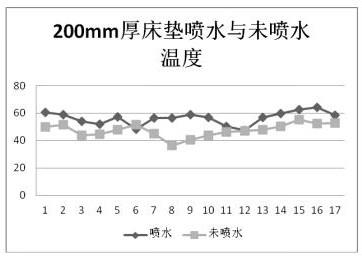
1.本发明涉及植物纤维床垫生产领域,特别是一种植物纤维床垫热压工艺。
背景技术:2.植物纤维床垫是指采用山棕、油棕、麻、竹纤维、椰壳纤维等植物纤维材料制备的床垫。中国专利90100464.2公开了一种植物纤维床垫的生产方法,植物纤维丝经卷曲后用气流吹成呈三维分布状后喷胶,使棕丝之间节点粘合得到植物纤维弹性片材,然后将弹性片材码叠,得到床垫。现有技术中,多层弹性片材码叠后,需要进行热压,将片材压制需要的厚度,本案申请人在2013年申请的中国专利cn103273601a公开了一种棕床垫热压成型方法及装置,用于床垫热压成型。长期使用发现,由于植物纤维弹性片材的纤维粗细、片材厚度等都不一样,同一批热压出来的床垫厚度、尺寸都会不一样,因此热压时需要精准控制弹性片材的整体温度,尽量使得床垫尺寸统一,控制要求高。而床垫热压需要的时间长(通常是15-100分钟不等),床垫越厚,热压时间越长。
技术实现要素:3.本发明的目的在于,提供一种植物纤维床垫热压工艺。可以减少热压时间,提高床垫质量,更为精准的控制床垫厚度。
4.本发明的技术方案:一种植物纤维床垫热压工艺,在植物纤维弹性片材热压前加入水分。
5.上述的植物纤维床垫热压工艺,所述水分与植物纤维弹性片材的重量比为0.5-5:100。
6.上述的植物纤维床垫热压工艺,所述水分与植物纤维弹性片材的重量比为1-3:100。
7.上述的植物纤维床垫热压工艺,所述加入水分是在植物纤维弹性片材上喷水。
8.上述的植物纤维床垫热压工艺,所述喷水压力为0.1-0.6mpa。
9.上述的植物纤维床垫热压工艺,所述喷水压力为0.2-0.4mpa。
10.上述的植物纤维床垫热压工艺,所述喷水采用直喷或雾化喷嘴。
11.上述的植物纤维床垫热压工艺,所述热压前5-60分钟加入水分。
12.上述的植物纤维床垫热压工艺,所述热压前10-30分钟加入水分。
13.本发明的有益效果:申请人实验发现,植物纤维弹性片材码叠上热压机之前,在片材表面喷上水。在热压时,热压板上的温度将床垫表面的水分气化,产生的水蒸气快速穿透至床垫内部,提升床垫内部升温速度,从而加速床垫中乳胶的胶凝速度,缩短热压时间,达到减少热压时间、提高床垫质量的目的。该效果适用于山棕、油棕、麻、竹纤维、椰壳纤维等所有现有的植物纤维。同时实验发现,热压时通入水蒸气并不能实现上述效果,反而因为水蒸气会使部分弹性片材收缩,导致床垫不均匀,影响床垫品质。因此在热压前加入水,而不是水蒸气。而加入水分过多,比如采用浸泡的方式,浸泡后床垫会变形,乳胶会脱落,影响粘
接效果。最终发现在片材表面喷上水分,能够提升热压效果,而不产生其他不良影响。
14.为证明本发明的效果,申请人实验对比如下:实验1,床垫内部温度影响实验。
15.实验方法:弹性片材码叠得到的床垫经预压后,将温度记录器插入床垫中间位置,然后一床喷水一床不喷水,进行床垫热压升温记录对比。分别对60mm、120mm、150mm、180mm和200mm厚度的床垫进行试验,结果见附图1-5。
16.对比可知,同种厚度规格的床垫,在同样喷水压力条件下,喷水床垫内部温度几乎都比未喷水床垫温度高,当床垫厚度在150mm及以下时,大部分温差集中在12-15℃,但当床垫厚度为180mm和200mm时,温差大部分集中在9-12℃。
17.床垫加入水分后,水分会不断挥发、流失,因此需要在5-60分钟内进行热压,否则热压时无法体现加水的效果。更好的是在10-30分钟内。
18.实验2,床垫热压时间影响实验。
19.实验方法:弹性片材码叠得到的床垫经预压后,将温度记录器插入床垫中间位置,然后一床喷水一床不喷水,将未喷水床垫按正常工艺进行热压,喷水床垫提前五分钟下热压机,然后按正常工艺硫化和吹冷,停放至第二天后进行切割测量床垫厚度,得出对比数据。分别对60mm、120mm、150mm和200mm厚度的床垫进行试验,经试验,对于60mm、120mm厚度的床垫,缩短热压时间的效果不明显,对于150mm、200mm厚度的床垫,热压时间长,在60分钟以上,可以减少3-5分钟的热压时间,有一定的效果。
20.实验3,喷水量实验实验方法:弹性片材码叠得到的床垫经预压后,将温度记录器插入床垫中间位置,然后通过调节喷水压力控制喷水量,将水分喷洒在床垫表面上,进行床垫热压升温记录对比。看不同的喷水量对热压效果的影响。
21.经实验,喷水量过少,床垫中的水分少,不利于热压的升温速度和最高温度,而喷水量过多,水分蒸发需要大量热能,会降低热压的升温速度,甚至会出现床垫变形,乳胶脱落的情况。经实验,水分与植物纤维弹性片材的重量比为0.5-5:100,能满足绝大部分植物纤维床垫热压所需。更好的是重量比为1-3:100。
22.实验4,喷水压力影响实验实验方法:弹性片材码叠得到的床垫经预压后,将温度记录器插入床垫中间位置,然后调节喷水压力,将水分喷洒在床垫表面上,进行床垫热压升温记录对比,得出对比数据。分别对60mm、120mm、150mm和200mm厚度的床垫进行试验,结果如下:经实验,喷水压力过小,水分集中在床垫表面,不利于渗透到床垫中间,热压时温度不均匀,同时在喷水量相同的情况下,压力越小,需要的时间越多,拖长了生产时间。而喷水压力小,不利于喷水量的控制,造成床垫中水分过多。经实验,喷水压力为0.1-0.6mpa适合绝大部分植物纤维床垫热压所需。更好的是,喷水压力为0.2-0.4mpa。
23.实验5,喷嘴影响实验实验方法,采用直喷型喷嘴和压缩空气雾化喷嘴进行试验。
24.结论:通过实验效果来看,两种都能将水均匀喷洒在床垫表面,均能达到床垫内部升温的效果,在相同喷水量的情况下,升温效果差不多,对床垫质量都没有影响。二者各有优缺点。
25.实验6,喷水对床垫质量影响实验方法,采用喷水和不喷水的床垫,按正常工艺进行热压、硫化和吹冷。然后对得到的床垫进行检测。目前进行了上千床的喷水实验和跟踪,基本可得出喷水对床垫质量没有负面影响。
26.总结,在热压前喷水,能够提高热压的最高温度,缩短热压升温时间,对于较厚的床垫,还能一定程度的缩短热压时间而不影响热压质量。同没有喷水相比,本发明的技术方案能够减少热压时间,提高床垫质量,更为精准的控制床垫厚度。
附图说明
27.图1-5是本发明的60mm、120mm、150mm、180mm和200mm厚度床垫内部温度影响实验数据对比图。
具体实施方式
28.下面结合实施例对本发明作进一步的说明,但并不作为对本发明限制的依据。
29.实施例1。一种植物纤维床垫热压工艺,在植物纤维弹性片材热压前加入水分。植物纤维丝经卷曲后用气流吹成呈三维分布状后喷胶,使棕丝之间节点粘合得到植物纤维弹性片材,然后将弹性片材码叠,进行热压。
30.进一步,所述水分与植物纤维弹性片材的重量比为0.5-5:100。更好的是,所述水分与植物纤维弹性片材的重量比为1-3:100。
31.所述加入水分是在植物纤维弹性片材上喷水。
32.进一步,所述喷水压力为0.1-0.6mpa。更好的是,所述喷水压力为0.2-0.4mpa。
33.所述喷水采用直喷或雾化喷嘴,喷嘴采用现有技术中的各种喷嘴,对实施效果影响不大。
34.进一步,所述热压前5-60分钟加入水分。更好的是,所述热压前10-30分钟加入水分。
35.实施例2。一种植物纤维床垫热压工艺,植物纤维丝经卷曲后用气流吹成呈三维分布状后喷胶,使棕丝之间节点粘合得到植物纤维弹性片材,然后将弹性片材码叠,在码叠的床垫上喷水。水分与植物纤维弹性片材的重量比为4:100。
36.所述加入水分是在植物纤维弹性片材上喷水。喷水d 压力为0.3mpa。
37.所述喷水采用直喷喷嘴,喷水后40分钟进行热压,热压得到200mm厚度的床垫。
38.实施例3。一种植物纤维床垫热压工艺,植物纤维丝经卷曲后用气流吹成呈三维分布状后喷胶,使棕丝之间节点粘合得到植物纤维弹性片材,然后将弹性片材码叠,在码叠的床垫上喷水。水分与植物纤维弹性片材的重量比为1:100。
39.所述加入水分是在植物纤维弹性片材上喷水。喷水d 压力为0.4mpa。
40.所述喷水采用直喷喷嘴,喷水后30分钟进行热压,热压得到150mm厚度的床垫。
41.实施例4。一种植物纤维床垫热压工艺,植物纤维丝经卷曲后用气流吹成呈三维分布状后喷胶,使棕丝之间节点粘合得到植物纤维弹性片材,然后将弹性片材码叠,在码叠的床垫上喷水。水分与植物纤维弹性片材的重量比为0.8:100。
42.所述加入水分是在植物纤维弹性片材上喷水。喷水d 压力为0.2mpa。
43.所述喷水采用直喷喷嘴,喷水后20分钟进行热压,热压得到60mm厚度的床垫。
44.实施例5。一种植物纤维床垫热压工艺,植物纤维丝经卷曲后用气流吹成呈三维分布状后喷胶,使棕丝之间节点粘合得到植物纤维弹性片材,然后将弹性片材码叠,在码叠的床垫上喷水。水分与植物纤维弹性片材的重量比为2:100。
45.所述加入水分是在植物纤维弹性片材上喷水。喷水d 压力为0.35mpa。
46.所述喷水采用直喷喷嘴,喷水后15分钟进行热压,热压得到120mm厚度的床垫。