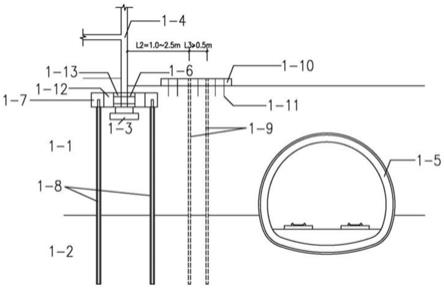
浅埋隧道邻近建筑隔离
‑
托换组合加固构造及其施工工艺
技术领域
1.本发明涉及隧道工程技术领域,具体涉及浅埋隧道邻近建筑隔离
‑
托换组合加固构造及其施工工艺。
背景技术:2.近年来,随着我国城镇化建设持续快速开展,城市用地紧缺与交通拥堵问题愈发严重,地铁建设作为一种解决城市交通问题的重要手段,其施工方法及对周围环境的影响也愈发受到关注。目前,由于城市地下交通隧道大多数位于主干道下方,而多采用浅埋暗挖方法进行施工。隧道在浅埋暗挖过程中如其临近范围内存在浅基础的砖混结构等此类对不均匀沉降较为敏感的建筑物时,易导致建筑物产生损伤、裂缝甚至倒塌、倾覆等事故;此外,由于部分城市地表以下土岩地层转换较快,隧道结构常处于土
‑
岩组合介质中,围岩物理力学参数急剧变化可能增大隧道施工及周边环境的安全的风险。
3.当前城市地下交通隧道所采取的保护法主要有隔离法、基础托换、地层加固等,各方法均有各自的局限性:隔离桩一般为设置在隧道两侧阻隔地基附加应力的单排钻孔灌注桩或微型桩,钻孔灌注桩在城市施工场地较难具备施工条件,而单排微型桩由于其长径比大、抗弯刚度较小,其阻隔应力的能力较差;基础托换技术是将上部荷载从原基础转移到新的托换结构上,但当土层因隧道工程施工而造成沉降时,并不能减少此地基沉降,势必使托换结构内力增加;地层加固法例如注浆法等在实际应用中于对承载力与变形有特殊要求的工程时有一定局限性。
4.综上,土岩组合地层中浅埋暗挖隧道施工期间针对临近建筑物的有效保护措施亟待提出与研究。
技术实现要素:5.针对上述存在的问题,本发明旨在提供可应用于土岩地层中的浅埋隧道邻近建筑隔离
‑
托换组合加固构造及其施工工艺,通过在土岩组合地层条件下应用双排微型钢管隔离桩体系与微型桩托换基础的组合构造,形成了多道抵抗不均匀沉降的防线,保证在既有沉降敏感型建筑物下方有隧道穿越时,减小基础及上部结构的因隧道施工而受到的不利影响,具有使用方便,承载能力高,隔离能力强的特点。
6.为了实现上述目的,本发明所采用的技术方案如下:
7.一种浅埋隧道邻近建筑隔离
‑
托换组合加固构造,所述组合加固构造在隧道施工前从地面提前施作,包括双排微型钢管隔离桩体系和微型桩托换基础,所述双排微型钢管隔离桩体系和微型桩托换基础均穿过土质地层嵌入岩质地层内;
8.所述双排微型钢管隔离桩体系设置在既有建筑物与在建隧道之间,且沿在建隧道侧面纵向布置,包括两排微型钢管隔离桩,所述微型钢管隔离桩的桩顶通过钢筋混凝土现浇顶板连接为一整体,所述钢筋混凝土现浇顶板通过若干插筋与地表连接;
9.所述微型桩托换基础包括相互连接的托换微型桩和微型桩承台梁,所述托换微型
桩对称设置在既有建筑物的原基础下端,所述微型桩承台梁设置在托换微型桩的顶端,且通过植筋、连梁和现浇混凝土与原基础连接。
10.优选的,所述的微型钢管隔离桩入岩质地层的嵌固深度不小于2.0m,同排的微型钢管隔离桩的横向间距为0.5~1.0m,双排微型钢管隔离桩体系中靠近既有建筑物外墙侧的微型钢管隔离桩距建筑物外墙距离为1.0m~2.5m,前、后排桩间距大于0.5m。
11.优选的,所述的微型钢管隔离桩和托换微型桩均包括热轧无缝钢管与其周围及管内的注浆体,热轧无缝钢管桩顶进入钢筋混凝土现浇顶板一定长度并可靠连接,前、后两排的微型钢管隔离桩均通过现浇钢筋混凝土顶板连接,所述现浇钢筋混凝土顶板内配置有板顶受力筋、板顶分布筋、板底分布筋、板底受力筋,所述插筋嵌入地表一定深度;所述热轧无缝钢管的直径为108mm,壁厚为4.5mm,所述钢管内部及管周填充水灰比为0.6的水泥浆,注浆压力不小于0.2mpa。
12.优选的,所述的托换微型桩桩顶进入微型桩承台梁一定长度,连梁与既有建筑物的结构柱通过植筋连接,微型桩承台梁、连梁与结构柱之间的空隙由现浇混凝土填充。
13.优选的,所述的既有建筑物为沉降敏感型建筑物或重要建筑物,所述原基础为毛石或钢筋混凝土独立基础,在建隧道为浅埋暗挖隧道。
14.一种浅埋隧道邻近建筑隔离
‑
托换组合加固构造的施工工艺,所述施工工艺包括:
15.步骤一:基础周围测量放线及隔离桩位测量放线
16.根据施工平面图确定地下管线实地位置并放出走向,在探沟开挖前,根据要求放出探沟基坑边线及定出桩位,确定为探沟开挖中心线两侧各外扩0.3m为探沟开挖边线;
17.步骤二:基础开挖及沟槽开挖
18.开挖沟槽至设计桩顶位置,且当建筑物有地下室时,需完全露出板顶,且保证钢管外露出沟槽底30cm,以便注浆作业;
19.步骤三:钢管桩制作
20.步骤四:微型钢管隔离桩及托换微型桩成孔
21.步骤五:拌制水泥浆
22.水泥浆采用专用灰浆搅拌机进行拌制,水灰比控制在0.6左右,把拌制的水泥浆放入钢制灰槽内,由注浆机注浆,对于湿陷性黄土地质,采用水泥水玻璃双液浆进行灌注,水泥水玻璃配比为1:1;
23.步骤六:送管
24.微型钢管隔离桩及托换微型桩在钢管插管过程中,利用丝扣对钢管进行对接,形成钢管桩结构;
25.步骤七:微型钢管隔离桩及托换微型桩注浆
26.步骤八:钢筋混凝土现浇顶板施工
27.在微型钢管隔离桩顶开挖基槽后布置板顶板底钢筋并浇筑混凝土,在现浇钢筋混凝土顶板上使用插筋将钢筋混凝土现浇顶板与地表固定连接;
28.步骤九:微型桩承台梁及连梁垫层施工
29.在钢筋混凝土现浇顶板施工的同时,进行微型桩承台梁及连梁垫层施工,在现有基础两侧挖土,在坑底浇筑不低于c15的素混凝土垫层,厚度不小于100mm;
30.步骤十:承台梁及连梁施工
31.在基础两侧挖好的坑中放入钢筋笼,钢管伸进连梁一定深度,将钢筋笼与钢管连接,并浇筑混凝土成型;
32.步骤十一:对原基础上柱与连梁进行植筋
33.植筋选用hrb400级及以上钢筋,钢筋直径不小于16mm;
34.步骤十二:浇筑混凝土连接连梁与原基础上柱。
35.步骤十三:监控量测
36.对在隧道轴线上方两侧1.5倍隧道基底深度范围内的所有建筑物的墙角、立柱或外墙每30m布一监测点进行变形监测,建筑物沉降点布设于基础类型、埋深和荷载有明显不同处及沉降缝、伸缩缝、新老建筑物连接处的两侧;监测点布设方法为直接用电锤在建筑物外侧墙体上打洞,将“l”型沉降标或直径不小于18mm的螺纹钢埋入钻孔中并用植筋胶加固。监测频率及监测报警值根据相关规范要求确定。
37.优选的,步骤四所述的微型桩成孔过程具体包括:
38.s401.进行钻孔作业,钻孔时做到桩位正,桩身直,钻机按导向管设计位置就位固定后,沿导向管施钻;
39.s402.施钻时,钻机开孔时钻速应低,钻进1.0m后转入正常钻速,潜孔钻机的钻杆每节长度为3m,钻孔时必须接杆;
40.s403.第一节钻杆钻入岩土层,尾部剩余20~30cm时停止钻进,人工用管钳卡紧钻杆,钻机低速反转,脱开钻杆;
41.s404.钻机沿导轨退出后,人工装入第二根钻杆,并在钻杆前端安装好联结套,钻机低速送至第一根钻杆尾部,方向对准后联结成一体,每次接长钻杆,按上述方法进行,并在钻孔钻至设计深度后,退钻杆成孔清孔。
42.优选的,步骤六所述送管的具体过程包括:
43.s601.钢管桩采用φ108热轧无缝钢管,按打桩先后顺序及桩的配套要求堆放;
44.s602.起吊钢管桩采用一点绑扎起吊,待吊到桩位进行插桩,清孔结束立即采用挖掘机配合简易架插入钢管,钢管外露出沟槽底30cm;
45.s603.为使钢管对接,在每孔的第一节管打设时,奇、偶孔分别用3m、4.5m的钢管,以后每节均采用4.5m长钢管;
46.s604.钢管接长时先将前一根钢管顶入钻好的孔内,采用内套管联结;
47.s605.当前一根钢管推进孔内,孔外剩余30~40cm时,人工装上后一节钢管,电焊工将钢管联结在内套管上,采用丝扣将两节钢管联成一体,丝扣长15cm;
48.s606.依次进行上述步骤s605,完成对钢管的连接。
49.优选的,步骤七所述的注浆过程中,需注意:
50.(1)托换微型桩及微型钢管隔离桩钻至设计桩长后,随即下入钢管,采用注浆泵进行水泥浆灌注,直至灌满,在软弱土层中为防止塌孔采用钻孔
‑
送管
‑
注浆流水作业;
51.(2)注浆采用水灰比0.6的水泥浆,注浆压力不小于0.2mpa,注浆后暂不拔管,直至水泥浆从管外流出为止,拔出注浆管后对钢管端部进行密封;
52.(3)在所述的注浆过程中,因一次注浆难以达到浆液充盈要求,为保证注浆质量和效果,注浆时分二次进行,一次注浆后2小时,待第一次注入浆液初凝后,进行二次压力注浆。
53.优选的,步骤十二所述的浇筑混凝土连接连梁与原基础上柱放入具体过程包括:
54.s1201.在新旧混凝土连接界面处做凿毛处理,凿毛混凝土表面并打出沟槽,沟槽深度8~10mm,间距1000mm;
55.s1202.湿润和清洗混凝土表面,在混凝土表面清洗干净充分湿润后,在浇筑混凝土前刷界面剂或素水泥浆,使原基础上柱与连梁胶结为整体,形成新旧基础的托换关系。
56.本发明的有益效果是:本发明公开了浅埋隧道邻近建筑隔离
‑
托换组合加固构造及其施工工艺,与现有技术相比,本发明的改进之处在于:
57.针对现有技术存在的问题,本发明设计了一种可应用于土岩地层中的浅埋隧道邻近建筑隔离
‑
托换组合加固构造及其施工工艺,通过利用微型桩托换基础与双排微型钢管隔离桩体系组合而成的隔离
‑
托换组合加固构造对施工于土岩组合地层中的浅埋暗挖隧道邻近的沉降敏感型建筑物进行基础及上部结构的保护;托换基础中的微型桩可辅助双排微型钢管隔离桩隔离附加应力,形成多道抵抗不均匀沉降的防线,进一步降低因隧道施工引起的地表沉降;其次,双排微型钢管隔离桩桩顶与现浇钢筋混凝土顶板可靠连接,桩底嵌入岩层足够深度所形成的底部支座刚接的刚架体系,其抗侧刚度与内力分布明显优于单排微型钢管桩,极大的增强了其隔离附加应力的能力;同时,将微型钢管隔离桩嵌入至岩体内部,增强了底部约束,提高了其隔离能力,将土岩界面突变的组合地层这一不利条件转化为有利条件;最后,微型桩托换基础及双排微型钢管隔离桩体系可在狭窄的场地中施工,施工灵活,对原有地基土扰动较小,施工对环境的污染及噪音较小,适合于在城区内施工,能够完全满足浅埋隧道近地接建筑物隔离桩的施工,具有使用方便,承载能力高,隔离能力强的特点。
附图说明
58.图1为本发明浅埋隧道邻近建筑隔离
‑
托换组合加固构造施工工艺的施工流程图。
59.图2是土岩组合地层浅埋隧道邻近建筑隔离
‑
托换组合加固示意图。
60.图3是既有建筑物基础托换示意图。
61.图4是双排微型钢管隔离桩大样图。
62.图5为本发明钻机钻孔过程中的隔离桩现场施工图。
63.图6为本发明注浆压浆过程中的隔离桩现场施工图。
64.图7为本发明监控点安装示意图。
65.图8为本发明实施例1玉函路东侧某公证处砌体结构图。
66.图9为本发明实施例1玉函路东侧被保护邻近建筑图。
67.图10为本发明实施例1工程2的隔离保护做法示意图。
68.图11为本发明实施例2验证计算有限元模型图。
69.图12为本发明实施例2有限元模型计算结果图。
70.图13为本发明实施例2有限元模型图。
71.图14为本发明实施例2观测点a处沉降值柱状图1。
72.图15为本发明实施例2观测点a处沉降值柱状图2。
73.图16为本发明实施例2观测点a处沉降值柱状图3。
74.图17为本发明实施例2观测点a处沉降值柱状图4。
75.图18为本发明实施例2墙体应变云图。
76.其中:在图6中:图(a)为本发明注浆压浆过程后的隔离桩布置图;图(b)为本发明注浆压浆过程中的注浆机分布图,在图11中:图(a)为本发明实施例2无隔离桩时有限元模型,图(b)为本发明实施例2有隔离桩时有限元模型;在图12中:图(a)为本发明实施例2有限元模型土层变位曲线图,图(b)为本发明实施例2有限元模型基底沉降曲线图;在图13中:图(a)为本发明实施例2单排隔离桩有限元模型,图(b)为本发明实施例2双排隔离桩有限元模型;在图18中:图(a)为本发明实施例2布置单排隔离桩时砌体结构墙体应变云图,图(b)为本发明实施例2布置双排隔离桩时砌体结构墙体应变云图;
[0077]1‑
1.土质地层,1
‑
2.岩质地层,1
‑
3.原基础,1
‑
4.既有建筑物,1
‑
5.在建隧道,1
‑
6.植筋,1
‑
7.微型桩承台梁,1
‑
8.托换微型桩,1
‑
9.微型钢管隔离桩,1
‑
10.钢筋混凝土现浇顶板,1
‑
11.插筋,1
‑
12.连梁,1
‑
13.现浇混凝土,1
‑
14.结构柱,2
‑
1.热轧无缝钢管,2
‑
2.注浆体,2
‑
3.板顶受力筋,2
‑
4.板顶分布筋,2
‑
5.板底分布筋,2
‑
6.板底受力筋。
具体实施方式
[0078]
为了使本领域的普通技术人员能更好的理解本发明的技术方案,下面结合附图和实施例对本发明的技术方案做进一步的描述。
[0079]
参照附图1~18所示的浅埋隧道邻近建筑隔离
‑
托换组合加固构造及其施工工艺,包括:
[0080]
施工流程图见图1,施工工艺包括以下步骤:
[0081]
步骤一:基础周围测量放线及隔离桩位测量放线
[0082]
根据业主提供的现场管线平面布置图,确定地下管线实地位置并放出走向;将探沟基坑边线、地下管线实地位置走向及隧道开挖轮廓线直观反映在路面,在探沟开挖前,根据设计要求放出探沟基坑边线及定出桩位,测量组按照提供的微型钢管隔离桩平面图的中线确定为探沟开挖中心线,两侧由微型钢管隔离桩各外扩0.3m,确定探沟开挖边线,确定基础与沟槽开挖范围。
[0083]
步骤二:基础开挖及沟槽开挖
[0084]
通过开挖了解管线平面布置图所示管线具体分布位置,进一步调查摸清地下管线、地下障碍物等分布、种类、及深度,场地外管线网分布,施工区域或有位探明地下管线通过;将发现的地下管线全部清理暴露出地面,探明管线路径、埋深;现场施工人员需认真检查,不能漏挖、错挖;若发现地下管线与业主提供的资料不符,及时通知设计单位;根据实地探查情况,对隔离微型桩桩位根据现场实际适当调整;
[0085]
沟槽开挖时,路面割缝后用小油锤破除,人工开挖,开挖时必须小心,用铁锨轻挖,不得用镐头、风镐等尖锐工具开挖;发现土质变化时应及时将覆盖物清除干净,以保证不损坏地下管线,开挖渣土装袋外运,保证渣土不落地;开挖施工过程中,所探明的管线详细记录种类、规格、根数、走向和深度;
[0086]
设计桩顶为地面下1m,当建筑物有地下室时,钢管高出板顶,钢管外露出沟槽底30cm以便于注浆作业。
[0087]
步骤三:钢管桩制作
[0088]
钢管桩可在集中区域加工,采用自卸货车或平板拖车等运输至现场,钢管应提前
进行除锈及防腐处理,对长度有变化的钢管应及提前加工准备。
[0089]
步骤四:微型桩成孔,工程现场如图5所示,具体包括:
[0090]
s401.将钻机进行调试,确保各方面达到要求后,开启操作手柄让钻机低速转动,调试合格钻机工作正常即可进行钻孔作业,成孔直径130mm,钻孔时做到桩位正,桩身直,钻机按导向管设计位置就位固定后,沿导向管施钻;
[0091]
s402.施钻时,防止过大颤动影响施钻精度,钻机开孔时钻速宜低,以保证开孔质量,钻进1.0m后转入正常钻速,潜孔钻机的钻杆每节长度为3m,钻孔时必须接杆;
[0092]
s403.第一节钻杆钻入岩土层,尾部剩余20~30cm时停止钻进,人工用两把管钳卡紧钻杆,钻机低速反转,脱开钻杆;
[0093]
s404.钻机沿导轨退后,人工装入第二根钻杆,并在钻杆前端安装好联结套,钻机低速送至第一根钻杆尾部,方向对准后联结成一体。每次接长钻杆,按上述方法进行;为保证钻机连续作业,现场配备两个钻头。钻孔钻至设计深度,退钻杆成孔清孔,现场施工情况见图3;
[0094]
对于斜桩可将带有吊锤的量角器置于钻杆上,通过调整钻杆,既使钻杆对准入土点,又要使钻杆竖直角符合设计要求,然后锁定立轴;施工时要注意钻孔偏斜度,及时用钻孔测斜仪进行成孔角度测量,纠正偏斜。
[0095]
步骤五:拌制水泥浆,水泥浆采用专用灰浆搅拌机进行拌制,水灰比控制在0.6左右,把拌制的水泥浆放入钢制灰槽内,由注浆机注浆;
[0096]
且在搅拌过程中需注意:
[0097]
注浆管由注浆机直接接入到钢管桩的注浆钢管上,接口处采用丝口连接,注浆管采用橡胶管输送;此外,对于湿陷性黄土地质,采用水泥水玻璃双液浆进行灌注,水泥水玻璃配比为1:1。
[0098]
步骤六:送管,具体包括:
[0099]
s601.钢管桩身采用φ108热轧无缝钢管,可集中在加工区域加工,采用自卸货车或平板拖车运至现场,用吊车卸于桩机一侧,按打桩先后顺序及桩的配套要求堆放,并注意方向;
[0100]
s602.起吊钢管桩采用一点绑扎起吊,待吊到桩位进行插桩,清孔结束立即采用挖掘机配合简易架插入钢管,钢管外露出沟槽底30cm,以便连接注浆管;
[0101]
s603.为使钢管接头错开,在每孔的第一节钢管打设时,奇、偶孔分别用3m、4.5m的钢管,以后每节均采用4.5m长钢管;
[0102]
s604.钢管接长时先将前一根钢管顶入钻好的孔内,采用内套管联结;
[0103]
s605.当前一根钢管推进孔内,孔外剩余30~40cm时,人工装上后一节钢管,电焊工将钢管联结在内套管上,采用丝扣将两节钢管联成一体,丝扣长15cm;
[0104]
s606.依次进行上述步骤s605,完成对钢管的连接。
[0105]
步骤七:注浆,现场施工情况见图6,需注意:
[0106]
(1)托换微型桩及微型钢管隔离桩钻至设计桩长后,随即下入钢管,采用注浆泵进行水泥浆灌注,直至灌满,在软弱土层中为防止塌孔采用钻孔
‑
送管
‑
注浆流水作业;
[0107]
(2)注浆采用水灰比0.6的水泥浆,注浆压力不小于0.2mpa,注浆后暂不拔管,直至水泥浆从管外流出为止,拔出注浆管后对钢管端部进行密封;
[0108]
(3)在所述的注浆过程中,因一次注浆难以达到浆液充盈要求,为保证注浆质量和效果,注浆时分二次进行,一次注浆后2小时,待第一次注入浆液初凝后,进行二次压力注浆;
[0109]
(4)注浆前,应全面检查注浆设备与材料,包括注浆泵、拌浆储浆系统、高压压浆管、压力表等,并用清水试泵;
[0110]
(5)微型桩钻至设计桩长后,随即下入钢管,用注浆泵灌注水泥浆,直至灌满为止,为防止塌孔采用钻孔
‑
送管
‑
注浆流水作业;
[0111]
(6)注浆前先进行注浆现场试验,根据实际情况确定合理注浆次数和单孔注浆量。正式注浆后不随意中断,力求连续作业,以保证注浆质量;
[0112]
(7)注浆采用水灰比0.6的水泥浆,注浆压力为0.2mpa,注浆泵需装设压力表,压力表量程为0~1.0mpa,注浆后暂不拔管,直至水泥浆从管外流出为止,拔出注浆管密封钢管端部,隔离桩注浆施工如图3所示;
[0113]
(8)在所述的注浆过程中,因一次注浆难以达到浆液充盈要求,为保证注浆质量和效果,注浆时分二次进行,一次注浆后2小时,待第一次注入浆液初凝后,进行二次压力注浆。
[0114]
步骤八:钢筋混凝土现浇顶板施工,在微型钢管桩顶开挖基槽后布置板顶板底钢筋并浇筑混凝土,在现浇钢筋混凝土顶板上使用插筋将钢筋混凝土现浇顶板与地表固定连接,双排微型钢管隔离桩体系大样图见图4。
[0115]
步骤九:在钢筋混凝土现浇顶板施工的同时,进行微型桩承台梁及连梁垫层施工,在现有基础两侧挖土,在坑底浇筑不低于c15的素混凝土垫层,厚度不小于100mm。
[0116]
步骤十:承台梁及连梁施工,在基础两侧挖好的坑中放入钢筋笼,钢管应伸进连梁一定深度内,将钢筋笼与钢管进行可靠连接,并浇筑混凝土成型,双排微型钢管隔离桩体系与托换基础的相对位置见图3。
[0117]
步骤十一:对原基础上柱与连梁进行植筋,植筋选用hrb400级及以上钢筋,钢筋直径不小于16mm。
[0118]
步骤十二:连梁与原基础上柱之间的空间通过浇筑混凝土的方式连接,施工中做好新旧界面的处理,凿毛混凝土表面并打出沟槽,沟槽深度8~10mm,间距1000mm,将混凝土表面清洗干净充分湿润后,在浇筑混凝土前刷界面剂或素水泥浆,保证连接面的质量及可靠性,使原基础上柱与连梁胶结为整体,形成新旧基础的托换关系,至此完成隔离托换组合加固构造,示意图见图2。
[0119]
步骤十三:监控量测
[0120]
为保证隧道暗挖结构的稳定和施工安全及防止建筑物开裂、倾斜、破坏,确保邻近建筑物及地下管线等周边环境的正常使用,对在隧道轴线上方两侧1.5倍隧道基底深度范围内的所有建筑物的墙角、立柱或外墙每30m布一监测点进行变形监测,建筑物沉降点布设于基础类型、埋深和荷载有明显不同处及沉降缝、伸缩缝、新老建筑物连接处的两侧;监测点布设方法为直接用电锤在建筑物外侧墙体上打洞,将“l”型沉降标(如图7所示)或直径不小于18mm的螺纹钢埋入钻孔中并用植筋胶加固。监测频率及监测报警值根据相关规范要求确定。
[0121]
通过上述施工工艺得到的浅埋隧道邻近建筑隔离
‑
托换组合加固构造见图2,包括
双排微型钢管隔离桩体系和微型桩托换基础,所述双排微型钢管隔离桩体系和微型桩托换基础均穿过土质地层1
‑
1嵌入岩质地层1
‑
2内,形成了多道抵抗不均匀沉降的防线,保证在既有沉降敏感型建筑物下方有隧道穿越时,减小基础及上部结构因隧道施工而受到的不利影响,此外,微型桩托换基础的微型钢管桩也可同时对浅埋暗挖隧道开挖引起的附加应力变化有辅助隔离作用,托换基础的微型钢管桩与双排微型钢管隔离桩体系共同工作,对远离基坑侧的基础进行保护;
[0122]
所述双排微型钢管隔离桩体系见图4,其设置在既有建筑物1
‑
4与在建隧道1
‑
5之间,且沿在建隧道1
‑
5侧面纵向布置,包括两排微型钢管隔离桩1
‑
9,所述微型钢管隔离桩1
‑
9的桩顶通过钢筋混凝土现浇顶板1
‑
10连接为一整体,所述钢筋混凝土现浇顶板1
‑
10通过若干插筋1
‑
11与地表连接;
[0123]
所述微型桩托换基础包括相互连接的托换微型桩1
‑
8和微型桩承台梁1
‑
7,所述托换微型桩1
‑
8对称设置在既有建筑物1
‑
4的原基础1
‑
3下端,所述微型桩承台梁1
‑
7设置在托换微型桩1
‑
8的顶端,且通过植筋1
‑
6、连梁1
‑
12和现浇混凝土1
‑
13与原基础1
‑
3连接,使得原有基础所承受的上部荷载由微型桩托换基础所承担。
[0124]
优选的,所述的微型钢管隔离桩1
‑
9入岩质地层1
‑
2的嵌固深度不小于2.0m,桩顶与现浇钢筋混凝土顶板1
‑
10可靠连接,使嵌入岩层足够深度的双排微型钢管隔离桩与钢筋混凝土顶板形成底部支座刚接的刚架体系,极大的增强其隔离附加应力的能力;同排的微型钢管隔离桩1
‑
9的横向间距为0.5~1.0m,双排微型钢管隔离桩体系中靠近既有建筑物1
‑
4外墙侧的微型钢管隔离桩1
‑
9距建筑物1
‑
4外墙距离为1.0m~2.5m,前、后排桩间距大于0.5m,且近隧道侧微型钢管隔离桩1
‑
9应尽量靠近在建隧道1
‑
5,近既有建筑物侧微型钢管隔离桩应尽可能靠近既有建筑物1
‑
4。
[0125]
优选的,所述的微型钢管隔离桩1
‑
9和托换微型桩1
‑
8均包括热轧无缝钢管2
‑
1与其周围及管内的注浆体2
‑
2,上述两种微型桩均通过机械钻孔方式安装,减小周围土体的扰动;所述热轧无缝钢管2
‑
1桩顶进入钢筋混凝土现浇顶板1
‑
10一定长度并可靠连接,前、后两排的微型钢管隔离桩1
‑
9均通过现浇钢筋混凝土顶板1
‑
10连接,所述现浇钢筋混凝土顶板1
‑
10内配置有板顶受力筋2
‑
3、板顶分布筋2
‑
4、板底分布筋2
‑
5、板底受力筋2
‑
6,所述插筋1
‑
11嵌入地表一定深度;所述热轧无缝钢管2
‑
1的直径为108mm,壁厚为4.5mm,所述钢管内部及管周填充水灰比为0.6的水泥浆,注浆压力不小于0.2mpa。
[0126]
优选的,所述的托换微型桩1
‑
8桩顶进入微型桩承台梁1
‑
7一定长度,连梁1
‑
12与既有建筑物1
‑
4的结构柱通过植筋1
‑
6连接,微型桩承台梁1
‑
7、连梁1
‑
12与结构柱之间的空隙由现浇混凝土1
‑
13填充。
[0127]
优选的,所述的既有建筑物1
‑
4为沉降敏感型建筑物或重要建筑物,所述原基础1
‑
3为毛石或钢筋混凝土独立基础,在建隧道1
‑
5为浅埋暗挖隧道。
[0128]
优选的,如上所述的双排微型钢管隔离桩体系可以与微型桩托换基础同时施工,通过并行施工缩短工期与节约成本。
[0129]
优选的,上述加固构造中所应用的双排微型钢管隔离桩体系与微型桩托换基础可在狭窄的场地中施工,施工灵活,对原有地基土扰动较小,施工对环境的污染及噪音较小,适合于在城区内施工。
[0130]
优选的,连梁与原基础上柱之间的空间以现浇混凝土进行填充,使原基础上结构
柱与连梁胶结为整体,形成新旧基础的托换关系。
[0131]
优选的,在土岩组合地层中,当土岩界面位于隧道起拱线位置及以上时,隧道开挖的土拱效应能得充分利用,基底沉降及砌体结构墙体应变均较小,远低于土岩界面位于隧道起拱线以下时产生的沉降及墙体应变,隧道施工可利用土拱效应这一特点,对周边环境的影响作出定性判断及预先加固建议;
[0132]
优选的,城市浅埋隧道采用微型钢管隔离桩,与钢筋砼灌注桩相比操作简单,施工方便快速,造价低效率高,节能减排,取得较好的社会经济环保效果。
[0133]
实施例1:本发明所述浅埋隧道近地接建筑物施工隔离桩结构的施工工艺的具体应用实例:
[0134]
1.工程一:
[0135]
在济南玉函路沿线,某公证处距离隧道最近,某公证处及邻近道路见图8;工程场地位于玉函路以东,某公证处b、c轴间为地上三层砖混结构(局部为两层),毛石混凝土条形基础,基础埋深1.75m;a轴为框架柱,一层为室外走廊,毛石混凝土条形基础,基础宽度0.8m,基础埋深1.3m。该处隧道边线距a轴柱约1.7m,隧道顶至地面10.37m;
[0136]
2.工程二:
[0137]
济南市顺河高架南延二期工程玉函路隧道北起顺河高架路南端南至英雄山路高架路北端,全长3.26km,是济南市快速路网规划系统的重要组成部分,其中明挖暗埋段全长0.91km,暗挖段全长2.35km。暗挖段采用双隧设计,两隧间距2~3m,埋深8~11m,标准断面净宽9.19m,净高7.3m,为城市超浅埋小净距隧道。隧道贯穿城市繁华地区,两侧楼房建筑物密布,多为60年代砖混结构,基本以4~6层居民楼为主,紧靠路边人行道,如图9所示;
[0138]
建筑基础下土层为杂填土、粉质粘土、中等湿陷性黄土,暗挖边线距离两侧楼房建筑最小2.5m。隧道围岩条件较差,地质为v级土石结合软弱围岩,黄黏土及湿陷性黄土洞段917m,遇水丧失强度,石灰岩洞段1418m,岩溶发育。
[0139]
3.上述工程一与工程二的场地范围内土层自上而下详述如下:
[0140]
(1)填土:分为杂填土、素填土及碎石素填土;
[0141]
①
杂填土:杂色,松散~稍密,含大量砖块、碎石、灰渣、混凝土块等建筑垃圾,该层分布较连续,上部多为道路结构层;该段范围厚度3.8m~8.0m,厚度向南减小;
[0142]
(2)黄土、碎石:该层以
②
黄土为主,局部为
②‑
1碎石;
[0143]
②
黄土:褐黄色,可~硬塑,局部呈坚硬状态,稍湿,含氧化铁、少量白色钙质条纹,具虫孔,局部含少量姜石;湿陷性黄土场地的湿陷类型为非自重湿陷性黄土场地;
[0144]
(3)粉质粘土、碎石:该层以
③
粉质粘土为主,局部为
③‑
1碎石;
[0145]
③
粉质粘土:浅棕黄~棕黄色,可~硬塑,局部呈坚硬状态,含铁锰氧化物、零星碎石,在拟建线路北部路西及中部两侧分布较多,其余路段该层分布不连续;
[0146]
(4)粘土、碎石、粉质粘土:该层以
④
粘土为主,局部有
④‑
1碎石与
④‑
2粉质粘土夹层;
[0147]
④
粘土:棕黄色,可~硬塑,局部呈坚硬状态,含铁锰氧化物、零星碎石;该层在分布不连续,在马鞍山路到七里山路之间分布较多,其余路段呈透镜体状分布;
[0148]
④‑
1碎石:杂色,中密,母岩成份为灰岩,次棱角状,粒径1~10cm,含量65~80%,
[0149]
④‑
2粉质粘土:棕黄色;可~硬塑,含铁锰氧化物,该亚层分布不连续,仅在道路沿
线部分钻孔呈薄层或透镜体状分布;
[0150]
(5)石灰岩、泥灰岩:
[0151]
⑤
中风化石灰岩:青灰色,局部为灰黄色、肉红色,坚硬,致密,隐晶结构,层状构造,钻探岩芯呈短柱状~柱状,柱长5~48cm,采取率50~95%,rqd=34~90,局部有裂隙发育,个别岩芯表面有溶蚀发育;
[0152]
⑤‑
1中风化石灰岩:青灰色,局部为灰黄色,钻探岩芯呈短柱状~柱状,柱长2~36cm,采取率30~48%,rqd=10~45,裂隙、溶蚀较发育,溶隙中充填棕红色硬塑粘土;
[0153]
⑤‑
2中风化石灰岩:青灰色,钻探岩芯呈碎块状、短柱状,柱长2~15cm,采取率15~30%,rqd=0~21,裂隙、溶蚀发育,溶隙中充填有棕红色硬塑粘土;
[0154]
4.具体建筑物隔离及托换加固设计如下:
[0155]
(2)针对工程一:
[0156]
为保证隧道施工过程中及以后建筑物的正常使用,对此建筑物应用隔离
‑
托换组合加固构造。采用双排微型钢管隔离桩进行隔离,微型钢管桩进行基础托换,见图2所示,具体加固内容如下:
[0157]
1、对柱下独立基础采取微型桩进行托换,桩顶新增承台梁,框架柱位置通过植筋及新浇混凝土与承台梁连接,同时在框架柱以西施工两排隔离桩,微型钢管隔离桩成孔直径130mm,主体为φ108钢管,南北向间距0.5m,东西向排距1m,微型桩底进入中风化岩石2m,桩顶做钢筋混凝土顶板;
[0158]
2、托换及隔离用微型桩均采用机械成孔,主体采用钢管,成孔直径130mm,桩底进入完整中风化岩石不小于2m(自承台底算起),微型桩顶部伸入承台50mm;微型桩钻至设计桩长后,下入钢管,用压力注水泥浆,直至灌满为止,注浆压力为0.2mpa;
[0159]
3、桩顶新增承台梁,南北向承台梁间每隔1.8m增设一根连梁,新增承台梁底设置100mm的c15混凝土垫层,承台梁与框架柱进行植筋,植筋采用直径16mm的hrb400级钢筋,插筋孔内灌结构胶;
[0160]
4、施工中须做好基础新旧界面的处理,凿去面层直至混凝土表面,凿毛且打出沟槽,沟槽深度8~10mm,间距100mm;将混凝土表面清洗干净充分湿润后,在浇筑混凝土前刷界面剂或素水泥浆,保证连接面的质量及可靠性。施工中严格控制混凝土基面的处理。
[0161]
(2)针对工程二:
[0162]
为保证浅埋隧道开挖施工中两侧楼房建筑物的安全性,采用钢管隔离桩对建筑物进行隔离加固处理,隔离桩剖面布置见图10所示:
[0163]
在开挖隧道与既有建筑物之间设置双排隔离桩,隔离桩采用φ108微型钢管桩,桩间距为0.5m,排距为1.0m,微型钢管隔离桩成孔直径130mm,桩底进入中风化岩石2m或进入隧道底以下2m;微型桩钻至设计桩长后,下入钢管,采用压力注水泥浆,注浆压力0.2mpa,桩顶制作混凝土顶板;上述微型钢管隔离桩体系对临近建筑物进行隔离保护,保护效果良好。
[0164]
上述工程一和工程二采用了如上所述的浅埋隧道近地接建筑物施工隔离桩结构后,均达到隔离保护的目的,在浅埋隧道开挖的过程中,托换组合加固构造对被保护建筑物起到了良好的保护作用。
[0165]
实施例2:土岩组合地层隧道施工隔离保护数值模拟,具体包括:
[0166]
本实施例以济南市玉函路城市隧道工程为依托,针对本区域典型土岩组合地层条
件,建立二维有限元模型,对有、无隔离桩和布置隔离桩时改变距建筑物距离、排数、间距等因素进行对比,分析不同情况下隔离桩的作用机理及布置原则。
[0167]
步骤一:模拟工况确定,具体包括:
[0168]
有限元模型采用整体式建模方法进行数值模拟,当土层厚度为15m,对有、无隔离桩这两种情况下,隧道施工对邻近砌体结构的影响进行对比分析,验证隔离桩的有效性;然后改变隔离桩的距离、排数、间距等条件,进而分析隔离桩的布置原则。
[0169]
步骤二:有限元计算模型参数,具体包括:
[0170]
s201.模型尺寸及参数选取
[0171]
建模隧道截面跨度11.13m,洞高9.23m,地层模型尺寸宽90m,深45m。隧道开挖前进行超前小导管支护,加固区宽度为0.75m,初支厚度0.3m。
[0172]
隧道东侧某行政楼为3层砖混结构,距隧道截面水平距离4.5m,层高3m,建筑长10.7m,高9.56m;砖混结构第一跨采用柱与板现浇承重,其余跨为纵横墙承重;基础为混凝土条形基础,埋深1.3m;横墙中间开窗,选用隔离桩桩径0.15m进行模拟。
[0173]
假设土层、岩层及超前小导管加固区均为均质材料,采用m
‑
c模型,隧道衬砌、隔离桩采用线弹性模型;将砂浆、砖块及构造柱整体建模,考虑砖砌墙体塑性状态开裂特点,纵横墙体采用von
‑
mises模型,墙体材料的非连续性及随着时间的损耗通过折减墙体弹性模量进行考虑;砌体结构的条基、柱基、柱、楼板、圈梁均采用线弹性模型,模型计算参数如表1;
[0174]
表1:材料物理力学参数
[0175][0176][0177]
s202.验证模型建立及分析
[0178]
为研究隔离桩作用的有效性,采用有限元软件进行模拟,为确保计算结果的准确性,需进行模型验证,验证模型选取土层厚度15m,砌体结构距隧道截面4.5m,通过对有、无隔离桩情况下的土层变形、邻近建筑物的沉降结果进行对比分析,以验证隔离桩的隔离作用,验证计算有限元模型见图11;
[0179]
计算结果如图12,分别为距地面2m处土体沉降曲线以及基底沉降曲线;由土体沉降曲线可知,有、无隔离桩时的土体变形差异显著,在隧道中线左侧的曲线近似重合;在隧道中线右侧,隔离桩两侧沉降量发生突变,曲线从隔离桩布置位置周围逐渐分离,直至全部通过邻近结构,最终又趋于重合;由基底沉降曲线可知,在无隔离桩时,基底最大沉降量
‑
1.45cm,结构两侧沉降差值0.6cm;而布置隔离桩时,基底最大沉降量
‑
0.20cm,结构两侧沉降差值0.18cm。在无隔离桩时,结构两侧沉降差值较大,不均匀沉降较为明显;布置隔离桩后结构两侧沉降差值很小,结构沉降较为均匀;
[0180]
由上述结果对比分析可知,隔离桩能够有效降低隧道施工引起的土体变形、基底沉降以及结构的不均匀沉降;因此,在隧道截面与建筑物之间布置隔离桩能够发挥其阻隔作用,阻隔土中应力传递,从而达到保护邻近建筑的目的。
[0181]
s203.不同工况分析
[0182]
为研究微型钢管隔离桩的隔离作用,在砌体结构上选取临近隧道端基础观测点a,通过改变隔离桩排数m、距结构外墙距离h、横向间距n、纵向间距k、等因素,分析观测点a的沉降变化,进而得出隔离桩的布置原则。模型共分为4组:第1组改变隔离桩的排数m,取m为1、2、3;第2组改变隔离桩距结构外墙距离h,取h为1m、2m、2.25m、2.5m、3.5m;第3组改变隔离桩的横向间距n,取n为0.5m、1.0m、1.5m、2.0m、2.5m;第4组改变隔离桩的纵向间距k,取k为0.5m、1.0m、1.5m、2.0m;有限元模型见图13;
[0183]
s204.隔离桩布置变化引起的砌体结构沉降分析
[0184]
(1)隔离桩排数变化
[0185]
隔离桩布置于隧道截面与砌体结构之间,当隔离桩距结构外墙的距离h、横向间距n、纵向间距k保持不变,仅改变隔离桩的排数m,取m为0、1、2、3,可得观测点a处的沉降值,见图14;由沉降柱状图可知,设置隔离桩前、后观测点a的沉降量变化显著,无隔离桩时,沉降量最大,随着隔离桩排数的增加,沉降值呈下降趋势,但变化趋势已趋于平缓,增加微型钢管隔离桩的排数虽能够进一步降低邻近结构沉降量,但减沉效果并不明显;
[0186]
(2)隔离桩距结构外墙的距离变化
[0187]
隔离桩布置在隧道截面与砌体结构之间,保持隔离桩排数m、横向间距n、纵向间距k均保持不变,当隔离桩单排布置时,改变隔离桩距结构外墙的距离h,取h为1m、2m、2.25m、2.5m、3.5m,可得观测点a处的沉降值,见图15;由沉降值柱状图可知,布置隔离桩前、后观测点a处的沉降差异显著,沉降量显著降低,可知隔离桩可有效减弱邻近建筑物的沉降。随着隔离桩距结构外墙距离不断增加,隔离桩的阻隔作用逐渐减弱,观测点a处的沉降量呈缓慢增加趋势。故隔离桩距结构外墙距离越近,其隔离效果越好。
[0188]
(3)隔离桩纵向间距变化
[0189]
隔离桩单排布置于隧道截面与砌体结构之间,保持隔离桩距结构外墙距离h、横向间距n不变,只改变其纵向间距k,取k为0.5m、1.0m、1.5m、2.0m,观测点a的沉降值见图16;
[0190]
由沉降值柱状图可知,随着纵向间距的增加,隔离桩的相对刚度逐渐减小,对土中应力的阻隔作用不断减弱。因此,当布置隔离桩时,应尽量减小其纵向间距,增加其相对刚度,从而阻隔土中应力传递,提高周围土体抗剪切能力,以获得更好的隔离效果。
[0191]
(4)隔离桩横向间距变化
[0192]
为研究横向间距变化对邻近砌体结构的影响,保持隔离桩距结构外墙的距离h、排数m、纵向间距k不变,改变隔离桩的横向间距n,取n为0.5m、1.0m、1.5m、2.0m、2.5m,可得观测点a处的沉降值,见图17;
[0193]
由沉降值柱状图可知,基础沉降值随横向间距的增加逐渐下降。随着隔离桩横向间距的增加,隔离桩一侧逐渐靠近建筑物,另一侧逐渐靠近隧道截面,隔离桩距离隧道截面越近,阻隔隧道施工引起土中应力的扩散作用越显著,隔离桩距离建筑物越近,对建筑物沉降的限制作用越强,两者效果叠加,增强了减沉效果。
[0194]
s205.隔离桩布置前后砌体结构应变变化分析
[0195]
由以上分析可知,隔离桩能有效阻隔土中应力传递,增强滑移面的抗剪能力,降低邻近建(构)筑物的沉降。由于砌体结构对不均匀沉降很敏感,隔离桩的设置使结构的沉降发生改变,墙体内力也将发生变化。通过对有、无隔离桩两种工况分别建模,隧道施工引起的墙体应变云图如图18所示;
[0196]
由墙体应变云图可知,隧道施工时,墙体应变最大值主要集中在开窗部位,设置隔离桩相对不设置隔离桩时最大应变值降低约90%。此外,由墙体应变值变化可知,隔离桩的布置对墙体同样有显著的加固作用;
[0197]
s206.综上实例可以得出:
[0198]
(1)随着隔离桩排数的增加,虽然使得邻近建筑物的沉降量越来越小,但减沉效果不明显,即通过增加隔离桩排数以获得更好减沉效果不太经济合理;双排微型钢管隔离桩的隔离保护效果与经济性较为突出。
[0199]
(2)当隔离桩单排布置时,距邻近建筑物越近,其减沉效果越好。因此,单排设置隔离桩保护邻近建筑物时,在满足施工条件的允许下,隔离桩应尽可能靠近待保护建筑物布置,同排微型钢管隔离桩间距宜为0.5m~1.0m;
[0200]
(3)当隔离桩双排布置时,随着排距的增加,其隔离效果越好,即双排布置隔离桩时,应一排靠近待保护建筑物,与建筑物间距离宜为1.0~2.5m,另一排应尽量靠近隧道截面位置;
[0201]
由以上结果可知微型钢管隔离桩隔离效果的有效性,提出了钢管隔离桩布置要求,可用于指导工程实践。
[0202]
以上显示和描述了本发明的基本原理、主要特征和本发明的优点。本行业的技术人员应该了解,本发明不受上述实施例限制,上述实施例和说明书中描述的只是说明本发明的原理,在不脱离本发明精神和范围的前提下,本发明还会有各种变化和改进,这些变化和改进都落入要求保护的本发明范围内。本发明要求保护范围由所附的权利要求书及其等效物界定。