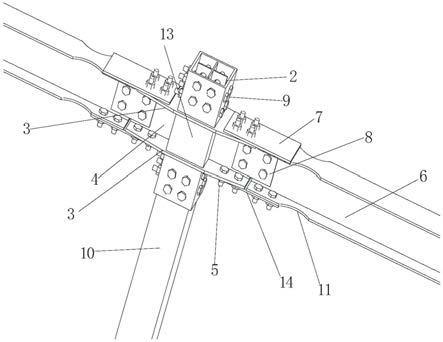
1.本实用新型涉及一种用于打包箱式的模块化钢结构房屋连接节点。属于房屋建筑技术领域。
背景技术:2.由于将预制好的标准模块单元在农村等道路交通不发达的地区整体运输时会存在有运输不方便等问题,所以采取一种打包箱式运输,打包箱式运输不是将在工厂预制好的标准模块单元整体运输,而是将在工厂预制好的梁柱等构件运输至施工现场,在现场完成对构件的拼装,这样就可以有效解决运输不方便的问题。
3.模块化建筑是指将建筑分成若干空间模块,模块内的一切结构骨架、设备、管线、装修、固定家具均已做好,外立面装修也可以完成,将这些模块构件运至施工现场,就像“搭建积木”一样拼装在一起的建筑。模块化建筑作为一种高度集成的装配式建筑,是建筑工业化发展的高级阶段,实现高预制率的同时具有绿色环保、施工高效、方便拆卸等技术优势,与装配式建筑的标准化设计、工厂化生产、装配化施工、一体化装修的建造模式高度吻合。
4.近年来尽管模块化钢结构建筑快速发展,但仍存在一些突出的问题。首先受标准模块单元的尺寸限制,模块的堆叠拼装使得模块节点连接几乎都有“多柱多梁”的特点,比如角柱的“两柱四梁”、边柱的“四柱八梁”和中柱的“八柱十六梁”等,这会导致节点位置处构件数量过多而导致施工安装过程复杂等问题出现;其次由于模块化钢结构连接节点的设计研究在保证其力学性能的基础上还要实现装配流程简单方便,因此在实际设计过程存在一定的难度。最后现有模块化建筑无法避免“多梁多柱多板”的问题。c.d.anna教授的论文《seismic overstrength in braced frames of modular steel buildings》研究结果表明,模块结构的双层梁协同工作状态难以达到理想状态,使结构受力性能产生较大的差异性;特别是“八柱十六梁”等多构件会交处的节点构造复杂、连接刚度小、整体性差等问题将对结构整体的承载能力、抗震性能造成极为不利的影响。
技术实现要素:5.本实用新型拟解决的技术问题是,目的在于针对连接方式的缺少,提供一种用于打包箱式的模块化钢结构房屋连接节点,该种结构实现了工厂焊接、现场装配的绿色高效节点连接,充分利用节点核心预制件的上/下外套筒、上/下水平隔板、核心区钢板的开口空间便于长贯穿螺栓和高强螺栓安装的特点,实现节点核心预制件与上部模块单元方钢管柱、下部模块单元方钢管柱与模块单元工字梁的连接。
6.为实现上述目的,本实用新型的技术方案是:
7.一种用于打包箱式的模块化钢结构房屋连接节点,包括上部方钢管柱、下部方钢管柱和工字梁;所述上部方钢管柱和下部方钢管柱通过节点核心预制件竖向连接,所述节点核心预制件工厂一体预制成型,包括外套筒、焊接在所述外套筒的两块水平隔板和位于两块所述水平隔板之间的核心区钢板,所述工字梁的上翼缘外侧焊接有第一外侧翼缘连接
盖板,所述工字梁的上翼缘通过第一外侧翼缘连接盖板和与水平隔板固定连接,所述工字梁的下翼缘通过第二外侧翼缘连接盖板和与水平隔板固定连接,所述工字梁的腹板通过腹板连接盖板与核心区钢板固定连接。所述腹板连接盖板将核心区钢板与工字梁栓接实现模块梁的水平拼接。
8.所述工字梁的上下翼缘内侧安装有内侧翼缘连接盖板,所述工字梁的上下翼缘通过第一外侧翼缘连接盖板和第二外侧翼缘连接盖板和内侧翼缘连接盖板与水平隔板固定连接。
9.所述上水平隔板、下水平隔板均设有螺栓孔,第一外侧翼缘连接盖板、内侧翼缘连接盖板和第二外侧翼缘连接盖板有与之相对应的螺栓孔,节点核心预制件与右侧工字梁连接时,所述第一外侧翼缘连接盖板左侧通过高强螺栓与上水平隔板和内侧翼缘连接盖板连接,所述第一外侧翼缘连接盖板右侧通过焊接与工字梁连接,所述内侧翼缘连接盖板右侧通过高强螺栓与工字梁和第一外侧翼缘连接盖板连接,所述内侧翼缘连接盖板左侧通过高强螺栓与下水平隔板和第二外侧翼缘连接盖板连接,所述内侧翼缘连接盖板右侧通过高强螺栓与工字梁和第二外侧翼缘连接盖板连接,实现工字梁与节点核心预制件的连接,将模块工字梁上/下翼缘所受的拉/压荷载传递至核心区,所述核心区钢板和工字梁腹板均设有螺栓孔,所述腹板连接盖板通过高强螺栓实现工字梁腹板与节点核心预制件核心区钢板的连接,将模块工字梁腹板所受的剪力传递至核心区钢板。
10.所述工字梁设有有效实现梁端塑性铰外移,避免梁柱节点发生脆性破坏的削弱梁段。
11.所述上部方钢管柱和下部方钢管柱内嵌有十字型钢板,外套筒套接在所述上部方钢管柱的下端和下部方钢管柱的上端,长贯穿螺栓贯穿所述外套筒、方钢管柱和十字型钢板实现上部方钢管柱、节点核心预制件与下部方钢管柱的紧密竖向连接。所述外套筒上下端侧壁上设有螺栓孔,下部方钢管柱上端侧壁和上部方钢管柱下端侧壁设有与外套筒侧壁相对应的螺栓孔,防止贯穿螺栓压力使上部模块单元方钢管柱下端与下部模块单元方钢管上端发生局部屈曲。
12.所述第一外侧翼缘连接盖板左侧通过高强螺栓与水平隔板可拆卸固定连接,所述第二外侧翼缘连接盖板左侧通过高强螺栓与水平隔板可拆卸固定连接,所述第二外侧翼缘连接盖板右侧通过高强螺栓与工字梁可拆卸固定连接。
13.所述内侧翼缘连接盖板左侧通过高强螺栓与水平隔板和外侧翼缘连接盖板可拆卸固定连接,所述内侧翼缘连接盖板右侧通过高强螺栓与工字梁和外侧翼缘连接盖板可拆卸固定连接。
14.所述外套筒被两块所述水平隔板分隔为下外套筒、中外套筒和上外套筒,所述下外套筒、中外套筒和上外套筒为相同尺寸的方钢板。
15.所述外套筒被两块所述水平隔板分隔为下外套筒、中外套筒和上外套筒,所述下外套筒和上外套筒为相同尺寸的方钢板,所述中外套筒的外轮廓尺寸较下外套筒和上外套筒的外轮廓尺寸小0.1-5cm,所述中外套筒与两块所述水平隔板形成的空间内浇筑有混凝土
16.与现有技术相比,本实用新型的有益效果在于:
17.本实用新型涉及的用于打包箱式的模块化钢结构房屋连接节点充分利用节点核
心预制件的上/下外套筒、上/下水平隔板、核心区钢板的开口空间便于长贯穿螺栓和高强螺栓安装的特点,实现节点核心预制件与上部模块单元方钢管柱、下部模块单元方钢管柱与模块单元工字梁的连接。模块单元工字梁进行了一定的削弱,利用梁段削弱位置处的塑性变形以及梁段拼接区的盖板滑移变形来实现耗能,保证节点域核心区的部件不会破坏,直接替换破坏的模块梁,从而实现塑性铰外移,震后可修复的目的。
18.本发明提供的用于打包箱式的模块化钢结构连接节点不止适用于平面节点,也适用于空间节点。本发明提供的用于打包箱式的模块化钢结构连接节点完全实现了工厂焊接、现场装配的绿色高效节点连接方式。
附图说明
19.为了更清楚地说明本实用新型实施案例或现有技术中的技术方案,下面将对实施案例或现有技术描述中所需要使用的附图作简单地介绍,显而易见地,下面描述中的附图仅仅是本实用新型的一些实施案例,对于本领域普通技术人员来讲,在不付出创造性劳动性的前提下,还可以根据这些附图获得其他的附图。
20.图1为本实用新型用于打包箱式的模块化钢结构房屋连接节点的下部方钢管柱和十字型钢板工厂焊接结构示意图。
21.图2为本实用新型用于打包箱式的模块化钢结构房屋连接节点的下部方钢管柱与节点核心预制件栓接结构示意图。
22.图3为本实用新型用于打包箱式的模块化钢结构房屋连接节点的节点核心预制件与带削弱梁段工字梁栓接结构示意图。
23.图4为本实用新型用于打包箱式的模块化钢结构房屋连接节点实施例1的示意图。
24.图5为本实用新型用于打包箱式的模块化钢结构房屋连接节点实施例2的示意图(1)。
25.图6为本实用新型用于打包箱式的模块化钢结构房屋连接节点实施例2的示意图(2)。
26.图7为本实用新型用于打包箱式的模块化钢结构房屋连接节点实施例2的示意图(3);
27.图8为本实用新型用于打包箱式的模块化钢结构房屋连接节点节点核心预制件的示意图(1);
28.图9为本实用新型用于打包箱式的模块化钢结构房屋连接节点节点核心预制件的示意图(2)。
29.图中:1-上部方钢管柱;2-十字型钢板;3-水平隔板;4-核心区钢板;5-高强螺栓;6-工字梁;7-第一外侧翼缘连接盖板;8-腹板连接盖板;9-长贯穿螺栓;10-下部方钢管柱;11-削弱梁段;12-内侧翼缘连接盖板;13-外套筒;14-第二外侧翼缘连接盖板。
具体实施方式
30.下面结合附图对本实用新型的具体实施方式作进一步说明。在此需要说明的是,对于这些实施方式的说明用于帮助理解本实用新型,但并不构成对本实用新型的限定。此外,下面所描述的本实用新型各个实施方式中所涉及的技术特征只要彼此之间未构成冲突
就可以相互组合。
31.参照图1-图9,一种用于打包箱式的模块化钢结构房屋连接节点,包括上部方钢管柱1、下部方钢管柱10和工字梁6;所述上部方钢管柱1和下部方钢管柱10通过节点核心预制件竖向连接,所述节点核心预制件工厂一体预制成型,包括外套筒13、焊接在所述外套筒13的两块水平隔板3和位于两块所述水平隔板3的核心区钢板4,所述工字梁6的上翼缘外侧焊接有第一外侧翼缘连接盖板7,所述工字梁6的上翼缘通过第一外侧翼缘连接盖板7和与水平隔板3固定连接,所述工字梁6的下翼缘通过第二外侧翼缘连接盖板14和与水平隔板3固定连接,所述工字梁6的腹板通过腹板连接盖板8与核心区钢板4固定连接。所述腹板连接盖板8将核心区钢板4与工字梁6栓接实现模块梁的水平拼接。核心区预制件模块设有贯通式隔板,使传力途径更加明确,梁端的力可以有效传递至节点核心区预制件模块,进而传递至方钢管柱模块。
32.在另一种情况下,所述工字梁6的上下翼缘内侧安装有内侧翼缘连接盖板12,所述工字梁6的上下翼缘通过第一外侧翼缘连接盖板7和第二外侧翼缘连接盖板14和内侧翼缘连接盖板12与水平隔板3固定连接。
33.所述上水平隔板3、下水平隔板3均设有螺栓孔,第一外侧翼缘连接盖板7、内侧翼缘连接盖板12和第二外侧翼缘连接盖板14有与之相对应的螺栓孔,节点核心预制件与右侧工字梁6连接时,所述第一外侧翼缘连接盖板7左侧通过高强螺栓5与上水平隔板3和内侧翼缘连接盖板12连接,所述第一外侧翼缘连接盖板7右侧通过焊接与工字梁6连接,所述内侧翼缘连接盖板12右侧通过高强螺栓5与工字梁6和第一外侧翼缘连接盖板7连接,所述内侧翼缘连接盖板12左侧通过高强螺栓5与下水平隔板3和第二外侧翼缘连接盖板14连接,所述内侧翼缘连接盖板12右侧通过高强螺栓5与工字梁6和第二外侧翼缘连接盖板14连接,实现工字梁6与节点核心预制件的连接,将模块工字梁6上/下翼缘所受的拉/压荷载传递至核心区,所述核心区钢板4和工字梁6腹板均设有螺栓孔,所述腹板连接盖板8通过高强螺栓5实现工字梁6腹板与节点核心预制件核心区钢板4的连接,将模块工字梁6腹板所受的剪力传递至核心区钢板4。
34.所述工字梁6设有有效实现梁端塑性铰外移,避免梁柱节点发生脆性破坏的削弱梁段11。工字梁6上翼缘与拼接区上翼缘连接盖板进行焊接,并对梁截面进行削弱设计,形成上翼缘焊有连接盖板的工字梁6模块。
35.所述上部方钢管柱1和下部方钢管柱10内嵌有十字型钢板2,外套筒13套接在所述上部方钢管柱1的下端和下部方钢管柱10的上端,长贯穿螺栓9贯穿所述外套筒13、方钢管柱和十字型钢板2实现上部方钢管柱1、节点核心预制件与下部方钢管柱10的紧密竖向连接。所述外套筒13上下端侧壁上设有螺栓孔,下部方钢管柱10上端侧壁和上部方钢管柱1下端侧壁设有与外套筒13侧壁相对应的螺栓孔。防止贯穿螺栓压力使上部模块单元方钢管柱下端与下部模块单元方钢管上端发生局部屈曲。
36.对于采用长贯穿螺栓9的节点,在柱体内部焊接了十字形加劲肋,用以防止柱体与核心区连接区域发生局部屈曲。
37.所述第一外侧翼缘连接盖板7左侧通过高强螺栓5与水平隔板3可拆卸固定连接,所述第二外侧翼缘连接盖板14左侧通过高强螺栓5与水平隔板3可拆卸固定连接,所述第二外侧翼缘连接盖板14右侧通过高强螺栓5与工字梁6可拆卸固定连接。
38.所述内侧翼缘连接盖板12左侧通过高强螺栓5与水平隔板3和外侧翼缘连接盖板可拆卸固定连接,所述内侧翼缘连接盖板12右侧通过高强螺栓5与工字梁6和外侧翼缘连接盖板可拆卸固定连接。
39.在一种情况下,所述外套筒13被两块所述水平隔板3分隔为下外套筒、中外套筒和上外套筒,所述下外套筒、中外套筒和上外套筒为相同尺寸的方钢板。
40.在另一种情况下,所述外套筒13被两块所述水平隔板3分隔为下外套筒、中外套筒和上外套筒,所述下外套筒和上外套筒为相同尺寸的方钢板,所述中外套筒的外轮廓尺寸较下外套筒和上外套筒的外轮廓尺寸小0.1-5cm,所述中外套筒与两块所述水平隔板3形成的空间内浇筑有混凝土。
41.实施例1:
42.本实施例提供的节点核心预制件与工字梁6单拼接盖板连接节点是由以下施工步骤获得的:
43.(1)下部方钢管柱10上端与十字型钢板2于工厂焊接,如图1所示;
44.(2)在下部方钢管柱10上端放入节点核心预制件,通过长贯穿螺栓9连接下部方钢管柱10、十字型钢板2和下部外套筒13,如图2所示,其中节点核心预制件是由上、下水平隔板3、核心区钢板4、外套筒13在工厂焊接而成;节点核心预制件的装配工艺为:将外套筒13分成三块,分别为下外套筒、中外套筒和上外套筒,在下外套筒上覆盖一下水平隔板并焊接连接,在下水平隔板上放置中外套筒和核心区钢板4并焊接连接,再覆盖一上水平隔板并焊接连接,在上水平隔板放置上外套筒并焊接连接。
45.(3)右侧模块单元工字梁6与节点核心预制件连接,将模块单元工字梁6上翼缘焊接第一外侧翼缘连接盖板7下落至节点核心预制件上水平隔板3,高强螺栓5连接节点核心预制件上水平隔板3和第一外侧翼缘连接盖板7,后安装第二外侧翼缘连接盖板14,高强螺栓5连接下水平隔板3和第二外侧翼缘连接盖板14左侧,高强螺栓5连接模块单元工字梁6下翼缘和第二外侧翼缘连接盖板14右侧,而后放置腹板连接盖板8,高强螺栓5连接节点核心预制件的腹板(核心区钢板4)与模块单元工字梁6的腹板,如图3所示;而后左侧模块单元工字梁6与节点核心预制件连接同上述连接方法。其中单拼接盖板连接模块单元工字梁6进行削弱梁段11;
46.(4)将上部模块单元方钢管柱下落至节点核心预制件的上部外套筒13,长贯穿螺栓9连接上部外套筒13、上部模块单元方钢管柱的下端和十字型钢板2。
47.以上完成连接,如图4所示。
48.实施例2:
49.本实施例提供的节点核心预制件与工字梁6双拼接盖板连接节点是由以下施工步骤获得的:
50.(1)下部模块单元方钢管柱上端与十字型钢板2于工厂焊接,如图1所示;
51.(2)在下部模块单元方钢管柱上端放入节点核心预制件,通过长贯穿螺栓9连接下部模块单元方钢管柱、十字型钢板2和下部外套筒13,如图2所示,其中节点核心预制件是由上、下水平隔板3,核心区钢板4,外套筒13工厂焊接而成;
52.(3)右侧模块单元工字梁6与节点核心预制件连接,将模块单元工字梁6上翼缘焊接第一外侧翼缘连接盖板7下落至节点核心预制件上水平隔板3,而后放置上翼缘内侧翼缘
连接盖板12,高强螺栓5连接节点核心预制件上水平隔板3和上翼缘第一外侧翼缘连接盖板7、内侧翼缘连接盖板12的左侧,之后高强螺栓5连接工字梁6和第一外侧翼缘连接盖板7、内侧翼缘连接盖板12的右侧;而后放置第二外侧翼缘连接盖板14、下翼缘内侧翼缘连接盖板12,高强螺栓5连接下水平隔板3和第二外侧翼缘连接盖板14、下翼缘内侧翼缘连接盖板12左侧,之后高强螺栓5连接模块单元工字梁6下翼缘和第二外侧翼缘连接盖板14、下翼缘内侧翼缘连接盖板12右侧,而后放置腹板连接盖板8,高强螺栓5连接节点核心预制件的腹板(核心区钢板4)与模块单元工字梁6的腹板,如图5所示;而后左侧模块单元工字梁6与节点核心预制件连接同上述连接方法。其中双拼接盖板连接模块单元工字梁6进行削弱梁段11;
53.(4)将上部模块单元方钢管柱下落至节点核心预制件的上部外套筒13,长贯穿螺栓9连接上部外套筒13、上部模块单元方钢管柱的下端和十字型钢板2。
54.以上完成连接,如图6所示。
55.型不限于所描述的实施方式。对于本领域的技术人员而言,在不脱离本实用新型原理和精神的情况下,对这些实施方式进行多种变化、修改、替换和变型,仍落入本实用新型的保护范围内。