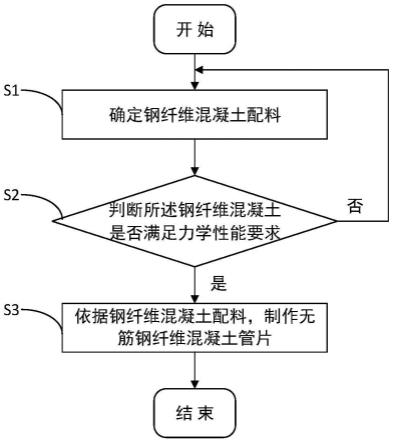
1.本发明属于隧道工程技术领域,涉及适用于盾构或tbm隧道的无筋高掺量钢纤维混凝土管片及制作。
背景技术:2.盾构(或tbm)隧道衬砌多采用普通钢筋混凝土管片,钢筋混凝土管片具有可靠的力学强度,耐腐蚀好,施工制作技术成熟,但在不断的使用过程中也暴露出用钢量大、生产工效低、易出现脆性破坏、局部破损率高等问题。而在钢筋混凝土中掺入钢纤维,可显著改善管片的抗拉性能,增强钢筋混凝土的韧性,弥补普通盾构管片的诸多问题。
3.钢纤维管片的应用可分为两类:第一类,使用钢纤维与钢筋组合共同受力的钢筋-钢纤维混凝土管片;第二类,使用钢纤维完全取代受力钢筋的无筋钢纤维混凝土管片。当隧道所处地层的地质条件好、围岩稳定、水土压力较小时,管片结构内力就会相对较小,例如建设于硬岩地层中的复合盾构隧道和tbm隧道等。在此情况下,即可采用第二类无筋钢纤维混凝土管片。无筋钢纤维混凝土管片不仅可弥补普通管片抗裂性的不足的问题,又可完全省去钢筋笼制作安装的繁琐工序,在简化制备工艺的同时,极大的减少了钢材用量,是钢纤维混凝土管片应用的主要方向。
4.但由于无筋钢纤维混凝土管片未配置受力钢筋,为保证其具备可靠的承载能力,所用钢纤维混凝土需要有较高的开裂后强度,且裂后强度稳定可靠,故无筋钢纤维混凝土管片的钢纤维掺量往往须达到40kg/m3~55kg/m3的水平,而高掺量的钢纤维又会导致混凝土和易性变差及钢纤维分散不均等问题,严重影响了管片规模化生产的质量,具体为:
5.(1)钢纤维掺入混凝土拌合料后,在拌合料中会起到支撑骨架作用,增大拌合料内部摩擦阻力,阻止拌合物的流动;同时,随着掺量的增加,钢纤维较大的比表面积,使得浆体无法较好的填充骨料空隙,并包裹骨料与纤维表面,拌合料的和易性变显著变差。
6.(2)钢纤维是将母材钢丝切断后制成的,其两端带有转折型端勾,其成品往往呈极其散乱蓬松的状态,且纤维之间空隙大、勾连程度高。如果直接运输到生产现场,将导致掺入混凝土的纤维勾连成团,无法有效分散。
技术实现要素:7.本发明的目的旨在克服现有技术的不足,提供一种无筋高掺量钢纤维混凝土管片及制备方法,解决混凝土和易性变差的问题,大幅减少管片破损及微裂缝数量,制备出具有良好抗拉、裂变性能的无筋高掺量钢纤维混凝土管片,满足盾构或tbm隧道需求。
8.首先,本发明提出了一种新的钢纤维混凝土配合比设计方法-比表面积替代法,建立了钢纤维掺量与胶凝材料、粗细骨料用量之间的直接关系。该方法可以保障添加钢纤维后,粗集料之间的砂浆厚度、降低钢纤维的骨架效应和内部摩擦力,从而保障和易性以满足现场搅拌、浇筑、振捣等施工的需求。
9.本发明提供的无筋高掺量钢纤维混凝土管片的制作方法,包括以下步骤:
10.s1、确定钢纤维混凝土配料;该步骤包括以下分步骤:
11.s11根据管片设计抗压强度,确定混凝土配料中水泥、粉煤灰、砂、石子、水和减水剂的基础配合比;
12.s12将钢纤维视为粗骨料,基于粗骨料“表面积”不变的原则,按照设定的钢纤维掺杂比例,利用钢纤维与混凝土中的粗骨料进行部分替换,得到初始钢纤维混凝土配料;
13.s13确定钢纤维替换前后每立方米混凝土配料的质量差;
14.s14依据步骤s13得到的质量差,确定每立方米钢纤维混凝土配料的调整质量,得到最终钢纤维混凝土配料;
15.s2、依据步骤s1得到的钢纤维混凝土配料,制作钢纤维混凝土开口梁,并进行三点弯曲试验,判断所述钢纤维混凝土是否满足力学性能要求;若满足力学性能要求,进入步骤s3,否则返回步骤s1;
16.s3、依据步骤s1得到的钢纤维混凝土配料,制作无筋钢纤维混凝土管片。
17.上述步骤s1的目的在于确定钢纤维混凝土配料,该配料中不仅还有高掺量的钢纤维,还将粗骨料表面积考虑在内,通过配料调整,尽量减少填充间隙,并保证水胶比和砂率等关键参数。
18.步骤s11中,根据管片设计抗压强度,按照常规手段得到混凝土中水泥、粉煤灰、砂、石子、水和减水剂的基础配合比(即混凝土配料),这里指的是重量配比。例如,按照《普通混凝土配合比设计规程》(jgj55)确定混凝土的基础配合比,具体为:水泥377kg/m3、粉煤灰77kg/m3、砂592kg/m3、石子1203kg/m3、水143kg/m3、减水剂7.20kg/m3。这里以石子作为粗骨料。
19.步骤s12中,即按照s
sf
=sz,将钢纤维和石子进行替换,s
sf
表示待替换钢纤维的总表面积,s
sf
=m
sf
*s
sf
,s
sf
定义为单位质量钢纤维的总表面积,单位cm2/g,m
sf
表示待替换钢纤维质量;s
sf
表示每立方米混凝土中待替换的石子的总表面积,sz=
△mz
*sz,sz定义为单位质量石子的总表面积,单位cm2/g,
△mz
表示被替换石子质量。
20.根据钢纤维和石子的比表面积之比可以确定钢纤维替换石子的比例,由此定义钢纤维替换比
21.则,
22.式中,m
z1
为替换前每立方米混凝土的石子用量;m
z2
为替换后每立方米混凝土的石子用量;m
sf
为每立方米混凝土钢纤维掺量。
23.由此可以确定初始钢纤维混凝土配料,即水泥、粉煤灰、砂、石子、水、减水剂和钢纤维的配合比。
24.步骤s13中,采用钢纤维对石子进行替换后,会引起体积的减小和混凝土总质量的减少,为了保持体积不变,需要再添加混凝土;钢纤维替换后每立方米钢纤维混凝土中混凝土配料需增加的总质量按照以下公式计算得到:
[0025][0026]
其中:v1表示单位体积,取1m3;m1为钢纤维替换前每立方米混凝土配料的总质量;m2为钢纤维替换后每立方米钢纤维混凝土配料的总质量(含钢纤维),
[0027]
步骤s14中,根据钢纤维替换前后每立方米混凝土配料的质量差,将每立方米混凝土减少的总质量,按照各组分比例不变的原则,调整增加至各个组分中,公式为:
[0028][0029][0030]
其中:m
i1
和m
i2
分别为调整前后,每立方米混凝土各个组分(除石子和钢纤维)的质量;mz为调后石子的组分质量。
[0031]
按照每立方米钢纤维掺杂量为40~55kg/m3,通过上述步骤s11-s14,可以确定钢纤维混凝土的配比组分为:钢纤维40-55kg/m3、水泥400-409kg/m3、粉煤灰82-83kg/m3、砂628-642kg/m3、石子1117-1084kg/m3、水152-155kg/m3、减水剂7.64-7.81kg/m3。
[0032]
钢纤维混凝土需要满足一定的力学性能,才能确保管片所用材料具备较好的裂后力学性能,用于无筋管片制备。为此,本发明进一步提供了一种对钢纤维混凝土力学性能的测试方法(即步骤s2),通过钢纤维混凝土的开口梁弯曲试验,测定钢纤维混凝土在外荷载作用下各个阶段的强度,并通过强度比值来判断钢纤维混凝土的材料力学性能是否满足用于无筋管片制备要求。
[0033]
上述步骤s2包括以下分步骤:
[0034]
s21配制钢纤维混凝土;
[0035]
s22制作钢纤维混凝土开口梁;
[0036]
s23对钢纤维混凝土开口梁进行三点弯曲试验,获取开口梁弹性范围内的最大强度(即比例极限强度)f
lop
、开口梁开裂后开口位移为0.5mm对应的第一残余强度f
r1
和开口位移为2.5mm对应的第二残余强度f
r3
;
[0037]
s24判断钢纤维混凝土是否满足以下力学性能要求,若满足以下力学性能要求,进入步骤3,否则返回步骤s1:
[0038]
(1)f
r1
/f
lop
≥1.0;
[0039]
(2)f
r3
/f
r1
≥1.0。
[0040]
上述步骤s21包括以下分步骤:
[0041]
s211按钢纤维混凝土配料,量取砂和石子,投入输送皮带,运输至搅拌装置;
[0042]
s212按钢纤维混凝土配料,量取钢纤维,通过震动加料器与输送皮带上的砂和石子同时加入到搅拌装置中;
[0043]
s213将运输至搅拌装置内的钢纤维、砂和石子进行干拌,干拌时间不少于30秒,再按顺序投入水泥、粉煤灰、水和减水剂,继续搅拌至少90秒,得到钢纤维混凝土。
[0044]
步骤s211中,所使用的砂为干净中砂,细度模数大于2.5,含泥量小于3%。所使用的石子为最大粒径不大于25mm的山碎石,级配连续,含泥量小于1%。
[0045]
步骤s212中,所使用的钢纤维应同时满足下述要求:
[0046]
条件1,所述钢纤维选用高强冷拉切断钢丝纤维,其抗拉强度不小于1000mpa;
[0047]
条件2,所述钢纤维的中部为平直段,其两端双折呈弯钩形;
[0048]
条件3,所述钢纤维两端之间相对长度为50-70mm,长径比应为55-75;
[0049]
条件4,所述钢纤维采用磁化排布工艺进行生产和包装。
[0050]
步骤s213中,干拌时间和继续搅拌时间的总搅拌时间控制在120~180秒之间。
[0051]
使用的水泥选用质量符合gb175规定的p
·
o52.5级低碱硅酸盐水泥或低碱普通硅酸盐水泥(碱含量≤0.6%),并控制水泥中铝酸三钙含量低于8%。粉煤灰选用符合gb1596标准的i级粉煤灰。减水剂选用低氯、低碱高效减水剂,例如聚羧酸减水剂,密胺系减水剂等。
[0052]
上述步骤s22中,本步骤中使用配制的钢纤维混凝土浇筑成150mm
×
150mm
×
550mm的小梁,并在成型试件的侧面做割缝处理制成开口梁,割缝深度25mm
±
1mm、长度为150mm,宽度为20~30mm。
[0053]
上述步骤s23中,所述开口梁弹性范围内的最大强度为试验曲线呈线性关系的区段内最大外荷载f
lop
所求得的强度;所述开口梁开裂后的残余强度为试验曲线中开口位移为0.5mm和2.5mm对应外荷载f
0.5
和f
2.5
所求得的强度,上述强度均可根据对应的试验外荷载按照以下公式计算得到:
[0054][0055]
式中,l表示三点弯曲试验中位于开口梁下方两个支座之间的跨距,b表示开口梁截面高度,h
sp
表示开口梁开裂后裂缝顶到开口梁顶面的高度。
[0056]
最后,本发明还提供了使用满足力学性能要求的无筋高掺量钢纤维混凝土制作管片的步骤,所制备的管片不仅可以改善管片的抗拉、抗裂性能,减少用钢量,简化制备工艺,还着重解决了高掺量钢纤维混凝土管片制备过程中,钢纤维在混凝土中分散不均的问题,可用于管片的规模化批量生产。
[0057]
上述步骤s3包括以下分步骤:
[0058]
s31配制钢纤维混凝土;
[0059]
s32将配制的钢纤维混凝土注入管片模具,当从下料口出现下料时,开启位于模具下方的振动台,对模具中的钢纤维混凝土进行振捣,直至钢纤维在混凝土中分散均匀;
[0060]
s33振捣结束后,所得到的钢纤维混凝土管片还需经抹面、蒸汽养护、脱模、二次水养等工序,得到无筋钢纤维混凝土管片。
[0061]
上述步骤s31与前面步骤s21相同,这里不再详细解释。
[0062]
上述步骤s32中,管片模具下料口位于成型管片拱背中央,使得钢纤维混凝土在下料和振动中向两侧自然流动。在下料口取样测量钢纤维混凝土坍落度在70-90mm之间,流动性良好。振捣频率12000-15000rpm,振动幅度2mm以下,振动时间为120~150秒。在振捣完成后的模具中取样,采用水洗法测量钢纤维混凝土的分散性。
[0063]
上述步骤s33,振捣完成后的钢纤维混凝土管片还需经历抹面、蒸汽养护、脱模、二次水养等工序,其工艺与普通混凝土管片相同。脱模后的管片模具经清洗后,返回步骤s31继续使用。
[0064]
本发明进一步提供了上述方法制作的无筋高掺量钢纤维混凝土管片。
[0065]
与现有技术相比,本发明提供的无筋高掺量钢纤维混凝土管片的制作方法具有以下有益效果:
[0066]
(1)本发明方法制作的无筋高掺量钢纤维混凝土管片可大幅减少管片破损及管片微裂缝数量,且具有良好的抗拉、抗裂性能。
[0067]
(2)本发明方法制作的无筋高掺量钢纤维混凝土管片具有较高的开裂后残余强度,且残余强度在较大开口位移范围(0.5-2.5mm)内稳定可靠,可用于硬岩地层中的复合盾构隧道和tbm隧道。
[0068]
(3)本发明方法制作的无筋高掺量钢纤维混凝土管片完全取消了钢筋笼制作安装工序,简化了制备工艺,减少了钢材用量。
[0069]
(4)本发明方法通过调整配料添加顺序,结合振捣操作解决了高掺量钢纤维混凝土和易性差和钢纤维分散不均的问题,适合管片的规模化生产。
附图说明
[0070]
图1为本发明无筋高掺量钢纤维混凝土管片的制作方法流程示意图;
[0071]
图2为本发明无筋高掺量钢纤维混凝土管片的制作方法中确定钢纤维混凝土配料流程示意图;
[0072]
图3为本发明无筋高掺量钢纤维混凝土管片的制作方法中力学性能要求判断流程示意图;
[0073]
图4为钢纤维形状示意图;
[0074]
图5为高掺量钢纤维混凝土开口梁三点弯曲试验获取的强度指标;其中,sf40表示钢纤维掺量为40kg/m3,sf45表示钢纤维掺量为45kg/m3,sf50表示钢纤维掺量为50kg/m3,sf55表示钢纤维掺量为55kg/m3;钢纤维掺量为45kg/m3的高掺量钢纤维混凝土制作方法见实施例1所示,其他钢纤维掺量的高掺量钢纤维混凝土制作方法与实施例1给出的方法相似,只要将相应的高纤维掺量替换即可。
具体实施方式
[0075]
下面结合附图对本发明各实施例的技术方案进行清楚、完整的描述,显然,所描述实施例仅仅是本发明的一部分实施例,而不是全部的实施例。基于本发明中的实施例,本领域普通技术人员在没有做出创造性劳动的前提下所得到的所有其它实施例,都属于本发明。
[0076]
实施例1
[0077]
本实施例提供的无筋高掺量钢纤维混凝土管片的制作方法,如图1-图3所示,其包括以下步骤:
[0078]
s1、确定钢纤维混凝土配料;该步骤包括以下分步骤:
[0079]
s11根据管片设计抗压强度,确定混凝土配料中水泥、粉煤灰、砂、石子、水和减水剂的基础配合比。
[0080]
本步骤中,根据管片设计抗压强度,按照《普通混凝土配合比设计规程》(jgj55)确定混凝土的基础配合比,具体为:水泥377kg/m3、粉煤灰77kg/m3、砂592kg/m3、石子1203kg/m3、水143kg/m3、减水剂7.20kg/m3,总质量为2399.2kg/m3。这里以石子作为粗骨料。
[0081]
s12将钢纤维视为粗骨料,基于粗骨料“表面积”不变的原则,按照设定的钢纤维掺杂比例,利用钢纤维与混凝土中的粗骨料进行部分替换,得到初始钢纤维混凝土配料。
[0082]
本步骤中,即按照s
sf
=sz,将钢纤维和石子进行替换,s
sf
表示待替换钢纤维的总表面积,s
sf
=m
sf
*s
sf
,s
sf
定义为单位质量钢纤维的总表面积,单位cm2/g,m
sf
表示待替换钢纤维质量;s
sf
表示每立方米混凝土中待替换的石子的总表面积,sz=
△mz
*sz,sz定义为单位质量石子的总表面积,单位cm2/g,
△mz
表示被替换石子质量。
[0083]
本实施例中,所选钢纤维和集配石子的比表面积分别为:s
sf
=6.79cm3/g和sz=1.69cm3/g,由此定义钢纤维替换比
[0084]
则,
[0085]
式中,m
z1
为替换前每立方米混凝土的石子用量;m
z2
为替换后每立方米混凝土的石子用量;m
sf
为每立方米混凝土钢纤维掺量。
[0086]
由此可以确定初始钢纤维混凝土配料,即水泥、粉煤灰、砂、石子、水、减水剂和钢纤维的配合比,即:钢纤维45kg/m3、水泥377kg/m3、粉煤灰77kg/m3、砂592kg/m3、石子1023kg/m3、水143kg/m3、减水剂7.20kg/m3。
[0087]
因此,钢纤维替换后每立方米钢纤维混凝土配料的总质量m2为:
[0088]
m2=2399.2-(4-1)
×
45=2264.2kg/m3。
[0089]
s13确定钢纤维替换前后每立方米混凝土配料的质量差。
[0090]
步骤s13中,采用钢纤维对石子进行替换后,会引起体积的减小和混凝土总质量的减少,为了保持体积不变,需要再添加混凝土;钢纤维替换后每立方米钢纤维混凝土中混凝土配料需增加的总质量按照以下公式计算得到:
[0091][0092]
其中:v1表示单位体积,取1m3;m1为钢纤维替换前每立方米混凝土配料的总质量;m2为钢纤维替换后每立方米钢纤维混凝土配料的总质量(含钢纤维)。
[0093]
s14依据步骤s3得到的质量差,确定每立方米钢纤维混凝土配料的调整质量,得到最终钢纤维混凝土配料。
[0094]
本步骤中,根据钢纤维替换前后每立方米混凝土配料的质量差,将每立方米混凝土减少的总质量,按照各组分比例不变的原则,调整增加至各个组分中,公式为:
[0095][0096][0097]
其中:m
i1
和m
i2
分别为调整前后,每立方米混凝土各个组分(除石子和钢纤维)的质量;mz为调后石子的组分质量。
[0098]
因此,各组分调整后的最终钢纤维混凝土的配比为:钢纤维45kg/m3、水泥403kg/m3、粉煤灰82kg/m3、砂633kg/m3、石子1106kg/m3、水153kg/m3、减水剂7.70kg/m3。
[0099]
s2、依据步骤s1得到的钢纤维混凝土配料,制作钢纤维混凝土开口梁,并进行三点弯曲试验,判断所述钢纤维混凝土是否满足力学性能要求;若满足力学性能要求,进入步骤s3,否则返回步骤s1。
[0100]
本步骤包括以下分步骤:
[0101]
s21配制钢纤维混凝土,包括以下分步骤:
[0102]
s211按钢纤维混凝土配料,量取砂和石子,投入输送皮带,运输至搅拌装置。
[0103]
本实施例中,所使用的砂为干净中砂,细度模数大于2.5,含泥量小于3%。所使用的石子粒径为5-25mm的山碎石,级配连续,含泥量0.76%。
[0104]
这里的搅拌装置可以为常规的较大搅拌设备,例如搅拌楼。
[0105]
s212按钢纤维混凝土配料,量取钢纤维,通过震动加料器与输送皮带上的砂和石子同时加入到搅拌装置中。
[0106]
本实施例中,所使用的钢纤维为高强冷拉切断钢丝纤维,抗拉强度为1500mpa。钢纤维的形状如图4,两端之间相对长度为50mm,长径比应为67,钢纤维的中部为平直段,其两端双折呈弯钩形。
[0107]
本实施例使用的钢纤维采用常规磁化排布工艺进行生产和包装。
[0108]
s213将运输至搅拌装置内的钢纤维、砂和石子进行30秒干拌,再按顺序投入水泥、粉煤灰、水和减水剂,继续搅拌90秒,得到钢纤维混凝土。
[0109]
本实施例使用的水泥选用质量符合gb175规定的p
·
o52.5级的低碱普通硅酸盐水泥。粉煤灰选用符合gb1596标准的i级粉煤灰。减水剂使用的是聚羧酸减水剂,减水率25%。
[0110]
s22制作钢纤维混凝土开口梁。
[0111]
使用配制的钢纤维混凝土浇筑成150mm
×
150mm
×
550mm的小梁,并在成型试件的侧面做割缝处理制成开口梁,割缝深度25mm、长度为150mm,宽度为20mm。
[0112]
s23对钢纤维混凝土开口梁进行三点弯曲试验,获取开口梁弹性范围内的最大强度(即比例极限强度)f
lop
、开口梁开裂后开口位移为0.5mm对应的第一残余强度f
r1
和开口位移为2.5mm对应的第二残余强度f
r3
。
[0113]
三点弯曲试验中得到的试验荷载-开口位移关系曲线如图5所示。
[0114]
开口梁弹性范围内的最大强度为试验曲线呈线性关系的区段内最大外荷载f
lop
所求得的强度;所述开口梁开裂后的残余强度为试验曲线中开口位移为0.5mm和2.5mm对应外荷载f
0.5
和f
2.5
所求得的强度,上述强度均可根据对应的试验外荷载按照以下公式计算得到:
[0115][0116]
式中,l表示三点弯曲试验中位于开口梁下方两个支座之间的跨距,b表示开口梁截面高度,h
sp
表示开口梁开裂后裂缝顶到开口梁顶面的高度。
[0117]
本实施例中,当钢纤维掺杂量为45kg/m3时,f
lop
=5.66mpa、f
r1
=6.03mpa、f
r3
=6.53mpa。
[0118]
s24判断钢纤维混凝土是否满足以下力学性能要求,若满足以下力学性能要求,进入步骤3,否则返回步骤s1:
[0119]
(1)f
r1
/f
lop
=1.07》1.0,即钢纤维混凝土开裂后强度大于开裂前线性强度峰值;
[0120]
(2)f
r3
/f
r1
=1.08》1.0,即钢纤维混凝土开口位移2.5mm时的残余强度大于开口位移0.5mm时的残余强度,裂后强度稳定。
[0121]
可判断该钢纤维混凝土可用于制作无筋管片。
[0122]
s3、依据步骤s1得到的钢纤维混凝土配料,制作无筋钢纤维混凝土管片。
[0123]
本实施例中采用前述配合比制作的钢纤维混凝土进行无筋钢纤维混凝土管片的规模化生产,为某地铁的tbm区间生产无筋高掺量钢纤维混凝土管片187环(使用钢纤维混凝土1506m3)。
[0124]
本步骤包括以下分步骤:
[0125]
s31配制钢纤维混凝土,包括以下分步骤:
[0126]
本步骤与前面步骤s21相同,这里不再详细解释。
[0127]
s32将配制的钢纤维混凝土注入管片模具,当从下料口出现下料时,开启位于模具下方的振动台,对模具中的钢纤维混凝土进行振捣。
[0128]
本实施例中,将搅拌完成的钢纤维混凝土以分层下料的方式注入专用管片模具,下料后开启振动台。管片模具下料口位于成型管片拱背中央,使得钢纤维混凝土在下料和振动中向两侧自然流动。
[0129]
在下料口取样测量钢纤维混凝土坍落度在70-90mm之间,流动性良好。振捣采用高频低幅震动,振捣频率14500rpm,振动幅度2mm以下,振动时间为120秒。在振捣完成后的模具中取样,采用水洗法测量钢纤维混凝土的分散性,结果显示所有样品钢纤维含量均在42-46kg/m3之间,表明分散性良好。
[0130]
s33振捣结束后,所得到的钢纤维混凝土管片还需经抹面、蒸汽养护、脱模、二次水养等工序,得到无筋钢纤维混凝土管片。
[0131]
本实施例中,振捣完成后的钢纤维混凝土管片还需经历抹面、蒸汽养护、脱模、二次水养等工序,其工艺与普通混凝土管片相同。脱模后的管片模具经清洗后,返回步骤s31继续使用。
[0132]
对比例
[0133]
为证明本发明所述为无筋高掺量钢纤维混凝土管片的质量及性能关键,将试生产中不同配比及工艺生产管片做如下对比:
[0134]
(1)按照本发明实施例所述配比组分(钢纤维45kg/m3、水泥403kg/m3、粉煤灰82kg/m3、砂633kg/m3、石子1106kg/m3、水153kg/m3、减水剂7.70kg/m3)拌合的高掺量钢纤维混凝土的塌落度可稳定在7-9cm,具有较好的和易性。
[0135]
按照现行标准《钢纤维混凝土》(jg/t472)中的假定质量法计算高掺量钢纤维混凝土配比组分为:钢纤维45kg/m3、水泥376kg/m3、粉煤灰77kg/m3、砂591kg/m3、石子1199kg/m3、水143kg/m3、减水剂7.18kg/m3。按照此配比进行拌合,塌落度小于5cm,甚至出现塌落度为0的现象。
[0136]
(2)按照本发明实施例所述管片制备方法,完成s3步骤后,在振捣完成后的钢纤维混凝土管片的拱顶和两侧取3个150
×
150
×
150mm的式样进行水洗法检测,3个样本中钢纤维体积率与配合比要求的钢纤维掺量的误差均不超过
±
5%。
[0137]
本领域的普通技术人员将会意识到,这里所述的实施例是为了帮助读者理解本发明的原理,应被理解为本发明的保护范围并不局限于这样的特别陈述和实施例。本领域的普通技术人员可以根据本发明公开的这些技术启示做出各种不脱离本发明实质的其它各种具体变形和组合,这些变形和组合仍然在本发明的保护范围内。