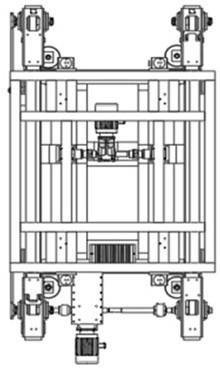
1.本发明属于碳化硅坯体成型技术领域,具体是一种新材料制品的生产方法。
背景技术:2.碳化硅俗称金刚砂,是硅与碳相键结而成的陶瓷状化合物;碳化硅在大自然以莫桑石这种罕见的矿物的形式存在,碳化硅可用于需要高耐用度的材料中,如汽车刹车片、离合器和防弹背心等;在发光二极管、早期的无线电探测器之类的电子器件制造中也有使用,通过lely法能生长出大块的碳化硅单晶,人造莫桑石就是通过切割由lely法制备的大块碳化硅单晶来获得的。
3.传统反应烧结的碳化硅产品的碳化硅坯体成型采用真空螺旋挤出方法和石膏模具注浆成型方法这两种方式,其中,真空螺旋挤出成型方法产生的碳化硅产品坯体致密度小于2.1g/cm3,成型后产品几何尺寸不稳定,碳化硅坯体转化率小于80%,形成碳化硅成品后sic含量小于88%;石膏模具注浆成型方法生成的碳化硅产品坯体密度小于1.8g/cm3,坯体形成周期长,劳动密集度大,碳化硅坯体转化率小于75%,形成碳化硅成品后sic含量小于85%,不能很好的满足市场对高密度、高碳化硅成品转化率的碳化硅坯体要求。
技术实现要素:4.解决的技术问题:针对现有技术的不足,本发明提供了一种新材料制品的生产方法,尤其对一种高体密度、高碳化硅成品转化率、高强度的碳化硅坯体成型方法,解决了背景技术中提到的问题。
5.技术方案:为实现以上目的,本发明通过以下技术方案予以实现:一种新材料制品的生产方法,包括如下具体步骤:s1、液压活塞挤出预成型,其中,碳化硅坯体的液压活塞挤出预成型中,需要使用液压活塞挤出模块,而后将挤出的坯体送入坯体内支撑模具中,最后使用三维转运模块,将坯体内支撑模具送入碳化硅预成型干燥系统中,得到碳化硅预成型坯体;s2、冷等静压二次成型;其中,碳化硅预成型坯体的冷等静压二次成型中,将经过s1处理后的坯体送入等静压坯体外隔离模块中,使其与冷等静压模块中介质隔离,最后使用内支撑模具脱模模块将坯体与坯体内支撑模具分离,送入坯体二次干燥系统二次脱水成型。
6.优选的,在所述s1中,所述碳化硅坯体挤出预成型中的液压活塞挤出模块用于将造粒后碳化硅原料通过其内部的造粒机构和成型模具生产出成型的碳化硅坯体;其中,液压活塞挤出模块包括粉料造粒机构、碳化硅坯体成型模具以及真空系统;
其中,粉料造粒机构安装在液压活塞挤出装备内部;碳化硅坯体成型模具设置在液压活塞挤出装备下端出料口处,真空系统设置在液压活塞挤出装备上端进料口处。
7.优选的,在所述s1中,所述碳化硅坯体挤出预成型中的坯体内支撑模具安装在所述液压活塞挤出模块的出料端,用于将成型后的碳化硅坯体支撑和固定。
8.优选的,在所述s1中,所述碳化硅坯体挤出预成型中的三维转运模块用于将预成型好的碳化硅坯体连同所述坯体内支撑模具输送至碳化硅预成型干燥系统。
9.优选的,在所述s1中,所述碳化硅坯体挤出预成型中的碳化硅预成型干燥系统用于将所述坯体内支撑模具支撑的碳化硅坯体干燥;具体为,将碳化硅坯体码放于碳化硅预成型干燥系统中的储坯架上,且预成型干燥系统中设置多段温控单元,用于控制所述预成型干燥系统中预成型坯体内水分均匀性和水分含量,碳化硅预成型干燥系统将进入其内部的预成型后的碳化硅坯体按照设定好的干燥曲线将坯体内水分进行排除和均化。
10.优选的,在所述s2中,所述碳化硅坯体冷等静压二次成型中的冷等静压模块用于将s1中所述液压挤出预成型坯体进行二次颗粒重塑,并对预成型坯体缺陷进行重新修复。
11.优选的,在所述s2中,所述碳化硅冷等静压坯体外部隔离模块用于将所述碳化硅预成型坯体包裹,将其和所述冷等静压模块内的等静压介质隔离。
12.优选的,在所述s2中,所述内支撑模具脱模模块用于将s1中预成型坯体从内支撑模具中脱离,且内支撑模具脱模模块表面涂设防渗透涂层;上述内支撑模具脱模模具是在坯管由冷等静压模块工序后将坯体内支撑模具脱除;坯体二次干燥系统是在坯管去除坯体内支撑模具工序后实施;坯管二次干燥系统是在预成型干燥系统工序之后进行,将经过预成型干燥系统后残留在坯管内水分进行进一步排除。
13.优选的,在所述s2中,所述坯体二次干燥系统用于将经过s1得到的碳化硅预成型坯体进行二次脱水。
14.有益效果:本发明采用液压活塞挤出预成型+冷等静压二次成型的生产工艺,通过这种结合成型方式可以得到一种高强度、小收缩、几何尺寸稳定的碳化硅坯体,活塞挤出预成型后坯体经过一级干燥系统将预成型后的坯体水分降到一定比例,坯体通过冷等静压进行二次成型,使得坯体强度达到更高水平,冷等静压后坯体进行二次干燥,将冷等静压后的坯体水分降低到结晶水状态,将坯体通过预成型+冷等静压工艺将碳化硅坯体强度达到一个高强度等级,使得经过后期真空反应烧结后形成的产品密度大于传统的要求。
15.附图说明
16.图1是本发明的整体流程示意图;图2是本发明的液压活塞挤出模块示意图;图3是本发明的三维转运模块示意图;图4是本发明的碳化硅预成型干燥系统中储坯架示意图;图5是本发明的冷等静压模块示意图;
图6是本发明的内支撑模具脱模模块示意图。
17.具体实施方式
18.本技术实施例通过提供一种新材料制品的生产方法,采用液压活塞挤出预成型+冷等静压二次成型的生产方法,解决现有技术中的问题。
19.本技术实施例中的技术方案为解决上述问题,总体思路如下:实施例1:本实施例给出液压活塞挤出预成型的具体方式,s1、液压活塞挤出预成型,其中,碳化硅坯体的液压活塞挤出预成型中,需要使用液压活塞挤出模块,而后将挤出的坯体送入坯体内支撑模具中,最后使用三维转运模块,将坯体内支撑模具送入碳化硅预成型干燥系统中,得到碳化硅预成型坯体。
20.在一些示例中,在s1中,碳化硅坯体挤出预成型中的液压活塞挤出模块用于将造粒后碳化硅原料通过其内部的造粒机构和成型模具生产出成型的碳化硅坯体;其中,液压活塞挤出模块中配置真空单元,且真空单元用于排除碳化硅坯体预成型坯体内的空气。
21.具体的,液压活塞挤出模块包括粉料造粒机构、碳化硅坯体成型模具以及真空系统;其中,粉料造粒机构安装在液压活塞挤出装备内部;碳化硅坯体成型模具设置在液压活塞挤出装备下端出料口处,真空系统设置在液压活塞挤出装备上端进料口处。
22.在s1中,碳化硅坯体挤出预成型中的坯体内支撑模具安装在液压活塞挤出模块的出料端,用于将成型后的碳化硅坯体支撑和固定,坯体内支撑模具安装在碳化硅坯体成型模具底端,负责支撑碳化硅坯体。
23.在s1中,碳化硅坯体挤出预成型中的三维转运模块用于将预成型好的碳化硅坯体连同坯体内支撑模具输送至碳化硅预成型干燥系统。
24.在s1中,碳化硅坯体挤出预成型中的碳化硅预成型干燥系统用于将坯体内支撑模具支撑的碳化硅坯体干燥;具体为,将碳化硅坯体码放于碳化硅预成型干燥系统中的储坯架上,且预成型干燥系统中设置多段温控单元,用于控制预成型干燥系统中预成型坯体内水分均匀性和水分含量。
25.实施例2:以实施例1为基础,本实施例给出冷等静压二次成型的具体方式,s2、冷等静压二次成型;其中,碳化硅预成型坯体的冷等静压二次成型中,将经过s1处理后的坯体送入等静压坯体外隔离模块中,使其与冷等静压模块中介质隔离,最后使用内支撑模具脱模模块将坯体与坯体内支撑模具分离,送入坯体二次干燥系统二次脱水成型。
26.在一些示例中,在s2中,碳化硅坯体冷等静压二次成型中的冷等静压模块用于将s1中液压挤出预成型坯体进行二次颗粒重塑,并对预成型坯体缺陷进行重新修复。
27.在s2中,碳化硅冷等静压坯体外部隔离模块用于将碳化硅预成型坯体包裹,将其
和冷等静压模块内的等静压介质隔离。
28.在s2中,内支撑模具脱模模块用于将s1中预成型坯体从内支撑模具中脱离,且内支撑模具脱模模块表面涂设防渗透涂层。
29.在s2中,坯体二次干燥系统用于将经过s1得到的碳化硅预成型坯体进行二次脱水。
30.上述内支撑模具脱模模具是在坯管由冷等静压模块工序后将坯体内支撑模具脱除;坯体二次干燥系统是在坯管去除坯体内支撑模具工序后实施;坯管二次干燥系统是在预成型干燥系统工序之后进行,将经过预成型干燥系统后残留在坯管内水分进行进一步排除。
31.实施本发明后得到的坯体强度高、收缩小、几何尺寸稳定、成品转化率高、成品碳化硅含量高、成品抗折强度高。
32.本发明的新型碳化硅坯体成型方式不但可以提高规则碳化硅坯体成型效率,而且将碳化硅坯体密度达到2.7g/cm3,抗折强度达到40mpa以上,碳化硅坯体转化成品率到达95%以上,碳化硅成品抗折强度达到130mpa以上,碳化硅成品净含sic比例高到95%以上,碳化硅成品体密度大于3.15g/cm3,碳化硅成品几何尺寸变形量满足0.1%范围内的产品比例达到86%以上。
33.通过采用上述技术方案:采用液压活塞挤出预成型+冷等静压二次成型的生产工艺,通过这种结合成型方式可以得到一种高强度、小收缩、几何尺寸稳定的碳化硅坯体,活塞挤出预成型后坯体经过一级干燥系统将预成型后的坯体水分降到一定比例,坯体通过冷等静压进行二次成型,使得坯体强度达到更高水平,冷等静压后坯体进行二次干燥,将冷等静压后的坯体水分降低到结晶水状态,将坯体通过预成型+冷等静压工艺将碳化硅坯体强度达到一个高强度等级,使得经过后期真空反应烧结后形成产品密度大于3.15g/cm3要求。
34.最后应说明的是:显然,上述实施例仅仅是为清楚地说明本发明所作的举例,而并非对实施方式的限定。对于所属领域的普通技术人员来说,在上述说明的基础上还可以做出其它不同形式的变化或变动。这里无需也无法对所有的实施方式予以穷举。而由此所引申出的显而易见的变化或变动仍处于本发明的保护范围之中。