板的外表面为所述钢管束的外表面,所述钢管主板的内表面与所述金属保温层的外表面为复合连接;所述第二多面体凸起具有表面粗糙度,其中,所
述表面粗糙度根据自密实混凝土的状态参数进行确定,所述自密实混凝土用于浇筑所述钢管束以形成剪力墙的组成单元。本发明能够将钢管束的钢管主板与金属保温层进行复合,通过金属保温层对硬化后的自密实混凝土进行一定程度的保温,增加自密实混凝土在寒冷条件的耐久性,同时,通过金属保温层内表面设置的第二多面体凸起,对硬化后的自密实混凝土进行位置限定,增加钢管束的表面对硬化后的自密实混凝土的束缚力,从而提高钢管束与硬化后的自密实混凝土的结合稳定性,进而提高剪力墙的组成单元的质量,最终提高剪力墙的质量。
[0069]
可选的,请参见图4,图4本发明实施例提供的提供一种钢管束的生产方法的流程图,如图4所示,所述钢管束的生产方法的步骤包括:
[0070]
s1、将第一型材预制成钢管主板以及将第二型材预制成金属保温层。
[0071]
在本发明实施例中,可以将第一型材预制成钢管主板的u型件和i型件,将u型件和i型件进行组装,刚可以得到钢管束的口型钢。同样的,可以将第二型材预制成金属保温层预制成金属保温层的u型件与i型件。
[0072]
在一种可能的实施例中,可以先将多个u型件进行焊接,在钢管主板与金属保温层复合后,再将复合后i型件焊接到在复合后u型件的开口上,得到钢管束组合结构。
[0073]
s2、根据钢管束所用于的剪力墙的施工参数,对金属保温层的外表面进行第一多面体凸起加工,以及对金属保温层的内表面进行第二多面体凸起加工。
[0074]
在本发明实施例中,上述剪力墙的施工参数根据建筑的高度以及剪力墙的组合形状等进行确定,具体的,可以根据剪力墙的组合形状对上述金属保温层的外表面进行第一多面体凸起加工。以及可以通过建筑的高度以及剪力墙的高度对金属保温层的内表面进行第二多面体凸起加工。
[0075]
其中,上述剪力墙的组合形状可以是c型、一字型、z字型、t字型、十字型或l型,上述剪力墙的组合形状是由钢管束作为组合单元进行组合而成的,具体可以通过焊接、法兰连接等连接方式进行组合。
[0076]
s3、根据自密实混凝土的状态参数对第二多面体凸起进行表面加工,以使第二多面体凸起具有表面粗糙度。
[0077]
其中,所述自密实混凝土用于浇筑所述钢管束以形成剪力墙的组成单元。上述第二多面体凸起具有表面粗糙度,是为了增加与自密实混凝土的接触面积,进一步增加钢管束对于自密实混凝土的束缚效果。上述表面粗糙度与自密实混凝土的状态参数进行确定。具体的,自密实混凝土的状态参数包括外加剂掺量、砂率、扩展度、拌合物状态、拌合时间。
[0078]
s4、根据第一多面体凸起对钢管主板的内表面进行多面体凹坑的加工,以使钢管主板的内表面与金属保温层的外表面相配合。
[0079]
s5、对钢管主板的内表面以及金属保温层的外表面进行复合,得到钢管束。
[0080]
在本发明实施例中,钢管主板的内表面与金属保温层的外表面可以采用焊接复合或者冲击复合,焊接复合可以采用搅拌摩擦焊进行焊接或其他的板材焊接技术进行,冲击复合可以采用冲压焊接或者爆炸焊接来进行复合。
[0081]
在一种可能的实施例中,可以将钢管主板的u型件与金属保温层的u型件进行复合,得到复合u型件,将钢管主板的i型件与金属保温层的i型件进行复合,得到复合i型件。可以将一个复合u型件与一个复合i型件进行焊接,得到一个钢管束。也可以将多个复合u型
件进行连接,连接方式可以是焊接也可以是法兰连接,得到多个连接好的u型件,再焊接一个大型的复合i型件。
[0082]
可选的,上述金属保温层的内表面包括第一凸起区与第二凸起区,上述第二多面体凸起设置在上述第一凸起区与上述第二凸起区中,其中,在同一平面上,两个上述第二凸起区间隔设置,多个上述第一凸起区设置在两个上述第二凸起区之间,上述根据上述钢管束所用于的剪力墙的施工参数,对上述金属保温层的内表面进行第二多面体凸起加工的步骤包括:计算不同建筑高度下,上述剪力墙所需要的施工参数;根据上述剪力墙所需要的施工参数,确定上述第一凸起区的形状、位置和数量。
[0083]
具体的,在本发明实施例中,上述第二凸起区可以设置为条状凸起区,该第二凸起区的条状凸起区沿上述钢管束的转角边缘设置,上述第一凸起区可以设置为条状凸起区,第一凸起区的条状凸起区与第二凸起区的条状凸起区垂直设置,以钢管束为纵向设置,钢管束的转角线也为纵向,则第二凸起区的条状凸起区的方向也为纵向,而第一凸起区的条状凸起区则为横向设置。上述第一凸起区也可以设置为块状凸起区,第一凸起区的块状凸起区设置在第二凸起区的条状凸起区之间。
[0084]
可选的,上述金属保温层的外表面包括第一复合区以及第二复合区,上述第一多面体凸起设置在上述第一复合区;上述钢管主板的内表面包括第三复合区以及第四复合区,上述与上述第一多面体相配合的多面体凹坑设置在上述第三复合区;上述剪力墙的施工参数包括剪力墙的组合形状以及剪力墙的设计高度,上述根据上述钢管束所用于的剪力墙的施工参数,对上述金属保温层的外表面进行第一多面体凸起加工的步骤包括:根据上述剪力墙的组合形状,确定上述第一复合区的形状、位置和数量;根据上述剪力墙的设计高度,确定上述第一复合区与上述第二复合区的面积比例;根据上述第一复合区的形状、位置和数量、上述第一复合区与上述第二复合区的面积比例,对上述金属保温层的外表面进行第一多面体凸起加工。
[0085]
在本发明实施例中,上述第一复合区与上述第二复合区的面积比例随着剪力墙的设计高度的增加而增加。可以理解的是,在金属保温层的面积不变的情况下,随着剪力墙的设计高度的增加,第一复合区的面积在变大。在本发明实施例中,上述剪力墙的组合形状可以是c型、一字型、z字型、t字型、十字型或l型,上述剪力墙的组合形状是由钢管束作为组合单元进行组合而成的,具体可以通过焊接、法兰连接等连接方式进行组合。
[0086]
具体的,当剪力墙的组合形状可以是c型时,第一复合区的形状可以是四边形,第一复合区的位置可以在两端与中间,数量为3;当剪力墙的组合形状可以是一字型时,第一复合区的形状可以是四边形,第一复合区的位置可以在两端,数量为2;当剪力墙的组合形状可以是z字型时,第一复合区的形状可以是多边形或半圆形,第一复合区的位置可以在两端和中间,数量为4(两端各一个第一复合区,中间两个复合区);当剪力墙的组合形状可以是t字型时,第一复合区的形状可以是多边形或半圆形,第一复合区的位置可以在两端和中间,数量为4(两端各一个第一复合区,中间两个复合区);当剪力墙的组合形状可以是十字型时,第一复合区的形状在交叉处的钢管束中可以是多边形或半圆形,第一复合区的位置可以在两端和中间,数量为4(两端各一个第一复合区,中间两个复合区),在非交叉处的钢管束中可以是四边形,第一复合区的位置可以在两端和中间,数量为3;当剪力墙的组合形状可以是l型时,第一复合区的形状可以是多边形或半圆形,第一复合区的位置可以在两端
和中间,数量为3。
[0087]
可选的,上述对上述金属保温层的内表面以及上述金属保温层的外表面进行复合,得到钢管束的步骤包括:将上述钢管主板与上述金属保温层进行对齐;将上述第二复合区与上述第四复合区通过焊接进行复合;将上述第一复合区与上述第三复合区通过冲击进行复合,得到钢管束。
[0088]
在本发明实施例中,上述金属保温层的外表面与钢管主板的内表面要进行复合,从而增加钢管束的强度。需要说明的是,本发明实施例不是在钢管主板之中增加保温材料层,而是采用复合的方式增加金属保温层,使得钢管主板的强度增加。
[0089]
在一种可能的实施例中,上述金属保温层的厚度不超过钢管主板的厚度,优选的,上述金属保温层的厚度为钢管主板的厚度的1/2。
[0090]
需要说明的是,上述第二复合区与上述第四复合区为喷丸抛光面,可以通过焊接进行复合,上述第一复合区与上述第三复合区为配合的凹凸面,可以通过冲击进行复合,上述冲击复合可以采用爆炸法进行复合,采用爆炸法进行复合还可以提升材料性能。
[0091]
可选的,上述剪力墙的施工参数包括剪力墙的组成单元的受力情况,上述第一多面体凸起为锥形多面体,上述方法还包括:根据上述剪力墙的组成单元的受力情况进行确定上述锥形多面体的凸起高度。
[0092]
在本发明实施例中,剪力墙的组成单元的受力情况随着安装高度的增加而增大,因此,锥形多面体的凸起高度根据剪力墙的安装高度的增加而增加。
[0093]
上述锥形多面体可以是多面体各个面的顶端汇集成一个点,也可以是多面体各个面的顶端汇集在一个与底端截面平行的面上,上述与底端截面平行的面的面积小于底端的截面面积。
[0094]
在本发明实施例,通过将第一型材预制成钢管主板以及将第二型材预制成金属保温层;根据所述钢管束所用于的剪力墙的施工参数,对所述金属保温层的外表面进行第一多面体凸起加工,以及对所述金属保温层的内表面进行第二多面体凸起加工;根据自密实混凝土的状态参数对所述第二多面体凸起进行表面加工,以使所述第二多面体凸起具有表面粗糙度,其中,所述自密实混凝土用于浇筑所述钢管束以形成剪力墙的组成单元;根据所述第一多面体凸起对所述钢管主板的内表面进行多面体凹坑的加工,以使所述钢管主板的内表面与所述金属保温层的外表面相配合;对所述钢管主板的内表面以及所述金属保温层的外表面进行复合,得到钢管束。本发明实施例所得到钢管束能够将钢管束的钢管主板与金属保温层进行复合,通过金属保温层对硬化后的自密实混凝土进行一定程度的保温,增加自密实混凝土在寒冷条件的耐久性,同时,通过金属保温层内表面设置的第二多面体凸起,对硬化后的自密实混凝土进行位置限定,增加钢管束的表面对硬化后的自密实混凝土的束缚力,从而提高钢管束与硬化后的自密实混凝土的结合稳定性,进而提高剪力墙的组成单元的质量,最终提高剪力墙的质量。
[0095]
以上所揭露的仅为本发明较佳实施例而已,当然不能以此来限定本发明之权利范围,因此依本发明权利要求所作的等同变化,仍属本发明所涵盖的范围。