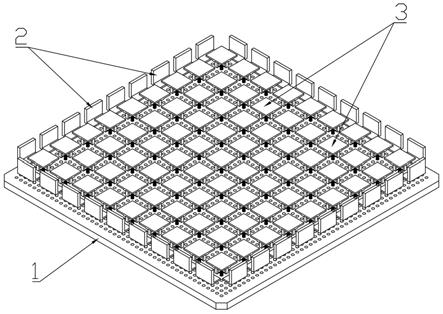
1.本发明涉及多晶硅锭切割技术领域,具体地涉及一种多晶硅锭开方尺寸可调节式锭台及使用方法。
背景技术:2.在半导体多晶硅锭的生产行业中,通常先由多晶铸锭炉铸产出长宽约1m的单块硅锭,再由金刚线开方机将其加工切割成36/49/64块的等边宽的小晶锭体,在硅锭开方环节中,由于行业技术的不断发展,硅片大尺寸化已是行业发展方向,硅锭切割后期会有不同硅锭尺寸的加工,以满足不同客户的需求。
3.现有的多晶硅开方机,其配套的铸锭台通常根据单一型号的多晶硅块定制而成,导致铸锭台的加工尺寸过于单一,更改加工的硅锭尺寸时需再次设计并定制全新晶锭台,并最终导致工艺变更的周期过长,且无法满足后续其他规格尺寸的硅锭加工;此外,现有的铸锭台底座与开方机之间为面接触设计,在切割多晶硅块的过程中会产生大量的硅粉并附着于此,导致在工作的过程中需要不间断的使用人工来祛除装置上的粉尘,否则会引起晶锭台与设备接触面不吻合,并使多晶硅块在切割过程中出现二次移位,并影响最终的切割质量,产出硅块s型面,严重的情况甚至会导致开方机断线和多晶硅锭产品报废的事故。
技术实现要素:4.鉴于背景技术所存在的技术问题,本发明所提供一种多晶硅锭开方尺寸可调节式锭台及使用方法,装置将固定的晶锭台改成网格化结构,解决了传统的开方机锭台只能加工单一尺寸的硅块缺陷,装置还在晶锭台底部增设冷却液流动空间,可有效降低人工清除硅粉的频率和难度,在提高工作效率的同时也提高了晶体硅的切割质量。
5.为了解决上述技术问题,本发明采取了如下技术方案来实现:一种多晶硅锭开方尺寸可调节式锭台,包括有调节底板、晶体调节底座和边料防护板,调节底板上开设有安装孔,晶体调节底座安设在安装孔内,边料防护板安设在晶体调节底座的外围处,进行切割工作时,多晶硅锭置于边料防护板的内侧和晶体调节底座的上端。
6.优选的方案中,调节底板上的安装孔内设有内螺纹并用于安装晶体调节底座和边料防护板。
7.优选的方案中,晶体调节底座包括底面板、支撑架、紧固螺丝和定位螺栓;所述底面板通过紧固螺丝与支撑架之间可拆卸式连接,支撑架的下端连接定位螺栓,定位螺栓与安装孔之间螺纹连接。
8.优选的方案中,边料防护板包括底板、侧挡板和插销;所述底板的上端面安设有侧挡板,底板的下端面设有插销,底板通过插销与安装孔插入式连接,侧挡板的宽度与底面板的宽度一致。
9.优选的方案中,底面板与多晶硅锭的接触面处设置有防滑胶垫。
10.一种多晶硅锭开方尺寸可调节式锭台,装置使用时包括以下步骤:step1:根据现场实际情况,在调节底板上均匀开设安装孔;step2:在调节底板上敷设一层塑料薄膜;step3:根据所需切割的多晶硅锭大小,将晶体调节底座安设在安装孔内,并使晶体调节底座在调节底板上呈矩阵排列;step4:将边料防护板安插在晶体调节底座的外围;step5:将待切割的多晶硅锭放置在边料防护板的内侧和晶体调节底座的上端;step6:用金刚线沿着晶体调节底座的间隔切割,使多晶硅锭分解成相同大小的矩形小块;step7:当需要调整多晶硅锭的切割尺寸时,将晶体调节底座从调节底板上拆除,并参照安装孔之间的孔距进行新的规划布局,然后重复上述步骤2至6。
11.在step1中,调节底板上的安装孔纵向孔心距和横向孔心距相等,所述安装孔之间的孔心间距设置在20mm
‑
40mm之间。
12.在step2中,晶体调节底座以调节底板中心处的安装孔为对称中心,并在晶体调节底座上呈对称矩阵分布,晶体调节底座与多晶硅锭的接触面设有防滑胶垫。
13.在step5中,在多晶硅锭切割的过程中,使用冷却液不间断的冲刷晶体调节底座和调节底板的间隔处。以对多晶硅锭进行持续降温和冲刷切割时堆积的硅粉。
14.本专利可达到以下有益效果:1、装置通过将调节底板与晶体调节底座进行组装,可提高锭台装置的灵活性,提高了硅块的加工范围,解决了硅锭开方机只能加工单一尺寸硅锭的缺陷,节省了变更技术方案所需要的成本;2、装置在晶锭台底部增设冷却液流动空间,可有效降低人工清除硅粉的频率和难度,提高了硅锭的切割质量,降低了开方机加工时的断线率,在提高了硅锭加工质量的同时也降低了硅锭开方机的维护成本。
附图说明
15.下面结合附图和实施例对本发明作进一步说明:图1为本发明整体结构拆解意图;图2为本发明整体结构安装意图;图3为本发明工作位安装结构示意图;图4为本发明晶体调节底座结构示意图;图5为本发明边料防护板结构示意图。
16.图中:调节底板1、安装孔101、边料防护板2、底板201、侧挡板202、插销203、晶体调节底座3、底面板301、支撑架302、紧固螺丝303、定位螺栓304、多晶硅锭4。
具体实施方式
17.实施案例1:多晶硅块单边长为200mm,单次加工数量为49块的多晶硅块制作:步骤1:在调节底板1上开设安装孔101,安装孔101的间距设置为30mm,安装孔101纵向孔心距和横向孔心距相等。
18.步骤2:为防止后续切割多晶硅锭4的过程中产生的硅粉堵塞安装孔101,调节底板1开孔完毕后要在板面敷设一层塑料薄膜。
19.步骤3:根据所需切割的多晶硅锭4大小,以调节底板1中心处的安装孔101为对称中心,使晶体调节底座3在调节底板1上以7*7的矩阵排布,纵横方向各设置7个晶体调节底座3,以形成49块的切割布局,晶体调节底座3之间间隔30mm。
20.步骤4:按照步骤2的规划布局,使晶体调节底座3下方的定位螺栓304与安装孔101螺纹连接,将边料防护板2安插在晶体调节底座3的外围,使边料防护板2下方的插销203垂直插入到安装孔101内固定,再将防滑垫敷设在底面板301的上方。
21.步骤5:将待切割的多晶硅锭4平稳的放置在边料防护板2的内侧和晶体调节底座3的上端。
22.步骤6:用金刚线沿着晶体调节底座3间隔切割多晶硅锭4,使多晶硅锭4分解成49块相同大小的矩形小块,在切割的过程中,需用冷却液沿着晶体调节底座3的间隔持续冲刷,对多晶硅锭4持续降温的并防止硅粉的堆积。
23.步骤7:多晶硅锭4切割完毕后,将49块硅锭从晶体调节底座3上取下,再将晶体调节底座3从调节底板1上拆除,根据下次切割的硅锭大小重新对晶体调节底座3进行规划布局,然后重复上述步骤2至步骤6。
24.实施案例2:多晶硅块单边长为300mm,单次加工数量为36块的多晶硅块制作:步骤1: 在调节底板1上开设安装孔101,安装孔101的间距设置为30mm,安装孔101纵向孔心距和横向孔心距相等。
25.步骤2:为防止后续切割多晶硅锭4的过程中产生的硅粉堵塞安装孔101,调节底板1开孔完毕后要在板面敷设一层塑料薄膜。
26.步骤3:根据所需切割的多晶硅锭4大小,以调节底板1中心处的安装孔101为对称中心,让晶体调节底座3在调节底板1上以6*6的矩阵排布,纵横方向各设置6个晶体调节底座3,以形成36块的切割布局,晶体调节底座3之间间隔80mm。
27.步骤4:按照步骤2的规划布局,使晶体调节底座3下方的定位螺栓304与安装孔101螺纹连接,将边料防护板2安插在晶体调节底座3的外围,使边料防护板2下方的插销203垂直插入到安装孔101内固定,再将防滑垫敷设在底面板301的上方。
28.步骤5:将待切割的多晶硅锭4平稳的放置在边料防护板2的内侧和晶体调节底座3的上端。
29.步骤6:用金刚线沿着晶体调节底座3间隔切割多晶硅锭4,使多晶硅锭4分解成49块相同大小的矩形小块,在切割的过程中,需用冷却液沿着晶体调节底座3的间隔持续冲刷,对多晶硅锭4持续降温的并防止硅粉的堆积。
30.步骤7:多晶硅锭4切割完毕后,将36块硅锭从晶体调节底座3上取下,再将晶体调节底座3从调节底板1上拆除,根据下次切割的硅锭大小重新对晶体调节底座3进行规划布局,然后重复上述步骤2至步骤6。
31.上述的实施例仅为本发明的优选技术方案,而不应视为对于本发明的限制,在互 不冲突的前提下,本发明记载的各项技术特征能够互相组合。本发明的保护范围应以权利 要求记载的技术方案,包括权利要求记载的技术方案中技术特征的等同替换方案为保护范围。即在此范围内的等同替换改进,也在本发明的保护范围之内。