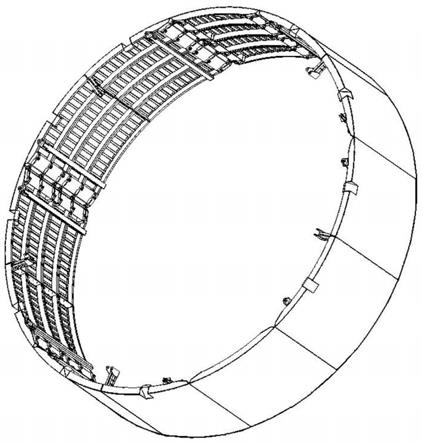
1.本发明属于岩土工程技术领域,具体涉及一种圆形基坑逆作滑模及其施工方法。
背景技术:2.二十世纪二十年代滑模施工技术开始逐渐兴起,到四十年代中期国外各国的滑模技术得到了很大的发展,中国在二十世纪三十年代开始使用手动的滑模设备进行滑模施工,到七十年代末,中国开始广泛推广并应用滑模施工技术。
3.近些年随滑模施工技术及滑模设备不断改进提升,滑模技术得到了快速推广,包括工业建筑中的贮煤仓、烟囱等结构和民用高层、超高层建筑。滑模施工的工艺也多种多样,如在大型工程中较常使用的横向滑模施工工艺以及液压爬模施工工艺等,这些多元化施工工艺的应用为滑模施工技术的成长发展提供了丰饶的土壤。
4.但目前滑模施工大部分仍以向上施工为主,以爬升为主,对于逆作向下的滑模施工方法,施工难度大,仍无合理可靠的技术方法可以借鉴。
技术实现要素:5.针对现有技术存在的问题,本发明提供一种圆形基坑逆作滑模及其施工方法,目的是通过滑动的模板替代传统的固定式模板,减少拆卸、组装模板的工序,优化了整个施工过程,保障安全的前提条件下提高工作效率,降低生产成本,缩短工期。
6.本发明的圆形基坑逆作滑模,采用组合模板结构,整圈模板结构由12片模板组成,在脱模位置对称设两片模板为脱模片,其余模板按两片为一组,用螺栓连接组合为5大扇组合模板,各扇铰接部位通过张拉丝杠调节成整圈固定环状结构;沿基坑口冠梁周圈均匀布置有提升系统,通过液压系统控制提升系统,控制滑模的提升和下降。
7.所述的模板采用厚度δ=10mm钢板制作,面板用[80
×
43
×
5mm的槽钢作为加劲肋,转角部位用厚度δ=10mm钢板作为边幅板;模板组合高度选4m,锥度按5mm控制,在半径方向模板上口大于设计尺寸2.5mm,下口小于设计尺寸2.5mm。
[0008]
所述的提升系统包括提升支架和滑升千斤顶,其中提升支架主要由32
#
工字钢制成,厚度δ=20mm及10mm钢板进行结构加固,采用“一字”悬臂梁,悬出端部又通过预埋拉杆支撑形成稳定的三角结构支架。
[0009]
所述的液压系统是自动调平液压控制台。
[0010]
本发明的圆形基坑逆作滑模施工方法,包括下述顺序进行的施工步骤:
[0011]
(1)混凝土浇筑:
[0012]
按以下顺序进行:就位
‑
下料
‑
平仓振捣
‑
脱模
‑
提升或下放
‑
钢筋绑扎
‑
就位
‑
下料;
[0013]
其中下料要求对称均匀;施工按分层30cm一层进行,采用插入式振捣器振捣,经常变换振捣方向,并避免直接振动爬杆及模板,振捣器插入深度不得超过下层混凝土内50mm,模板提升或下放时停止振捣;滑模提升或下放根据具体根据施工情况确定合理的提升速度,初次模板初次滑升要缓慢进行,并在此过程中对提升系统、液压控制系统、模板变形情
况进行全面检查,发现问题及时处理,待一切正常后方可进行正常浇筑和滑升,平稳提升和下放速度控制在100~180mm/min范围内,最优的速度为150mm/min。
[0014]
(2)滑模脱模:
[0015]
从下往上,对称松两片脱模片连接丝杠,观察脱模片与混凝土粘结情况,再对称拉松各扇模片丝杆,脱模过程中适当提升油顶辅助作业。
[0016]
(3)滑模提升和下放:
[0017]
施工进入正常浇筑,保持连续施工,观察和分析混凝土表面情况,根据现场条件确定合理的滑升速度和分层浇筑厚度;
[0018]
模板提升需在脱模状态下进行,模板与现浇混凝土墙距离100mm以上,方可提升;
[0019]
提升过程中检查千斤顶的情况,观察钢绞线上的压痕和受力状态是否正常,检查模板的水平度;
[0020]
(4)表面修整及养护:
[0021]
混凝土脱模后立即进行闸墩混凝土表面修整,用抹子在混凝土表面作原浆压平或修补,如表面平整亦可不做修整,同时在辅助盘上设洒水管对混凝土进行养护;
[0022]
(5)门洞、梁窝、预埋件施工:
[0023]
井筒内的门洞、梁窝、金属结构预埋件等预埋工作,在滑模施工期间依据钢丝垂线和钢尺定位在操作盘上进行预留,在辅助盘上进行门洞、梁窝模板拆除和预埋钢板、插筋进行处理,模板拆除后清洗涂油,再次复用;
[0024]
(6)滑模控制:
[0025]
为保证结构中心不发生偏移,门洞、梁窝和预埋件位置准确,利用井口桁架梁和井帮固定四根垂线进行中心测量控制,同时也保证其它部位的测量要求;
[0026]
滑模水平控制是利用千斤顶的同步器进行水平控制,或者利用水准仪测量,进行水平检查;
[0027]
(7)滑模拆除:
[0028]
滑模滑升或下降至指定位置时,将滑模滑空后,利用井口提升系统在井口或圈梁部位拆除;
[0029]
其中,所述的滑模装置拆除应注意以下事项:
[0030]
1)必须在统一指挥下进行,并预先编制安全措施;
[0031]
2)操作人员必须配带安全帽及安全带;
[0032]
3)拆卸的滑模部件要严格检查,捆绑牢固后下放。
[0033]
与现有技术相比,本发明的特点和有益效果是:
[0034]
(1)本发明用滑动的模板替代了传统的固定式模板,减少了拆卸、组装模板的工序,优化了整个施工过程,保障安全的前提条件下提高了工作效率,降低生产成本,缩短工期。
[0035]
(2)本发明施工过程中钢筋绑扎、混凝土浇筑、滑模升降平行作业,各工序连续进行互相适应,施工效率高。
[0036]
(3)本发明能够实现圆形基坑的混凝土浇筑的快速施工。比传统的木模板具有高效、快速、美观及节约等多个方面的优势。
附图说明
[0037]
图1是本发明的滑模结构体示意图;
[0038]
图2是本发明的滑模提升系统示意图;
[0039]
图3是本发明的滑模液压系统示意图;
[0040]
图4是本发明的侧模结构示意图;
[0041]
图5是本发明的提升支架示意图;
[0042]
图6是本发明的单元组合模板示意图;
[0043]
图7是本发明的成型结构示意图;
[0044]
图8是本发明的脱模片组合成环示意图;
[0045]
其中:1:滑模模板;2:地连墙;3:平衡梁;4:钢绞线;5:穿心油缸;6:提升支架;7:预埋件;8:冠梁。
具体实施方式
[0046]
下面结合实施例对本技术的技术方案做进一步说明。
[0047]
本实施例中模板的提升和下降主要由对称设置在冠梁上的6套提升机构进行升降及悬吊,滑升千斤顶选用hy
‑
100型10吨千斤顶,滑升动力装置为zyxt
‑
36型自动调平液压控制台。
[0048]
实施例
[0049]
本实施例的圆形基坑逆作滑模结构如图1、图4、图6和图8所示,采用组合模板结构,整圈模板结构由12片滑模模板1组成,在脱模位置对称设两片模板为脱模片,其余模板按两片为一组,用螺栓连接组合为5大扇组合模板,各扇铰接部位通过张拉丝杠调节成整圈固定环状结构;沿基坑口冠梁周圈均匀布置有提升系统,通过液压系统控制提升系统,如图2和图3所示,控制滑模的提升和下降。
[0050]
首先利用井开挖期间提升系统完成井口冠梁提升支架及预埋安装,该提升系统作为滑模施工期间的提升、下降设施。
[0051]
根据井口布置图,完成提升支架的焊接安装、井口安全护栏安装,井口混凝土下料斗安装等,并完成封井口工作。然后形成井上下提升系统,同时完成井下供电电缆敷设、照明系统形成。
[0052]
滑模按设计制作后,进行组装调试,并按表1质量标准进行检查调整。
[0053]
表1滑模质量控制标准
[0054][0055]
滑模组装检查合格后,安装千斤顶,液压系统,插入钢绞线并进行加固,然后进行试滑升3~5个行程,对提升系统、液压控制系统及模板变形情况进行全面检查,发现问题及时解决,确保施工顺利进行。滑模下井组装前,自上而下对井壁进行冲洗,清撬浮渣、锚喷空洞处理,完成底板混凝土面凿毛和冲洗工作。待底板冲洗干净,达到组装条件时,进行测量放线工作,由测量队给出设计轮廓线和十字中心线。
[0056]
利用井口20t龙门吊,将模体分块下放至井底进行组装。组装完毕进行验收后,完成钢筋绑扎和千斤顶、钢绞线、平衡梁安装,模板封堵,同时将模体底部相连通道支立一圈木模板形成斜锥底模结构。
[0057]
其井下组装步骤如下:
[0058]
(1)在井口将每两片模板用螺栓固定组合为5扇单元模板,如附图6所示。
[0059]
(2)用龙门吊先将4扇单元模板下放到井底组装,组装成两半环。
[0060]
(3)用龙门吊先将余下1扇单元模板下放到井底组装,成型结构如附图7所示。
[0061]
(4)提升油缸就位,预穿钢绞线、用龙门吊下放平衡梁与模板连接。
[0062]
(5)平衡梁、钢绞线与模板组对连接。
[0063]
(6)用龙门吊下放脱模片,与单元模片组装及合模,成型如附图8所示。
[0064]
(7)模板间组装调节丝杠、组装走道板等附件。
[0065]
(8)模板就位:通过提升系统调平、就正,再调节丝杠张拉成要求环面尺寸。
[0066]
拼装完成后,后续施工包括以下步骤:
[0067]
(1)钢筋绑扎、钢绞线更换。模体就位后,按设计进行钢筋绑扎、焊接,搭接及焊接要符合设计规范要求,混凝土浇筑后必须露出端面一层横筋,钢筋绑扎间距符合要求,相邻钢筋的接头要错开。
[0068]
(2)混凝土运输。滑模施工用混凝土由搅拌站提供,拌合车运到工地,由下料溜管下至分料盘,然后通过竹节筒入仓。
[0069]
(3)钢筋垂直运输。加工好的钢筋采用井口提升进行垂直运输,其它材料用提升系统悬吊吊笼下放到分料盘上,人工向下放。
[0070]
(4)钢绞线更换。更换钢绞线必须在脱模状态下并有龙门吊辅助提吊,且底模支护
牢固的情况下进行。
[0071]
(5)混凝土浇筑。按以下顺序进行:就位
‑‑
下料
‑‑
平仓振捣—脱模—提升(下放)
‑‑
钢筋绑扎—就位
‑‑
下料。滑模提升(下放)根据具体情况确定合理的提升速度,提升和下放速度控制在150mm/min左右。
[0072]
(6)滑模脱模。对称松两脱模片连接丝杠(从下往上),观察脱模片与混凝土粘结情况,再对称拉松各扇模片丝杆。脱模过程中可适当调节提升油顶辅助作业。
[0073]
(7)滑模提升和下放。施工进入正常浇筑,应尽量保持连续施工,根据现场条件确定合理的滑升速度和分层浇筑厚度。模板提升需在脱模状态下进行,模板与现浇混凝土墙距离100mm以上,方可提升。
[0074]
(8)表面修整及养护。用抹子在混凝土表面作原浆压平或修补,如表面平整亦可不做修整。
[0075]
(9)门洞、梁窝、预埋件施工。井筒内的门洞、梁窝、金属结构预埋件等预埋工作,在滑模施工期间依据钢丝垂线和钢尺定位在操作盘上进行预留。模板拆除后清洗涂油,再次复用。
[0076]
(10)滑模控制。滑模中线控制:利用井口桁架梁和井帮固定四根垂线进行中心测量控制,同时也保证其它部位的测量要求。滑模水平控制:一是利用千斤顶的同步器进行水平控制,二是利用水准仪测量,进行水平检查。
[0077]
(11)滑模拆除。滑模滑升至指定位置时,将滑模滑空后,利用井口提升系统在井口或圈梁部位拆除。
[0078]
上述仅为本发明的具体实施例,但本发明并不局限于此,凡利用此构思对本发明进行非实质性的改动,均应包含在本发明的保护范围之内。