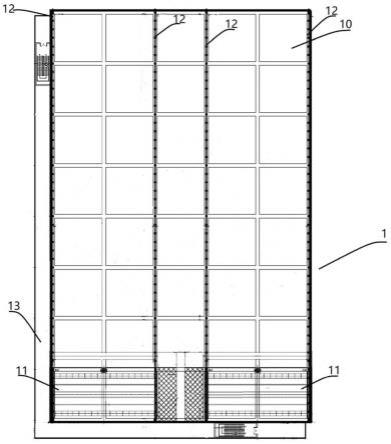
1.本发明涉及垃圾填埋场的建造领域,尤其是涉及一种露天填埋场系统。
背景技术:2.随着中国经济的快速发展,大量的人口涌入城市,城市的规模和域界不断扩大,我们在享受繁荣的同时,也正经受生存环境不断恶化带来的后果,一方面城市人口激增,生活垃装也剧增,我国城市垃圾的处理方法自前还比较单一,其主要方法是填埋,约占整小垃圾处理方法的90%以上,焚挠仅占很少部分,因而导致属于填埋垃圾的土地资源越来越紧缺,垃圾与人们争取空间的矛盾越来越激化;另一方面,我国所采用的填埋方法基本上是随意堆放的方法,未经无害化处理,原来处于城市边缘的垃圾填运场正成为新的城市中心,未经处理的填埋场不断散发臭气,蚊蝇滋生,造成严重的空气污染,不断释放曲沼气给附近生活的居民带来安全隐患。
3.未经处理的垃圾填埋物一般存在以下的直接危害:
4.1、垃圾场不断散发的恶臭气体主要由甲烧(又称沼气)和其也有毒有害气体组成。甲烷是一种高效的燃料,但如果处理不当,在近居民区释放,一旦遭遇火星易燃易爆,给生命和财产带来威胁;另一方面,甲烷也是一种温室效应很强的气体〈是二氧化碳的二十倍),若大量对空中直接排放,容易对大气臭氧层造成破坏,导致人类赖以生存的大气环境变坏。
5.2、垃圾填埋场渗透出的沥出液包含垃圾中所有的有毒成分,如重金属、高有机复合物、有害细菌、邮寄病菌等,如果不加处理,很容易造成填埋场下游土壤破坏,或污染下游地下水甚至水萍饮用水,特到是在下雨天污水横流。
6.自前国内外对垃圾填埋场的渗沥液一般的处理过程是在排放之前对其进行一系列的生化处理,包括清除有礼物、不溶物、无机物处理。
7.目前常用的渗沥液处理过程为,由生化反应罐、过滤器、第一阶段反渗透罐、第二阶段反渗透罐、描水泵等组成,根据垃圾填埋场的规模和降雨量,每个垃圾填埋场的渗沥液排放量介于5000至30000立方米之间.设备投入的资金非常高,其每一个设备的投入在15万至100万人民币之间,总投资资金介于1500万到1亿人民币之间。在中国,建设一个适中的渗沥液污水处理厂平均投资约4000万人民币。
8.公开号为cn 112871946 a的一项中国发明申请专利公开了一种密封型井式垃圾场填埋场气体排放结构,包括若干井式填埋堆,所述井式填埋堆截面呈矩形,各个所述井式填埋堆内壁从上至下间隔均匀设置有若干气液导出口,所述气液导出口通过垂直设置于井式填埋堆侧壁内的分离通道连通,若干所述气液导出口内通过转轴活动安装有密封扇形板,所述密封扇形板位于分离通道一侧固定安装有挤压弹簧,本发明通过井式填埋堆的设置,相较于开放式露天分层覆土填埋方式而言,废气的溢散情况更容易管控,同一井式填埋堆内不同高度区域的垃圾均能进行发酵废物和渗沥液的回收,使得渗沥液和废气的疏散更加均匀,便于集中进行收集处理,大大提高了垃圾填埋选址周围地下水和空气质量状况。但是该技术方案整个填埋场缺乏刚性,不适用于吨级垃圾填埋的处理,在实际操作过程中无
法确保按照国家标准处理垃圾填埋场产生的有害物质。
9.综上所述,现有技术的处理过程存在以下的不足:
10.1、投资额很大,国内地方财政难以承受,在国内难以推广蓝用。
11.2、该处理过程依然会产生污泥、高浓度污水,仍需要采取垃获填埋和其他后续处理方法;处理过程由于采用化学物,会造成二次污染。
12.3、持续支出的日常运营费用很高。
13.4、渗沥液与雨污水不分,大大加重了系统的处理负荷,浪费了部分投资和自常运营费用;特到是对于多雨的南方地区,浪费比例更高。
14.5、需额外占用土地资源。
15.由上可知,目前亟需开发一种刚性填埋系统,项目费用合理又能解决上述问题,适合我国垃圾填埋场的广泛推广。
技术实现要素:16.本发明的目的是为了解决上述问题,提供一种投入成本低、社会机经济效益好的刚性垃圾填埋场系统。
17.为实现上述目的,本发明提供了一种露天填埋场系统,包括:填埋场,为高于地面的钢筋混凝土露天建筑,填埋场包括多个阵列式排布的填埋单元,填埋单元的内壁附有防渗结构,填埋单元的顶部设有封闭结构;沿填埋场露天的一面的列项混凝土壁的顶端铺设有至少两条相对平行的轨道;至少一个吊车平台装置,包括装吊支撑平台和位于装吊支撑平台底部的移动组件,移动组件与轨道相适配并能沿所述轨道前进;装吊支撑平台上设有悬吊工位,悬吊工位上安装有定柱悬臂吊起重机;其中,填埋单元底部还设有导排系统,用于渗沥液的导排外运。
18.根据本技术的实施例,防渗结构包括所述填埋单元侧壁的防渗结构和底部的防渗结构,侧壁的防渗结构从内向外依次设置为0.35m钢筋混凝土隔墙、3mm纤维增强塑料、600g/m2长丝聚酯土工布、2.0mmhdpe单糙面土工膜、600g/m2长丝聚酯土工布;底部的防渗结构从下至上依次为钢筋混凝土底板、3mm纤维增强塑料、600g/m2聚酯土工布、2.0mmhdpe光面土工膜、600g/m2聚丙烯过滤有纺土工布、6.3mm土工复合排水网、200g/m2pe土工滤网。
19.根据本技术的实施例,填埋单元设有防渗加固装置,防渗加固装置包括环绕填埋单元内壁中部设置以及位于填埋单元开口端外围的锚固装置。
20.根据本技术的实施例,锚固装置包括镀锌扁铁和对镀锌扁铁的两端、中部进行固定的射钉,射钉与镀锌扁铁的连接处进行了焊接加固。
21.根据本技术的实施例,导排系统包括导流坡、导流管和排水泵,导流坡位于填埋单元的底面并与填埋单元的底面成2%的坡度;导排管沿导流坡的坡底邻接的填埋单元的侧壁设置,并且与填埋单元的底面垂直,导排管的进口设有导流口伸向坡底;排水泵的进水口连接导排管的出口,排水泵的出口连接回收装置。
22.根据本技术的实施例,横向相邻的两个填埋单元的导流坡相向设置,纵向相邻的导流坡同向设置,从而使得阵列式排布的4个填埋单元的渗沥液向一处汇集。
23.根据本技术的实施例,导排管采用hdpe膜带焊接的方式固定到所述填埋单元的内壁上。
24.根据本技术的实施例,定柱悬臂吊起重机包括立柱、横梁、环链电动葫芦和驱动系统,立柱底部固定安装在悬吊工位上;横梁可旋转地安装在立柱的顶部并与立柱相垂直;环链电动葫芦沿横梁设置;驱动系统包括3个电机,其中一个电机用以驱动横梁以立柱为轴心进行360度的回转,另外两个电机分别用以驱动环链电动葫芦沿横梁做水平运动和垂直于横梁做上下运动。
25.根据本技术的实施例,封闭结构由下至上依次为导气层、防渗层和阻隔层,导气层采用砂砾导气层,并在导气层内安装气体导出管;防渗层采用高密度聚乙烯防渗膜,高密度聚乙烯防渗膜下层采用长丝聚酯土工布做为膜下保护层;高密度聚乙烯防渗膜上层采用600g/
㎡
长丝聚酯土工布做为膜上保护层;阻隔层采用防渗钢筋混凝土。
26.根据本技术的实施例,填埋场在周边及底层设置有目视检测通道,所述目视检测通道采用钢筋混凝土框架结构。
27.本发明技术方案相对于现有技术的有益效果是:
28.1、本技术的露天刚性填埋场,利用刚性填埋场本体单元作为吊车的承载,实现吊车的全方位移动,通过用吊车平台代替顶棚、协同渗沥液处理等方式,使得其建设费用、设备费用大大低于常规的填埋场,运营人员也显著减少,大大降低了运营费用。
29.2、本发明对每个填埋单元设置了导排系统,可以将雨污水和渗沥液分开处理,对于没有填埋物的填埋单元导出雨污水满足周边生产用水需求,已填埋的单元导出渗沥液通过外运处置,大大降低了处理系统的负荷,节省了投入和日常运营费用,提高了投资和使用效益
30.3、由于填埋场需要用水来完成垃圾的无害化过程,雨水的收集和运用,加快了填埋场垃圾的生化反应过程,节省了资源,实现刚性填埋的多功能及集约型的经济效益,提高了刚性填埋场的整体经济效益。
31.4、本技术的处理系统设备简单,只需建设填埋场,占地少。
32.5、本技术的防渗结构加固方法采用1500*40*4mm的镀锌扁铁与3条m10射钉,射钉处补焊的组合模式,价格便宜,施工方便,并具有较好的力学和耐久性能。
附图说明
33.图1本发明实施例的填埋场的俯视图;
34.图2为本发明实施例的工艺流程图
35.图3为本发明实施例中一阵列填埋场的导流示意图;
36.图4为本发明实施例中导排系统的结构示意图;
37.图5为本发明实施例的应用场景图。
38.附图标记说明如下:
39.1.填埋场,10.填埋单元,11.吊车平台装置,12.轨道,13.人行平台,14.目视检测通道,101.导排管,102.hdpe膜带,103.导流坡,1011.导流口。
40.其中,附图上的箭头代表液体流向。
具体实施方式:
41.下面结合附图和具体实施例对本发明作进一步说明。以下实施例用于说明本发
明,但不用来限制本发明的范围。
42.请参见图1、图3、图4和图5所示,示出了一种露天填埋场系统,包括填埋场1、与填埋场1匹配的吊车平台装置11以及设置在填埋场1内部的导排系统。
43.填埋场1主体采用钢筋砼水池结构浇筑,后期封场采用预制混凝土板封场。为便于日后巡查,及时发现填埋场1渗沥液产生、设施运营情况等,在填埋场1周边及底层设置有目视检测通道14,通道采用钢筋混凝土框架结构。根据人体平均视线高度1.5m,考虑观察时最高角度约30
°
,故可得出目视检测层高2.1m,检修夹层为主体下部混凝土柱支撑的空间。检修夹层地坪表面设环氧树脂层,防止事故时渗漏的污水进入地下土层及水体。
44.填埋场1包括多个阵列式排布的填埋单元10,填埋单元10的内壁附有防渗结构,填埋单元10的顶部设有封闭结构;沿所述填埋场1露天的一面的列项混凝土壁的顶端铺设有至少两条相对平行的轨道12。
45.本实施例中,填埋场1设计为:每个标准填埋单元10区域内部尺寸:长
×
宽
×
高=5.2m
×
5.2m
×
9.0m。每个填埋单元10有效填埋区域面积=5.2m
×
5.2m=27.04m 2,有效容积243.36m3,满足《危险废物填埋污染控制标准》(gb18598-2019)“每个填埋单元10面积不超过50
㎡
且容积不得超过250m
3”的要求。经计算,本实施例中填埋场填埋库容6800m3。
46.本实施例中,填埋场1防水等级除符合gb50108一级防水标准外,还应在钢筋混凝土与废物接触面上覆有防渗、防腐材料。因此,防渗结构包括填埋单元10侧壁的防渗结构和底部的防渗结构,侧壁的防渗结构从内向外依次设置为0.35m钢筋混凝土隔墙、3mm纤维增强塑料、600g/m2长丝聚酯土工布、2.0mmhdpe单糙面土工膜、600g/m2长丝聚酯土工布;底部的防渗结构从下至上依次为钢筋混凝土底板、3mm纤维增强塑料、600g/m2聚酯土工布、2.0mmhdpe光面土工膜、600g/m2聚丙烯过滤有纺土工布、6.3mm土工复合排水网、200g/m2pe土工滤网。
47.本实施例中,基于对填埋单元10蓄水及导排的要求,需要对防渗结构采取加固技术。填埋单元10设有防渗加固装置,防渗加固装置包括环绕填埋单元10内壁中部设置以及位于所述填埋单元10开口端外围的锚固装置。锚固装置包括镀锌扁铁和对镀锌扁铁的两端、中部进行固定的射钉,射钉与镀锌扁铁的连接处进行了焊接加固。本实施例中,采用1500*40*4mm的镀锌扁铁与3条m10射钉组合的加固模式,射钉处进行补焊,价格便宜,施工方便,并具有较好的力学和耐久性能。
48.本实施例中,采用封闭结构的目的在于:避免危险废物填埋过程中产生的有害气体直接释放到空气中造成空气污染;避免有害固体废弃物直接与人体接触。根据《危险废物安全填埋处置工程建设技术要求》和《危险废物填埋污染控制标准》(gb18598-2019)的技术要求,填埋单元10填满后应及时对该单元进行封闭,封闭结构应包括1.5mm以上高密度聚乙烯防渗膜及抗渗混凝土。因此,对填埋单元10封场工程具体要求如下:1)封场系统由下至上应依次为导气层、防渗层和阻隔层:
①
导气层在封场系统的最底部建设30cm厚的砂砾导气层,并在导气层内安装气体导出管。气体导出管可由dn110
×
10.0的高密度聚乙烯制成,竖管下端与安装在导气层中的气体收集横管相接,竖管上端露出地面部分应设成倒u型,整个气体导出管成倒t型,气体收集横管带孔并用无纺布包裹。导气管与复合衬层交界处应进行袜式套封或法兰密封。
②
防渗层:防渗层采用1.5mm厚的高密度聚乙烯防渗膜,防渗膜下层采用400g/
㎡
长丝聚酯土工布做为膜下保护层,防渗膜上层采用600g/
㎡
长丝聚酯土工布做
为膜上保护层。防渗层采用与填埋单元10防渗结构相同的锚固方式。
③
阻隔层阻隔层采用c30防渗钢筋混凝土(防渗等级p10)、板厚度150mm、配筋为双层双向φ10@200。2)封场后系统的坡度应大于2%,保证表面雨水向外排出。封闭后应对渗沥液进行永久的收集和处理,并定期清理渗沥液收集系统。封闭后应对提升泵站、气体导出系统、电力系统等做定期维护。应预留定期维护与监测的经费,确保在封场后至少持续进行30年的维护和监测。封闭后,必须对排气管进行正确保养,防止雨水通过排气管直接进入填埋场1
49.吊车平台装置11包括装吊支撑平台和位于装吊支撑平台底部的移动组件,移动组件与轨道12相适配并能沿轨道12前进;装吊支撑平台上设有悬吊工位,悬吊工位上安装有定柱悬臂吊起重机。
50.进一步地,移动组件可采用车轮组件,填埋场1顶部设有的轨道12上设置有相应的车轮槽,车轮于车轮槽接触,并可沿车轮槽前进和停靠。
51.本实施例中,装吊支撑平台的形状、尺寸与填埋单元10相匹配,可完全覆盖单个填埋单元10的长与宽,实现有效的雨水隔离。进一步地,装吊支撑平台整体采用防腐防锈材质制造,如采用钢板或铁板制造平台,其他构件也采用钢铁构件,在钢铁构件上喷锌或喷铝,锌、铝是负电位和钢铁形成牺牲阳极保护作用从而使钢铁基本得到了保护。目前用喷铝涂层来防腐蚀,其特点如下:喷铝涂层与钢铁基体结合力牢固、涂层寿命长,长期经济效益好;工艺灵活,适用于重要的大型及难维修的钢铁结构的长效防护,可现场施工。同时,平台的金属框架也可刷涂氯化橡胶银粉漆、环氧钛白漆2道或喷涂聚脲弹性体(spua)来进行防腐。
52.本实施例中,定柱悬臂吊起重机包括立柱、横梁、环链电动葫芦和驱动系统,立柱底部固定安装在悬吊工位上,可采用螺丝固定;横梁可旋转地安装在立柱的顶部并与立柱相垂直;环链电动葫芦沿横梁设置。驱动系统包括3个电机,其中一个电机用以驱动横梁以立柱为轴心进行360度的回转,另外两个电机分别用以驱动环链电动葫芦沿横梁做水平运动和垂直于横梁做上下运动。
53.填埋单元10底部还设有导排系统,用于渗沥液的导排外运以及雨污水的导出应用。
54.本实施例中,导排系统包括导流坡103、导流管和排水泵。如图4所示,导流坡103位于填埋单元10的底面并与填埋单元10的底面成2%的坡度;导排管101沿导流坡103的坡底邻接的填埋单元10的侧壁设置,并且与填埋单元10的底面垂直,导排管101的进口设有导流口1011伸向坡底;排水泵的进水口连接导排管101的出口,排水泵的出口连接回收装置。渗沥液堆积后,利用排水泵,通过预埋的导排管101进行抽排,外运处置
55.进一步地,本实施例中,每个填埋单元10的底部采用水泥砂浆按2%找坡,坡的底部铺设6.3mm土工复合排水网座位渗滤液导流层。
56.进一步地,采用hdpe膜带102焊接到填埋单元10侧壁防渗层的方式固定导排管101。本实施例中,导排管101采用花纹管
57.进一步地,如图3所示,横向相邻的两个填埋单元10的导流坡103相向设置,纵向相邻的导流坡103同向设置,使得阵列式排布的4个填埋单元10的渗沥液向一处汇集,从而提高导水效率。
58.如图1所示,本实施例中,整个露天填埋场1设有登高楼梯、人行平台13、吊车平台装置11和填埋单元10。其中填埋场1的顶端铺设了4条轨道12,相应地,两个装吊支撑平台架
设在轨道12上,每个装吊支撑平台完全覆盖相邻的两个填埋单元10。
59.如图2所示,本技术的一个实施例中填埋场的工艺流程如下:
60.通过车载运输,危险废物采取吨袋模式进场,吨袋危险废物通过暂存库或填埋场1外侧堆砌层高3米进行暂时存放,暂存处设有防雨罩棚,可收集雨水,外排至初期雨水池;
61.通过自动化的驱动和控制系统,装吊支撑平台上的起重机将吊起危险废物填埋到相应的填埋单元10,产生的填埋气体,自由放散。
62.每一个单元格填埋完毕,进行单独封闭。
63.所有单元格填埋完毕后,进行终场覆盖。
64.本填埋场1,正在填埋单元10(未单独封场)通过装吊支撑平台进行雨水分离,杜绝渗沥液产生;同时未填埋单元10,可用作雨水搜集,搜集的雨水可用于附近的生产车间工艺用水,实现雨水回用的水资源利用效益。
65.综上所述,本技术的技术方案具有以下有益效果:
66.1、本技术的露天刚性填埋场1,利用刚性填埋场1本体单元作为吊车的承载,实现吊车的全方位移动,通过用吊车平台代替顶棚、协同渗沥液处理等方式,使得其建设费用、设备费用大大低于常规的填埋场1,运营人员也显著减少,大大降低了运营费用。
67.2、本发明对每个填埋单元10设置了导排系统,可以将雨污水和渗沥液分开处理,对于没有填埋物的填埋单元10导出雨污水满足周边生产用水需求,已填埋的单元导出渗沥液通过外运处置,大大降低了处理系统的负荷,节省了投入和日常运营费用,提高了投资和使用效益
68.3、由于填埋场1需要用水来完成垃圾的无害化过程,雨水的收集和运用,加快了填埋场1垃圾的生化反应过程,节省了资源,实现刚性填埋的多功能及集约型的经济效益,提高了刚性填埋场1的整体经济效益。
69.4、本技术的处理系统设备简单,只需建设填埋场1,占地少
70.5、本技术的防渗结构加固方法采用1500*40*4mm的镀锌扁铁与3条m10射钉,射钉处补焊的组合模式,价格便宜,施工方便,并具有较好的力学和耐久性能。
71.以上仅为本发明较佳的实施例,并非因此限制本发明的实施方式及保护范围,对于本领域技术人员而言,应当能够意识到凡运用本发明说明书及图示内容所作出的等同替换和显而易见的变化所得到的方案,均应当包含在本发明的保护范围内。