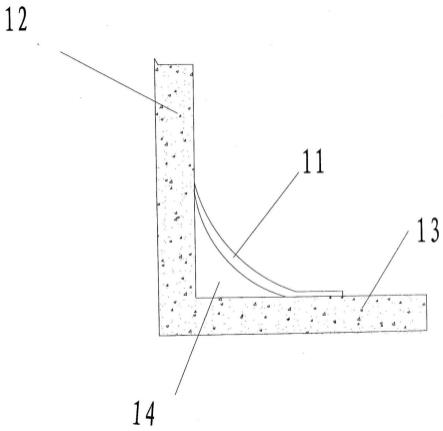
1.本实用新型涉及一种混凝土预制件模具,特别涉及一种屋面泛水位置处铺贴的罗马弧形预制件的预制胎具的模具。
背景技术:2.在建筑物屋顶面的施工中,屋面防水层施工完成后,需要在屋面泛水位置,即女儿墙与屋面之间的转角连接处,设置罗马弧的弧形转角,以利于屋顶雨水的排出;现有技术在对罗马弧施工时,是采用现场支设方木、木胶板、钢模板的方法,现浇混凝土并通过人工抹灰成型的,存在施工时间长,成型的罗马弧的尺寸和观感均难以控制的缺陷,特别是屋顶面面积较大时,经常出现施做完成的罗马弧的外形不一致,严重影响到了屋顶面的观感;若用预制的方法预制成罗马弧的弧形预制件,再将该预制件安装到屋面泛水位置,可解决罗马弧外观一致性的问题,但存在预制罗马弧的预制件的模具属异形结构模具,加工难度大,制作成本高,模具的重复使用率也低,如何开发一种现场施做简单、容易、低成本,可就地取材,并可根据预制的罗马弧的量,来动态控制模具成本的罗马弧形预制件的预制模具,成为现场施工中的一个课题。
技术实现要素:3.本实用新型提供了一种屋面泛水位置安装的弧形预制件的预制胎具的模具,解决了如何在施工现场低成本制作弧形预制件的简易模具来高质量完成屋顶面弧形转角施做的技术问题。
4.本实用新型是通过以下技术方案解决以上技术问题的:
5.本实用新型的总体构思是:利用现场已有的廉价材料,根据各材料的特性,将这些特性组合利用起来,依次制作澳松板胎膜和石膏胎膜的两中间胎膜,最后得到类似于玻璃钢材料的仿玻璃钢简易模具,在该简易模具上完成罗马弧形预制件的预制,得到的该简易模具具有低成本、轻质、高强、防水、耐侯性的优点,并且可根据预制罗马弧预制件的数量,控制仿玻璃简易模具的厚度及成本,实现了物尽其用和经济低成本。
6.一种屋面泛水位置安装的弧形预制件的预制胎具及模具,包括湿水后的澳松板,将湿水后的澳松板弯曲成型为木质弧形底模板,木质弧形底模板的形状和弧度是与预制作的罗马弧形预制件的形状和弧度完全相同,在木质弧形底模板的两端分别设置有木质堵头板,在木质弧形底模板的下底面上设置有支座;在木质弧形底模板的凹槽中,均匀地涂刮有石膏混合浆料,石膏混合浆料的厚度为3厘米。
7.在木质弧形底模板的凹槽中均匀地涂刮的石膏混合浆料干燥脱模后,脱模得到石膏胎膜,在石膏胎膜上设置有弧形背面,在弧形背面上,从内向外,依次叠铺有第一块细白金纱玻璃纤维网格布、第一层1毫米厚的中温乙烯基树脂胶层、第二块细白金纱玻璃纤维网格布、第二层1毫米厚的中温乙烯基树脂胶层、第三块细白金纱玻璃纤维网格布和第三层1毫米厚的中温乙烯基树脂胶层。
8.在弧形背面上叠铺的三层细白金纱玻璃纤维网格布和三层中温乙烯基树脂胶层干燥后,脱模得到仿玻璃钢简易模具,在仿玻璃钢简易模具的凹槽中,均匀地涂刮有c20聚丙烯纤维增强混凝土料,c20聚丙烯纤维增强混凝土料的厚度为3厘米,该3厘米厚的c20聚丙烯纤维增强混凝土料干燥后,脱模得到罗马弧形预制件。
9.本实用新型是依据澳松板湿水后可自由弯曲的特性,并根据罗马弧预制件的设计几何形状,将澳松板湿水后弯曲成与罗马弧预制件的形状和弧度相同的底模模具板;并充分利用石膏材料可塑性、快凝性、轻质、低成本的特性,以石膏为原材料,与水按比例配合,并辅以一定比例的矿粉材料,制作出胎模泥,将胎模泥分层刮抹在用澳松板制作的底模模具中,待石膏凝固干燥后,脱模得到石膏胎模;再以石膏胎模为模具,将三层白金纱玻璃纤维网格布和三层中温乙烯基树脂胶贴附在石膏胎模上,最后,得到类似玻璃钢材质的仿玻璃钢简易模具,模具具有轻质、高强、防水、耐侯性好的特点,用现场拌制的c20聚丙烯纤维增强混凝土料制作出增强混凝土料的弧形预制件;本发明制作的胎膜及模具成本低廉,现场操作简单容易,预制件成型好,不仅适用于屋面泛水处预制件的制作,也同样适用于土建施工现场其他异性混凝土预制件的制作。
附图说明
10.图1是本实用新型的罗马弧形预制件11安装在女儿墙处时的结构示意图;
11.图2是本实用新型相邻的两罗马弧形预制件11拼接时的结构示意图;
12.图3是本实用新型的澳松板的底模模具的结构示意图;
13.图4是本实用新型在制作石膏胎膜5时的结构示意图;
14.图5是本实用新型在石膏胎膜5上制作仿玻璃钢简易模具9时的结构示意图;
15.图6是本实用新型在仿玻璃钢简易模具9上制作罗马弧形预制件11时的结构示意图。
具体实施方式
16.下面结合附图对本实用新型进行详细说明:
17.一种屋面泛水位置安装的弧形预制件的预制胎具及模具,包括湿水后的澳松板,将湿水后的澳松板弯曲成型为木质弧形底模板1,木质弧形底模板1的形状和弧度是与预制作的罗马弧形预制件11的形状和弧度完全相同,在木质弧形底模板1的两端分别设置有木质堵头板2,在木质弧形底模板1的下底面上设置有支座3;在木质弧形底模板1的凹槽中,均匀地涂刮有石膏混合浆料4,石膏混合浆料4的厚度为3厘米。
18.在木质弧形底模板1的凹槽中均匀地涂刮的石膏混合浆料4干燥脱模后,脱模得到石膏胎膜5,在石膏胎膜5上设置有弧形背面6,在弧形背面6上,从内向外,依次叠铺有第一块细白金纱玻璃纤维网格布8、第一层1毫米厚的中温乙烯基树脂胶层7、第二块细白金纱玻璃纤维网格布、第二层1毫米厚的中温乙烯基树脂胶层、第三块细白金纱玻璃纤维网格布和第三层1毫米厚的中温乙烯基树脂胶层。
19.在弧形背面6上叠铺的三层细白金纱玻璃纤维网格布和三层中温乙烯基树脂胶层干燥后,脱模得到仿玻璃钢简易模具9,在仿玻璃钢简易模具9的凹槽中,均匀地涂刮有c20聚丙烯纤维增强混凝土料,c20聚丙烯纤维增强混凝土料的厚度为3厘米,该3厘米厚的c20
聚丙烯纤维增强混凝土料干燥后,脱模得到罗马弧形预制件11。
20.一种屋面泛水位置安装的弧形预制件的预制及铺贴方法,包括以下步骤:
21.第一步、根据预安装屋顶面泛水位置处罗马弧预制件的形状和弧度,将澳松板湿水后,弯曲制作成木质弧形底模板1,使木质弧形底模板1的形状和弧度与预安装屋顶面泛水位置处罗马弧预制件的形状和弧度相同;在木质弧形底模板1的两端,分别安装木质堵头板2,在木质弧形底模板2的下底面上安装支座3,得到澳松板的底模模具;
22.第二步、制作石膏混合浆料:取石膏粉,并按所取石膏粉重量的3%取生石灰粉,将两者搅拌均匀,加水拌和,得到石膏混合浆料4;
23.第三步、将第二步得到的石膏混合浆料4,涂刮到第一步得到的底模模具中的木质弧形底模板1的凹槽中,涂刮分三次进行,每次涂刮的厚度为1厘米,待上一层石膏混合浆料4凝固后,再刮涂下一层石膏混合浆料4;
24.第四步、待底模模具中刮涂的三层石膏混合浆料4凝固干透后,将其脱出,得到石膏胎膜5;
25.第五步、根据第四步得到的石膏胎膜5的弧形背面6的面积,裁剪得到三块与弧形背面6的面积相同的细白金纱玻璃纤维网格布8;将第一块细白金纱玻璃纤维网格布8平整地铺贴到石膏胎膜5的弧形背面6上,在第一块细白金纱玻璃纤维网格布8上,涂刷第一层1毫米厚的中温乙烯基树脂胶层7,再叠加铺设第二块细白金纱玻璃纤维网格布,再涂刷第二层1毫米厚的中温乙烯基树脂胶层,再叠加铺设第三块细白金纱玻璃纤维网格布,最后,再涂刷第三层1毫米厚的中温乙烯基树脂胶层;待胶干后,将由三层白金纱玻璃纤维网格布和三层中温乙烯基树脂胶组成的仿玻璃钢简易模具9,从石膏胎膜5上脱下;
26.第六步、配制c20聚丙烯纤维增强混凝土料:按以下重量比,取水泥、砂子、直径小于或等于0.5毫米的石子、水和聚丙烯纤维五种材料,重量比为:水泥:砂子:石子:水:聚丙烯纤维=1:2.67:3.22:0.57:0.1-0.01;先将按以上比例取到的水泥、砂子、石子和水,搅拌均匀,然后,再惨入按以上比例取到的聚丙烯纤维,再次搅拌均匀后,得到配制好的c20聚丙烯纤维增强混凝土料10;
27.第七步、将第六步配制好的c20聚丙烯纤维增强混凝土料10,均匀涂刮到第五步得到的仿玻璃钢简易模具9的凹槽中,刮涂料层要均匀,其厚度为3厘米,通过游标卡尺及白绳拉线,对涂刮的c20聚丙烯纤维增强混凝土料的厚度进行控制;成型为增强混凝土料的弧形预制件,四小时后,脱模得到罗马弧形预制件11,对其浇水养护7天;
28.第八步、在女儿墙12与屋顶面保护层13之间的转角处,设置聚合物粘结砂浆14,将第七步浇水养护后的罗马弧形预制件11粘贴在聚合物粘结砂浆14上。
29.在相邻的两罗马弧形预制件11之间的拼接缝中,设置有沥青砂浆或耐侯胶泥15;在罗马弧形预制件11的表面上喷射涂料面层。
30.聚丙烯纤维与水泥的结合力好,可加强纤维与基料的握裹力,纤维能够阻止混凝土的离析现象发生,加强浇注体的整体均匀性,可减少混凝土的脆性,对混凝土的韧性有加强作用,提高混凝土的抗裂性、抗渗性、抗冲磨性、抗冻能力、抗爆能力,并改善混凝土的和易性;中温乙烯基树脂胶为粘稠状,施工时主要是采用刮和刷的方式,不会产生流坠现象;配制好的c20聚丙烯纤维增强混凝土为干硬性料,在仿玻璃钢简易模具9中成型性好;罗马弧弧形预制件11成型后,立即在构件表面覆盖塑料薄膜,并经4小时养护后脱模,根据气温
情况,一般浇水养护7天后即可起吊;完成一定批量后,统一运至屋面进行安装,安装时在屋面与女儿墙接触处采用聚合物粘结砂浆进行粘结,构件之间的缝隙采用沥青砂浆或耐侯胶泥进行勾缝处理,并根据屋面统一色调可以在其表面喷射涂料面层。