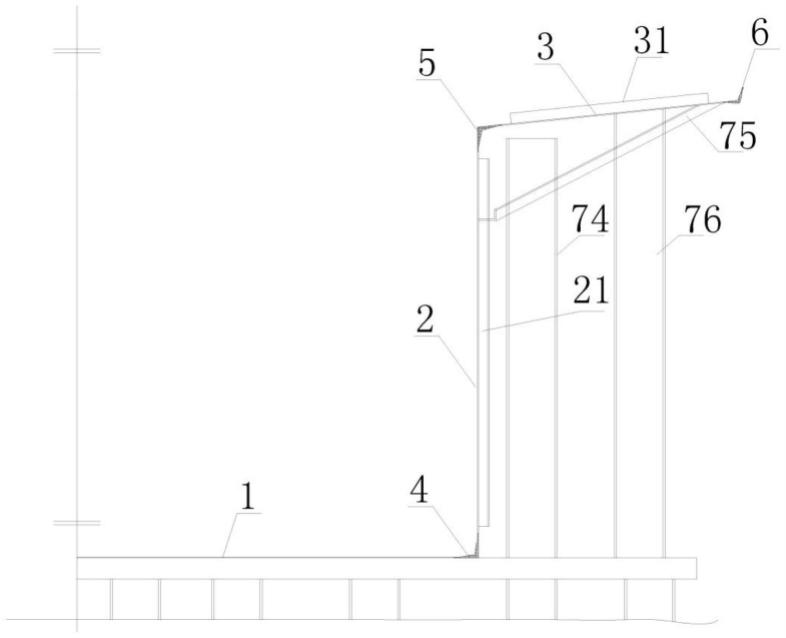
1.本发明属于土建施工技术领域,尤其涉及一种钢衬里底板及截锥体模块化结构及其施工方法。
背景技术:2.我国核电已进入到安全高效发展时期,随着市场化进程的推进,核电业主对缩短建造工期,降低工程造价和提高工程质量越来越提出更高的目标要求。模块化设计与建造技术是在国内外核电建设中被实践所证明,是减少现场施工量、降低安全隐患、缩短建造工期和降低工程造价的有效方式,同时也是我国目前解决核电安全高效批量建设与资源短缺、质量安全之间矛盾的有效措施之一。
3.模块化建造技术从根本上改变了传统的核电建造模式,由过去分散的劳动密集型逐步转向工厂内集约型预制模式。它对传统施工理念大量引人平行作业,依靠先进的设计、制造和建造技术,将土建、安装、调试等工序进行深度交叉,对核电建设项目的工期、造价、质量和安全文明施工均带来巨大的影响。
4.核岛安全壳钢衬里是核岛反应堆厂房的密封性内衬金属结构,其主要功能是防止事故状态下放射性物质外泄,是反应堆厂房的重要安全防护屏障之一,属于核质保一级、核安全二级设备。随着我国核电建设步伐的加快和建造要求的提高,传统的施工工艺已难以满足现代核电建设的需要,开发新的、更高效的核电站钢衬里施工工艺,以满足“安全、优质、高效”的核电站建设要求,已成为核电站核岛土建承包商急需解决的重要难题之一。
5.华龙一号核电站安全壳钢衬里结构上分为底板、截锥体、筒体、钢衬里附件 (贯穿件套筒、闸门套筒及锚固件)、牛腿和穹顶等几部分。其中底板及截锥体由材质为p265gh、厚度为6mm的钢板焊接而成,传统技术是车间制作板,现场实体按工序拼装焊接,工序时间长。
6.作为国产三代大型压水堆先进堆型,华龙一号核电站的建造质量和施工效率受到各方面关注,而安全壳钢衬里作为核二级设备,其施工质量和效率须得到充分的提升。为了提高建造效率,华龙一号核电站安全壳钢衬里底板及截锥体部分拟采用模块化整体预制及吊装安装施工。模块化施工,底板现场安装构件尺寸大,底板焊缝背面要求磨平后整体模块化吊装就位,因此原型钢龙骨做垫板的焊接工艺满足不了模块化施工要求。
7.依赖于大量人力投入“人海战术”的生产方式已经越来越不能满足目前核工程建造的需求,通过模块化技术及有效的工艺措施可以有效的解决过于依赖劳动力的问题,是提高效率、降低人工成本的最有效方法。
8.为了解决施工工期问题,必须研究开发出新的施工及高效自动焊焊接工艺来,进一步提高施工及焊接施工效率,保证焊接质量,降低人工成本及施工周期,为后续施工提供保障。
技术实现要素:9.本发明提供一种钢衬里底板及截锥体模块化结构及其施工方法,以克服现有技术
的缺陷。
10.为实现上述目的,本发明提供一种钢衬里底板及截锥体模块化结构,具有这样的特征:模块化结构是由中心区圆形底板、侧面壁板和斜段环板组成的薄板盆状结构;所述中心区圆形底板为水平设置的圆形结构;所述侧面壁板为侧壁竖直设置的环形结构;所述斜段环板为侧壁沿由下向上方向向外倾斜设置的斜面环形结构;侧面壁板的下端通过第一过渡段与中心区圆形底板周边固定;侧面壁板的上端通过第二过渡段与斜段环板的下端固定;所述中心区圆形底板由若干块底板拼装而成,若干块底板分为长方形底板、梯形底板和带圆弧底板三类;若干长方形底板拼装成矩形,作为中心区圆形底板的中心部分;若干梯形底板拼装在若干长方形底板周围,与若干长方形底板共同拼装成八边形;若干带圆弧底板拼装在若干梯形底板周围,与若干长方形底板和若干梯形底板同拼装成中心区圆形底板;所述侧面壁板由若干块壁板拼装而成;所述斜段环板由若干块斜板拼装而成;斜板的数量与壁板的数量相等并一一对应,斜板下端通过第二过渡段与相应的壁板的上端固定。
11.进一步,本发明提供一种钢衬里底板及截锥体模块化结构,还可以具有这样的特征:其中,所述中心区圆形底板由24块底板拼装而成,分别为8块长方形底板、8块梯形底板和8块带圆弧底板,各块底板通过焊接拼装;所述侧面壁板由12块壁板拼装而成,各壁板之间通过焊接拼装成整体;所述斜段环板由12块斜板拼装而成,各斜板之间通过焊接拼装成整体。
12.进一步,本发明提供一种钢衬里底板及截锥体模块化结构,还可以具有这样的特征:其中,所述侧面壁板的壁板的外侧焊接有环向角钢和竖向角钢;
13.进一步,本发明提供一种钢衬里底板及截锥体模块化结构,还可以具有这样的特征:其中,所述斜段环板的斜板的内侧焊接有径向角钢。
14.进一步,本发明提供一种钢衬里底板及截锥体模块化结构,还可以具有这样的特征:其中,所述斜段环板的上口固定有第三过渡段。
15.本发明还提供一种钢衬里底板及截锥体模块化结构的施工方法,具有这样的特征:
16.第一步、搭建拼装平台;拼装平台包括底部的支撑架与上部的平铺钢板两部分,整体拼装平台呈圆形;拼装平台对应场焊缝位置的平铺钢板之间预留间隙;
17.第二步、制作第一过渡段、第二过渡段和第三过渡段;
18.第三步、制作中心区圆形底板的底板;
19.第四步、制作侧面壁板的壁板;
20.第五步、制作斜段环板的斜板;
21.第六步、按拼装线拼装中心区圆形底板,分24块底板拼装;中心区圆形底板的具体拼装流程为:位于中心的底板吊装就位-位于中心的底板现场组对-配重块及焊接工装设置-位于中心的底板现场焊接-无损检测-余量切割-位于外围的底板就位-位于外围的底板现场组对-配重快及焊接工装设置-位于外围的底板现场焊接-无损检测-整体尺寸检查;
22.第七步:拼装侧面壁板:分12块壁板拼装,每块壁板两端头部位的外侧设有扶壁柱,由扶壁柱调整垂直度及半径,半径、垂直度合格后先焊接11条缝,另1条缝最后焊接,上口预留不小于30mm余量,下料时保证正偏差;现场组对时进行二次切割,以保证整体尺寸符合设计要求;侧面壁板的具体拼装流程为:现场测量放线-设置扶壁柱-吊装就位壁板-调整
定位后安插间隙板、眼镜板、圆锥销-焊纵缝的平台安装-纵缝组对-纵缝焊接、无损检测-环缝组对-环缝焊接、无损检测-切割收缩纵缝余量-收缩纵缝及剩余环缝焊接-连接角钢安装和连接件焊接
‑ꢀ
现场油漆修补-安装上口走道板;
23.第八步:拼装斜段环板:分12块斜板拼装,设置48根斜支撑;斜段环板的具体拼装流程为:现场测量放线-设置斜板支撑柱-吊装就位斜板-调整定位后插间隙板、眼镜板、圆锥销、标高调整板纵缝组对-纵缝焊接、无损检测-环缝组对
‑ꢀ
环缝焊接、无损检测-切割收缩纵缝余量-收缩纵缝及剩余环缝焊接-无损检测-整体尺寸检查。
24.进一步,本发明提供一种钢衬里底板及截锥体模块化结构的施工方法,还可以具有这样的特征:其中,第一步中,搭建拼装平台的具体方法为:
25.s1.1、预制场地清理,根据地形高程选取基准高程,定位放线;
26.s1.2、混凝土基础浇筑及顶面埋件安装;
27.s1.3、支撑柱轴线位置定位放线,测量基础顶面埋件高程,以最高点为基准进行支撑柱安装,支撑柱下端同埋件焊接;
28.s1.4、支撑柱顶面标高及平整度检查;
29.s1.5、标高合格后,支撑柱上架设主梁,主梁同支撑柱顶通过螺栓连接;次梁搭设在主梁上,通过螺栓连接,次梁之间采用角钢连接,顶面高程同次梁高程,采用焊接连接;
30.s1.6、放线、铺平铺钢板:平铺钢板铺设位置放线;铺设平铺钢板,中心区圆形底板的拼缝位置留设150~200mm空隙,平铺钢板上铺一层防火布。
31.进一步,本发明提供一种钢衬里底板及截锥体模块化结构的施工方法,还可以具有这样的特征:其中,第二步中,第一过渡段、第二过渡段和第三过渡段的制作方法均为:领料-放线-切割下料-标识移植-折弯成型-坡口机加工-弯曲成型
‑ꢀ
消应力热处理-拼接坡口加工-拼接坡口检查-拼接组对-焊接-变形矫正-无损检测
‑ꢀ
尺寸检查-编号存放;第一过渡段和第二过渡段的预制安装,采用30mm板折弯需求的折弯机加工,将钢板下料成长条状;用折弯机折弯成l型钢;采用铣床将 l型钢两边铣切出相应的过渡区域,用卷弧设备卷制成相应的弧形,对折弯区进行消应力热处理,通过焊接拼装成一个圆环;根据放线位置进行就位;第三过渡段的预制安装,采用22mm板折弯需求的折弯机加工,将钢板下料成长条状;用折弯机折弯成l型钢;采用铣床将l型钢两边铣切出相应的过渡区域,用卷弧设备卷制成相应的弧形,对折弯区进行消应力热处理,通过焊接拼装成一个圆环;根据放线位置进行就位。
32.进一步,本发明提供一种钢衬里底板及截锥体模块化结构的施工方法,还可以具有这样的特征:其中,第三步中,长方形底板和梯形底板的制作流程为:领料-下料-拼接板组对-焊接-校正-无损检测-二次切割-尺寸检查-编号存放;带圆弧底板的制作流程为:领料-下料-拼接板组对-焊接-校正-无损检测-二次切割-尺寸检查-与第一过渡段组对-焊接-校正-无损检测-尺寸检查-编号存放;带圆弧底板长度上预留不小于25mm余量,每块梯形底板组焊完成后在长度及宽度方向均预留不小于10mm余量,余量端均在靠近外侧侧面壁板方向;
33.第四步中,拼装侧面壁板的壁板的制作方法为:领料-下料-拼接板组对-焊接
ꢀ‑
校正-无损检测-二次切割-尺寸检查-贯穿件和加劲肋位置放线-检查-拼接板在胎模上固定成形-加劲肋角钢与壁板组对-检查-在壁板上压好工字钢梁-加劲肋角钢与壁板焊接-校
正-无损检测-连接件定位-连接件焊接-连接件检查-整体尺寸检查
‑ꢀ
走道平台螺杆焊接及验收-喷砂油漆-编号存放;
34.第五步中,拼装斜段环板的斜板的制作方法为:领料-下料-标识移植-拼接板组对-焊接-校正-无损检测-与第二过渡段组对-焊接-校正-无损检测-尺寸检查-喷砂油漆-编号存放;斜板长度方向各增加不小于30mm余量。
35.进一步,本发明提供一种钢衬里底板及截锥体模块化结构的施工方法,还可以具有这样的特征:其中,中心区圆形底板采用激光智能跟踪mag自动焊接方法和陶质衬垫单面焊双面成形高效焊接工艺;组对焊缝宽度为5~8mm;底板背面采用陶质衬垫作为非永久衬垫使背面焊缝强制成形,实现钢衬里单面焊双面成形焊接施工,陶质衬垫粘贴时保证衬垫中心线与焊缝中心线对齐,并确保铝箔胶带固定牢固;侧面壁板采用激光跟踪mag自动焊接方法,陶质衬垫作为非永久衬垫,焊接时托住焊缝熔敷金属使背面焊缝强制成形,实现焊缝的单面焊双面成形;焊接过程中经过打底、层间清理及盖面三道工序;焊接以两条收缩缝中间的壁板为中心,一半焊缝沿顺时针方向焊接,另一半沿逆时针进行焊接;横缝采用在远离立缝收缩缝的一段开始分段沿顺时针方向进行连续焊接;斜段环板焊接同侧面壁板采用激光跟踪mag自动焊接方法。
36.本发明的有益效果在于:本发明提供一种钢衬里底板及截锥体模块化结构及其施工方法,对钢衬里底板(中心区圆形底板)及截锥体(侧面壁板、斜段环板) 采用整体模块化施工,分型分块进行优化,优化方案减少了焊接工程量,方便现场施工,可以有效节约工期,保证质量及密封性,提高了劳动效率,有利于缩短主关键线路50天,创造经济效益5000万元。具体的:
37.1、基于分型分块进行优化,优化方案减少了焊接工程量,方便现场施工;优化成对称结构,更有利于焊接变形的控制;更有利于机械焊的实施;减少了现场拼接焊缝,加强节点的现场对接焊缝减少了56%;底板拼接焊缝减少了约75m,减少焊缝可提高了底板施工质量,节约了焊工资源,减少了无损检测工程量。
38.2、设计了一种拼装平台,拼装平台包含支撑架与平铺钢板两部分,底部为型钢支架,上部为25mm钢板满铺,整体平台呈圆形,直径为44.2m,现场焊缝位置平台钢板之间预留一定的间隙,便于操作人员从下方贴陶瓷衬垫及焊缝无损检测。拼装平台上表面距地面高度约为1625mm。拼装平台方便人员拼装操作,且保证了整个底板拼装的平整度。
39.3、研发了激光智能跟踪mag自动焊焊接方法,并在核电钢衬里底板模块拼装中应用,底板焊接合格率达100%,且焊接变形满足设计要求,且大大节约了核级焊工资源。
40.4、底板与四周的第一过渡段在预制车间采用埋弧焊焊接成一个整体,避免现场环形焊缝焊条电弧焊,节约了焊工资源。
41.5、底板与四周的第一过渡段焊接成一个整体,第一过渡段的现场拼接焊缝仅8条,减少了10条对接焊缝,更有利于加强节点焊接质量及变形控制。
42.6、基础处理工作量少,支架平台可重复使用,无需重新填土,完工后无需重新再挖土。
附图说明
43.图1是钢衬里底板及截锥体模块化结构的结构示意图;
44.图2是钢衬里底板及截锥体模块化结构和其配套施工工装的局部结构示意图;
45.图3是第一过渡段的结构示意图;
46.图4是第二过渡段的结构示意图;
47.图5是第三过渡段6的结构示意图;
48.图6是模块化结构、拼装平台和配套施工工装的立体结构示意图;
49.图7是模块化结构、拼装平台和配套施工工装的平面结构示意图;
50.图8是中心区圆形底板的各底板的标号示意图;
51.图9是拼缝(焊缝)示意图;
52.图10是中心区圆形底板单元分区示意图。
具体实施方式
53.以下结合附图来说明本发明的具体实施方式。
54.如图1-5所示,本实施例提供一种钢衬里底板及截锥体模块化结构,模块化结构是由中心区圆形底板1、侧面壁板2和斜段环板3组成的薄板盆状结构。
55.中心区圆形底板1为水平设置的圆形结构。侧面壁板2为侧壁竖直设置的环形结构。斜段环板3为侧壁沿由下向上方向向外倾斜设置的斜面环形结构。侧面壁板2的下端通过第一过渡段4与中心区圆形底板1周边固定;侧面壁板2的上端通过第二过渡段5与斜段环板3的下端固定。斜段环板3的上口固定有第三过渡段6,用于连接其他结构。
56.中心区圆形底板1由若干块底板拼装而成,若干块底板分为长方形底板、梯形底板和带圆弧底板三类;若干长方形底板拼装成矩形,作为中心区圆形底板1 的中心部分;若干梯形底板拼装在若干长方形底板周围,与若干长方形底板共同拼装成八边形;若干带圆弧底板拼装在若干梯形底板周围,与若干长方形底板和若干梯形底板同拼装成中心区圆形底板1。侧面壁板2由若干块壁板拼装而成。斜段环板3由若干块斜板拼装而成。斜板的数量与壁板的数量相等并一一对应,斜板下端通过第二过渡段5与相应的壁板的上端固定。
57.具体的,中心区圆形底板1由24块底板拼装而成,分别为8块长方形底板、 8块梯形底板和8块带圆弧底板,各块底板通过焊接拼装。侧面壁板2由12块壁板拼装而成,各壁板之间通过焊接拼装成整体。斜段环板3由12块斜板拼装而成,各斜板之间通过焊接拼装成整体。
58.其中,侧面壁板2的壁板的外侧焊接有环向角钢和竖向角钢21作为加劲肋。斜段环板3的斜板的内侧焊接有径向角钢31。
59.具体的,中心区圆形底板1的底板为6mm厚度p265gh钢板,中心区圆形底板1的直径为39.4m。侧面壁板2的壁板为6mm厚度p265gh钢板,外侧焊接的环向角钢为∠125
×
80
×
10环向角钢、竖向角钢为∠75
×
50
×
8竖向角钢;侧面壁板2的直径为39.4m,高度为3.056m。斜段环板3的斜板为6mm厚度p265gh,斜段环板3的直径从39.4m过渡到43.336m,高差为190mm,宽度为 1850mm。第一过渡段4和第二过渡段5均为30mm厚度的p265gh钢板;第三过渡段6为22mm厚度的p265gh钢板。钢衬里底板及截锥体模块化结构的重量达115t。
60.钢衬里底板及截锥体模块化结构的施工方法包括以下步骤:
61.第一步、搭建拼装平台,如图6和7所示,拼装平台用于钢衬里底板及截锥体模块化结构的拼装搭建;拼装平台包括底部的支撑架与上部的平铺钢板两部分;底部的支撑架为
型钢支架,由h300
×
300
×
10
×
15高1150支撑柱71、hw250
ꢀ×
250
×9×
14主梁72、hw200
×
200
×8×
12次梁73及连接支撑角钢l100
×
10 构成;上部的平铺钢板25mm;整体拼装平台呈圆形,直径为44.2m,上表面距地面高度约为1625mm;拼装平台对应场焊缝位置的平铺钢板之间预留间隙,以便于操作人员从下方贴陶瓷衬垫及焊缝无损检测。
62.搭建拼装平台的具体方法为:
63.s1.1、预制场地清理,根据地形高程选取基准高程,定位放线;
64.s1.2、混凝土基础浇筑及顶面埋件安装;
65.s1.3、支撑柱轴线位置定位放线,测量基础顶面埋件高程,以最高点为基准进行支撑柱71安装,支撑柱71下端同埋件焊接;
66.s1.4、支撑柱71顶面标高及平整度检查;
67.s1.5、标高合格后,支撑柱71上架设主梁72,主梁72同支撑柱顶通过螺栓连接;次梁73搭设在主梁72上,通过螺栓连接,次梁73之间采用角钢连接,顶面高程同次梁73高程,采用焊接连接;
68.s1.6、放线、铺平铺钢板:平铺钢板铺设位置放线;铺设平铺钢板,中心区圆形底板1的拼缝位置留设150~200mm空隙。
69.确认钢衬里模块拼装场地已经按照要求完成施工,满足模块拼装所需的空间。拼装平台已经安装完成,并组织验收合格。
70.拼装平台安装完成后,在拼装平台上铺设一层防火布,并通过核岛测量控制网将轴线和标高引测至拼装平台,检查拼装平台外形尺寸、轴线、标高等,验收合格后办理工序交接手续。施工区域照明和通道满足施工要求后方可开工。在平铺钢板上铺一层防火布可避免模块化结构构件与拼装平台相粘连。
71.拼装平台设计以单元模块为设计思路,分为中心处方形模块单元、梯形模块单元以及外围的带弧度模块单元,单元间为钢衬里底板现场拼接缝位置,用于设置焊接工装、贴合陶瓷衬垫、rt射线拍片等。
72.采用拼装平台可大范围减少混凝土施工作业平台的土方回填量,同时采用拼装平台单元模块装配式施工减少对主关键线路的工期需求,拆除方便可以循环利用,方便其他机组使用。
73.第二步、制作第一过渡段4、第二过渡段5和第三过渡段6。
74.第一过渡段4、第二过渡段5和第三过渡段6的制作方法均为:领料-放线
‑ꢀ
切割下料-标识移植-折弯成型-坡口机加工-弯曲成型-消应力热处理-拼接坡口加工-拼接坡口检查-拼接组对-焊接-变形矫正-无损检测-尺寸检查-编号存放;
75.第一过渡段4和第二过渡段5的预制安装,采用30mm板折弯需求的折弯机加工,将钢板下料成长条状;用折弯机折弯成l型钢;采用铣床将l型钢两边铣切出相应的过渡区域,用卷弧设备卷制成相应的弧形,对折弯区进行消应力热处理,通过焊接拼装成一个圆环;根据放线位置进行就位;
76.第三过渡段6的预制安装,采用22mm板折弯需求的折弯机加工,将钢板下料成长条状;用折弯机折弯成l型钢;采用铣床将l型钢两边铣切出相应的过渡区域,用卷弧设备卷制成相应的弧形,对折弯区进行消应力热处理,通过焊接拼装成一个圆环;根据放线位置进行就位。
77.第三步、制作中心区圆形底板1的底板。中心区圆形底板1的各底板的标号如图8所示。
78.长方形底板和梯形底板(4~11、13~16、19、20、22、23)的制作流程为:领料-下料-拼接板组对-焊接-校正-无损检测-二次切割-尺寸检查-编号存放。带圆弧底板(1~3、12、17、18、21、24)的制作流程为:领料-下料-拼接板组对
‑ꢀ
焊接-校正-无损检测-二次切割-尺寸检查-与第一过渡段4组对-焊接-校正-无损检测-尺寸检查-编号存放。
79.带圆弧底板(1~3、12、17、18、21、24)长度上预留不小于25mm余量,每块梯形底板(4、5、8、13、22、23、11、16)组焊完成后在长度及宽度方向均预留不小于10mm余量,余量端均在靠近外侧侧面壁板2方向。
80.第四步、制作侧面壁板2的壁板。侧面壁板2中各壁板和斜段环板3中各斜板的标号如图9所示。
81.拼装侧面壁板2的壁板的制作方法为:领料-下料-拼接板组对-焊接-校正-无损检测-二次切割-尺寸检查-贯穿件和加劲肋位置放线(若有)-检查-拼接板在胎模上固定成形-加劲肋角钢与壁板组对-检查-在壁板上压好工字钢梁-加劲肋角钢与壁板焊接-校正-无损检测-连接件定位-连接件焊接-连接件检查-整体尺寸检查
‑ꢀ
走道平台螺杆焊接及验收(若有)-喷砂油漆-编号存放。
82.第五步、制作斜段环板3的斜板。
83.拼装斜段环板3的斜板的制作方法为:领料-下料-标识移植-拼接板组对-焊接-校正-无损检测-与第二过渡段5组对-焊接-校正-无损检测-尺寸检查-喷砂油漆
‑ꢀ
编号存放。
84.斜板长度方向各增加不小于30mm余量。斜板与第二过渡段5组对焊接完成后对s01b、02b、04b、05b、07b、08b、10b、11b的余量进行切除,s03b、06b、 09b、12b的余量现场组对时进行二次切割,以保证整体尺寸符合设计要求。
85.第六步、由测量人员测出中心区圆形底板的中心坐标、十字中心线、角度线、半径,以十字中心线为绝对坐标,放出中心区圆形底板拼装定位线及0
°
、90
°
、 180
°
、270
°
度轴线。
86.底板由平板车从车间运至拼装场地附近空地上,再使用汽车吊进行倒运及吊装就位。汽车吊站位选择拼装平台东北侧及西侧;采用85吨汽车吊,吊物最大吊装半径30m满足吊机施工性能要求。
87.按拼装线拼装中心区圆形底板1,分24块底板拼装,如图10所示,按5个单元焊接。
88.中心区圆形底板的具体拼装流程为:位于中心的底板吊装就位-位于中心的底板现场组对-配重块及焊接工装设置-位于中心的底板现场焊接-无损检测-余量切割-位于外围的底板就位-位于外围的底板现场组对-配重快及焊接工装设置-位于外围的底板现场焊接-无损检测-整体尺寸检查。
89.底板就位后利用倒链调节底板之间的缝隙,调节完成后,进行相邻底板之间的组装固定。
90.中心区圆形底板的拼装焊接分单元进行,4、5、6、7号底板组焊为单元1, 9、10、14、15号底板组焊为单元2,19、20、22、23号底板组焊为单元3,8、 13号底板组焊为单元4,11、16号底板组焊为单元5,各单元拼装完成后,再进行单元与单元之间的拼装焊接。对4、5、11、16、22、23、8、13进行二次测量,切割余量,外侧圆弧形底版在长度方向均有30mm~50mm余量,供现场拼装时调节切割。
91.对于单元1、单元2和单元3的拼焊,先焊接短焊缝,再焊接长焊缝,短焊缝焊接时,一条焊缝的打底和盖面均由单元中心朝单元边界连续焊接。长焊缝的打底和盖面分两段进行,从靠近焊缝中心的位置,向两端进行焊接。单元4和单元5的拼焊按上述短焊缝的要求进行,各单元之间的拼焊按上述长焊缝的要求进行。
92.8块带圆弧底板(含第一过渡段)组对完成且第一过渡段各分段之间的拼接缝焊接完成后,切割位于中心的底板外边缘的余量,组对带圆弧底板与位于中心的底板,8条收缩缝及其左右两侧各约1m的长度暂不组对。组对完成后,采用自动焊设备焊接八边形焊缝。焊接时,打底从靠近焊缝中间位置,分两段朝焊缝两端进行,盖面可根据轨道数量选择分段焊接或朝一个方向连续焊接。
93.焊接完成后,再组对8条收缩缝及其左右两侧剩余的焊缝。组对完成后,收缩缝采用mag自动焊焊接,收缩缝左右两侧的剩余焊缝采用mag自动焊,每条焊缝均从y型焊缝交叉点向外焊接,避免焊接应力在焊缝交叉点集中,造成较大的焊接变形。
94.底板焊接前,在焊缝两侧采用方形钢板配重均匀布置,钢板中心处根据需要采用型钢配重均匀分布,数量及大小根据实际情况调整。配重块的设置不得增大焊缝的焊接难度,避免减小施焊空间、阻碍焊工的习惯操作及焊机摆放位置等。一条焊缝,可以沿着焊缝长度方向,用一根或多根(根与根之间刚性连接)型钢在所有u型铁下表面点焊,提高结构刚性,进一步减少焊缝的波浪变形。
95.第七步:拼装侧面壁板2:分12块壁板拼装,每块壁板两端头部位的外侧设有h300
×
30扶壁柱74,由扶壁柱74调整垂直度及半径,半径、垂直度合格后先焊接11条缝,另1条缝最后焊接,上口预留不小于30mm余量(现场切割),下料时保证正偏差,长度方向板s05c及s12c各增加不小于100mm余量;现场组对时进行二次切割,以保证整体尺寸符合设计要求。
96.侧面壁板2的具体拼装流程为:现场测量放线-设置扶壁柱-吊装就位壁板
‑ꢀ
调整定位后安插间隙板、眼镜板、圆锥销-焊纵缝的平台安装-纵缝组对-纵缝焊接、无损检测-环缝组对-环缝焊接、无损检测-切割收缩纵缝余量-收缩纵缝及剩余环缝焊接-连接角钢安装和连接件焊接-现场油漆修补-安装上口走道板。
97.具体的,侧面壁板就位标高为-8.071m。在中心区圆形底板的第一过渡段上放出侧面壁板下口的定位角度线,并将图纸所标预制构件的编号记于相应位置。
98.通过扶壁柱固定、就位壁板以及调节壁板垂直度,扶壁柱两侧或单侧增加斜撑角钢;扶壁柱由hw300型钢制作而成,共设置24根,每块壁板两端处定位2 根扶壁柱,距离钢板约200mm。
99.在侧面壁板内、外侧分别挂置施工作业平台,在吊装壁板之前,先把内侧走道板安装好,便于壁板就位作业。等所有壁板吊装就位完成后,再安装外侧走道板。外侧平台挂在壁板上口环向角钢ll25
×
80
×
10上,内侧平台固定在已焊好的螺栓上。
100.在第一过渡段上点焊定位靠板,在靠板间使用楔铁以调整并固定壁板。
101.吊装采用φ1.6
×
25m钢丝蝇、8m
×
3.2t链条与倒链配合的方法吊装壁板,通过倒链调节筒壁板的状态,倒链处利用φ15钢丝绳进行二次防坠。利用板外侧上弧形角钢开设的吊装孔挂设2根链条,使用卡环进行连接:板内侧由2根钢丝绳、倒链和链条配合连接,底部用角钢及卡环连接投设在作业平台附定螺栓上,壁板最大单重为2.79t,。
102.施工人员操作倒链以调整壁板的垂直度,利用δ=3mm间隙版、圆锥销和φ 10圆钢
对壁板间的间隙错边进行调整,同时固定壁板。
103.壁板在安装过程中的垂直度,利用全站仪架在核岛控制点上,然后通过测半径来检查每块钢板的垂直度。
104.壁板组对应在吊装时将壁板一个接一个定位,在组对过程中,应同时调整上口的垂直度和下口的环缝,只有当两者都符合要求后才可将相邻板固定,壁板 s05c与s12c都留有余量,在组对到s05c后进行半径调整切割余量,组对到最后一块版s12c后等其他纵缝全部焊接完成,检查上口周长后再进行切割组对焊接。纵缝组对后将壁板下侧巳调节好的环缝进行组对点焊。
105.每块壁板安装就位后,安装焊接纵缝平台或设置快装脚手架。
106.点焊和焊接由合格的焊工进行施焊,定位焊焊缝厚度不超过5mm,焊缝长度为10~20mm,间距为l00mm~200mm,根据需要进行调整。正式焊接时,按照焊接工艺卡中规定的参数进行焊接。采用靠板进行刚性固定,按以下焊接顺序进行焊接:步骤一:焊接除收缩缝以外的11条纵缝,焊接时由上至下分段退焊,每段长度不得超过500mm;步骤二:进行环缝的焊接,从收缩缝对面的环缝开始,均匀分布在圆周上,以该环缝为中心,向两边同时进行对称的同方向的分段退焊,每段长度不得超过500mm。步骤三:环缝焊接到收缩缝两边约1.5m处放样,切割收缩缝的余量,并组对施焊预留环缝和收缩缝。步骤四:焊缝无损检测合格后,进行连接角钢的组对和焊接。
107.第八步:拼装斜段环板3:斜段环板3分12块斜板拼装,设置48根斜支撑 75。斜段环板3安装时,下方设置型钢柱作为斜板支撑柱76,用于支撑斜段环板 3,并调整其标高。
108.斜段环板3的具体拼装流程为:现场测量放线-设置斜板支撑柱-吊装就位斜板-调整定位后插间隙板、眼镜板、圆锥销、标高调整板纵缝组对-纵缝焊接、无损检测-环缝组对-环缝焊接、无损检测-切割收缩纵缝余量-收缩纵缝及剩余环缝焊接-无损检测-整体尺寸检查。
109.具体的,斜段环板就位标高为-5.19m。在壁板上放出斜段环板下口的定位角度钱,并将图纸所标预制构件的编号记于相应位置。
110.斜段环板的斜板在车间设置临时径向角钢∠75
×
50
×
8,设置于斜板内侧。间隔1.5m~2.0m,距端部1m,并设置单块起吊吊点。
111.斜段环板吊装前,在拼装工装上设置48根斜板支撑柱,每块斜段下方均匀布置4根,距离侧面壁板约1500mm,设置斜撑,最后调整斜板支撑柱上口标高,使-5.00m标高第三过渡段落于斜板支撑柱上,且第三过渡段上口标高同时满足图纸要求。
112.斜段环板的斜板的吊装使用4根8
×
3.2t链条与倒链配合的方法进行,通过倒链调节斜板的就位角度;其中2根链条通过卡环挂设在斜板外侧上口环向角钢吊装孔上;剩余2根链条通过2t倒链、钢板夹钩挂在斜板底部,倒链处利用φ15 钢丝绳作为防坠绳,钢丝绳通过卡环与链条及下部钢板夹连接,钢板夹与斜板间加设护角,以s12b相邻斜板为起点,逆时针向或者顺时针方向一次吊装就位,安装至s05b时,采用全站仪测量巳安装斜板上口第三过渡段半径,调整后切割 s05b余量,安装至s12b时再次测量上周长及标高,满足要求后切割s12b余量,最大单重为2.52t.。
113.其中,中心区圆形底板1采用激光智能跟踪mag自动焊接方法和陶质衬垫单面焊双面成形高效焊接工艺;组对焊缝宽度为5~8mm;短焊缝焊接由单元中心朝单元边界连续焊
接;长焊缝焊接从焊缝中心分段朝焊缝两端进行;底板背面采用陶质衬垫作为非永久衬垫使背面焊缝强制成形,实现钢衬里单面焊双面成形焊接施工,陶质衬垫粘贴时保证衬垫中心线与焊缝中心线对齐,并确保铝箔胶带固定牢固;
114.侧面壁板2采用激光跟踪mag自动焊接方法,陶质衬垫作为非永久衬垫,焊接时托住焊缝熔敷金属使背面焊缝强制成形,实现焊缝的单面焊双面成形;焊接过程中经过打底、层间清理及盖面三道工序,且焊丝可实现连续焊接;焊接以两条收缩缝中间的壁板为中心,一半焊缝沿顺时针方向焊接,另一半沿逆时针进行焊接;横缝采用在远离立缝收缩缝的一段开始分段沿顺时针方向进行连续焊接;
115.斜段环板3焊接同侧面壁板2采用激光跟踪mag自动焊接方法。
116.除上述实施例外,本发明还可以有其它实施方式。凡等同采用替换或等效变换形成的技术方案,均落在本发明要求的保护范围。