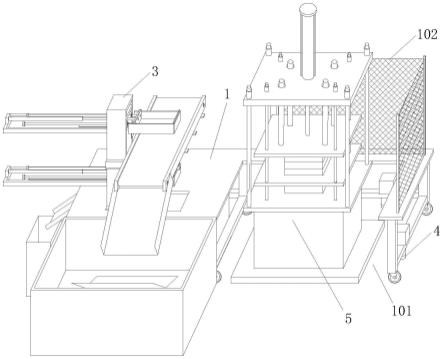
1.本发明涉及热压铸工艺设备技术领域,特别地,涉及一种热压铸设备。
背景技术:2.陶瓷产品的热压铸成型是一种应用广泛的陶瓷生产工艺,其基本原理是,利用石蜡受热熔化和遇冷凝固的特点,将无可塑性的瘠性陶瓷粉料与热石蜡液均匀混合形成可流动的浆料,在一定压力下注入金属模具中成型,待浆料冷却凝固后脱模取出成型好的坯体,坯体经过后续排蜡和烧结处理,进而得到最终陶瓷产品。
3.现有的陶瓷产品热压铸设备,所成型的陶瓷坯体,一般采用自由降落的方式收集陶瓷坯体物料,以利于下一批次的陶瓷坯体热压铸成型,如中国发明专利cn101229656a、中国发明专利cn2715952y等。自由降落收集物料的方式,下落的高度不可能设置过高,设置过高容易导致陶瓷坯体的碎裂,而热压铸机生产不同型号的产品时,所使用的压铸模具不同,其出料高度会相应变化,固定的收料高度并不适用于所有产品,因此能够收集的物料非常有限;而使用多台热压铸机分别生产限定型号的产品,不仅成本高昂,且不利于生产计划的调整,切换产品型号后需要人工实时的进行物料转移,自动化程度不高,生产效率受到限制。
4.现有的陶瓷产品热压铸设备,还有另一种方式收集坯体物料的方式,如中国发明专利cn104260188a,采用负压抽吸的方式将压铸成型的陶瓷坯体转移至摆放平台,以便于进行下一批次的陶瓷坯体热压铸成型。但是,这些陶瓷坯体物料的收集方式,无法连续的进行物料的转送,同样需要人工介入,将堆积过多的物料进行转移,且一旦转移不及时,可能导致设备出现问题,需要人工实时地进行值守,否则无法进行连续的生产作业,自动化程度不高,生产效率受到限制;另外,负压抽吸进行物料转移的方式,无法适应于带孔的产品,且容易出现物料掉落的风险;还有,热压铸设备压铸陶瓷坯体时,作为废料的冒口切除后,会散落在机台上,废料在机台上堆积过多会影响正常生产,需要人工进行清理,为了保证生产环境整洁,清理下来的废料同样需要进行收集、转送。
技术实现要素:5.本发明提供了一种热压铸设备,以解决现有的陶瓷产品热压铸设备自动化程度低,动作精度难以控制,导致次品率高、陶瓷坯料和废料不能分别收集并转送,难以实现连续生产,生产效率低的技术问题。
6.根据本发明的一个方面,提供一种热压铸设备,包括支架本体和热压铸机,所述支架本体用于支承依次从热压铸机中接取陶瓷坯体物料和废料并分别进行转送的物料输出组件,所述热压铸机包括用于从底部热压注入混合浆料的基础模组、与所述基础模组在竖直方向上相对可活动地布设的用于压盖在所述基础模组上以与所述基础模组围合形成混合浆料热压注入空间的活动模组,所述物料输出组件包括:呈悬挑布设的用于悬停至第一接料工位以从所述活动模组的物料输出端承接陶瓷坯体物料并转送至第一下料工位输出
的陶瓷坯体物料转送机构、布设于第一下料工位下方的用于将所述陶瓷坯体物料转送机构输出的陶瓷坯体物料传送输出并进行收集的水平输送收集机构、呈悬挑布设的用于悬停至第二接料工位以从所述活动模组的废料输出端承接废料并转送在第二下料工位输出的废料转送机构以及处于第二下料工位下方的用于将所述废料转送机构输出的废料导出并收集的废料收集机构。
7.进一步地,所述陶瓷坯体物料转送机构包括用于悬停至第一接料工位以从所述活动模组的物料输出端承接陶瓷坯体物料并转送至第一下料工位输出的第一接料盒、与所述第一接料盒连接的用于驱使所述第一接料盒在第一接料工位和第一下料工位之间沿水平方向往复运动的第一水平驱动机构、用于驱使悬停至第一下料工位的所述第一接料盒进行下料的第一下料驱动机构以及用于承载所述第一水平驱动机构的第一转送支架;所述第一接料盒通过所述第一水平驱动机构悬置于所述第一转送支架的靠近热压铸机的一侧;所述水平输送收集机构包括处于所述陶瓷坯体物料转送机构与所述废料转送机构之间的物料输送带、处于所述物料输送带的物料输出端的导料槽以及处于所述导料槽的输出端的接料箱;所述第一接料盒在第一下料工位的竖向投影完全落于所述物料输送带的输送区域内;所述接料箱内还设有与所述导料槽的输出端位置匹配并用于对下落的陶瓷坯体物料进行柔性承接或弹性缓冲承接并导入至所述接料箱内腔中的保护垫;所述废料转送机构包括用于悬停至第二接料工位以从所述活动模组的废料输出端承接废料并转送至第二下料工位输出的第二接料盒、与所述第二接料盒连接的用于驱使所述第二接料盒在第二接料工位和第二下料工位之间沿水平方向往复运动的第二水平驱动机构、用于驱使悬停至第二下料工位的所述第二接料盒进行下料的第二下料驱动机构以及用于承载所述第二水平驱动机构的第二转送支架;所述第二接料盒通过所述第二水平驱动机构悬置于所述第二转送支架的靠近热压铸机的一侧;所述废料收集机构包括处于所述陶瓷坯体物料转送机构和所述废料转送机构下方以承载所述陶瓷坯体物料转送机构和所述废料转送机构的底座,所述底座上开设有废料入口,所述第二接料盒在第二下料工位的竖向投影完全落于所述废料入口区域内,所述废料入口的下方设有废料导出槽,所述废料导出槽的输出端朝向远离热压铸机的方向布设,所述废料导出槽的输出端设有废料箱。
8.进一步地,所述活动模组包括:用于与所述基础模组竖向压合以形成浇道并构成陶瓷坯体物料的底部成型模的浇道成型模组、用于与所述浇道成型模组配合以热压铸成型陶瓷坯体物料的坯体成型模组、与所述坯体成型模组插接配合以构成陶瓷坯体物料的顶部成型模并用于通过与坯体成型模相对运动以实现陶瓷坯体物料脱模的坯体顶部插接模组以及与所述坯体顶部插接模组插接配合并依次穿过所述坯体顶部插接模组和所述坯体成型模组进而伸入至所述浇道成型模组内的用于成型陶瓷坯体物料的内孔并通过与所述浇道成型模组相对运动以实现冒口从陶瓷坯体物料上断开后脱出的型芯模组。
9.进一步地,所述基础模组上设有主固定框架、主滑轨以及主驱动装置,所述主滑轨和所述主驱动装置呈竖向布设,所述活动模组可滑动地布设于所述主滑轨上,所述主驱动装置的固定端固定于所述主固定框架上,所述主驱动装置的动力输出端连接并固定在所述活动模组,用于驱动所述活动模组整体上升远离所述基础模组或整体下降压合于所述基础模组上。
10.进一步地,所述浇道成型模组包括滑动布设于所述主滑轨上的浇道基板以及设于
所述浇道基板上的浇道模,所述浇道模的底部开设有用于与所述基础模组的混合浆料输出口一一对应布设的浇道,所述浇道模的上表面开设有用于与陶瓷坯体物料的底部外形相匹配的坯体沉槽,浇道与坯体沉槽一一对应布设,浇道与对应的坯体沉槽连通且浇道连通至坯体沉槽的连通部位处于成型陶瓷坯体物料的其中一个内孔所在位置;所述主驱动装置的动力输出端连接并固定在所述浇道模上和/或所述浇道基板上。
11.进一步地,所述坯体成型模组包括滑动布设于所述主滑轨上的坯体成型框架、呈竖向的设于所述坯体成型框架上的用于驱使所述坯体成型框架移动相对靠近所述浇道成型模组或移动相对远离所述浇道成型模组的坯体成型驱动装置以及设于所述坯体成型框架上的坯体模,所述坯体模与所述浇道成型模组相对布设;所述坯体模上开设有上下贯通的用于所述坯体顶部插接模组插接配合并成型陶瓷坯体物料的贯通腔孔,贯通腔孔与浇道成型模组的坯体沉槽一一对应布设并上下贯通配合以形成完整的陶瓷坯体物料成型腔。
12.进一步地,所述坯体顶部插接模组包括呈竖向的设于坯体成型框架上的坯体脱模驱动装置、设于所述坯体脱模驱动装置的动力输出端的坯体脱模压板以及布设于所述坯体脱模压板的下表面的用于插接悬置于贯通腔孔内以配合热压铸成型陶瓷坯体物料并上下动作以实现陶瓷坯体物料脱模的坯体顶模,所述坯体顶模与贯通腔孔一一对应布设。
13.进一步地,所述型芯模组包括呈竖向的布设于所述坯体成型框架上的型芯驱动装置、呈竖向的布设于所述坯体成型框架上的辅助滑轨、可滑动地布设于所述辅助滑轨上并固定在所述型芯驱动装置的动力输出端上的型芯基板以及设于所述型芯基板下表面的型芯杆;所述型芯杆穿设于所述坯体顶模内并朝向所述浇道成型模组方向延伸,且所述型芯杆与陶瓷坯体物料的内孔的成型位置一一对应布设;同一陶瓷坯体物料的成型位置的所述型芯杆的延伸长度不同,其中相对较短的所述型芯杆与所述浇道成型模组的浇道对应布设,以使混合浆料经浇道从所述型芯杆与浇道之间的间隙流入进而热压铸成型陶瓷坯体物料,而相对较长的所述型芯杆顶抵于所述浇道成型模组的坯体沉槽的槽底。
14.进一步地,所述支架本体上设有用于调整所述物料输出组件的朝向和/或高度的调整机构,所述调整机构包括用于承载所述物料输出组件的支撑板、用于调整所述支撑板的朝向的转动机构和/或调整所述支撑板高度的升降机构。
15.进一步地,所述支架本体上设有用于支承给热压铸机供给浆料的加料装置,所述加料装置包括物料容器,所述物料容器上设有用于对所述物料容器内腔中的物料进行搅拌的搅拌组件以及处于所述搅拌组件侧向的用于通过向所述物料容器的底部冲压的方式将所述物料容器内的物料向外冲压泵送的冲压机构,所述物料容器的底板上设有用于所述冲压机构对应布设的导料沉槽,所述导料沉槽的下部连接有用于将物料输送至热压铸模具内的物料输送管道;所述冲压机构包括固设于所述物料容器顶板上的冲压驱动装置、与所述冲压驱动装置的输出端连接并伸入至所述物料容器内腔中的转接杆以及处于所述转接杆端部的冲压塞,所述冲压驱动装置、所述转接杆和所述冲压塞沿竖向布设。
16.本发明具有以下有益效果:
17.本发明实施例的热压铸设备,物料输出组件呈悬挑的布设在热压铸机的侧向,采用水平往复运动的方式伸入至热压铸机内,并从热压铸机的活动模组的输出端依次承接陶瓷坯体物料以及废料,陶瓷坯体物料通过转送方式输出,废料集中收集,以便于热压铸机进行下一批次的热压铸以及后续的输出;由于接料时伸入至热压铸机内,而下料时转移至热
压铸机外,进而实现物料的转送及下料输出,物料的转送、下料、输出过程不会影响到热压铸机的连续运转,且由于下料处于热压铸机外,使得物料的下料方式可以根据需要任意布设,并且具有足够的布设空间,进而使热压铸机进行陶瓷热压铸得以不间断的连续生产运行,物料转送、下料、输出过程采用全自动方式,无需人工值守,且不用担心物料堆积过量而影响热压铸机的连续工作。具体地,陶瓷坯体物料转送机构的设置高度与热压铸机的陶瓷坯体物料输出的高度相匹配,当热压铸机的热压铸完成后并使模具抬升,此时陶瓷坯体物料转送机构水平伸入热压铸机内并悬停于第一接料工位,即热压铸机的模具正下方且彼此之间的距离恰当(优选地,彼此之间的距离为陶瓷坯体物料的下落距离,为10cm~50cm,以避免陶瓷坯体物料下落时不易发生冲击破坏,进而确保陶瓷坯体物料的质量合格;过小的距离,会影响热压铸机的热压铸过程;过大的距离,会导致陶瓷坯体物料下落时的冲击力过大而增加了碎裂的几率,增加了产品的次品率和不合格率),然后模具下料并落于陶瓷坯体物料转送机构内,陶瓷坯体物料转送机构退出热压铸机,然后将陶瓷坯体物料下落至水平输送收集机构并实现陶瓷坯体物料的传送输出及收集;由于废料的承接无需考虑废料是否会受到冲击力破坏,仅需要考虑废料能够完全落入且不易跳出即可,因此废料转送机构布设于陶瓷坯体物料转送机构的下方并处于水平输送收集机构的下方,当陶瓷坯体物料转送机构从热压铸机中承接完陶瓷坯体物料并退出热压铸机后,废料转送机构伸入至热压铸机内,并从热压铸机的模具下方承接掉落的废料(热压铸机的模具废料出料随着工艺的不同,可能存在一次下料或多次下料),然后废料转送机构退出热压铸机并向废料收集机构输出废料,进而完成一次热压铸机物料输出过程,以此循环进行,从而达到辅助热压铸机连续工作的目的。另外,物料输出组件采用悬挑的方式进行布设及运动,陶瓷坯体物料及废料的接取、转送、下料、输出过程以及其布设位置、运动轨迹选择了对热压铸机影响最小的方式,进而提高热压铸机的生产效率,且可以适用于各种热压铸机的物料输出,适用性强。整个结构简单,容易匹配于各种热压铸机以进行物料的输出,且不会影响热压铸机的生产工艺过程,确保热压铸机可以稳定、连续地运行。通过将加料装置和物料输出组件安装在支架本体上,支架本体上开设有用于固定热压铸机的安装槽,安装槽通过连接件与热压铸机固定连接。热压铸机通过螺栓、插销、连接法兰等常用连接件连接与固定在安装槽上;或者热压铸机通过顶抵在上安装槽的预设沟槽内,以实现彼此之间的定位和限位;这种固定连接的一体式结构能对加料装置起到保护作用,保证加料装置不会倾倒,保证生产顺利进行,同时,为物料输出组件提供稳定的支撑,能提升空间利用率,节约生产空间;通过支架本体上的调整机构调节物料输出组件的朝向和/或接料高度,能适用不同高度的热压铸机,能避免接料高度过高导致自由下落的陶瓷坯体损坏,用于不同物料的收集,能减少人工干预,提升生产效率;而且一体式的结构集浆料供应、坯料及废料分别收集转送功能集为一体,与热压铸机装配简单,能省去繁杂的安装过程,节约时间成本。本发明实施例的热压铸设备自动化程度高,动作精度高,适用于各种带有通孔的陶瓷坯体物料的批量生产,能够减少故障率,提升产品良品率,保证产品质量,提高生产效率。
18.除了上面所描述的目的、特征和优点之外,本发明还有其它的目的、特征和优点。下面将参照图,对本发明作进一步详细的说明。
附图说明
19.构成本技术的一部分的附图用来提供对本发明的进一步理解,本发明的示意性实施例及其说明用于解释本发明,并不构成对本发明的不当限定。在附图中:
20.图1是本发明优选实施例的支撑框架的结构示意图;图2是本发明优选实施例的支架本体的结构示意图;图3是本发明优选实施例的加料装置的结构示意图;图4为本发明优选实施例的冲压机构的结构示意图,图4(a)是本发明优选实施例的冲压机构的结构示意图之一;图4(b)是本发明优选实施例的冲压机构的结构示意图之二;图4(c)是本发明优选实施例的冲压机构的结构示意图之三;图4(d)是本发明优选实施例的冲压机构的结构示意图之四;图5是本发明优选实施例的搅拌组件的结构示意图之一;图6是本发明优选实施例的搅拌组件的结构示意图之二;图7是本发明优选实施例的物料输出组件的结构示意图;图8是本发明优选实施例的物料输出组件从热压铸机中承接陶瓷坯体物料的结构示意图;图9是本发明优选实施例的物料输出组件从热压铸机中承接废料以及陶瓷坯体物料下料输出的结构示意图;图10是本发明优选实施例的陶瓷坯体物料转送机构与废料转送机构的组合结构示意图;
21.图11是本发明优选实施例的第一接料盒处于接料工位接料状态的结构示意图;图12是本发明优选实施例的第一接料盒处于下料工位准备下料状态的结构示意图;图13是本发明优选实施例的第一接料盒处于下料工位下料状态的结构示意图;图14是本发明优选实施例的升降机构的结构示意图之一;图15是本发明优选实施例的升降机构的结构示意图之二;图16是本发明优选实施例的升降机构的结构示意图之三;图17是本发明优选实施例的热压铸模具组件的热压注入混合浆料状态的结构示意图;图18是本发明优选实施例的热压铸模具组件的活动模组整体抬升冷却以及型芯模组上下动作以使冒口废料断裂脱出状态的结构示意图;图19是本发明优选实施例的热压铸模具组件的坯体顶部插接模组上下动作以使陶瓷坯体物料脱出状态的结构示意图;图20是本发明优选实施例的热压铸模具组件的活动模组整体下压前型芯模组上下动作以疏通浇道状态的结构示意图。
22.图例说明:1、支架本体;101、安装槽;102、防护网;2、加料装置;21、物料容器;2101、加料口;21011、支撑台阶;21012、插接配合件;2102、避让槽;22、搅拌组件;2201、搅拌驱动装置;2202、转动桨轴;2203、搅拌桨;22031、搅拌主框;22032、搅拌副框;23、冲压机构;2301、冲压驱动装置;2302、转接杆;2303、冲压塞;24、导料沉槽;25、物料输送管道;26、盖板;2601、延伸部;3、物料输出组件;31、陶瓷坯体物料转送机构;3101、第一接料盒;31011、传力板;31012、外框板;31013、活动底板;31014、缓冲构造;3102、第一水平驱动机构;31021、第一水平驱动气缸或第一水平驱动油缸;31022、第一导向支撑滑杆;31023、第一限位构造;3103、第一下料驱动机构;31031、下料基板;31032、l形中转板;31033、下料驱动气缸或下料驱动油缸;3104、第一转送支架;32、水平输送收集机构;3201、物料输送带;3202、导料槽;3203、接料箱;3204、保护垫;33、废料转送机构;3301、第二接料盒;3302、第二水平驱动机构;33021、第二水平驱动气缸或第二水平驱动油缸;33022、第二导向支撑滑杆;33023、第二限位构造;3303、第二下料驱动机构;3304、第二转送支架;34、废料收集机构;3401、底座;3402、废料入口;3403、废料导出槽;3404、废料箱;4、调整机构;41、支撑板;42、转动机构;4201、转动盘;4202、限位机构;43、升降机构;4301、伸缩杆;4302、定位件;4303、调节支撑螺栓;4304、剪式支架;44、万向轮;45、支撑件;5、热压铸机;51、基础模组;5101、主
固定框架;5102、主滑轨;5103、主驱动装置;5104、基座;5106、流道底模;51061、主流道;51062、副流道;51063、输出通道;51064、保温输送管路;52、活动模组;53、浇道成型模组;5301、浇道基板;5302、浇道模;54、坯体成型模组;5401、坯体成型框架;5402、坯体成型驱动装置;5403、坯体模;55、坯体顶部插接模组;5501、坯体脱模驱动装置;5502、坯体脱模压板;5503、坯体顶模;56、型芯模组;5601、型芯驱动装置;5602、辅助滑轨;5603、型芯基板;5604、型芯杆;57、冷却通道;58、合模定位孔或合模定位销;59、距离传感器。
具体实施方式
23.以下结合附图对本发明的实施例进行详细说明,但是本发明可以由下述所限定和覆盖的多种不同方式实施。
24.如图1、图2、图7、图8、图9和图10所示,本实施例的热压铸设备,包括支架本体1,支架本体1用于支承给热压铸机5供给浆料的加料装置2以及支承依次从热压铸机5中接取陶瓷坯体物料和废料并分别进行转送的物料输出组件3,支架本体1上设有用于调整物料输出组件3的朝向和/或高度的调整机构4;热压铸机5包括用于从底部热压注入混合浆料的基础模组51、与基础模组51在竖直方向上相对可活动地布设的用于压盖在基础模组51上以与基础模组51围合形成混合浆料热压注入空间的活动模组52,物料输出组件3用于依次从热压铸机中接取陶瓷坯体物料和废料并分别进行转送,包括:呈悬挑布设的用于悬停至第一接料工位以从活动模组52的物料输出端承接陶瓷坯体物料并转送至第一下料工位输出的陶瓷坯体物料转送机构31、布设于第一下料工位下方的用于将陶瓷坯体物料转送机构31输出的陶瓷坯体物料传送输出并进行收集的水平输送收集机构32、呈悬挑布设的用于悬停至第二接料工位以从活动模组52的废料输出端承接废料并转送在第二下料工位输出的废料转送机构33以及处于第二下料工位下方的用于将废料转送机构33输出的废料导出并收集的废料收集机构34。料输出组件呈悬挑的布设在热压铸机的侧向,采用水平往复运动的方式伸入至热压铸机内,并从热压铸机的活动模组52的输出端依次承接陶瓷坯体物料以及废料,陶瓷坯体物料通过转送方式输出,废料集中收集,以便于热压铸机进行下一批次的热压铸以及后续的输出;由于接料时伸入至热压铸机内,而下料时转移至热压铸机外,进而实现物料的转送及下料输出,物料的转送、下料、输出过程不会影响到热压铸机的连续运转,且由于下料处于热压铸机外,使得物料的下料方式可以根据需要任意布设,并且具有足够的布设空间,进而使热压铸机进行陶瓷热压铸得以不间断的连续生产运行,物料转送、下料、输出过程采用全自动方式,无需人工值守,且不用担心物料堆积过量而影响热压铸机的连续工作。具体地,陶瓷坯体物料转送机构31的设置高度与热压铸机的陶瓷坯体物料输出的高度相匹配,当热压铸机的热压铸完成后并使模具抬升,此时陶瓷坯体物料转送机构31水平伸入热压铸机内并悬停于第一接料工位,即热压铸机的模具正下方且彼此之间的距离恰当(优选地,彼此之间的距离为陶瓷坯体物料的下落距离,为10cm~50cm,以避免陶瓷坯体物料下落时不易发生冲击破坏,进而确保陶瓷坯体物料的质量合格;过小的距离,会影响热压铸机的热压铸过程;过大的距离,会导致陶瓷坯体物料下落时的冲击力过大而增加了碎裂的几率,增加了产品的次品率和不合格率),然后模具下料并落于陶瓷坯体物料转送机构31内,陶瓷坯体物料转送机构31退出热压铸机,然后将陶瓷坯体物料下落至水平输送收集机构32并实现陶瓷坯体物料的传送输出及收集;由于废料的承接无需考虑废料是否会受到
冲击力破坏,仅需要考虑废料能够完全落入且不易跳出即可,因此废料转送机构33布设于陶瓷坯体物料转送机构31的下方并处于水平输送收集机构32的下方,当陶瓷坯体物料转送机构31从热压铸机中承接完陶瓷坯体物料并退出热压铸机后,废料转送机构33伸入至热压铸机内,并从热压铸机的模具下方承接掉落的废料(热压铸机的模具废料出料随着工艺的不同,可能存在一次下料或多次下料),然后废料转送机构33退出热压铸机并向废料收集机构34输出废料,进而完成一次热压铸机物料输出过程,以此循环进行,从而达到辅助热压铸机连续工作的目的。另外,物料输出组件3采用悬挑的方式进行布设及运动,陶瓷坯体物料及废料的接取、转送、下料、输出过程以及其布设位置、运动轨迹选择了对热压铸机影响最小的方式,进而提高热压铸机的生产效率,且可以适用于各种热压铸机的物料输出,适用性强。整个结构简单,容易匹配于各种热压铸机以进行物料的输出,且不会影响热压铸机的生产工艺过程,确保热压铸机可以稳定、连续地运行。本实施例将加料装置2和物料输出组件3安装在支架本体1上,支架本体1上开设有用于固定热压铸机的安装槽101,安装槽101通过连接件与热压铸机固定连接。热压铸机通过螺栓、插销、连接法兰等常用连接件连接与固定在安装槽101上;或者热压铸机通过顶抵在上安装槽101的预设沟槽内,以实现彼此之间的定位和限位;这种固定连接的一体式结构能对加料装置2起到保护作用,保证加料装置2不会倾倒,保证生产顺利进行,同时,为物料输出组件3提供稳定的支撑,能提升空间利用率,节约宝贵的生产空间;通过支架本体1上的调整机构4调节物料输出组件3的朝向和/或接料高度,能适用不同高度的热压铸机,能避免接料高度过高导致自由下落的陶瓷坯体损坏,用于不同物料的收集,能减少人工干预,提升生产效率;而且一体式的结构集浆料供应、坯料及废料分别收集转送功能集为一体,与热压铸机装配简单,能省去繁杂的安装过程,节约时间成本。具体的支架本体1的顶部上设置有工作台面,将加料装置2安装于工作台面下方,物料输出组件3安装在工作台面的顶面上,工作台面下方还可放置电控箱,工作台面上设置工具箱,生产所需工具可放置于工具箱内;可选地,支架本体1的侧面和/或底部设置挡板。可选的,挡板与支架本体1通过卡槽卡接、通过连接件(螺栓、插销常用连接件)固定连接、或者通过铰链可转动地连接。可选的,挡板上开设有透气孔或者观察窗。
25.可选地,陶瓷坯体物料转送机构31与废料转送机构33可以采用相同的结构,仅需要通过控制器实现两者的协调控制,进而匹配于热压铸机的下料(陶瓷坯体物料下料以及废料下料)。可选地,陶瓷坯体物料转送机构31与废料转送机构33也可以采用不同的结构,例如将废料转送机构33直接设置成布设于热压铸机下方的料斗,由于废料无需要率掉落破损问题,因此也无需考虑承接物料的高度,因此可以在热压铸机下方设置足够的空间布设料斗,进而可以持续承接废料,且不易影响到热压铸机的连续运行。可选地,陶瓷坯体物料转送机构31与废料转送机构33为整体结构;具体地,第一转送支架3104与第二转送支架3304为整体结构。可选地,陶瓷坯体物料转送机构31、水平输送收集机构32、废料转送机构33为整体结构;具体地,第一转送支架3104与第二转送支架3304为整体结构,水平输送收集机构32连接并固定在第一转送支架3104和/或第二转送支架3304上。
26.如图7、图8、图9和图10所示,本实施例中,陶瓷坯体物料转送机构31包括用于悬停至第一接料工位以从热压铸机的物料输出端承接陶瓷坯体物料并转送至第一下料工位输出的第一接料盒3101、与第一接料盒3101连接的用于驱使第一接料盒3101在第一接料工位和第一下料工位之间沿水平方向往复运动的第一水平驱动机构3102、用于驱使悬停至第一
下料工位的第一接料盒3101进行下料的第一下料驱动机构3103以及用于承载第一水平驱动机构3102的第一转送支架3104。第一接料盒3101通过第一水平驱动机构3102悬置于第一转送支架3104的靠近热压铸机的一侧。陶瓷坯体物料转送机构31呈悬挑的布设在热压铸机的侧向,采用水平往复运动的方式,使第一接料盒3101在第一接料工位与第一下料工位之间进行位置切换;当热压铸机热压铸完成并将进行脱料时,第一接料盒3101伸入陶瓷热压铸机内并悬置于第一接料工位以承接陶瓷坯体物料,然后第一接料盒3101移动至第一下料工位进行下料,以便于热压铸机进行废料下料以及后续下一批次的热压铸以及后续的接料;由于接料时第一接料盒3101伸入至热压铸机内,而下料时转移至热压铸机外(此时热压铸机能够继续进行后续动作,例如脱出废料、下一批次的热压铸成型),进而实现陶瓷坯体物料的转送,陶瓷坯体物料的转送过程不会影响到热压铸机的连续运转,且由于下料处于热压铸机外,使得物料的下料方式可以根据需要任意布设,并且具有足够的布设空间,进而使热压铸机进行陶瓷热压铸得以不间断的连续进行,物料转送过程采用全自动方式,无需人工值守,且不用担心物料堆积过量而影响热压铸机的连续工作。具体地,整个结构采用第一转送支架3104进行整体的结构支撑,第一水平驱动机构3102用于驱使第一接料盒3101在第一接料工位与第一下料工位之间往复移动,当热压铸机热压铸完成后,第一水平驱动机构3102驱使第一接料盒3101移动至第一接料工位,悬置于热压铸机的物料输出端下方(热压铸模具下方10cm~50cm的位置),以从热压铸机的物料输出端承接陶瓷坯体物料,然后通过第一水平驱动机构3102驱使第一接料盒3101移动至第一下料工位,热压铸机进行废料脱出以及下一批次的热压铸,而第一下料驱动机构3103驱使第一接料盒3101下料,进而完成一个陶瓷坯体物料的转送周期;以此进行循环动作,进而实现陶瓷坯体物料的连续生产以及连续转送。另外,陶瓷坯体物料转送机构31采用悬挑的方式进行布设及运动,其布设位置及运动轨迹可以选择对热压铸机影响最小的方式,进而提高热压铸机的生产效率,且可以适用于各种热压铸机的物料转送,适用性强。整个结构简单,容易匹配于各种热压铸机以进行物料的转送,且不会影响热压铸机的生产工艺过程,确保热压铸机可以稳定、连续地运行。
27.如图7、图8、图9和图10所示,本实施例中,第一水平驱动机构3102包括装配于第一转送支架3104上的第一水平驱动气缸或第一水平驱动油缸31021,第一水平驱动气缸或第一水平驱动油缸31021的动力输出端与第一接料盒3101连接。第一水平驱动机构3102还包括至少一组用于第一接料盒3101水平运动导向和对第一接料盒3101进行辅助支撑的第一导向支撑滑杆31022,第一导向支撑滑杆31022可滑动地装配在第一转送支架3104上且一端与第一接料盒3101固定连接,第一导向支撑滑杆31022与第一水平驱动气缸或第一水平驱动油缸31021平行布设。可以根据实际工况选择采用第一水平驱动气缸或第一水平驱动油缸31021;其中,第一水平驱动气缸动作速度快且结构轻便,适合于生产工艺速度相对较高、生产效率高的环境使用,以便于快速悬置在第一接料工位进行接料及快速回收至第一下料工位进行下料;第一水平驱动油缸作用力大,适合于驱动质量相对较大、承载物料相对较多的第一接料盒3101使用。第一水平驱动机构3102除了动力部分(第一水平驱动气缸或第一水平驱动油缸31021),还包括与动力部分平行布设的第一导向支撑滑杆31022,用于对第一接料盒3101的水平往复运动进行运动导向;由于第一接料盒3101采用悬挑方式进行水平往复运动,采用第一导向支撑滑杆31022与动力部分(第一水平驱动气缸或第一水平驱动油缸
31021)协同进行第一接料盒3101的支撑,以确保第一接料盒3101运动过程的结构稳定性,特别是在运动行程相对较大时,该稳定效果更加明显。可选地,第一导向支撑滑杆31022设置有两组,两组第一导向支撑滑杆31022在第一接料盒3101上的连接点与动力部分(第一水平驱动气缸或第一水平驱动油缸31021)在第一接料盒3101上的连接点呈三角形布设,以形成对第一接料盒3101的稳定支撑以及稳定驱动,避免第一接料盒3101在远距离往复水平运动过程中发生振动或抖动,确保物料可以稳定承接并实现稳定下料。第一导向支撑滑杆31022的远离第一接料盒3101的一端设有用于确保第一接料盒3101悬停于第一接料工位的第一限位构造31023。可选地,第一限位构造31023可以处于第一导向支撑滑杆31022远离第一接料盒3101的端部,也可以处于第一导向支撑滑杆31022靠近端部的位置。可选地,第一限位构造31023采用固定于第一导向支撑滑杆31022的橡胶块、硅胶块或金属块。可选地,第一转送支架3104朝向第一限位构造31023的位置布设有缓冲垫,通过缓冲垫与第一限位构造31023之间的接触配合以实现第一接料盒3101精准悬停至接料工位的同时,避免彼此之间产生冲击破坏。第一转送支架3104包括支撑架、设于支撑架上的用于与第一导向支撑滑杆31022滑动配合的滑套以及处于支撑架远离第一接料盒3101的一侧并向外延伸布设的用于承载第一水平驱动气缸或第一水平驱动油缸31021的驱动支架。可选地,第一水平驱动气缸或第一水平驱动油缸31021的动力输出端呈悬挑的穿过支撑架并与第一接料盒3101连接;第一导向支撑滑杆31022可滑动地穿设于滑套内并与第一接料盒3101连接;通过第一水平驱动气缸或第一水平驱动油缸31021驱动第一接料盒3101水平运动的同时,通过第一导向支撑滑杆31022进行运动导向,并连同第一转送支架3104共同支撑第一接料盒3101进行悬挑地水平运动。
28.如图11、图12和图13所示,本实施例中,第一接料盒3101包括与第一水平驱动机构3102连接的传力板31011、与传力板31011连接并围合形成多边形外框的外框板31012以及处于底部并可沿水平方向移动的活动底板31013,传力板31011、外框板31012和活动底板31013共同围合形成上开口的接料内腔。第一下料驱动机构3103包括固定于外框板31012下方的下料基板31031、与活动底板31013连接的l形中转板31032、布设于下料基板31031与l形中转板31032之间的下料驱动气缸或下料驱动油缸31033。l形中转板31032朝向远离第一接料盒3101的方向延伸,且l形中转板31032的折弯部处于远离第一接料盒3101的一端,下料驱动气缸或下料驱动油缸31033处于l形中转板31032的折弯部与下料基板31031之间。当第一接料盒3101悬停于下料工位时,通过下料驱动气缸或下料驱动油缸31033驱动l形中转板31032朝向远离第一接料盒3101的方向移动,以带动活动底板31013从第一接料盒3101底部滑开并开启第一接料盒3101的下开口,进而使第一接料盒3101内的物料向下掉落,然后再通过下料驱动气缸或下料驱动油缸31033驱动l形中转板31032朝向第一接料盒3101运动以带动活动底板31013封闭第一接料盒3101的下开口。可以根据实际工况选择采用下料驱动气缸或下料驱动油缸31033;其中,下料驱动气缸动作速度快且结构轻便,适合于生产工艺速度相对较高、生产效率高的环境使用,以便于快速拉动活动底板31013,进而使物料下落,且由于抽动速度快,对活动底板31013上的物料影响小,物料几乎以原有停留位置下落;下料驱动油缸作用力大,适合于驱动质量相对较大、承载物料相对较多的第一接料盒3101使用,使得第一接料盒3101下开口能够完全打开,使得物料全部掉落,不易出现卡停、开启不完全、物料无法正常下落等的问题。
29.如图11、图12和图13所示,本实施例中,传力板31011与第一水平驱动机构3102之间和/或传力板31011朝向接料内腔的一侧布设有缓冲构造31014;和/或外框板31012朝向接料内腔的一侧布设有缓冲构造31014。缓冲构造31014的上端面与接料内腔的上端面齐平或者高于接料内腔的上端面。由于第一接料盒3101处于悬挑状态,并经由第一水平驱动机构3102和第一下料驱动机构3103进行驱动,并用于承接物料,因此容易受到多方的冲击作用力影响,而通过合理的布设缓冲构造31014,以缓冲和降低第一接料盒3101受到的冲击作用力,进而提高第一接料盒3101甚至整个物料转送装置的使用寿命。另外,将缓冲构造31014的上端面高度设置成高于接料内腔的上端面高度,能够形成朝向接料内腔的导料构造,同时保护接料内腔的上端面不容易受到冲击破坏。可选地,接料内腔中处于第一接料盒3101运动方向的两端布设有缓冲构造31014,且至少一端的缓冲构造31014的上端面高于接料内腔的上端面,由于该两端与第一接料盒3101的运动方向保持一致,因此在运动过程中最容易受到冲击力破坏,而通过布设缓冲构造31014能够有效减缓受到的冲击力破坏,进而提高第一接料盒3101的使用寿命。
30.本实施例中,活动底板的上表面为光面,能够最大限度地减小活动底板与陶瓷坯体物料之间的摩檫力,使得活动底板在运动开启过程中不容易对陶瓷坯体物料产生作用力,避免陶瓷坯体物料受到作用力而发生破裂,进而提高产品的质量;另外还由于活动底板与陶瓷坯体物料之间采用光面配合,当活动底板运动打开时,不容易引起陶瓷坯体物料的跳动或移动,进而避免陶瓷坯体物料从第一接料盒3101上方跳出,而全部从下开口掉落,确保陶瓷坯体物料转送过程的稳定。
31.如图7、图8和图9所示,本实施例中,水平输送收集机构32包括处于陶瓷坯体物料转送机构31与废料转送机构33之间的物料输送带3201、处于物料输送带3201的物料输出端的导料槽3202以及处于导料槽3202的输出端的接料箱3203。可选地,物料输送带3201的布设方向与陶瓷坯体物料转送机构31与热压铸机的排布方向垂直或呈角度布设,以将下落至物料输送带3201上的陶瓷坯体物料输送至远离热压铸机的区域位置,并经由导料槽3202导入至接料箱3203内进行集中收集。第一接料盒3101在第一下料工位的竖向投影完全落于物料输送带3201的输送区域内,以使陶瓷坯体物料可以完全落于物料输送带3201的输送区域范围内,避免掉落至物料输送带3201外。可选地,物料输送带3201两侧布设有用于导料护板,用于防止陶瓷坯体物料掉落至物料输送带3201外。可选地,处于第一下料工位的第一接料盒3101的活动底板的上表面与物料输送带3201的上表面之间的具体为5cm-50cm,防止陶瓷坯体物料掉落时发生冲击力破坏,避免第一接料盒3101与物料输送带3201之间构成彼此的阻碍,同时还为了使陶瓷坯体物料转送机构31和水平输送收集机构32具有足够的布设空间。可选地,物料输送带3201采用橡胶输送带、树脂输送带或硅胶输送带;或者物料输送带3201表面附着有弹性保护层,以防止陶瓷坯体物料掉落时发生刚性碰撞而损伤。接料箱3203内还设有与导料槽3202的输出端位置匹配并用于对下落的陶瓷坯体物料进行柔性承接或弹性缓冲承接并导入至接料箱3203内腔中的保护垫3204;陶瓷坯体物料经由物料输送带3201输送至导料槽3202,经由导料槽3202滑向接料箱3203内腔中,通过在接料箱3203内腔中匹配于导料槽3202的物料输出位置布设保护垫3204,可以缩短陶瓷坯体物料下降的距离,且可以避免陶瓷坯体物料下落时受到刚性冲击力,很好的保护陶瓷坯体物料,进而为后续陶瓷坯体物料的排蜡、烧结并最终获得合格产品提供质量基础保证。
32.本实施例中,物料输送带3201为双向输送机,双向输送机的两端均对应布设有导料槽3202和接料箱3203。为陶瓷坯体物料的输出提供多个方向的选择,提升物料转送输出的效率和转送输出量,进而延长热压铸机的工作时长,利于大批了的陶瓷热压铸生产。
33.如图7、图8和图9所示,本实施例中,废料转送机构33包括用于悬停至第二接料工位以从热压铸机的废料输出端承接废料并转送至第二下料工位输出的第二接料盒3301、与第二接料盒3301连接的用于驱使第二接料盒3301在第二接料工位和第二下料工位之间沿水平方向往复运动的第二水平驱动机构3302、用于驱使悬停至第二下料工位的第二接料盒3301进行下料的第二下料驱动机构3303以及用于承载第二水平驱动机构3302的第二转送支架3304。第二接料盒3301通过第二水平驱动机构3302悬置于第二转送支架3304的靠近热压铸机的一侧。可选地,废料转送机构33可以采用陶瓷坯体物料转送机构31同样的结构,区别在于:废料转送机构33无需考虑废料的破损,仅需要考虑废料能够完全落于输送线路中,防止废料掉出即可。可选地,第二转送支架3304与第一转送支架3104设置成一体成型的整体结构,或者设置成组合拼装成的整体结构。
34.如图7、图8、图9和图10所示,本实施例中,第二水平驱动机构3302包括装配于第二转送支架3304上的第二水平驱动气缸或第二水平驱动油缸33021,第二水平驱动气缸或第二水平驱动油缸33021的动力输出端与第二接料盒3301连接;第二水平驱动机构3302还包括至少一组用于第二接料盒3301水平运动导向和对第二接料盒3301进行辅助支撑的第二导向支撑滑杆33022,第二导向支撑滑杆33022可滑动地装配在第二转送支架3304上且一端与第二接料盒3301固定连接,第二导向支撑滑杆33022与第二水平驱动气缸或第二水平驱动油缸33021平行布设;第二导向支撑滑杆33022的远离第二接料盒3301的一端设有用于确保第二接料盒3301悬停于第二接料工位的第二限位构造33023。可选地,第二水平驱动机构3302可以采用如第一水平驱动机构3102同样的结构。可选地,第二水平驱动机构3302与第一水平驱动机构3102平行布设,且彼此之间留有间距,以方便布设物料输送带3201,为物料输送带3201的布设提供足够的布设空间,即依据物料输送带3201限制第二水平驱动机构3302与第一水平驱动机构3102之间的最小距离;且依据热压铸机内腔的区域空间、热压铸机内模具的运动轨迹以及模具与第一接料盒3101之间的最小间距,以限制第二水平驱动机构3302与第一水平驱动机构3102之间的最大距离。
35.如图7、图8和图9所示,本实施例中,废料收集机构34包括处于陶瓷坯体物料转送机构31和废料转送机构33下方以承载陶瓷坯体物料转送机构31和废料转送机构33的底座3401,底座3401与支架本体1的下方,底座3401上开设有废料入口3402,支架本体1的工作台面上开设有与废料入口3402匹配的开口,第二接料盒3301在第二下料工位的竖向投影完全落于废料入口3402区域内,废料入口3402的下方设有废料导出槽3403,废料导出槽3403的输出端朝向远离热压铸机的方向布设,废料导出槽3403的输出端设有废料箱3404。具体地,底座3401处于废料转送机构33下方;悬置于第二下料工位的第二接料盒3301的下开口完全处于底座3401的废料入口3402区域范围内。可选地,废料入口3402上还设有大端朝向第二接料盒3301的下开口的锥形导料斗,既能够缩短第二接料盒3301下料的距离,同时又能够完全接收第二接料盒3301下料的废料,避免废料掉出。废料入口3402的输出端与废料导出槽3403对接,掉落至废料导出槽3403上的废料随着废料导出槽3403的斜坡面滑落至废料箱3404内。可选地,废料入口3402下方与废料导出槽3403相对的一侧布设有鼓风机,通过鼓风
机鼓风以驱使并加快废料经由废料导出槽3403导出。可选地,鼓风机的输出端与废料导出槽3403的槽底面之间呈角度布设,夹角为30
°‑
80
°
,风并非顺着废料导出槽3403流动,而是作用于废料导出槽3403内壁,以对废料导出槽3403内的物料形成向废料箱3404方向的辅助推动力,且不易使废料携带的粉尘向空气中飞散(利用废料导出槽3403壁体的反射作用以实现降尘的目的);角度过小容易使废料从废料导出槽3403的输出端向外溅射而掉落至废料箱3404外;角度过大容易产生较大的能量损失,且无法推动物料沿着废料导出槽3403导出,而容易产生废料堆积。可选地,废料导出槽3403的内表面成光面。本实施例中,物料输出组件3还包括设于支架本体1上的控制器,控制器分别与陶瓷坯体物料转送机构31、水平输送收集机构32和废料转送机构33电连接。
36.如图17所示,本实施中,活动模组52包括:用于与基础模组51竖向压合以形成浇道并构成陶瓷坯体物料的底部成型模的浇道成型模组53、用于与浇道成型模组53配合以热压铸成型陶瓷坯体物料的坯体成型模组54、与坯体成型模组54插接配合以构成陶瓷坯体物料的顶部成型模并用于通过与坯体成型模相对运动以实现陶瓷坯体物料脱模的坯体顶部插接模组55以及与坯体顶部插接模组55插接配合并依次穿过坯体顶部插接模组55和坯体成型模组54进而伸入至浇道成型模组53内的用于成型陶瓷坯体物料的内孔并通过与浇道成型模组53相对运动以实现冒口从陶瓷坯体物料上断开后脱出的型芯模组56。热压铸机在活动模组52相对于固定的基础模组51上下运动以实现彼此之间的合模配合的基础上,对活动模组52进行改进,基础模组51保持预设的温度,并使配制的混合浆料经由基础模具朝向合模后的活动模组52内加压输出,以实现陶瓷坯体物料的热压注成型。活动模具包括浇道成型模组53,浇道成型模组53既作为与基础模具对接的浇道,浇道处于成型陶瓷坯体物料的内孔所处位置,以使得作为废料的冒口处于内孔位置,充分利用了废弃区域,使得冒口的切除简单化,且冒口去除过程对于陶瓷坯体物料的基体结构影响小,使得基础模组51、活动模组52的模腔布局更为合理;同时又作为陶瓷坯体物料热压铸成型的底模,以使得成型陶瓷配体物料的合模缝处于陶瓷配体物料的侧壁上,相对于合模缝处于转角部位更加方便后续处理去除合模缝并保证外形尺寸精度。活动模具包括处于浇道成型模组53上方,并用于与浇道成型模组53合模形成陶瓷坯体物料成型腔的坯体成型模组54以及与坯体成型模组54插接配合以构成陶瓷坯体物料的顶部成型模的坯体顶部插接模组55,即合模后由坯体顶部插接模组55、坯体成型模组54和浇道成型模组53合共同围合形成陶瓷坯体物料成型腔,进而实现陶瓷坯体物料热压注成型,同时还有利于热压铸成型后的冒口与陶瓷坯体物料的分别脱模并输出,具体地,先在合模状态下活动模组52整体上升并通过型芯模组56使混合浆料冷却凝结成型并使冒口断裂并输出,然后使浇道成型模组53分离,以进行陶瓷坯体物料的脱模输出,最后再通过型芯模组56使活动模组52合模成整体再次进行浇道疏通,以便于进行活动模组52与基础模组51的合模,进行下一批次的混合浆料热压注入。坯体顶部插接模组55还用于通过与坯体成型模的相对运动,以实现陶瓷坯体物料热压铸成型后的脱模,由于坯体顶部插接模组55作为陶瓷坯体物料的顶模,脱模时采用了顶部整面的往复振动推送,进而实现陶瓷坯体物料的脱出,所产生推送作用力作用于陶瓷坯体物料的整个上表面,不容易产生应力集中现象,因此对陶瓷坯体物料的影响小。坯体顶部插接模组55与坯体成型模组54采用插接配合,型芯模组56与坯体顶部插接模组55采用插接配合,且型芯模组56依次穿过坯体顶部插接模组55和坯体成型模组54进而伸入至浇道成型模组53内,且上述各
活动模彼此之间的插接配合、穿设配合均与陶瓷坯体物料的成型区域一一对应并同轴布设,进而实现整个活动模组52中各个活动模彼此之间的定中定位,确保各活动模的动作精度的精准控制,有效降低动作过程中的故障率,从而使得陶瓷坯体物料的热压铸成型质量得以保证,且加工效率也能够得以保证。另外,采用穿设于坯体顶部插接模组55和坯体成型模组54并伸入至浇道成型模组53内的型芯模组56,型芯模组56既能够作为成型陶瓷坯体物料的内孔的芯模,又作为切除处于内孔位置的冒口并将冒口顶出的冒口切除脱模模具;具体地,合模状态的活动模组52整体抬升以基础模组51后进行冷却凝结成型,然后通过型芯模组56往复振动推送,以使冒口从陶瓷坯体物料的内孔位置断裂并被推出,然后再进行陶瓷坯体物料的脱模,最后活动模组52合模后再经由型芯模组56相对于活动模组52向下运动以疏通浇道,进而实现活动模具下压至基础模组51上进行下一批次的混合浆料热压注入。整个结构简单,模具布局合理,活动模组52的活动同轴度能够得以保证,进而确保热压铸成型的陶瓷坯体物料的质量,且冒口设计于陶瓷坯体物料的内孔位置,对陶瓷坯体物料的质量影响小。适用于各种带有通孔的陶瓷坯体物料的批量生产,且能够减少故障率,提升产品良品率,保证产品质量。可选地,活动模组52的底部设有与基础模组51相匹配的导向定位沉槽,活动模组52下压过程中基础模组51经由导向定位沉槽进行定中定位,进而实现活动模组52精准下压至基础模组51上。可选地,控制器分别与基础模组51、活动模组52、浇道成型模组53、坯体成型模组54、坯体顶部插接模组55以及型芯模组56电连接,以实现彼此之间的协调控制。本实施例的热压铸设备自动化程度高,动作精度高,适用于各种带有通孔的陶瓷坯体物料的批量生产,能够减少故障率,提升产品良品率,保证产品质量,提高生产效率。
37.如图17、图18、图19和图20所示,本实施例中,基础模组51上设有主固定框架5101、主滑轨5102以及主驱动装置5103,主滑轨5102和主驱动装置5103呈竖向布设,活动模组52可滑动地布设于主滑轨5102上,主驱动装置5103的固定端固定于主固定框架5101上,主驱动装置5103的动力输出端连接并固定在活动模组52,用于驱动活动模组52整体上升远离基础模组51或整体下降压合于基础模组51上。主驱动装置5103与主滑轨5102平行布设;通过主驱动装置5103驱动活动模组52整体相对于基础模组51进行下压动作或抬升动作,通过活动模组52与主滑轨5102之间的滑动配合,既能够确保活动模组52动作过程的稳定性,同时确保动作精度。可选地,主驱动装置5103采用直线式液压油缸或直线式液压气缸。
38.如图17、图18、图19和图20所示,本实施例中,浇道成型模组53包括滑动布设于主滑轨5102上的浇道基板5301以及设于浇道基板5301上的浇道模5302,浇道模5302的底部开设有用于与基础模组51的混合浆料输出口一一对应布设的浇道,浇道模5302的上表面开设有用于与陶瓷坯体物料的底部外形相匹配的坯体沉槽,浇道与坯体沉槽一一对应布设,浇道与对应的坯体沉槽连通且浇道连通至坯体沉槽的连通部位处于成型陶瓷坯体物料的其中一个内孔所在位置。在浇道模5302的底部开设浇道,并在浇道模5302的上部开设坯体沉槽,既能够使得热压铸成型的陶瓷坯体物料的合模缝处于外侧壁上以便于后期加工去除;同时还为了使浇道模5302本身的加工精度更高,由于浇道的设计位置需要处于陶瓷坯体物料的内孔所处位置,如果单纯仅在浇道模5302上开设浇道,很难使浇道模5302的浇道与坯体成型模组54上的陶瓷坯体物料成型腔的内孔位置对应,而将浇道和坯体沉槽分别设置在浇道模5302的上下表面,能够精准的控制浇道处于陶瓷坯体物料成型腔的内孔位置,进而提高陶瓷坯体物料的成品质量。主驱动装置5103的动力输出端连接并固定在浇道模5302上
和/或浇道基板5301上。可选地,浇道模5302由基础模组51向活动模组52方向呈下沉式的设置在浇道基板5301上;即浇道基板5301朝向基础模组51的方向形成一个下沉式的导向定位沉槽,浇道模5302处于导向定位沉槽内。具体地,当活动模组52朝向基础模组51方向移动下压时,先由导向定位沉槽容纳基础模组51的流道底模5106,并对流道底模5106进行导向定位,然后才使得浇道模5302与流道底模5106进行合模形成组合浇道。
39.如图17、图18、图19和图20所示,本实施例中,浇道模5302内还布设有环绕于浇道和坯体沉槽外的用于流通冷却介质以对浇道和坯体沉槽内的混合浆料进行冷却的冷却通道57。当活动模组52下压至基础模组51上并完成热压注入混合浆料后,活动模组52整体上升,此时通过向冷却通道57泵入冷却介质以使混合浆料冷却凝结成型,然后抽出冷却介质;通过冷却介质的流量及流速控制,以实现对混合浆料的降温控制,进而控制陶瓷坯体物料热压铸成型凝结的降温梯度控制;再依次进行冒口切除及输出、开模后的陶瓷坯体物料的脱模输出、合模后的浇道疏通以及活动模组52下压至基础模组51进行依次循环的混合浆料热压注入。浇道模5302的上表面设有用于坯体成型模组54相对靠近时进行导向和定位的合模定位孔或合模定位销58。可选地,合模定位销的自由端设置成球面,当合模接触时先与球面接触,实现导向,进而再完全匹配连接实现彼此之间的定位。可选地,合模定位孔的孔口转角设置成弧形角或倒角,且孔底设置成凹球面,当合模接触时先与孔口的弧形角或倒角接触,实现导向,进而再完全匹配连接并与孔底的凹球面进行进一步的导向和定位。浇道基板5301上设有用于感应浇道成型模组53移动靠近基础模组51时的相对距离并感应从热压铸模具组件外伸入并靠近浇道成型模组53的相对距离的距离传感器59。控制器接收距离传感器59输出的信号,以判断浇道基板5301下压至与基础模组51的预设距离以及下压后保持的时间,进而实现对活动模组52下压或上升的过程精准控制。距离传感器59布设于浇道基板5301的靠向热压铸模具组件外的部位布设;当外界有人或者物体经过距离传感器59并进入到活动模组52活动范围时,距离传感器59输出相应信号至控制器,控制器依据该信号控制热压铸模具组件停机,以避免产生风险,起到为安全考虑的停机的目的。
40.如图17、图18、图19和图20所示,本实施例中,坯体成型模组54包括滑动布设于主滑轨5102上的坯体成型框架5401、呈竖向的设于坯体成型框架5401上的用于驱使坯体成型框架5401移动相对靠近浇道成型模组53或移动相对远离浇道成型模组53的坯体成型驱动装置5402以及设于坯体成型框架5401上的坯体模5403,坯体模5403与浇道成型模组53相对布设。坯体模5403上开设有上下贯通的用于坯体顶部插接模组55插接配合并成型陶瓷坯体物料的贯通腔孔,贯通腔孔与浇道成型模组53的坯体沉槽一一对应布设并上下贯通配合以形成完整的陶瓷坯体物料成型腔。浇道成型模组53和坯体成型模组54的上下滑动均处于主滑轨5102上,即滑动基准保持一致。坯体成型框架5401可滑动地布设于主滑轨5102上,并通过坯体成型驱动装置5402驱动坯体成型框架5401上下移动,而坯体模5403处于坯体成型框架5401,即通过坯体成型驱动装置5402驱动坯体成型框架5401并带动坯体模5403与浇道成型模组53合模;具体地,坯体模5403与浇道成型模组53的浇道模5302合模,并使坯体沉槽与贯通腔孔一一对应并合模构成陶瓷坯体物料的成型腔;而坯体顶部插接模组55作为陶瓷坯体物料的成型腔的顶模。通过控制坯体顶部插接模组55在贯通腔孔内的插接位置,以控制陶瓷坯体物料的厚度,进而实现不同厚度的陶瓷坯体物料的热压铸成型。坯体成型驱动装置5402采用直线式液压油缸或直线式液压气缸。
41.如图17、图18、图19和图20所示,本实施例中,坯体模5403内还布设有环绕于贯通腔孔外的用于流通冷却介质以对贯通腔孔内的混合浆料进行冷却的冷却通道57。当活动模组52下压至基础模组51上并完成热压注入混合浆料后,活动模组52整体上升,此时通过向冷却通道57泵入冷却介质以使混合浆料冷却凝结成型,然后抽出冷却介质;通过冷却介质的流量及流速控制,以实现对混合浆料的降温控制,进而控制陶瓷坯体物料热压铸成型凝结的降温梯度控制;再依次进行冒口切除及输出、开模后的陶瓷坯体物料的脱模输出、合模后的浇道疏通以及活动模组52下压至基础模组51进行依次循环的混合浆料热压注入。坯体模5403的下表面设有用于相对靠近浇道成型模组53时进行导向和定位的合模定位孔或合模定位销58。可选地,合模定位销的自由端设置成球面,当合模接触时先与球面接触,实现导向,进而再完全匹配连接实现彼此之间的定位。可选地,合模定位孔的孔口转角设置成弧形角或倒角,且孔底设置成凹球面,当合模接触时先与孔口的弧形角或倒角接触,实现导向,进而再完全匹配连接并与孔底的凹球面进行进一步的导向和定位。
42.如图17、图18、图19和图20所示,本实施例中,坯体顶部插接模组55包括呈竖向的设于坯体成型框架5401上的坯体脱模驱动装置5501、设于坯体脱模驱动装置5501的动力输出端的坯体脱模压板5502以及布设于坯体脱模压板5502的下表面的用于插接悬置于贯通腔孔内以配合热压铸成型陶瓷坯体物料并上下动作以实现陶瓷坯体物料脱模的坯体顶模5503,坯体顶模5503与贯通腔孔一一对应布设。陶瓷坯体物料进行热压铸成型前,通过坯体脱模驱动装置5501控制坯体顶模5503在贯通腔孔内的悬置位置,以控制陶瓷坯体物料的厚度。陶瓷坯体物料热压铸成型后,并处于陶瓷坯体物料的脱模输出阶段时,通过坯体脱模驱动装置5501驱动坯体脱模压板5502并带动坯体顶模5503往复动作产生振动力和推动力,以逐步顶推陶瓷坯体物料,进而实现陶瓷坯体物料的脱模和输出,同时对陶瓷坯体物料的刚性破坏小。坯体脱模驱动装置5501通过呈板状的坯体脱模压板5502均匀地向各个坯体顶模5503施力,以使得坯体顶模5503分别对对应的贯通腔孔内的陶瓷坯体物料施加往复振动力和顶推力。可选地,坯体脱模驱动装置5501采用直线式往复电机、直线式往复气缸、直线式往复油缸、无杆气缸等,或者采用现有的类似驱动装置。
43.如图17、图18、图19和图20所示,本实施例中,型芯模组56包括呈竖向的布设于坯体成型框架5401上的型芯驱动装置5601、呈竖向的布设于坯体成型框架5401上的辅助滑轨5602、可滑动地布设于辅助滑轨5602上并固定在型芯驱动装置5601的动力输出端上的型芯基板5603以及设于型芯基板5603下表面的型芯杆5604。型芯杆5604与坯体顶模5503是插接套设关系,坯体顶模5503套设于型芯杆5604外并实现彼此之间的滑动配合。通过型芯驱动装置5601施加作用力,以使型芯基板5603相对于坯体成型框架5401而在辅助滑轨5602上滑动,以及使型芯杆5604在陶瓷坯体物料的成型腔悬停以作为陶瓷坯体物料的内孔成型芯模,进而实现型芯杆5604对处于陶瓷坯体物料的内孔位置的冒口进行切除动作、浇道疏通动作或者充当内孔芯模的三重功能。型芯杆5604穿设于坯体顶模5503内并朝向浇道成型模组53方向延伸,且型芯杆5604与陶瓷坯体物料的内孔的成型位置一一对应布设,型芯杆5604与陶瓷坯体物料的内孔一一对应布设,以作为内孔成型的芯模。同一陶瓷坯体物料的成型位置的型芯杆5604的延伸长度不同,其中相对较短的型芯杆5604与浇道成型模组53的浇道对应布设,以使混合浆料经浇道从型芯杆5604与浇道之间的间隙流入进而热压铸成型陶瓷坯体物料,而相对较长的型芯杆5604顶抵于浇道成型模组53的坯体沉槽的槽底。陶瓷
坯体物料具有多个内孔,其中一个内孔位置布设有浇道,而用于成型该内孔的型芯杆5604需要留有供混合浆料注入陶瓷坯体物料成型腔的注入间隙,因此该位置处的型芯杆5604相对于其他位置的型芯杆5604的相对长度较短;而其他位置由于没有布设浇道,因此需要成型完整的内孔,型芯杆5604需要伸入至浇道成型模组53内并与浇道成型模组53的坯体沉槽的槽底顶抵接触。可选地,型芯驱动装置5601采用直线式往复电机、直线式往复气缸、直线式往复油缸、无杆气缸等,或者采用现有的类似驱动装置。
44.如图17、图18、图19和图20所示,本实施例中,基础模组51包括基座5104和流道底模5106,流道底模5106固定于基座5104的上表面并与浇道成型模组53上下相对布设,加料装置2通过保温输送管路51064连通至流道底模5106,基座5104内布设有用于为保温输送管路51064或流道底模5106的至少一个供热保温的供热保温装置。流道底模5106内设有主流道51061、副流道51062和输出通道51063,主流道51061与保温输送管路51064连通,且主流道51061分别与副流道51062连通,副流道51062连通至输出通道51063,输出通道51063与活动模组52上的浇道一一对应布设。由于混合浆料配置过程以及输送过程需要保证预设的温度,否则容易发生凝结,因此相应地,流道底模5106需要确保混合浆料保持预热温度,需要设置相应地保温系统,保温系统可以采用现有热压铸机公知常用的热浴系统。
45.如图1所示,本实施例中,支架本体1上设有用于调整所述物料输出组件3的朝向和/或高度的调整机构4,调整机构4包括用于承载物料输出组件3的支撑板41、用于调整支撑板41的朝向的转动机构42和/或调整支撑板41高度的升降机构43。可选地,支撑板41的初始位置与支架本体1的工作台面齐平,升降机构43通过支撑板41调节物料输出组件3的上下高度时,支架本体1的工作台面为支撑板41的竖向最低位置,此时,支撑板41的竖向投影形状可以是任意形状,调整机构4贯穿支架本体1的工作台面与支撑板41连接,即可驱动支撑板41旋转和/或升降。可选地,支撑板41的初始位置与支架本体1的工作台面齐平,支架本体1的工作台面上开设于支撑板41相匹配的开窗,此时,支撑板41的竖向投影形状为圆形,调整支撑板41的高度时,支撑板41的边缘与支架本体1的工作台面出现缝隙,工作台面上的物品易从缝隙落入工作台面下方,可能损坏调整机构4,因此,在支撑板41的边缘和/或开窗的边缘设置竖向的侧板,以避免杂物损坏调整机构4。
46.如图1、图2、图14、图15和图16所示,本实施例中,转动机构42包括设于支撑板41上且与支撑板41转动连接的转动盘4201,转动盘4201或支撑板41上布设用于限制转动盘4201转动的限位机构4202。可选地,支撑板41与转动盘4201同轴设置,支撑板41和转动盘4201上均开设有限位孔,限位孔一一对应布设并上下贯通,支撑板41转动至合适位置后,将限位插销插入支撑板41和转动盘4201上的限位孔,从而限制支撑板41与转动盘4201的相对转动。可选地,支撑板41或转动盘4201沿周向布设限位孔,支撑板41转动至合适位置后,将限位插销插入沿周向布设限位孔即可限制支撑板41与转动盘4201的相对转动。可选地,限位机构4202还可以是与限位孔匹配的限位螺栓、限位弹片或限位挡块,这种限位方式结构简单,成本低。可选地,限位机构4202为齿轮齿条机构(包括驱动和限位)、蜗轮蜗杆机构(包括驱动),旋转电机、伺服电机或舵机,通过驱动+自带定位的方式进行限位,自动化程度高,调整精度高。
47.如图1、图2、图14、图15和图16所示,本实施例中,升降机构43沿竖向安装于支架本体1上,升降机构43的顶部与支撑板41的底部连接,以调整支撑板41的高度。升降机构43包
括呈竖向布设的伸缩杆4301和用于固定伸缩杆4301支撑高度的定位件4302,伸缩杆4301的一端安装于支架本体1上,另一端与支撑板41的底部连接;或者升降机构43为设于支撑板41底部的调节支撑螺栓4303,调节支撑螺栓4303与支架本体1通过螺纹连接;或者升降机构43为剪式支架4304,剪式支架4304的一端安装于支架本体1上,另一端与支撑板41底部连接,以调整支撑板41的高度。这种调整机构4仅调节整物料输出组件3的朝向和/或高度,调节精度高。调整机构4包括用于使支架本体1移动行走的万向轮44和用于支架本体1移动行走后进行固定定位的支撑件45,支撑件45使支架本体1整体抬升以使万向轮44离地,进而实现支架本体1的固定定位。通过万向轮44可改变整个支架本体1的朝向,从而调整物料输出组件3的朝向,调整到位后,支撑件45抵顶底面,使得支架本体1整体抬升,万向轮44离地支架本体1定位完成,这种调整机构4结构简单,适合移动整个支架本体1的朝向和/或高度。支撑件45沿竖向布设,支撑件45为气动撑脚、液压撑脚或升降机;支架本体1上设有用于遮挡热压铸机的背面和远离物料输出组件3一侧的防护网102,热压铸机的正面设有两个相对的光栅,光栅受到遮挡时,压铸组件会强制停止压合动作,以免伤到工人的手部;物料输出组件3从热压铸机的一侧进出压铸组件,将收集坯料和废料并分别转送;为了保障压铸组件和工人的人身安全,在热压铸机不需要进出操作的立面设置防护网102,防护网102能阻隔体积较大的杂质及工人的肢体进入热压铸机的压铸组件,为提供稳定的生产环境。
48.如图3所示,本实施例中,所述支架本体1上设有用于支承给热压铸机5供给浆料的加料装置2,加料装置2包括物料容器21,物料容器21上设有用于对物料容器21内腔中的物料进行搅拌的搅拌组件22以及处于搅拌组件22侧向的用于通过向物料容器21的底部冲压的方式将物料容器21内的物料向外冲压泵送的冲压机构23,物料容器21的底板上设有用于冲压机构23对应布设的导料沉槽24,导料沉槽24的下部连接有用于将物料输送至热压铸模具内的物料输送管道25。本发明用于热压铸设备的加料装置2,采用物料容器21作为瘠性陶瓷原料与热石蜡熔液混合浆料的盛装容器,形成相对封闭的空腔,以防止外界杂质进入,同时确保空腔内的混合浆料的所处环境处于稳定,特别是特别是确保温度环境趋于稳定,减少混合浆料发生分散或凝结的几率;同时,通过在物料容器21上安装搅拌组件22,实时的对物料容器21内的混合浆料进行搅拌,以防止混合浆料分散或凝结;通过在搅拌组件22的侧向布设冲压机构23,冲压机构23采用竖向冲压的方式,冲压动作过程完全在混合浆料内完成,不会带入空气而产生气泡,并且定时定量、预设冲击力的将盛装容器内的混合浆料通过物料输送管道25压送至热压铸模具内,即热压铸模具合模后进行冲压机构23的冲压动作,进而确保热压铸得到的陶瓷产品的密度和质量稳定。由于冲压送料部分处于搅拌组件22的侧向,混合浆料缓慢加入物料容器21后先逐步落入至搅拌区域经搅拌组件22搅拌,以使混合浆料保持混合状态并使混合浆料中可能含有的气泡(空气)逐步向外溢出,并且经由搅拌组件22的搅拌作用进而产生离心力,使混合浆料呈螺旋状的逐步向冲压机构23方向移动,搅拌过程与冲压过程彼此之间的相互影响小,并且彼此之间产生的互补的作用效果,即搅拌组件22确保混合浆料保持混合并排出气体,冲压机构23将搅拌处理过的混合浆料冲压输出,因此可以适时且缓慢的向搅拌区域进行加料,以确保物料容器21内的物料量,使得物料容器21内的物料量始终高于冲压区域,避免冲压机构23的动作过程压入空气。整个结构简单,冲压输送的物料量能够得到稳定且精准的控制,进而确保热压铸成型的陶瓷产品的密度和质量稳定,从而得到合格的陶瓷产品,且陶瓷产品的合格率得以保证。可选地,冲压机
构23的冲压行程可控和/或冲压作用力可控。可选地,搅拌组件22的搅拌速度可控。可选地,冲压机构23设置有多组,多组冲压机构23分别为多个热压铸模具冲压送料。可选地,搅拌组件22的搅拌速度为40rpm~200rpm,确保混合浆料处于混合状态,且能够使得混合浆料内的气泡逐渐溢出,同时不容易带入空气;搅拌速度过快,超过200rpm,容易带入空气,且使搅拌区域外围出现固液分离、分散现象;搅拌速度过慢,低于40rpm,无法使混合浆料保持混合状态而发生分散现象,同时容易使搅拌区域以外的混合浆料出现凝固的现象。可选地,导料沉槽24采用与冲压机构23相匹配的槽。可选地,导料沉槽24外围设置为锥形结构或者台阶形结构。可选地,导料沉槽24设置为弧形沉槽、半球形沉槽、半椭圆形沉槽、圆锥形沉槽或圆柱形沉槽。可选地,导料沉槽24设置为上部为圆柱形,下部为弧形、半球形、半椭圆形、圆锥形。可选地,物料容器21的内壁面和/或外壁面和/或壁体基体内设有保温隔热层。可选地,物料容器21的内壁面还附着有防止物料粘附的涂层。可选地,物料容器21外表面设有用于使使混合浆料保持流动性且不发生凝结的稳定温度的温控装置。可选地,温控装置采用布设于物料容器21外的电热模块,以及布设于物料容器21内腔的温度传感器,以及分别与电热模块和温度传感器电连接的温度控制器。可选地,温控装置采用布设于物料容器21外的热蒸汽系统以及布设于物料容器21内腔的温度传感器,热蒸汽系统用于对物料容器21提供热蒸汽,以与物料容器21内腔进行热交换,使物料容器21内腔均匀受热,进而实现物料容器21内腔的温度控制。可选地,温控装置采用布设于物料容器21外的热油系统以及布设于物料容器21内腔的温度传感器,热油系统用于对物料容器21提供热油浴环境,以与物料容器21内腔进行热交换,使物料容器21内腔均匀受热,进而实现物料容器21内腔的温度控制。
49.如图3、图4(a)、图4(b)、图4(c)和图4(d)所示,本实施例中,冲压机构23包括固设于物料容器21顶板上的冲压驱动装置2301、与冲压驱动装置2301的输出端连接并伸入至物料容器21内腔中的转接杆2302以及处于转接杆2302端部的冲压塞2303,冲压驱动装置2301、转接杆2302和冲压塞2303沿竖向布设。整个冲压机构23采用竖直方向布设,即冲压驱动装置2301的沿竖直向下的输出动力,并经由转接杆2302传递向下冲压力,使冲压塞2303向导料沉槽24内冲压。可选地,冲压驱动装置2301采用冲压气缸或者冲压液压缸。冲压塞2303的冲压面朝向导料沉槽24方向布设,冲压塞2303的冲压面为弧形面、球面或锥面。如图4(a)和图4(b)所示,冲压塞2303的冲压面为弧形面。图4(c)和图4(d)所示,冲压塞2303的冲压面为锥面。导料沉槽24的径向截面形状与冲压塞2303的竖向投影形状相匹配,导料沉槽24的槽底面形状与冲压塞2303的冲压面形状相匹配,物料输送管道25从导料沉槽24的槽底面连通至导料沉槽24的内腔;导料沉槽24的槽深与冲压塞2303的轴向高度相匹配,或者导料沉槽24的槽深大于冲压塞2303的轴向高度。当导料沉槽24的槽深大于冲压塞2303的轴向高度,可以通过调节冲压塞2303的行程,进而控制冲压输送量,进而适应于不同的冲压输送要求;例如,换上内腔空间相对较大的热压铸模具时,冲压塞2303的行程增加;换上内腔空间相对较小的热压铸模具时,冲压塞2303的行程减小。当导料沉槽24的槽底面形状与冲压塞2303的冲压面形状相匹配时,可以实现定量的冲压输送,以确保热压铸成型的陶瓷产品密度和质量稳定。可选地,导料沉槽24设置成阶梯形构造,进而可以匹配于不同尺寸型号的冲压塞2303。可选地,导料沉槽24设置成圆锥形沉槽,且圆锥形沉槽尺寸大于冲压塞2303,进而可以匹配于不同尺寸型号的呈锥体的冲压塞2303。可选地,冲压塞2303的行程长度为10mm~150mm。物料输送管道25、导料沉槽24、冲压塞2303、转接杆2302以及冲压驱动装置
2301同轴布设。以使得冲压作用力沿竖直方向地直线输出,既能够向物料输送管道25均匀地向冲压输送物料,同时冲压过程中使周边的物料均匀地翻滚并进而向冲压区域补充物料,避免产生乱流、旋流而影响物料输送,进而确保热压铸成型的陶瓷产品的密度和质量稳定,从而得到合格的陶瓷产品,且陶瓷产品的合格率得以保证。
50.如图3所示,本实施例中,物料容器21与支架本体1的工作台面围合形成容纳腔,支架本体1的上方开设有用于向物料容器21内加料的加料口2101,加料口2101上封盖有盖板26,以便于向物料容器21内及时补充物料。可选地,加料口2101竖向正对于搅拌组件22的搅拌区域,以使得物料直接落入搅拌区域,并维持混合状态并充分排出气泡,然后通过搅拌产生的离心力缓慢向冲压机构23方向流动,进而被冲压输出。可选地,盖板26内侧布设有保温隔热层。加料口2101呈半圆状,加料口2101的直线边上还开设有用于方便搅拌组件22拆装的避让槽2102,搅拌组件22沿径向插装至避让槽2102内并固定于物料容器21的顶板上。盖板26与加料口2101的形状相匹配,且盖板26的直线边沿板面向外延伸形成用于盖合于部分避让槽2102的延伸部2601,以封闭物料容器21,确保物料容器21形成相对封闭的空腔。可选地,盖板26与加料口2101之间还设有密封圈。加料口2101上设有用于从底部支撑盖板26边缘的支撑台阶21011,和/或盖板26与加料口2101之间设有插接配合件21012或卡接配合件,和/或盖板26与加料口2101之间通过铰链可转动地连接。确保盖板26能够快速封闭且密封加料口2101,避免外界杂质落入,同时避免物料容器21内温度降低。
51.如图3、图5和图6所示,本实施例中,搅拌组件22包括固设于物料容器21顶板上的搅拌驱动装置2201、设于搅拌驱动装置2201的动力输出端并伸入至物料容器21内腔中的转动桨轴2202以及布设于转动桨轴2202上的搅拌桨2203。搅拌桨2203包括搅拌主框22031和搅拌副框22032;搅拌主框22031的搅拌轨迹大于搅拌副框22032的搅拌轨迹,以形成呈空间的立体搅拌效果,使各个搅拌区域内的各个区域均能够受到搅拌力的作用,确保物料处于混合状态,并使气泡容易溢出。如图5所示,搅拌主框22031与搅拌副框22032呈平板框,组合构成沿径向方向的内外双层搅拌。如图6所示,搅拌主框22031与搅拌副框22032呈十字交叉布设,组合构成呈立体的搅拌构造,能够全范围的接触到搅拌区域内的物料并进行搅拌。根据需要,选择搅拌桨2203不同的组合构造,以适应于不同的搅拌需要。搅拌主框22031和/或搅拌副框22032由板片组合构成,板片的宽度方向沿搅拌桨2203转动轨迹的切线方向布设,使得搅拌过程中,能够非常平缓的搅拌物料,避免带入空气。
52.以上仅为本发明的优选实施例而已,并不用于限制本发明,对于本领域的技术人员来说,本发明可以有各种更改和变化。凡在本发明的精神和原则之内,所作的任何修改、等同替换、改进等,均应包含在本发明的保护范围之内。