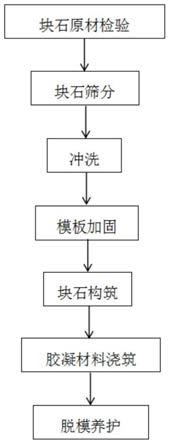
1.本发明涉及防护工程技术领域,具体涉及一种高强固结体施工方法。
背景技术:2.在高寒地区工程施工过程中,其地质主要为砂卵石层,赋存孔隙潜水或微承压水,水位位于1.6~2.0m之间,因基础埋深位于地下水水位以下,需进行降水施工。加之施工区域面积较大,施工时需同时进行开挖施工。因此,降水采用大面积井点降水施工,另外施工区下部地质主要为砂卵石,采用传统冲击钻进行施工时,容易造成塌孔,从而影响施工进度。
3.另外,在施工过程中,部分施工区域基础开挖时出现深度较深的液化层,对本工程施工进度造成影响;对于新建工程,其结构中的高强固结体施工对于工程施工而言,尤为重点,其中块石质量及码放形式、胶凝材料配合比以及浇筑过程进行试验与控制,确保固结体施工满足防护工程的要求。
技术实现要素:4.基于上述技术问题,本发明通过对高强固结体施工工法的研究,对块石质量及码放形式、胶凝材料配合比以及浇筑过程进行试验与控制,目的是提供一种高强固结体施工方法。
5.本发明保护一种高强固结体施工方法,具体步骤包括如下:
6.步骤1,块石原材检验:块石原材检验项目包括块石粒径、含泥量、抗压强度、表观密度、坚固性;其中,块石要求表观密度不小于2500kg/m3,单轴抗压强度最低不小于80mpa,平均抗压强度不小于100mpa,块石粒径选择20~70cm,表面冲洗干净;
7.步骤2,块石筛分:对块石现场进行尺量,按200~500mm、500~700mm两个级配范围进行初步分类堆放,便于后续块石摆放施工;块石断面形状宜为梯形或楔形,中部饱满,最长边不大于最短边的3倍;块石要求质地坚硬,无裂缝、无夹泥薄弱层、无风化、无尖角薄边;
8.步骤3,冲洗:在现场用水泵或洒水车对块石进行冲洗,主要是洗去表面石屑、泥垢或水锈等污物,并达到湿润块石表面的目的,以便与胶凝材料粘结;
9.步骤4,模板加固:模板由定型钢模、模板卡、拱形槽钢梁、拉杆及高强螺栓组成,先由槽钢加工出拱形槽钢梁,通过一端焊接于三维波纹钢板上的螺杆和连接螺杆与三维波纹钢板的连接螺栓拉接固定;通过调整穿在螺杆上拱形槽钢梁上下的螺母可方便的控制胶凝材料结构的厚度;定型模板四周均设卡扣孔,模板安装时,通过模板卡相互连接,拱形槽钢梁和定型钢模上均设限位孔,由活动卡销将拱形槽钢梁和定型钢模连接固定;拱形槽钢梁与定型钢模的限位孔孔距、孔径应严格相符;
10.加固时,拱形槽钢梁下端固定于基础角钢上,基础胶凝材料浇筑完成时,在基础适当位置埋设预埋钢筋;再用角钢与预埋钢筋焊接固定;拱形槽钢梁间距1.5m,也可以根据定型钢模尺寸调整,与三维波纹钢板焊接的拉杆横向间距为2m,纵向间距为3m,拉杆与拱形槽
钢梁通过高强螺栓连接;拱形槽钢梁安装时必须定位准确、通线检查、牢固可靠,定型钢模安装于拱形槽钢梁内侧,每层定型钢模安装后,应及时通线检查其直线性,如有偏差,可用楔形木块加以调整;
11.步骤5,块石构筑:采用人工码放,利用塔吊将块石运至码放地点,码放时遵循大头朝下,小头朝上,大石搭架,中石填空,小石塞缝的原则,码放要平稳;块石入仓根据固结体浇筑顺序分层进行,每层堆积高度不大于1.2m;仓内摆放块石前,在模板上口挂设保护层控制边线,按10cm控制,块石码放后保护层不小于5cm;
12.步骤6,胶凝材料浇筑:因固结体块石码放较密,胶凝材料入仓后不能进行振捣,且需保证浇筑密实,达到抗压强度要求;为保证固结体遮弹层的施工质量,改善胶凝材料流动度,提高胶凝材料抗压强度、降低水化热,减少胶凝材料裂缝、增加胶凝材料密实度,采用含有s95级矿粉的胶凝材料进行浇筑,浇筑胶凝材料时浇筑高度低于块石表面10cm;
13.步骤7,脱模养护:胶凝材料浇筑完成12小时后,进行侧面模板的拆除,侧面模板拆除后对胶凝材料进行保温及洒水养护。
14.进一步的,所述步骤4中,定型钢模的长为1.5m,宽为0.5m,预埋钢筋为φ25,预埋钢筋间距和排距均为1.5m;与预埋钢筋焊接固定的角钢两个边宽均为50cm,厚度5mm。
15.进一步的,所述步骤6中,胶凝材料浇筑采用泵送方式,胶凝材料拌制完成在拌合站出站前和施工现场浇筑前分别进行扩展度测试。
16.进一步的,所述步骤6中,所述的胶凝材料由重量份的如下原料组成:水泥15~30份、粉煤灰1~5份、s95级矿粉0.5~4份、细骨料25~40份、粗骨料一10~16份、粗骨料二28~45份、外加剂0.1~1.2份、水5~8份。
17.进一步的,所述细骨料的粒径为<3mm,粗骨料一的粒径为3~5mm,粗骨料二粒径为5~7mm。
18.进一步的,所述水泥为52.5级。
19.相比于现有的技术,本发明具有如下有益效果:
20.本发明高强固结体施工方法,施工过程安全可靠、施工效率高且对工程施工质量有保证。其中,胶凝材料掺和物sk粉改为s95级矿粉,可以降低胶凝材料成本、提高胶凝材料抗压强度、降低水化热,减少胶凝材料裂缝、增加胶凝材料密实度,节约了一定的费用。
附图说明
21.图1为本发明施工方法流程图;
22.图2为本发明模板模板加固结构示意图。
23.图中,1、定型钢模;2、拱形槽钢梁;4、高强螺栓;5、模板卡。
具体实施方式
24.下面将结合实施例对本发明的技术方案进行清楚、完整地描述,显然,所描述的实施例仅是本发明一部分实施例,而不是全部的实施例。基于本发明中的实施例,本领域普通技术人员在没有做出创造性劳动前提下所获得的所有其他实施例,都属于本发明保护的范围。
25.实施例1
26.本发明保护一种高强固结体施工方法,具体步骤包括如下:
27.步骤1,块石原材检验:块石原材检验项目包括块石粒径、含泥量、抗压强度、表观密度、坚固性;其中,块石要求表观密度不小于2500kg/m3,单轴抗压强度最低不小于80mpa,平均抗压强度不小于100mpa,块石粒径选择20cm,表面冲洗干净;
28.步骤2,块石筛分:对块石现场进行尺量,按200~500mm、500~700mm两个级配范围进行初步分类堆放,便于后续块石摆放施工;块石断面形状宜为梯形或楔形,中部饱满,最长边不大于最短边的3倍;块石要求质地坚硬,无裂缝、无夹泥薄弱层、无风化、无尖角薄边;
29.步骤3,冲洗:在现场用水泵或洒水车对块石进行冲洗,主要是洗去表面石屑、泥垢或水锈等污物,并达到湿润块石表面的目的,以便与胶凝材料粘结;
30.步骤4,模板加固:模板由定型钢模、模板卡、拱形槽钢梁、拉杆及高强螺栓组成,先由槽钢加工出拱形槽钢梁,通过一端焊接于三维波纹钢板上的螺杆和连接螺杆与三维波纹钢板的连接螺栓拉接固定;通过调整穿在螺杆上拱形槽钢梁上下的螺母可方便的控制胶凝材料结构的厚度;定型模板四周均设卡扣孔,模板安装时,通过模板卡相互连接,拱形槽钢梁和定型钢模上均设限位孔,由活动卡销将拱形槽钢梁和定型钢模连接固定;拱形槽钢梁与定型钢模的限位孔孔距、孔径应严格相符;
31.加固时,拱形槽钢梁下端固定于基础角钢上,基础胶凝材料浇筑完成时,在基础适当位置埋设预埋钢筋;再用角钢与预埋钢筋焊接固定;拱形槽钢梁间距1.5m,也可以根据定型钢模尺寸调整,与三维波纹钢板焊接的拉杆横向间距为2m,纵向间距为3m,拉杆与拱形槽钢梁通过高强螺栓连接;拱形槽钢梁安装时必须定位准确、通线检查、牢固可靠,定型钢模安装于拱形槽钢梁内侧,每层定型钢模安装后,应及时通线检查其直线性,如有偏差,可用楔形木块加以调整;
32.步骤5,块石构筑:采用人工码放,利用塔吊将块石运至码放地点,码放时遵循大头朝下,小头朝上,大石搭架,中石填空,小石塞缝的原则,码放要平稳;块石入仓根据固结体浇筑顺序分层进行,每层堆积高度不大于1.2m;仓内摆放块石前,在模板上口挂设保护层控制边线,按10cm控制,块石码放后保护层不小于5cm;
33.步骤6,胶凝材料浇筑:因固结体块石码放较密,胶凝材料入仓后不能进行振捣,且需保证浇筑密实,达到抗压强度要求;为保证固结体遮弹层的施工质量,改善胶凝材料流动度,提高胶凝材料抗压强度、降低水化热,减少胶凝材料裂缝、增加胶凝材料密实度,采用含有s95级矿粉的胶凝材料进行浇筑,浇筑胶凝材料时浇筑高度低于块石表面10cm;
34.步骤7,脱模养护:胶凝材料浇筑完成12小时后,进行侧面模板的拆除,侧面模板拆除后对胶凝材料进行保温及洒水养护。
35.优化的,所述步骤4中,定型钢模的长为1.5m,宽为0.5m,预埋钢筋为φ25,预埋钢筋间距和排距均为1.5m;与预埋钢筋焊接固定的角钢两个边宽均为50cm,厚度5mm。
36.优化的,所述步骤6中,胶凝材料浇筑采用泵送方式,胶凝材料拌制完成在拌合站出站前和施工现场浇筑前分别进行扩展度测试。
37.优化的,所述步骤6中,所述的胶凝材料由重量份的如下原料组成:水泥15份、粉煤灰1份、s95级矿粉0.5份、细骨料25份、粗骨料一10份、粗骨料二28份、外加剂0.1份、水5份。
38.优化的,所述细骨料的粒径为<3mm,粗骨料一的粒径为3mm,粗骨料二粒径为5mm。
39.进一步的,所述水泥为52.5级。
40.实施例2
41.本发明保护一种高强固结体施工方法,具体步骤包括如下:
42.步骤1,块石原材检验:块石原材检验项目包括块石粒径、含泥量、抗压强度、表观密度、坚固性;其中,块石要求表观密度不小于2500kg/m3,单轴抗压强度最低不小于80mpa,平均抗压强度不小于100mpa,块石粒径选择70cm,表面冲洗干净;
43.步骤2,块石筛分:对块石现场进行尺量,按200~500mm、500~700mm两个级配范围进行初步分类堆放,便于后续块石摆放施工;块石断面形状宜为梯形或楔形,中部饱满,最长边不大于最短边的3倍;块石要求质地坚硬,无裂缝、无夹泥薄弱层、无风化、无尖角薄边;
44.步骤3,冲洗:在现场用水泵或洒水车对块石进行冲洗,主要是洗去表面石屑、泥垢或水锈等污物,并达到湿润块石表面的目的,以便与胶凝材料粘结;
45.步骤4,模板加固:模板由定型钢模、模板卡、拱形槽钢梁、拉杆及高强螺栓组成,先由槽钢加工出拱形槽钢梁,通过一端焊接于三维波纹钢板上的螺杆和连接螺杆与三维波纹钢板的连接螺栓拉接固定;通过调整穿在螺杆上拱形槽钢梁上下的螺母可方便的控制胶凝材料结构的厚度;定型模板四周均设卡扣孔,模板安装时,通过模板卡相互连接,拱形槽钢梁和定型钢模上均设限位孔,由活动卡销将拱形槽钢梁和定型钢模连接固定;拱形槽钢梁与定型钢模的限位孔孔距、孔径应严格相符;
46.加固时,拱形槽钢梁下端固定于基础角钢上,基础胶凝材料浇筑完成时,在基础适当位置埋设预埋钢筋;再用角钢与预埋钢筋焊接固定;拱形槽钢梁间距1.5m,也可以根据定型钢模尺寸调整,与三维波纹钢板焊接的拉杆横向间距为2m,纵向间距为3m,拉杆与拱形槽钢梁通过高强螺栓连接;拱形槽钢梁安装时必须定位准确、通线检查、牢固可靠,定型钢模安装于拱形槽钢梁内侧,每层定型钢模安装后,应及时通线检查其直线性,如有偏差,可用楔形木块加以调整;
47.步骤5,块石构筑:采用人工码放,利用塔吊将块石运至码放地点,码放时遵循大头朝下,小头朝上,大石搭架,中石填空,小石塞缝的原则,码放要平稳;块石入仓根据固结体浇筑顺序分层进行,每层堆积高度不大于1.2m;仓内摆放块石前,在模板上口挂设保护层控制边线,按10cm控制,块石码放后保护层不小于5cm;
48.步骤6,胶凝材料浇筑:因固结体块石码放较密,胶凝材料入仓后不能进行振捣,且需保证浇筑密实,达到抗压强度要求;为保证固结体遮弹层的施工质量,改善胶凝材料流动度,提高胶凝材料抗压强度、降低水化热,减少胶凝材料裂缝、增加胶凝材料密实度,采用含有s95级矿粉的固结体胶凝材料进行浇筑,浇筑胶凝材料时浇筑高度低于块石表面10cm;
49.步骤7,脱模养护:胶凝材料浇筑完成12小时后,进行侧面模板的拆除,侧面模板拆除后对胶凝材料进行保温及洒水养护。
50.进一步的,所述步骤4中,定型钢模的长为1.5m,宽为0.5m,预埋钢筋为φ25,预埋钢筋间距和排距均为1.5m;与预埋钢筋焊接固定的角钢两个边宽均为50cm,厚度5mm。
51.优化的,所述步骤6中,胶凝材料浇筑采用泵送方式,胶凝材料拌制完成在拌合站出站前和施工现场浇筑前分别进行扩展度测试。
52.优化的,所述步骤6中,所述的固结体胶凝材料由重量份的如下原料组成:水泥30份、粉煤灰5份、s95级矿粉4份、细骨料40份、粗骨料一16份、粗骨料二45份、外加剂1.2份、水8份。
53.优化的,所述细骨料的粒径为<3mm,粗骨料一的粒径为5mm,粗骨料二粒径为7mm。
54.进一步的,所述水泥为52.5级。
55.实施例3
56.本发明方法中,胶凝材料掺和物sk粉改为s95级矿粉,可以降低胶凝材料成本、提高胶凝材料抗压强度、降低水化热,减少胶凝材料裂缝、增加胶凝材料密实度,节约了一定的费用。具体对比如下:
57.在固结体遮弹层施工中胶凝材料采用基础配合比和调整后的配合比进行对比,就两种方法进行如下对比:
58.表1胶凝材料原基础配合比
[0059][0060]
表2优化后胶凝材料基础配合比
[0061][0062]
经过测算,原基础配合比单价为858元/m3,优化后的配合比综合单价为760元/m3,调整后的配合比每方节约98元。
[0063]
根据设计图纸的固结体遮弹层工程量,优化后的方法共节约84.28万元。
[0064]
尽管已经示出和描述了本发明的实施例,对于本领域的普通技术人员而言,可以理解在不脱离本发明的原理和精神的情况下可以对这些实施例进行多种变化、修改、替换和变型,本发明的范围由所附权利要求及其等同物限定。