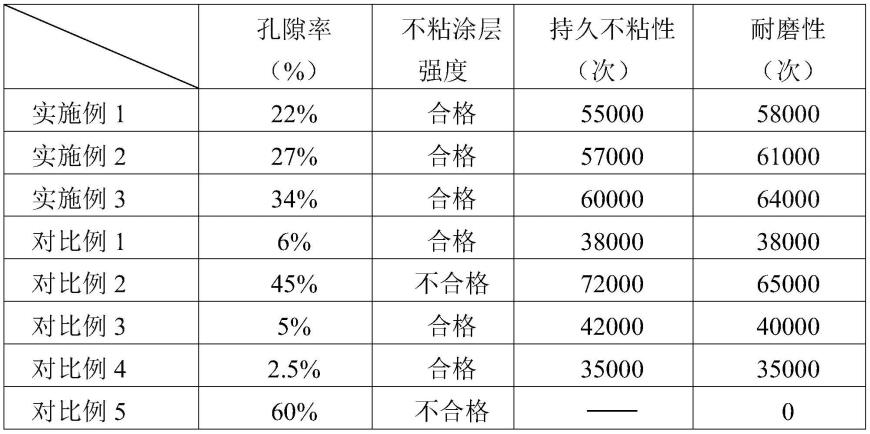
1.本技术涉及厨房用品技术领域,更具体地讲,涉及一种锅具及其制备方法。
背景技术:2.不粘锅在烹饪时不会在锅底上粘上食物,避免了传统锅具在烹饪过程中时常发生食物粘锅的现象,从而能够避免食物出现焦糊以及因为焦糊引起有害物质产生的问题。不粘锅不仅降低了锅具的清洗难度,同时还能够轻松煎、炒食物,避免传统锅具需要较多的油脂来防止食物粘锅,最大限度地减少用油,降低用户对脂肪的摄入量,顺应了现代人追求低脂肪、低热量的消费潮流。因此,不粘锅成为很多家庭的首选。
3.市场上的锅具主要是通过涂覆不粘层来实现不粘效果,其中,陶瓷涂料和有机硅树脂涂料是较为常见的不粘层。虽然陶瓷涂料和有机硅树脂涂料均能作为锅具的不粘层使用,但是在使用过程中存在较为明显的问题。比如,陶瓷涂料形成的不粘层持久不粘性差,使用3~6个月后不粘层就容易脱落;而有机硅树脂涂料形成的不粘层在高温或明火的条件下容易发黄或发灰,并且不粘层在高温下硬度下降,容易产生“回粘”现象。
技术实现要素:4.为了解决上述问题中的一个或多个,本发明提供一种具有良好的不粘性和持久不粘性并且制备工艺简单的锅具。
5.本技术第一方面的实施例提供一种锅具,该锅具包括:锅具基体;不粘涂层,形成在锅具基体的内表面上,所述不粘涂层由包括非晶合金和多孔陶瓷材料的复合材料形成,所述复合材料为非晶合金包覆在多孔陶瓷材料表面的颗粒,所述多孔陶瓷材料为非晶合金和多孔陶瓷材料质量和的5%~30%。
6.采用包含非晶合金和多孔陶瓷材料且呈颗粒状的复合材料在锅具的内表面上形成不粘涂层,形成的不粘涂层在很大程度上保留了非晶合金中的非晶结构,并且同时还最大程度保留了多孔陶瓷材料中的孔隙结构;因此,不粘涂层利用非晶结构具有低表面能的特点和多孔材料的吸油形成油膜的特性实现锅具的不粘,并且形成的不粘涂层具有好的耐磨性以及持久不粘性。
7.在一些实施例中,所述不粘涂层中的非晶相占比为60%~100%,所述不粘涂层的孔隙率为20~40%。不粘涂层中非晶相占比确保形成的不粘涂层在使用过程中不会发生粘黏现象,并且同时还可降低对喷涂工艺的要求。而不粘涂层的孔隙率有利于不粘涂层吸油形成油膜,在一定程度上对非晶相低表面能带来的不粘性能进行强化。
8.在一些实施例中,所述多孔陶瓷材料包括硅藻土、沸石粉和膨润土中的至少一种;所述非晶合金包括fe基非晶合金、zr基非晶合金、cu基非晶合金、al基非晶合金、mg基非晶合金、ti基非晶合金和等原子比高熵非晶合金中的至少一种。
9.在一些实施例中,所述不粘涂层的厚度为100μm~500μm,所述颗粒状的复合材料的粒度为60~100μm。该厚度的涂层具有致密性好、耐磨性好的特点,并且还可避免涂层制
备过程中热量集中,导致非晶结构组织发生晶化转变引起不粘涂层的不粘性降低的问题。
10.本技术中第二方面实施例提供一种锅具的制备方法,包括:将锅具基体预热;将复合粉末喷涂在锅具基体的内表面,在所述锅具基体的内表面上形成不粘涂层,所述复合粉末包括非晶合金材料和多孔陶瓷材料,所述多孔陶瓷材料为非晶合金和多孔陶瓷材料质量和的5%~30%。
11.在一些实施例中,所述不粘涂层中的非晶相占比为60%~100%,所述不粘涂层的孔隙率为20~40%。
12.在一些实施例中,所述复合粉末由多孔陶瓷粉末和非晶合金粉末包覆形成,且非晶合金粉末包覆在多孔陶瓷粉末的外表面。非晶合金粉末包覆在多孔陶瓷材料粉末表面的复合粉末在喷涂时通常只有复合粉末表层的非晶合金粉末受热熔化,避免多孔陶瓷材料受热导致其孔隙结构被破坏,且复合粉末随着非晶合金粉末熔融后一起附着在锅具基体的内表面上。因此,采用复合粉末形成的涂层,多孔陶瓷材料中的孔隙结构被保留,增加了涂层的孔隙率,利于涂层吸油形成油膜,提高了涂层的不粘性。
13.在一些实施例中,所述复合粉末的粒度为60~100μm。该粒度范围内的复合粉末具有好的流动性,在喷涂过程中不容易堵塞喷枪,便于施工。
14.在一些实施例中,所述多孔陶瓷粉末的粒度为35~60μm,所述非晶合金粉末的粒度为10~20μm。两种粉末之间具有一定的粒度差,有利于非晶合金粉末包覆在多孔陶瓷粉末的外表面形成复合粉末。
15.在一些实施例中,所述多孔陶瓷材料包括硅藻土、沸石粉和膨润土中的至少一种;所述非晶合金粉末至少包括fe基非晶合金粉末、zr基非晶合金粉末、cu基非晶合金粉末、al基非晶合金粉末、mg基非晶合金粉末、ti基非晶合金粉末和高熵非晶合金粉末中的一种。所述高熵非晶合金可以是等原子比高熵非晶合金。
具体实施方式
16.现在,将在下文更充分地描述本发明的构思。
17.不粘锅能够实现不粘主要有三个方向:(1)锅具自身的表面具有低表面能;(2)锅具的表面设有微观凹凸结构,该凹凸结构形成类似于荷叶疏水疏油的表面;(3)锅具表面涂覆多孔储油材料,多孔储油材料吸收食用油后能够在锅具的表面形成稳定油膜,形成的油膜实现锅具不粘。
18.非晶合金又称为液态金属,其相对于普通材料具有更低的表面能,表现出良好的不粘性。具体地,非晶合金的非晶结构具有长程无序、短程有序的特性,因此具有较低的表面能。此外,非晶合金不像晶体合金一样具有晶界、孪晶、晶格缺陷、位错、层错等结构缺陷,也没有异相、析出物、偏析以及其他成分起伏,是一种混乱的无序结构,在化学上有高度的均匀一致性,受到外力时不存在晶界滑移等塑性变形。发明人同时还发现多孔陶瓷材料能够将食用油存储下来形成油膜,形成的油膜可以实现锅具的不粘。
19.对此,发明人首先尝试将非晶合金粉末和多孔陶瓷材料粉末混合后直接热喷涂在锅具基体的内表面上以形成不粘涂层,该不粘涂层利用非晶结构具有低表面能的特点和多孔陶瓷材料的吸油形成油膜的特性实现锅具的不粘,经测试由此形成的锅具具有不粘效果。但是,发明在对不粘涂层进一步分析时发现,不粘涂层中的多孔材料的含量偏低;并且,
尽管喷涂时非晶合金粉末和多孔材料粉末都按相同质量比混合,但每次喷涂形成的不粘涂层中的多孔材料的含量也不相同。其原因是多孔材料和非晶合金的密度和熔点不同,若两种粉末混合后直接进行热喷涂,具有密度小和熔点更高特点的多孔材料粉末在热喷涂过程中沉积率低,而具有密度大和熔点低的非晶合金粉末沉积率高,最终导致涂层中非晶合金和多孔材料比例无法控制。
20.基于此,发明人通过将非晶合金粉末包覆在多孔陶瓷材料粉末的外表面上,形成一种具有核壳结构的复合粉末,从而利用非晶合金比多孔陶瓷材料密度大和熔点低的特性,热喷涂时多孔陶瓷材料随着熔融的非晶合金一起沉积在锅具基体的内表面上,如此,不仅提高了多孔材料的沉积率,同时还使得不粘涂层中的非晶合金和多孔陶瓷材料的质量比例实现可控,经测试该锅具表面的不粘涂层具有更好的不粘效果和持久不粘性。
21.根据本技术,复合粉末可以采用包覆工艺进行制备,比如喷雾造粒工艺,下面以喷雾造粒工艺为例对复合粉末的制备进行描述,具体包括以下步骤。
22.(1)制备原料粉末,将非晶合金粉末和多孔陶瓷粉末均匀混合。
23.具体地,将非晶合金粉末和多孔陶瓷粉末分别放入球磨机中进行球磨,多孔陶瓷粉末可以选用纯度高于99.5%的硅藻土粉末、沸石粉末和膨润土中的至少一种,球磨后非晶合金粉末的粒度为10~20μm、多孔陶瓷粉末的粒度为35~60μm。球磨后的两种粉末之间具有一定的粒度差,有利于在包覆过程中形成核壳结构。再将球磨后的多孔陶瓷粉末和非晶合金粉末充分混合得到原料粉末,其中,基于原料粉末的总质量,多孔陶瓷粉末的质量比为5%~30%;该质量比范围内的多孔陶瓷粉末与非晶合金粉末的质量差较大,可以确保在喷雾造粒过程中有足够的非晶合金粉末包覆在多孔陶瓷粉末的外表面。
24.(2)制备浆料,将原料粉末、粘结剂和溶剂进行充分混合后得到浆料;此外,还可以添加助剂以及填料。
25.基于浆料的总质量,浆料中的原料粉末的质量分数可以是30~60%,优选地为40%~50%;浆料中的粘结剂的质量分数可以是1%~10%,优选地为3%~8%;浆料中的助剂的质量分数可以是0.2%~1%;浆料中的填料的质量分数可以是5%~20%,优选地为8%~15%;浆料中的溶剂的质量分数可以是20%~60%,优选地为是40%~55%。
26.在浆料制备时,粘结剂主要是将浆料中的原料粉末以及填料等粘结在一起,避免喷雾造粒形成的复合粉末粒度过小或者无法形成核壳结构。粘结剂可以选自于聚乙烯醇、聚乙烯吡咯烷酮或羧甲基纤维素钠。助剂包括消泡剂和分散剂,消泡剂和分散剂可以按任意比进行混合,其中,消泡剂主要是消除浆料中的气泡或泡沫,分散剂主要是让浆料中各组分均匀分散。消泡剂可以是有机硅油或聚醚改性硅油,比如二甲基硅油,分散剂可以是柠檬酸或三乙基己基磷酸。填料用于调节浆料粘度,减缓浆料中非晶合金粉末沉降。填料可以是石墨粉末或炭黑粉末。溶剂作为一种介质,便于原料粉末、粘结剂、助剂、填料和溶剂进行混合制成浆料。溶剂可以是无水乙醇、丙酮或去离子水。
27.(3)喷雾造粒,获得复合粉末。
28.首先,将制备的浆料进行雾化使浆料形成液滴状,对呈液滴状的浆料进行干燥后得到复合粉末。作为示例,浆料被喷雾干燥的条件可以是:在惰性气氛中进行雾化,具体地,采用99.999%的氩气气氛,雾化压力为0.3~0.6mpa,优选为0.4~0.5mpa;雾化气流流量为0.5~5m3/h,优选为1.0~3.0m3/h;进风口温度为60~100℃,优选为80~100℃;出风口温度
为100~150℃,优选为120~150℃。但是,喷雾干燥获得的复合粉末中的非晶合金和陶瓷材料之间结合强度不够稳定,因此,根据本发明的方法还可以进一步将复合粉末进行烧结,烧结的温度根据复合粉末的物性曲线进行升温,烧结的条件可以是:在低温区50~200℃烧结并保温15~30min,然后在高温区200~600℃烧结并保温2~4h。
29.(4)将上述制备的复合粉末进行筛分,获得不同粒度的复合粉末。最终选取粒度为60~100μm的粉末颗粒,作为用于喷涂到锅具基体上的复合粉末。
30.另外,本技术中的非晶合金粉末可以将非晶合金通过雾化制粉方法制取,以fe基非晶合金粉末为例对非晶合金粉末制备进行说明,其雾化制备方法如下所述。
31.首先,将熔融的fe基非晶合金射向高速旋转(表面线速度可达100m/s)的铜制急冷盘上,在离心力的作用下,熔融的fe基非晶合金雾化后凝固成的细粒就会向四周散开,并通过装在盘上四周的气体喷嘴喷吹惰性气体以加速冷却。在使用该方法制备非晶合金粉末时,熔融的非晶合金的冷却速率可达106k/s,使熔融的非晶合金来不及结晶就以过冷态凝固,形成具有非晶结构的非晶合金粉末。
32.上述的关于fe基非晶合金粉末的制备方法也适用于其它非晶合金粉末的制备。
33.下面将上述制备的复合粉末热喷涂在锅具基体的表面来对本技术中第一方面实施例提供的一种锅具的制备方法进行说明,该锅具的制备方法具体包括以下步骤:
34.步骤s110:对锅具基体表面进行预处理;
35.步骤s120:对锅具基体预热;
36.步骤s130:将喷雾造粒制备的复合粉末喷涂在锅具基体的内表面上,以形成不粘涂层。
37.步骤s140:对形成有不粘涂层的表面进行砂光处理,砂光后涂层表面粗糙度ra为1~2μm。
38.在步骤s110中对基体表面处理的目的主要是为了提高不粘涂层与锅具基体之间的结合力。锅具基体的表面处理可以包括清洗和喷砂处理,清洗步骤可以清除基体表面的油污,比如用碱性溶剂对基体的表面进行清洗,碱性溶剂可以是稀释的氢氧化钠溶液。而喷砂处理可以增大基体表面的粗糙度,有利于不粘涂层牢固附着在锅具基体上,经喷砂处理后的锅具基体表面粗糙度ra为2~5μm。
39.在步骤s120中采用加热炉对锅具基体进行预热,预热的目的是为了减少锅具基体与喷出的复合粉末之间的温差,减少锅具基体与不粘涂层之间的热应力,从而提高不粘涂层质量以及不粘涂层与锅具基体之间的结合强度。作为示例,锅具基体的预热温度可以是200~300℃。
40.在步骤s130中可以采用等离子喷涂工艺。在等离子喷涂工艺过程中,可以先将锅具放入喷涂腔室中,并将喷涂腔室抽至一定真空,然后充入氩气进行保护,避免喷涂过程中非晶合金被氧化而导致形成的涂层中引入杂质;再将复合粉末等离子喷涂在预热后的锅具基体的内表面,最后得到具有不粘涂层的锅具。
41.作为示例,喷涂腔室抽至真空度为3pa,充入氩气至6
×
103pa;等离子喷涂工艺的条件为:转移弧功率30kw,电弧电流600a~800a,喷涂距离120mm,喷涂角度60
°
~80
°
,送粉速度:10~40g/min,氢气压力:0.3~0.7mpa、流量5~10l/min。
42.此外,由于通过造粒获得的复合粉末具有核壳结构,因此,在步骤s130中,等离子
喷涂时复合粉末表层的非晶合金层受热熔化,避免了多孔陶瓷材料受热导致其孔隙结构被破坏,且随着非晶合金一起附着在锅具基体的表面上。此外,通过将非晶合金粉末包覆在多孔陶瓷外表面上形成包覆颗粒后再进行喷涂,避免了由于多孔陶瓷材料密度小、熔点高的原因导致其沉积率低的问题。因此,在采用上述复合粉末进行喷涂形成的涂层中,确保了多孔陶瓷材料的沉积率,并且多孔陶瓷材料中的孔隙结构被保留,增加了涂层的孔隙率,利于涂层吸油形成油膜,实现涂层的不粘性。
43.另外,等离子喷涂采用的复合粉末的粒度为60~100μm,在该粒度范围内的复合粉末具有好的流动性,在等离子喷涂过程中不容易堵塞喷枪,便于施工。
44.在一些实施例中,多孔陶瓷材料可以包括硅藻土、沸石粉和膨润土中的至少一种,然而,本技术不限于此,本领域技术人员可以在本技术的教导下选用其它多孔陶瓷材料。非晶合金粉末可以包括fe基非晶合金粉末、zr基非晶合金粉末、cu基非晶合金粉末、al基非晶合金粉末、mg基非晶合金粉末、ti基非晶合金粉末和高熵非晶合金粉末中的一种。高熵非晶合金可以是等原子比高熵非晶合金或者是近似等原子比高熵非晶合金。
45.本技术中第二方面的实施例提供一种锅具,该锅具通过第一方面的实施例可制备出,所述的锅具包括:锅具基体;不粘涂层,形成在锅具基体的内表面上,所述不粘涂层由包括非晶合金和多孔陶瓷材料的复合粉末通过喷涂工艺形成,所述复合材料为非晶合金包覆在多孔陶瓷材料表面的颗粒,所述多孔陶瓷材料为非晶合金和多孔陶瓷材料质量和的5%~30%。
46.在本实施例中,颗粒状的复合材料经等离子喷涂形成在锅具基体内表面上的不粘涂层在很大程度上保留了非晶合金中的非晶结构,并且同时还最大程度保留了多孔陶瓷材料中的孔隙结构,因此,形成的不粘涂层不仅具有非晶结构的低表面能,使涂层具有不粘效果;同时还具有多孔陶瓷材料吸油并在不粘涂层的表面形成油膜的特性,形成的油膜对由非晶合金的低表面能产生的不粘性进行强化,进一步提高不粘涂层的不粘效果。本实施例中的颗粒状的复合材料的粒度可以是60~100μm。
47.此外,形成的不粘涂层中多孔陶瓷材料均匀分布,有利于在不粘涂层的表面形成均匀的油膜,提高不粘涂层的不粘效果;其次,多孔陶瓷材料均匀分布有利于不粘涂层受热均匀,可避免由于多孔陶瓷材料分布不均造成不粘涂层的厚度不一致,最终导致不粘涂层在使用过程中局部过薄出现烧蚀。
48.另外,多孔陶瓷材料具有更好的耐磨性以及高的熔点,可避免在热喷涂过程中温度过高导致多孔陶瓷材料发生熔融,造成孔隙结构的损坏,增强涂层的耐磨性;其次,多孔陶瓷材料良好的耐磨性可避免形成的不粘涂层在使用过程中由于磨损造成孔隙结构的破坏,导致无法吸油形成油膜,而具有好的耐磨性的多孔陶瓷材料延长了不粘涂层的使用寿命。
49.另外,由于非晶合金没有像晶体合金那样具有晶界、孪晶、晶格缺陷、位错、层错等结构缺陷,而且没有异相、析出物、偏析以及其他成分起伏,在化学上有高度的均匀一致性,受到外力时不存在晶界滑移等塑性变形形式,具有更高的强度,因此,进一步增强了不粘涂层的耐磨性,使锅具表面的涂层产生持久不粘性。
50.在一些实施例中,不粘涂层中的非晶相占比为60%~100%,不粘涂层的孔隙率为20~40%。不粘涂层中60%~100%非晶相占比确保形成的不粘涂层在使用过程中不会发
生粘黏现象,并且同时还可降低对等离子喷涂工艺的要求。而不粘涂层20~40%的孔隙率有利于不粘涂层吸油形成油膜,在一定程度上对非晶相低表面能带来的不粘性能进行强化。本实施中的孔隙率包括热喷涂工艺产生的2%~10%的孔隙率以及多孔陶瓷材料本身的孔隙结构所具有的孔隙率。热喷涂的工艺过程产生的孔隙率控制在2~10%,可以确保形成的不粘涂层的强度和耐磨性,并同时还具有一定的吸油效果;而由于多孔陶瓷材料本身的孔隙为其固有结构,由多孔陶瓷材料的孔隙结构导致的孔隙率不会影响不粘涂层的强度。因此,通过增加添加多孔陶瓷材料,能够使涂层的孔隙率在20%~40%范围内,一方面能够确保涂层的强度,同时还能够提高涂层的孔隙率有利于涂层储油形成油膜,提高涂层的不粘性。
51.在一些实施例中,非晶合金为fe基非晶合金、zr基非晶合金、cu基非晶合金、al基非晶合金、mg基非晶合金、ti基非晶合金和高熵非晶合金中的一种或多种,在本技术中,当非晶合金为多种时,合金之间可以按任意值进行混合。上述的非晶合金主要元素成分包括:fe、zr、cu、al、mg和ti中的至少一种,其它元素可以包括sn、ni、pb、zn、nd、ga、mo、hf、cr、ca、y、si、p、b和c中的至少一种。根据本技术的一些实施例,zr基非晶合金可以是zr60-cu23-al10-ni5-hf2或zr65-ti-ni10-al10-cu15;fe基非晶合金可以是fe80-cr5-mo6-b4-si5、fe50-zr20-cr9-b6-cu10-y5、fe87.4-si6.7-b2.4-cr2.7-c0.8、fe90-b7-si3;高熵非晶合金可以是等原子比高熵非晶合金,例如fe-sn-pb-p-c。
52.根据本发明的实施例,可以采用等离子热喷涂工艺将复合粉末喷涂到锅具基体的表面上,形成不粘涂层。在一些实施例中,形成的不粘涂层的厚度为100-500μm。可以通过多次喷涂形成,例如,每次喷涂厚度为30-50μm。当不粘涂层的厚度小于100μm时,热喷涂时通常只需要喷涂1到2层的复合材料就可形成,后续将不再继续热喷涂离子对沉积的不粘涂层进行夯实,导致沉积粒子受力变形较小,形成的不粘涂层致密度较差,其从结构上表现出疏松多孔,最终导致不粘涂层的强度较差、耐磨性不够。若涂层的厚度大于500μm时,热喷涂制备时会导致涂层中热量集中,促使非晶合金中的部分非晶结构组织发生晶化转变,降低不粘涂层中非晶相的占比,最终引起不粘涂层的不粘性降低。
53.实施例
54.下面以fe基非晶合金粉末为fe50-zr20-cr9-b6-cu10-y5合金粉末、多孔陶瓷材料为硅藻土为例对本技术中的锅具制备进行详细的介绍。
55.实施例1
56.复合粉末的制备方法,具体包括以下步骤:
57.步骤210:首先,将fe50-zr20-cr9-b6-cu10-y5合金粉末和纯度高于99.5%的硅藻土分别放入球磨机进行球磨,球磨后fe50-zr20-cr9-b6-cu10-y5合金粉末的粒度为10~13μm、硅藻土的粒度为40~42μm;然后将球磨后的fe50-zr20-cr9-b6-cu10-y5合金粉末和硅藻土混合后获得原料粉末,其中,fe50-zr20-cr9-b6-cu10-y5合金粉末的质量占比为94%,硅藻土的质量占比为6%。
58.步骤220:将原料粉末、粘结剂、助剂、填料和溶剂充分混合后得到浆料;其中,原料粉末的质量分数42%;粘结剂为聚乙烯醇,其质量分数为5%;助剂为二甲基硅油和柠檬酸,二甲基硅油和柠檬酸按质量比1:1进行混合,助剂的质量分数为0.5%;填料为炭黑,其质量分数为11%;溶剂为去离子水,其质量分数为41.5%。
59.步骤230:首先将浆料进行雾化并让浆料形成液滴状,对呈液滴状的浆料进行干燥,最后获得复合粉末。其中,浆料被喷雾干燥的条件是:在氩气气氛下进行雾化,雾化压力为0.5mpa、雾化气流流量为2.8m3/h、进风口温度为80℃、出风口温度为120℃;雾化液滴中的水分被蒸发,获得复合粉末。为了进一步提高复合粉末中的非晶合金和陶瓷材料的结合强度,将复合粉末进一步烧结,复合粉末烧结的条件为:在低温区180℃烧结并保温30min,在高温区480℃烧结并保温3h。
60.步骤240:将步骤230获得复合粉末进行筛分,筛分出粒度在80~86μm之间的复合粉末。
61.将本实施例中获得的复合粉末喷涂在锅具基体的表面,在锅具基体上形成不粘涂层。
62.锅具的制备方法具体包括以下步骤:
63.步骤310:对锅具基体表面进行预处理
64.首先用0.8%的naoh溶液、15%的碳酸钠溶液和15%偏硅酸钠为主要成分的清洗剂溶液对锅具基体的表面油污进行清洗,然后在清洗后的锅具基体表面进行喷砂,得到表面粗糙度ra为3μm的锅具基体。
65.步骤320:锅具基体预热
66.通过加热炉将表面预处理后的锅具基体预热到280℃。
67.步骤330:等离子喷涂
68.等离子喷涂过程中,可以先将锅具放入喷涂腔室中,再将喷涂腔室抽真空度3pa,然后再往喷涂腔室中冲入氩气至6
×
103pa;最后在转移弧功率30kw、电弧电流700a、喷涂距离120mm、喷涂角度75
°
、送粉速度为25g/min、氢气压力为0.6mpa、氢气流量为8l/min的条件下将复合粉末喷涂在预热后的锅具基体上,形成不粘涂层;其中,复合粉末为实施例1制备,获得的不粘涂层的厚度为250μm。
69.步骤340、不粘涂层的后续处理
70.将步骤330中获得的不粘涂层自然冷却,然后采用120目砂纸对不粘涂层的表面进行砂光处理,砂光后其的表面粗糙度ra为2μm,获得具有不粘性的锅具。
71.实施例2
72.除了步骤110中原料粉末中硅藻土的质量占比为15%之外,按照上述实施例1中所述方法制备复合粉末,然后按照上述实施例1中所述方法进行锅具的制备。
73.实施例3
74.除了步骤110中的原料粉末中硅藻土的质量占比为25%之外,按照上述实施例1中所述方法制备复合粉末,然后按照上述实施例1中所述方法进行锅具的制备。
75.对比例1
76.除了步骤110中的原料粉末中硅藻土的质量占比为2%之外,按照上述实施例1中所述方法制备复合粉末,然后按照上述实施例1中所述方法进行锅具的制备。
77.对比例2
78.除了步骤110中的原料粉末中硅藻土的质量占比为50%之外,按照上述实施例1中所述方法制备复合粉末,并按照上述实施例1中所述方法进行锅具的制备。
79.对比例3
80.采用球磨后粒度为10~13μm的fe50-zr20-cr9-b6-cu10-y5合金粉末和粒度为40~42μm的硅藻土进行混合获得原料粉末,获得的原料粉末直接等离子喷涂形成不粘涂层,且原料粉末中硅藻土的质量占比为6%之外,按照上述实施例1中所述方法进行锅具的制备。
81.对比例4
82.除了步骤330中等离子喷涂时选用粒度为10~13μm的非晶合金粉末之外,按照上述实施例1中所述方法进行锅具的制备。
83.对比例5
84.除了步骤330中等离子喷涂时选用粒度为40~42μm的硅藻土之外,按照上述实施例1中所述方法进行锅具的制备。
85.性能指标测试
86.1、将上述实施例1~3和对比例1~4中获得的锅具进行性能测试,并将测试结果记录在表1中,具体对其进行下述测试:
87.(1)锅具中不粘涂层的孔隙率检测
88.本技术中锅具上的不粘涂层的孔隙率通过金相显微镜观察样品截面,再通过iqmeterial软件设置不同衬度对其进行孔隙率测量。
89.(2)锅具上不粘涂层的强度测试
90.采用500g钢球从50cm高处垂直落下砸在锅具的内表面,不粘涂层不出现裂纹、破损、脱落则合格,反之不合格。
91.(3)锅具上不粘涂层的耐磨性测试
92.本技术中锅具表面的不粘涂层的耐磨性测试参照gb/t32095.2-2015进行,记录不粘涂层磨穿露底的耐磨次数。
93.(4)锅具上不粘涂层的持久不粘性测试
94.本技术中锅具表面不粘涂层的持久不粘性测试是在耐磨性测试的过程中增加一步每摩擦1000次做一个煎蛋测试,记录连续两次煎蛋出现“差(x)”时对应的摩擦次数。
95.表1性能指标测试结果
[0096][0097]
从表1中看出,本技术中通过将呈颗粒状且非晶合金包覆在多孔陶瓷材料表面的
复合材料经等离子喷涂形成不粘涂层,使形成的锅具具有好的不粘效果、持久不粘性以及耐磨性。
[0098]
从实施例1和对比例3中的测试结果可以看出,造粒形成的复合粉末热喷涂形成的不粘涂层比两种粉末直接混合后形成的不粘涂层具有更大的孔隙率、更好的耐磨性和持久不粘性。
[0099]
从实施例1~3和对比例2的测试结果可以看出,当原料粉末中多孔陶瓷粉末的质量占比过大时,造粒形成的复合粉末喷涂形成的涂层的具有大的孔隙率、好的耐磨性以及持久不粘性,但是形成的不粘涂层的强度不够,导致不粘涂层的使用寿命缩短。
[0100]
从实施例1和对比例1可以看出,原料粉末中多孔陶瓷材料的质量占比大于6%时造粒获得的复合粉末热喷涂形成的不粘涂层的耐磨性和持久不粘性效果提升明显。从实施例1~3和对比例4~5的测试结果发现,仅采用非晶合金形成的不粘涂层的孔隙率低,持久不粘性以及耐磨性也较差,而仅采用多孔陶瓷材料形成的不粘涂层根本无法使用。
[0101]
上面对本技术的具体实施方式进行了详细描述,虽然已表示和描述了一些实施例,但本领域技术人员应该理解,在不脱离由权利要求及其等同物限定其范围的本技术的原理和精神的情况下,可以对这些实施例进行修改和完善(例如,可以对不同实施例中描述的不同特征进行组合),这些修改和完善也应在本技术的保护范围内。