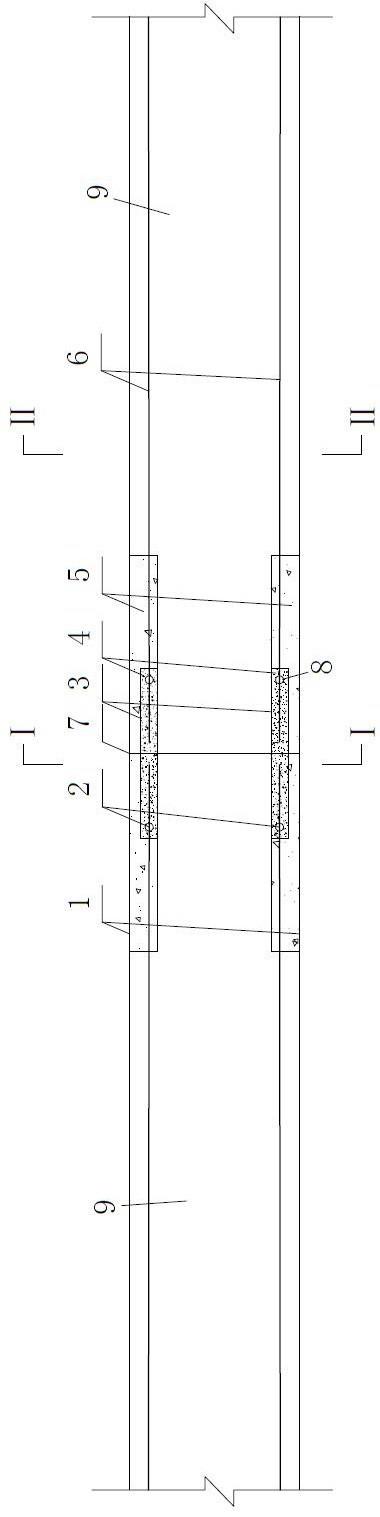
1.本发明涉及一种通过套筒连接的预制拼装钢筋混凝土梁结构及施工方法,涉及土木工程领域。
背景技术:2.随着国家经济转型,产业结构的调整,我国正向工厂化、标准化的“制造”方式转变。目前,我国极大部分的结构都是采用现浇钢筋混凝土技术建造。随着装配式混凝土技术的推广应用,为了保证装配式混凝土结构在结构性能上不低于现浇混凝土结构,我国也制定相应的混凝土结构技术规程,包括从结构设计到构件预制和现场施工等方面,基本思路是将现浇混凝土结构经过合理的拆分、工厂预制构件、现场拼装等环节。其中拆分有利于工厂预制,也要有利于现场拼装,且拼装后的结构要满足结构的安全性和功能性要求。为此,出现了多种形式的拆分及拼装连接方式,其连接方式直接影响到施工速度及结构安全性,更受到广泛的关注。
3.与传统现浇混凝土结构相比,装配式混凝土结构中存在更多的接缝,这些接缝的不仅直接决定结构的整体安全性,而且也影响着结构的耐久性及实用功能性。预制装配结构的连接方式需根据结构形式、抗震设防烈度、施工、运输、拼装等因素综合考虑。根据国内外的试验研究及应用调研,通过几种连接构造的对比,考虑到国外既有经验的可靠度及国内理念接受度,国内采用的连接构造多选用灌浆套筒连接构造。将螺纹钢筋插入金属套筒内部,再灌注高强灌浆料拌合物,利用灌浆料凝结固化后与螺纹钢筋之间形成的粘结锚固传递应力而实现钢筋对接连接的方式,简称为套筒灌浆连接,可分为全灌浆套筒连接和半灌浆套筒连接。
4.现有的钢筋与套筒之间的连接通常是由竖向插入完成,施工技术难,在实际过程中,会出现套筒和插筋各自的位置测量结果符合要求,但拼接时依然安装不上的问题。
技术实现要素:5.鉴于现有技术的不足,本发明所要解决的技术问题是提供一种通过套筒连接的预制拼装钢筋混凝土梁结构及施工方法。
6.为了解决上述技术问题,本发明的技术方案是:一种通过套筒连接的预制拼装钢筋混凝土梁结构,所述的预制拼装钢筋混凝土梁由预制构件进行端部对接组成,相邻预制构件的连接端侧四周均设有用以方便施工时拨移灌浆套筒位置的预留凹槽,预留凹槽上的灌浆套筒两端均与露出预留凹槽的主钢筋端部连接,预留凹槽上均设有后填混凝土层。
7.优选的,所述预留凹槽均位于预制构件连接端侧内部的主钢筋侧面,相对接的预留凹槽需在同一条直线上,并且预留凹槽两边完成面保持在同一平面上。
8.优选的,所述预制构件各面边缘在主钢筋位置处均设置预留凹槽,所述预制拼装钢筋混凝土梁截面任意一边上的两个预留凹槽边长总和应小于预制拼装钢筋混凝土梁截面边长的2/3。
9.优选的,所述灌浆套筒的内径大于筒内主钢筋的直径至少1.5cm;灌浆套筒内灌注有水泥浆填充层,水泥浆填充层为灌浆料或高强砂浆。
10.优选的,所述灌浆套筒长度小于单侧的预留凹槽长度,预留凹槽截面尺寸比灌浆套筒外径大至少3cm。
11.优选的,所述灌浆套筒设置进浆孔及出浆孔,出浆孔距离灌浆套筒端部不得大于3cm,同时出浆孔高于进浆孔。
12.优选的,相邻预制构件的相对主筋在接缝处之间的距离不得大于灌浆套筒长度的1/3,确保灌浆套筒连接的作用,使相邻预制构件通过灌浆套筒连接形成一体共同受力。
13.一种通过套筒连接的预制拼装钢筋混凝土梁结构的施工方法,按以下步骤进行:(1)施工预制构件台座,安装钢模板:制作钢筋混凝土台座或全钢结构台座,上铺钢板作为预制构件底模板;外侧模采用定形钢模板与台座配套设计;模板准确就位后,通过对拉螺栓对模板进行加固;(2)绑扎与安装钢筋笼:检查底模板和侧模板,并涂刷隔离剂,吊装钢筋笼放入预制的钢模板内,并固定保护层厚度;(3)安装端模板和预埋件:安装端模板;安装用于灌浆套筒连接主筋的盒子,以形成预留凹槽;弹线确定两侧钢筋混凝土梁相对预留凹槽贴合位置,使预留凹槽两边完成面保持在同一平面上;(4)在模板内浇筑混凝土:在钢筋及模板验收合格后进行混凝土的浇筑,采用附着式振动器并附振动棒进行振捣,一般混凝土不在下沉,无显著气泡上升,混凝土表面出现薄层水泥浆,并有均匀的外观和平面为止;(5)混凝土养护:当气温较高时,混凝土强度增长满足施工进度要求,采用自然养护;当外界气温不能满足工程进度要求时,则采用蒸汽养护;(6)预制拼装钢筋混凝土梁运输与安装:运输预制构件,将灌浆套筒套进一侧预留凹槽内的主钢筋,并将灌浆套筒放置在该侧预制构件的预留凹槽内,组装相邻预制构件;(7)移动灌浆套筒并灌浆:将灌浆套筒拨移至梁接缝中间,密封灌浆套筒端部,沿着灌浆套筒的进浆孔注浆,当出浆孔有浆体均匀流出时停止注浆;而后在预留凹槽内后填混凝土;后填混凝土为比预制构件的混凝土强度高一级混凝土或高强砂浆或灌浆料封堵;(8)依此循环,将若干条预制构件相互拼接。
14.与现有技术相比,本发明具有以下有益效果:该结构现场浇筑工序少,现场可以节省大量的人工,可以降低劳动强度,加快施工速度;模板可以重复使用,并且预制构件的耐久性会优于现浇构件,能够充分发挥混凝土的力学性能,有着明显的经济效益。本发明使得预制拼装钢筋混凝土梁装配化,实现工厂工业化生产、现场直接拼装,具有现场施工湿作业少、施工周期短、构件质量有保证、经济环保等优点,具有良好的工程推广前景。
15.下面结合附图和具体实施方式对本发明做进一步详细的说明。
附图说明
16.图1为本发明实施例的钢筋连接立面图。
17.图2为本发明实施例的钢筋连接平面图。
18.图3为图1的
ⅰ‑ⅰ
断面图。
19.图4为图1的
ⅱ‑ⅱ
断面图。
20.图5为灌浆套筒大样图。
21.图中:1-预留凹槽,2-进浆孔,3-灌浆套筒,4-水泥浆填充层,5-后填混凝土层,6-主钢筋,7-接缝,8-出浆孔,9-预制构件,10-橡胶塞。
具体实施方式
22.下面结合附图及实施例对本发明做进一步说明。
23.应该指出,以下详细说明都是示例性的,旨在对本技术提供进一步的说明。除非另有指明,本文使用的所有技术和科学术语具有与本技术所属技术领域的普通技术人员通常理解的相同含义。
24.需要注意的是,这里所使用的术语仅是为了描述具体实施方式,而非意图限制根据本技术的示例性实施方式。如在这里所使用的,除非上下文另外明确指出,否则单数形式也意图包括复数形式,此外,还应当理解的是,当在本说明书中使用术语“包含”和/或“包括”时,其指明存在特征、步骤、操作、器件、组件和/或它们的组合。
25.如图1~5所示,本实施例提供了一种通过套筒连接的预制拼装钢筋混凝土梁结构,预制拼装钢筋混凝土梁内布置有主钢筋,所述的预制拼装钢筋混凝土梁由预制构件进行端部对接组成,相邻预制构件的连接端侧四周均设有用以方便施工时拨移灌浆套筒位置的预留凹槽,预留凹槽上的灌浆套筒两端均与露出预留凹槽的主钢筋端部连接,预留凹槽上均设有后填混凝土层,填充预留凹槽与灌浆套筒之间的间隙,使两相连接的预制构件通过灌浆套筒的连接形成一体共同受力。
26.在本发明实施例中,预留凹槽位于预制构件的连接端侧四个边缘。
27.在本发明实施例中,所述预留凹槽均位于预制构件连接端侧内部的主钢筋侧面,相对接的预留凹槽需在同一条直线上,并且预留凹槽两边完成面保持在同一平面上。
28.在本发明实施例中,所述预制构件各面边缘在主钢筋位置处均设置预留凹槽,所述预制拼装钢筋混凝土梁截面任意一边上的两个预留凹槽边长总和应小于预制拼装钢筋混凝土梁截面边长的2/3。
29.在本发明实施例中,所述灌浆套筒的内径大于筒内主钢筋的直径至少1.5cm;灌浆套筒内灌注有水泥浆填充层,水泥浆填充层为灌浆料或高强砂浆。
30.在本发明实施例中,所述灌浆套筒长度小于单侧的预留凹槽长度,预留凹槽截面尺寸比灌浆套筒外径大至少3cm。
31.在本发明实施例中,所述灌浆套筒设置进浆孔及出浆孔,用于注浆并判断停止灌浆时间,出浆孔距离灌浆套筒端部不得大于3cm,同时出浆孔高于进浆孔。
32.在本发明实施例中,相邻预制构件的相对主筋在接缝处之间的距离不得大于灌浆套筒长度的1/3,确保灌浆套筒连接的作用,使相邻预制构件通过灌浆套筒连接形成一体共同受力。
33.在本发明实施例中,灌浆套筒的端部固定有橡胶塞,橡胶塞上设有主钢筋穿入孔。
34.一种通过套筒连接的预制拼装钢筋混凝土梁结构的施工方法,按以下步骤进行:(1)施工预制构件台座,安装钢模板:制作钢筋混凝土台座或全钢结构台座,上铺钢板作为预制构件底模板;外侧模采用定形钢模板与台座配套设计;模板准确就位后,通过
对拉螺栓对模板进行加固;(2)绑扎与安装钢筋笼:检查底模板和侧模板,并涂刷隔离剂,吊装钢筋笼放入预制的钢模板内,并固定保护层厚度;(3)安装端模板和预埋件:安装端模板;安装用于灌浆套筒连接主筋的盒子,以形成预留凹槽;弹线确定两侧钢筋混凝土梁相对预留凹槽贴合位置,使预留凹槽两边完成面保持在同一平面上;(4)在模板内浇筑混凝土:在钢筋及模板验收合格后进行混凝土的浇筑,采用附着式振动器并附振动棒进行振捣,一般混凝土不在下沉,无显著气泡上升,混凝土表面出现薄层水泥浆,并有均匀的外观和平面为止;(5)混凝土养护:当气温较高时,混凝土强度增长满足施工进度要求,采用自然养护;当外界气温不能满足工程进度要求时,则采用蒸汽养护;(6)预制拼装钢筋混凝土梁运输与安装:运输预制构件,将灌浆套筒套进一侧预留凹槽内的主钢筋,并将灌浆套筒放置在该侧预制构件的预留凹槽内,组装相邻预制构件;(7)移动灌浆套筒并灌浆:将灌浆套筒拨移至梁接缝中间,密封灌浆套筒端部,沿着灌浆套筒的进浆孔注浆,当出浆孔有浆体均匀流出时停止注浆;而后在预留凹槽内后填混凝土;后填混凝土为比预制构件的混凝土强度高一级混凝土或高强砂浆或灌浆料封堵;预留凹槽提供灌浆套筒的拨移空间,使灌浆套筒连接主钢筋更加简便快捷。
35.(8)依此循环,将若干条预制构件相互拼接。
36.以上所述,仅是本发明的较佳实施例而已,并非是对本发明作其它形式的限制,任何熟悉本专业的技术人员可能利用上述揭示的技术内容加以变更或改型为等同变化的等效实施例。但是凡是未脱离本发明技术方案内容,依据本发明的技术实质对以上实施例所作的任何简单修改、等同变化与改型,仍属于本发明技术方案的保护范围。